Home>Articles>What Hand Tools Are Needed For A Fleet Maintenance
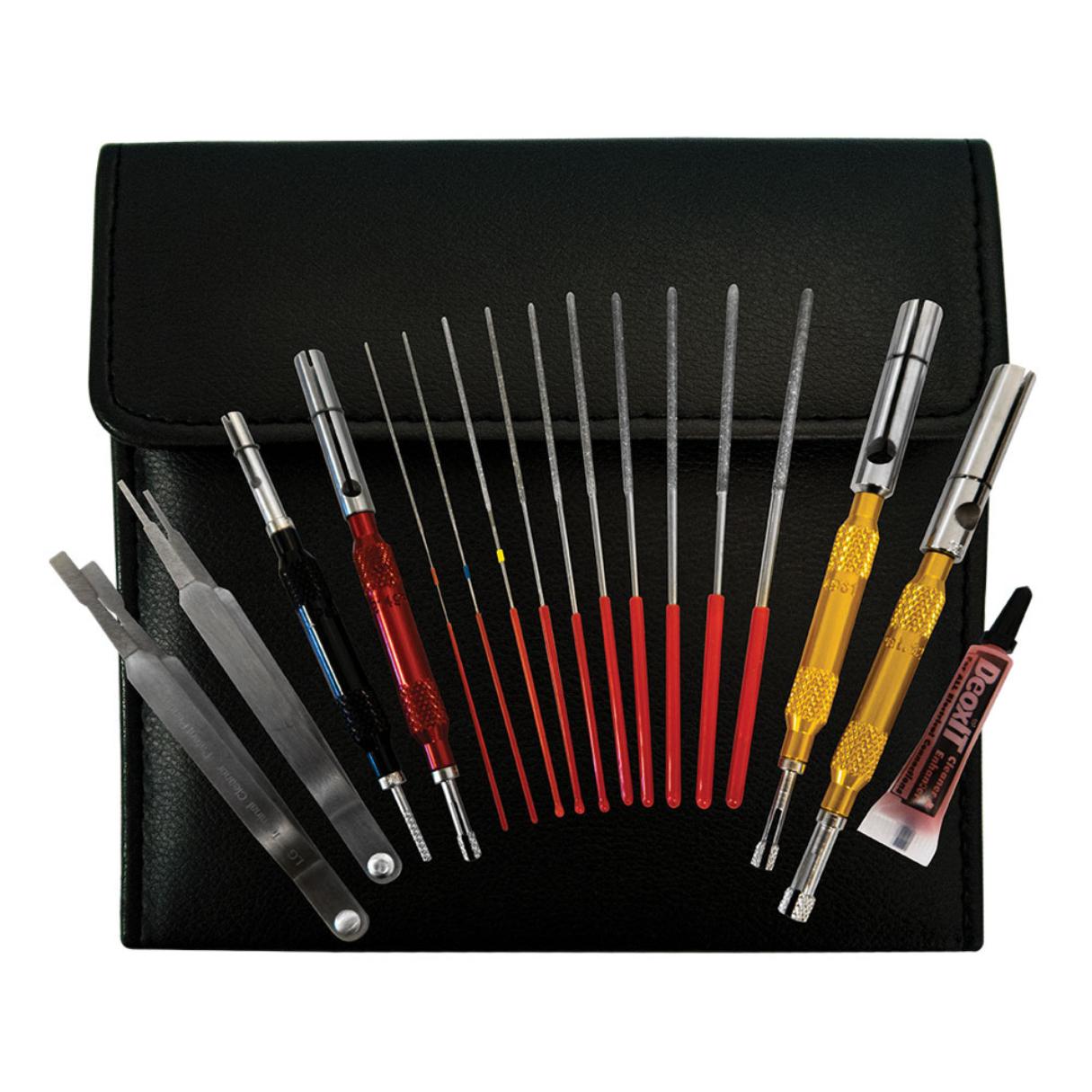
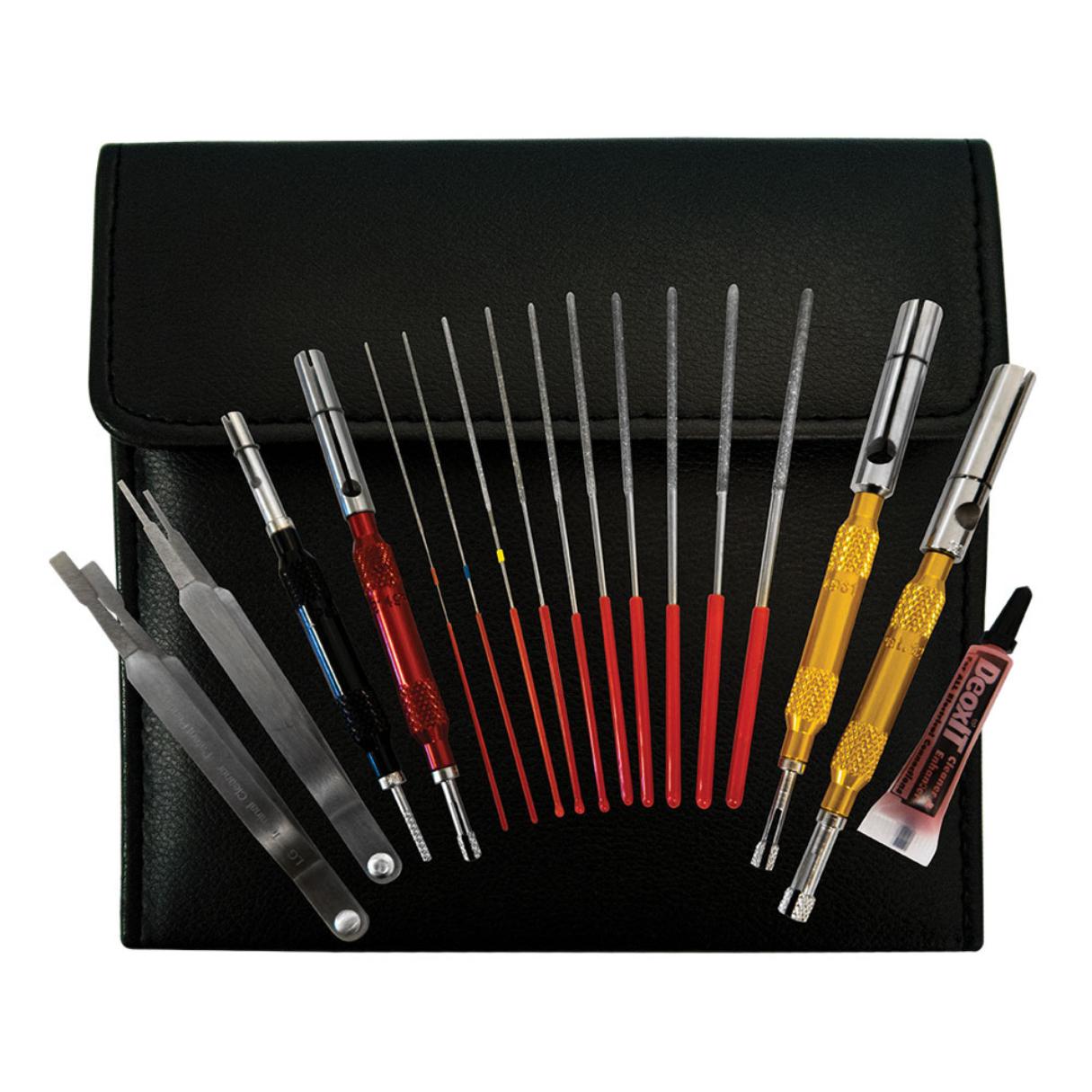
Articles
What Hand Tools Are Needed For A Fleet Maintenance
Modified: January 9, 2024
Discover the essential hand tools required for efficient fleet maintenance. Read our informative articles on the must-have tools for keeping your fleet in top shape.
(Many of the links in this article redirect to a specific reviewed product. Your purchase of these products through affiliate links helps to generate commission for Storables.com, at no extra cost. Learn more)
Introduction
When it comes to fleet maintenance, having the right tools is essential. Whether you are a professional mechanic or a do-it-yourself enthusiast, having a well-equipped toolbox is crucial for keeping your fleet in top shape. Hand tools, in particular, play a significant role in maintaining and repairing various components of vehicles.
In this article, we will discuss the hand tools that are commonly needed for fleet maintenance. From wrenches to screwdrivers and pliers to hammers, each of these tools serves a specific purpose and is indispensable in the world of automotive repairs.
Having a comprehensive set of hand tools not only ensures that you are prepared for a wide range of maintenance tasks, but it also allows you to work efficiently and effectively. Let’s dive into the world of hand tools and explore what you need to have in your toolbox for fleet maintenance.
Key Takeaways:
- Having a well-equipped toolbox with essential hand tools such as wrenches, screwdrivers, pliers, and hammers is crucial for efficiently maintaining and repairing fleet vehicles.
- Selecting high-quality hand tools, using them safely, and maintaining them properly contribute to safe and efficient fleet maintenance operations, ensuring longevity and enhancing productivity.
Read more: What Hand Tools Do I Need As A Mechanic
Common Hand Tools
When it comes to fleet maintenance, there are several common hand tools that every mechanic or DIY enthusiast should have in their toolbox. These tools are versatile, reliable, and essential for a wide range of maintenance and repair tasks.
Let’s take a closer look at some of the most common hand tools used in fleet maintenance:
Wrenches
Wrenches are a staple in any toolbox. They come in various sizes and types such as open-end wrenches, box-end wrenches, and adjustable wrenches. Wrenches are used to tighten or loosen fasteners like nuts, bolts, and screws. Having a set of wrenches in different sizes ensures that you can tackle any fastening job.
Screwdrivers
Screwdrivers are essential for removing or tightening screws and other fasteners. Flathead screwdrivers and Phillips-head screwdrivers are the two most common types. Flathead screwdrivers have a flat blade, while Phillips-head screwdrivers have a cross-shaped blade. It’s important to have screwdrivers in different sizes to accommodate various screw types and sizes.
Pliers
Pliers are versatile tools that are used for gripping, bending, and cutting. They come in different types such as needle-nose pliers, slip-joint pliers, and cutting pliers. Needle-nose pliers are ideal for reaching into tight spaces, while cutting pliers are used for cutting wires and other materials.
Read more: What Do I Need To Sharpen Hand Tools
Hammers
Hammers are necessary for tasks that require force or precision. They are used for driving nails, removing dents, and breaking apart components. There are different types of hammers available, including claw hammers, ball-peen hammers, and rubber mallets. Each has its own purpose and is useful in different situations.
Sockets and Socket Sets
Sockets and socket sets are used in conjunction with a ratchet handle to tighten or loosen bolts and nuts. They come in a wide variety of sizes to fit different fasteners. Socket sets usually include a range of socket sizes, extensions, and adapters, making them a valuable addition to any tool collection.
Tape Measures
Tape measures are essential for measuring distances accurately. Whether you need to measure the length of a component or the clearance between two parts, a tape measure is an indispensable tool. Look for a durable and easy-to-read tape measure that can handle the demanding nature of fleet maintenance tasks.
These are just a few of the common hand tools used in fleet maintenance. As you dive deeper into the world of automotive repairs, you may find the need for additional specialized tools. However, having a solid foundation with these common hand tools will help you handle a wide range of maintenance and repair tasks with confidence.
Wrenches
Wrenches are an essential hand tool for fleet maintenance, as they are used to tighten or loosen fasteners such as nuts, bolts, and screws. There are various types of wrenches available, each designed for specific applications and offering unique advantages.
Let’s take a closer look at some of the most commonly used wrenches in fleet maintenance:
- Open-End Wrenches: Open-end wrenches, also known as “spanners,” have a U-shaped opening at one or both ends. They provide a firm grip on the fastener and allow for quick adjustments. Open-end wrenches come in different sizes to fit various bolt and nut sizes.
- Box-End Wrenches: Box-end wrenches have a closed-end with a six-point or twelve-point socket. They provide a more secure grip on the fastener and are less likely to slip compared to open-end wrenches. Box-end wrenches are great for applying more torque and are available in different sizes.
- Combination Wrenches: Combination wrenches combine the features of both open-end and box-end wrenches. They have an open-end on one side and a closed-end on the other. This versatile design allows for fast adjustments with the open-end and secure tightening or loosening with the box-end.
- Adjustable Wrenches: Adjustable wrenches, also known as “crescent wrenches,” feature an adjustable jaw that can fit a wide range of fastener sizes. They are ideal for situations where you don’t have the exact size wrench available. Adjustable wrenches have a movable jaw that can be adjusted by sliding it along a worm gear.
- Torque Wrenches: Torque wrenches are specialized wrenches used to apply a specific amount of torque to a fastener. They are often used in precision applications where the proper amount of tightening is critical. Torque wrenches have a built-in mechanism that clicks or releases when the desired torque level is reached.
When selecting wrenches for fleet maintenance, it’s important to consider the types of fasteners you will be working with and the specific requirements of your tasks. Having a variety of wrenches in different sizes and types will ensure that you have the right tool for any job. Additionally, investing in high-quality wrenches made from durable materials will ensure their longevity and performance.
Remember to use wrenches correctly, applying force in the direction that is specified by the fastener. Avoid using an adjustable wrench if the exact size wrench is available, as adjustable wrenches may slip and cause damage to the fastener or the wrench itself. Regularly inspect your wrenches for any signs of wear or damage and replace them as necessary to maintain safe and efficient fleet maintenance operations.
Screwdrivers
Screwdrivers are essential hand tools for fleet maintenance as they are used to tighten or loosen screws and other fasteners. They come in different types and sizes to accommodate various screw heads and applications.
Here are some of the most commonly used screwdrivers in fleet maintenance:
- Flathead Screwdrivers: Flathead screwdrivers have a flat, straight blade that fits into the slotted screw heads. They are widely used in different industries and can handle a variety of applications. Flathead screwdrivers come in different sizes to fit various screw sizes. They are commonly used for general-purpose tasks.
- Phillips-Head Screwdrivers: Phillips-head screwdrivers have a cross-shaped blade that fits into the Phillips-style screw heads. They are designed to provide better torque and prevent cam-out (slipping out of the screw head) during use. Phillips-head screwdrivers are commonly used in automotive and other industries. Like flathead screwdrivers, they come in different sizes.
- Torx Screwdrivers: Torx screwdrivers have a six-pointed star-shaped tip that fits into Torx screw heads. This design provides better grip and minimizes the risk of stripping the screw head. Torx screws are commonly found in automotive applications, such as engine components and electrical connections.
- Hex Screwdrivers: Hex screwdrivers, or Allen wrenches, are used to tighten or loosen screws with a hexagonal socket. They are commonly used in machinery, automotive, and furniture assembly. Hex screwdrivers are available in individual sizes or as part of a set.
- Precision Screwdrivers: Precision screwdrivers are used for delicate and intricate tasks that require a smaller size and more precise control. They are commonly used for electronics, small appliances, and other precision applications. Precision screwdriver sets often include various types of screwdriver tips and sizes.
When selecting screwdrivers for fleet maintenance, it’s important to consider the types of screws you will be encountering and the specific requirements of your tasks. Having a wide range of screwdrivers in different sizes and types ensures that you have the right tool for every job.
Additionally, it is essential to use the correct size and type of screwdriver for each screw. Using the wrong-sized or incorrect type of screwdriver can lead to stripped screw heads, damage to the screw or surrounding components, and difficulty in tightening or loosening the screws.
Investing in high-quality screwdrivers made from durable materials will ensure their longevity and performance. Regularly inspect your screwdrivers for any signs of wear or damage, such as bent or worn-out blades, and replace them if necessary to maintain safe and efficient fleet maintenance operations.
Remember to always apply strong and steady pressure when using screwdrivers to avoid slipping and potential injuries. By having a well-stocked collection of screwdrivers and using them correctly, you can easily tackle a wide range of maintenance and repair tasks in your fleet.
Pliers
Pliers are versatile hand tools that are essential in fleet maintenance. They are designed to grip, hold, bend, and cut various materials, making them indispensable for a wide range of tasks.
Let’s take a closer look at some of the most commonly used pliers in fleet maintenance:
- Needle-Nose Pliers: Needle-nose pliers have long, slender jaws that taper to a point. They are ideal for reaching into tight spaces and performing delicate tasks. Needle-nose pliers can grip small objects, bend wires, and access hard-to-reach areas with precision.
- Slip-Joint Pliers: Slip-joint pliers are versatile and feature an adjustable pivot point that allows you to change the jaw opening. They can be used for general gripping, bending, and holding tasks. Slip-joint pliers have multiple notches near the joint, enabling you to set the jaw width to accommodate various sizes of materials.
- Locking Pliers: Locking pliers, also known as Vise-Grip pliers, have a jaw that can be locked in place, providing a strong, secure grip on materials. They are commonly used for holding, clamping, and removing stubborn fasteners. The locking mechanism allows you to apply constant pressure without needing to continuously grip the handles.
- Cutting Pliers: Cutting pliers, also called wire cutters or side cutters, have sharp jaws that are designed to cut different types of wire and other materials. They are ideal for trimming electrical wires, cutting zip ties, and snipping through small metal components. Cutting pliers come in different sizes and cutting capacities.
- Tongue and Groove Pliers: Tongue and groove pliers, often referred to as Channellock pliers, have an adjustable jaw that can be set to various widths using multiple notches. These pliers provide a secure grip on objects of different sizes and shapes. They are commonly used for plumbing tasks, gripping pipes, and turning fittings.
When selecting pliers for fleet maintenance, consider the specific tasks you will be performing. It’s essential to have a variety of pliers that can handle different materials, sizes, and gripping needs. Investing in high-quality pliers made from durable materials will ensure their longevity and performance.
When using pliers, always use the appropriate grip and avoid applying excessive force that may damage the pliers or the material you are working on. Inspect your pliers regularly for any signs of wear or damage, such as loose joints or worn-out cutting edges, and replace them as necessary to maintain safe and efficient fleet maintenance operations.
By having a well-rounded collection of pliers and using them correctly, you will be equipped to handle a wide range of tasks in your fleet maintenance routine.
Hammers
Hammers are essential hand tools for fleet maintenance, as they are used for a variety of tasks such as driving nails, removing dents, and breaking apart components. They come in different types and sizes, each serving specific purposes in the world of automotive repairs.
Let’s take a closer look at some of the most commonly used hammers in fleet maintenance:
- Claw Hammer: Claw hammers are one of the most versatile hammers and are commonly used in a wide range of applications. They feature a flat striking surface on one end for driving nails and a V-shaped claw on the other end for removing nails. Claw hammers are available in different sizes and have various handle materials to choose from.
- Ball-Peen Hammer: Ball-peen hammers, also known as engineer’s hammers, have a striking face on one end and a rounded peen on the other end. They are commonly used in metalworking and are great for shaping, riveting, and bending metal. Ball-peen hammers are available in different head weights and handle lengths.
- Dead Blow Hammer: Dead blow hammers are designed to minimize rebound and provide a controlled striking force. They are filled with shot or sand, which absorbs the shock upon impact. Dead blow hammers are ideal for tasks that require precise and controlled striking, such as working with delicate parts or dislodging stubborn components.
- Rubber Mallet: Rubber mallets are made with a rubber or plastic head and are used when a softer striking force is required. They are less likely to cause damage or leave marks on delicate surfaces. Rubber mallets are commonly used in automotive repairs for tasks such as installing trim pieces and adjusting body components.
- Sledgehammer: Sledgehammers are heavy-duty hammers with a large, flat striking surface. They are designed for heavy impact and are commonly used for demolishing, driving stakes, and breaking apart larger components. Sledgehammers are available in various weights, and the length of the handle can vary depending on the intended application.
When selecting hammers for fleet maintenance, consider the specific tasks you will be performing and the materials you will be working with. It’s important to choose the right type and size of hammer to ensure that the striking force is appropriate for the job. Additionally, investing in hammers with durable materials and ergonomic handles will ensure their longevity and provide a comfortable grip during use.
Always use hammers with caution, wearing appropriate safety gear such as goggles and gloves. Inspect your hammers regularly for any signs of wear or damage, such as loose heads or worn-out handles, and replace them as necessary to maintain safe and efficient fleet maintenance operations.
By having a variety of hammers and using them correctly, you will be well-equipped to handle a wide range of maintenance and repair tasks in your fleet.
Sockets and Socket Sets
Sockets and socket sets are indispensable hand tools for fleet maintenance. They are used in conjunction with a ratchet handle to tighten or loosen bolts and nuts. Sockets are designed to fit onto the fastener head, providing a secure grip and allowing for efficient and precise application of torque.
Let’s take a closer look at sockets and socket sets commonly used in fleet maintenance:
- Sockets: Sockets come in various sizes and types to accommodate different fasteners. They have a hexagonal opening (also known as drive) on one end to fit onto the fastener head. Sockets are available in both metric and standard (imperial) sizes, so it’s important to have a comprehensive set that includes both systems. They are typically made from high-quality steel for durability and can be used with a variety of handle options.
- Socket Sets: Socket sets are collections of sockets that come in a convenient case or tray, organized by size and type. They often include a ratchet handle, extensions, and adapters. Socket sets are available in various sizes and configurations, offering versatility and efficiency when it comes to fleet maintenance. A socket set ensures that you have a wide selection of sockets readily available for different tasks.
- Impact Sockets: Impact sockets are specially designed to withstand the high torque generated by impact wrenches. They are made from thicker, more robust materials to handle the powerful forces exerted during use. Impact sockets are commonly used in heavy-duty applications, such as suspensions, engine work, and tire changes.
- Deep Sockets: Deep sockets have a longer body, allowing them to reach fasteners in recessed or hard-to-reach areas. They are perfect for situations where a standard socket cannot provide adequate access. Deep sockets are commonly used in automotive repairs, particularly in engine compartments and underneath vehicles.
- Spark Plug Sockets: Spark plug sockets are designed specifically for removing or installing spark plugs. They have a rubber insert or a magnetic feature to securely hold the spark plug during installation or removal. Spark plug sockets come in specific sizes to fit the varying sizes of spark plugs used in different vehicles.
When selecting sockets and socket sets for fleet maintenance, consider the specific fasteners you will be working with and the types of tasks you will be performing. It’s important to have a variety of socket sizes and types to accommodate different bolts and nuts. Investing in high-quality sockets made from durable materials will ensure their longevity and effective performance.
Regularly inspect your sockets for any signs of wear or damage, such as deformed openings or damaged drive edges. Replace any worn-out sockets to maintain safe and efficient fleet maintenance operations. Proper use of sockets and ensuring that they are securely attached to a ratchet handle will minimize the risk of slippage and potential injuries.
By having a comprehensive set of sockets and socket sets, you will be well-equipped to handle a wide range of maintenance and repair tasks in your fleet.
Tape Measures
Tape measures are essential hand tools for fleet maintenance as they are used for accurately measuring distances, lengths, and clearances. Whether you need to measure components, check alignment, or ensure proper fits, a tape measure is an indispensable tool in your toolbox.
When it comes to tape measures, there are a few key factors to consider:
Durability
Since fleet maintenance tasks can be demanding and rugged, it’s important to choose a tape measure that is built to withstand the harsh conditions of the automotive environment. Look for tape measures that have a durable, impact-resistant casing, and a strong, sturdy blade that can handle repeated use and potential drops.
Length and Width
Tape measures come in various lengths and widths. Common tape measure lengths range from 16 to 35 feet, with some longer options available for specialized applications. The width of the blade can vary as well. Choose a length and width that suits your specific needs and the types of measurements you will be taking in your fleet maintenance tasks.
Readability
Opt for a tape measure that has large, easy-to-read markings and numbers. A clear and visible measurement scale on both sides of the blade will ensure accurate and efficient measurements. It’s also beneficial to have markings in both inches and centimeters to cater to different measurement requirements.
Read more: What Hand Tools Do I Need For Woodworking
Locking Mechanism
Look for tape measures that feature a reliable locking mechanism to secure the blade in place while taking measurements. A good locking mechanism ensures that the tape measure stays in position, allowing you to read the measurement without the blade retracting.
Additional Features
Some tape measures offer additional features that can be useful for fleet maintenance. For example, a belt clip allows for convenient storage and easy access, while a magnetic tip allows you to securely attach the tape measure to metal surfaces for hands-free measuring. These extra features can enhance the usability and versatility of the tape measure.
Having a quality tape measure in your toolbox ensures accurate measurements, which is crucial for various tasks in fleet maintenance. Whether you are measuring the length of a component, checking clearances between parts, or ensuring proper fits, a reliable tape measure is an invaluable tool to have on hand.
Regularly inspect and clean your tape measure to maintain its accuracy and functionality. If you notice any damage or wear, replace the tape measure to ensure precise measurements in your fleet maintenance efforts.
By choosing a sturdy and reliable tape measure that meets your specific needs, you will be equipped to handle precise measurements and ensure the proper functioning and maintenance of your fleet vehicles.
Pry Bars
Pry bars are versatile hand tools that are commonly used in fleet maintenance for various tasks, such as prying, lifting, and aligning components. These sturdy and durable tools are invaluable when it comes to tackling stubborn and tightly secured parts.
Here are some key points about pry bars:
Types of Pry Bars
There are different types of pry bars available, each designed for specific applications. Common types of pry bars include:
- Crowbars: Crowbars have a flat, chisel-like blade on one end and a curved, hooked end on the other. They are commonly used for prying and leveraging tasks, such as removing trim panels, pulling nails, or separating components.
- Flat Pry Bars: Flat pry bars, also known as flat bars or wrecking bars, have a wider and flatter blade compared to crowbars. They are ideal for heavier prying tasks, such as removing floorboards, prying apart assemblies, or sliding materials into place.
- Trim Pry Bars: Trim pry bars, sometimes called trim pullers, have a thin and sharp blade designed specifically for removing trim pieces, moldings, and other delicate materials without causing damage. They are especially useful in automotive interiors for removing panels and trim without leaving unsightly marks.
Read more: What Is A Hand Tool
Choosing the Right Pry Bar
When selecting pry bars for fleet maintenance, consider the specific tasks you will be performing and the materials you will be working with. Make sure to choose a pry bar that is strong and sturdy enough to handle the force required, as well as one that is appropriate for the size and shape of the components you are working with.
Safety Considerations
Using pry bars requires caution and proper technique to avoid injuries or damage. Here are a few safety tips:
- Use pry bars with appropriate grip and leverage to minimize the risk of slipping or losing control.
- Avoid applying excessive force or prying at an awkward angle, as it may lead to the bar slipping or components breaking unexpectedly.
- Wear protective gloves and eyewear to protect yourself from potential hazards, such as flying debris or sharp edges.
- Inspect your pry bars regularly for any signs of wear, such as bent blades or loose handles. Replace worn or damaged pry bars to maintain safe and efficient fleet maintenance operations.
Pry bars are incredibly useful tools in fleet maintenance, allowing you to easily pry apart, lift, or align components. By choosing the right pry bars for the job and using them safely and correctly, you can efficiently handle various maintenance and repair tasks in your fleet with ease.
Files
Files are versatile hand tools that are commonly used in fleet maintenance for shaping, smoothing, and removing material from various surfaces. They are essential for tasks that require precision and accuracy, such as filing down rough edges, deburring metal, or shaping components for proper fit.
Types of Files
There are different types of files available, each designed for specific applications. Here are some common types of files used in fleet maintenance:
- Flat Files: Flat files have a flat, rectangular shape with parallel sides and a single-cut or double-cut pattern of teeth. They are used for general purpose filing and smoothing of flat surfaces, such as metal, plastic, or wood.
- Half-Round Files: Half-round files have one flat side and one curved side, resembling a semicircle. They are ideal for filing curved surfaces, such as pipes, contours, or grooves.
- Round Files: Round files have a cylindrical shape and are commonly used for filing holes, slots, or concave surfaces. They come in different diameters to accommodate various hole sizes.
- Triangle Files: Triangle files have three flat sides and a tapered, triangular shape. They are often used for filing corners, angles, or grooves with precision.
- Needle Files: Needle files have a small, slender shape with various profiles, including flat, round, or triangular. They are commonly used for intricate and detailed filing work, such as working on small components or delicate parts that require precise shaping.
Read more: What Are The 10 Hand Tools
Choosing the Right File
When selecting files for fleet maintenance, consider the specific tasks you will be performing and the materials you will be working with. Choose the appropriate file with the right shape, size, and tooth pattern to achieve the desired result. It’s important to have a variety of file types in your collection to handle different filing requirements.
Safe Handling and Maintenance
While using files, it’s important to follow proper safety precautions to avoid injuries and achieve the best results:
- Always wear protective gloves and eyewear when filing to protect yourself from potential hazards, such as flying debris and sharp edges.
- Secure the workpiece firmly to prevent slipping or accidental movements while filing.
- Apply even and consistent pressure while filing to avoid creating uneven surfaces or removing too much material.
- Regularly clean your files, removing any debris or filings that may clog the teeth, to maintain optimum performance.
- Inspect your files regularly for any signs of wear, such as dull or damaged teeth. Replace worn-out files to ensure efficient fleet maintenance operations.
Files are reliable tools that allow for precise shaping and smoothing in fleet maintenance. By choosing the right file for the job, practicing safe handling techniques, and properly maintaining your files, you can achieve professional results and ensure the longevity of your fleet vehicles.
Wire Cutters
Wire cutters are essential hand tools used in fleet maintenance for cutting and trimming wires, cables, and electrical components. They are designed with sharp jaws and a cutting edge to provide clean and precise cuts, making them indispensable for electrical repairs, wire stripping, and other related tasks.
Types of Wire Cutters
There are various types of wire cutters available, each designed for specific applications. Here are some common types of wire cutters used in fleet maintenance:
- Diagonal Cutters: Diagonal cutters, also known as side cutters or diagonal pliers, have jaws that form a diagonal tip. They are ideal for cutting through wires, cables, and small components. The angled cutting edge allows you to reach into tight spaces and provide flush cuts.
- Needle-Nose Pliers with Wire Cutter: Needle-nose pliers often feature a built-in wire cutter near the base of the jaws. These pliers are excellent for gripping and maneuvering small wires, making them efficient for intricate electrical work.
- Cable Cutters: Cable cutters are heavy-duty wire cutters designed to cut through larger cables and wires, such as those used in automotive applications. They are commonly used to cut battery cables, electrical cables, and other thick-gauge wires.
- Ratcheting Wire Cutters: Ratcheting wire cutters provide increased cutting power through a ratcheting mechanism. This allows for easier cutting of thicker wires and cables by applying force gradually, reducing hand strain and providing clean, precise cuts.
- Wire Strippers: While not strictly wire cutters, wire strippers are essential tools that combine cutting and stripping capabilities. They are used to remove insulation from electrical wires without damaging the conductive wire strands. Wire strippers have specially designed cutting edges and notches that allow for precise stripping of different wire gauges.
Read more: What Are Insulated Hand Tools?
Choosing the Right Wire Cutters
When selecting wire cutters for fleet maintenance, consider the specific tasks you will be performing and the sizes of wires you will be working with. Choose wire cutters that are suitable for your needs in terms of cutting capabilities, grip comfort, and durability.
Safety Considerations
When using wire cutters, it’s important to follow proper safety measures to avoid injuries:
- Always wear protective gloves and eyewear to safeguard yourself from potential hazards, such as flying wire fragments or accidental wire recoil.
- Make sure the wire you are cutting is not live or connected to any power source to prevent electrical shocks.
- Ensure a stable and secure work surface, especially when cutting thicker wires or cables, to prevent slipping or unexpected movements.
- Regularly inspect your wire cutters for any signs of wear or damage, such as dull blades or loose joints. Replace worn-out wire cutters to maintain safe and efficient fleet maintenance operations.
Wire cutters are indispensable tools for fleet maintenance, allowing you to easily and accurately cut wires and cables. By choosing the appropriate wire cutters for your specific needs and using them safely and correctly, you can efficiently handle electrical repairs and wire-related tasks in your fleet with confidence.
Utility Knives
Utility knives, also known as box cutters or razor knives, are versatile hand tools used in fleet maintenance for a wide range of cutting tasks. They feature a retractable blade that can be easily extended or retracted as needed, making them incredibly handy for various applications.
Features and Uses
Utility knives are designed to provide precision and control while cutting different materials. Here are some key features and common uses of utility knives in fleet maintenance:
- Retractable Blade: The retractable blade of a utility knife enables safe storage and prevents accidental cuts when not in use. The blade can be easily extended and locked into place when cutting through different materials.
- Blade Options: Utility knives can accommodate a variety of blade styles and types. Common blade types include standard straight-edge blades, hook blades for cutting materials like carpet, and serrated blades for grip and control on tougher materials. Some utility knives even offer the ability to switch out blades for specific cutting applications.
- Cutting Various Materials: Utility knives are suitable for cutting a wide range of materials, including but not limited to packaging materials, cardboard, plastic, rubber, fiberglass, and lightweight materials. Their versatility makes them useful in multiple fleet maintenance tasks.
- Stripping Insulation: Utility knives with specially designed blades can be used for stripping insulation from electrical wires. The sharp edge allows for precise, controlled cuts without damaging the conductive wire strands.
- Emergency Situations: In addition to regular maintenance tasks, utility knives can come in handy during emergency situations, such as cutting through seat belts or freeing trapped occupants in case of accidents or emergencies.
Safety Considerations
While using utility knives, it’s crucial to prioritize safety to prevent accidents and injuries:
- Always exercise caution and focus when using a utility knife.
- Ensure that the blade is securely locked in place before use and that it retracts completely when not in use.
- When cutting, apply controlled and even pressure to maintain accuracy and prevent slips.
- Wear protective gloves when handling materials that may cause cuts or abrasions.
- Regularly inspect the utility knife for any signs of wear, such as dull blades or loose components. Replace worn-out utility knives to maintain safe and efficient fleet maintenance operations.
Choosing the Right Utility Knife
When selecting a utility knife for fleet maintenance, consider the specific tasks you will be performing and the materials you will be cutting. Look for a utility knife with a comfortable grip, a sturdy and durable construction, and a mechanism that allows for easy blade changes and adjustments. Additionally, ensure that the knife has a reliable locking mechanism to prevent accidental blade extensions.
By choosing the right utility knife for your needs and using it safely and correctly, you can perform a wide range of cutting tasks efficiently and effectively in your fleet maintenance endeavors.
Conclusion
In fleet maintenance, having the right hand tools is essential for efficiently and effectively performing various maintenance and repair tasks. The hand tools discussed in this article – wrenches, screwdrivers, pliers, hammers, sockets and socket sets, tape measures, pry bars, files, wire cutters, and utility knives – play crucial roles in fleet maintenance operations.
Wrenches are used for tightening and loosening fasteners, while screwdrivers allow for the removal and installation of screws. Pliers provide a versatile grip for bending, cutting, and gripping different materials. Hammers are instrumental for tasks that require force or precision, such as driving nails and removing dents. Sockets and socket sets are indispensable for tightening and loosening bolts and nuts. Tape measures ensure accurate measurements for component fitting and clearance checks.
Pry bars are vital for prying, lifting, and aligning components, while files allow for precise shaping and smoothing of surfaces. Wire cutters are indispensable when it comes to cutting and trimming wires and cables, while utility knives provide versatility in cutting various materials. Each of these hand tools serves unique purposes, helping to maintain and repair fleet vehicles efficiently and effectively.
When selecting hand tools, it is essential to consider the specific tasks at hand and choose tools that are durable, reliable, and properly suited to the demands of fleet maintenance. Additionally, using these tools safely, following proper techniques, and regularly inspecting and maintaining them contribute to safe and efficient fleet maintenance operations.
By having a well-equipped toolbox consisting of these essential hand tools, fleet maintenance professionals and DIY enthusiasts will be well-prepared to handle a wide range of maintenance and repair tasks. Investing in high-quality hand tools and maintaining them properly will ensure their longevity and enhance the productivity of fleet maintenance operations.
Remember, having the right hand tools is a solid foundation for successful fleet maintenance, improving efficiency and helping to keep your fleet vehicles in top shape for optimal performance and longevity.
Frequently Asked Questions about What Hand Tools Are Needed For A Fleet Maintenance
Was this page helpful?
At Storables.com, we guarantee accurate and reliable information. Our content, validated by Expert Board Contributors, is crafted following stringent Editorial Policies. We're committed to providing you with well-researched, expert-backed insights for all your informational needs.
0 thoughts on “What Hand Tools Are Needed For A Fleet Maintenance”