Home>Renovation & DIY>Tools & Equipment>What Mineral Is Used For Most Sandpaper
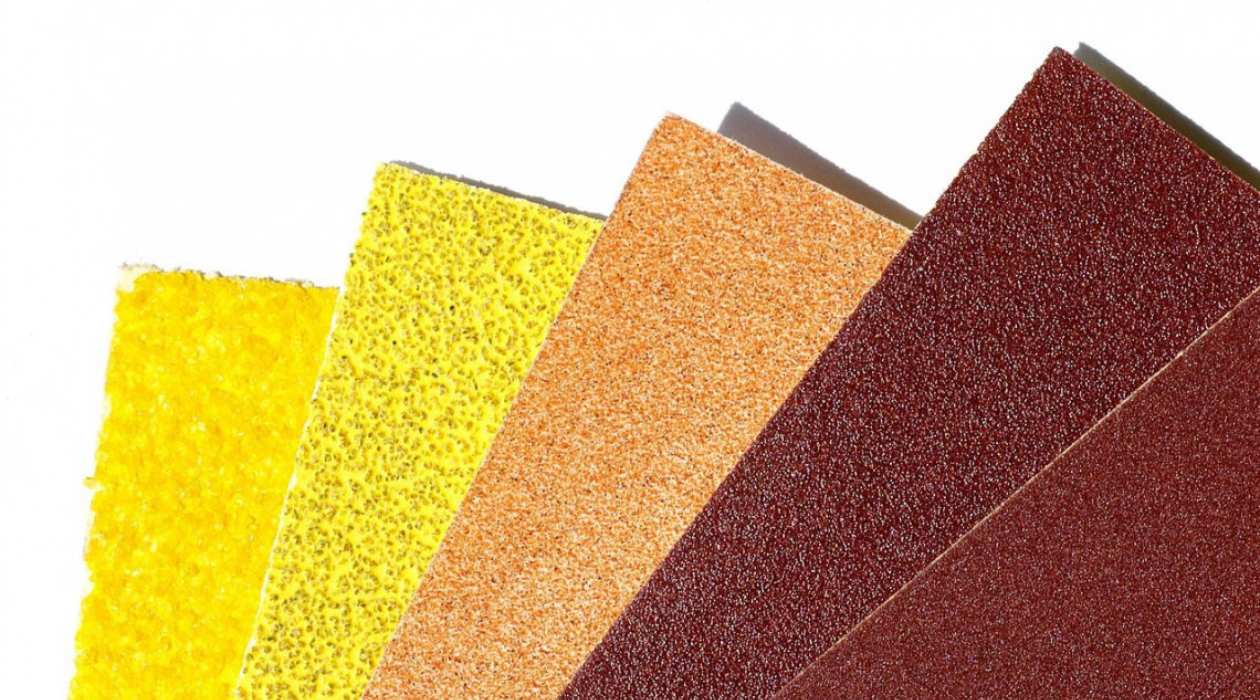
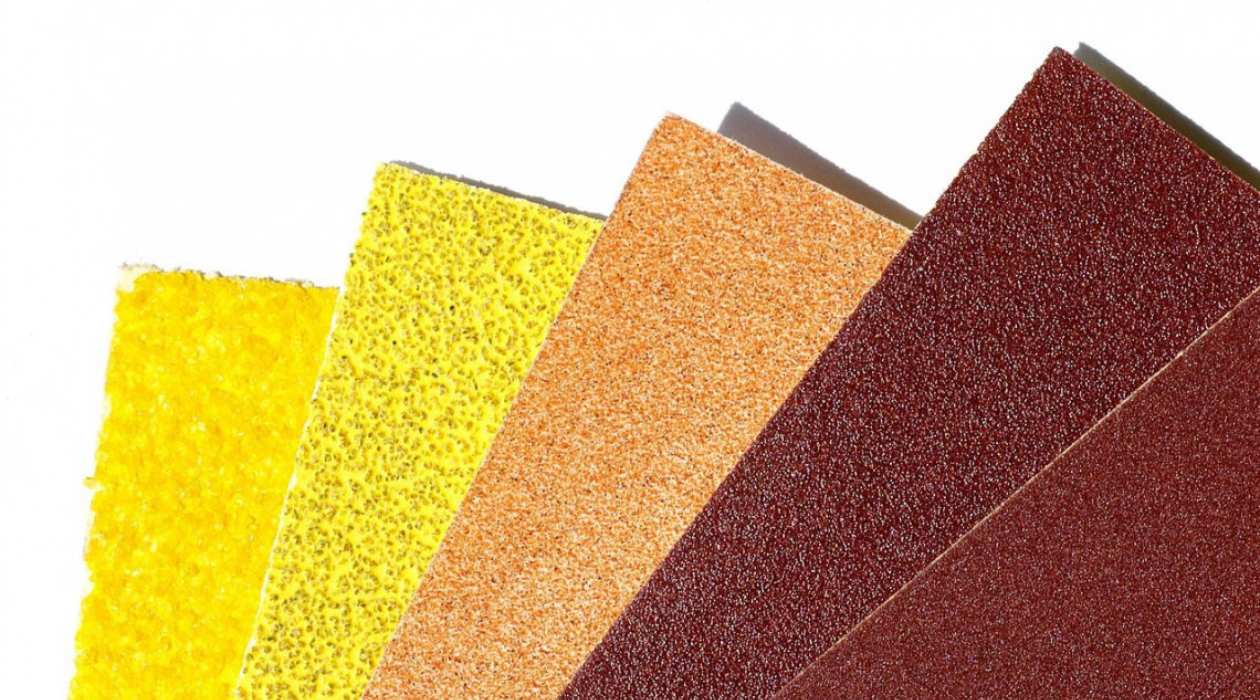
Tools & Equipment
What Mineral Is Used For Most Sandpaper
Modified: January 9, 2024
Discover the essential mineral used in most sandpaper for tools and equipment. Find out how this mineral enhances the abrasive properties of sandpaper.
(Many of the links in this article redirect to a specific reviewed product. Your purchase of these products through affiliate links helps to generate commission for Storables.com, at no extra cost. Learn more)
Introduction
Welcome to the fascinating world of sandpaper and the minerals that make it effective. Sandpaper is a staple tool in every handyman’s arsenal. Whether you are preparing a wooden surface for painting, refinishing furniture, or smoothing out uneven edges, sandpaper is essential for achieving a professional finish.
But have you ever wondered what exactly makes sandpaper so effective? It all boils down to the abrasive minerals embedded in its surface. These minerals provide the cutting power necessary to remove unwanted material and create a smooth, polished finish.
In this article, we will delve into the world of abrasive minerals used in sandpaper, exploring their characteristics, benefits, and applications. From the widely-used silica sand to the aggressive zirconia alumina, we will unravel the secrets behind these minerals and their role in creating the perfect sanding experience.
So, let’s dive in and discover the mineral wonders that bring our sandpaper to life!
Key Takeaways:
- Sandpaper’s effectiveness is derived from abrasive minerals like silica sand, garnet, aluminum oxide, zirconia alumina, and silicon carbide. Understanding their unique properties is crucial for achieving optimal results in sanding tasks.
- The diverse range of minerals used in sandpaper, including emery, diamond, ceramic abrasives, CBN, cerium oxide, almandine, and tripoli, offer specialized properties for specific sanding applications. Choosing the right mineral and grit size is essential for achieving smooth and professional finishes.
Read more: What Is Sandpaper Used For
History of Sandpaper
Sandpaper, as we know it today, has come a long way since its humble origins. Its history can be traced back to ancient civilizations, where craftsmen used abrasive materials to smooth and shape various surfaces.
One of the earliest records of sandpaper dates back to the 13th century, during the Song Dynasty in China. At that time, sandpaper was made by gluing crushed shells, sand, or glass to parchment or animal skin. It was primarily used for smoothing wooden surfaces and preparing them for painting or lacquering.
The production of sandpaper gained momentum in the 18th century with the invention of the Industrial Revolution and the discovery of new materials. In Europe, sandpaper became a vital tool for craftsmen in industries such as woodworking, metalworking, and automotive manufacturing.
During the 19th century, advancements in manufacturing techniques led to the production of sandpaper in larger quantities and with improved quality. The use of better adhesives for bonding abrasive materials to backing materials revolutionized the sandpaper industry. This allowed for more precise and efficient sanding, leading to higher-quality finishes.
In the early 20th century, sandpaper underwent further advancements with the introduction of synthetic materials. Instead of natural abrasives like sand or crushed shells, manufacturers began using minerals such as aluminum oxide, silicon carbide, and garnet for improved performance and consistency.
Today, sandpaper is produced using advanced manufacturing processes that ensure uniformity and quality. Different grit sizes and abrasive materials are available to suit specific applications, making sandpaper an indispensable tool in various industries.
From its humble beginnings in ancient times to its evolution into a modern-day tool, sandpaper has played a crucial role in shaping the world of craftsmanship. It continues to be an essential tool for professionals and DIY enthusiasts alike, enabling the achievement of smooth, polished, and professionally-finished surfaces.
Understanding Abrasive Minerals
Abrasive minerals are the key components that give sandpaper its cutting power. These minerals are selected for their hardness, durability, and ability to remove material effectively. Understanding these minerals is essential to choose the right sandpaper for your specific sanding needs.
There are several factors to consider when evaluating abrasive minerals:
- Hardness: The hardness of an abrasive mineral determines its effectiveness in removing material. Harder minerals have sharp edges that can cut through surfaces more efficiently.
- Durability: Durability refers to the ability of an abrasive mineral to withstand the sanding process without breaking down or losing its cutting power.
- Aggressiveness: Some minerals are more aggressive than others. Aggressiveness refers to the speed at which the mineral removes material. A more aggressive mineral may remove material faster but may also cause more significant scratches.
- Friability: Friability refers to the ability of an abrasive mineral to break down during use. Some minerals are designed to fracture as they wear, revealing fresh cutting edges and prolonging the life of the sandpaper.
By understanding these properties, you can choose the appropriate abrasive mineral for your specific sanding task, ensuring optimal results.
Furthermore, different minerals excel in different applications. Some minerals are ideal for rough sanding and material removal, while others are more suited for fine finishing and polishing. Learning about the different minerals used in sandpaper will help you make an informed decision when selecting the right sandpaper for your project.
In the next sections, we will explore some of the most commonly used abrasive minerals in sandpaper, including their characteristics, benefits, and applications. From versatile silica sand to aggressive zirconia alumina and fine-grained silicon carbide, these minerals play a vital role in achieving smooth and professional finishes on a variety of surfaces.
Common Minerals Used in Sandpaper
When it comes to sandpaper, various minerals are used as abrasives to provide the cutting power required for effective sanding. Let’s take a closer look at some of the most common minerals used in sandpaper:
- Silica Sand: Silica sand is one of the most widely used minerals in sandpaper. It is composed of silicon dioxide and has a crystalline structure. Silica sand is known for its hardness and ability to slice through material, making it ideal for heavy-duty sanding tasks. It is commonly used in woodworking, metalworking, and drywall applications.
- Garnet: Garnet is a mineral known for its natural beauty. It is widely used as an abrasive due to its excellent cutting properties. Garnet sandpaper is highly versatile and can be used on a variety of surfaces, including wood, metal, and fiberglass. It is known for its durability and ability to produce a smooth finish without leaving excessive scratches.
- Aluminum Oxide: Aluminum oxide is a versatile abrasive mineral used in sandpaper. It is known for its hardness, durability, and exceptional cutting power. Aluminum oxide sandpaper is commonly used in both hand sanding and machine sanding applications. It is suitable for a wide range of materials, including wood, metal, and plastic.
- Zirconia Alumina: Zirconia alumina is a tough and aggressive mineral used in sandpaper. It is derived from a mixture of zirconium oxide and aluminum oxide. Zirconia alumina sandpaper is known for its exceptional durability and performance in heavy stock removal applications. It is commonly used for grinding and shaping metal and can withstand high heat and pressure.
- Silicon Carbide: Silicon carbide is a popular mineral used in sandpaper, particularly for fine finishing applications. It is known for its hardness and ability to provide a smooth, consistent finish. Silicon carbide sandpaper is commonly used in automotive refinishing, woodworking, and stone polishing. It is also suitable for sanding non-ferrous metals.
These are just a few examples of the minerals used in sandpaper. Each mineral offers unique characteristics that make it suitable for specific sanding tasks. By understanding the properties of these minerals, you can choose the right sandpaper for your project, ensuring excellent results and a professional finish.
Characteristics and Uses of Silica Sand
Silica sand is one of the most commonly used minerals in sandpaper. It is composed of silicon dioxide and has unique characteristics that make it a versatile abrasive for various sanding applications.
Here are some of the characteristics of silica sand:
- Hardness: Silica sand is known for its exceptional hardness. Its crystalline structure allows it to slice through material effectively, making it ideal for heavy-duty sanding tasks.
- Durability: Silica sand is highly durable, which means it can withstand the sanding process without breaking down quickly. This durability ensures long-lasting sandpaper performance.
- Cutting Power: Due to its hardness, silica sand offers excellent cutting power. It can remove material efficiently, making it suitable for coarse sanding and material removal.
Now, let’s dive into the various uses of silica sand in sandpaper:
- Woodworking: Silica sandpaper is commonly used in woodworking for preparing wooden surfaces for painting, staining, or varnishing. It is effective in removing old finishes, smoothing out rough surfaces, and shaping wood.
- Metalworking: Silica sandpaper is also used in metalworking applications. It can remove rust, paint, and corrosion from metal surfaces. It is often used for rough sanding and preparing metal surfaces for painting or welding.
- Drywall Sanding: Silica sandpaper is suitable for sanding drywall before painting or applying texture. It can smooth out joint compound and provide a uniform surface for paint or texture application.
- DIY Projects: Silica sandpaper is widely used in various DIY projects, such as refinishing furniture, restoring antique pieces, and preparing surfaces for crafts and home improvement projects.
When using silica sandpaper, it is important to take proper safety precautions. Silica can become airborne during sanding, posing a risk to your health. It is recommended to work in well-ventilated areas, wear protective masks and goggles, and follow proper dust control measures.
Overall, silica sand is an essential mineral in the world of sandpaper. Its hardness, durability, and cutting power make it suitable for a wide range of sanding applications. Whether you’re working on wood, metal, or drywall, silica sandpaper can help you achieve a smooth, professional finish.
Read more: What Is Mineral Glass
Benefits and Applications of Garnet Sand
Garnet sand is a versatile abrasive mineral known for its natural beauty and exceptional cutting properties. It offers a range of benefits and finds applications in various sanding tasks. Let’s explore some of the advantages and uses of garnet sand:
Benefits of Garnet Sand:
- Effective Cutting Power: Garnet sand is known for its excellent cutting capabilities. Its sharp edges allow it to quickly and efficiently remove material without causing excessive damage or scratching.
- Durability: Garnet sand is highly durable and can withstand rigorous sanding processes without breaking down. This durability ensures that the sandpaper remains effective for extended periods, reducing the need for frequent replacements.
- Low Dust Generation: Garnet sand produces minimal dust during sanding, making it a cleaner option compared to some other abrasive minerals. This characteristic is particularly beneficial for health and safety reasons, as it minimizes the risk of inhaling fine particles.
- Smooth Finish: Garnet sand is known for leaving a smooth finish after sanding. It is capable of removing imperfections and creating a polished surface, making it a preferred choice for applications that require a high-quality finish.
- Versatility: Garnet sand can be used on a variety of surfaces, including wood, metal, and fiberglass. Its versatility makes it suitable for various industries and applications.
Applications of Garnet Sand:
- Woodworking: Garnet sandpaper is commonly used in woodworking for sanding wooden surfaces, including furniture, cabinets, and flooring. It is effective in removing old finishes, smoothing out rough patches, and preparing the wood for a flawless finish.
- Metalworking: Garnet sandpaper is also widely used in metalworking applications. It can remove rust, scale, and paint from metal surfaces, allowing for proper preparation before painting, welding, or further processing.
- Fiberglass and Composites: Garnet sand is often used in sanding fiberglass and composite materials. It effectively smooths out the surfaces and achieves a polished finish, ensuring proper adhesion of coatings and finishes.
- DIY Projects: Garnet sandpaper is a popular choice for DIY enthusiasts working on various projects, such as refinishing furniture, restoring antiques, or sanding surfaces for crafts and home improvement.
It’s important to note that garnet sandpaper comes in different grit sizes to accommodate different sanding needs. Coarser grits are suitable for heavy material removal, while finer grits are ideal for achieving a smooth and polished finish.
With its exceptional cutting power, durability, and versatility, garnet sand remains a top choice for many craftsmen, professionals, and DIY enthusiasts. Whether you’re working on wood, metal, or fiberglass, garnet sandpaper can help you achieve outstanding sanding results.
Silicon carbide is the most commonly used mineral for sandpaper due to its hardness and ability to cut through a variety of materials.
Aluminum Oxide: A Versatile Mineral for Sanding
Aluminum oxide is a widely used mineral in the world of sandpaper. With its exceptional hardness, durability, and cutting power, it is known for its versatility and effectiveness in various sanding applications. Let’s explore the characteristics, benefits, and applications of aluminum oxide:
Characteristics of Aluminum Oxide:
- Hardness: Aluminum oxide is a very hard mineral, ranking just below diamond on the Mohs hardness scale. This hardness allows it to effectively cut through a wide range of materials, including wood, metal, and plastic.
- Durability: One of the key advantages of aluminum oxide is its durability. It can withstand the rigors of sanding without breaking down or losing its cutting power, making it a long-lasting abrasive option.
- Cutting Power: Aluminum oxide offers exceptional cutting power, allowing for efficient material removal during the sanding process. This makes it ideal for both coarse sanding and fine finishing applications.
Benefits of Aluminum Oxide:
- Wide Range of Grits: Aluminum oxide sandpaper is available in various grit sizes, ranging from coarse to very fine. This allows for versatile use in different stages of the sanding process, from heavy material removal to fine polishing.
- Smooth and Consistent Finish: Aluminum oxide sandpaper leaves a smooth and uniform finish after sanding. It is capable of removing imperfections, scratches, and surface irregularities, resulting in a professional-looking surface.
- Effective on Multiple Surfaces: Aluminum oxide is suitable for sanding a variety of materials, including wood, metal, plastic, and even some composites. Its versatility makes it a go-to choice for professionals and DIY enthusiasts across different industries.
- Efficiency and Speed: Aluminum oxide sandpaper allows for efficient and speedy sanding due to its cutting power and durability. It helps to save time and effort without compromising the quality of the finished product.
Applications of Aluminum Oxide:
- Woodworking: Aluminum oxide sandpaper finds extensive use in woodworking projects. It is suitable for tasks such as preparing wood surfaces for painting, smoothing out rough spots, and removing old finishes or paint.
- Metalworking: Aluminum oxide is also commonly used in metalworking applications. It can effectively remove rust, scale, and paint from metal surfaces, allowing for proper surface preparation before further processing or finishing.
- Plastic and Composite Materials: Aluminum oxide sandpaper is suitable for sanding plastic and composite materials. It helps to smooth out surfaces and achieve the desired finish, ensuring proper adhesion of coatings and finishes.
- Automotive Refinishing: Aluminum oxide sandpaper is widely used in automotive refinishing for tasks like sanding body panels, removing paint or clear coat, and achieving a smooth surface before painting or polishing.
Aluminum oxide sandpaper is available in various forms, including sheets, rolls, discs, and belts, to accommodate different sanding tools and preferences. Whether you’re working on wood, metal, plastic, or automotive surfaces, aluminum oxide is a dependable choice for achieving excellent sanding results.
Zirconia Alumina: The Tough and Aggressive Option
Zirconia alumina is a mineral widely used in sandpaper, known for its toughness, aggressiveness, and ability to withstand demanding sanding applications. Let’s delve into the characteristics, benefits, and applications of zirconia alumina:
Characteristics of Zirconia Alumina:
- High Hardness and Toughness: Zirconia alumina is a mineral with exceptional hardness and toughness. It resists wear and can withstand high pressure and heat, making it suitable for heavy stock removal and rough sanding tasks.
- Self-Sharpening Properties: Zirconia alumina has self-sharpening capabilities. As the surface wears down, new sharp cutting edges are exposed, ensuring consistent cutting performance over the life of the sandpaper.
- Abrasive Aggressiveness: Zirconia alumina is known for its aggressive cutting action. It quickly removes material and can handle challenging surfaces, such as hardened steel, stainless steel, and cast iron.
- Heat Resistance: Zirconia alumina is highly resistant to heat, making it an excellent choice for high-speed sanding applications. It can withstand the friction generated during intense sanding without losing its cutting power.
Benefits of Zirconia Alumina:
- Extreme Durability: Zirconia alumina sandpaper is incredibly durable, making it ideal for tough sanding tasks that require long-lasting abrasives. It offers extended life and minimizes the need for frequent replacement.
- Fast and Efficient Material Removal: Due to its aggressive cutting properties, zirconia alumina sandpaper allows for fast and efficient material removal, helping to save time and effort in sanding applications.
- Consistent Performance: The self-sharpening nature of zirconia alumina ensures consistent cutting performance throughout the sanding process. It maintains its aggressiveness and cutting power, resulting in even and uniform sanding results.
- Versatile Application: Zirconia alumina is suitable for a wide range of applications, including grinding, blending, deburring, and weld removal. It is commonly used in metal fabrication, automotive, and manufacturing industries.
Applications of Zirconia Alumina:
- Metalworking: Zirconia alumina sandpaper excels in metalworking applications. It is ideal for sanding and shaping various metals, including stainless steel, cast iron, and hardened steel. It effectively removes welds, rust, and paint, leaving a smooth and clean surface.
- Woodworking: While zirconia alumina is primarily used in metalworking, it can also be used for heavy stock removal in woodworking projects. It is useful for sanding hardwoods, removing old varnish, or shaping wood surfaces.
- Automotive and Marine Refinishing: Zirconia alumina sandpaper is commonly employed in automotive and marine refinishing for the removal of paint, primer, and body filler. It can handle tough surfaces and deliver superior material removal rates.
- Industrial and Manufacturing Applications: Zirconia alumina is widely used in various industrial and manufacturing settings. It is effective for sanding, grinding, and shaping metal components, ensuring smooth and precise finishes.
When using zirconia alumina sandpaper, it is essential to choose the appropriate grit size for your specific application. Coarser grits are suitable for heavy material removal, while finer grits are ideal for achieving a smoother finish. Additionally, proper safety precautions, such as wearing protective gear, should be followed when working with zirconia alumina due to its aggressive nature.
Zirconia alumina sandpaper provides the strength, durability, and cutting power needed for challenging sanding tasks. With its aggressive performance and exceptional versatility, it is a reliable choice for professionals seeking optimal results in demanding sanding applications.
Silicon Carbide: Ideal for Fine Finishing
Silicon carbide is a popular mineral used in sandpaper, particularly for fine finishing applications. It offers unique characteristics that make it an excellent choice for achieving smooth and precise finishes. Let’s explore the benefits, characteristics, and applications of silicon carbide:
Characteristics of Silicon Carbide:
- Hardness: Silicon carbide is a very hard mineral, second only to diamond on the Mohs hardness scale. Its hardness allows it to cut through even the toughest materials, making it effective for fine finishing applications.
- Fineness: Silicon carbide has a fine crystalline structure, resulting in a consistent and uniform cutting action. It produces a smooth and even finish, eliminating scratch marks and imperfections.
- Heat Resistance: Silicon carbide is highly heat resistant, allowing for high-speed sanding without damaging the sandpaper. It can withstand the friction generated during fine finishing, ensuring the longevity of the abrasive material.
- Wear Resistance: Silicon carbide exhibits excellent wear resistance, making it durable and long-lasting. This allows for extended use without significant degradation of the sandpaper, reducing the need for frequent replacement.
Benefits of Silicon Carbide:
- Fine Finishing Capability: Silicon carbide is renowned for its ability to achieve an exceptionally smooth and refined finish. It is ideal for applications that require precision and a flawless surface, such as woodworking veneers, automotive paint preparation, or polishing of stone and glass.
- Consistent Performance: Silicon carbide sandpaper delivers consistent and predictable results. Its fine structure ensures even cutting action and allows for precise control over the sanding process, resulting in uniform finishes every time.
- Use on Various Materials: Silicon carbide is versatile and can be used on a wide range of materials, including wood, metal, plastics, and composites. It handles different surfaces with efficiency and finesse, allowing for comprehensive sanding application.
- Excellent Surface Quality: Silicon carbide’s fine grit allows for exceptional surface smoothness and reduction of visible scratches. It is often the preferred choice for achieving a high-quality finish on delicate materials like glass or metal sculptures.
Applications of Silicon Carbide:
- Woodworking: Silicon carbide sandpaper is commonly used in woodworking for fine finishing tasks. It is suitable for sanding between coats of paint or varnish, smoothing out edges, and achieving a polished surface on wooden projects.
- Automotive and Aerospace Industries: Silicon carbide is utilized in automotive and aerospace industries for automotive paint refinishing, aerospace part preparation, and aircraft component finishing. It ensures precise and flawless finishes on various surfaces.
- Glass and Stone Polishing: Silicon carbide sandpaper is perfect for polishing glass, ceramics, and natural stone surfaces. It effectively removes imperfections, blemishes, or scratches, creating a mirror-like, smooth finish.
- Electronic Components: Silicon carbide’s non-metallic properties make it suitable for sanding electronic components during manufacturing or repair. Its delicacy ensures gentle handling of sensitive parts and avoids damage.
When working with silicon carbide sandpaper, it’s important to choose the appropriate grit size for the desired finish. Coarser grits are ideal for initial sanding and material removal, while finer grits are best for achieving a polished and refined surface.
Silicon carbide offers unparalleled performance when it comes to fine finishing. With its hardness, fineness, and exceptional heat resistance, it ensures superior results on a variety of materials. Whether it’s woodworking, automotive applications, or polishing delicate surfaces, silicon carbide is the go-to choice for achieving smooth and flawless finishes.
Read more: What Is Sandpaper Used For In Art
Other Minerals Used in Sandpaper
While minerals like silica sand, garnet, aluminum oxide, zirconia alumina, and silicon carbide are among the most commonly used in sandpaper, there are several other minerals that also play a role in the world of abrasives. These minerals offer unique properties and benefits that make them suitable for specific sanding applications. Let’s explore some of these other minerals:
Emery: Emery is a natural mineral composed of a mixture of corundum and magnetite or hematite. It is known for its hardness and durability. Emery sandpaper is commonly used in metalworking for tasks like polishing and removing rust from metal surfaces.
Diamond: Diamond is the hardest mineral known, and its hardness is unmatched. While not commonly used in traditional sandpaper, diamond abrasives are utilized in diamond-coated discs and pads for the most demanding sanding and grinding applications on hard materials like stone, ceramics, and glass.
Ceramic Abrasives: Ceramic abrasives are made from a mixture of minerals, including alumina and zirconia. They are known for their high heat resistance, toughness, and ability to provide aggressive cutting power. Ceramic abrasives excel in heavy grinding and stock removal applications.
Cubic Boron Nitride (CBN): CBN is a synthetic mineral made from boron and nitrogen. It is second in hardness only to diamond. CBN abrasives are used for grinding and shaping high-speed steels, superalloys, and hardened materials. They are commonly found in specialized grinding wheels and belts.
Cerium Oxide: Cerium oxide is a rare-earth mineral renowned for its polishing capabilities. It is often used for fine polishing and restoration of glass, lenses, and optical components. Cerium oxide is available in powder form and is typically mixed with water to create a polishing slurry.
Almandine: Almandine is a type of garnet mineral commonly used in waterjet cutting. It is selected for its hardness and ability to withstand high-pressure water jets when used as an abrasive in waterjet cutting machines.
Tripoli: Tripoli, also known as rottenstone, is a porous, fine-grained rock composed of the mineral siliceous earth. It is used as a polishing agent for wood furniture and can produce a smooth, lustrous finish.
These are just a few examples of the other minerals used in sandpaper and abrasive applications. Each mineral offers unique characteristics that make it suitable for specific sanding tasks and materials.
When choosing sandpaper for your project, consider the material you’re working with and the desired finish. The right mineral choice, in combination with the appropriate grit size, will ensure optimal results and help you achieve the desired surface quality.
While silica sand, garnet, aluminum oxide, zirconia alumina, and silicon carbide are commonly encountered in sandpaper, don’t overlook the diverse range of other minerals used in abrasives. Their specialized properties and applications make them valuable assets in achieving superior sanding results.
Conclusion
Sandpaper is an essential tool for achieving smooth, polished surfaces in a wide range of applications. The cutting power of sandpaper is derived from the abrasive minerals embedded in its surface. Understanding these minerals and their characteristics is crucial for selecting the right sandpaper for each sanding task.
Throughout history, sandpaper has evolved from crude materials like crushed shells to the advanced abrasive minerals we use today. Silica sand, with its hardness and cutting power, remains a staple in sandpaper for heavy-duty applications. Garnet offers exceptional cutting properties and versatility, while aluminum oxide provides durability and versatility for various materials. Zirconia alumina, with its toughness and aggressiveness, tackles demanding sanding tasks. Silicon carbide excels in fine finishing, producing smooth and refined finishes on a variety of materials.
In addition to these commonly used minerals, other minerals like emery, diamond, ceramic abrasives, cubic boron nitride (CBN), cerium oxide, almandine, and tripoli also play a role in specialized sanding applications and polishing tasks.
Choosing the right mineral and grit size for your sandpaper needs is essential to achieving optimal results. Coarser grits are suitable for material removal, while finer grits are ideal for fine finishing and polishing.
Whether you’re a professional craftsman or a DIY enthusiast, understanding the minerals used in sandpaper empowers you to select the appropriate abrasive material for your specific projects. By leveraging the cutting power and unique properties of these minerals, you can achieve smooth and professional finishes on wood, metal, plastic, glass, and various other surfaces.
So, the next time you reach for sandpaper, remember the mineral wonders that lie within. They are the secret behind the effectiveness and versatility of this essential tool. Choose the right mineral, harness its cutting power, and embark on your sanding journey with confidence!
Frequently Asked Questions about What Mineral Is Used For Most Sandpaper
Was this page helpful?
At Storables.com, we guarantee accurate and reliable information. Our content, validated by Expert Board Contributors, is crafted following stringent Editorial Policies. We're committed to providing you with well-researched, expert-backed insights for all your informational needs.
0 thoughts on “What Mineral Is Used For Most Sandpaper”