Home>Articles>What Is The Purpose Of The Commutator In An Electric Motor
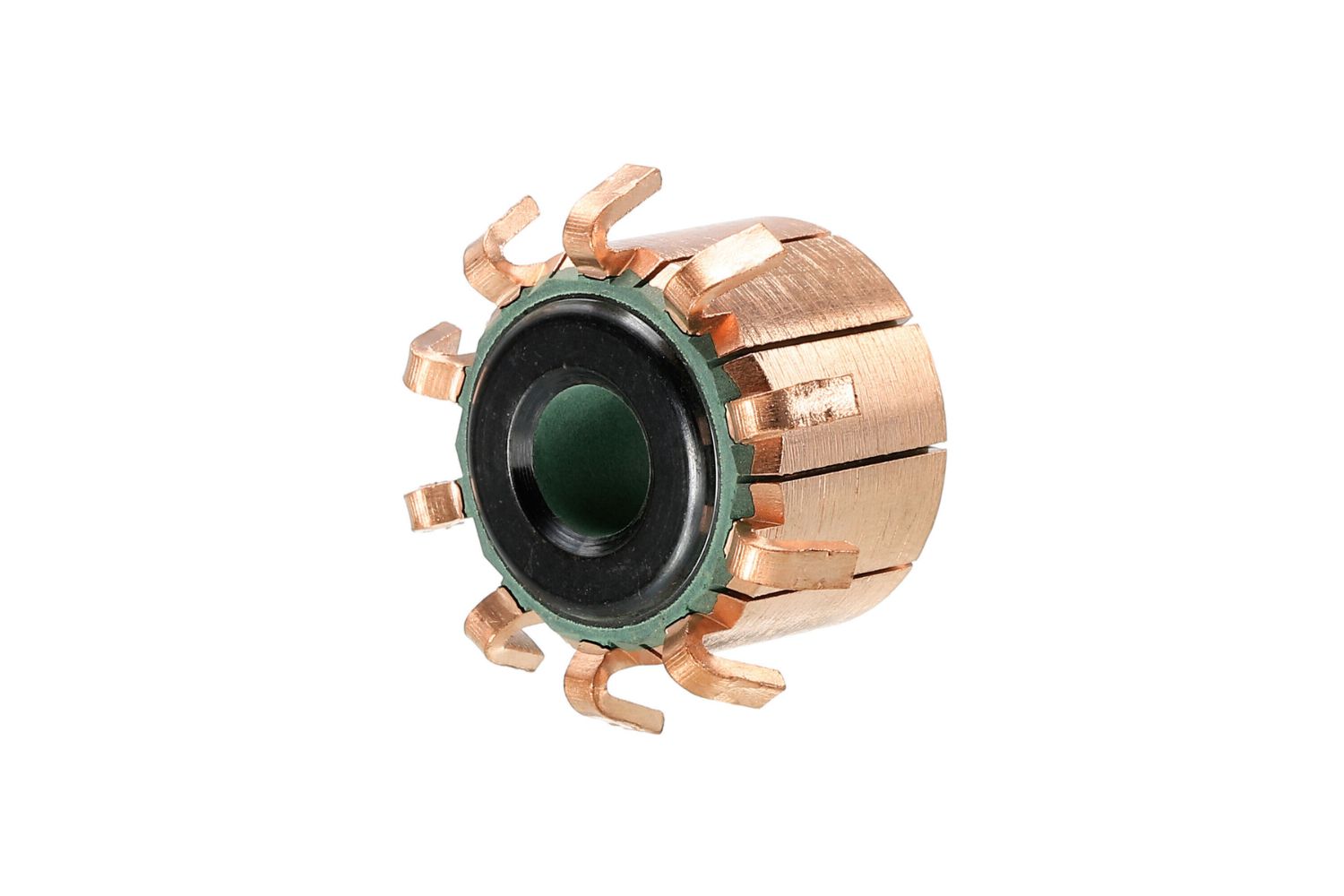
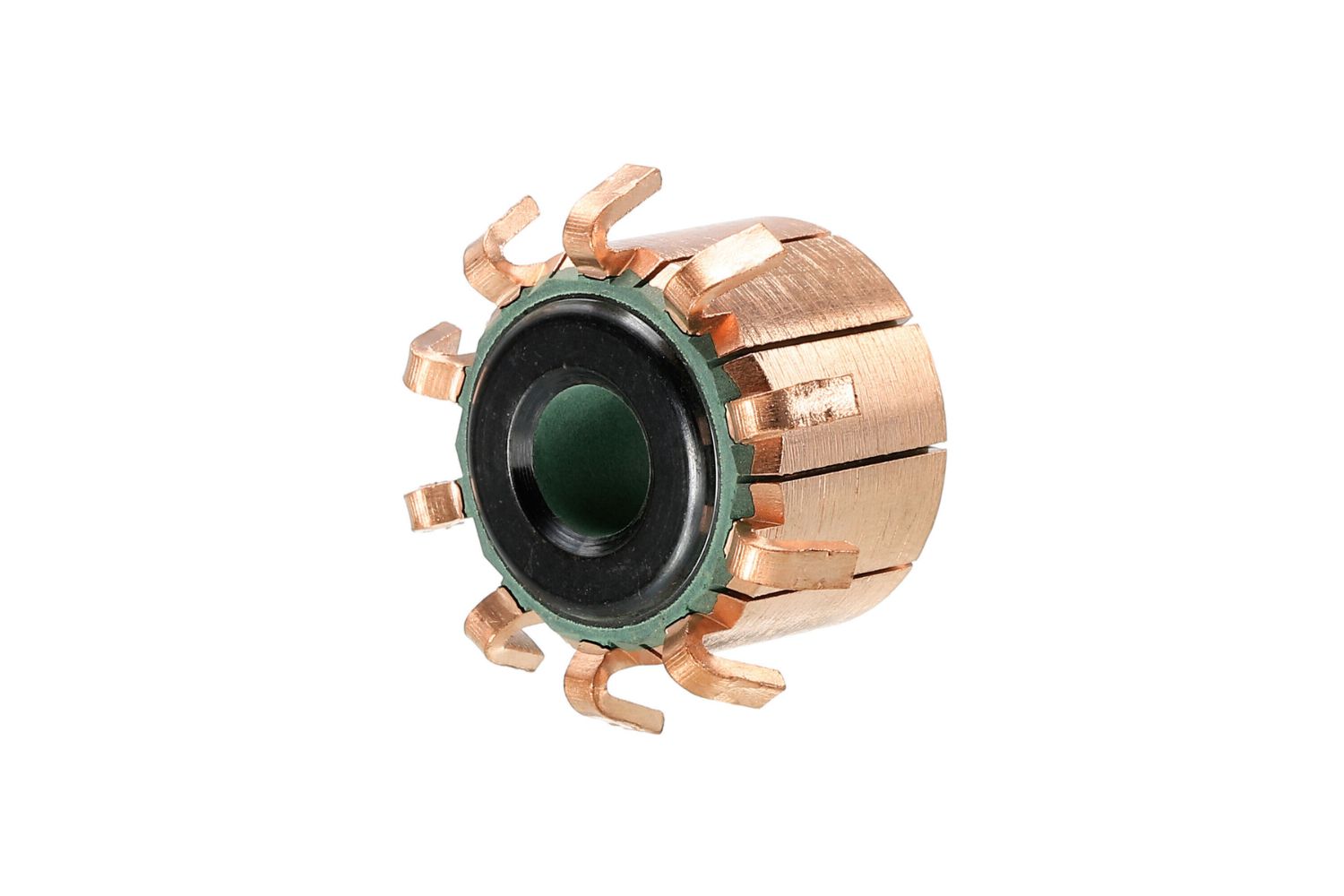
Articles
What Is The Purpose Of The Commutator In An Electric Motor
Modified: January 8, 2024
Learn the purpose of the commutator in an electric motor in this informative article. Discover how it helps to provide a continuous and efficient flow of electrical current.
(Many of the links in this article redirect to a specific reviewed product. Your purchase of these products through affiliate links helps to generate commission for Storables.com, at no extra cost. Learn more)
Introduction
Electric motors are an essential component of numerous devices and machinery, powering everything from household appliances to industrial equipment. Within these motors, a commutator plays a crucial role in converting electrical energy into mechanical motion.
In this article, we will explore the purpose and function of the commutator in an electric motor. We will delve into its components, how it works, and why it is vital for the motor’s operation. Moreover, we will discuss common issues that may arise with the commutator and the best practices for its maintenance.
By understanding the significance of the commutator, we can gain insight into the workings of electric motors and appreciate their importance in our daily lives.
Key Takeaways:
- The commutator is a crucial component in DC electric motors, ensuring unidirectional current flow and smooth rotation. Regular maintenance and care are essential for optimal performance and longevity.
- Understanding the function and importance of the commutator empowers us to appreciate the intricate mechanics behind electric motors and their impact on our daily lives.
Definition of a Commutator
A commutator is a vital part of a direct current (DC) electric motor. It is a cylindrical device typically made of copper segments, known as commutator bars, that are insulated from one another. The commutator is mounted on the motor’s rotor shaft and is in electrical contact with the armature winding.
The commutator serves as an electrical switch or a mechanical rectifier that allows the current to flow in a specific direction through the armature winding. It facilitates the conversion of alternating current (AC) to direct current (DC) within the motor, resulting in the continuous rotation of the rotor.
Commutators are commonly found in DC motors, such as those used in household appliances, automobile starters, and various industrial applications that require precise control over motor speed and torque.
It is important to note that commutators are not present in alternating current (AC) motors, as the periodic reversal of current direction in AC motors obviates the need for a commutator.
Components of an Electric Motor
An electric motor is a complex device composed of several key components that work together to convert electrical energy into mechanical motion. Understanding these components is crucial to comprehend the role of a commutator in the motor’s functioning. Let’s take a closer look at each component:
- Stator: The stator is the stationary part of the motor that houses the core and windings. It consists of laminated iron cores and copper coils, which generate a magnetic field when electric current flows through them.
- Rotor: The rotor is the moving part of the motor. It contains a shaft and a series of conductive bars, known as the armature winding, that spin inside the stator’s magnetic field. The rotor is responsible for generating the mechanical motion of the motor.
- Commutator: As discussed earlier, the commutator is a cylindrical device mounted on the rotor shaft. It is made up of insulated copper segments or bars that allow the flow of current in a specific direction through the armature winding.
- Brushes: Brushes are conductive carbon or graphite blocks that make contact with the commutator’s surface. They play a vital role in transferring electrical current from the stationary part of the motor to the rotating commutator.
- Bearings: Bearings are mechanical components that support and facilitate the smooth rotation of the motor’s rotor shaft. They help reduce friction and ensure proper alignment and stability.
These components work in harmony to convert electrical energy into mechanical motion. The stator’s magnetic field interacts with the rotor’s conductive armature winding, generating a rotational force that powers various applications and devices.
Function of a Commutator
The primary function of a commutator in an electric motor is to ensure the unidirectional flow of current in the armature winding. It achieves this by periodically reversing the direction of current in the winding as the rotor spins within the stator’s magnetic field. Let’s delve deeper into the specific functions of a commutator:
- Current Switching: The commutator acts as an electrical switch, allowing the current to flow in the armature winding in a controlled manner. As the rotor rotates, different segments of the commutator come into contact with the brushes, which connect to different sections of the armature winding. This switching process ensures that the current flows in the same direction throughout the rotation, resulting in a continuous torque production.
- Conversion of AC to DC: In a DC electric motor, the commutator plays a crucial role in converting the alternating current (AC) provided by the power source into direct current (DC) within the armature winding. As the commutator switches the direction of current flow, it rectifies the AC current, ensuring that it flows in a single direction in the armature winding. This conversion is essential for the motor to produce a consistent and controlled rotational motion.
- Maintenance of Magnetic Field: The commutator also plays a role in maintaining the magnetic field required for the motor’s operation. The current flowing through the armature winding interacts with the stator’s magnetic field, creating a rotational force. The commutator ensures that the armature winding receives a continuous and unidirectional current flow, which keeps the magnetic field stable and enables the motor to generate consistent torque.
- Minimizing Electrical Losses: By efficiently switching the current direction, the commutator helps minimize electrical losses within the motor. It ensures that the armature winding is always supplied with the appropriate current, reducing wastage and enhancing the motor’s efficiency and overall performance.
In essence, the commutator serves as a crucial component in an electric motor, enabling the conversion of electrical energy into mechanical motion through the controlled flow of current in the armature winding.
How a Commutator Works
The functioning of a commutator in an electric motor relies on the principles of current switching and rectification. To understand how a commutator works, let’s explore the step-by-step process:
- Initial Position: When the motor is at rest, the rotor and commutator are stationary. The brushes make contact with specific segments of the commutator, connecting them to different sections of the armature winding.
- Power Supply: Once the motor is turned on, an external power supply energizes the armature winding. The current flows through the brushes onto the commutator, initiating the motor’s operation.
- Rotor Rotation: As the electric current flows through the energized armature winding, a magnetic field is generated. Due to the interaction between this field and the stator’s magnetic field, a torque is produced, causing the rotor to start rotating.
- Current Switching: As the rotor spins, different commutator segments come into contact with the brushes. The commutator bar that was previously connected to the positive end of the power supply is now connected to the negative end, and vice versa. This switching of the commutator bars ensures that the current flowing through the armature winding maintains a constant direction.
- Conversion of AC to DC: By switching the current direction at precisely timed intervals, the commutator rectifies the alternating current (AC) provided by the power source, converting it into direct current (DC) within the armature winding. This conversion allows for a consistent flow of current in a single direction, enabling the motor to produce steady mechanical rotation.
- Continuous Rotation: The repeated switching of the commutator segments and the conversion of AC to DC ensure that the armature winding receives a continuous and unidirectional current flow. This sustained flow of current maintains the magnetic field, generating a steady rotational force that keeps the motor spinning.
Through its precise switching and rectification actions, the commutator enables an electric motor to convert electrical energy into mechanical motion. It ensures the controlled flow and direction of current, resulting in the smooth and continuous rotation of the motor’s rotor.
The purpose of the commutator in an electric motor is to reverse the direction of the current in the rotor windings, ensuring continuous rotation. This allows the motor to maintain a consistent direction of rotation.
Importance of a Commutator in an Electric Motor
The commutator plays a crucial role in the operation and performance of an electric motor. Its importance lies in several key aspects that contribute to the motor’s functionality and efficiency. Let’s explore the significance of a commutator in an electric motor:
- Direction of Current: The commutator ensures the unidirectional flow of current in the armature winding of a DC motor. By periodically reversing the direction of current as the rotor rotates, the commutator enables the production of continuous torque, resulting in smooth and consistent mechanical motion.
- Conversion of AC to DC: In a DC motor, the commutator plays a vital role in converting the alternating current (AC) provided by the power source into direct current (DC) within the armature winding. This rectification process is essential for maintaining a constant direction of current and enabling the motor to function effectively.
- Precise Control: The commutator allows precise control over the motor’s speed and torque. By regulating the timing and duration of the current switching, the motor’s performance can be optimized for different applications. This level of control is especially important in devices where accurate speed control and torque production are critical.
- Efficiency and Power Output: The efficient current switching and rectification provided by the commutator minimize electrical losses within the motor. By ensuring a continuous and unidirectional current flow in the armature winding, the commutator maximizes the motor’s efficiency, resulting in improved power output and reduced energy consumption.
- Smooth Operation: The commutator helps maintain a stable magnetic field within the motor. This stability ensures a smooth and consistent operation by reducing vibrations, noise, and erratic movement. It also helps prevent issues such as sparking or arcing, which can cause damage and decrease the motor’s lifespan.
- Reliability and Durability: A properly functioning commutator is crucial for the overall reliability and durability of an electric motor. Regular maintenance and care of the commutator, such as cleaning and lubrication, can prolong its lifespan and prevent issues that may affect the motor’s performance.
Considering these factors, it is evident that a commutator is not only a critical component but also an essential contributor to the smooth, efficient, and reliable operation of an electric motor.
Common Issues with Commutators
While commutators are vital components in electric motors, they can experience certain issues that may affect the motor’s performance. Understanding these common issues can help identify and address problems promptly. Here are some of the most common issues that can arise with commutators:
- Wear and Tear: Over time, the constant friction between the brushes and the commutator can cause wear and tear. This wear can result in the formation of grooves or ridges on the commutator’s surface, affecting the contact between the brushes and the commutator and leading to poor performance or even motor failure.
- Brush Alignment: Improper alignment of the brushes can cause uneven contact with the commutator, resulting in arcing, sparking, or loss of power. It is crucial to ensure that the brushes are properly aligned and make consistent contact across the commutator’s surface.
- Brush Performance: The brushes themselves can wear down or become damaged due to continuous use. This wear can cause reduced conductivity and poor contact with the commutator, leading to issues such as overheating, power loss, or erratic motor performance. Regular inspection and replacement of brushes are necessary to maintain optimal performance.
- Contamination: Dirt, dust, or other contaminants can accumulate on the commutator’s surface over time, hindering proper electrical contact with the brushes. Contamination can lead to increased friction, overheating, and even electrical shorts. Regular cleaning of the commutator is essential to prevent such issues.
- Poor Lubrication: Inadequate lubrication of the commutator can cause increased friction between the brushes and the commutator’s surface. This friction can generate excessive heat, resulting in damage to the commutator and brushes. Correct lubrication is necessary to ensure smooth operation and prevent premature wear.
- Overheating: Excessive current flow or inadequate cooling can cause the commutator to overheat. High temperatures can lead to deformation, melting of insulation, or even the formation of carbon deposits on the commutator’s surface. Overheating not only affects the commutator but also the overall performance and lifespan of the motor.
It is important to address these common issues promptly to prevent further damage and ensure the efficient and reliable operation of the electric motor. Regular maintenance, inspection, and addressing any issues with the commutator can help extend its lifespan and optimize motor performance.
Maintenance and Care of a Commutator
Proper maintenance and care of the commutator are essential for ensuring the reliable operation and longevity of an electric motor. By following these maintenance practices, you can minimize the occurrence of issues and optimize the performance of the commutator:
- Regular Cleaning: Periodically clean the commutator to remove any accumulated dirt, dust, or debris. Use a soft brush or compressed air to gently clean the surface, ensuring not to damage the commutator or dislodge any insulation material.
- Brush Inspection and Replacement: Regularly inspect the brushes for wear, damage, or improper alignment. Replace worn-out or damaged brushes promptly to prevent issues such as poor conductivity, arcing, or excessive friction.
- Lubrication: Apply a suitable lubricant to the commutator to reduce friction between the brushes and the surface. Use a lubricant recommended by the motor manufacturer and follow the guidelines for proper application to prevent excess lubrication or contamination.
- Alignment and Spring Pressure: Ensure that the brushes are properly aligned and make consistent contact with the commutator’s surface. Check the spring pressure of the brushes and adjust if necessary to ensure optimal contact and conductivity.
- Controlled Operating Temperature: Prevent excessive heat buildup by monitoring the motor’s operating temperature. Ensure adequate cooling mechanisms are in place, such as proper ventilation and cooling fans, to help dissipate heat from the commutator and other components.
- Prevent Contamination: Protect the commutator from contamination by keeping the motor and its surroundings clean. Minimize exposure to dust, moisture, and other debris that can negatively impact the commutator’s performance.
- Regular Inspection: Conduct routine inspections of the commutator, brushes, and overall motor performance. Look for signs of wear, damage, or any abnormal behavior that may indicate potential issues. Address any identified problems promptly to prevent further damage or deterioration.
- Consult Manufacturer Guidelines: Always refer to the motor manufacturer’s guidelines and recommendations regarding maintenance and care specific to your motor model. These guidelines provide valuable insights into the best practices for preserving the commutator and optimizing the motor’s performance.
By implementing these maintenance practices and caring for the commutator, you can significantly extend its lifespan and ensure reliable operation of the electric motor. Regular attention and proactive maintenance will help minimize issues and optimize the motor’s efficiency and longevity.
Conclusion
The commutator is a critical component in any DC electric motor, playing a pivotal role in converting electrical energy into mechanical motion. Its function of controlling the direction of current flow through the armature winding ensures the generation of continuous torque and the smooth rotation of the motor’s rotor.
Understanding the importance of the commutator in an electric motor provides insight into the intricate workings of these devices and their significance in various applications. From household appliances to industrial machinery, electric motors power a wide range of essential devices that we rely on daily.
Regular maintenance and care of the commutator, including cleaning, lubrication, and brush inspection, are vital for ensuring its optimal performance and extending its lifespan. By addressing common issues such as wear and tear, improper alignment, and contamination, you can prevent motor failure and maximize efficiency.
Overall, the commutator is a fundamental component that contributes to the reliability, efficiency, and longevity of an electric motor. Its precise switching and rectification processes allow for precise control, smooth operation, and the conversion of alternating current to direct current.
As technology continues to advance, electric motors and their components, including the commutator, will continue to play a crucial role in powering the devices and machinery that drive our modern world. Understanding the purpose and importance of the commutator empowers us to appreciate the intricate mechanics behind electric motors and their impact on our daily lives.
Frequently Asked Questions about What Is The Purpose Of The Commutator In An Electric Motor
Was this page helpful?
At Storables.com, we guarantee accurate and reliable information. Our content, validated by Expert Board Contributors, is crafted following stringent Editorial Policies. We're committed to providing you with well-researched, expert-backed insights for all your informational needs.
0 thoughts on “What Is The Purpose Of The Commutator In An Electric Motor”