Home>diy>Building & Construction>How To Calculate Construction Labor Cost
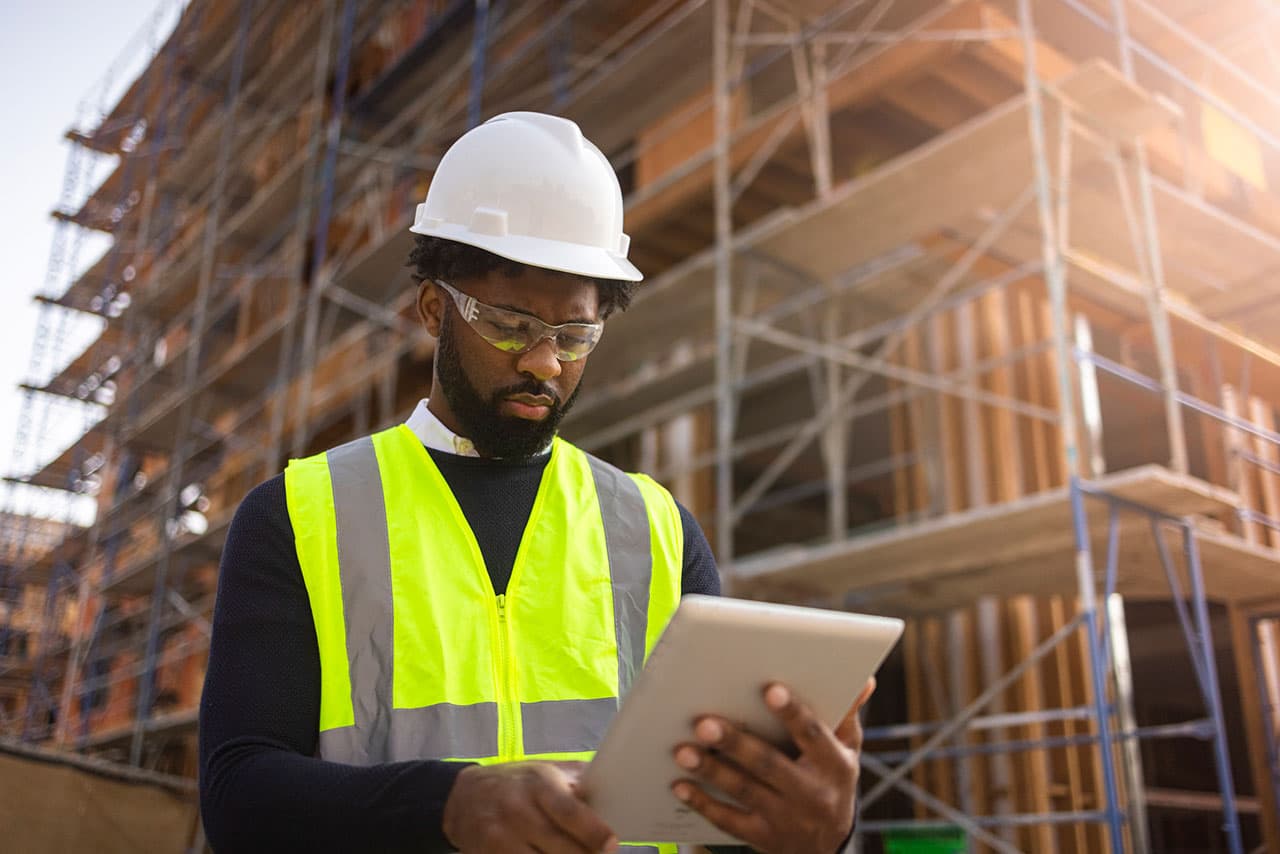
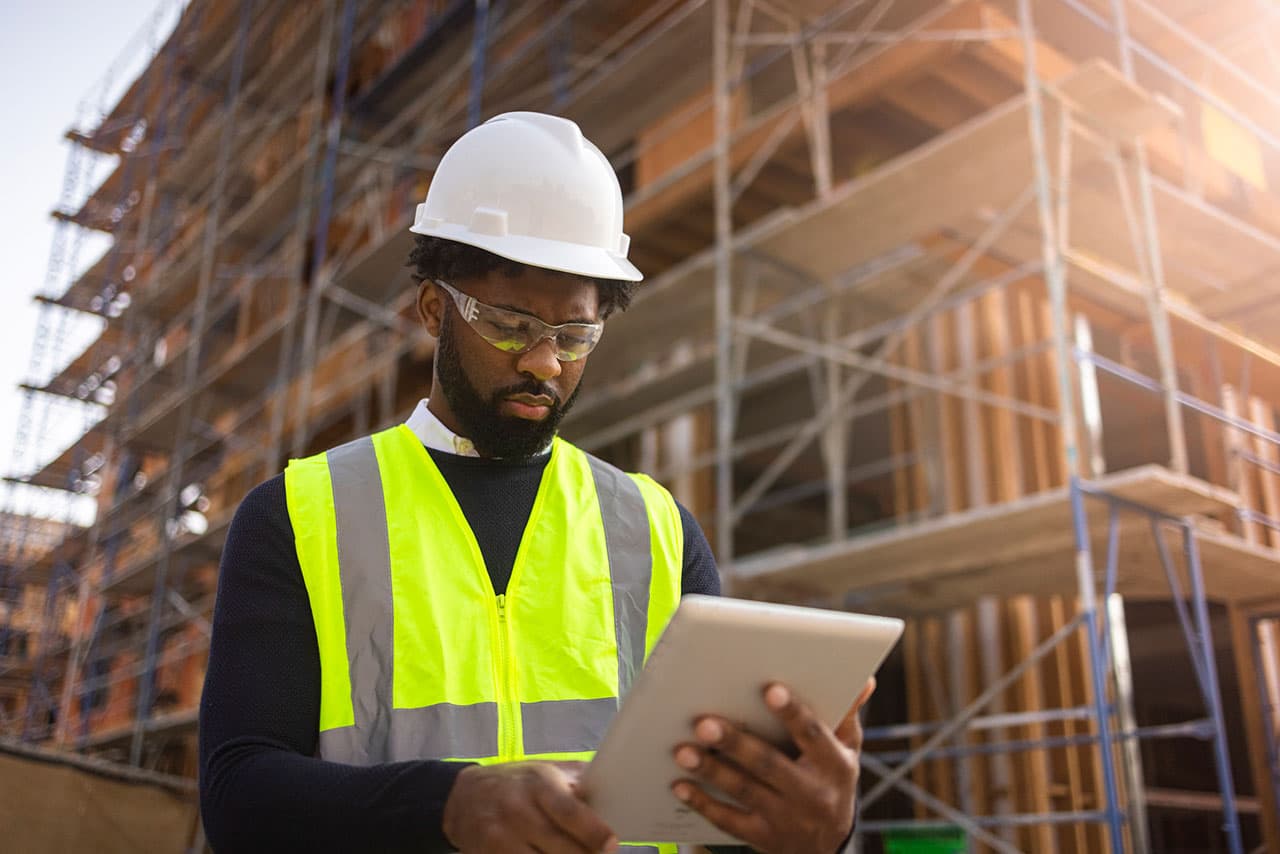
Building & Construction
How To Calculate Construction Labor Cost
Modified: December 7, 2023
Learn how to calculate labor costs for building construction projects. Gain insights into estimating wages, hours, and overall expenses to streamline your construction budgeting.
(Many of the links in this article redirect to a specific reviewed product. Your purchase of these products through affiliate links helps to generate commission for Storables.com, at no extra cost. Learn more)
Introduction
Welcome to the world of construction labor cost estimation! As a building construction expert, understanding how to calculate labor costs is essential to successfully plan and execute any construction project. Labor costs make up a significant portion of the overall project budget, so accurate estimation is crucial for financial planning and project management.
In this article, we will explore the factors that affect construction labor costs, methods to determine labor cost per hour, techniques for estimating labor hours, strategies to bridge the gap between labor cost and project budget, and effective ways to track and manage labor costs. By the end of this article, you will have a comprehensive understanding of how to calculate construction labor costs and optimize your project’s budget.
Construction labor costs can vary greatly based on multiple factors such as project complexity, location, labor market conditions, and skill requirements. It is important to consider these factors when estimating labor costs to ensure accuracy and avoid cost overruns during the construction process.
So let’s dive into the key factors that influence construction labor costs and explore effective ways to calculate and manage these costs in your construction projects.
Key Takeaways:
- Accurate estimation of labor costs and hours is crucial for successful construction project planning and financial management. Consider factors like project complexity, location, and skill requirements to optimize budgeting.
- Implementing effective strategies for managing and tracking labor costs throughout the project ensures better financial control, improved decision-making, and successful project outcomes within the allocated budget.
Factors Affecting Construction Labor Cost
Several factors come into play when determining construction labor costs. These factors not only influence the overall cost but also impact the efficiency and productivity of the labor force. Understanding these factors will help you make more accurate estimates and effectively manage labor costs. Here are the key factors to consider:
- Project Complexity: The complexity and scope of the project have a direct impact on labor costs. Projects that involve intricate designs, specialized construction techniques, or unique architectural features require skilled labor with specialized knowledge, which can increase the labor cost.
- Location: The location of the construction site also plays a significant role in determining labor costs. Areas with higher costs of living, higher wages, or remote locations that require transportation and accommodation expenses may incur higher labor costs.
- Labor Market Conditions: The supply and demand of labor in the local market affect labor costs. During periods of high demand and limited labor supply, such as a construction boom, labor costs tend to increase. Conversely, during economic downturns or in regions with a surplus of available labor, labor costs may be lower.
- Skill Requirements: Different construction projects require varying levels of skill and expertise. Tradespeople with highly specialized skills, such as electricians or plumbers, may command higher wages compared to general laborers. Skilled labor is typically more expensive but can lead to higher quality work.
- Project Duration: The time required to complete a project affects labor costs as well. Longer projects may incur higher labor costs due to factors like increased overhead expenses, extended working hours, and potential overtime costs.
- Working Conditions: The working conditions at the construction site can impact labor productivity and costs. Factors such as extreme weather conditions, hazardous environments, limited access, or confined spaces can slow down work progress, leading to increased labor costs.
By considering these factors and their potential impact on labor costs, you can make more accurate estimations and ensure that your project budget aligns with the reality of construction labor costs.
Determining Labor Cost per Hour
Once you have identified the factors that influence construction labor costs, the next step is to determine the labor cost per hour. This is an important metric that helps in estimating the overall labor cost for the project. Here are some key considerations for determining the labor cost per hour:
- Labor Rate: The labor rate is the base hourly wage paid to the workers. It can vary based on factors such as location, skill level, and labor market conditions. To determine the labor rate, you can research industry standards, consult labor unions, or use historical data from previous projects.
- Benefits and Overhead Costs: In addition to the labor rate, it is crucial to consider benefits and overhead costs associated with labor. These include expenses such as insurance, taxes, workers’ compensation, employee benefits, and equipment usage. Adding these costs to the labor rate provides a more accurate picture of the actual labor cost per hour.
- Overtime and Special Conditions: If your project requires overtime work or involves specialized conditions that warrant additional compensation, you need to factor in the overtime rate or adjust the labor cost per hour accordingly. Be sure to account for any legal regulations or collective bargaining agreements that may affect overtime rates.
- Efficiency and Productivity: Labor efficiency and productivity play a significant role in labor cost determination. Highly skilled and experienced workers can complete tasks more quickly and efficiently, resulting in lower labor costs. On the other hand, inexperienced or inefficient labor may require additional hours to complete the same scope of work, increasing labor costs.
- Labor Segmentation: Some projects may require different types of labor, such as skilled tradespeople, general laborers, or supervisors. Each labor segment may have different labor rates and associated costs. Segmenting labor costs helps in more accurately estimating the overall labor cost per hour.
By taking into account these factors and considerations, you can determine the labor cost per hour for your construction project. This will provide you with a baseline figure to estimate the overall labor cost and facilitate effective project budgeting.
Estimating Labor Hours
Accurately estimating labor hours is crucial for effective project planning and budgeting. Estimating labor hours involves predicting the amount of time it will take for workers to complete specific tasks or project milestones. Here are some key steps to help you estimate labor hours:
- Define Tasks: Clearly define the tasks that need to be completed in the project. Break them down into smaller, manageable components to make estimation more precise. Assign specific tasks to different labor segments based on their skill sets.
- Historical Data: Utilize historical data from previous projects that are similar in nature and scope. Analyze the labor hours required to complete similar tasks in the past to develop a baseline for estimation. Adjust the data based on any differences in project conditions or scope.
- Expertise and Experience: Consider the expertise and experience level of the labor force. Skilled workers with extensive experience are likely to complete tasks more efficiently, requiring fewer labor hours. Inexperienced or less skilled workers may take longer to complete the same tasks.
- Task Complexity: Assess the complexity of each task and how it may impact labor hours. Tasks that require specialized knowledge or intricate techniques may take longer to complete. Factor in any additional time needed for setup, coordination, and quality control.
- Work Breakdown Structure (WBS): Develop a work breakdown structure that breaks down the project into smaller, manageable components. Assign labor hours to each component based on the complexity, skill requirement, and historical data. Summing up the labor hours for all components will provide an estimation of the total labor hours.
- Consider Dependencies: Take into account any dependencies between tasks. Some tasks may need to be completed sequentially, while others can be done in parallel. Adjust the labor hours estimation based on these dependencies to ensure a realistic timeline.
- Consultation: Seek input from subject matter experts, project managers, and experienced team members to validate your labor hours estimation. Their insights and expertise can help identify any potential gaps or areas where labor hours may need to be adjusted.
Remember, labor hour estimation is not an exact science, and unforeseen circumstances or project-specific challenges may impact the actual labor hours required. Regular monitoring and adjustment of the estimation throughout the project will help ensure accuracy and allow for effective project management.
When calculating construction labor costs, consider factors such as the type of work, labor rates, productivity, and overhead expenses. Use historical data and industry benchmarks for accurate estimates.
Bridging the Gap between Labor Cost and Project Budget
Effective budgeting is essential to ensure that labor costs align with the overall project budget. Bridging the gap between labor cost and project budget requires careful planning and proactive management. Here are some strategies to help you bridge this gap:
- Accurate Estimation: As discussed earlier, accurate estimation of labor costs and labor hours is the foundation for effective budgeting. Take into account all relevant factors, such as project complexity, location, labor market conditions, and task dependencies, to ensure realistic estimates.
- Contingency Reserve: Include a contingency reserve in your project budget to account for unforeseen labor cost variations. Set aside a percentage of the budget specifically for potential labor cost overruns or unexpected labor-related expenses. This reserve acts as a safety net and helps bridge any gaps that may arise during the project.
- Regular Monitoring: Continuously monitor and track labor costs throughout the project. Compare actual labor costs against the estimated costs to identify any deviations or discrepancies. This allows for timely corrective actions and adjustments to stay within the project budget.
- Labour Productivity: Focus on improving labor productivity to optimize labor costs. Implement strategies to enhance efficiency, streamline processes, and promote effective communication and collaboration among workers. Enhancing productivity can help reduce labor hours, thus minimizing labor costs.
- Supplier and Contractor Negotiation: Engage in effective negotiation with suppliers and contractors to ensure competitive prices and favorable labor contracts. Explore partnerships and long-term agreements that offer cost-saving benefits. Carefully review contractual terms to avoid any hidden labor cost escalations.
- Value Engineering: Implement value engineering techniques to identify potential cost-saving opportunities without sacrificing quality. Look for alternative construction methods, material substitutions, or design modifications that can lower labor costs while maintaining project integrity.
- Change Management: Effectively manage changes to the project scope or specifications to mitigate any potential impact on labor costs. Implement a robust change control process to evaluate the cost implications and seek approval before proceeding with any scope changes that may affect labor costs.
By employing these strategies, you can bridge the gap between labor cost and project budget, ensuring that your construction project stays on track financially and delivers the desired outcomes within the allocated budget.
Tracking and Managing Labor Costs
Tracking and managing labor costs throughout the duration of a construction project are crucial for effective budget control and financial management. By implementing robust tracking and management procedures, you can identify any variations or discrepancies in labor costs and take the necessary actions to mitigate them. Here are some essential steps for tracking and managing labor costs:
- Timekeeping Systems: Implement a reliable timekeeping system to accurately record the hours worked by each laborer. This can be done through manual timesheets or automated software. Regularly review and reconcile the recorded hours to ensure accuracy in labor cost calculations.
- Checklists and Job Progress Reports: Develop checklists and job progress reports for supervisors to track the completion of tasks by the labor force. These reports can help measure productivity, identify any delays or inefficiencies, and assess the alignment of labor costs with the project timeline.
- Cost Code Tracking: Assign cost codes to various labor activities and expenses. This allows you to track and analyze the specific labor costs associated with each aspect of the project, providing better visibility into the overall labor cost breakdown.
- Regular Cost Review: Conduct regular reviews of labor costs against the project budget. Compare the actual labor costs incurred with the estimated costs to identify any deviations. Analyze the root causes of variances and take corrective measures to manage costs effectively.
- Change Order Management: Maintain a structured change order management process to address any changes or revisions in the project scope that may impact labor costs. These changes might involve additional labor hours, adjustments in labor rates, or modifications to labor requirements. Ensure that proper documentation, approvals, and cost adjustments are made for all change orders.
- Communication and Documentation: Foster effective communication among project stakeholders, including contractors, laborers, and management. Clearly communicate the budgetary constraints and encourage the reporting of labor-related issues or concerns. Maintain thorough documentation of labor-related activities, including timesheets, invoices, change orders, and other relevant records.
- Continuous Improvement: Regularly assess the effectiveness of your labor cost tracking and management processes. Look for areas where improvements can be made to enhance accuracy, efficiency, and cost control. Use lessons learned from previous projects to refine your labor cost tracking and management techniques.
By implementing these strategies, you can effectively track and manage labor costs throughout the construction project, allowing for better financial control, improved decision-making, and successful project outcomes within the allocated budget.
Conclusion
Calculating construction labor costs is a critical part of project planning and management. By understanding the factors that influence labor costs, determining the labor cost per hour, estimating labor hours, and effectively bridging the gap between labor cost and project budget, you can optimize your construction project’s financial success.
Accurate estimation of labor costs and labor hours lays the foundation for effective budgeting. Consider factors such as project complexity, location, labor market conditions, and skill requirements when determining labor costs. Taking into account benefits, overhead costs, and any special conditions will help you determine the labor cost per hour with greater accuracy.
Estimating labor hours involves predicting the time required for different tasks or project milestones. By defining tasks, utilizing historical data, considering expertise and experience, and developing a work breakdown structure, you can estimate labor hours more effectively.
Bridging the gap between labor cost and project budget requires careful planning and proactive management. Including a contingency reserve, regularly monitoring labor costs, focusing on labor productivity, and effectively managing supplier and contractor negotiations can help bridge this gap and keep your project within budget.
Tracking and managing labor costs throughout the project is essential for effective financial control. Implementing timekeeping systems, using checklists and job progress reports, tracking cost codes, conducting regular cost reviews, and managing change orders are all vital steps in tracking and managing labor costs effectively.
In conclusion, understanding how to calculate construction labor costs and implementing effective strategies for managing and tracking those costs are crucial for successful project execution. By considering the factors that influence labor costs, accurately estimating labor hours, bridging the gap between labor cost and project budget, and implementing robust tracking and management processes, you can enhance your construction project’s financial outcomes, ensuring a successful and cost-effective construction experience.
Frequently Asked Questions about How To Calculate Construction Labor Cost
Was this page helpful?
At Storables.com, we guarantee accurate and reliable information. Our content, validated by Expert Board Contributors, is crafted following stringent Editorial Policies. We're committed to providing you with well-researched, expert-backed insights for all your informational needs.
0 thoughts on “How To Calculate Construction Labor Cost”