Home>diy>Building & Construction>How To Calculate Overhead Cost For Construction
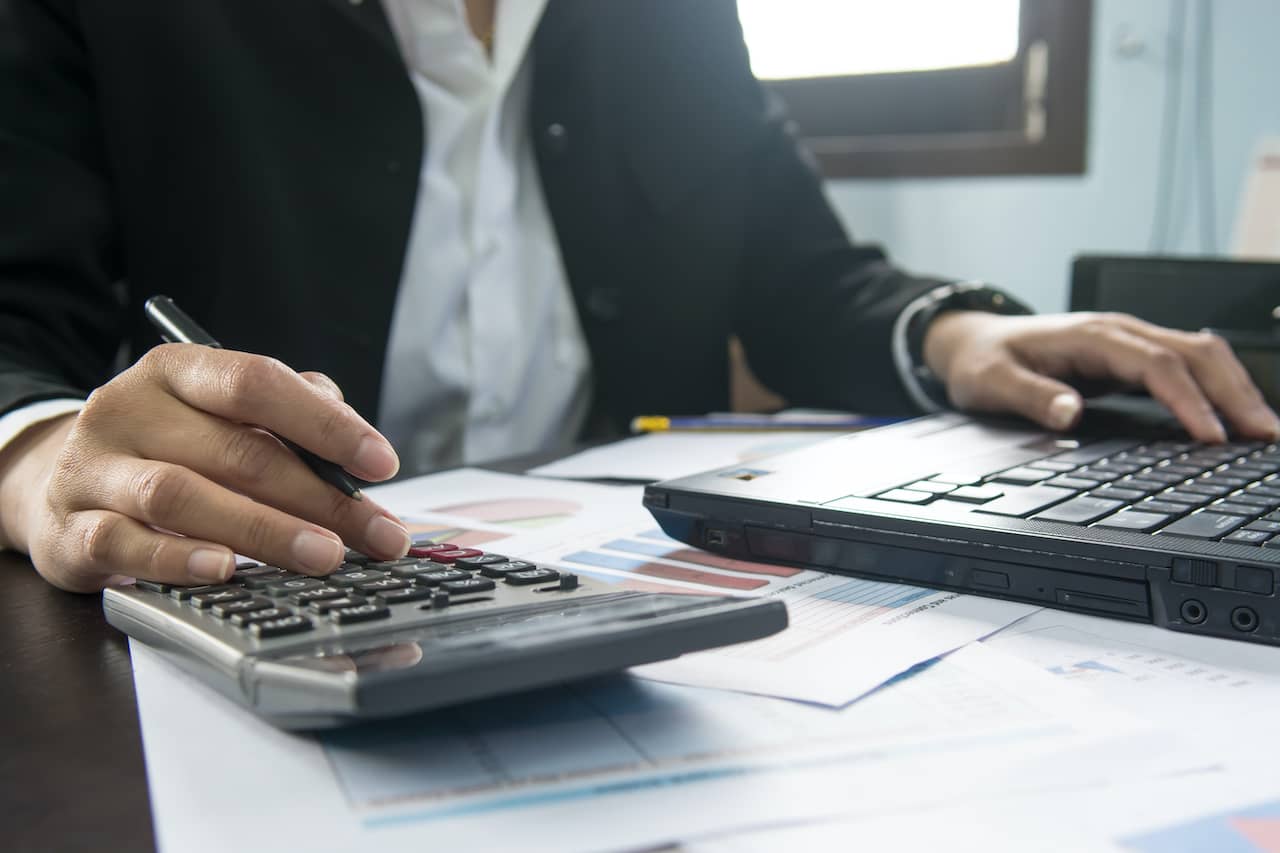
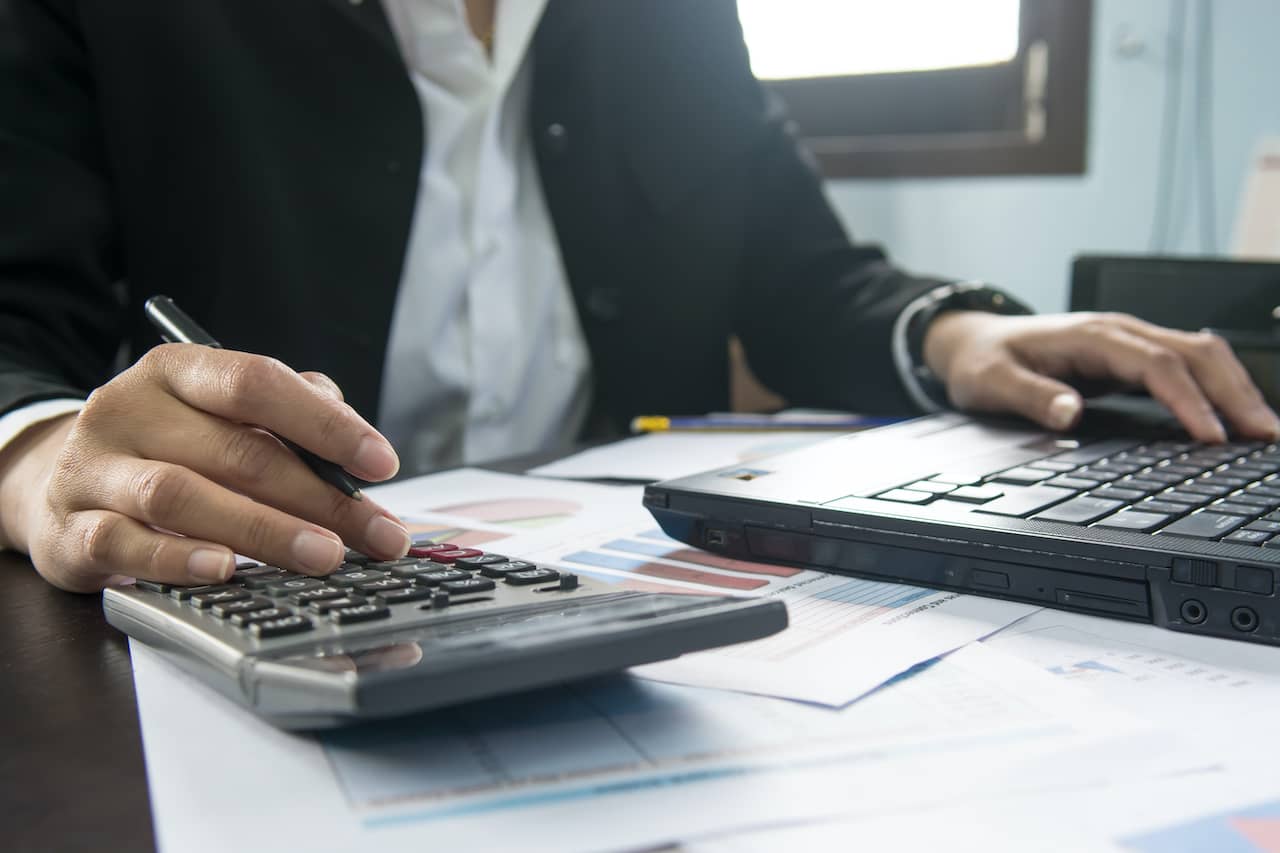
Building & Construction
How To Calculate Overhead Cost For Construction
Modified: January 24, 2024
Learn how to accurately calculate overhead costs for building construction projects with this comprehensive guide. Maximize profitability and minimize financial risks.
(Many of the links in this article redirect to a specific reviewed product. Your purchase of these products through affiliate links helps to generate commission for Storables.com, at no extra cost. Learn more)
Introduction
Calculating overhead costs is a crucial aspect of managing construction projects. It allows builders and contractors to accurately estimate the total cost of a project and determine the profitability of their ventures. Not accounting for overhead costs can lead to financial difficulties and project delays, making it essential to understand how to calculate and allocate these expenses.
In the construction industry, overhead costs refer to expenses that are not directly attributed to a specific project or task but are necessary for the overall operation of a construction business. These costs are incurred regardless of the size or scope of a project and include expenses such as administrative salaries, office rent, utilities, equipment maintenance, insurance, and other general expenses.
The calculation of overhead costs is essential for establishing an accurate project budget and determining the appropriate pricing for bids and contracts. It helps contractors ensure that all costs are covered while maintaining a healthy profit margin. Understanding the components and factors affecting overhead costs is crucial for accurate budgeting and financial management in the construction industry.
Throughout this article, we will explore the various components of overhead costs, the difference between direct and indirect costs, as well as the factors that influence overhead expenses in construction. We will also provide a step-by-step guide on how to calculate overhead costs and allocate them to projects effectively. By the end of this article, you will have a solid understanding of the importance of overhead cost calculation and how to implement it in your construction projects.
Key Takeaways:
- Accurate overhead cost calculation is crucial for construction projects, enabling realistic budgeting, competitive pricing, and informed resource allocation. Understanding and managing overhead costs drives financial success and project profitability.
- Monitoring and adjusting overhead costs is essential for construction companies to maintain control, identify cost-saving opportunities, and ensure accurate financial management. Proactive cost control measures contribute to long-term sustainability and profitability.
Read more: What Is Overhead Cost In Construction
Definition of Overhead Costs in Construction
In the construction industry, overhead costs are the expenses incurred by a construction company that are not directly attributed to a specific project or task, but are necessary for the overall operation of the business. These costs are ongoing and are incurred regardless of the size or scope of a construction project.
Overhead costs in construction include a wide range of expenses, such as administrative salaries, office rent, utilities, equipment maintenance, insurance, accounting fees, and other general expenses. They are essential for the day-to-day functioning of the construction company and are necessary to support the construction activities.
Unlike direct costs, which can be easily attributed to a specific project or task, overhead costs are indirect and cannot be directly allocated to a particular job. Instead, they are allocated to projects based on predetermined allocation rates or formulas. The allocation of overhead costs ensures that these expenses are proportionally distributed among the different projects and tasks undertaken by the construction company.
It is important to note that overhead costs are not included in the direct cost of a project, which includes labor, materials, and equipment directly used in the construction process. Overhead costs are separate and are accounted for separately to accurately assess the profitability and financial health of the company.
Understanding and accurately calculating overhead costs is crucial for builders, contractors, and construction project managers. By properly accounting for these expenses, construction professionals can develop accurate project budgets, set competitive prices for bids and contracts, and make informed decisions about resource allocation.
Now that we have a clear understanding of what overhead costs entail in the construction industry, let’s explore the importance of calculating these costs for construction projects.
Importance of Calculating Overhead Costs for Construction
Calculating overhead costs is a vital component of effective financial management in the construction industry. It plays a crucial role in ensuring accurate project budgeting, determining the profitability of projects, and making informed business decisions. Here are a few key reasons why calculating overhead costs is essential:
1. Accurate Project Budgeting: By calculating overhead costs and incorporating them into project budgets, construction professionals can develop a comprehensive understanding of the total expenses involved in a project. This enables them to set realistic budgets, allocate resources efficiently, and avoid potential cost overruns or inadequate funding.
2. Optimal Pricing and Bidding: Accurate overhead cost calculations allow contractors to determine the appropriate pricing for bids and contracts. By factoring in overhead expenses, construction companies can ensure that they are covering all costs while also including a reasonable profit margin. This helps to maintain competitiveness in the market and increase the chances of winning profitable contracts.
3. Profitability Assessment: Overhead cost calculations provide insights into the profitability of construction projects. By comparing the overhead costs incurred with the revenue generated from projects, contractors can assess the financial health of their ventures. This information helps them identify areas of improvement, make adjustments to maximize profitability, and make informed decisions regarding future projects.
4. Resource Allocation: Calculating overhead costs helps contractors allocate resources effectively. By understanding the costs associated with various activities and departments, construction professionals can make strategic decisions on how to allocate labor, equipment, and materials. This ensures that resources are utilized in the most efficient and cost-effective manner, ultimately enhancing productivity and reducing waste.
5. Financial Planning and Control: Accurate overhead cost calculations provide a solid foundation for financial planning and control in the construction industry. By having a clear understanding of the costs incurred for the operation of the business, construction companies can develop sound financial strategies, manage cash flow effectively, and make informed decisions related to investments and expansion.
6. Project Evaluation and Performance Analysis: Calculating overhead costs allows for a comprehensive evaluation of project performance. By comparing actual overhead costs with estimated costs, construction professionals can identify areas of improvement, measure project efficiency, and take corrective actions if necessary. This evaluation helps in improving future project estimations and overall project management practices.
In summary, calculating overhead costs is essential for accurate project budgeting, optimal pricing and bidding, profitability assessment, resource allocation, financial planning and control, and project evaluation. By understanding and incorporating overhead costs into construction management, professionals can ensure the success and profitability of their projects, and drive the growth of their businesses.
Components of Overhead Costs in Construction
Overhead costs in construction consist of various expenses that are necessary for the overall operation of a construction business but are not directly attributed to specific projects. These costs are incurred regardless of the size or scope of the projects undertaken. Here are some common components of overhead costs in construction:
1. Administrative Expenses: These include the salaries and benefits of administrative staff, office supplies, communication expenses, legal fees, and other general administrative costs. These expenses are essential for the smooth operation of the construction company and the management of various projects.
2. Rent and Utilities: The cost of office space, warehouse facilities, and equipment storage is considered a part of overhead costs. Additionally, utilities such as electricity, water, heating, and cooling are also included in overhead expenses.
3. Insurance: Construction companies must carry various types of insurance, including general liability insurance, workers’ compensation insurance, and equipment and property insurance. The premiums paid for these insurance policies are categorized as overhead costs.
4. Equipment Maintenance and Repairs: Construction companies rely on various types of equipment and machinery for their operations. The cost of maintaining, repairing, and servicing this equipment, as well as the depreciation of equipment over time, is considered part of overhead costs.
5. Training and Development: Construction companies often invest in the training and development of their employees to enhance their skills and knowledge. Expenses related to training programs, workshops, and certifications are included in overhead costs.
6. Licensing and Permit Fees: Construction projects require obtaining necessary licenses and permits from authorities. The fees associated with obtaining and renewing these licenses and permits are considered overhead costs.
7. Marketing and Advertising: Promoting a construction company and its services requires marketing and advertising efforts. Expenses related to website development, marketing campaigns, advertising materials, and trade show participation are considered part of overhead costs.
8. Accounting and Legal Services: Construction companies often require the assistance of accounting and legal professionals to manage their finances, tax obligations, and legal compliance. The fees for these services are categorized as overhead expenses.
9. Office Equipment and Software: Computers, printers, software licenses, and other office equipment necessary for administrative tasks and project management are considered overhead costs.
Each construction company may have additional components of overhead costs that are specific to their operations. It is important for construction professionals to examine their business expenses thoroughly and categorize them correctly to ensure accurate calculation of overhead costs.
Understanding the components of overhead costs is crucial for accurately estimating the total expenses of a construction project and ensuring that these costs are appropriately allocated. By having a comprehensive understanding of the various components, construction professionals can make informed decisions about budgeting, pricing, and resource allocation, ultimately leading to better financial management and project outcomes.
Direct Costs vs. Indirect Costs
In the construction industry, it is important to distinguish between direct costs and indirect costs when calculating project expenses and allocating costs. Understanding the difference between these two types of costs is crucial for accurate budgeting and financial management. Here’s a breakdown of direct costs and indirect costs in construction:
Direct Costs:
Direct costs, also known as project costs or job costs, are expenses that are directly attributable to a specific project or task. These costs can be easily identified and allocated to a particular project. Examples of direct costs in construction include:
- Materials: The cost of raw materials, such as lumber, concrete, steel, and electrical components, directly used in the construction process.
- Labor: The wages and benefits paid to workers directly involved in the construction project, including construction workers, engineers, and supervisors.
- Equipment: The cost of renting or purchasing equipment and machinery used specifically for a particular project.
- Subcontractor Fees: Payments made to subcontractors hired to perform specific tasks or trades within the project scope.
- Permits and Fees: The expenses associated with obtaining permits and paying regulatory fees directly related to the project.
Direct costs are typically variable costs that rise or fall based on the size and complexity of the project. These costs are directly linked to the completion of specific construction activities and can be easily measured and tracked.
Indirect Costs:
Indirect costs, also known as overhead costs or general costs, are expenses that are not directly attributable to a specific project or task but are necessary for the overall operation of a construction company. These costs are incurred regardless of whether a project is in progress or not. Examples of indirect costs in construction include:
- Administrative Salaries: The wages and benefits paid to administrative staff who support the company’s overall operations.
- Office Rent and Utilities: The cost of office space, utilities, and other facilities used for administrative purposes.
- Insurance: Premiums paid for general liability insurance, workers’ compensation insurance, and other types of insurance coverage.
- Equipment Maintenance: The cost of maintaining and repairing office equipment, vehicles, and machinery used for general company operations.
- Marketing and Advertising: Expenses related to marketing campaigns, advertising materials, and promotional activities used to promote the company’s services and brand.
- Accounting and Legal Services: Fees paid for accounting services, legal counsel, and other professional services necessary for the company’s financial management and legal compliance.
Indirect costs are typically fixed costs that do not vary based on the size or complexity of a specific project. Instead, they are allocated to projects based on predetermined allocation rates or formulas, often as a percentage of direct costs.
Understanding the distinction between direct costs and indirect costs is essential for accurately estimating project budgets, pricing contracts, and determining the overall profitability of construction projects. By properly allocating these costs, construction professionals can ensure that all expenses are accounted for, maintain profitability, and make informed decisions regarding resource allocation and business growth.
Read more: How To Calculate Construction Labor Cost
Factors Affecting Overhead Costs in Construction
Overhead costs in construction can be influenced by various factors that impact the overall operation and expenses of a construction business. It is important for construction professionals to understand these factors to accurately estimate and manage their overhead costs. Here are some key factors that can affect overhead costs in construction:
1. Company Size and Structure: The size and structure of a construction company can significantly impact its overhead costs. Larger companies may have higher overhead costs due to the need for more administrative staff, larger office spaces, and increased operational expenses. Additionally, the structure of the company, whether it is centralized or decentralized, can influence how overhead costs are allocated and managed.
2. Project Volume and Complexity: The volume and complexity of construction projects can directly impact overhead costs. Projects that are larger in scale or involve more intricate designs and technologies may require additional administrative support, specialized equipment, and increased supervision, resulting in higher overhead expenses.
3. Geographic Location: The geographic location of a construction project can impact overhead costs. Expenses such as rent, labor wages, and material transportation costs can vary based on the region or locality. Higher costs of living or a shortage of skilled labor in certain areas can increase overhead costs.
4. Industry Regulations and Compliance: The regulatory environment and compliance requirements in the construction industry can contribute to overhead costs. Construction companies must invest in ensuring compliance with safety regulations, building codes, environmental standards, and licensing requirements. Compliance-related expenses for training, inspections, certifications, and permits can add to the overall overhead costs.
5. Technology and Equipment: Adopting and maintaining technology and equipment can impact overhead costs. Construction companies that invest in advanced software, construction management systems, and state-of-the-art equipment may incur higher expenses for training, software licenses, equipment maintenance, and upgrades.
6. Labor Costs and Skill Level: Labor costs, including salaries, wages, and benefits, have a direct impact on overhead costs. Additionally, the level of skill and expertise required for a project can influence labor costs. Projects that require highly skilled tradespeople or specialized professionals may incur higher overhead expenses.
7. Market Conditions and Competition: Market conditions and competitive factors can affect overhead costs. In a highly competitive market, construction companies may need to invest more in marketing and advertising efforts to secure projects, resulting in higher overhead expenses. Pricing pressures and market fluctuations can also influence administrative salaries, subcontractor fees, and material costs.
8. Health and Safety: Maintaining a safe working environment is crucial in the construction industry. Expenses related to safety training, equipment, and compliance with health and safety regulations can impact overhead costs. Additionally, insurance premiums for workers’ compensation and general liability coverage can be influenced by a company’s safety record.
9. Economic Factors: Economic factors, such as inflation rates, interest rates, and cost fluctuations of materials and supplies, can impact overhead costs. Higher inflation or volatile market conditions can increase the prices of office supplies, equipment, and insurance premiums, contributing to higher overhead expenses.
By considering these factors, construction professionals can better plan, budget, and manage their overhead costs. Understanding the specific factors that affect overhead costs in their particular construction business allows them to make informed decisions, ensure accurate project estimates, and maintain profitability.
Steps to Calculate Overhead Costs for Construction
Calculating overhead costs accurately is essential for construction professionals to understand the total expenses involved in a project and determine the appropriate pricing and resource allocation. Here are the steps to effectively calculate overhead costs for construction:
Step 1: Identify Direct Costs:
First, identify and gather all direct costs associated with the construction project. These costs include materials, labor, equipment, subcontractor fees, permits, and any other expenses directly attributable to the specific project. Direct costs are typically tracked and recorded in project-specific cost accounts.
Step 2: Determine Indirect Costs:
Next, identify and collect all indirect costs that are essential for the overall operation of the construction company. These costs include administrative salaries, office rent, utilities, insurance, equipment maintenance, and other general overhead expenses. Indirect costs are typically recorded in separate accounts that are not project-specific.
Step 3: Allocate Indirect Costs to Cost Centers:
Allocate the indirect costs to cost centers or departments within the construction company. Cost centers can include administrative departments, project management teams, finance, and human resources. This allocation allows for a more accurate distribution of overhead expenses to different areas of the business.
Step 4: Calculate Overhead Allocation Rate:
To calculate the overhead allocation rate, divide the total indirect costs by a suitable allocation base. Common allocation bases in construction include direct labor hours, direct labor costs, or total project costs. For example, if the total indirect costs are $100,000 and the allocation base is direct labor hours, and the company expects to have 10,000 direct labor hours for all projects, the overhead allocation rate would be $10 per direct labor hour.
Step 5: Allocate Overhead Costs to Projects:
Once the overhead allocation rate is determined, allocate overhead costs to individual projects based on the allocation base for each project. Multiply the allocation base (e.g., direct labor hours or costs) for each project by the overhead allocation rate to determine the allocated overhead costs for that specific project. This step ensures that each project bears a fair share of the overhead costs.
Step 6: Calculate Overhead Cost per Unit:
If needed, calculate the overhead cost per unit. This step is especially useful if the construction project involves producing units of a product or completing repetitive tasks. Divide the total allocated overhead costs for the project by the number of units produced or tasks completed. This calculation provides insights into the overhead cost incurred per unit of output.
Step 7: Monitor and Adjust Overhead Costs:
Continuously monitor and review overhead costs throughout the project and make adjustments as necessary. This can involve revisiting the overhead allocation rate, reassessing cost centers, and incorporating any changes or new information that may affect the accuracy of the overhead cost calculations. Regular evaluation and adjustment help ensure that the overhead costs are accurately represented.
By following these steps, construction professionals can calculate overhead costs accurately, allocate them effectively to projects, and make informed decisions regarding budgeting, pricing, and resource allocation. Accurate overhead cost calculations contribute to the profitability and financial health of construction projects, enabling successful project completion and business growth.
Step 1: Identify Direct Costs
When calculating overhead costs in construction, the first step is to identify and gather all the direct costs associated with the specific construction project. Direct costs are expenses that can be directly attributed to the project and are incurred solely for its completion. These costs are typically tracked and allocated to specific cost accounts for accurate estimation and control of project expenses. Here are some key points to consider when identifying direct costs:
1. Materials: Identify all materials required for the construction project, including raw materials, building components, fixtures, and finishing materials. This may include items such as lumber, concrete, steel, piping, electrical wiring, hardware, and paint.
2. Labor: Determine the labor costs associated with the project. This includes wages, salaries, and benefits for all individuals involved in the construction activities, such as construction workers, supervisors, engineers, and project managers. It is important to consider both direct labor costs (for individuals directly working on the project) and indirect labor costs (for individuals providing support to the project).
3. Equipment: Take into account the costs of equipment and machinery necessary for the project. This includes both the purchase and rental costs of construction equipment, tools, and vehicles. Consider any depreciation or maintenance costs associated with the use of the equipment.
4. Subcontractor Fees: If subcontractors are hired for specific tasks within the project, identify and include their fees. This could include subcontractors for specialized trades like plumbing, electrical work, HVAC installation, or landscaping.
5. Permits and Fees: Consider any costs related to permits, licenses, inspections, and fees required by government and regulatory bodies. This may include building permits, environmental impact assessments, zoning permits, and other necessary legal and regulatory approvals.
6. Travel and Transportation: Include any travel expenses or transportation costs directly associated with the project. This may include transportation of materials to the construction site, travel costs for project managers or team members, and fuel expenses for company vehicles used in project-related activities.
7. Direct Proportionate Costs: Identify any other costs that can be directly allocated to the project based on their direct proportionate relationship. For example, if a specific project occupies a certain percentage of office space, a portion of the rent and utilities can be attributed as a direct cost to that project.
8. Other Miscellaneous Direct Costs: Consider any miscellaneous direct costs that are specific to the project. This may include costs for temporary structures, site setup, safety equipment, site security, and temporary utilities.
By identifying all direct costs accurately, construction professionals can develop a comprehensive understanding of the project expenses and ensure that these costs are effectively allocated and accounted for. This step sets the foundation for the accurate calculation and management of overhead costs in construction projects.
When calculating overhead costs for construction, be sure to include expenses such as insurance, utilities, equipment maintenance, and office expenses. These costs are essential for running the construction business and should be factored into the overall project budget.
Step 2: Determine Indirect Costs
After identifying the direct costs associated with a construction project, the next step in calculating overhead costs is to determine the indirect costs. Indirect costs, also known as overhead costs, are expenses that are not directly attributable to a specific project but are necessary for the overall operation of the construction company. These costs support the day-to-day functioning of the business and are incurred regardless of the size or scope of individual projects. Here are some key considerations when determining indirect costs:
1. Administrative Expenses: Include the costs associated with administrative functions, such as salaries and benefits for administrative staff, office supplies, communication expenses, legal fees, accounting services, and other general administrative costs. These expenses support the smooth operation and management of the construction company as a whole.
2. Office Rent and Utilities: Consider the costs of office space rental, including lease payments, property taxes, and maintenance fees. Also, include utility expenses such as electricity, water, heating, cooling, and telecommunications services required to operate the company’s administrative and support functions.
3. Insurance: Account for the costs of insurance coverage necessary for the construction company to protect against various risks. This includes general liability insurance, workers’ compensation insurance, and equipment and property insurance.
4. Equipment Maintenance and Repairs: Include the costs associated with the maintenance, repairs, and servicing of office equipment, vehicles, tools, and machinery used for administrative purposes. This may involve regular maintenance contracts, repairs by external vendors, or in-house maintenance staff.
5. Marketing and Advertising: Consider the expenses related to marketing and advertising efforts to promote the construction company’s services and attract clients. This may include costs for website development, marketing campaigns, advertising materials, online marketing platforms, and participation in trade shows or industry events.
6. Training and Development: Account for the costs associated with employee training programs, workshops, seminars, certifications, and other professional development activities. This includes ongoing education to enhance skills and knowledge in various areas of the construction business.
7. Licensing and Permit Fees: Consider the expenses associated with obtaining and renewing licenses, permits, certifications, and regulatory compliance fees required for the operation of the construction company. This may include fees for professional licenses, trade licenses, building permits, and environmental compliance.
8. Accounting and Legal Services: Include the costs of accounting services, legal counsel, and other professional services necessary for financial management, tax compliance, legal advice, and contracts. This may involve fees for bookkeeping, tax preparation, auditing, contract review, and other legal support.
9. Office Equipment and Software: Account for the costs of office equipment, such as computers, printers, scanners, and software licenses required for administrative tasks and project management. This includes the purchase, leases, or maintenance contracts for office equipment and software applications.
It is important to thoroughly review and categorize the various indirect costs specific to the construction company’s operations. By accurately determining the indirect costs, construction professionals can more effectively allocate and manage overhead expenses, ensuring accurate project budgeting, pricing, and financial planning.
Read more: How To Calculate House Construction Cost
Step 3: Allocate Indirect Costs to Cost Centers
Once the direct and indirect costs are identified, the next step in calculating overhead costs for construction projects is to allocate the indirect costs to cost centers. Cost centers are specific departments or functions within a construction company that incur indirect costs. Allocating indirect costs to cost centers allows for a more accurate distribution of overhead expenses. Here are the key steps to allocate indirect costs:
1. Identify Cost Centers: Determine the different cost centers or departments within the construction company that incur indirect costs. Common cost centers may include administration, project management, finance, human resources, and equipment maintenance.
2. Understand Cost Center Functions: Gain a thorough understanding of the functions and activities performed by each cost center. This helps to identify the specific indirect costs associated with each department and ensures that the allocation is appropriate.
3. Allocate Based on Proportional Usage: Allocate the indirect costs to each cost center based on its proportional usage of the resources that generate those costs. For example, if the administration department occupies 20% of the total office space, allocate 20% of the rent and utilities expenses to the administration cost center.
4. Use Allocation Factors: Determine appropriate allocation factors based on the specific characteristics of each cost center. These factors may be determined by square footage, headcount, direct labor hours, or any other suitable metric that reflects the proportional usage of resources by each department.
5. Collect Data: Gather relevant data required for the allocation process. This may include information on the square footage occupied by each department, the number of employees in each cost center, or the total direct labor hours worked by each department.
6. Calculate Allocations: Apply the allocation factors to the total indirect costs to determine the amount that should be allocated to each cost center. Multiply the indirect costs by the appropriate allocation factor for each department to calculate the portion of costs to be allocated.
7. Record Allocation Entries: Record the allocated costs in the accounting system by creating entries that transfer the appropriate amount from the overall indirect cost account to the respective cost centers. These entries should clearly indicate the amount and the basis of allocation for future reference and transparency.
8. Review and Adjust Allocation: Regularly review and analyze the allocation process to ensure accuracy and fairness. Adjust the allocation methodology if changes occur within the company’s structure, cost centers, or resource usage patterns.
By allocating indirect costs to specific cost centers, construction professionals can accurately distribute overhead expenses among different departments within the company. This allows for a more accurate assessment of the costs associated with each department’s operations and helps in budgeting, cost analysis, and making informed decisions about resource allocation. Effective allocation of indirect costs contributes to the overall financial management and profitability of construction projects.
Step 4: Calculate Overhead Allocation Rate
Calculating the overhead allocation rate is a key step in accurately distributing overhead costs to individual construction projects. The overhead allocation rate establishes the formula or percentage used to allocate indirect costs to each project based on a suitable allocation base. Here’s a breakdown of the steps to calculate the overhead allocation rate:
1. Determine the Total Indirect Costs: Add up all the indirect costs identified in Step 2. This includes costs such as administrative expenses, office rent, utilities, insurance, equipment maintenance, marketing, and other general overhead costs incurred by the construction company.
2. Select an Allocation Base: Choose a suitable allocation base, often referred to as a cost driver or cost allocation factor. This base should be a measure that is closely related to the consumption of indirect costs by the projects. Common allocation bases used in construction include direct labor hours, direct labor costs, or total project costs.
3. Calculate the Allocation Base: Calculate the total value of the chosen allocation base for all projects collectively. For example, if the chosen allocation base is direct labor hours, sum up the total direct labor hours estimated or worked for all projects within a certain time period.
4. Divide Total Indirect Costs by Allocation Base: Divide the total indirect costs by the total value of the allocation base calculated in the previous step. This will give the overhead allocation rate per unit of the chosen allocation base. For example, if the total indirect costs are $100,000 and the total direct labor hours for all projects are 10,000, the overhead allocation rate would be $10 per direct labor hour.
5. Express the Rate as a Percentage: If desired, convert the overhead allocation rate into a percentage by multiplying the rate by 100. This percentage represents the portion of indirect costs that will be allocated to each project based on the allocation base.
6. Document the Overhead Allocation Rate: It is crucial to document the calculated overhead allocation rate for future reference and transparency. Include the precise calculation methodology, the chosen allocation base, and any other pertinent information to ensure consistency and accuracy in further calculations.
The overhead allocation rate serves as a guide for accurately allocating indirect costs to individual construction projects. By establishing a clear and consistent formula for allocating overhead expenses, construction professionals can ensure that each project bears its fair share of indirect costs in proportion to its consumption of the chosen allocation base. This helps in accurately estimating project budgets, setting appropriate pricing for bids and contracts, and making informed financial decisions. Regular review and adjustment of the overhead allocation rate may be necessary to reflect changes in business operations, cost structures, or market conditions.
Step 5: Allocate Overhead Costs to Projects
Once the overhead allocation rate has been calculated, the next step is to allocate the overhead costs to individual construction projects based on their usage of the chosen allocation base. This step ensures that each project bears a fair share of the indirect costs. Here’s a breakdown of the steps to allocate overhead costs to projects:
1. Gather Project-Specific Data: Collect project-specific data related to the allocation base chosen in Step 4. For example, if the allocation base is direct labor hours, gather the total estimated or actual direct labor hours worked on each project.
2. Multiply Data by Overhead Allocation Rate: Multiply the project-specific data (e.g., direct labor hours, direct labor costs, or total project costs) for each individual project by the overhead allocation rate calculated in Step 4. This yields the allocated overhead costs specific to each project.
3. Record Allocated Overhead Costs: Record the allocated overhead costs in project-specific accounts or as separate line items within the project’s budget or cost management system. This helps in tracking and monitoring the distribution of overhead expenses to individual projects.
4. Verify Accuracy and Consistency: Review the allocation calculations to ensure accuracy and consistency. Double-check the project-specific data used and verify that the allocated overhead costs are reasonable and proportionate to the chosen allocation base.
5. Consider Adjustments: If significant changes in project scope or resource usage occur during the course of a project, consider adjusting the allocation of overhead costs accordingly. This helps to ensure that the allocated overhead costs reflect the current circumstances and remain fair and accurate.
6. Document the Allocation: It is crucial to document the allocation of overhead costs to individual projects for future reference and transparency. Clearly record the methodology, data used, and calculations made to demonstrate how the overhead costs were allocated to each project.
Allocating overhead costs to individual construction projects based on their usage of the chosen allocation base enables a fair distribution of indirect costs and helps in accurately estimating the total cost of each project. By incorporating the overhead costs into project budgets, construction professionals can ensure that all expenses are accounted for and that the project remains financially viable. This allocation process provides clarity and transparency in understanding the indirect costs associated with each project and assists in making informed decisions regarding resource allocation, pricing, and profitability analysis. Regular monitoring and adjustment of the overhead cost allocations may be necessary to accommodate changes in project dynamics or business operations.
Step 6: Calculate Overhead Cost per Unit
In addition to allocating overhead costs to individual construction projects, it can be beneficial to calculate the overhead cost per unit. This step is particularly useful when the construction project involves producing units or completing repetitive tasks. Determining the overhead cost per unit provides insights into the overhead costs incurred for each unit of output. Here are the steps to calculate the overhead cost per unit:
1. Identify the Unit of Output: Determine the unit of output or the basis by which the project’s work is measured. This could be the number of completed units, square footage, linear feet, or any other relevant measure that represents the quantity of work completed.
2. Calculate the Total Allocated Overhead Costs: Sum up the allocated overhead costs for all the projects within a certain time period. These allocated costs are the indirect costs that have been distributed to each project using the overhead allocation rate.
3. Determine the Total Output Units: Calculate the total number of units produced or tasks completed for all the projects within the same time period. This should align with the unit of output identified in step 1.
4. Divide Total Allocated Overhead Costs by Total Output Units: Divide the total allocated overhead costs by the total number of output units. This calculation yields the overhead cost per unit of output.
5. Analyze and Interpret Results: Analyze the calculated overhead cost per unit and evaluate its significance in relation to the project’s progress and profitability. Compare it to other cost metrics, such as direct costs or market benchmarks, to gain insights into cost-efficiency and cost control.
6. Consider Variations and Adjustments: Recognize that the overhead cost per unit may fluctuate over time due to changes in project scale, production volume, or resource utilization. Monitor these variations and adjust the cost per unit calculation as needed to reflect the most accurate and up-to-date insights.
7. Document the Calculation and Results: Document the methodology used to calculate the overhead cost per unit, including the specific time period and projects included in the calculation. Record the results for reference and comparisons during project evaluation and future cost analysis.
Calculating the overhead cost per unit provides a helpful metric to evaluate the efficiency of production and resource utilization within a construction project. By understanding the overhead costs incurred per unit of output, construction professionals can make informed decisions related to pricing strategies, cost control measures, and productivity improvements. This analysis contributes to more accurate forecasting and budgeting for future projects, as well as identifying areas for cost reduction and process optimization. Regular assessment and adjustment of the overhead cost per unit will aid in maintaining cost efficiency and improving overall project profitability.
Read more: What Is Considered Overhead In Construction
Step 7: Monitor and Adjust Overhead Costs
Monitoring and adjusting overhead costs is a crucial step in the management of construction projects. It enables construction professionals to maintain control over expenses, identify potential cost savings, and ensure that overhead costs remain accurate and reflective of the current business operations. Here are the key steps to effectively monitor and adjust overhead costs:
1. Regular Tracking and Reporting: Establish a system for tracking and reporting overhead costs on an ongoing basis. This includes maintaining records of both direct and indirect costs, as well as the allocation of overhead expenses to projects and cost centers. Regularly review and analyze these records to identify any discrepancies or areas that require further investigation.
2. Comparative Analysis: Conduct regular comparative analysis of overhead costs to ensure they are in line with expectations and industry norms. Compare current overhead costs to historical data from previous projects or industry benchmarks to identify any significant deviations or areas for improvement.
3. Identify Cost Variances: Identify any significant variances or unexpected fluctuations in overhead costs. Investigate the reasons behind these variances, such as changes in project scope, unexpected expenses, or inefficiencies in resource utilization. Understanding the root causes of cost variances can help in implementing corrective measures.
4. Engage in Continuous Cost Control: Implement proactive cost control measures to manage overhead costs effectively. This may involve optimizing resource allocation, streamlining administrative processes, negotiating better terms with suppliers, or identifying opportunities for cost-saving initiatives.
5. Adjust Allocation Methodology, if Necessary: Regularly evaluate the allocation methodology used to distribute overhead costs to projects and cost centers. If changes occur within the company’s structure, cost centers, or resource usage patterns, consider adjusting the allocation methodology to ensure it accurately reflects the specific needs and circumstances of the business.
6. Review Resource Utilization: Assess the utilization of resources, such as labor, equipment, and materials, within the construction projects. Identify any inefficiencies or areas where resources are not effectively utilized, as this can contribute to higher overhead costs. Implement strategies to optimize resource utilization and minimize wastage.
7. Evaluate Overhead Allocation Rate: Periodically review and assess the overhead allocation rate calculated in Step 4. Consider whether the chosen allocation base is still relevant and reflective of the company’s operations. Adjust the overhead allocation rate if necessary to maintain accuracy and alignment with current business conditions.
8. Regular Cost Reduction Strategies: Continuously explore opportunities for cost reduction and efficiency improvement. This may involve renegotiating contracts with suppliers, seeking competitive pricing, implementing technology solutions to streamline processes, or investing in employee training to enhance productivity.
9. Document and Communicate Changes: Document any adjustments, changes, or improvements made to overhead costs and the allocation process. Communicate these changes to relevant stakeholders, including project managers, finance teams, and senior management, to ensure transparency and alignment throughout the organization.
By effectively monitoring and adjusting overhead costs, construction professionals can proactively manage expenses and improve the financial performance of projects and the overall business. Regular review and assessment of overhead costs allow for early identification of issues, timely decision-making, and the implementation of appropriate cost control measures. This continuous improvement approach helps ensure the financial success and long-term sustainability of construction projects.
Conclusion
Calculating and managing overhead costs is vital for the success of construction projects and the overall financial health of construction companies. Accurately estimating and allocating overhead costs allows construction professionals to develop realistic project budgets, set competitive pricing, and make informed decisions about resource allocation. Throughout this article, we have examined the key steps involved in calculating and managing overhead costs in construction.
We started by defining overhead costs as those expenses that are necessary for the overall operation of a construction business but are not directly attributed to a specific project. These costs include administrative salaries, office rent, utilities, insurance, equipment maintenance, and other general expenses. Understanding the components and factors influencing overhead costs is essential for accurate budgeting and financial management.
The article then outlined the difference between direct costs and indirect costs, with direct costs being expenses directly attributable to a specific project, and indirect costs being those required for the overall operation of the business. By grasping this distinction, construction professionals can effectively allocate costs and assess project profitability.
We delved into the factors influencing overhead costs, such as company size and structure, project volume and complexity, geographic location, industry regulations, and economic factors. Being aware of these factors helps construction professionals make accurate estimations and adjust their finances accordingly.
The step-by-step guide provided a practical approach to calculating overhead costs, including identifying direct costs, determining indirect costs, allocating indirect costs to cost centers, calculating the allocation rate, allocating overhead costs to projects, and optionally calculating the overhead cost per unit. Each step is crucial for accurate cost assessment and effective financial management in construction projects.
Lastly, we emphasized the importance of monitoring and adjusting overhead costs. Continuously tracking expenses, comparing costs to benchmarks, controlling costs, and regularly reviewing and adjusting allocation methodologies all contribute to maintaining profitability and efficient resource management.
In conclusion, understanding and effectively managing overhead costs in construction is paramount for successful project execution and long-term financial sustainability. By accurately estimating and allocating these costs, construction professionals can ensure profitability, make informed decisions, and optimize the use of resources. With a comprehensive understanding of the components, factors, and steps involved in calculating overhead costs, construction companies can enhance their financial management practices and drive the success of their projects and business as a whole.
Frequently Asked Questions about How To Calculate Overhead Cost For Construction
Was this page helpful?
At Storables.com, we guarantee accurate and reliable information. Our content, validated by Expert Board Contributors, is crafted following stringent Editorial Policies. We're committed to providing you with well-researched, expert-backed insights for all your informational needs.
0 thoughts on “How To Calculate Overhead Cost For Construction”