Home>diy>Building & Construction>How To Save On Construction Costs
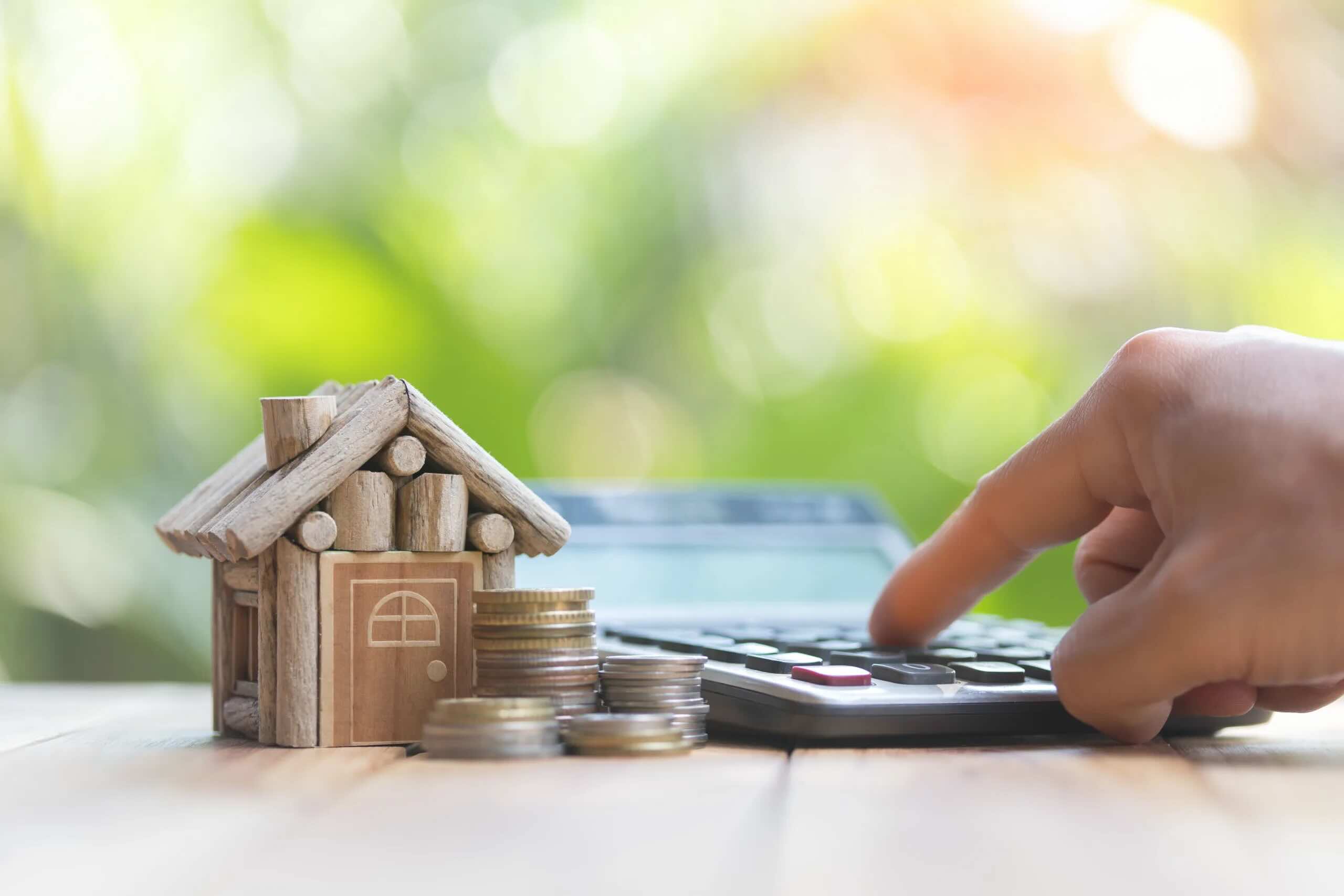
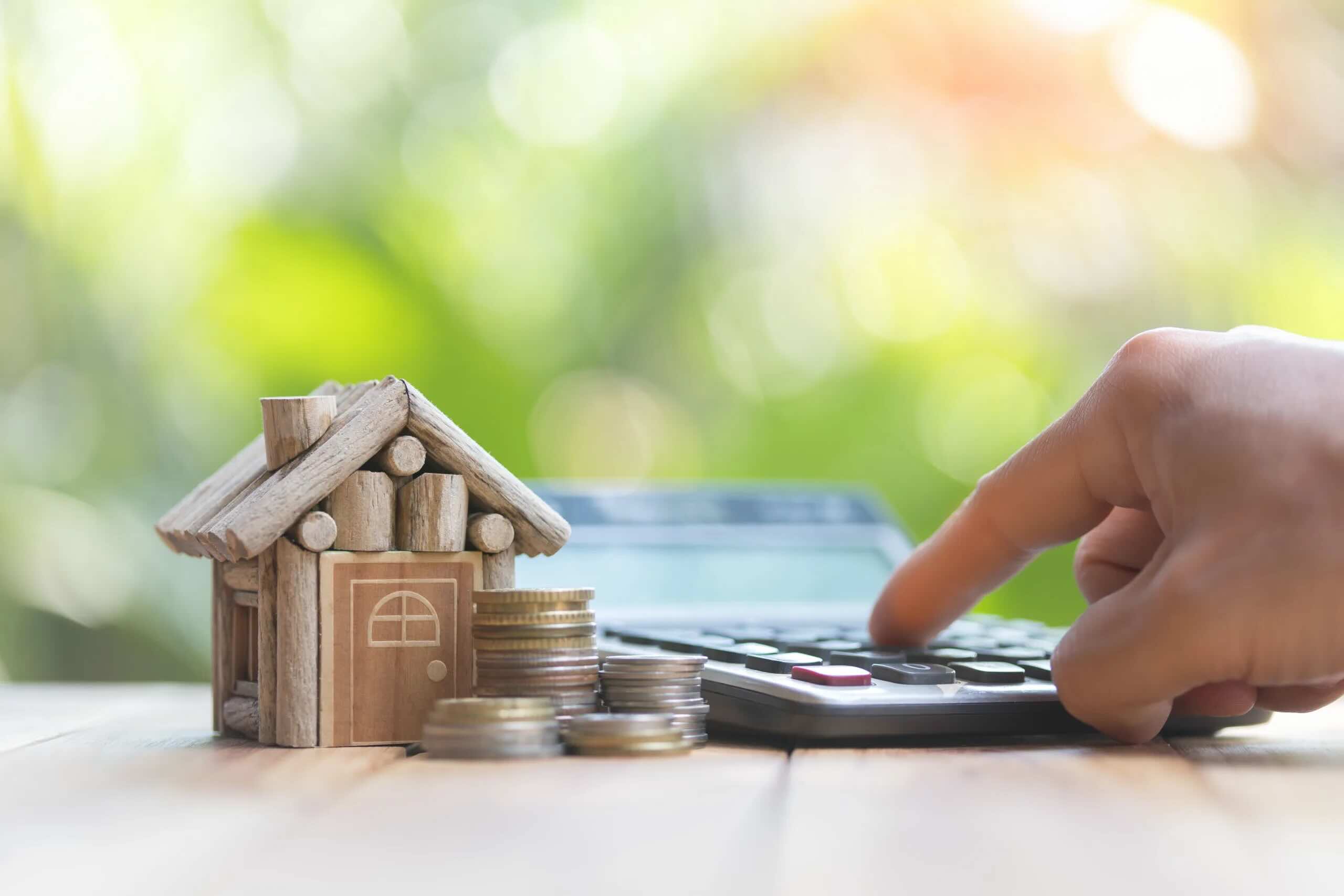
Building & Construction
How To Save On Construction Costs
Modified: October 18, 2024
Learn effective strategies to save on construction costs in the building construction industry. Find out how to maximize your budget and minimize expenses.
(Many of the links in this article redirect to a specific reviewed product. Your purchase of these products through affiliate links helps to generate commission for Storables.com, at no extra cost. Learn more)
Introduction
When it comes to construction projects, managing costs is a top priority. Whether you are embarking on a small renovation or a large-scale building construction, finding ways to save on expenses can significantly impact your bottom line. In this article, we will explore some effective strategies to help you save on construction costs without compromising the quality or integrity of your project.
Construction costs can quickly add up, making it crucial to have a well-defined budget from the outset. By evaluating your project budget, you can identify areas where cost savings can be made. Consider allocating funds to essential aspects of the project while looking for ways to save on non-essential elements.
Prioritizing your needs allows you to focus on the critical aspects of your construction project. Identify the core requirements and ensure that they are given priority in your budget. By doing so, you can allocate resources more efficiently and avoid overspending on less critical areas.
Exploring alternative materials and methods is another effective way to save on construction costs. Traditional building materials can be expensive, but there are often more affordable alternatives available. Research different materials, such as composite materials or engineered wood, which can provide cost savings without compromising performance or durability.
Consider utilizing prefabricated or modular construction methods, which can help reduce costs and construction time. Prefabricated components, such as walls or even entire rooms, can be manufactured off-site and then assembled on-site. This streamlined process can save both time and money while maintaining quality.
Getting multiple bids from contractors is essential to ensure that you are getting the best value for your money. Request detailed estimates from reputable contractors and compare their pricing, qualifications, and proposed timelines. This competitive bidding process can help you find the most cost-effective option without sacrificing quality.
Key Takeaways:
- Prioritize essential aspects of your construction project to allocate resources efficiently and avoid overspending on non-essential elements, ensuring cost savings without compromising quality.
- Explore alternative materials, prefabricated construction, and value engineering to identify cost-saving opportunities, optimize the design, and avoid costly change orders, ultimately achieving cost efficiencies without sacrificing project quality.
Read more: How To Save Money On Air Conditioning Costs
Evaluate Your Project Budget
One of the first and most critical steps in saving on construction costs is evaluating your project budget. Having a clear understanding of your financial limitations will allow you to make informed decisions and prioritize your spending.
Start by determining the overall budget for your construction project. Consider factors such as the scope of work, desired quality level, and any specific requirements or constraints. It’s important to be realistic about what you can afford and to allocate funds accordingly.
Next, break down your budget into different categories or phases of the project. This will help you identify areas of potential cost savings and ensure that you allocate funds effectively. Consider the following categories:
- Materials: Evaluate the estimated costs of the necessary materials for your project. Research alternative options that may be more cost-effective without compromising quality.
- Labor: Determine the projected labor costs, including wages, employment taxes, and insurance. Consider the complexity of the work and the availability of skilled labor when estimating these costs.
- Equipment: Assess the need for equipment rentals or purchases. Research different suppliers for the best prices, and ensure that you only acquire the equipment you truly need for the project.
- Permits and Fees: Account for any necessary permits, inspections, or regulatory fees. Be sure to understand the requirements and associated costs upfront to avoid unexpected expenses later on.
- Contingency: Set aside a contingency fund for unexpected costs or potential changes in the scope of work. It’s best to have a buffer to handle unforeseen circumstances without jeopardizing the project’s finances.
By evaluating each category of your budget, you can identify areas where there may be opportunities to save. Look for cost-effective alternatives or ways to streamline processes without compromising safety or quality.
Remember, it’s essential to strike a balance between cost savings and achieving your desired outcome. Cutting corners or sacrificing quality to save money may end up costing you more in the long run if you have to deal with repairs or replacements.
Take the time to thoroughly evaluate your project budget and make sure you have a clear understanding of your financial limitations. This knowledge will guide your decision-making process as you explore cost-saving measures throughout the construction project.
Prioritize Your Needs
When it comes to construction projects, it’s essential to prioritize your needs to maximize cost savings and ensure that your budget is allocated wisely. By focusing on the most critical aspects of your project, you can avoid overspending on non-essential elements.
Start by identifying the core requirements of your construction project. What are the key functionalities and features that must be included? Determine the non-negotiables and establish them as your top priorities. These may include structural integrity, safety measures, compliance with building codes, or specific design elements that are essential to your project’s success.
Once you have identified your project’s core needs, allocate resources accordingly. Concentrate on ensuring that these critical aspects are well-funded and executed flawlessly. This includes using high-quality materials, hiring skilled and experienced contractors, and implementing proper quality control measures.
However, it’s important to note that prioritizing needs doesn’t mean neglecting other aspects of your project. It simply means allocating resources in a way that focuses on the essentials first. By doing so, you can ensure that your project meets the necessary requirements while avoiding unnecessary expenses.
When considering non-essential elements or optional features, evaluate their impact on the project’s overall functionality and value. Ask yourself whether these features are necessary or if they can be scaled back or eliminated without compromising the project’s goals.
For example, in a residential construction project, consider whether luxurious finishes or extravagant landscaping features are essential to meet your project objectives. By prioritizing your needs, you may discover that cost-efficient alternatives can still meet your requirements without breaking the bank.
Additionally, be open to compromise and alternative solutions that can help you achieve your project’s goals within your budget constraints. Collaborate with your architects and contractors to explore different design options and value engineering techniques. This process involves finding creative ways to reduce costs without sacrificing the overall functionality or aesthetics of the project.
By prioritizing your needs, you can make informed decisions about where to allocate your financial resources. This approach ensures that the most critical aspects of your project receive the attention and investment they require, while non-essential elements can be adjusted or eliminated to achieve cost savings.
Remember, effective prioritization requires careful consideration and a clear understanding of your project goals and objectives. By focusing on the essentials, you can maximize cost savings without compromising the overall success of your construction project.
Explore Alternative Materials and Methods
When it comes to saving on construction costs, exploring alternative materials and methods is a smart strategy. Traditional building materials and techniques can be costly, but there are often more affordable options available that can still deliver high-quality results.
One way to save on material costs is to research alternative materials that provide similar or even enhanced performance at a lower price point. For example, instead of using traditional solid wood for structural elements, consider engineered wood products. Engineered wood is made by bonding together multiple layers of wood veneers, resulting in a strong and cost-effective alternative.
Composite materials are also worth considering. These materials are created by combining different components, such as fibers or resins, to achieve specific characteristics. For example, fiberglass-reinforced panels (FRPs) offer durability and resistance to corrosion, making them a viable alternative to traditional steel or concrete in certain applications.
Another way to save on construction costs is by exploring alternative building methods. Traditional construction can be time-consuming and labor-intensive, leading to increased costs. Consider prefabricated or modular construction methods, which involve manufacturing building components off-site and assembling them on-site.
Prefabricated construction allows for greater efficiency and cost savings as components are produced in a controlled environment, reducing construction time and waste. Modular construction takes this concept further, allowing for entire rooms or units to be built off-site and installed directly at the construction site. This not only saves time and labor costs but also allows for greater precision and quality control.
Moreover, alternative methods such as 3D printing are gaining traction in the construction industry. 3D printing enables the creation of complex shapes and structures using additive manufacturing techniques, eliminating the need for molds or formwork. This innovative method can save both time and material costs.
When considering alternative materials and methods, it’s important to analyze their suitability for your specific project. Factors such as building codes, structural requirements, and climate conditions should be taken into account. Consulting with architects, engineers, and construction professionals will provide valuable insights into the feasibility and cost-effectiveness of different options.
By exploring alternative materials and methods, you can discover cost-efficient solutions that maintain the required quality and functionality of your construction project. This proactive approach allows you to achieve your objectives while effectively managing your budget.
Consider Prefabricated or Modular Construction
When it comes to saving on construction costs, one approach that is gaining popularity is the use of prefabricated or modular construction methods. These innovative techniques offer numerous benefits, including cost savings, shorter construction timelines, and improved quality control.
Prefabricated construction involves the manufacturing of building components off-site in a controlled environment. These components, such as walls, floors, or roof trusses, are then transported to the construction site and assembled. This method allows for precise manufacturing and reduces the need for on-site labor, resulting in significant cost savings.
One of the primary advantages of prefabricated construction is the reduced construction time. Since the components are manufactured concurrently with site preparation, the overall project timeline is significantly shortened. This not only helps save on labor costs but also reduces the financing and overhead expenses associated with longer construction periods.
Modular construction takes prefabrication to the next level by constructing entire rooms or units off-site and then transporting and assembling them on-site. This approach offers even greater efficiency and cost savings. Entire modules, such as bathroom pods or kitchen units, can be manufactured simultaneously while site work and foundation preparation are taking place.
By using modular construction, project managers can reduce the on-site labor needs and address the shortage of skilled labor in many areas. Additionally, the modular technique allows for higher precision and quality control as the components are produced in a controlled factory environment with stringent quality standards.
Another cost-saving aspect of prefabricated and modular construction is the ability to optimize material usage. With precise measurements and pre-planning, waste is significantly reduced compared to traditional construction. This minimizes material costs and environmental impact, making it a sustainable choice as well.
It’s important to note that prefabricated and modular construction methods are not limited to specific building types. These techniques have been successfully applied in various sectors, including residential, commercial, and industrial construction.
Before considering prefabricated or modular construction for your project, it’s crucial to collaborate closely with architects, contractors, and suppliers who specialize in these methods. Their expertise will ensure that the design and manufacturing processes are aligned with your project’s requirements and local building codes.
While prefabricated and modular construction may not be suitable for every project, exploring these options can lead to significant cost savings while maintaining high-quality standards. By considering these innovative techniques, you can optimize cost efficiency without compromising on the functionality or aesthetics of your construction project.
Read more: How To Reduce Construction Cost
Get Multiple Bids from Contractors
One of the most effective ways to save on construction costs is by obtaining multiple bids from contractors. By soliciting bids from different construction companies, you can compare prices, services, and timelines, ultimately finding the most cost-effective option for your project.
Start by creating a list of potential contractors who have experience in the type of project you are undertaking. Consider recommendations from friends, colleagues, or industry professionals, and thoroughly research each contractor’s reputation, qualifications, and previous work.
Once you have a shortlist of contractors, provide them with a detailed scope of work and project specifications. This will enable them to provide accurate and thorough bids. Be sure to include all relevant details, such as architectural plans, engineering requirements, and any specific materials or finishes you desire.
When reviewing the bids, pay close attention to the breakdown of costs and the scope of work included. Ensure that each bid covers all aspects of the project, including permits, materials, labor, and any additional services, such as cleanup or disposal of construction waste.
Comparing bids solely based on the overall cost may not provide an accurate picture of the project. Look beyond the numbers and evaluate the value provided by each contractor. Consider the following factors:
- Experience and Qualifications: Does the contractor have relevant experience in similar projects? Check their qualifications, certifications, and references to ensure their competence.
- Timeline: Examine the proposed schedule provided by each contractor. Consider whether it aligns with your project’s timeline and any deadlines you need to meet.
- Quality of Work: Review the contractor’s previous projects and assess the quality of their workmanship. Look for testimonials or client feedback to gauge their reputation for delivering high-quality results.
- Communication and Collaboration: Evaluate each contractor’s communication skills and willingness to collaborate. A contractor who is receptive to your ideas and provides regular updates can contribute to a smoother and more cost-effective construction process.
It’s also important to clarify any assumptions made by the contractors in their bids. Ensure that there are no hidden costs or exclusions that may affect the final price. Clear communication and transparency are key to avoiding any surprises down the line.
Remember, the lowest bid may not always be the best choice. Assess the overall value and reputation of the contractors, as well as their ability to meet your project’s unique requirements and specifications.
Obtaining multiple bids gives you the opportunity to negotiate and potentially lower costs. Once you have gathered sufficient information, engage in discussions with the contractors to address any concerns and explore potential cost-saving measures.
By diligently reviewing multiple bids and considering the factors mentioned above, you can make an informed decision and select a contractor who offers the best value for your construction project. This approach will help you optimize cost savings without compromising on quality or the successful completion of your project.
Consider using alternative building materials such as recycled or reclaimed materials to save on construction costs. These materials can often be found at a lower cost and can add unique character to your project.
Optimize the Design for Cost Efficiency
Design plays a crucial role in the cost of a construction project. By optimizing the design for cost efficiency, you can save significant amounts of money without compromising the functionality or aesthetics of your building. Here are some strategies to consider:
- Functional Space Planning: Ensure that the floor plan maximizes the use of space and minimizes wasted areas. Eliminate unnecessary hallways, open up common areas, and prioritize the placement of essential rooms and features.
- Efficient Layout: Optimize the arrangement of rooms and utilities to minimize the need for excessive plumbing or wiring runs. Strategic placement of bathrooms, kitchens, and utility rooms can reduce the length of pipes and cables, saving on materials and installation costs.
- Structural Simplicity: A complex structural design can significantly increase construction costs. Consider simpler structural systems that meet your project’s needs without excessive complexity. Additionally, work with your structural engineer to find cost-effective alternatives for materials like steel or concrete.
- Energy Efficiency: Incorporating energy-efficient design features can save on long-term operational costs. Use natural lighting to reduce the need for artificial lighting, prioritize insulation and thermal control measures to minimize heating and cooling needs, and consider energy-efficient appliances and systems.
- Standardize Components: Design with standard sizes and materials to take advantage of economies of scale. This can simplify construction and reduce material waste, as well as allow for easier maintenance and repairs down the line.
- Multifunctional Spaces: Consider designing spaces that serve multiple purposes. For example, a room designed to function as both a guest bedroom and a home office can optimize space usage and reduce the need for additional rooms.
Collaboration between the architect, contractor, and other professionals involved in the project is essential to optimize the design for cost efficiency. Start by clearly defining your budget and goals to guide the design process. Regular meetings and open communication will allow for discussions on design alternatives that can save money.
Additionally, engaging in value engineering can help identify cost-saving opportunities without compromising the quality or performance of the design. Value engineering involves analyzing the design and making suggestions for alternative materials, construction methods, or systems that provide similar functionality but at a lower cost.
It’s important to strike a balance between cost efficiency and meeting your project’s requirements. While optimizing the design can lead to significant savings, it’s crucial to consider long-term implications and the overall value of the construction project.
By focusing on cost-efficient design elements and leveraging the expertise of professionals, you can optimize the design for cost efficiency without sacrificing the functionality, aesthetics, or long-term sustainability of your project.
Utilize Value Engineering
Value Engineering is a systematic and collaborative approach that can help optimize a construction project’s value by identifying cost-saving opportunities. By leveraging value engineering techniques, you can reduce construction costs without compromising quality, safety, or functionality. Here’s how to effectively utilize value engineering:
1. Assemble a Value Engineering Team: Form a team that includes key stakeholders such as architects, engineers, contractors, and relevant experts. This multidisciplinary team will bring diverse perspectives and expertise to the value engineering process.
2. Define Project Objectives and Constraints: Clearly outline your project’s goals, budget, timeline, and any specific constraints or limitations. This provides a framework for the value engineering process and helps ensure that proposed changes align with project requirements.
3. Analyze and Evaluate the Design: Evaluate the current design to identify potential areas for cost reduction. This includes analyzing materials, systems, and construction methods to identify any unnecessary complexities or redundancies. Look for opportunities to streamline the design without compromising functionality or safety.
4. Brainstorm and Generate Ideas: Encourage open brainstorming sessions with the value engineering team. Explore alternative design options, materials, and construction techniques that can achieve the same project objectives more efficiently and cost-effectively.
5. Assess Cost Implications: Evaluate the potential cost savings and benefits associated with each value engineering idea. Consider not only the upfront construction costs but also long-term maintenance, energy efficiency, and lifecycle costs. This comprehensive analysis ensures that proposed changes are true value enhancements.
6. Prioritize and Implement Changes: Prioritize the value engineering ideas based on their potential cost savings and alignment with project objectives. Determine which changes are feasible and practical to implement within the project’s constraints. Work with the design and construction teams to integrate the approved changes seamlessly.
7. Evaluate Risk and Impact: Assess the potential risks and impacts associated with value engineering changes. Consider factors such as safety, code compliance, and durability. Collaborate with the design and engineering professionals to ensure that any modifications maintain or enhance the project’s quality and standards.
8. Continual Monitoring and Review: Consistently monitor the value engineering changes as the construction progresses. Regularly review and assess their effectiveness in achieving the desired cost savings and other project objectives. Make adjustments as necessary to optimize value throughout the construction process.
Value engineering is not about cutting corners or compromising on quality; it’s about finding more efficient ways to achieve the desired outcome. By leveraging value engineering techniques, you can identify cost-saving opportunities, improve project efficiency, and enhance overall value without sacrificing the integrity of your construction project.
Seek Cost-Saving Opportunities During Construction
Cost-saving opportunities can arise throughout the construction process, and actively seeking them can help you optimize your project’s budget. By incorporating these strategies, you can identify and implement cost-saving measures without compromising the quality or functionality of your construction project.
1. Efficient Project Management: Implement strong project management practices to ensure smooth coordination and efficient use of resources. This includes effective scheduling, communication, and supervision to minimize delays, errors, and rework that can inflate costs.
2. Material Optimization: Monitor and track material usage to avoid wastage. Keep a careful inventory to prevent over-ordering or under-utilizing materials. Utilize offcuts or salvaged materials where appropriate, and encourage reuse or recycling to reduce waste disposal costs.
3. Value-Engineered Solutions: Continuously explore value-engineered solutions during the construction phase. Engage with your construction team and subcontractors to identify areas where cost savings can be achieved without compromising quality. This can involve reevaluating material choices, construction methods, or technology applications.
4. Subcontractor Consolidation: Consider consolidating subcontracting services to a single provider or a select few, rather than hiring multiple contractors for various tasks. This can help reduce administrative overhead, streamline project management, and negotiate better rates through economies of scale.
5. Energy-Efficient Systems and Equipment: Explore energy-efficient systems, equipment, and technologies for your project, such as LED lighting, high-efficiency HVAC systems, or renewable energy sources. While the initial upfront costs may be slightly higher, the long-term energy savings can offset the initial investment and result in overall cost savings throughout the project’s lifespan.
6. Streamlined Change Order Process: Implement a streamlined change order process to minimize unnecessary changes and ensure that any required modifications are efficiently executed. Clear communication, documentation, and evaluation of change requests can prevent costly delays and disputes.
7. Workforce Efficiency: Optimize labor productivity by ensuring clear communication, proper training, and skilled supervision. Encourage open dialogue between subcontractors and construction teams to identify potential productivity improvements and address any issues promptly.
8. Ongoing Cost Analysis: Continually monitor and analyze costs throughout the construction process. Regularly review budget performance, cost variances, and projected vs. actual expenses. This enables you to identify areas where costs may be exceeding expectations and take corrective actions as needed.
9. Use of Technology: Leverage construction management software, digital tools, and Building Information Modeling (BIM) to streamline processes, improve collaboration, and automate tasks. These technologies can help reduce manual errors, improve productivity, and increase efficiency, leading to potential cost savings.
Remember, seeking cost-saving opportunities during construction requires proactive engagement and ongoing evaluation. Regularly communicate with your construction team, subcontractors, and suppliers to identify potential cost-saving measures and implement them effectively. By embracing these strategies, you can create a more efficient and cost-effective construction process.
Read more: What Are Construction Costs
Avoid Costly Change Orders
Change orders are a common occurrence in construction projects, but they can be a source of significant cost overruns if not managed effectively. By implementing proactive strategies to avoid costly change orders, you can minimize disruptions, maintain budget control, and ensure the successful completion of your project. Here are some key approaches to consider:
1. Clear and Detailed Initial Planning: Invest time and effort in the initial planning phase to clearly define project requirements, specifications, and design parameters. Engage with architects, engineers, and other stakeholders to thoroughly review the plans and ensure that everyone has a comprehensive understanding of the project scope and objectives. This will help minimize the need for changes later on.
2. Robust Design Development: Thoroughly develop the design and documentation before construction begins. Anticipate potential design changes or challenges and address them proactively. Engage with designers and contractors to identify and resolve any design conflicts or potential issues early in the process, reducing the need for change orders during construction.
3. Effective Communication and Collaboration: Establish open and clear lines of communication with all project stakeholders. Encourage regular meetings and discussions to address any concerns or changes early on. Maintain open dialogue between the design team, contractor, subcontractors, and clients to ensure that everyone is aligned with project goals and potential design modifications.
4. Comprehensive Contracts and Specifications: Ensure that contracts and specifications are thorough, precise, and clearly state the responsibilities, deliverables, and expectations of each party involved. Clearly define the procedures for handling change orders and establish a process that includes proper documentation, cost estimation, and approval protocols.
5. Regular Site Visits and Inspections: Conduct regular site visits and inspections to identify any issues or discrepancies early on. This can help identify potential changes before they become costly change orders. Regular communication and collaboration with the construction team will enable you to address any emerging issues promptly and find cost-effective solutions.
6. Proper Project Management: Employ effective project management techniques to ensure that the project stays on track and within budget. Monitor progress and expenditures, identify any potential deviations or risks that could lead to change orders, and take proactive steps to mitigate these risks. Timely intervention and proactive risk management can prevent small issues from escalating into costly change orders.
7. Engage Stakeholders in Decision Making: Involve all stakeholders in the decision-making process to ensure that their concerns and requirements are considered. This helps minimize conflicts and reduces the likelihood of later changes driven by misunderstandings or unaddressed concerns.
8. Regular Documentation and Record Keeping: Maintain thorough documentation throughout the construction process. Keep a record of all communication, decisions, and variations to design or scope. This documentation will serve as a valuable resource if disputes or claims arise, and will provide clarity and transparency in case of change orders.
By implementing these strategies, you can minimize the occurrence of costly change orders and maintain better control over your project’s budget and timeline. Consistent communication, proactive planning, and effective project management are essential to avoid unnecessary expenses and ensure a successful construction project.
Conclusion
Managing and saving on construction costs is a critical aspect of any building project. By implementing the strategies outlined in this article, you can achieve cost efficiencies without compromising the quality or integrity of your construction project.
Evaluating your project budget and prioritizing your needs provide a roadmap for effective cost management. By allocating resources based on the essential requirements, you can avoid overspending on non-essential elements.
Exploring alternative materials and methods can lead to significant cost savings. Consider utilizing prefabrication or modular construction techniques, as they offer streamlined processes, shorter construction timelines, and overall financial benefits.
Seeking multiple bids from contractors allows you to compare prices and services, ultimately selecting the most cost-effective option. Additionally, optimizing the design for cost efficiency through practical space planning and material selection can result in substantial savings.
Utilizing value engineering techniques helps identify cost-saving opportunities throughout the construction process. By continuously evaluating design alternatives and materials, you can achieve efficiencies and maximize value without compromising the project’s objectives.
During construction, actively seeking cost-saving opportunities and avoiding costly change orders is crucial. Proper project management, effective communication, and proactive risk mitigation strategies help minimize unnecessary expenses and keep the project on track and within budget.
In conclusion, successfully saving on construction costs requires a combination of careful planning, continuous evaluation, collaboration, and proactive management. By implementing these strategies, you can achieve cost efficiencies without sacrificing the quality or timely completion of your construction project, ultimately maximizing value and ensuring its success.
Frequently Asked Questions about How To Save On Construction Costs
Was this page helpful?
At Storables.com, we guarantee accurate and reliable information. Our content, validated by Expert Board Contributors, is crafted following stringent Editorial Policies. We're committed to providing you with well-researched, expert-backed insights for all your informational needs.
0 thoughts on “How To Save On Construction Costs”