Home>diy>Building & Construction>What Does DD Mean In Construction
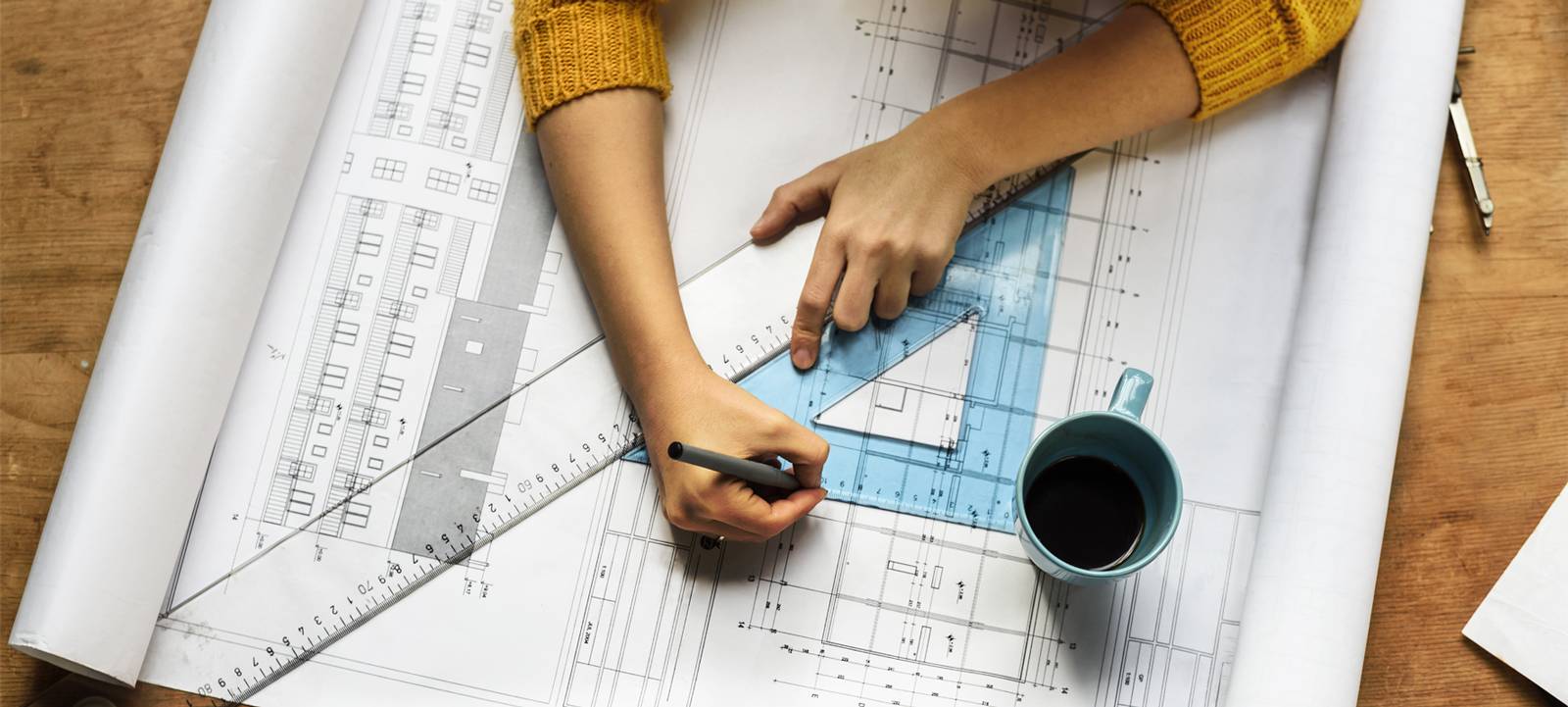
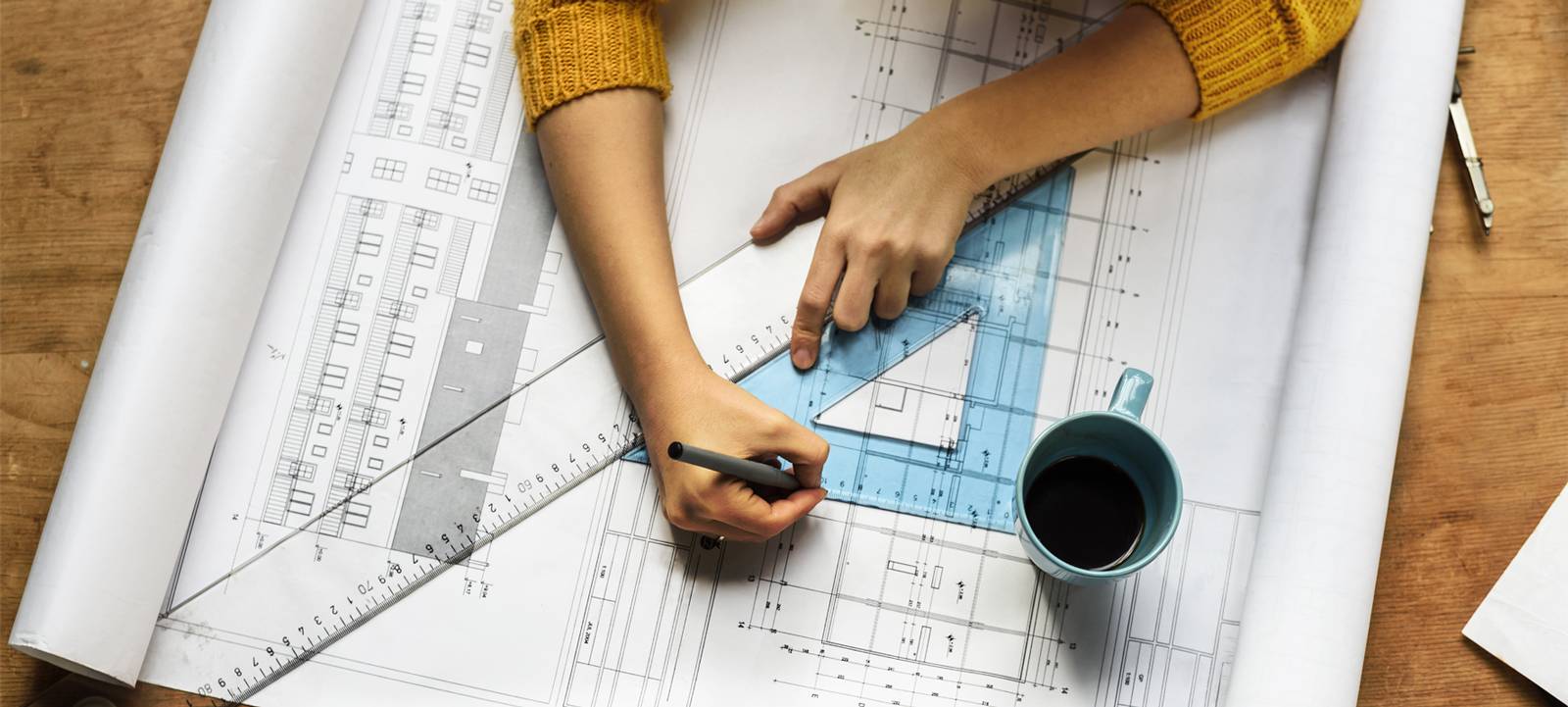
Building & Construction
What Does DD Mean In Construction
Modified: January 24, 2024
Learn what DD means in construction and how it relates to building-construction projects. Gain insight into common uses and importance in the industry.
(Many of the links in this article redirect to a specific reviewed product. Your purchase of these products through affiliate links helps to generate commission for Storables.com, at no extra cost. Learn more)
Introduction
In the ever-evolving world of construction, staying up-to-date with the latest technologies and methodologies is crucial for success. One such innovation that has revolutionized the industry is the implementation of Digital Design (DD) in construction projects. DD, also known as Building Information Modeling (BIM), is a computer-based process that allows construction professionals to create detailed virtual models of buildings and infrastructure.
With DD, architects, engineers, and contractors can collaborate seamlessly, streamline workflows, and optimize the construction process from design to completion. Gone are the days of relying solely on paper plans and blueprints; DD has transformed the way construction projects are conceptualized, planned, and executed.
In this article, we will delve into the world of DD in construction. We will explore the definition of DD, its various types, the importance and benefits of implementing DD in construction projects, as well as the challenges and risks it presents. Additionally, we will discuss best practices for implementing DD, showcase some successful case studies, and provide insights into future trends and innovations in the field.
Key Takeaways:
- Digital Design (DD) in construction, also known as Building Information Modeling (BIM), revolutionizes the industry by enhancing collaboration, visualization, and project efficiency. It is essential for successful and competitive construction projects in the digital age.
- The future of Digital Design (DD) in construction holds exciting advancements, including AI, IoT integration, VR/AR, generative design, cloud computing, robotics, and advanced data analytics. These innovations will reshape the construction landscape, optimizing collaboration and sustainability.
Definition of DD in Construction
Digital Design (DD) in construction refers to the utilization of computer-based technologies, commonly known as Building Information Modeling (BIM), to create virtual representations of building projects. DD involves the creation and management of digital models that encompass the entire lifecycle of a construction project, from initial conceptualization to facility management.
DD goes beyond traditional 2D drawings and blueprints by incorporating three-dimensional elements and rich data attributes. These digital models typically contain a wealth of information, including geometric data, material specifications, structural components, plumbing and electrical systems, and more. By utilizing DD, all stakeholders in a construction project can visualize and analyze the design in a highly detailed and interactive manner.
The use of DD in construction offers numerous advantages. Firstly, it allows for better visualization and understanding of the project, enabling stakeholders to identify and resolve potential issues early in the planning stage. Additionally, DD facilitates efficient collaboration and coordination among architects, engineers, contractors, and other professionals involved in the project.
Furthermore, DD enables the integration of scheduling and cost information, providing a comprehensive view of project timelines, resource allocation, and budgetary considerations. This integration allows for more accurate project planning, reducing the likelihood of delays, cost overruns, and rework.
Overall, DD empowers construction professionals to optimize project efficiency, minimize errors, and improve communication between all project participants. As technology continues to advance, the scope and capabilities of DD are expanding, leading to even greater innovations in the construction industry.
Types of DD in Construction
Digital Design (DD) in construction encompasses a variety of techniques and tools that enable the creation of virtual models and simulations. Here are some common types of DD used in the construction industry:
- BIM (Building Information Modeling): BIM is a comprehensive DD methodology that involves the creation and management of digital representations of a building project. BIM models are composed of intelligent objects that contain information about the physical and functional characteristics of the elements they represent. BIM allows for the integration of various aspects such as architecture, structure, mechanical systems, and electrical systems into a single, centralized model.
- Virtual Reality (VR) and Augmented Reality (AR): VR and AR technologies have revolutionized the way construction professionals interact with digital models. VR provides an immersive experience by creating a virtual environment that can be explored using specialized headsets, while AR overlays digital information onto the real-world environment, enhancing the visualization and understanding of project elements.
- 3D Printing: 3D printing, also known as additive manufacturing, can be used in conjunction with DD to create physical models and prototypes. 3D printers can use digital designs to construct physical objects layer by layer, allowing for accurate and detailed representations of building components.
- Simulation and Visualization: DD enables the simulation and visualization of complex construction processes. This includes simulating the construction sequence, logistics planning, and even simulating how a building will perform under various conditions such as wind, temperature, or seismic events. These simulations aid in identifying potential issues and optimizing project outcomes.
- Laser Scanning and Point Clouds: Laser scanning technology captures precise measurements of existing structures and environments, generating point cloud data. This data can be imported into DD software to create accurate models, aiding in renovation or retrofitting projects by providing a detailed starting point for the design process.
These are just a few examples of the types of DD in construction. As technology continues to advance, new methods and tools are constantly emerging, further enhancing the capabilities and possibilities of DD in the construction industry.
Importance of DD in Construction
Digital Design (DD) has become an essential component of the construction industry due to the numerous benefits it offers. Here are some key reasons why implementing DD is crucial for construction projects:
- Enhanced Collaboration: DD facilitates collaboration and communication among all stakeholders involved in a construction project. With a centralized digital model, architects, engineers, contractors, and other professionals can work together in real-time, making it easier to share information, provide feedback, and resolve conflicts. This collaborative approach leads to improved project outcomes and reduced errors.
- Better Visualizations: Traditional 2D drawings can be challenging to interpret, especially for non-technical stakeholders. DD provides three-dimensional visualizations that are more intuitive and realistic, allowing clients, investors, and other stakeholders to better understand the project. This leads to increased engagement and trust.
- Early Clash Detection: DD enables the identification and resolution of potential clashes and interferences early in the design phase. Through clash detection software, conflicts between architectural, structural, and MEP (mechanical, electrical, plumbing) systems can be highlighted and addressed before construction begins. This proactive approach minimizes costly rework and delays.
- Improved Planning and Project Management: DD integrates scheduling, cost estimating, and resource management into the model, providing a comprehensive view of the project. This allows for more accurate planning, better resource allocation, and the ability to evaluate the impact of design changes on the project timeline and budget.
- Reduced Construction Errors and Rework: By visualizing the project in a digital environment, potential errors can be identified and resolved before construction begins. This reduces expensive rework and ensures a higher level of quality and accuracy in the final built structure.
- Streamlined Facility Management: The digital model created during DD can be carried over to facility management, providing valuable information for maintenance, repairs, and renovations. This streamlines future operations by delivering accurate documentation and facilitating efficient facilities management.
Overall, DD in construction enhances collaboration, visualizations, clash detection, planning, and project management, while reducing errors and improving facility management. It is evident that DD is no longer just a trend but a fundamental tool for successful construction projects in the digital age.
Benefits of DD in Construction
Digital Design (DD) has brought about a multitude of benefits to the construction industry. Here are some of the key advantages of implementing DD in construction projects:
- Improved Design Accuracy: DD allows for the creation of highly accurate and detailed digital models. This precision helps reduce design errors, ensuring that the final built structure matches the intended design. Design changes can be easily made within the digital model, minimizing the need for costly modifications during the construction phase.
- Enhanced Visualization: DD provides a three-dimensional representation of the project, allowing stakeholders to visualize the design more realistically. This leads to better decision-making, as clients, architects, and engineers can better understand the spatial relationships and aesthetics of the project. With interactive virtual walkthroughs, stakeholders can experience the design from various perspectives.
- Efficient Clash Detection: Clash detection tools in DD software enable early identification of conflicts between different building systems, such as structural and MEP components. This allows for clash resolution before construction begins, reducing rework, cost overruns, and delays. Clash detection also improves coordination among different trades, ensuring a smoother construction process.
- Optimized Resource Management: DD enables accurate quantity takeoffs, facilitating precise material ordering and resource allocation. This minimizes material wastage and ensures that the required resources are available at the right time, improving project efficiency and reducing costs.
- Enhanced Construction Planning: DD provides the ability to simulate and analyze construction sequences, allowing for optimized project planning. This includes evaluating logistics, scheduling, and sequencing of construction activities. The visualization of the construction process aids in identifying potential issues and optimizing project timelines.
- Improved Communication and Collaboration: DD promotes effective communication and collaboration among project stakeholders. With a digital model as a centralized platform, architects, engineers, contractors, and clients can easily share and access project information. Real-time collaboration reduces miscommunication, enhances coordination, and improves overall project outcomes.
- Better Cost Estimation: DD allows for accurate cost estimation by integrating design data with quantities and prices, helping stakeholders to make informed financial decisions. This enables better budget planning, reduces the risk of cost overruns, and ensures the project stays within the allocated budget.
- Streamlined Facility Management: The digital model created during DD can be utilized for ongoing facility management. It provides valuable information for maintenance, repairs, and renovations, improving the efficiency of building operations. Facility managers can easily access and update the digital model, ensuring accurate documentation for future maintenance needs.
These benefits collectively contribute to improved project outcomes, reduced errors and rework, enhanced collaboration, and increased overall efficiency. DD has undoubtedly become an essential tool in the construction industry, delivering significant advantages to all stakeholders involved.
DD in construction stands for “Design Development.” It is the phase in the design process where the initial concept is refined and detailed drawings are created. This phase is crucial for finalizing the design before moving on to construction.
Challenges and Risks Related to DD in Construction
While Digital Design (DD) offers numerous benefits to the construction industry, it also presents some challenges and risks that need to be addressed. Here are some key challenges and risks related to DD in construction projects:
- Learning Curve: Implementing DD in construction requires a level of technical expertise and training. Professionals need to familiarize themselves with DD software, tools, and processes, which can have a learning curve. Adequate training and support are essential to ensure successful adoption and utilization of DD technology.
- Data Accuracy and Quality: DD relies heavily on the accuracy and quality of data input into the digital models. Inaccurate or incomplete data can lead to errors and discrepancies in the design and construction process. It is crucial to ensure that data sources are reliable and regularly updated to maintain the integrity of the digital models.
- Technology Compatibility and Integration: Different stakeholders may use different software or versions, which can create compatibility issues when sharing and collaborating on the digital models. Integration challenges may arise when attempting to connect various software applications and systems. Proper coordination and standardized protocols are necessary to resolve these compatibility and integration concerns.
- Data Security and Privacy: Construction projects involve sensitive and proprietary information. Protecting intellectual property and ensuring the privacy and security of project data can be a challenge. Proper data management practices, including secure storage and sharing protocols, should be implemented to mitigate the risks of data breaches and unauthorized access.
- Costs and Budgetary Considerations: Implementing DD in construction projects may require an initial investment in hardware, software, and training. Additionally, ongoing maintenance and updates need to be factored into the project budget. The cost of implementing DD should be carefully evaluated to ensure that the benefits outweigh the expenses.
- Legal and Contractual Issues: The use of DD raises unique legal and contractual considerations. Intellectual property rights, ownership of digital models, liability issues, and contract modifications need to be carefully addressed and clearly defined in project contracts and agreements. Legal experts specializing in construction and technology law should be consulted to ensure compliance and mitigate legal risks.
- Dependency on Technology: DD relies heavily on technology, and any technological failure or data loss can have significant implications for a construction project. Backup and disaster recovery plans should be in place to safeguard the digital models and ensure minimal disruption in case of technology-related issues.
While these challenges and risks exist, they can be effectively managed by establishing appropriate protocols, investing in training and support, and having a comprehensive risk management strategy in place. Despite the challenges, the benefits and long-term value of incorporating DD into construction projects make it well worth the effort to overcome these hurdles.
Best Practices for Implementing DD in Construction
To ensure a successful implementation of Digital Design (DD) in construction projects, it is important to follow best practices that optimize the utilization and benefits of DD. Here are some key best practices to consider:
- Establish Clear Project Objectives: Clearly define the project objectives and communicate them to all stakeholders. This will help set a common understanding of the project requirements and expectations, ensuring alignment throughout the DD process.
- Invest in Training and Education: Provide comprehensive training to all team members involved in the DD process. This includes architects, engineers, contractors, and subcontractors. Ensuring that all individuals are proficient in DD tools and processes will improve collaboration and efficiency.
- Collaboration and Communication: Foster a collaborative environment where all stakeholders actively participate and communicate effectively. Implement tools and platforms that facilitate real-time collaboration, enabling seamless exchange of information and feedback.
- Standardize Workflows and Protocols: Establish standardized workflows and protocols for DD implementation across the entire project team. This includes naming conventions, file management, and information exchange protocols. Consistency in these areas promotes efficiency and avoids confusion.
- Regular Data Validation and Maintenance: Ensure that the data used in the DD process is accurate and up-to-date. Regularly validate and update data sources to maintain the integrity of the digital models. Implement data management protocols to manage changes and revisions effectively.
- Integrated Project Delivery: Utilize an integrated project delivery approach where all stakeholders work collaboratively from the early stages of the project. Encourage multidisciplinary coordination and involvement, aligning the design, construction, and operations teams to maximize the benefits of DD.
- Embrace Clash Detection and Resolution: Make use of clash detection tools to identify and resolve conflicts between different building systems early in the design phase. Regularly conduct clash detection exercises and implement an effective resolution process to minimize rework and delays.
- Continuous Quality Control and Assurance: Implement quality control measures throughout the DD process to identify errors or inconsistencies. Regularly review and validate the digital models to ensure accuracy and adherence to project requirements.
- Monitor and Adapt: Continuously monitor the progress and outcomes of the DD implementation. Gather feedback from stakeholders and make necessary adjustments to optimize the process. Embrace a culture of continuous improvement to enhance the effectiveness of DD in future projects.
- Document and Archive: Establish a system to document and archive the digital models and related project data. This ensures that valuable information is accessible for future reference, facility management, and potential renovations or expansions.
By following these best practices, construction professionals can effectively implement DD in their projects, maximizing the benefits and leveraging the full potential of this transformative technology. Successful DD implementation requires a combination of technical proficiency, effective communication, standardized processes, and a commitment to ongoing improvement.
Case Studies of Successful DD Projects in Construction
Digital Design (DD) has been instrumental in transforming the construction industry, enabling the successful completion of complex projects with improved efficiency and reduced errors. Let’s take a look at some notable case studies highlighting the successes achieved through the implementation of DD in construction.
- Burj Khalifa, Dubai: The iconic Burj Khalifa, the tallest building in the world, stands as a testament to the power of DD in construction. DD played a crucial role in the design and construction of the skyscraper, allowing the project team to accurately visualize the building’s intricate components and ensure structural integrity. The use of DD aided in scheduling, coordination of various trades, and clash detection, resulting in the successful completion of this architectural marvel.
- Taisei Smart Mega Panel System, Japan: The Taisei Smart Mega Panel System is a revolutionary construction method that utilizes DD extensively. The system involves the manufacturing of prefabricated panels that integrate structural elements, mechanical systems, and finishes. The digital model of the structure, created through DD, allows for accurate manufacturing and assembly, reducing construction time and costs. This method has been used successfully in various projects, including the construction of hospitals and high-rise buildings in Japan.
- Veterans Affairs (VA) Hospitals, United States: DD has been widely adopted in the design and construction of VA Hospitals across the United States. By implementing DD, these projects achieved improved coordination among various trades, enhanced clash detection, and facilitated seamless collaboration between the VA and the project team. The use of DD resulted in more efficient construction processes, reduced rework, and ultimately delivered advanced medical facilities to serve veterans.
- Terminal 2, Chhatrapati Shivaji International Airport, India: The development of Terminal 2 at Mumbai’s Chhatrapati Shivaji International Airport utilized DD extensively. The digital model enabled the coordination of architectural, structural, MEP, and airport systems, ensuring smooth operations and passenger flow within the terminal. DD facilitated effective clash detection, enabling timely resolution and minimizing construction delays. The successful implementation of DD played a crucial role in the timely completion of this ambitious project.
- Masdar City, Abu Dhabi: Masdar City, a sustainable urban development project in Abu Dhabi, made extensive use of DD to create a digital model of the entire city. The digital model allowed for effective planning, simulation, and optimization of energy systems, transportation networks, and sustainable infrastructure. This DD-driven approach contributed to the realization of a highly sustainable and environmentally-friendly community.
These case studies demonstrate the significant impact that DD has had on construction projects worldwide. The successful application of DD in these projects has resulted in improved coordination, reduced errors, enhanced collaboration, and streamlined construction processes. These achievements highlight the immense value that DD brings to the construction industry in realizing ambitious and innovative projects.
Future Trends and Innovations in DD for Construction
Digital Design (DD) has already revolutionized the construction industry, but the advancements and future trends in this field are set to further transform and enhance the way construction projects are conceived and executed. Here are some key future trends and innovations in DD for construction:
- Artificial Intelligence (AI) and Machine Learning: AI and machine learning algorithms can analyze vast amounts of data generated during the DD process, helping to identify patterns, optimize designs, and automate certain tasks. This technology can assist in generating design alternatives, estimating project costs, and even predicting and preventing potential risks or issues.
- Internet of Things (IoT) Integration: The integration of IoT devices and sensors with DD models allows for real-time monitoring and data collection during construction and throughout the lifecycle of a building. This data can be used to analyze performance, monitor energy usage, and optimize building operations, leading to increased efficiency and sustainability.
- Virtual and Augmented Reality (VR/AR): VR and AR technologies are expected to become more prevalent in the DD process, enabling stakeholders to experience and interact with virtual models in immersive and intuitive ways. These technologies will enhance collaboration and communication, allowing for better visualization, design reviews, and on-site construction guidance.
- Generative Design: Generative design is a process that uses algorithms and computational power to explore and generate numerous design alternatives based on given parameters and constraints. Through iterative optimization processes, generative design can produce innovative and efficient design solutions, pushing the boundaries of architectural and structural possibilities.
- Cloud Computing: Cloud computing platforms will continue to play a significant role in DD, providing scalable and accessible environments for storing, accessing, and collaborating on digital models. Cloud-based solutions enable real-time collaboration, facilitate remote work, and ensure seamless information exchange among project stakeholders.
- Robotics and Automation: The integration of robotics and automation with DD has the potential to revolutionize construction processes. Robotic systems can be used for tasks such as 3D printing, prefabrication, and modular construction, enabling faster and more precise construction. Automation can also be applied to repetitive tasks, freeing up human resources for more complex and creative efforts.
- Advanced Data Analytics: As digital models become more complex, the analysis of large datasets becomes crucial. Advanced data analytics techniques can extract valuable insights from the digital models, helping to optimize construction processes, improve resource management, and enhance building performance.
These future trends and innovations in DD will further enhance collaboration, optimization, and efficiency in construction projects. By embracing these advancements, the industry can unlock new possibilities, achieve higher levels of sustainability, and deliver buildings that meet the evolving needs of society.
Read more: What Does NOC Mean In Construction
Conclusion
Digital Design (DD) has revolutionized the construction industry, enabling professionals to create, visualize, and manage detailed digital models of buildings and infrastructure. The implementation of DD, also known as Building Information Modeling (BIM), has brought numerous benefits to construction projects, including improved collaboration, enhanced visualization, optimized planning, and reduced errors.
Throughout this article, we explored the definition of DD in construction and its various types, showcasing its importance and the benefits it offers. DD has proven to be essential in achieving accurate designs, efficient clash detection, and streamlined construction processes. It has facilitated better communication and coordination among stakeholders, resulting in successful project outcomes.
Nevertheless, DD implementation comes with challenges and risks that need to be addressed. These challenges include the learning curve, data accuracy, compatibility issues, and legal considerations. By following best practices, construction professionals can mitigate these risks and optimize the benefits of DD.
Looking into the future, we anticipate exciting advancements in DD for construction. Artificial intelligence, machine learning, IoT integration, VR/AR, generative design, cloud computing, robotics, and advanced data analytics will continue to reshape the construction landscape. These innovations will enhance collaboration, automate processes, improve design optimization, and allow for more sustainable and efficient construction practices.
In conclusion, the adoption and utilization of DD in construction is no longer a luxury but a necessity for staying competitive and delivering successful projects. By embracing the power of DD and staying abreast of the latest trends and innovations, the construction industry can continue to evolve and thrive in the digital age.
Frequently Asked Questions about What Does DD Mean In Construction
Was this page helpful?
At Storables.com, we guarantee accurate and reliable information. Our content, validated by Expert Board Contributors, is crafted following stringent Editorial Policies. We're committed to providing you with well-researched, expert-backed insights for all your informational needs.
0 thoughts on “What Does DD Mean In Construction”