Home>diy>Building & Construction>What Does QC Mean In Construction
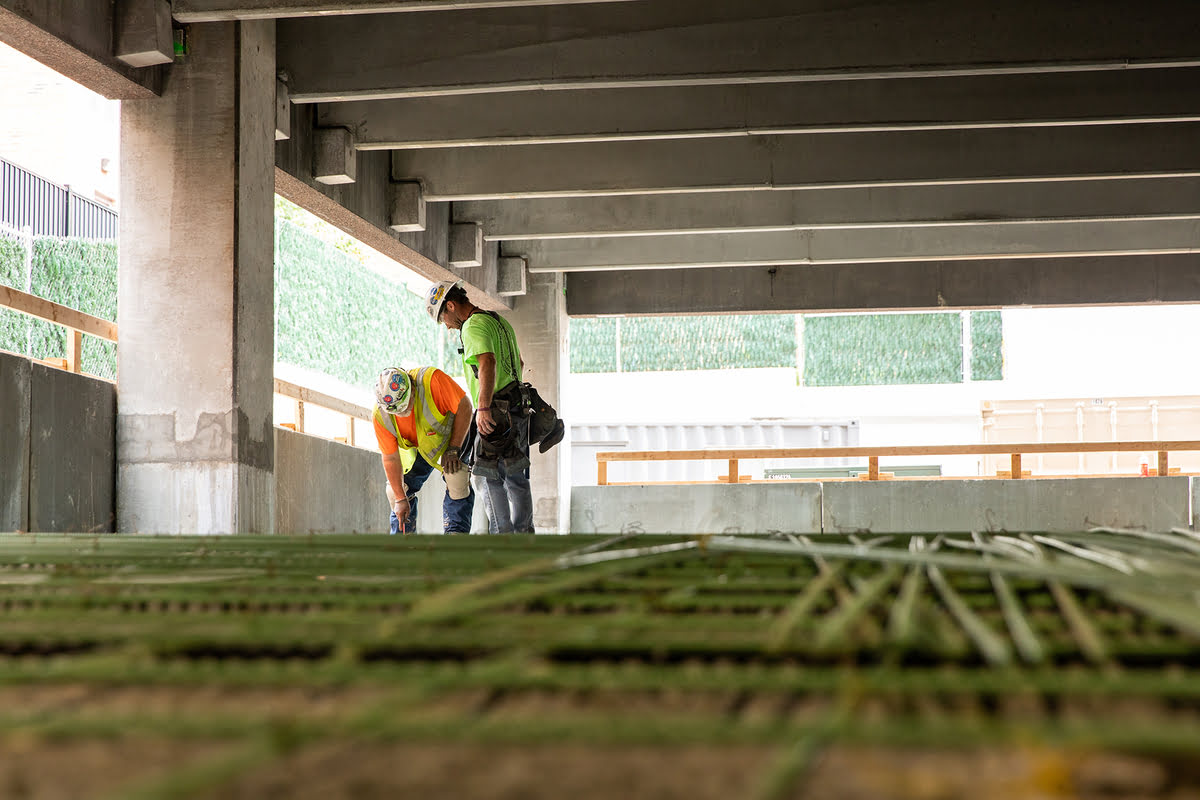
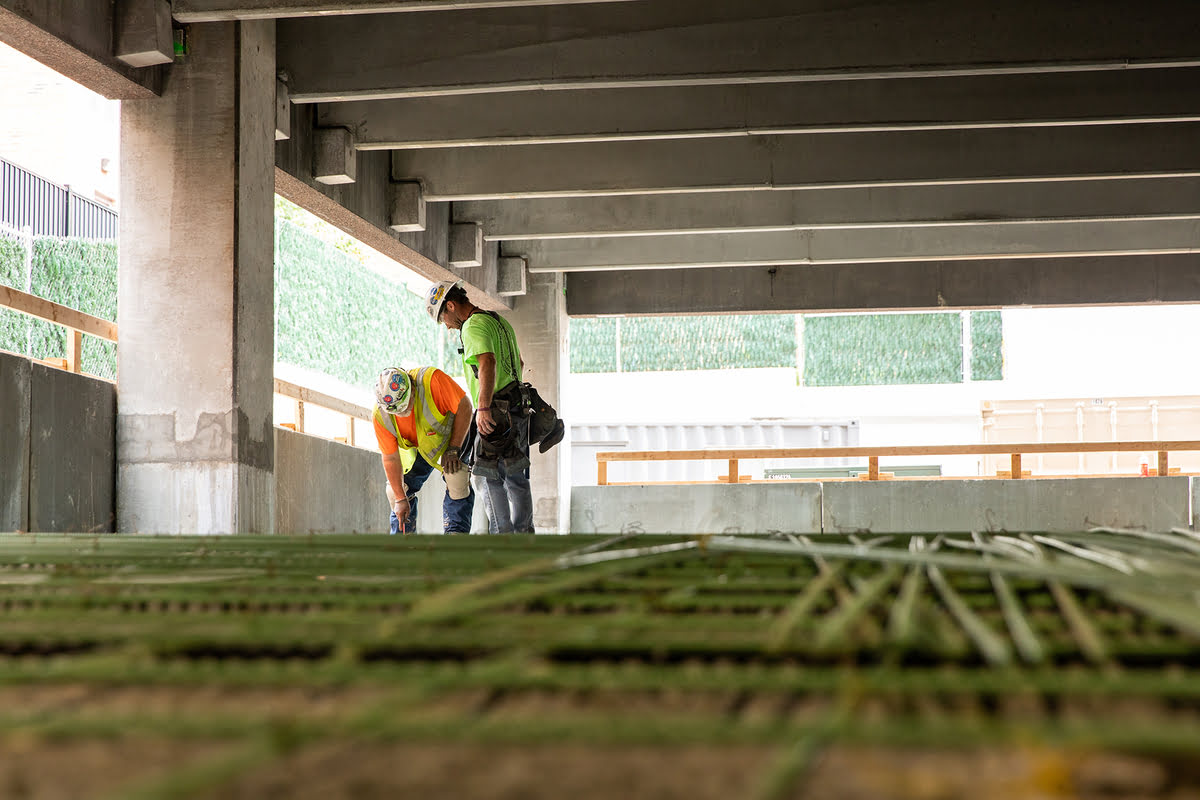
Building & Construction
What Does QC Mean In Construction
Modified: March 6, 2024
Find out the meaning of QC in construction and how it relates to building-construction. Explore the importance of quality control in the construction industry.
(Many of the links in this article redirect to a specific reviewed product. Your purchase of these products through affiliate links helps to generate commission for Storables.com, at no extra cost. Learn more)
Introduction
Welcome to the world of construction, where the beauty and functionality of buildings are brought to life. As any seasoned builder will tell you, constructing a building is no easy feat. It requires meticulous planning, skilled craftsmanship, and a commitment to delivering top-notch quality. In the realm of construction, one term you may come across is “QC,” which stands for Quality Control.
QC plays a vital role in ensuring that construction projects meet the highest standards of quality. It involves systematic processes and procedures that monitor, assess, and verify various aspects of a construction project to ensure it adheres to industry regulations and client requirements.
In this article, we will explore the definition of QC in construction, discuss its importance, delve into the various processes involved, and highlight the role of QC in ensuring project quality. We will also explore the benefits of implementing QC, the challenges it presents, and best practices for effective QC in the construction industry.
So, put on your hard hat and join us on this journey to discover the world of QC in construction!
Key Takeaways:
- Quality Control (QC) in construction ensures buildings meet high standards, prevent errors, and prioritize safety. It involves checks, inspections, and audits to deliver top-notch projects that stand the test of time.
- Implementing QC processes offers benefits like enhanced project quality, cost savings, improved safety, and client satisfaction. Despite challenges, best practices like regular inspections and continual improvement drive success in construction QC.
Read more: What Does QA/QC Mean In Construction
Definition of QC in Construction
Quality Control (QC) in construction refers to the systematic processes, measures, and activities undertaken to ensure that the construction project is executed with precision and adheres to specific quality standards. It is an essential component of construction management that focuses on preventing defects, reducing errors, and enhancing the overall quality of the construction project.
QC involves a series of checks, inspections, and tests conducted at various stages of the construction process to ensure that the materials, workmanship, and final product meet the required specifications and industry standards. These checks are performed by trained professionals who have a deep understanding of construction processes and quality metrics.
The primary objective of QC is to identify and rectify any deviations, discrepancies, or non-compliance with quality standards before they become larger issues. By conducting rigorous quality checks, construction teams can minimize rework, avoid costly delays, and deliver a safe and high-quality end result for clients.
QC in construction encompasses several key aspects, such as:
- Materials Testing: This involves examining and testing the materials used in the construction process, such as concrete, steel, bricks, and other building components, to ensure they meet the required specifications and standards.
- Inspections: Inspections are conducted to assess the quality of workmanship, installations, and adherence to design plans. This includes structural inspections, electrical inspections, plumbing inspections, and more.
- Documentation and Record-keeping: Proper documentation of all quality-related activities, including test results, inspection reports, and certifications, helps track the progress and compliance of the construction project.
- Quality Audits: Regular audits are conducted to evaluate the effectiveness of the QC processes, identify areas for improvement, and ensure ongoing compliance with quality standards.
Overall, QC in construction is a proactive approach to quality management that aims to uphold the highest standards throughout the construction process. By implementing robust QC processes, construction companies can build trust with their clients, enhance their reputation in the industry, and deliver projects that stand the test of time.
Importance of QC in Construction
Quality Control (QC) is of utmost importance in the construction industry. It ensures that projects are built to meet the required standards, specifications, and regulations. Let’s delve into the key reasons why QC holds such significance in construction:
1. Ensuring Safety
The safety of occupants, workers, and the general public is paramount in construction. QC processes help identify potential hazards and ensure that construction projects are built to withstand environmental factors and adhere to safety regulations. By implementing rigorous QC measures, construction companies can minimize the risk of accidents, property damage, and structural failures.
2. Meeting Quality Standards
QC is crucial for meeting quality standards set by regulatory bodies, industry organizations, and clients. It ensures that materials, workmanship, installations, and processes align with the specified standards. By consistently adhering to these standards, construction companies can deliver high-quality projects that meet or exceed client expectations.
Read more: What Is QA/QC In Construction
3. Minimizing Rework and Cost Overruns
Implementing QC processes can help identify and rectify issues early in the construction process, minimizing the need for rework. By catching and addressing issues promptly, construction companies can save time, money, and resources. QC also helps in preventing cost overruns by ensuring that projects are executed efficiently, reducing the risk of unexpected expenses caused by poor quality workmanship or materials.
4. Enhancing Reputation and Building Trust
A strong commitment to QC demonstrates a construction company’s dedication to delivering high-quality projects. By consistently meeting quality standards, construction companies can build a positive reputation in the industry, earn client trust, and attract new customers. Satisfied clients are more likely to give positive referrals and engage in repeat business.
5. Ensuring Compliance with Regulations
The construction industry is subject to various regulations and codes that are in place to ensure safety, sustainability, and environmental protection. QC processes help ensure that construction projects comply with these regulations, avoiding potential legal issues and penalties. By staying on top of regulatory requirements, construction companies can ensure their projects are legally compliant and environmentally friendly.
6. Improving Efficiency and Productivity
QC processes promote efficiency and productivity by identifying bottlenecks, streamlining workflows, and improving communication within the construction team. By implementing quality checks and measures, construction companies can optimize their processes, reduce delays, and deliver projects on time and within budget.
In summary, QC in construction is essential for ensuring safety, meeting quality standards, minimizing rework and cost overruns, enhancing reputation, ensuring compliance with regulations, and improving overall efficiency. By prioritizing QC, construction companies can create a competitive advantage, provide value to their clients, and contribute to the growth and success of the industry as a whole.
QC Processes in Construction
Implementing effective Quality Control (QC) processes is necessary to ensure that construction projects meet the highest standards of quality. These processes involve various steps and activities that are carried out at different stages of the construction project. Let’s explore some of the key QC processes in construction:
1. Pre-Construction QC
The QC process begins even before the construction phase. During the pre-construction stage, extensive planning and preparation take place to ensure that quality is maintained throughout the project. This includes conducting thorough site inspections, analyzing soil conditions, reviewing design plans, and verifying the availability and quality of construction materials.
2. Material Testing and Validation
One of the key aspects of QC is the testing and validation of construction materials. Samples of materials such as concrete, steel, asphalt, and aggregates are tested at accredited laboratories to ensure they meet the required quality standards and specifications. Material testing helps identify any potential issues or deficiencies and ensures that only high-quality materials are used in the construction process.
3. Inspection and Quality Checks
Regular inspections and quality checks play a critical role in QC. Trained inspectors assess various aspects of the construction project, including workmanship, installations, and compliance with design plans and regulatory requirements. Inspections are conducted at different stages of the construction process, such as foundation, framing, electrical work, plumbing, and finishing. By identifying and addressing any deviations or deficiencies early on, construction teams can maintain quality and avoid costly rework.
Read more: What Does Masonry Construction Mean
4. Documentation and Record-Keeping
Effective documentation and record-keeping are essential components of QC processes. Detailed documentation includes recording test results, inspection reports, certifications, and any changes or modifications made during the construction process. This documentation helps track project progress, identify potential issues, and ensure compliance with quality standards and industry regulations.
5. Quality Audits
Periodic quality audits are conducted to evaluate the effectiveness of the QC processes. These audits involve a thorough review of the construction project to assess compliance with quality standards, adherence to regulatory requirements, and the overall effectiveness of the QC processes. Audits help identify areas for improvement, implement corrective measures, and ensure ongoing compliance with quality standards.
6. Client Feedback and Satisfaction
QC processes also incorporate client feedback and satisfaction measurements. Construction companies collect feedback from clients to assess their satisfaction levels with the project quality and overall experience. This feedback provides valuable insights for improving QC processes and enhancing customer satisfaction in future projects.
By consistently implementing these QC processes, construction companies can ensure that the construction project progresses smoothly, adheres to quality standards, and meets or exceeds client expectations.
Role of QC in Ensuring Project Quality
Quality Control (QC) plays a crucial role in ensuring project quality in the construction industry. It involves a systematic approach to monitor and manage various aspects of a construction project to ensure that it meets the highest standards. Let’s explore the key roles of QC in ensuring project quality:
Read more: What Does ISO Mean In Construction
1. Compliance with Standards and Specifications
QC ensures that the construction project complies with the required standards, specifications, and industry regulations. This includes adherence to building codes, safety standards, environmental regulations, and other relevant guidelines. By implementing QC processes, construction teams can identify any deviations from the standards and take corrective actions to ensure compliance.
2. Early Identification and Resolution of Issues
QC processes involve regular inspections, checks, and tests to identify any issues or discrepancies early in the construction process. By detecting problems at an early stage, construction teams can take prompt corrective actions, minimizing the impact on project quality. This includes addressing design flaws, material deficiencies, workmanship issues, and other potential risks that may compromise the project’s quality.
3. Mitigating Risks and Ensuring Safety
QC is integral to ensuring the safety of a construction project. By implementing safety protocols and conducting regular inspections, QC processes help identify and address potential safety hazards. This includes assessing structural integrity, electrical systems, fire safety measures, and other critical components to mitigate risks and ensure a safe working environment for construction workers and future occupants of the building.
4. Maintaining Consistency and Quality Standards
QC plays a significant role in maintaining consistency and upholding quality standards throughout the construction project. By implementing standardized QC processes, construction teams can ensure that all workmanship, materials, and installations meet the required specifications. This consistency helps achieve uniform quality across the project, regardless of the different contractors, subcontractors, or project phases involved.
Read more: What Does Furring Mean In Construction
5. Enhancing Client Satisfaction
One of the primary goals of QC is to achieve client satisfaction by delivering a high-quality project that meets or exceeds their expectations. By implementing robust QC processes, construction companies can ensure that the project is completed according to the agreed-upon standards, specifications, and timeline. This, in turn, enhances client satisfaction and fosters long-term relationships, which are essential for the success and growth of the construction business.
6. Continual Improvement
QC processes involve regular evaluations and audits to identify areas for improvement. By analyzing past projects, QC teams can identify trends, best practices, and areas of improvement to refine their processes and enhance project quality in future endeavors. Continual improvement is a core principle of QC, allowing construction companies to stay updated with industry advancements and deliver even better quality projects.
In summary, QC plays a vital role in ensuring project quality by ensuring compliance with standards and specifications, early identification and resolution of issues, mitigating risks, maintaining consistency, enhancing client satisfaction, and facilitating continual improvement. By prioritizing QC, construction companies can build a reputation for excellence, foster client trust, and deliver projects that surpass expectations.
Benefits of Implementing QC in Construction
Implementing Quality Control (QC) processes in construction offers numerous benefits for both construction companies and clients. Let’s explore some of the key advantages of incorporating QC practices into construction projects:
1. Enhanced Project Quality
The primary benefit of QC is the assurance of enhanced project quality. By implementing stringent QC processes, construction companies can ensure that the project meets or exceeds the required standards, specifications, and regulations. This results in a high-quality end product that is safe, durable, and meets client expectations.
Read more: What Does “Level” Mean In Construction
2. Reduced Rework and Cost Savings
QC processes help minimize rework by identifying and addressing issues early in the construction process. By catching problems before they escalate, construction companies can save time, money, and resources that would otherwise be wasted on rectifying errors. Reducing rework contributes to cost savings and allows projects to be completed more efficiently.
3. Improved Safety and Risk Mitigation
QC plays a key role in ensuring the safety of the construction project. By implementing safety protocols, conducting regular inspections, and identifying potential hazards, construction teams can mitigate risks and create a safer working environment. This helps protect workers, occupants, and the public from accidents, injuries, and property damage.
4. Client Satisfaction and Trust
QC processes contribute to client satisfaction and build trust. By delivering high-quality projects that meet the agreed-upon standards, construction companies can exceed client expectations and foster long-term relationships. Satisfied clients are more likely to provide positive referrals and engage in repeat business, helping to grow the reputation and success of the construction company.
5. Competitive Advantage
Implementing QC processes gives construction companies a competitive edge. Quality workmanship, attention to detail, and a commitment to delivering top-notch projects set companies apart from the competition. Clients are more likely to choose a construction company with a proven track record of QC practices, as it provides a level of assurance and reliability.
Read more: What Does NOC Mean In Construction
6. Compliance with Regulations
QC ensures compliance with industry regulations, building codes, and environmental standards. By adhering to these requirements, construction companies avoid potential legal issues, penalties, or delays caused by non-compliance. Compliance with regulations also contributes to the safety, sustainability, and overall reputation of the construction project.
7. Continual Improvement
QC processes facilitate continual improvement within construction companies. Regular evaluations, audits, and feedback loops provide insights into areas for improvement. By analyzing past projects and implementing lessons learned, construction companies can refine their processes, enhance their efficiency, and deliver even better quality projects.
In summary, implementing QC in construction provides numerous benefits, including enhanced project quality, reduced rework and cost savings, improved safety and risk mitigation, client satisfaction and trust, competitive advantage, compliance with regulations, and opportunities for continual improvement. Investing in QC practices is essential for construction companies that strive for excellence and desire to deliver projects that exemplify quality and meet client expectations.
Challenges and Limitations of QC in Construction
Implementing Quality Control (QC) processes in construction can present certain challenges and limitations that need to be addressed to ensure effective project execution. Let’s explore some of the common challenges and limitations of QC in construction:
1. Complexity of Construction Projects
Construction projects can be complex and multifaceted, involving numerous stakeholders, intricate designs, and tight timelines. This complexity can make it challenging to implement QC processes consistently and thoroughly throughout the project. Coordinating quality checks across different phases, trades, and contractors requires robust planning and coordination.
Read more: What Does Turnkey Mean In Construction
2. Cost and Resource Constraints
Implementing QC practices can require additional resources, including hiring trained personnel, investing in testing equipment, and conducting regular inspections. The cost of implementing QC measures can pose a challenge, particularly for small and budget-constrained construction companies. Balancing the need for quality with budgetary constraints is a common limitation in QC implementation.
3. Time Constraints and Schedule Pressures
Construction projects often operate under strict timelines and schedule pressures. This can make it challenging to dedicate sufficient time for comprehensive QC processes. The need to meet deadlines and ensure project completion on time can sometimes result in shortcuts or reduced focus on QC, leading to potential quality issues.
4. Fragmented Supply Chains and Contractors
Construction projects typically involve multiple contractors, subcontractors, and suppliers, leading to fragmented supply chains. Coordinating quality standards and ensuring consistency across different entities can be challenging. Communication gaps, varying levels of expertise, and the enforcement of quality standards among subcontractors can pose challenges to maintaining overall project quality.
5. Human Error and Workmanship Issues
Human error and workmanship issues are common challenges in construction. Despite the implementation of QC processes, errors can still occur due to oversight, lack of training, or negligence. Ensuring a high level of workmanship across all trades and addressing human error through ongoing training and quality checks is a continuous challenge in QC implementation.
Read more: What Does Subgrade Mean In Construction
6. Evolving Regulations and Standards
Construction industry regulations and standards are subject to change and updates. Staying up-to-date with evolving regulations and ensuring compliance can be a challenge for construction companies. Adapting QC processes to align with new standards and regulatory requirements requires continuous education and monitoring.
7. Subjectivity and Interpretation
QC processes in construction often involve subjective assessments and interpretations. Determining the acceptability of workmanship, identifying defects, or assessing compliance with design plans can have varying interpretations. Ensuring consistency in subjective assessments and maintaining objectivity are challenges in QC implementation.
While these challenges and limitations exist, they can be overcome through careful planning, effective communication, ongoing training, and a commitment to quality. By recognizing these challenges and addressing them proactively, construction companies can improve their QC processes and successfully deliver high-quality projects.
Best Practices for Effective QC in Construction
Implementing effective Quality Control (QC) practices is essential for ensuring the highest standards of quality in construction projects. Here are some best practices to consider for effective QC implementation:
1. Develop a Comprehensive QC Plan
Start by developing a comprehensive QC plan that outlines the specific QC processes, procedures, and standards to be implemented throughout the project. This plan should incorporate all relevant industry regulations, client requirements, and quality standards. Clearly define roles and responsibilities, along with the timeline for each phase of the project.
Read more: What Does Soffit Mean In Construction
2. Training and Education
Educate and train all personnel involved in the construction project on QC procedures, industry standards, and best practices. Provide ongoing training to ensure that all employees are up-to-date with the latest QC techniques, methodologies, and regulatory changes. This helps ensure that everyone understands their roles and responsibilities in maintaining project quality.
3. Implement Regular Inspections
Conduct regular inspections at various stages of the construction project to assess workmanship, installations, and compliance with design plans and regulatory requirements. Inspections should be carried out by trained personnel with expertise in the specific area under review. Develop a checklist or template to ensure consistency and comprehensiveness during inspections.
4. Material Testing and Validation
Implement a thorough material testing and validation process to ensure that all construction materials meet the required quality standards and specifications. Partner with accredited laboratories or suppliers to conduct these tests and keep proper documentation of the results. Strictly adhere to material acceptance criteria and reject any materials that do not meet the specified requirements.
5. Document and Track QC Activities
Maintain comprehensive documentation of all QC activities, including inspection reports, test results, certifications, and changes made during the construction process. Use digital tools and software to track and manage these documents effectively. This documentation serves as evidence of compliance and helps identify areas for improvement.
Read more: What Does “FRP” Mean In Construction
6. Foster Collaboration and Communication
Promote collaboration and open communication among all stakeholders involved in the construction project. Encourage regular meetings, feedback sessions, and quality assurance forums to discuss QC findings, address issues, and implement corrective actions. Effective communication helps ensure that all parties are aligned with project goals and quality standards.
7. Continual Improvement and Lessons Learned
Implement a system for capturing lessons learned throughout the project and sharing them with the team. Conduct post-project reviews to analyze successes and areas for improvement. Use these insights to refine QC processes, update the QC plan, and enhance project quality in future endeavors.
8. Implement Quality Audits
Regularly conduct quality audits to assess the effectiveness of the QC processes and ensure ongoing compliance with quality standards. These audits should be carried out by impartial auditors who have a deep understanding of QC practices. Use the findings from these audits to identify areas for improvement and implement corrective actions.
By implementing these best practices, construction companies can establish a strong foundation for effective QC in their projects. This not only ensures project quality but also enhances client satisfaction, fosters trust, and contributes to the overall success and growth of the organization.
Conclusion
Quality Control (QC) plays a vital role in the construction industry, ensuring that projects are built to meet the highest standards of quality and safety. By implementing effective QC processes, construction companies can achieve enhanced project quality, reduced rework, improved safety measures, and increased client satisfaction.
In this article, we explored the definition of QC in construction and the importance it holds in ensuring project excellence. We discussed various QC processes, including material testing, inspections, documentation, and quality audits that are integral to maintaining project quality throughout the construction journey.
We also highlighted the key roles of QC in construction – ensuring compliance with standards, early issue identification, risk mitigation, and client satisfaction. Moreover, we delved into the benefits of implementing QC practices, such as enhanced project quality, cost savings, improved safety measures, and a competitive advantage in the industry.
The article also covered the challenges and limitations in QC implementation, including the complexity of construction projects, cost constraints, time pressures, and the need to address human error. Despite these challenges, construction companies can overcome them through careful planning, resource allocation, ongoing training, and a commitment to continual improvement.
To achieve effective QC, construction companies should follow best practices, including developing a comprehensive QC plan, providing training and education, conducting regular inspections, implementing material testing, documenting QC activities, fostering collaboration and communication, and conducting quality audits.
In conclusion, QC in construction is crucial for delivering high-quality projects that meet industry regulations, client expectations, and safety standards. By prioritizing and investing in QC processes, construction companies can build a strong reputation, foster client trust, and contribute to the growth and success of the industry as a whole.
Frequently Asked Questions about What Does QC Mean In Construction
Was this page helpful?
At Storables.com, we guarantee accurate and reliable information. Our content, validated by Expert Board Contributors, is crafted following stringent Editorial Policies. We're committed to providing you with well-researched, expert-backed insights for all your informational needs.
0 thoughts on “What Does QC Mean In Construction”