Home>diy>Building & Construction>What Is A JHA In Construction
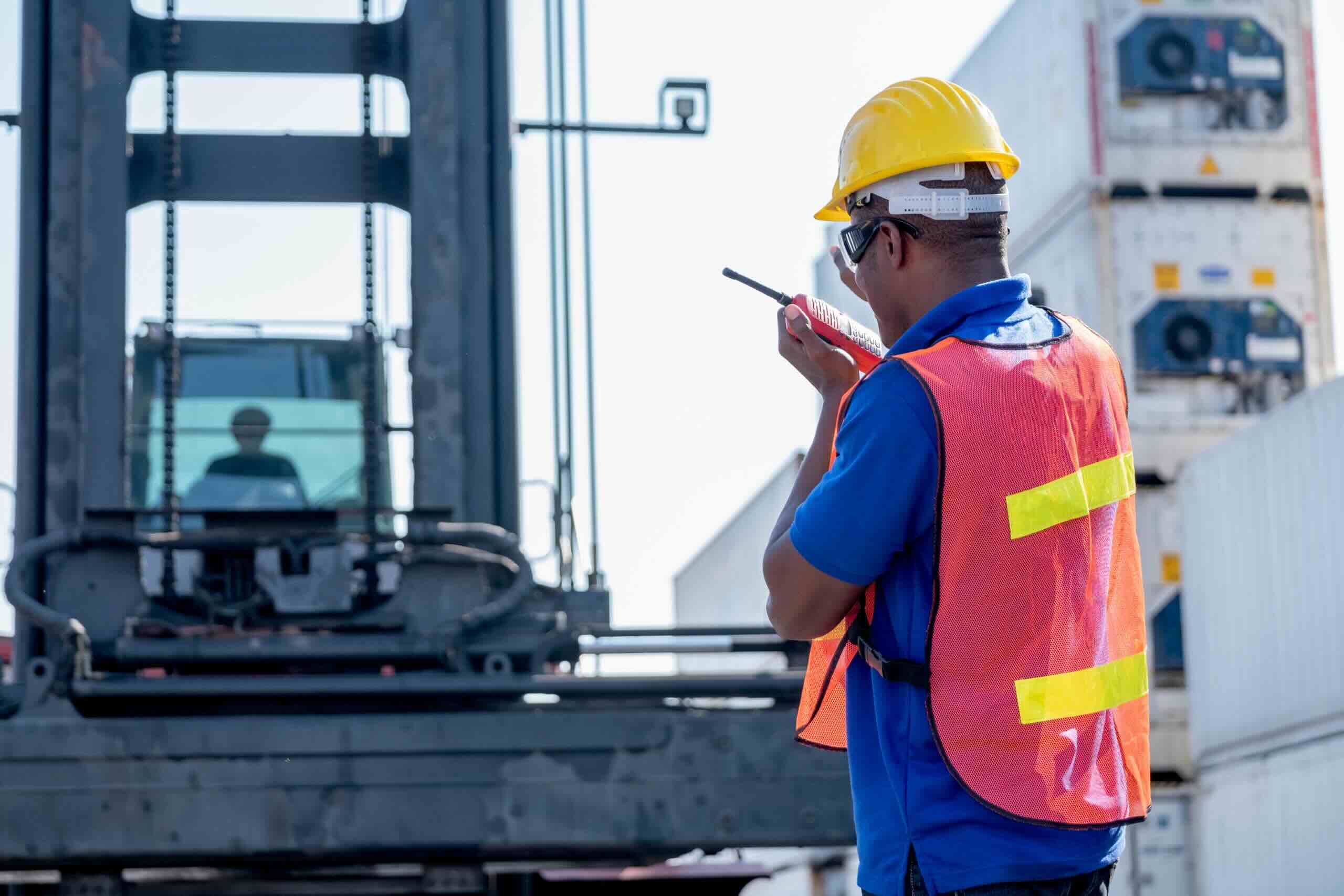
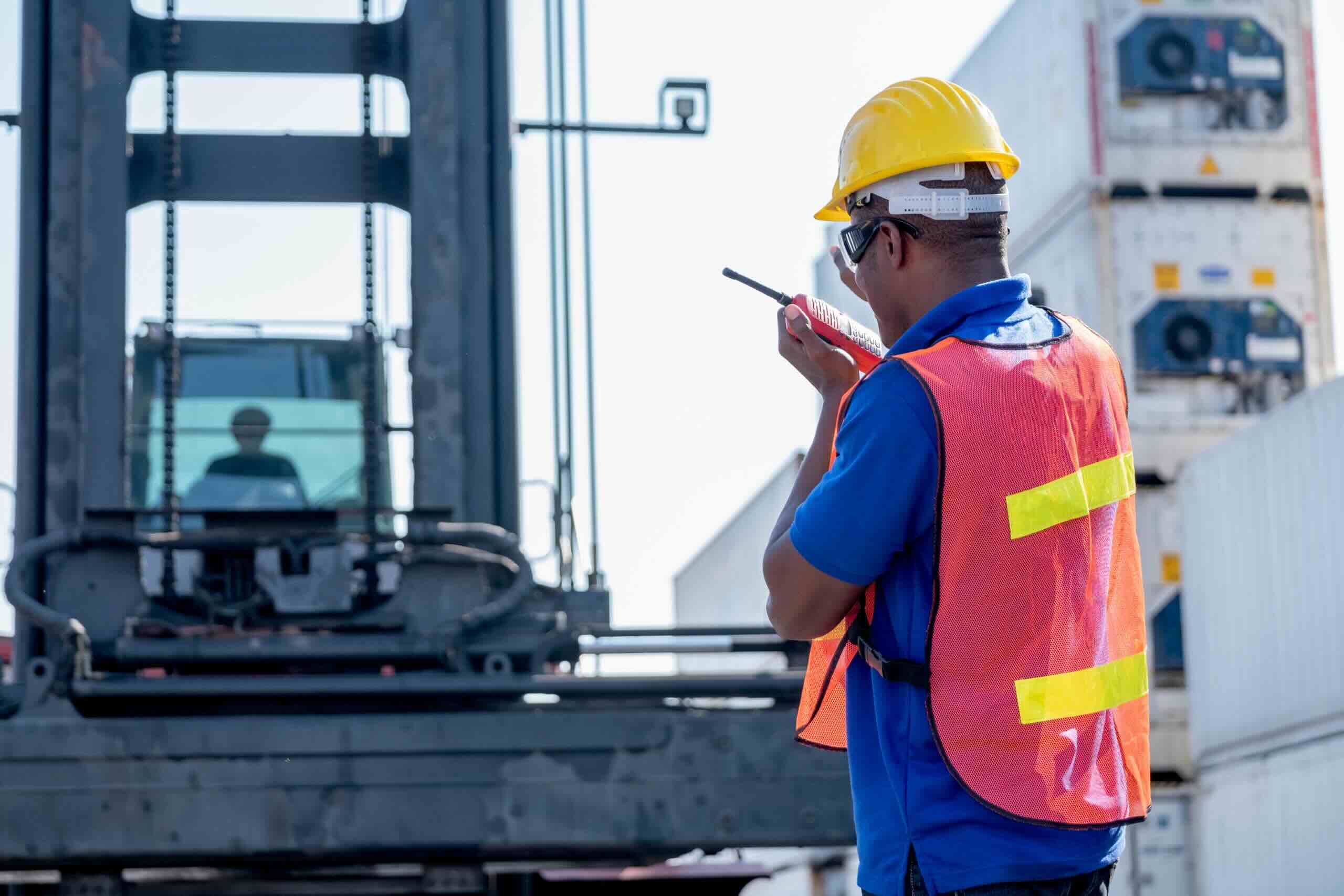
Building & Construction
What Is A JHA In Construction
Modified: December 7, 2023
Learn about the importance of Job Hazard Analysis (JHA) in building construction. Ensure safety by identifying potential risks and implementing preventive measures.
(Many of the links in this article redirect to a specific reviewed product. Your purchase of these products through affiliate links helps to generate commission for Storables.com, at no extra cost. Learn more)
Introduction
In the field of construction, ensuring the safety of workers and minimizing risks is of paramount importance. Construction sites are inherently hazardous environments, and without proper precautions, accidents can occur, resulting in injuries or even fatalities. This is where a Job Hazard Analysis (JHA) comes into play. A JHA is a critical tool used to identify and manage potential hazards in construction projects.
By conducting a JHA, construction companies can proactively assess the risks associated with specific tasks and implement measures to mitigate them. This proactive approach not only promotes the well-being of workers but also helps to prevent costly and time-consuming accidents and delays on job sites.
It is important to understand the definition, significance, and key components of a JHA in order to fully comprehend its benefits and how it can be effectively implemented in the construction industry. This article aims to provide a comprehensive overview of JHA in construction and shed light on its importance and implementation procedures.
Key Takeaways:
- Prioritizing JHA in construction ensures worker safety, prevents accidents, and promotes a proactive hazard identification culture, ultimately leading to successful and profitable outcomes.
- Overcoming JHA challenges through commitment, worker engagement, regular updates, and fostering a safety culture enhances its effectiveness in creating a safer work environment.
Read more: What Is Jha In Construction
Definition of JHA
A Job Hazard Analysis (JHA), also known as a Job Safety Analysis (JSA), is a systematic process used to identify potential hazards associated with specific tasks or jobs within a construction project. It involves breaking down the job into individual steps and analyzing each step to identify potential hazards, assess the associated risks, and determine appropriate control measures to prevent accidents.
The primary goal of a JHA is to ensure that workers understand the hazards associated with their tasks and are equipped with the necessary knowledge and protective measures to perform their jobs safely. It provides a detailed roadmap for safely executing job tasks, reducing the likelihood of accidents and injuries.
A JHA typically considers various factors, such as the nature of the work, tools and equipment used, the work environment, and worker capabilities. It takes into account potential hazards such as falls, electrical hazards, chemical exposures, repetitive motions, and other risks that may arise during different stages of a construction project.
While a JHA is commonly used in the construction industry, it can also be implemented in other sectors where hazardous tasks are performed, such as manufacturing, oil and gas, and transportation. It is an essential component of any robust safety management system and is an OSHA (Occupational Safety and Health Administration) requirement in many countries.
It is crucial to conduct a JHA whenever a new job or task is introduced, or when changes occur in processes, equipment, or work environment that may affect the safety of workers. Regularly reviewing and updating JHA documents ensures that they remain accurate and effective in protecting workers from potential hazards.
By diligently conducting JHA, construction companies can demonstrate their commitment to worker safety, comply with legal and regulatory requirements, and create a culture of safety awareness within the organization.
Importance of JHA in Construction
The implementation of a comprehensive Job Hazard Analysis (JHA) is crucial in the construction industry due to the inherent risks and hazards involved in construction projects. Here are several reasons why JHA holds significant importance:
- Identification of Potential Hazards: Construction sites are dynamic environments with multiple potential hazards. A JHA enables the identification of specific hazards associated with each task or job, allowing for targeted risk mitigation measures. By identifying and addressing hazards proactively, construction companies can prevent accidents and injuries.
- Worker Safety: The primary objective of JHA is to ensure the safety and well-being of workers. By analyzing specific job tasks, a JHA enables the development and implementation of safety protocols, procedures, and protective measures to minimize the risk of injuries or illnesses.
- Compliance with Regulations: Many countries have strict regulations and compliance requirements related to workplace safety. Conducting a JHA helps construction companies ensure compliance with these regulations, avoiding costly penalties and legal issues.
- Enhanced Productivity: Implementing a JHA can lead to increased productivity on construction sites. By identifying potential hazards and designing efficient work processes and safety protocols, workers can perform their tasks with confidence and focus, resulting in improved productivity levels.
- Prevention of Accidents and Delays: Accidents on construction sites can lead to delays in project timelines and increased costs. By identifying hazards and implementing preventive measures through JHA, construction companies can minimize the risk of accidents, ensuring projects are completed on time and within budget.
- Improved Communication and Training: JHA requires the involvement of workers, supervisors, and other stakeholders in the analysis process. This facilitates effective communication and collaboration, ensuring that workers are aware of the risks and understand the necessary precautions. Additionally, JHA identifies the need for specific training requirements, enabling focused training programs for workers.
In summary, JHA plays a vital role in maintaining a safe work environment, promoting worker well-being, complying with regulations, and preventing accidents and delays on construction sites. By prioritizing JHA, construction companies demonstrate their commitment to safety and create a culture of proactive hazard identification and risk mitigation.
Key Components of a JHA
A comprehensive Job Hazard Analysis (JHA) consists of several key components that form the foundation of the analysis process. Understanding these components is essential for conducting an effective JHA in the construction industry:
- Job Identification: The first step in a JHA is to clearly identify the job or task being analyzed. This includes specifying the work area, job title, and a detailed description of the task. It is important to define the scope and boundaries of the job to ensure accurate hazard identification.
- Job Steps: Once the job is identified, it is broken down into individual steps or actions required to complete the task. Each step should be well-defined and sequential, allowing for a detailed analysis of potential hazards associated with each specific action.
- Hazard Identification: During this stage, potential hazards associated with each job step are identified. Hazards can include physical, chemical, biological, and ergonomic factors. It is essential to consider all possible hazards and their potential consequences on worker safety.
- Risk Assessment: After identifying hazards, the next step is to assess the level of risk associated with each hazard. This involves evaluating the likelihood and severity of potential injuries or incidents. Risk assessment provides a basis for determining appropriate control measures to minimize or eliminate hazards.
- Control Measures: Once hazards and associated risks are identified, control measures are implemented to mitigate the risks. This can include engineering controls, administrative controls, and personal protective equipment (PPE). The goal is to eliminate or minimize the hazards to ensure worker safety.
- Documentation: A JHA should be properly documented to ensure clarity and accountability. Documentation includes recording all steps of the job, identified hazards, risk assessments, and control measures. This documentation serves as a reference for future job analysis, training, and compliance purposes.
- Communication and Training: Effective communication is crucial when implementing a JHA. All stakeholders involved in the job, including workers, supervisors, and management, need to be informed about the hazards and control measures identified during the JHA process. Additionally, specific training should be provided to ensure workers understand the potential hazards and safety protocols.
- Periodic Review and Updates: A JHA is not a one-time process. It should be regularly reviewed and updated to reflect any changes in the job, processes, or work environment. Regular review ensures that the JHA remains current and effective in identifying and controlling hazards.
By incorporating these key components into the JHA process, construction companies can systematically analyze job tasks, identify hazards, assess risks, implement control measures, and ensure continuous improvement in worker safety and health.
Steps to Conduct a JHA
Conducting a Job Hazard Analysis (JHA) is a systematic process that involves several steps to ensure a comprehensive analysis of potential hazards and their associated risks. By following these steps, construction companies can effectively identify and mitigate risks, ensuring the safety of workers on the job site:
- Select the Job: Choose the specific job or task that will be analyzed. This can be a specific construction activity, such as operating heavy machinery or working at heights.
- Break Down the Job into Steps: Clearly define the sequence of steps required to complete the job or task. Each step should be concise and easy to understand. For complex jobs, it may be necessary to break them down into subtasks.
- Identify Hazards: Analyze each step and identify potential hazards associated with the task. This can include physical hazards, such as falls or exposure to harmful substances, as well as ergonomic or environmental hazards.
- Assess Risks: Evaluate the likelihood and severity of potential accidents or injuries arising from each hazard identified. This assessment helps prioritize risks and determine the appropriate control measures needed.
- Implement Control Measures: Develop and implement control measures to eliminate or minimize the identified hazards. This can involve engineering controls, administrative controls, and the use of personal protective equipment (PPE).
- Communicate and Train: Communicate the findings of the JHA to all individuals involved in the job, including workers, supervisors, and management. Provide clear instructions on the required safety protocols and ensure that workers are properly trained.
- Monitor and Review: Continuously monitor the effectiveness of the implemented control measures. Regularly review the JHA to ensure it remains up to date and reflects any changes in the job or work environment.
- Document and Maintain Records: Record all aspects of the JHA, including job steps, identified hazards, risk assessments, and control measures. Documentation serves as a reference for future job analysis, training, and compliance purposes.
- Periodic Review and Updates: Review and update the JHA periodically, especially when there are changes to the job, work processes, or regulations. This ensures that the JHA remains effective in identifying and controlling hazards.
By following these steps, construction companies can systematically analyze job tasks, identify hazards, assess risks, implement control measures, and ensure continuous improvement in worker safety. Conducting a JHA helps create a safer work environment, reduces the likelihood of accidents and injuries, and promotes a culture of safety awareness on construction sites.
When conducting a Job Hazard Analysis (JHA) in construction, be sure to involve workers who are familiar with the tasks being analyzed. Their input is crucial for identifying potential hazards and developing effective safety measures.
Read more: What Is Construction
Benefits of Implementing JHA in Construction
Implementing a Job Hazard Analysis (JHA) in the construction industry offers numerous benefits that contribute to a safer and more productive work environment. Here are several key advantages of incorporating JHA into construction projects:
- Enhanced Worker Safety: The primary benefit of JHA is improved worker safety. By systematically identifying and mitigating potential hazards, construction companies can provide workers with the necessary knowledge and protective measures to perform their tasks safely. This reduces the risk of accidents, injuries, and illnesses on the job site.
- Accident Prevention: JHA plays a vital role in accident prevention. By proactively identifying hazards and implementing control measures, construction companies can significantly reduce the likelihood of accidents. This leads to a safer work environment and decreases the potential for costly insurance claims, legal issues, and project delays.
- Increased Efficiency and Productivity: JHA helps improve work processes and job efficiency. By analyzing job tasks and identifying potential hazards, construction companies can develop more efficient work methods and implement appropriate safety protocols. This leads to streamlined operations, decreased downtime, and increased productivity.
- Compliance with Regulations: The construction industry is subject to various safety regulations and standards. Implementing JHA ensures compliance with these regulations, protecting both workers and the company from legal and regulatory penalties. By documenting the JHA process, companies can demonstrate their commitment to safety and adherence to industry standards.
- Quality Control: JHA goes beyond identifying hazards; it also helps identify areas in need of improvement and ensures the quality of work. By assessing risks and implementing control measures, construction companies can prevent errors, defects, and rework. This enhances the overall quality of the project and reduces the need for costly repairs or corrections.
- Improved Communication and Collaboration: JHA requires input from all stakeholders, including workers, supervisors, and management. This promotes effective communication and collaboration, creating a shared understanding of the risks involved in specific tasks. It fosters a culture of safety awareness and encourages open dialogue regarding safety concerns and suggestions for improvement.
- Cost Savings: Investing in JHA can lead to long-term cost savings. By preventing accidents and minimizing workplace injuries, companies can reduce medical costs, workers’ compensation claims, and equipment damage. Additionally, the prevention of project delays and disruptions translates into significant cost savings over time.
In summary, implementing JHA in construction projects offers a range of benefits, including improved worker safety, accident prevention, increased efficiency and productivity, compliance with regulations, enhanced quality control, improved communication, and cost savings. By prioritizing the implementation of JHA, construction companies prioritize the well-being of their workers and create a culture of safety and excellence on the job site.
Challenges in Conducting JHA
While implementing a Job Hazard Analysis (JHA) in the construction industry is essential for ensuring worker safety, it is not without its challenges. The following are some common challenges that construction companies may face when conducting a JHA:
- Limited Time and Resources: One of the main challenges in conducting a JHA is allocating sufficient time and resources. Construction projects often have tight schedules, and dedicating time for JHA analysis can be seen as a potential barrier to project completion. Adequate resources, such as personnel and tools, are necessary to conduct thorough JHA assessments.
- Complexity and Variety of Job Tasks: Construction projects involve various job tasks with unique hazards. Analyzing each task and identifying the associated hazards can be complex, particularly in large-scale projects with multiple job functions. It requires expertise and knowledge of potential hazards in different construction trades.
- Engagement and Participation: Obtaining full participation from all stakeholders, especially workers, can be challenging. Workers may view JHA as an additional burden or disruption to their daily tasks. Overcoming resistance and fostering active engagement is crucial to ensure accurate hazard identification and effective implementation of control measures.
- Changing Work Environment: Construction sites are dynamic, with changing conditions and evolving hazards. It can be challenging to keep the JHA updated as new hazards emerge or when there are modifications to the job scope, work processes, or equipment. Regular review and updates are necessary to ensure the JHA remains relevant and effective.
- Language and Literacy Barriers: Language and literacy barriers can hinder effective JHA implementation, especially in multicultural work environments. Clear communication and translation of JHA documents and instructions are crucial to ensure understanding and compliance among all workers.
- Documentation and Record-Keeping: Maintaining accurate and updated JHA records can be challenging, particularly in fast-paced construction environments. Lack of proper documentation can lead to confusion, improper implementation of control measures, and difficulties in demonstrating compliance with safety regulations.
- Training and Communication: Effective training and communication of JHA findings and control measures are key to successful implementation. However, ensuring that all workers receive the necessary training and comprehend the hazards and safety protocols can be a challenge, especially when dealing with a large workforce or frequent turnover.
- Legal and Regulatory Compliance: Compliance with safety regulations and legal requirements can be challenging, as different jurisdictions may have varying standards and guidelines. Staying up to date with regulatory changes and ensuring JHA aligns with the specific legal framework adds complexity to the JHA process.
Despite these challenges, construction companies must recognize the importance of overcoming these obstacles to ensure the successful implementation of JHA. By addressing these challenges proactively, construction companies can create a safer work environment and promote the well-being of their workers.
Tips for Effective JHA Implementation
Implementing a Job Hazard Analysis (JHA) in the construction industry requires careful planning and execution to ensure its effectiveness. The following are some tips to enhance the implementation of JHA and promote worker safety:
- Commitment from Management: Establish a strong commitment to safety from top management. This sets the tone for the organization and encourages worker participation, resource allocation, and support for JHA implementation.
- Engage Workers: Involve workers in the JHA process from the beginning. Seek their input, encourage their active participation, and value their knowledge and experience in identifying hazards and suggesting control measures. This creates a sense of ownership and increases the likelihood of successful implementation.
- Provide Training: Ensure that all workers involved in the job receive comprehensive training on hazard identification, risk assessment, and the use of control measures. Training should be ongoing, and refresher courses may be necessary to reinforce safety protocols and updated JHA procedures.
- Regular Communication: Maintain open lines of communication with workers, supervisors, and management regarding JHA findings, control measures, and safety updates. Regularly discuss the importance of JHA and address any concerns or questions that arise throughout the process.
- Adapt JHA to the Work Environment: Tailor the JHA to the specific work environment and tasks involved. Consider the unique hazards and risks associated with each job, and customize the control measures accordingly. This ensures that the JHA is relevant, practical, and effective in mitigating potential hazards.
- Update JHA Regularly: Review and update the JHA regularly to reflect any changes in working conditions, equipment, or job processes. This ensures that the JHA remains accurate and up to date, reflecting the evolving nature of construction projects and the associated hazards.
- Promote a Safety Culture: Foster a culture of safety by recognizing and rewarding safe work practices. Encourage workers to report hazards and near misses, and promptly address any safety concerns that arise. Continuous reinforcement of safety practices and positive reinforcement for adherence to JHA protocols create a safer work environment.
- Monitor and Evaluate: Regularly monitor and evaluate the effectiveness of JHA implementation. This can be done through inspections, audits, and incident reporting. Use this feedback to identify areas for improvement and make necessary adjustments to control measures and procedures.
- Document and Maintain Records: Document all aspects of the JHA process, including hazard identification, risk assessments, control measures, training records, and updates. Proper record-keeping ensures clarity, accountability, and compliance with safety regulations.
- Seek Professional Guidance: If needed, consider seeking assistance from safety professionals or consultants who specialize in JHA implementation. Their expertise and experience can provide valuable insights, ensuring a thorough and effective JHA process.
By following these tips, construction companies can enhance the implementation of JHA and create a safer work environment for their workers. Prioritizing worker safety through effective JHA implementation not only reduces the risk of accidents and injuries but also improves operational efficiency and promotes the overall success of construction projects.
Conclusion
In the construction industry, implementing a Job Hazard Analysis (JHA) is crucial for ensuring worker safety, preventing accidents, and promoting a culture of proactive hazard identification and risk mitigation. By conducting a JHA, construction companies can systematically analyze job tasks, identify potential hazards, assess risks, implement control measures, and create a safer work environment.
A JHA helps to identify specific hazards associated with each task or job, assess their associated risks, and determine appropriate control measures to prevent accidents and injuries. It enhances worker safety by equipping them with the necessary knowledge and protective measures to perform their tasks safely. Additionally, JHA aids in compliance with safety regulations, enhances communication and collaboration among stakeholders, and improves productivity and quality control on construction sites.
Conducting a JHA is not without its challenges, such as limited time and resources, complexity of job tasks, engagement and participation of workers, changing work environments, language barriers, documentation requirements, training, and legal compliance. However, by recognizing and addressing these challenges proactively, construction companies can overcome them and ensure effective JHA implementation.
To achieve successful JHA implementation, it is important to obtain commitment from top management, engage workers in the process, provide comprehensive training, maintain regular communication, tailor the JHA to the work environment, and regularly update the JHA. Promoting a safety culture, monitoring and evaluating the implementation, documenting the process, and seeking professional guidance if necessary are also essential for effective JHA implementation.
In conclusion, prioritizing the implementation of the JHA process is essential in the construction industry. By incorporating JHA into construction projects, companies demonstrate their commitment to worker safety, comply with safety regulations, prevent accidents and injuries, enhance productivity, and create a safer work environment for everyone involved. An effective JHA implementation ensures that construction projects are executed with the highest level of safety, ultimately leading to successful and profitable outcomes.
Frequently Asked Questions about What Is A JHA In Construction
Was this page helpful?
At Storables.com, we guarantee accurate and reliable information. Our content, validated by Expert Board Contributors, is crafted following stringent Editorial Policies. We're committed to providing you with well-researched, expert-backed insights for all your informational needs.
0 thoughts on “What Is A JHA In Construction”