Home>diy>Building & Construction>What Is A Punch List In Construction
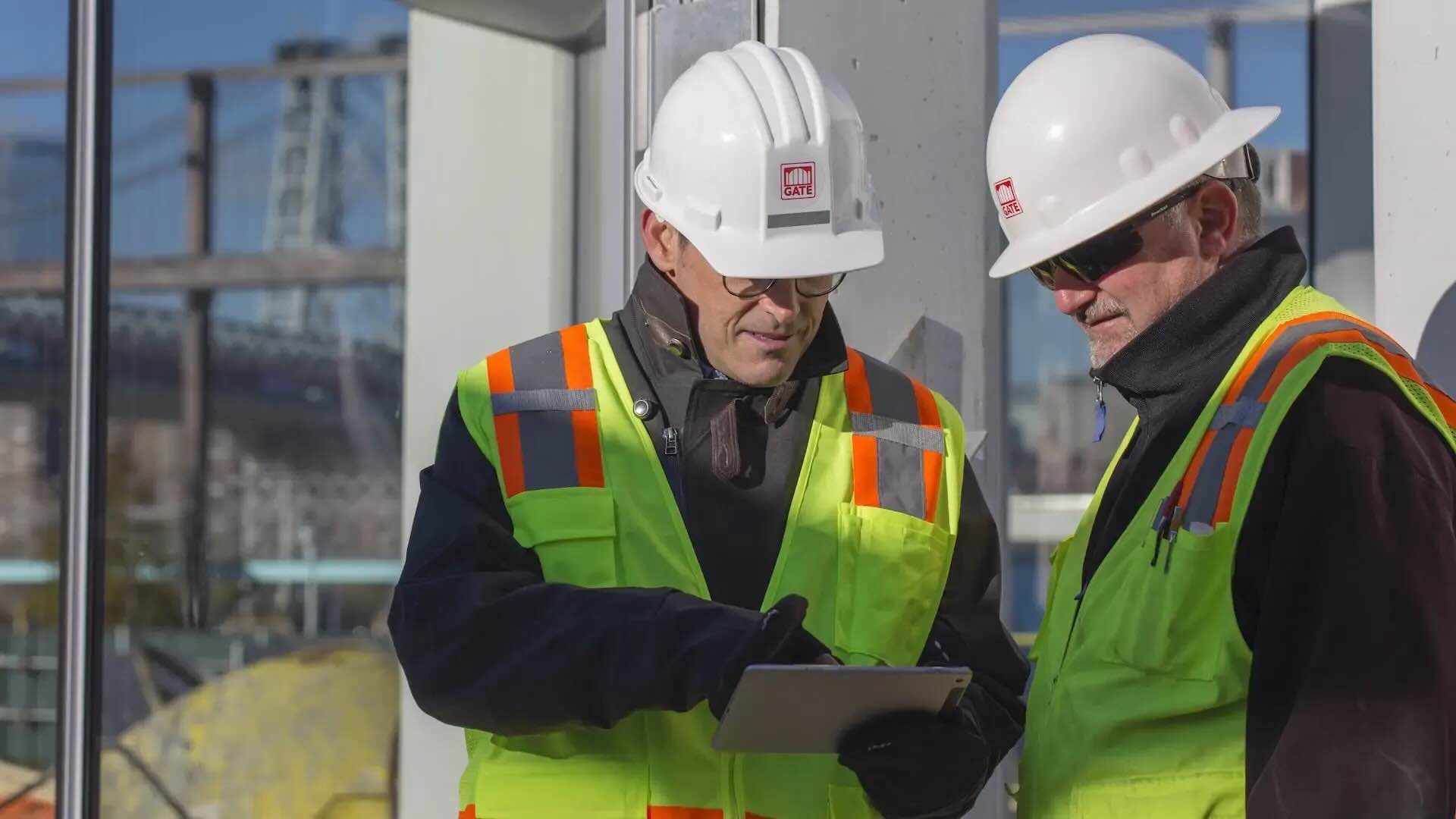
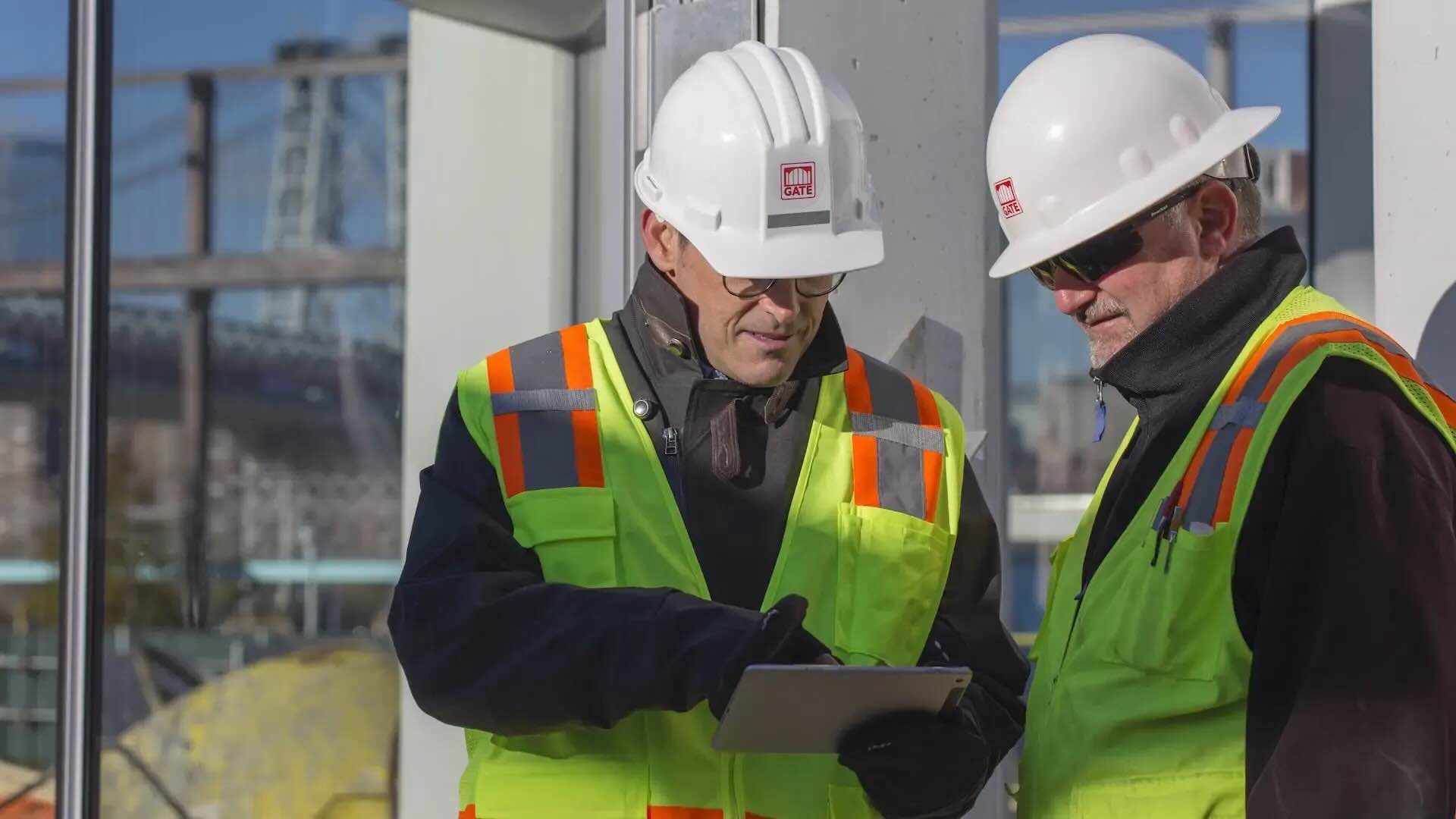
Building & Construction
What Is A Punch List In Construction
Modified: December 7, 2023
Learn about the purpose and importance of a punch list in building construction. Ensure a smooth project completion with this essential checklist.
(Many of the links in this article redirect to a specific reviewed product. Your purchase of these products through affiliate links helps to generate commission for Storables.com, at no extra cost. Learn more)
Introduction
Welcome to the dynamic world of construction, where careful planning, skilled labor, and a keen eye for detail come together to create magnificent structures. Building construction is known for its complexity, involving numerous stages and multiple teams working in tandem to bring a project to fruition. However, even the most meticulously planned construction projects can encounter small issues and defects that need to be addressed before the project can be considered complete.
This is where a punch list comes in. In the world of construction, a punch list serves as a vital tool to ensure that all the finishing touches are in place, allowing for a smooth handover to the client or owner. It may sound like a simple checklist, but a punch list plays a significant role in ensuring that the project meets the required standards of quality and functionality.
So, what exactly is a punch list in construction? Let’s dive into the details.
Key Takeaways:
- A punch list in construction is a vital checklist that ensures quality, client satisfaction, and legal protection by addressing remaining tasks and deficiencies before project completion.
- Effective punch list execution involves early initiation, thorough inspections, clear documentation, and continuous improvement, leading to successful project closeout and client satisfaction.
Read more: What Is Punch Work In Construction
Definition of a Punch List in Construction
A punch list, also known as a snag list, is a document that outlines all the remaining tasks, repairs, and corrections that need to be addressed before the construction project can be considered fully completed. It serves as a checklist to identify and rectify any deficiencies, defects, or omissions in the construction process.
The term “punch list” originated from the practice of using a pen or pencil to “punch” a small hole next to the item that needs attention, indicating that it has been reviewed and needs to be fixed or completed. In modern times, punch lists have evolved into digital formats, making it easier to track and manage the outstanding items.
A punch list typically consists of detailed descriptions, drawings, and specifications of the identified issues or incomplete tasks. It may include items such as surface imperfections, installation errors, operational malfunctions, missing finishes, or any other deficiencies that need to be resolved.
The creation of a punch list is usually done during the final stages of a construction project, just before the handover to the owner or client. It is a collaborative effort involving various stakeholders, including the contractor, architect, project manager, and client, to ensure that the project meets the defined standards and specifications.
Now that we understand the definition of a punch list, let’s explore its purpose in the construction process.
Purpose of Punch List
The primary purpose of a punch list in construction is to ensure that the final product meets the expected standards of quality and functionality. It serves as a comprehensive guide to identify and rectify any issues or deficiencies that may have been overlooked during the construction process.
Here are some specific purposes of a punch list:
- Quality Assurance: By conducting a thorough inspection of the construction site and documenting any imperfections, a punch list helps ensure that the final product is of high quality. It allows for a systematic review of the entire project, including finishes, installations, and overall workmanship.
- Completion and Handover: A punch list facilitates the process of completing the construction project by identifying all outstanding tasks and ensuring that they are properly addressed. Once all items on the punch list are resolved, the project can be handed over to the client or owner with confidence.
- Client Satisfaction: Addressing the items on a punch list demonstrates a commitment to client satisfaction. It allows the client to see that their concerns and expectations are taken seriously and that any issues will be promptly resolved before final acceptance.
- Cost Control: By identifying and addressing deficiencies early on, a punch list helps control costs. It allows for efficient allocation of resources to rectify the issues without prolonging the project timeline or incurring additional expenses.
- Legal Protection: A well-documented punch list provides legal protection for both the contractor and the client. It ensures that all parties are aware of their respective responsibilities and can mitigate any potential disputes or claims that may arise after project completion.
- Project Closeout: The punch list serves as a crucial component of the project closeout process. It acts as a final checklist to confirm that all required tasks have been completed before final documentation, such as warranties and certificates, can be issued.
In summary, a punch list plays a vital role in the construction process by ensuring quality assurance, facilitating completion and handover, promoting client satisfaction, controlling costs, providing legal protection, and facilitating the project closeout process.
Common Items Found in a Punch List
A punch list in construction can vary depending on the specific project and its requirements. However, there are several common items that are often found in punch lists across different construction projects. These items typically encompass areas where errors, omissions, or deficiencies are commonly observed. Let’s explore some of these common items:
- Finishes: Issues related to finishes are prevalent in punch lists. This may include uneven paint application, scratches or dents on walls or surfaces, missing or damaged trim, or improperly installed flooring.
- Plumbing and Electrical: Punch lists often include items related to plumbing and electrical systems, such as leaking faucets, malfunctioning electrical outlets, improper wiring, or plumbing fixture installations that require adjustment or repair.
- Doors and Windows: Problems with doors and windows are commonly identified in punch lists. This may involve issues such as misaligned doors or windows, faulty locks or handles, incorrect sizing, or improper sealing.
- Functional Components: Any components or systems that are not operating as intended may be included in the punch list. This can involve issues with HVAC systems, ventilation, lighting fixtures, or any other functional elements that require adjustment or repair.
- Cosmetic Defects: Punch lists often address cosmetic defects such as visible cracks in walls, uneven surfaces, or inadequate paint coverage. These defects can affect the overall visual appeal of the completed project.
- Cleanup and Debris: An important aspect of punch lists is ensuring that the construction site is cleaned up and free of debris. This includes removing construction materials, tools, and other items that should not be present during the final stages of the project.
- Documentation and Paperwork: Punch lists can also include items related to documentation and paperwork. This may involve missing permits, incomplete record-keeping, or insufficient documentation for warranties, certificates, or manuals.
- Safety and Accessibility: Punch lists may identify any safety hazards or accessibility issues that need to be resolved. This can include inadequate lighting, improper handrails or guardrails, or any other elements that may pose a risk to safety or hinder accessibility.
It is important to note that the items found in a punch list can vary depending on the scope and complexity of the construction project. A comprehensive and detailed inspection of the project is crucial to identify all the necessary items that need to be included.
Now that we have a clear understanding of the common items found in a punch list, let’s explore why addressing these items is of utmost importance.
A punch list in construction is a list of items that need to be completed or corrected before the project is considered finished. It’s important to regularly update and review the punch list to ensure all tasks are completed before final inspection.
Importance of Addressing Punch List Items
Addressing the items on a punch list is crucial for various reasons. Ignoring or neglecting these items can have significant implications for the overall success of the construction project and client satisfaction. Let’s examine the importance of addressing punch list items:
- Quality Assurance: By addressing punch list items, you ensure that the final product meets the expected standards of quality. Resolving deficiencies and errors helps to enhance the overall appearance, functionality, and longevity of the construction project.
- Client Satisfaction: It is essential to prioritize client satisfaction by addressing punch list items promptly and efficiently. By demonstrating a commitment to rectifying any issues or deficiencies, you build trust and credibility with the client and provide them with a final product that meets their expectations.
- Compliance with Specifications: Addressing punch list items ensures that the project adheres to the specified requirements and standards. This includes compliance with building codes, safety regulations, and any other contractual obligations.
- Legal Protection: Resolving punch list items helps protect all parties involved from potential legal disputes. By addressing any outstanding issues, you minimize the risk of future claims or liabilities related to construction defects or incomplete work.
- Operational Functionality: Correcting punch list items ensures the proper functioning of all systems and components within the construction project. This includes addressing plumbing or electrical issues, HVAC malfunctions, or any other operational deficiencies that may impact the functionality of the structure.
- Positive Reputation: Successfully addressing and resolving punch list items contributes to a positive reputation for the construction company. Satisfied clients are more likely to provide positive feedback and recommendations, leading to potential future business opportunities.
- Project Completion and Handover: Resolving punch list items is essential for the final completion and handover of the project. It signifies that all necessary tasks have been completed and that the project is ready for occupancy or use by the client.
- Cost Control: By promptly addressing punch list items, you can control costs associated with rework or repairs. It is more cost-effective to address and fix issues during the punch list phase rather than waiting for them to become bigger problems down the line.
Ignoring punch list items can lead to dissatisfied clients, costly rework, and potential legal disputes. It is crucial to recognize the importance of addressing these items and allocate the necessary resources to resolve them effectively.
Now that we understand the importance of addressing punch list items, let’s explore how to create and manage a punch list effectively.
Read more: How To Get New Construction Listings
Creating and Managing a Punch List
The creation and management of a punch list requires careful planning, meticulous attention to detail, and effective communication among all project stakeholders. Here are some essential steps to follow in order to create and manage a punch list effectively:
- Walk-through Inspection: Conduct a thorough walk-through inspection of the construction site. This involves examining every area of the project and documenting any deficiencies, errors, or incomplete tasks. Pay attention to finishes, installations, functional components, and any other areas of concern.
- Prioritize Items: Once the inspection is complete, prioritize the items on the punch list based on their severity and impact on the project. Start with critical issues that need immediate attention, and then proceed with less urgent items. This helps ensure that the most crucial tasks are addressed first.
- Document in Detail: Document each item on the punch list in detail. Include descriptions, drawings, photographs, or any other supporting documentation that provides clear instructions on what needs to be addressed or corrected. This helps avoid confusion and ensures that all parties have a clear understanding of the issues.
- Assign Responsibility: Assign responsibility for each item on the punch list to the relevant team members or subcontractors. Clearly communicate who is responsible for addressing and resolving each item, along with any specific instructions or requirements.
- Establish Timelines: Set realistic timelines for addressing and resolving the punch list items. Communicate these timelines to the responsible parties and ensure that they understand the importance of completing the tasks within the allocated time frame.
- Regular Follow-up: Regularly follow up with the responsible parties to monitor the progress of punch list item resolution. Provide necessary support or guidance to overcome any challenges or obstacles that may arise during the process.
- Re-Inspection: Once the punch list items have been addressed, conduct a re-inspection to verify that all tasks have been completed satisfactorily. Ensure that the quality and functionality of the resolved items meet the required standards.
- Documentation and Sign-off: Document the completion of each punch list item and obtain sign-off from all relevant parties. This serves as evidence that the identified issues have been addressed and resolved to the satisfaction of the project stakeholders.
Effective communication and collaboration among all project stakeholders are key to the successful creation and management of a punch list. Regular meetings, clear documentation, and a systematic approach facilitate the smooth resolution of punch list items.
Now that we understand how to create and manage a punch list, let’s explore some best practices for executing the punch list process.
Best Practices for Punch List Execution
Executing a punch list effectively requires careful planning, efficient communication, and attention to detail. By following these best practices, you can ensure a smooth and successful punch list process:
- Start Early: Initiate the punch list process early in the construction project to allow ample time for inspections, item identification, and resolution. Starting early ensures that there is sufficient time to address any issues and minimizes the risk of unnecessary delays.
- Collaborate with Stakeholders: Involve all relevant project stakeholders, including the contractor, architect, project manager, and client, in the punch list process. Effective collaboration enhances communication and ensures that everyone is aligned in terms of expectations, priorities, and responsibilities.
- Thorough Inspection: Conduct a detailed and comprehensive inspection of the construction site to identify all deficiencies and incomplete tasks. A thorough inspection minimizes the chances of overlooking any crucial punch list items.
- Clear and Detailed Documentation: Document each punch list item with clear and concise descriptions, including any necessary supporting documentation such as photographs or drawings. Detailed documentation helps avoid misunderstandings and ensures that all parties have a clear understanding of the issues and requirements.
- Prioritize and Categorize: Prioritize the punch list items based on their severity and impact on the project. Categorize them into critical, high-priority, and lower-priority items. This allows for a systematic approach to addressing the items and ensures that the most important tasks are dealt with first.
- Communication and Follow-up: Maintain open lines of communication with the responsible parties for each punch list item. Regularly follow up to monitor progress, provide support, and address any challenges that may arise. Effective communication helps keep the punch list process on track and ensures timely resolution.
- Verify Resolutions: Conduct a thorough re-inspection to verify that all punch list items have been addressed and resolved to the required standards. Confirm that the quality and functionality of the resolved items meet the expectations outlined in the punch list.
- Obtain Sign-off: Obtain sign-off from all relevant parties once the punch list items have been successfully resolved. This signifies that the identified issues have been satisfactorily addressed and helps mitigate any potential future disputes.
- Continuous Improvement: Learn from the punch list process and incorporate any lessons learned into future projects. Continuous improvement ensures that the quality of construction and the effectiveness of the punch list process continue to evolve and improve over time.
By following these best practices, you can streamline the punch list execution process and ensure that all outstanding items are addressed promptly and effectively.
Now, let’s wrap up our discussion on punch lists in construction.
Conclusion
A punch list is an essential tool in the construction industry, serving as a checklist to identify and address any remaining tasks, repairs, or corrections before the completion of a project. It plays a vital role in ensuring quality assurance, client satisfaction, and compliance with specifications. Ignoring or neglecting punch list items can have significant consequences, including legal disputes, dissatisfied clients, and increased costs.
Creating and managing a punch list requires careful planning, thorough inspections, clear documentation, and effective communication among all project stakeholders. By following best practices such as starting early, collaborating with stakeholders, and prioritizing and categorizing items, you can execute the punch list process efficiently. Regular follow-up, re-inspections, obtaining sign-offs, and continuous improvement are also essential for successful punch list execution.
Addressing the common items found in a punch list, such as finishes, plumbing and electrical issues, doors and windows, and functional components, ensures the quality and functionality of the final product. It also helps achieve client satisfaction, maintain a positive reputation, and minimize legal risks.
In the dynamic world of construction, the punch list serves as a powerful tool to wrap up projects successfully. It ensures that no loose ends are left behind and allows for a smooth and seamless handover to the client. By addressing punch list items promptly and effectively, construction professionals can deliver projects that meet the highest standards of quality, functionality, and client satisfaction.
Remember, a well-executed punch list is the final step towards a job well done in the construction process.
Frequently Asked Questions about What Is A Punch List In Construction
Was this page helpful?
At Storables.com, we guarantee accurate and reliable information. Our content, validated by Expert Board Contributors, is crafted following stringent Editorial Policies. We're committed to providing you with well-researched, expert-backed insights for all your informational needs.
0 thoughts on “What Is A Punch List In Construction”