Home>diy>Building & Construction>What Is A Subfloor In Construction
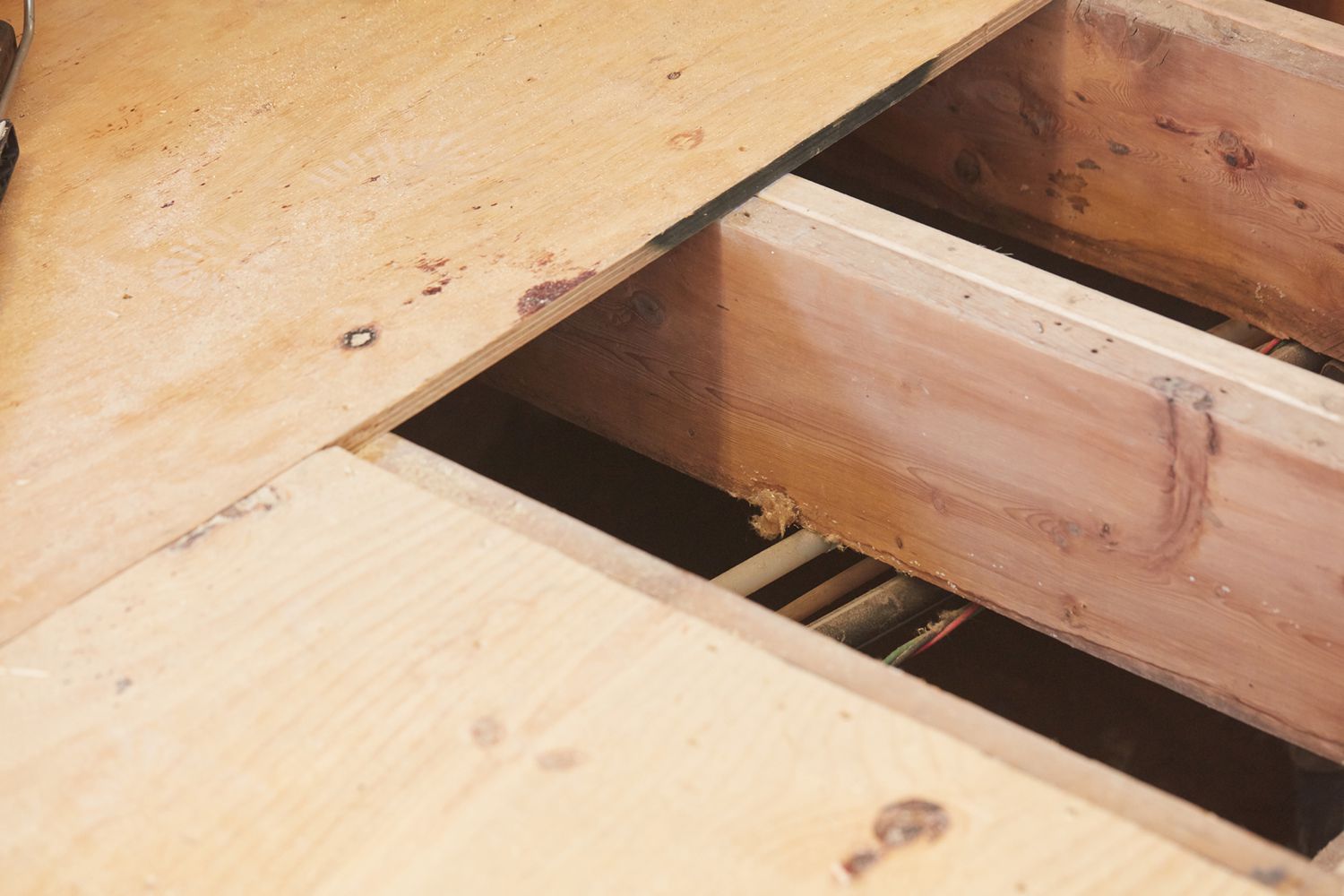
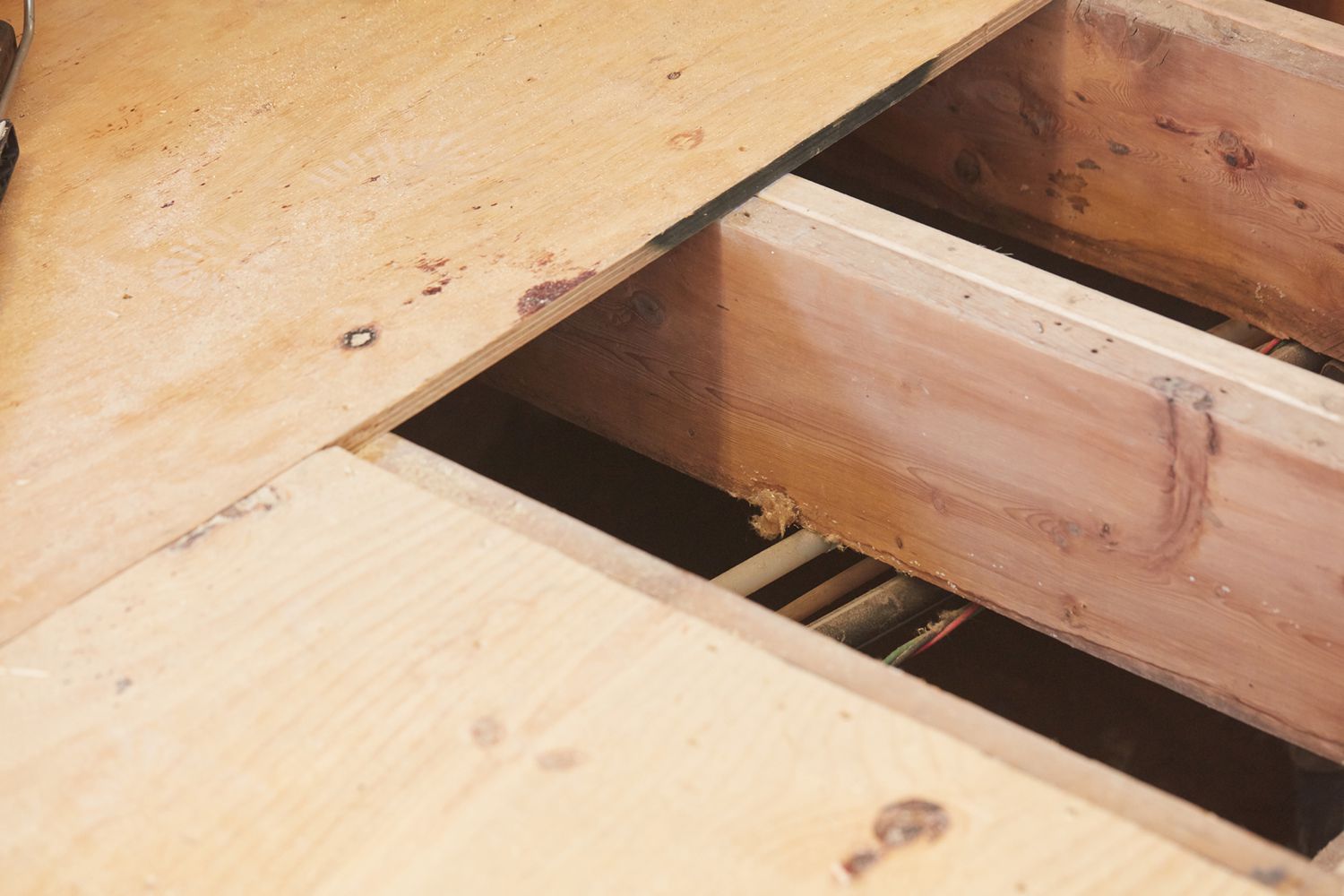
Building & Construction
What Is A Subfloor In Construction
Modified: December 7, 2023
Learn about the importance of subfloors in building construction and how they provide a sturdy foundation for flooring materials.
(Many of the links in this article redirect to a specific reviewed product. Your purchase of these products through affiliate links helps to generate commission for Storables.com, at no extra cost. Learn more)
Introduction
Welcome to the fascinating world of construction! When it comes to building a solid foundation, understanding the importance of a subfloor is crucial. The subfloor is an essential component of any building structure, providing a sturdy base for the flooring materials above. In this article, we will take a closer look at what exactly a subfloor is, its purpose, different types of subfloor materials, installation methods, and common issues that may arise.
A subfloor refers to the layer of material that is installed directly onto the joists or concrete slab of a building. Its primary function is to provide stability, structural integrity, and sound insulation to the flooring system. Acting as the “foundation” for the final flooring materials, the subfloor serves as a crucial intermediary layer that contributes to the overall performance and longevity of the floor.
There are various types of subfloor materials used in construction, with each having its own set of advantages and considerations. Plywood, oriented strand board (OSB), and concrete are the most common materials used for subflooring.
Plywood subfloors are made from thin layers of wood veneers glued together, creating a strong and stable surface. Their uniform composition and dimensional stability make them an excellent choice for residential and commercial applications. Plywood subfloors are available in different thicknesses, with the most common being ¾ inch.
OSB subfloors, on the other hand, are composed of wood strands compressed and bonded with resin. They are known for their affordability and structural strength. OSB panels are available in various thicknesses and are commonly used in light commercial and residential construction.
Concrete subfloors are typically found in commercial buildings and basements. They are created by pouring a mixture of cement, sand, and aggregate onto a prepared surface. Concrete subfloors offer exceptional durability and are ideal for areas prone to moisture and high traffic.
Choosing the right type of subfloor material depends on factors such as the building’s budget, the specific requirements of the flooring system, and the environmental conditions. Each material has its own advantages and disadvantages that need to be considered before making a decision.
Key Takeaways:
- A sturdy subfloor is crucial for a durable flooring system. Plywood, OSB, and concrete are popular materials, each with unique advantages and considerations. Proper installation and maintenance are essential for long-term stability.
- Promptly addressing subfloor damage is vital for maintaining a safe and reliable foundation. From moisture control to troubleshooting common issues, proactive measures ensure the integrity and longevity of the flooring system.
Read more: What Is A Subfloor
Definition of a Subfloor
A subfloor is the layer of material that is installed directly on top of the floor joists or concrete slab of a building. It serves as the base for the final flooring materials to be installed above it. The purpose of the subfloor is to provide stability, support, and a level surface for the flooring system.
The subfloor acts as a foundation for the flooring, preventing it from sagging or flexing under weight and movement. It also helps to distribute the load evenly across the floor joists, ensuring structural integrity. Additionally, the subfloor adds insulation and soundproofing qualities, minimizing noise transmission between floors.
Subfloors are typically made from various materials, including plywood, oriented strand board (OSB), and concrete, depending on the specific needs of the building and the flooring system.
When constructing a building, the subfloor is typically installed before any other finishing materials, such as hardwood, tile, or carpet. This allows for a smooth and even surface, ensuring the proper installation and performance of the final flooring materials.
In some cases, a subfloor may also incorporate additional features such as vapor barriers or radiant heat systems. These elements are designed to mitigate moisture issues and provide comfort enhancements, respectively.
The quality and construction of the subfloor play a crucial role in the overall integrity and longevity of the flooring system. A well-built and properly installed subfloor ensures that the final flooring materials perform as intended and are resistant to wear, moisture, and other potential sources of damage.
Overall, the subfloor is an essential component of any building structure, providing a solid foundation for the flooring system. It is a crucial consideration in construction projects, as it directly impacts the stability, durability, and overall performance of the building’s floors.
Purpose and Importance of a Subfloor
The subfloor plays a crucial role in the construction of any building, providing both functional and practical benefits. Understanding the purpose and importance of a subfloor is essential for ensuring a durable and long-lasting flooring system. Let’s explore why the subfloor is such a critical component:
1. Structural Stability: One of the primary purposes of a subfloor is to provide structural stability to the flooring system. It acts as a solid and level base, preventing the floor from sagging or flexing. By distributing the weight evenly across the floor joists or concrete slab, the subfloor helps to maintain the overall integrity of the building’s structure.
2. Support for Flooring Materials: A well-built subfloor provides a sturdy foundation for the final flooring materials, such as hardwood, laminate, tile, or carpet. It ensures that the flooring materials are properly supported, reducing the risk of uneven surfaces, cracking, or premature wear and tear.
3. Sound Insulation: The subfloor can add a layer of sound insulation, making the floors more peaceful and reducing noise transmission between floors. It minimizes the sound of footsteps, household activities, and other ambient noises, enhancing the comfort and privacy of the building’s occupants.
4. Moisture Protection: Depending on the subfloor material used, it can provide a certain level of moisture protection. For example, concrete subfloors have inherent resistance to moisture, making them ideal for areas prone to high humidity or moisture issues like basements or bathrooms. Properly sealed and installed subfloors can also include vapor barriers, preventing moisture from penetrating the flooring materials and causing damage.
5. Insulating Properties: Some subfloor materials, such as plywood or OSB, have insulating qualities, helping to reduce heat loss or gain through the floors. This can lead to energy savings and increased comfort within the building.
6. Preparation for Flooring Installation: The subfloor provides a level and even surface for the installation of final flooring materials. It eliminates any imperfections or irregularities in the underlying structure, ensuring a seamless and professional-looking installation.
7. Longevity of the Flooring System: A well-designed and properly installed subfloor can significantly extend the lifespan of the flooring system. It minimizes the risk of damage, such as warping, buckling, or excessive wear, by providing a stable and supportive foundation for the flooring materials.
Overall, the purpose and importance of a subfloor cannot be overstated. It contributes to the structural integrity, durability, and overall performance of the flooring system in a building. By investing in a quality subfloor, you can ensure the long-term success of your flooring materials and optimize the comfort and functionality of your space.
Types of Subfloor Materials
When it comes to choosing the right subfloor material for your building project, it’s essential to consider factors such as budget, environmental conditions, and the specific requirements of the flooring system. Different materials offer various advantages and considerations. Let’s explore three common types of subfloor materials:
1. Plywood Subfloor: Plywood is a highly popular and widely used subfloor material. It is constructed by gluing and compressing multiple thin layers of wood veneers together. The layers are arranged with alternating grain directions, creating a strong and stable panel.
Advantages: Plywood subfloors are renowned for their dimensional stability and uniform composition. They offer excellent resistance to moisture and temperature changes. Additionally, plywood subfloors provide a smooth and level surface for the installation of final flooring materials.
Considerations: Plywood subfloors can be more expensive than other options. Additionally, they are prone to swelling or rotting if exposed to prolonged moisture. Proper subfloor preparation and sealing are crucial to mitigate these risks.
2. Oriented Strand Board (OSB) Subfloor: OSB is an engineered wood product made by compressing wood strands with resin and wax. The strands are arranged in layers and oriented in different directions, resulting in a strong and durable panel.
Advantages: OSB subfloors are known for their affordability, making them a popular choice for residential and light commercial applications. They offer excellent structural strength and are resistant to warping or delamination. OSB subfloors also contribute to energy efficiency, as they have insulating properties.
Considerations: Unlike plywood, individual OSB strands may be susceptible to moisture absorption if exposed to prolonged damp conditions. Proper installation and moisture control measures, such as proper sealing and ventilation, are necessary to prevent issues.
3. Concrete Subfloor: Concrete subfloors are typically found in commercial buildings or basements. They are created by pouring a mixture of cement, sand, and aggregate onto a prepared surface.
Advantages: Concrete subfloors are exceptionally durable, resistant to moisture, and have excellent load-bearing capabilities. They also offer high thermal mass, improving energy efficiency and temperature regulation. Concrete subfloors are suitable for areas prone to high traffic or moisture, such as kitchens or bathrooms.
Considerations: Concrete subfloors can be more expensive and time-consuming to install compared to other options. They require proper curing time and may require additional measures, such as moisture barriers or insulation, to mitigate potential issues. Additionally, their rigidity may result in a less forgiving surface for the final flooring materials.
Each type of subfloor material has its own set of advantages and considerations. It’s important to carefully evaluate your project’s specific needs, budget, and environmental conditions before selecting the most suitable option. Proper installation, subfloor preparation, and maintenance are key to ensuring the longevity and performance of your flooring system.
Plywood Subfloor
Plywood is a popular and commonly used subfloor material in construction. It is composed of thin layers of wood veneers that are glued and compressed together, creating a strong and durable panel. Plywood subfloors offer numerous advantages and considerations that make them a preferred choice for many building projects.
Advantages of Plywood Subfloor:
- Dimensional Stability: Plywood subfloors are known for their excellent dimensional stability. The layers of wood veneers are arranged with alternating grain directions, which helps minimize changes in size, shape, or warping due to temperature and moisture fluctuations. This stability ensures a long-lasting and reliable subfloor.
- Strength and Durability: Plywood is a remarkably strong and durable material. It has high load-bearing capacities, making it suitable for supporting heavy furniture, equipment, and foot traffic. Its structural strength contributes to the longevity and stability of the flooring system.
- Moisture Resistance: Plywood subfloors have inherent moisture resistance properties. The glues used in the manufacturing process make the panels resistant to water penetration. However, it is important to note that prolonged exposure to moisture can still cause swelling or delamination. Therefore, proper installation and moisture control measures, such as proper sealing and a vapor barrier, are essential to prevent potential issues.
- Smooth and Level Surface: Plywood subfloors offer a smooth and flat surface for the installation of final flooring materials. This ensures easier and more seamless floor installations, reducing the risk of unevenness or gaps in the flooring system.
- Versatility: Plywood subfloors are compatible with a wide range of flooring materials, including hardwood, laminate, tile, and carpet. They provide a stable foundation that works well with different types of finishes, allowing for flexibility in design and aesthetics.
Considerations for Plywood Subfloor:
- Cost: Plywood subflooring can be more expensive than other options, such as OSB (oriented strand board). The cost depends on factors such as the thickness and grade of the plywood. However, considering its durability and performance, the investment in a quality plywood subfloor typically pays off in the long run.
- Moisture Control: While plywood has inherent moisture resistance, it is still vulnerable to damage if continually exposed to high levels of moisture. It is essential to properly prepare and seal the subfloor to create a protective barrier against moisture. Additionally, maintaining a controlled indoor environment and addressing any potential sources of moisture is crucial to prevent long-term damage.
- Installation: Proper installation of plywood subfloors is vital to ensure its effectiveness and longevity. This includes correctly fastening the panels to the floor joists, leaving expansion gaps, and using appropriate adhesives and fasteners. Following manufacturer guidelines and industry best practices is essential for a successful installation.
Plywood subfloors offer a solid foundation for the flooring system, providing stability, strength, and moisture resistance. Their dimensional stability and versatility make them a reliable choice for various building projects. By understanding the advantages and considerations of plywood subfloors and following proper installation and maintenance practices, you can create a durable and long-lasting flooring system for your space.
Read more: How To Install Subfloor In Basement
OSB Subfloor
Oriented Strand Board (OSB) is a widely used subfloor material in construction. It is an engineered wood product made by compressing wood strands with resin and wax. OSB subfloors offer several advantages and considerations that make them a popular choice for many building projects.
Advantages of OSB Subfloor:
- Affordability: OSB subfloors are known for their cost-effectiveness, making them a preferred choice for residential and light commercial applications. Compared to other subfloor materials, such as plywood, OSB is generally more budget-friendly.
- Structural Strength: OSB panels have excellent structural strength due to the arrangement of wood strands in layers. This makes them highly resistant to warping, delamination, and other forms of damage. OSB subfloors can withstand heavy loads and foot traffic without compromising their integrity.
- Insulating Properties: OSB has natural insulating properties, offering some thermal resistance. This can improve energy efficiency by reducing heat loss or gain through the flooring system, enhancing the comfort of the living or working space.
- Moisture Resistance: OSB subfloors are moisture resistant to a certain extent. However, it is important to note that individual wood strands may be susceptible to moisture absorption if the subfloor is exposed to prolonged damp conditions. Proper installation, including sealing the edges and surface, and ensuring proper ventilation, is crucial for preventing moisture-related issues.
- Compatibility with Various Flooring Materials: OSB subfloors can be used with a wide range of flooring materials, including hardwood, laminate, tile, and carpet. Whether it’s for residential or light commercial spaces, OSB provides a stable and reliable foundation for various finishes.
Considerations for OSB Subfloor:
- Moisture Control: While OSB subfloors have inherent moisture resistance, it is important to protect them from direct exposure to excessive moisture. Installing a moisture barrier, such as a vapor barrier, and ensuring proper ventilation can help minimize the risk of moisture-related issues. It is important to follow best practices and manufacturer guidelines to maintain the structural integrity of the OSB subfloor.
- Thermal Expansion and Contraction: Like any wood-based material, OSB can expand and contract with changes in temperature and humidity. Proper expansion gaps should be left at the edges of the subfloor and appropriate acclimation methods should be followed during installation to allow for dimensional changes over time.
- Proper Installation: Proper installation of OSB subfloors is crucial for their performance and longevity. This includes ensuring adequate panel spacing, using appropriate adhesives and fasteners, and following manufacturer guidelines. Accurate fastening to the floor joists is essential for maintaining structural stability.
OSB subfloors offer a cost-effective and durable solution for residential and light commercial projects. By understanding the advantages and considerations of OSB subfloors and following proper installation and maintenance practices, you can create a solid foundation for your flooring system that is resistant to damage and provides stability for years to come.
Concrete Subfloor
A concrete subfloor is a common choice for commercial buildings and basements. It is created by pouring a mixture of cement, sand, and aggregate onto a prepared surface, providing a solid and durable base for the flooring system. Concrete subfloors offer several advantages and considerations that make them suitable for various applications.
Advantages of Concrete Subfloor:
- Durability and Strength: Concrete subfloors are highly durable and have excellent load-bearing capabilities. They can withstand heavy traffic and are resistant to wear and tear, making them ideal for high-traffic areas in commercial spaces.
- Moisture Resistance: Concrete is naturally moisture-resistant, making it a suitable choice for areas prone to moisture or water exposure. It helps prevent issues such as warping, rotting, or mold growth that can occur with other subfloor materials.
- Fire Resistance: Concrete has excellent fire resistance properties, providing an added level of safety and protection to the building. It can help contain the spread of fire and protect the integrity of the structure.
- Thermal Mass: Concrete has high thermal mass, which means it can absorb and store heat energy. This can contribute to increased energy efficiency by regulating temperature fluctuations in the building and potentially reducing heating and cooling costs.
- Design Flexibility: Concrete subfloors offer design flexibility, as they can be left as the final flooring option or serve as a base for various finishes, such as epoxy coatings, polished concrete, or tile. The versatility of concrete allows for a wide range of aesthetic options.
Considerations for Concrete Subfloor:
- Installation Time and Complexity: Installing a concrete subfloor can be more time-consuming and complex compared to other subfloor materials. It requires proper planning, preparation, and professional expertise to ensure a level and properly cured surface.
- Moisture Concerns: While concrete is inherently moisture-resistant, it is not fully impervious to water penetration. Without proper sealing and moisture barriers, moisture can seep through the concrete and impact the flooring materials above. It is important to address any potential moisture issues through proper sealing, drainage systems, and moisture control methods.
- Rigidity: Concrete is a rigid material, which means it may not provide the same level of comfort underfoot as other subfloor materials with more cushioning or flexibility. The hardness of concrete can impact the comfort and shock-absorbing properties of the flooring system. Proper underlayment or floor coverings can be added to enhance comfort if desired.
- Surface Preparation: Proper surface preparation is essential for the installation of a concrete subfloor. This involves cleaning, leveling, and smoothing the surface before pouring the concrete. Any imperfections or irregularities can affect the final result and the performance of the flooring materials.
Concrete subfloors offer strength, durability, and moisture resistance, making them an excellent choice for commercial and basement environments. By considering the advantages and considerations of a concrete subfloor and ensuring proper installation and maintenance, you can create a stable and long-lasting foundation for your flooring system.
Advantages and Disadvantages of Different Subfloor Materials
Choosing the right subfloor material for your building project is crucial for the overall performance and longevity of the flooring system. Each type of material comes with its own set of advantages and disadvantages. Let’s explore the pros and cons of three common subfloor materials: plywood, oriented strand board (OSB), and concrete.
Plywood Subfloor:
- Advantages:
- Dimensional stability: Plywood subfloors are known for their excellent dimensional stability and uniform composition.
- Strength and durability: Plywood has high structural strength and can withstand heavy loads and foot traffic.
- Moisture resistance: Plywood subfloors offer inherent moisture resistance, although proper installation and sealing are necessary to prevent long-term damage.
- Smooth and level surface: Plywood provides a smooth and level surface for easier installation of the final flooring materials.
- Versatility: Plywood is compatible with various flooring materials, allowing for flexibility in design and finishes.
- Disadvantages:
- Cost: Plywood subflooring can be more expensive compared to other options like OSB.
- Potential for moisture damage: Prolonged exposure to moisture can cause plywood to swell or rot if not properly sealed and maintained.
OSB Subfloor:
- Advantages:
- Affordability: OSB subfloors are generally more budget-friendly compared to plywood.
- Structural strength: OSB panels offer excellent structural strength and resistance to warping or delamination.
- Insulating properties: OSB provides some thermal resistance, contributing to energy efficiency.
- Compatibility with various flooring materials: OSB subfloors work well with a wide range of finishes.
- Disadvantages:
- Moisture concerns: Although OSB is moisture-resistant, individual wood strands can absorb moisture if exposed to prolonged dampness.
- Thermal expansion and contraction: OSB, like any wood-based material, can expand and contract with changes in temperature and humidity.
Concrete Subfloor:
- Advantages:
- Durability and strength: Concrete subfloors are highly durable and have excellent load-bearing capabilities.
- Moisture resistance: Concrete is naturally moisture-resistant and helps prevent issues like warping or mold growth.
- Fire resistance: Concrete provides added fire resistance and can contain the spread of fire.
- Design flexibility: Concrete subfloors can be left as the final flooring or serve as a base for various finishes.
- Disadvantages:
- Installation time and complexity: Installing a concrete subfloor can be more time-consuming and complex compared to other options.
- Moisture concerns: While concrete is moisture-resistant, it still requires proper sealing and moisture control measures to prevent long-term damage.
- Rigidity: Concrete is a rigid material and may not provide the same cushioning and comfort as other subfloor materials.
Each subfloor material offers unique benefits and considerations. Plywood provides stability and versatility, OSB offers affordability and structural strength, while concrete brings durability and moisture resistance. It’s important to carefully evaluate your project’s specific needs, budget, and environmental conditions to determine the most suitable subfloor material for your flooring system.
When constructing a subfloor, make sure to use moisture-resistant materials to prevent damage from water and humidity. This will help to maintain the structural integrity of the building over time.
Installation Process for a Subfloor
The installation of a subfloor requires careful planning, proper preparation, and attention to detail. Whether you’re working with plywood, OSB, or concrete, following a systematic process will help ensure a sturdy and reliable foundation for your flooring system. Here is a general overview of the installation process:
1. Subfloor Preparation:
Before installing the subfloor, it’s important to prepare the underlying surface. This involves cleaning the area to remove any debris, ensuring the floor joists or concrete slab are structurally sound, and addressing any necessary repairs or adjustments. If installing over a concrete slab, test for moisture and consider applying a moisture barrier if needed.
2. Measure and Cut Subfloor Material:
Measure the dimensions of the room and transfer these measurements onto the subfloor material, whether it’s plywood, OSB, or preparing the concrete slab. Use a saw or appropriate cutting tool to cut the panels to fit the specified dimensions, leaving space for expansion gaps against walls and obstructions.
3. Install the Subfloor:
Begin installing the subfloor panels starting from one corner of the room. With plywood or OSB, align the edges of the panels with the center of the floor joists, staggering the seams to enhance stability. Fasten the panels to the floor joists or concrete slab using appropriate nails, screws, or adhesives according to the manufacturer’s recommendations. Leave expansion gaps between panels and around the perimeter of the room to allow for natural movement.
4. Secure the Subfloor:
Ensure that the subfloor is firmly secured to the floor joists or concrete slab. Use a level to check for any unevenness and adjust as necessary. Proper fastening is crucial for structural integrity and to prevent squeaking or shifting of the subfloor.
5. Insulate the Subfloor (optional):
If insulation is desired, install a layer of insulation material, such as rigid foam boards, between the subfloor and the flooring material. This can help improve energy efficiency and provide additional comfort by minimizing heat loss or gain through the floor.
6. Subfloor Finishing:
Depending on the chosen flooring material, additional steps may be required to prepare the subfloor for installation. This may include installing a moisture barrier, applying a primer or sealer, or performing additional leveling or smoothing if necessary. Follow the manufacturer’s instructions and industry best practices for the specific flooring material being used.
During the installation process, it is crucial to follow safety guidelines, wear appropriate personal protective equipment, and adhere to local building codes and regulations. If you are uncertain about any aspect of the installation, consult with a professional or seek advice from experts in the field.
By following a systematic installation process for your subfloor, you can create a solid foundation for your flooring system. Proper preparation, precision cutting, secure fastening, and attention to detail will ensure a reliable and long-lasting subfloor that contributes to the overall durability and performance of your space.
Read more: What Is Pre-Construction In Construction
Subfloor Preparation
Proper subfloor preparation is a critical step in ensuring the success and longevity of your flooring system. Before installing the subfloor, it is important to thoroughly prepare the underlying surface. This involves several key steps to ensure that the subfloor will be stable, level, and ready for the installation of the flooring material. Here is a guide to subfloor preparation:
1. Clean the Subfloor:
Start by cleaning the subfloor to remove any dirt, debris, or adhesive residues. Use a broom, vacuum, or appropriate cleaning tools to thoroughly clean the surface. Make sure all areas are free from dust and any loose particles.
2. Inspect for Structural Integrity:
Inspect the floor joists or concrete slab to ensure they are structurally sound. Check for any signs of rot, decay, or damage that may compromise the stability of the subfloor. If necessary, make any repairs or reinforcements to ensure the subfloor will have a solid foundation.
3. Check for Levelness:
Using a long level or a straight edge, check for levelness across the subfloor. Any areas that are significantly uneven may require additional preparation. If the subfloor is concrete, you may need to use a self-leveling compound to fill in low spots and create a level surface. For wood subfloors, consider shimming or adding additional support to achieve a level surface.
4. Address Moisture Concerns:
Moisture is a common issue that can affect the performance of the subfloor and the flooring material. For concrete subfloors, it is crucial to test for moisture. Use a moisture meter or conduct a calcium chloride test to determine if there is excess moisture. If moisture levels are high, it may be necessary to address this issue with the use of a moisture barrier, such as a vapor barrier or moisture-resistant underlayment.
5. Ensure Proper Ventilation:
Proper ventilation is essential to prevent moisture build-up and potential damage to the subfloor. Ensure that there is adequate airflow by providing vents or exhaust fans in areas where moisture is more likely to accumulate, such as bathrooms or kitchens. This will help maintain a balanced and controlled environment, minimizing the risk of moisture-related issues.
6. Prepare for Subfloor Installation:
Prior to installing the subfloor, gather all the necessary materials and tools. This may include the subfloor panels (plywood, OSB, etc.), fasteners (nails, screws, adhesive), a saw for cutting the panels, a level for checking for levelness, and appropriate safety equipment. Follow the manufacturer’s instructions and adhere to local building codes and regulations.
By taking the time to properly prepare the subfloor, you are setting the stage for a successful flooring installation. Addressing structural integrity, levelness, moisture concerns, and ventilation will help ensure that the subfloor is stable, level, and ready to support the flooring material. Following these steps will contribute to the durability, performance, and longevity of your flooring system.
Subfloor Installation Methods
When it comes to installing a subfloor, there are several methods that can be utilized depending on the specific requirements of the project. The choice of installation method may vary based on factors such as the type of subfloor material, the subfloor’s location, and the desired outcome. Here are some common subfloor installation methods:
1. Glue-Down Method:
The glue-down method is commonly used for installing plywood or OSB subfloors. In this method, subfloor panels are secured to the floor joists or concrete slab using a suitable flooring adhesive. The adhesive is applied evenly to the subfloor, and then the panels are laid in place, ensuring proper alignment. Weight may be temporarily applied to the panels to help with adhesion. This method offers a strong and secure bond between the subfloor and the underlying surface.
2. Nail-Down Method:
The nail-down method is typically used for plywood or OSB subfloors that will be fastened using nails or screws. In this method, subfloor panels are attached to the floor joists by driving nails or screws through the panels and into the joists. The fasteners are typically spaced at regular intervals along the edges and field of the panels to ensure a secure connection. This method provides a reliable and structurally sound subfloor.
3. Floating Method:
The floating method is commonly used for laminate or engineered wood flooring installations. It involves the use of an underlayment, such as foam or cork, placed over the subfloor. The flooring material is then laid directly on top of the underlayment, without being physically attached to the subfloor. The individual flooring pieces or planks are typically secured together using a tongue-and-groove system. This method allows for the natural expansion and contraction of the flooring material and offers flexibility in case of future changes or repairs.
4. Self-Leveling Compound:
For concrete subfloors that are uneven or have low spots, a self-leveling compound can be used to create a smooth and level surface. The compound is mixed according to the manufacturer’s instructions and then poured onto the subfloor. It self-levels, filling in low areas and creating a flat surface. This method is suitable for addressing minor imperfections in the subfloor before installing the final flooring material.
It’s important to note that the choice of installation method may depend on the specific subfloor material, the manufacturer’s recommendations, and industry best practices. It is crucial to follow the instructions provided by the manufacturer to ensure a proper and long-lasting subfloor installation.
Before undertaking any subfloor installation, it’s recommended to consult with a professional or refer to relevant building codes and regulations. Proper installation techniques and attention to detail will help create a reliable, level, and structurally sound subfloor that will serve as a strong foundation for your flooring system.
Subfloor Insulation
Insulating the subfloor can provide numerous benefits, including improved energy efficiency, soundproofing, and enhanced comfort. Subfloor insulation helps to create a thermal barrier between the floor and the space below, reducing heat loss or gain and promoting a more comfortable indoor environment. Here are some key considerations and methods for subfloor insulation:
1. Insulation Materials:
There are various insulation materials that can be used for subfloor insulation, including:
- Fiberglass insulation: Fiberglass batts or rolls are a common choice for subfloor insulation. They are effective at reducing heat transfer and are relatively easy to install. However, it’s important to use insulation with the appropriate R-value for your climate and ensure proper installation to avoid gaps or compression.
- Rigid foam insulation: Rigid foam boards provide excellent thermal insulation and moisture resistance. They are often used for subfloor insulation in areas prone to moisture, such as basements. Rigid foam boards are lightweight, easy to handle, and can be cut to fit the desired dimensions.
- Spray foam insulation: Spray foam insulation is another option for subfloor insulation. It can provide superior air sealing and insulation properties by filling gaps and cavities. However, professional installation is typically required for spray foam insulation.
- Cellulose insulation: Cellulose insulation is made from recycled paper products and provides good thermal performance. It can be blown into the subfloor cavity using specialized equipment, ensuring complete coverage and minimizing air leakage.
2. Installation Methods:
The installation method for subfloor insulation will depend on the insulation material chosen and the specific subfloor construction. Here are a few common installation methods:
- Batt insulation between floor joists: This method involves placing fiberglass batts or rigid foam insulation between the floor joists. The insulation is sized to fit snugly between the joists, ensuring complete coverage. It’s important to use insulation with the appropriate R-value and install it with the vapor barrier facing the conditioned space.
- Rigid foam insulation on the underside of the subfloor: For concrete subfloors or when access to the subfloor cavity is limited, rigid foam insulation can be installed on the underside of the subfloor. The foam boards are attached using adhesive or mechanical fasteners, providing insulation and serving as a thermal barrier.
- Spray foam insulation in subfloor cavities: Spray foam insulation can be applied directly into the subfloor cavities, filling them completely and providing an effective air seal. This method helps prevent air leakage and provides superior insulation properties. However, professional installation is recommended for spray foam insulation.
3. Considerations for Moisture Control:
Moisture control is an important consideration when insulating the subfloor. It’s important to ensure that the subfloor and the insulation material are not exposed to moisture that could cause damage or mold growth. Proper ventilation, moisture barriers, and addressing any sources of moisture are crucial steps to prevent moisture-related issues.
Before insulating the subfloor, it’s recommended to consult with a professional or refer to relevant building codes and regulations. The insulation material and installation method should be chosen based on the specific requirements of your project and climate. Proper installation and attention to sealing, gaps, and coverage will ensure effective subfloor insulation that contributes to energy efficiency, comfort, and soundproofing in your space.
Common Issues and Troubleshooting
While a well-installed subfloor can provide a sturdy foundation for your flooring system, certain issues can arise over time that require attention and troubleshooting. By promptly identifying and addressing these issues, you can maintain the integrity and performance of your subfloor. Here are some common issues associated with subfloors and some troubleshooting tips:
1. Moisture Damage:
Moisture can pose a significant threat to subfloors, especially those made of wood-based materials like plywood or OSB. Prolonged exposure to moisture can cause swelling, warping, or delamination, resulting in an unstable or weakened subfloor. To troubleshoot moisture damage, it’s important to identify and address the source of moisture. Improve ventilation, address plumbing leaks promptly, and consider installing moisture barriers or proper waterproofing measures as necessary. Damaged sections of the subfloor may need to be replaced to ensure stability.
2. Subfloor Squeaks or Movement:
Squeaky or creaking subfloors can be caused by several factors, including the subfloor separating from the joists, loose fasteners, or inadequate adhesive. To troubleshoot subfloor squeaks or movement, locate the source by walking across the floor and pinpointing the areas of noise. Strengthen loose areas by adding additional fasteners such as screws or nails to reconnect the subfloor to the joists. If necessary, apply adhesive between the subfloor and joists to minimize movement and eliminate squeaks. Proper installation and securing of the subfloor during construction can help prevent these issues from occurring in the first place.
3. Uneven or Out-of-Level Subfloor:
An uneven or out-of-level subfloor can cause problems when installing flooring materials, resulting in an unsightly or unstable final flooring system. If you encounter an uneven subfloor, there are a few troubleshooting options. For plywood or OSB subfloors, shims can be used to level out low spots. Grinding or filling techniques can be employed for concrete subfloors. In more severe cases, professional help may be required to resurface or level the subfloor.
4. Subfloor Mold or Mildew:
Mold or mildew growth on the subfloor can not only compromise the structural integrity but also pose health risks. To troubleshoot mold or mildew, address the underlying moisture issue first. Improve ventilation, address leaks or excess humidity, and ensure proper drainage if applicable. Thoroughly clean the affected area using appropriate cleaning solutions and techniques, removing any visible mold or mildew. If the mold or mildew has penetrated into the subfloor, some sections may need to be replaced to ensure a mold-free environment.
5. Subfloor Damage from Pests:
Pests like termites or rodents can cause damage to subfloors, particularly if they have access to the floor cavities. If you suspect pest infestation, it’s important to address the issue promptly. Consult with pest control professionals to eradicate the pests and implement preventive measures to protect the subfloor and prevent future infestations. Depending on the severity of the damage, you may need to repair or replace sections of the damaged subfloor.
By promptly addressing these common issues, you can maintain the integrity and longevity of your subfloor. Regular inspection, proper maintenance, and attending to any signs of damage or problems will help ensure a stable and reliable foundation for your flooring system.
Read more: What Is Construction
Signs of a Damaged Subfloor
A subfloor is a crucial component of any building’s structure, providing stability and support for the flooring system. It’s important to be aware of the signs of a damaged subfloor so you can address issues promptly and prevent further damage. Here are some common signs that indicate a damaged subfloor:
1. Sagging or Uneven Floors: A subfloor that is damaged or weakened may lead to sagging or uneven floors. If you notice areas of the floor that dip or feel unsteady when walked upon, it may indicate structural issues with the subfloor.
2. Excessive Creaking or Squeaking: While some degree of noise is normal in floors, excessive creaking or squeaking may be a sign of a damaged subfloor. Loose fasteners, separated subfloor panels, or inadequate adhesive can cause these noises as the subfloor moves against the floor joists.
3. Bouncy or Soft Spots: When walking across the floor, if you feel areas that give a bouncy or spongy sensation, it may indicate a compromised subfloor. This can be due to moisture damage, weakened subfloor panels, or inadequate support from the floor joists.
4. Cupping or Buckling of Flooring Materials: Cupping or buckling of flooring materials, such as hardwood or laminate, is often a visible sign of moisture damage in the subfloor. Excessive moisture can cause the subfloor to swell or become uneven, leading to the distortion of the flooring materials.
5. Mold or Mildew Growth: If you notice mold or mildew growth on the surface of the subfloor or detect a musty odor in the room, it may indicate moisture infiltration and potential damage to the subfloor. Mold or mildew can compromise the integrity of the subfloor and pose health risks.
6. Visible Water Stains or Discoloration: Water stains or discoloration on the subfloor can indicate previous or ongoing moisture issues. This can weaken the subflooring material and lead to further damage if not addressed promptly.
7. Pests Infestation: Infestations by pests such as termites or rodents can cause significant damage to subfloors. Look for signs of termite tunnels, rodent droppings, or other indications of pest activity. These pests can weaken or consume the subfloor material, compromising its integrity.
If you notice any of these signs of a damaged subfloor, it’s important to take action. Consult with a professional contractor or flooring specialist to assess the extent of the damage and determine the necessary repairs or replacements. Addressing subfloor issues promptly will ensure the stability, longevity, and safety of your flooring system.
Repairing a Subfloor
Repairing a damaged subfloor is crucial for maintaining the structural integrity and stability of your flooring system. Whether the damage is due to moisture, pests, or general wear and tear, addressing it promptly is essential to prevent further deterioration. Here are some steps to guide you in repairing a damaged subfloor:
1. Assess the Extent of Damage:
Begin by assessing the extent of the damage. Inspect the subfloor for signs of moisture damage, pest infestation, or structural issues. Determine the areas that require repair or replacement, and evaluate whether the damage is localized or widespread.
2. Remove Damaged Subfloor Sections:
If the damage is limited to specific sections, carefully remove those portions of the subfloor. Use a circular saw, reciprocating saw, or other appropriate tools to cut out the damaged sections. Take care to avoid damaging surrounding subfloor or floor joists during the removal process.
3. Reinforce Floor Joists (if necessary):
If the floor joists show signs of damage or weakness, reinforcing them may be necessary. Install additional supports, such as sister joists or braces, to provide stability and strength to the floor structure. Consult with a professional contractor if you are unsure about the extent of reinforcement required.
4. Replace Subflooring:
Once the damaged sections are removed, cut replacement subfloor panels to fit the dimensions of the openings. The replacement panels should have the same thickness as the existing subfloor. Ensure a tight fit and proper alignment of the replacement panels to maintain structural integrity.
5. Secure Subfloor Panels:
Secure the replacement subfloor panels to the floor joists using appropriate fasteners such as screws or nails. Space the fasteners evenly along the panels, ensuring a secure attachment. Take care not to overdrive fasteners that could damage the subfloor or cause unevenness in the surface.
6. Level and Smooth the Surface:
If necessary, use a leveling compound or self-leveling underlayment to fill any gaps or unevenness between the subfloor panels. This will create a smooth and level surface for the installation of the final flooring material. Follow the manufacturer’s instructions for mixing and applying the leveling compound or self-leveling underlayment.
7. Install the Final Flooring:
Once the subfloor repair is complete and the surface is level and smooth, you can proceed with installing the final flooring material of your choice. Follow the manufacturer’s instructions for proper installation techniques and recommended adhesives or fasteners.
8. Address the Underlying Cause of Damage:
Lastly, it’s important to address the underlying cause of the subfloor damage to prevent future issues. Whether it’s addressing moisture problems, improving ventilation, or implementing pest control measures, take proactive steps to prevent further damage and protect the repaired subfloor.
Repairing a damaged subfloor requires careful planning, attention to detail, and adherence to proper construction techniques. If you are uncertain about the repair process, it is advisable to consult with a professional contractor or flooring specialist to ensure the repairs are carried out correctly.
By addressing subfloor damage promptly and effectively, you can maintain the stability and strength of your flooring system, ensuring a safe and durable foundation for your space.
Conclusion
A sturdy and well-maintained subfloor is the foundation of a successful flooring system. Understanding the purpose, installation methods, and materials used in subfloor construction is essential for a durable and long-lasting structure.
Throughout this article, we have explored various aspects of subfloors, including their definition, types of materials, installation methods, and common issues that may arise. Plywood, OSB, and concrete are popular choices for subflooring, each offering unique advantages and considerations.
Plywood subfloors are known for their dimensional stability, strength, and versatility. OSB subfloors are popular due to their affordability and structural strength. Concrete subfloors provide durability, moisture resistance, and excellent load-bearing capabilities.
When installing a subfloor, proper preparation and attention to detail are crucial. From subfloor insulation to troubleshooting common issues, it’s important to follow recommended guidelines and consult with professionals when necessary. Ensuring adequate ventilation, addressing moisture concerns, and maintaining a level and secure subfloor are key to the overall performance of the flooring system.
By staying vigilant and promptly addressing any signs of subfloor damage, such as sagging, squeaking, moisture damage, or pests, you can safeguard the stability and structural integrity of your flooring system. Repairing and reinforcing the subfloor as needed will prevent further deterioration and maintain a safe and reliable foundation for your space.
In conclusion, the subfloor is an indispensable component of any building structure. Its purpose goes beyond providing stability; it acts as a crucial foundation for the final flooring materials, contributing to the overall durability, performance, and aesthetics of the space. By understanding the intricacies of subfloor construction, selecting the appropriate materials, and following proper installation and maintenance practices, you can ensure a solid foundation that withstands the test of time.
Frequently Asked Questions about What Is A Subfloor In Construction
Was this page helpful?
At Storables.com, we guarantee accurate and reliable information. Our content, validated by Expert Board Contributors, is crafted following stringent Editorial Policies. We're committed to providing you with well-researched, expert-backed insights for all your informational needs.
0 thoughts on “What Is A Subfloor In Construction”