Home>diy>Building & Construction>What Is A Tieback In Construction
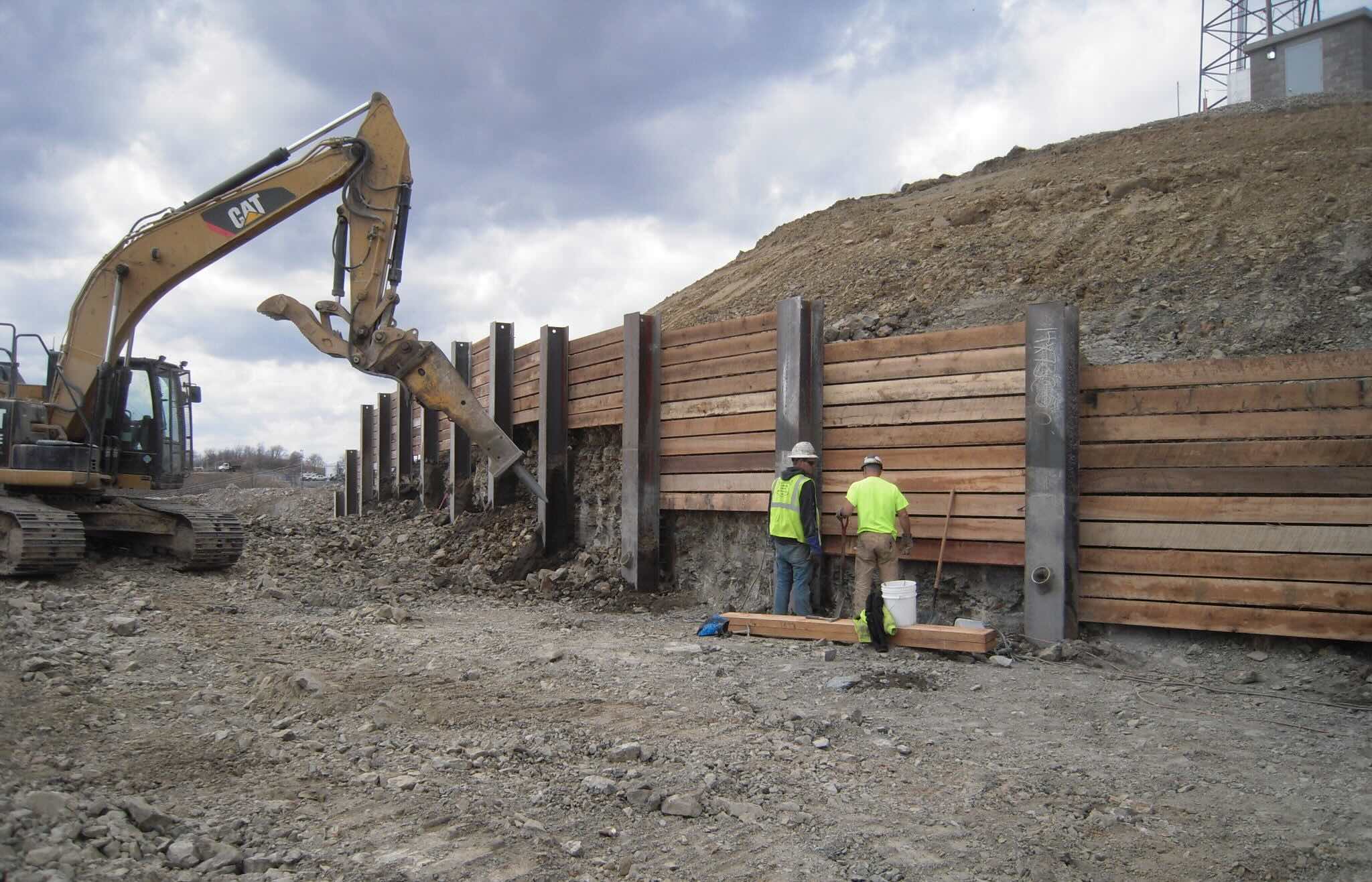
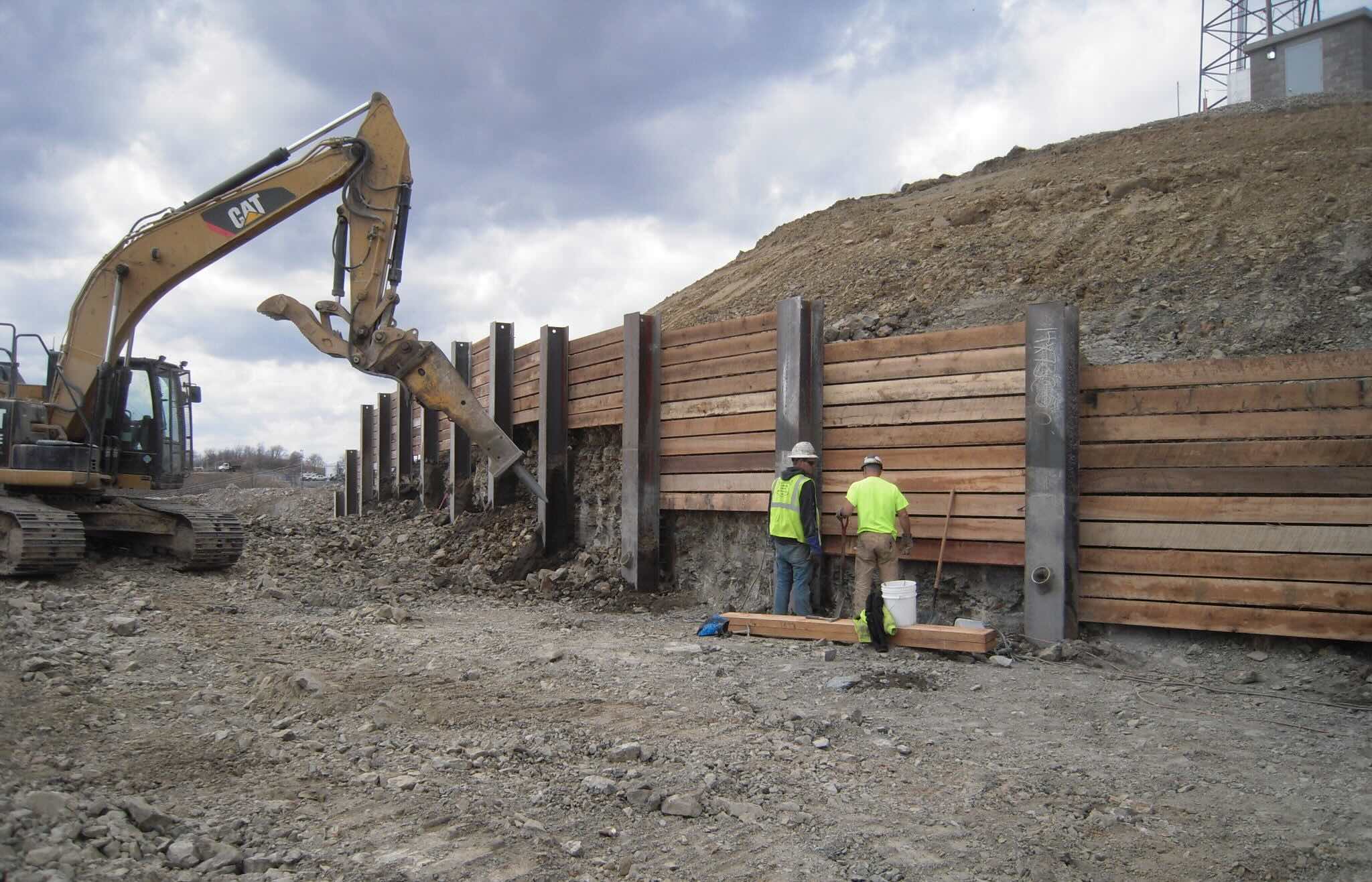
Building & Construction
What Is A Tieback In Construction
Modified: December 7, 2023
Learn about tiebacks in construction, an essential technique used in building construction projects. Discover their purpose and benefits in ensuring structural stability.
(Many of the links in this article redirect to a specific reviewed product. Your purchase of these products through affiliate links helps to generate commission for Storables.com, at no extra cost. Learn more)
Introduction
Welcome to the world of construction, where every project is a masterpiece in progress. In the realm of building construction, there are numerous techniques and methodologies that ensure structural stability and longevity. One such technique that plays a crucial role in many construction projects is tiebacks.
Tiebacks are a fundamental element in the construction industry, providing reinforcement and stability to various structures. Whether it’s a high-rise building, a retaining wall, or a bridge, tiebacks are indispensable in maintaining structural integrity.
In this article, we will delve into the world of tiebacks in construction, exploring their definition, purpose, installation process, design considerations, challenges, and case studies to provide you with a comprehensive understanding of this crucial construction element.
So, let’s strap ourselves in and embark on this journey to discover the intriguing world of tiebacks.
Key Takeaways:
- Tiebacks are crucial in construction, providing stability to structures like retaining walls and foundations. They offer design flexibility, cost-effectiveness, and play a vital role in securing iconic projects like the Brooklyn Bridge and the Hoover Dam Bypass.
- The installation process and design considerations for tiebacks require careful planning and analysis of soil and load conditions. While tiebacks offer numerous benefits, challenges such as site constraints, ground conditions, and maintenance requirements need to be carefully considered for successful implementation.
Read more: How To Make Tiebacks For Drapes
Definition of Tieback in Construction
Before we dive into the intricacies of tiebacks, let’s define what exactly they are in the context of construction.
A tieback, also known as an anchor or ground anchor, is a structural element used to provide lateral support and prevent the movement or failure of a retaining wall, foundation, or other similar structures. It consists of a tendon, typically made of steel, that is installed into the ground and connected to the structure being supported.
The purpose of a tieback is to transfer the tensile forces created by soil pressure or external loads back into the ground, thereby improving stability and preventing excessive movement or deformation of the structure. Tiebacks are typically used in situations where space limitations or soil conditions make other support methods, such as braces or piles, impractical or uneconomical.
Tiebacks work on the principle of soil anchoring, where the load is transmitted to the surrounding soil through friction and mechanical interlock between the tendon and the ground. The tendon is often encased in grout or a sheath to enhance its performance and protect it from corrosion.
Now that we have a clear understanding of what a tieback is, let’s explore the purpose and benefits of incorporating tiebacks in construction projects.
Purpose and Benefits of Tiebacks
Tiebacks serve a crucial purpose in construction projects by providing additional support and stability to structures. Let’s explore some of the key benefits and purposes of integrating tiebacks into construction:
- Retaining Wall Stability: One of the primary purposes of tiebacks is to enhance the stability of retaining walls. These walls are utilized to retain soil behind them and prevent slope failure. Tiebacks anchor the wall to the surrounding soil, counteracting the lateral forces exerted by the retained soil and ensuring the wall remains intact.
- Foundation Support: Tiebacks can also be used to provide additional support to foundations, particularly in areas with expansive or unstable soil. They help distribute the vertical loads from the structure to a larger soil area, reducing the risk of settlement and ensuring the stability of the foundation.
- Prevention of Wall Movement: In situations where there is a possibility of wall movement due to external forces or soil pressures, tiebacks can prevent such movement by restraining the wall. This is especially crucial for structures located in areas prone to seismic activity or where there is a need to withstand high wind loads.
- Increased Design Flexibility: Incorporating tiebacks into a construction project provides designers with increased flexibility in creating efficient and cost-effective structures. The use of tiebacks allows for the construction of taller and thinner walls, which can help save space and reduce the overall cost of the project.
- Cost-Effective Solution: Tiebacks often offer a cost-effective solution compared to alternative methods of support, such as deep foundations or additional excavation. By utilizing tiebacks, construction projects can save on material and labor costs, making them an attractive option for many projects.
The utilization of tiebacks in construction projects offers various benefits, including enhanced stability, increased flexibility, and cost-effectiveness. Now that we understand the purpose and benefits of tiebacks, let’s explore the different types of tiebacks commonly used in the construction industry.
Types of Tiebacks
When it comes to tiebacks in construction, different types of tiebacks are available to suit various structural and environmental conditions. Let’s take a closer look at the most common types of tiebacks:
- Passive Tiebacks: Passive tiebacks, also known as deadman tiebacks, rely on the passive resistance of the soil to anchor the structure. These tiebacks consist of a tendon, typically made of steel, connected to the structure and extending into the soil. The tendon is anchored at one end and is placed in a trench or drilled hole in the ground. Passive tiebacks are primarily used in situations where the soil conditions are stable and can provide the necessary resistance.
- Active Tiebacks: Active tiebacks, also known as live tiebacks, actively exert force on the soil to provide support. They consist of a tendon that is tensioned after installation to induce pressure on the soil. The tension is maintained throughout the life of the structure to ensure stability. Active tiebacks are commonly used in situations where the soil conditions are less stable and require constant reinforcement.
- Temporary Tiebacks: Temporary tiebacks are used during the construction phase to provide temporary support to structures or excavation walls. These tiebacks are typically removed once the permanent support system is installed. Temporary tiebacks offer flexibility and ease of installation, allowing construction activities to proceed efficiently.
- Permanent Tiebacks: Permanent tiebacks are designed to provide long-term stability to structures. These tiebacks are installed as part of the permanent support system and remain in place throughout the life of the structure. Permanent tiebacks are commonly used for retaining walls, foundation support, and other critical structures where long-term stability is essential.
- Soil Nailing: Soil nailing is a specialized technique that involves the installation of tiebacks into the soil to stabilize slopes or excavations. In this method, steel bars or anchors are drilled into the unstable soil, and then a reinforcing mesh is attached to the bars. The tiebacks provide reinforcement to the soil, preventing further slope movement or failure.
- Anchored Sheet Piles: Anchored sheet piles are used in situations where sheet pile walls require additional support to resist horizontal forces. In this method, tiebacks are installed to anchor the sheet piles to the surrounding soil, increasing the overall stability of the wall.
Each type of tieback has its advantages and is selected based on the specific requirements of the project. Now that we have explored the different types of tiebacks, let’s move on to understanding the installation process of tiebacks in construction.
Installation Process of Tiebacks
The installation process of tiebacks in construction involves several steps to ensure proper anchoring and stability. Let’s walk through the general process of installing tiebacks:
- Site Preparation: Before installing tiebacks, the site needs to be properly prepared. This includes clearing the area of any obstructions, excavating the necessary trenches or holes, and ensuring the soil is appropriately compacted.
- Drilling or Excavation: Depending on the type of tieback and soil conditions, holes or trenches may need to be drilled or excavated. This is done using specialized equipment such as drilling rigs or excavators. The depth and spacing of the tieback holes are determined by the design requirements and the specific project conditions.
- Tendon Installation: Once the holes or trenches are prepared, the tendon is installed. The tendon, typically made of high-strength steel, is inserted into the hole or trench and secured at the anchor end. The other end is connected to the structure that requires support.
- Grouting or Corrosion Protection: In some cases, the tendon may be encased in grout or a protective sheath to enhance its performance and protect it from corrosion. This helps improve the bond between the tendon and the surrounding soil, ensuring effective load transfer.
- Tensioning: Active tiebacks require tensioning to exert force on the soil and provide support. This is typically done using hydraulic jacks or other specialized equipment. The tension applied to the tendon should be carefully controlled to prevent overloading or failure.
- Testing and Monitoring: Once the tiebacks are installed and tensioned, they are subjected to testing and monitoring. This ensures that the tiebacks meet the required load capacity and performance standards. Monitoring systems, such as strain gauges or inclination sensors, may be installed to continuously monitor the behavior and performance of the tiebacks.
- Backfilling and Site Restoration: After the tiebacks are installed and properly tested, the excavated holes or trenches are backfilled with suitable materials, ensuring proper compaction. The site is then restored to its original condition, including the restoration of any disturbed landscaping or structures.
It is important to note that the installation process of tiebacks may vary depending on the specific project requirements, soil conditions, and design specifications. Professional engineers and specialized contractors play a crucial role in ensuring the proper installation and performance of tiebacks.
Now that we have explored the installation process of tiebacks, let’s move on to discussing some important design considerations for tiebacks in construction.
A tieback in construction is a structural element used to support retaining walls, excavations, or other ground structures. It provides lateral support to prevent soil movement and maintain stability.
Read more: What Is Pre-Construction In Construction
Design Considerations for Tiebacks
Designing tiebacks in construction requires careful consideration of various factors to ensure their effectiveness and long-term stability. Here are some important design considerations for tiebacks:
- Soil Analysis: A thorough analysis of the soil conditions is crucial for designing tiebacks. The properties of the soil, including its strength, permeability, and stability, will determine the appropriate type of tieback and the required load capacity.
- Load Analysis: The loads that the tiebacks will bear, including soil pressures, live loads, and seismic forces, must be accurately determined. This allows the engineer to design tiebacks with the appropriate capacity to resist these loads without compromising the stability of the structure.
- Tieback Spacing: The spacing between tiebacks is an essential consideration to ensure uniform distribution of forces along the structure. Closer spacing may be required in areas with higher soil pressures or to control wall movement, while wider spacing may be suitable in stable soil conditions.
- Corrosion Protection: If the tieback tendon is exposed to corrosive elements, appropriate corrosion protection measures, such as protective coatings or grout encasement, should be incorporated into the design. This helps prevent deterioration and ensures the long-term performance of the tiebacks.
- Anchor Design: The design of the anchor or termination point of the tieback is critical to ensure proper load transfer from the structure to the tieback tendon. The anchor should be capable of accommodating the expected forces and should be properly installed and tested to ensure its reliability.
- Consideration of Surcharge Loads: Surcharge loads, such as adjacent structures, vehicles, or heavy equipment, should be taken into account in tieback design. These additional loads can impact the stability of the structure and should be accounted for to ensure the tiebacks can withstand the combined forces.
- Construction Sequence: The construction sequence, including the timing of tieback installation and the sequence of excavation and backfilling, should be carefully planned to minimize the risk of ground movements or instability during construction.
- Monitoring and Maintenance: Designing an effective monitoring system during construction and throughout the life of the structure is crucial. Regular inspections and maintenance of the tiebacks are essential to identify any potential issues or deterioration in a timely manner and ensure continued performance.
By considering these important design factors, engineers can develop safe and efficient tieback systems that provide the necessary support and stability to construction projects. Now that we have discussed the design considerations, let’s explore the challenges and limitations associated with tiebacks.
Challenges and Limitations of Tiebacks
While tiebacks are a valuable support system in construction, they do come with certain challenges and limitations that need to be considered. Let’s explore some of the common challenges and limitations associated with tiebacks:
- Site Constraints: The installation of tiebacks may be limited by site constraints such as underground utilities, obstructions, or limited access. These constraints can hinder the proper installation and may require alternative support methods or modifications to the design.
- Ground Conditions: The behavior of the soil can present challenges in tieback design. Unstable or weak soil conditions may reduce the load-bearing capacity of the tiebacks and require additional measures, such as soil improvement or alternate support systems.
- Corrosion and Deterioration: Tiebacks that are exposed to corrosive environments, such as marine or high chloride areas, may be susceptible to corrosion. Regular inspection and maintenance are required to ensure the integrity of the tiebacks and to address any corrosion or deterioration issues in a timely manner.
- Load Requirements: In some cases, the required load capacity for tiebacks may be significant, especially for structures subjected to high lateral forces or heavy loads. Ensuring that tiebacks can withstand these loads without excessive deformation or failure requires careful design and selection of suitable materials and components.
- Construction Interference: Construction activities adjacent to existing structures may interfere with the installation or performance of tiebacks. The impact of nearby excavations or vibrations from construction equipment on the stability of the tiebacks needs to be carefully considered and mitigated.
- Maintenance and Monitoring: Tiebacks require regular maintenance and monitoring to ensure their ongoing performance. This includes inspections, load testing, and addressing any potential issues promptly. The cost and effort associated with maintenance can be a limitation in some projects.
- Cost Considerations: The cost of designing and installing tiebacks can be substantial, especially in projects with complex soil conditions or large load requirements. The cost-effectiveness of tiebacks needs to be evaluated against alternative support systems or construction methods to determine their feasibility.
While tiebacks offer significant benefits in many construction scenarios, it is essential to evaluate the challenges and limitations associated with their use. This allows engineers and project teams to make informed decisions and implement appropriate measures to address any potential issues.
Now, let’s examine some case studies and examples to understand how tiebacks have been successfully implemented in real-world construction projects.
Case Studies and Examples
To truly understand the effectiveness and versatility of tiebacks in construction, let’s explore a few case studies and examples:
1. Brooklyn Bridge, New York City: The iconic Brooklyn Bridge is an impressive example of how tiebacks played a vital role in the construction of this historic structure. The bridge’s stone towers are supported by a series of tieback rods that anchor into bedrock. These tiebacks provide additional stability and prevent excessive movement of the towers due to wind and traffic loads.
2. Dubai Metro Red Line Extension: The Dubai Metro Red Line Extension project utilized tiebacks to provide lateral support to excavation walls during the construction of underground stations. Temporary tiebacks were installed to prevent soil movement and maintain stability during the construction process. This allowed for efficient and safe excavation activities, ensuring the successful completion of the project.
3. Seattle Seawall Replacement, Washington: The replacement of the aging seawall in Seattle incorporated tiebacks to reinforce the new structure. In this project, tiebacks were installed to provide lateral support and prevent movement of the new seawall due to wave forces and soil pressure. The tiebacks enabled the construction of a structurally sound and durable seawall, protecting the shoreline and enhancing resiliency against coastal erosion.
4. Hoover Dam Bypass, Nevada-Arizona: The construction of the Hoover Dam Bypass involved the use of tiebacks to stabilize the deep excavations and retain the surrounding rock mass. Long-term, permanent tiebacks were installed to provide support to the retaining walls along the steep slopes. These tiebacks ensured the safety and stability of the bypass structure, allowing for the efficient and successful completion of the project.
These case studies demonstrate the versatility and effectiveness of tiebacks in a variety of construction projects. Whether it’s supporting iconic bridges, securing underground structures, reinforcing seawalls, or stabilizing slopes, tiebacks have proven to be a reliable and efficient support system.
As we conclude our exploration of tiebacks in construction, let’s recap what we’ve learned and highlight their significance.
Conclusion
Tiebacks are a fundamental component in the world of construction, providing crucial reinforcement and stability to various structures. From retaining walls and foundations to bridge abutments and excavation support systems, tiebacks play a vital role in maintaining structural integrity and preventing movement or failure.
In this article, we defined tiebacks as structural elements used to provide lateral support, discussed their purpose and benefits, explored different types of tiebacks, and examined the installation process and design considerations associated with them. We also highlighted the challenges and limitations that come with the use of tiebacks and showcased several case studies where tiebacks have been successfully implemented in real-world construction projects.
By incorporating tiebacks, construction projects can enjoy increased stability, design flexibility, and cost-effectiveness. Tiebacks allow for the construction of taller and thinner structures, provide additional support to foundations and retaining walls, and enable engineers to mitigate challenging soil conditions.
While tiebacks bring numerous advantages, it’s essential to consider site constraints, ground conditions, and maintenance requirements. Designing and implementing tiebacks require careful planning, proper analysis of soil and load conditions, and regular monitoring to ensure their long-term performance.
With an array of successful applications, from iconic bridges to underground structures, tiebacks demonstrate their effectiveness and reliability in securing and enhancing the resilience of diverse construction projects.
As construction continues to evolve, tiebacks will remain an integral part of the industry, providing the necessary support and stability needed for safe and successful project completion. So, the next time you walk across a bridge or admire a towering building, remember that tiebacks are working behind the scenes, ensuring the integrity and longevity of these impressive structures.
Frequently Asked Questions about What Is A Tieback In Construction
Was this page helpful?
At Storables.com, we guarantee accurate and reliable information. Our content, validated by Expert Board Contributors, is crafted following stringent Editorial Policies. We're committed to providing you with well-researched, expert-backed insights for all your informational needs.
0 thoughts on “What Is A Tieback In Construction”