Home>diy>Building & Construction>What Is CMU In Construction
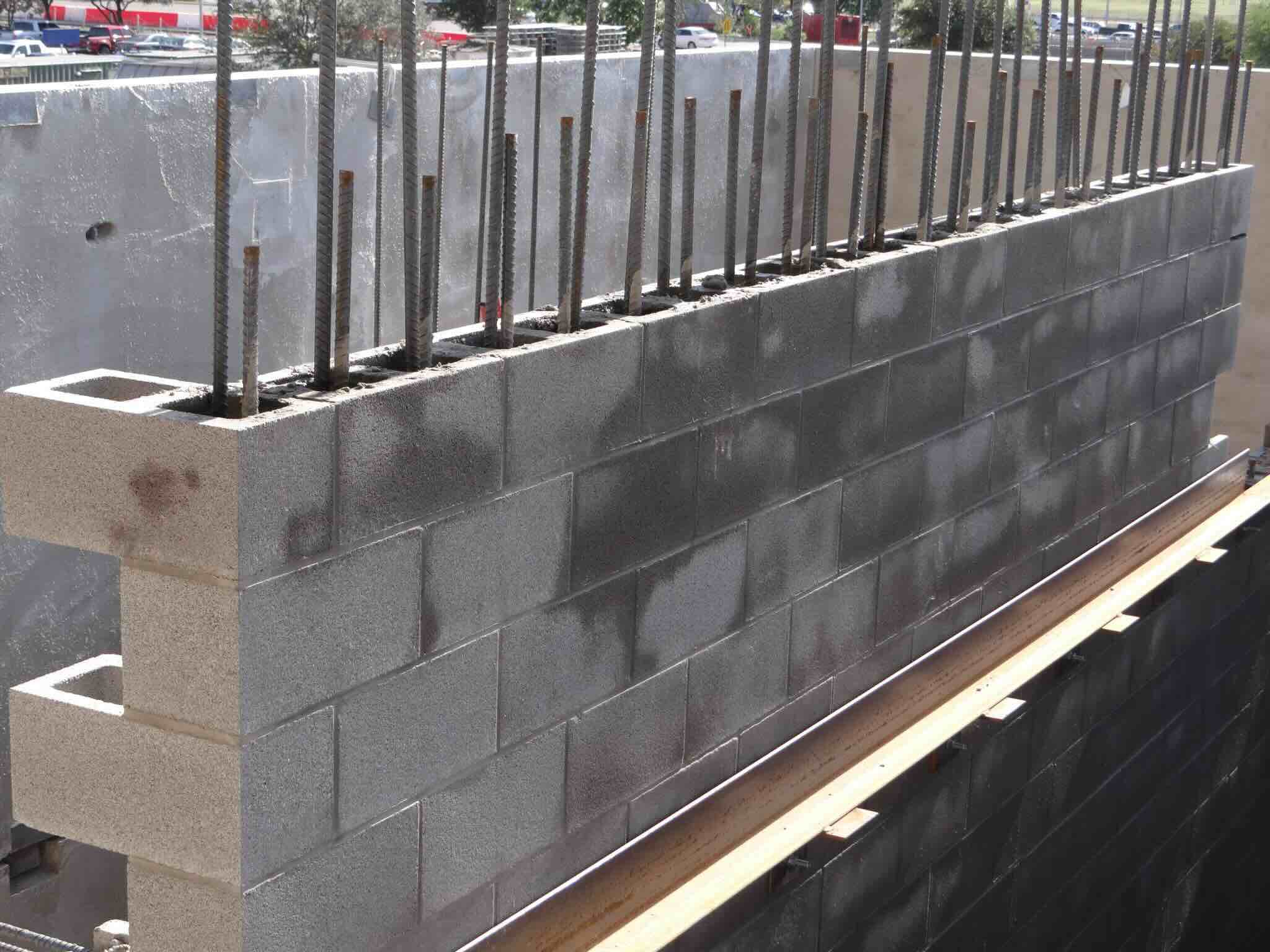
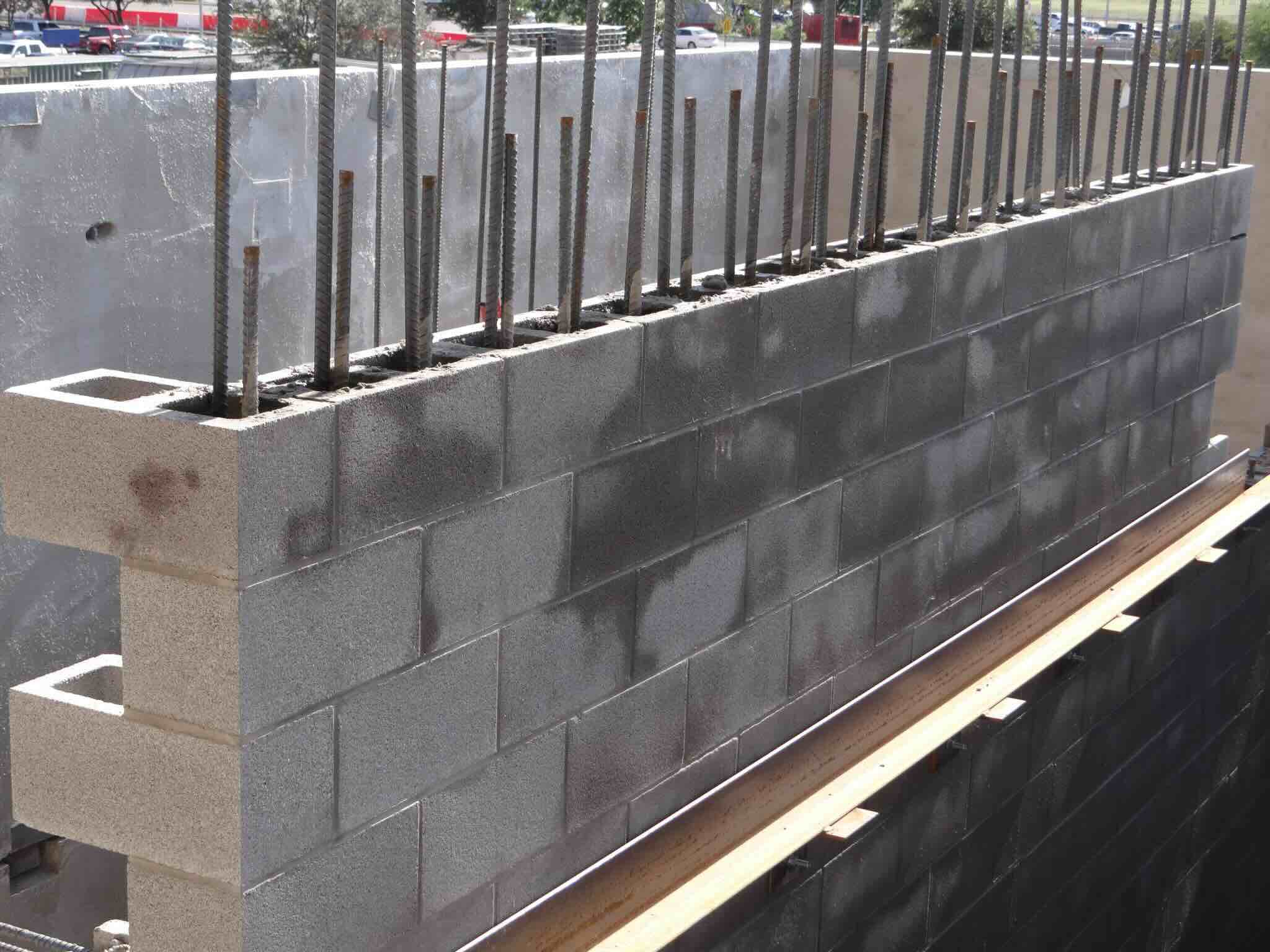
Building & Construction
What Is CMU In Construction
Modified: May 6, 2024
Discover what CMU (Concrete Masonry Unit) is in the context of building construction. Learn about its uses, benefits, and importance in creating durable structures.
(Many of the links in this article redirect to a specific reviewed product. Your purchase of these products through affiliate links helps to generate commission for Storables.com, at no extra cost. Learn more)
Introduction
When it comes to building construction, there are various elements and materials that play a crucial role in determining the strength, durability, and overall quality of the structure. One such material is CMU, which stands for Concrete Masonry Unit. CMU is a commonly used building material in construction projects due to its versatility, affordability, and numerous advantages.
CMU, also known as concrete block or cinder block, is a prefabricated construction material made from a mixture of cement, aggregates, and water. It is formed into rectangular or square blocks and cured to achieve the desired strength and durability.
In this article, we will explore the definition of CMU, its composition and characteristics, common uses in construction, advantages and disadvantages, different types, manufacturing process, construction techniques, and provide some tips for working with CMU. By the end of this article, you will have a comprehensive understanding of CMU and its significance in the construction industry.
Key Takeaways:
- CMU, or Concrete Masonry Unit, is a versatile and durable building material used in construction for its strength, fire resistance, and design flexibility, making it a popular choice for various architectural and structural needs.
- Understanding the composition, characteristics, types, manufacturing process, and construction techniques of CMU is essential for architects, builders, and construction professionals to make informed decisions and ensure successful implementation in their projects.
Definition of CMU
CMU, which stands for Concrete Masonry Unit, refers to a prefabricated construction material commonly known as concrete block or cinder block. It is a standardized building element made from a mixture of Portland cement, aggregates (such as sand or gravel), and water. CMU blocks are available in various sizes, shapes, and configurations to accommodate different construction requirements.
CMU blocks are manufactured through a process called concrete masonry production. This process involves mixing the ingredients in a specific ratio to achieve the desired consistency. The mixture is then poured into molds and cured under controlled conditions. Once cured, the blocks are ready for use in construction projects.
The primary function of CMU blocks is to provide structural support and form the exterior or interior walls of a building. They can also be used for partitions, retaining walls, and other load-bearing applications. CMU blocks offer a combination of strength, durability, fire resistance, thermal insulation, and soundproofing properties, making them a popular choice in the construction industry.
CMU is a versatile building material that can be used in various construction methods, including load-bearing walls, reinforced masonry walls, and cavity walls. It can be combined with other construction materials, such as steel reinforcement, to enhance its structural capabilities. The flexibility of CMU allows architects and builders to create aesthetically pleasing designs while ensuring the strength and stability of the structure.
Overall, CMU is a fundamental component of modern construction, widely used in residential, commercial, and industrial projects. Its reliability, affordability, and versatility make it a preferred choice for builders and architects alike. With its extensive range of sizes, shapes, finishes, and colors, CMU offers endless design possibilities while meeting the functional and structural requirements of any construction project.
Composition and Characteristics of CMU
CMU, or Concrete Masonry Unit, is composed of a mixture of Portland cement, aggregates, and water. The cement acts as the binding agent, while the aggregates provide strength and stability to the structure. The exact proportions of cement and aggregates may vary depending on the specific application and desired properties of the CMU blocks.
The aggregates used in CMU can include sand, gravel, crushed stone, or a combination of these materials. The size and grading of the aggregates are important factors in determining the strength and density of the CMU blocks. Finer aggregates can result in smoother finishes, while coarser aggregates contribute to a more textured appearance.
One of the key characteristics of CMU is its versatility in terms of shape and size. CMU blocks come in various dimensions, including standard sizes such as 8-inch, 10-inch, and 12-inch widths, and heights ranging from 4 inches to 16 inches. This allows for flexibility in designing and constructing walls of different thicknesses and dimensions.
In addition to its flexibility, CMU offers several other desirable characteristics. Firstly, CMU blocks have excellent fire resistance properties, making them suitable for use in fire-rated walls and structures. They can withstand high temperatures for extended periods without losing their structural integrity.
Secondly, CMU provides good thermal insulation. The air pockets created by the voids in the blocks help to reduce heat transfer, keeping buildings cool in summer and warm in winter. This energy-efficient feature can contribute to lower heating and cooling costs.
Furthermore, CMU has good sound insulation properties. The density and mass of the blocks help to absorb and block sound transmission, resulting in quieter indoor environments. This is particularly beneficial in residential and commercial buildings where noise control is important.
CMU is also highly durable and resistant to environmental factors, including moisture, pests, and weathering. Its robust construction ensures long-lasting performance and minimal maintenance requirements. Additionally, CMU blocks can be manufactured with different surface finishes, such as smooth, textured, or split-face, to meet specific design preferences.
Overall, CMU combines strength, durability, fire resistance, thermal insulation, soundproofing capabilities, and design versatility. These characteristics make CMU a popular choice in the construction industry for a wide range of applications, from residential buildings to commercial complexes and industrial facilities.
Common Uses of CMU in Construction
CMU, or Concrete Masonry Unit, is a widely used building material in construction due to its versatility and numerous advantages. Here are some common applications of CMU in construction:
- Exterior and Interior Walls: CMU blocks serve as the primary building blocks for constructing walls in residential, commercial, and industrial structures. They provide structural support, act as a barrier against elements, and contribute to the overall stability and strength of the building.
- Load-Bearing Walls: CMU walls can bear heavy loads and distribute the weight to the foundation. They are commonly used in low-rise buildings, such as single-family homes, schools, and office buildings, to provide structural support.
- Partition Walls: CMU blocks can be used to create interior partition walls, dividing spaces into rooms or sections. These walls help to define different areas within a structure and offer privacy and soundproofing capabilities.
- Retaining Walls: CMU blocks are ideal for constructing retaining walls, which are designed to hold back soil or other materials. Retaining walls provide stability to sloping landscapes, prevent erosion, and create terraced areas for landscaping or building purposes.
- Facades: CMU blocks can be used as an architectural feature to enhance the aesthetic appeal of a building. They can be combined with other materials, such as brick veneer or architectural precast concrete panels, to create visually appealing facades.
- Foundations: CMU blocks are commonly used in foundation walls, providing a stable and durable base for the entire structure. The strength and durability of CMU blocks make them suitable for supporting the weight of the building and protecting against soil moisture.
- Soundproof Rooms: CMU walls offer excellent sound insulation properties, making them ideal for constructing rooms where noise control is essential. This is particularly valuable in buildings such as recording studios, theaters, or conference rooms.
- Fire-Rated Walls: CMU blocks have excellent fire resistance properties, making them an ideal choice for constructing fire-rated walls. Fire-rated walls are designed to contain the spread of fire and provide protection to occupants and neighboring structures.
These are just a few examples of the many applications of CMU in construction. With its strength, durability, versatility, and wide range of sizes and finishes, CMU continues to be a preferred building material for various architectural and structural needs.
Advantages and Disadvantages of CMU Construction
CMU, or Concrete Masonry Unit, construction offers several advantages and disadvantages that should be considered when selecting it as a building material:
Read more: What Is Pre-Construction In Construction
Advantages:
- Strength and Durability: CMU blocks are known for their strength and durability, making them suitable for load-bearing applications. They can withstand adverse weather conditions, impact, and wear, ensuring long-lasting performance.
- Fire Resistance: CMU construction provides excellent fire resistance. CMU blocks can withstand high temperatures for extended periods without losing their structural integrity, making them a safe choice for fire-rated walls.
- Thermal Insulation: CMU blocks offer good thermal insulation properties. The air pockets created by the voids in the blocks help to reduce heat transfer, resulting in energy-efficient buildings and reduced heating and cooling costs.
- Soundproofing: CMU walls have good sound insulation capabilities, reducing noise transmission between rooms or from external sources. This is particularly beneficial in residential and commercial buildings where noise control is important.
- Resistance to Pests and Moisture: CMU blocks are resistant to pests, such as termites, and do not provide a food source or nesting area. They are also highly resistant to moisture, minimizing the risk of water damage and mold growth.
- Versatility in Design: CMU blocks come in various sizes, shapes, and finishes, allowing for flexibility in architectural design. They can be combined with other materials to create unique patterns, textures, and color schemes.
- Economical: CMU construction is generally more cost-effective compared to other building systems. The availability of the material, simplicity of installation, and durability contribute to its affordability.
Disadvantages:
- Weight: CMU blocks are heavy, which can pose challenges during transportation, handling, and installation. Additional structural support may be required to accommodate the weight of the blocks.
- Limited Insulation: While CMU blocks provide some level of thermal insulation, they are not as efficient as other insulation materials. Supplementary insulation methods may be needed to achieve higher energy efficiency.
- Construction Time: CMU construction can take longer compared to lightweight building systems. The curing time of the blocks and the skill required for precise installation can extend the construction timeline.
- Precision and Skill: Proper installation of CMU blocks requires skill and attention to detail. Any errors in alignment or mortar application can compromise the structural integrity of the walls.
- Maintenance: While CMU blocks are durable, they may require regular maintenance to address cracking, chipping, or staining. Regular inspections and repairs are essential to maintain the appearance and performance of the CMU walls.
- Consideration of Thermal Movement: CMU walls may experience thermal expansion and contraction, leading to cracking over time. Proper design considerations and the use of expansion joints can help mitigate this issue.
When considering CMU construction, weighing the advantages and disadvantages is crucial to determine if it aligns with the specific requirements of the project. Consulting with architects and builders can provide valuable insights and help make an informed decision.
Different Types of CMU
CMU, or Concrete Masonry Unit, is available in various types, each offering unique characteristics and applications. Here are some of the different types of CMU:
- Standard CMU: Standard CMU blocks have a rectangular shape and are available in different sizes, such as 8-inch, 10-inch, and 12-inch widths, and heights ranging from 4 inches to 16 inches. They are commonly used in general construction projects for load-bearing and non-load-bearing walls.
- Solid CMU: Solid CMU blocks are denser and heavier compared to standard CMU. They have a solid core without any voids or cavities. Solid CMU blocks offer enhanced structural strength and are often used in areas that require increased load-bearing capacity.
- Hollow CMU: Hollow CMU blocks, also known as cavity blocks, have one or more hollow cores inside, which reduce the weight of the block while maintaining its strength. These hollow cores can be used to run pipes, electrical conduits, or provide additional insulation. Hollow CMU is commonly used in both load-bearing and non-load-bearing walls.
- Architectural CMU: Architectural CMU blocks are designed to offer aesthetic appeal in addition to their functional properties. They come in various textures, finishes, and colors, allowing architects and builders to create visually pleasing designs. Architectural CMU is often chosen for its decorative purposes in facades and accent walls.
- Lintel CMU: Lintel CMU blocks are specifically designed with an integrated steel reinforcement, typically called a lintel, to support the load of openings such as doors and windows. This eliminates the need for installing separate lintels, simplifying construction and ensuring structural stability.
- Split-Face CMU: Split-face CMU blocks have a textured surface that is achieved by splitting or scoring one or both faces of the block during the manufacturing process. The textured surface provides a visually appealing finish without requiring additional surface treatments or finishes.
- Grouted CMU: Grouted CMU refers to the construction technique of filling the cores of the CMU blocks with grout, a cementitious mix. This adds strength, stability, and fire resistance to the walls. Grouted CMU walls are commonly used in areas that require enhanced structural integrity and fire-rated partitions.
These are just a few examples of the different types of CMU available in the construction industry. It’s important to choose the appropriate type based on the specific requirements of the project, including load-bearing capacity, aesthetics, weather resistance, and fire rating.
CMU stands for Concrete Masonry Unit, which is a standard size rectangular block used in building construction. It is a versatile and durable material for walls, partitions, and structural components.
Manufacturing Process of CMU
The manufacturing process of CMU, or Concrete Masonry Unit, involves a series of steps to produce the blocks used in construction. Here is an overview of the typical manufacturing process:
- Batching: The process begins with batching, where the raw materials are measured and combined in specific proportions. The main ingredients include Portland cement, aggregates (such as sand, gravel, or crushed stone), and water. The precise ratios of the materials depend on the desired strength and characteristics of the CMU blocks.
- Mixing: Once the materials are batched, they are combined in a mixing machine to create a homogenous mixture. The mixing process ensures that all the ingredients are evenly distributed, resulting in consistent quality throughout the batch.
- Molding: The mixed material is then transferred to a block molding machine. The machine consists of a mold or molds with the desired shape and size of the CMU blocks. The mixture is poured into the molds and compacted to remove air voids and ensure proper alignment and consistency.
- Curing: After molding, the blocks are left in the molds for a specific period to cure and gain strength. Curing can be done through various methods, including air drying, steam curing, or using curing chambers. The duration of curing depends on factors such as the type of cement used and specific project requirements.
- Demolding: Once the blocks have reached the desired strength, they are removed from the molds. This is done carefully to avoid any damage to the blocks. Demolding can be done manually or using automated equipment depending on the scale of production.
- Finishing: After demolding, the CMU blocks may undergo additional finishing processes. This can include smoothing the surface, adding texture or patterns, or applying surface treatments such as paint or coatings. Finishing processes are often done to enhance the aesthetics of the blocks or provide specific functional properties.
- Packaging and Distribution: Once the CMU blocks are finished, they are packaged and prepared for distribution. They are typically palletized and wrapped to protect them during transportation. The blocks are then distributed to construction sites or suppliers for use in building projects.
The manufacturing process of CMU combines precision, quality control, and careful handling to produce durable and reliable building blocks. It is important for manufacturers to adhere to industry standards and guidelines to ensure the blocks meet the required specifications and performance criteria.
By following these manufacturing processes, CMU manufacturers can produce high-quality blocks that meet the construction industry’s needs for strength, durability, and versatility.
Read more: What Is Construction
CMU Construction Techniques
CMU, or Concrete Masonry Unit, construction involves various techniques to ensure the proper installation and assembly of CMU blocks. These techniques play a crucial role in achieving structural integrity, stability, and longevity. Here are some common CMU construction techniques:
- Mortar Bedding: The most widely used technique in CMU construction is mortar bedding. It involves applying a layer of mortar on the foundation or footing, followed by carefully laying the CMU blocks in a staggered pattern. The blocks are pressed into the mortar bed and leveled to ensure they are aligned and plumb.
- Vertical Reinforcement: To reinforce CMU walls and enhance their structural strength, vertical reinforcement is often incorporated. Reinforcing bars, commonly known as rebar, are inserted vertically into the hollow cores of the CMU blocks. The rebar is then secured with grout or mortar to provide additional reinforcement against lateral forces.
- Horizontal Bond Beams: Bond beams are horizontal reinforcing elements that run through the top course of the CMU wall. These beams are created by filling the hollow cores of the top course with grout and inserting horizontal reinforcement bars. Bond beams help to distribute loads and provide added stability to the wall.
- Collar Joints: Collar joints are horizontal mortar joints that are reinforced with steel reinforcement to enhance the strength and stability of the wall. These joints are typically formed by inserting ladder-shaped reinforcement into the mortar joints at specific intervals.
- Masonry Veneer: In some cases, CMU walls are combined with masonry veneer to achieve architectural aesthetics. The CMU wall provides the structural support, while the masonry veneer, such as brick or stone, is applied as a decorative facing material. This technique combines the durability and strength of CMU with the visual appeal of the masonry veneer.
- Control Joints: Control joints are intentional breaks in the CMU wall that allow for movement and control cracking. These joints are usually spaced at regular intervals and are filled with a flexible sealant to accommodate thermal expansion and contraction.
- Grouting: Grouting is the process of filling the voids or cores of the CMU blocks with a cementitious mixture. This technique provides increased strength, stability, and fire resistance to the CMU walls. Grouting is commonly used in load-bearing walls or areas that require enhanced structural integrity.
Proper execution of these construction techniques is essential to ensure a well-constructed and durable CMU wall. Skillful placement of CMU blocks, careful application of mortar, reinforcement installation, and attention to detail during the construction process contribute to the overall quality and performance of the CMU structure.
It is important to work with experienced contractors and follow industry standards and guidelines to ensure the successful implementation of CMU construction techniques for any given project.
Tips for Working with CMU in Construction
Working with CMU, or Concrete Masonry Unit, requires attention to detail, proper planning, and adherence to best practices. Here are some tips to consider when working with CMU in construction:
- Proper Handling and Storage: CMU blocks can be heavy, so it’s important to use proper lifting techniques and equipment to prevent injury. Additionally, ensure that CMU blocks are stored in a dry and stable environment to prevent moisture absorption and damage.
- Precise Layout: Plan the layout of the CMU walls carefully, ensuring accurate measurements and alignment. Use layout lines, string lines, or laser levels to ensure the walls are straight and level. This will contribute to the overall structural integrity and aesthetics of the project.
- Preparation of Foundation: Ensure that the foundation or footing is properly prepared and leveled before starting the CMU construction. A level, firm, and adequately compacted base will provide a stable foundation for the walls and ensure proper alignment.
- Quality Mortar Mix: Use a high-quality mortar mix that meets the required specifications. Properly proportioned mortar will provide good adhesion, strength, and durability. Follow the instructions provided by the mortar manufacturer for mixing and application.
- Consistent Mortar Joint Thickness: Maintain consistency in mortar joint thickness throughout the project. This will result in a visually pleasing appearance and consistent bond strength between the CMU blocks.
- Effective Mortar Application: Apply mortar evenly and in an adequate quantity to ensure proper bonding between the CMU blocks. Use a trowel to spread the mortar, filling the gaps between blocks, and remove excess mortar to maintain a clean and uniform appearance.
- Proper Reinforcement Placement: When incorporating vertical or horizontal reinforcement, ensure that it is properly placed and secured within the CMU walls. Follow the structural engineer’s specifications and local building codes to ensure reinforcing bars are adequately embedded and spaced.
- Control Joint Placement: Install control joints at appropriate intervals to allow for movement and prevent cracking. Follow the recommended spacing provided by structural engineers or local building codes. Fill control joints with a flexible sealant to accommodate expansion and contraction.
- Grouting Techniques: If grouting the CMU walls, ensure proper consolidation and filling of the grout into the voids or cores. Use appropriate equipment and techniques to eliminate air pockets and achieve a solid and uniform grout fill.
- Regular Inspections: Conduct regular inspections during and after the CMU construction process to identify any issues or defects. Address any cracks, gaps, or structural concerns promptly to maintain the integrity and performance of the CMU walls.
By following these tips, you can ensure the successful installation and construction of CMU walls. It is important to consult with experienced professionals, including architects, engineers, and contractors, to ensure compliance with local building codes and industry standards throughout the construction process.
Conclusion
CMU, or Concrete Masonry Unit, is a versatile and widely used building material in construction projects. Its strength, durability, fire resistance, thermal insulation properties, and design flexibility make it a popular choice for a wide range of applications in residential, commercial, and industrial construction.
In this article, we explored the definition of CMU and its composition, including the mixture of cement, aggregates, and water. We discussed the common uses of CMU in construction, such as exterior and interior walls, load-bearing walls, partition walls, retaining walls, facades, foundations, and soundproof rooms. We also examined the advantages and disadvantages of CMU construction, highlighting its strength, fire resistance, durability, and affordability, while acknowledging factors such as weight, maintenance, and construction time.
Furthermore, we discussed the various types of CMU available, including standard, solid, hollow, architectural, lintel, split-face, and grouted CMU blocks. Understanding these types can help in selecting the most appropriate option based on specific project requirements and design objectives.
We also explored the manufacturing process of CMU, which involves batching, mixing, molding, curing, demolding, finishing, and packaging. This process ensures the production of high-quality CMU blocks that meet industry standards and performance criteria.
Additionally, we discussed important CMU construction techniques such as mortar bedding, vertical reinforcement, horizontal bond beams, collar joints, masonry veneer, control joints, and grouting. These techniques contribute to the stability, strength, and longevity of CMU structures.
Finally, we provided tips for working with CMU in construction, including proper handling and storage, precise layout, preparation of the foundation, use of high-quality mortar mix, consistent mortar joint thickness, effective mortar application, proper reinforcement placement, control joint placement, grouting techniques, and regular inspections.
In conclusion, CMU is a versatile and reliable building material that offers numerous benefits for construction projects. Its combination of strength, durability, fire resistance, and thermal insulation properties provides a solid foundation for any structure. By understanding the characteristics, applications, and construction techniques related to CMU, architects, builders, and construction professionals can make informed decisions and ensure the successful implementation of CMU in their projects.
If you found the details on CMU construction intriguing, you'll be equally fascinated by our coverage of masonry construction. Diving into the nitty-gritty of how various building materials like brick, stone, and concrete are used in masonry work, this article sheds light on the skills and techniques that make masonry construction a cornerstone of the building industry. Whether you're a DIY enthusiast or a seasoned builder, understanding these fundamentals can significantly improve your construction projects. Don't miss out on this essential read!
Frequently Asked Questions about What Is CMU In Construction
Was this page helpful?
At Storables.com, we guarantee accurate and reliable information. Our content, validated by Expert Board Contributors, is crafted following stringent Editorial Policies. We're committed to providing you with well-researched, expert-backed insights for all your informational needs.
0 thoughts on “What Is CMU In Construction”