Home>Garden Essentials>How Much Does Infill Affect Strength
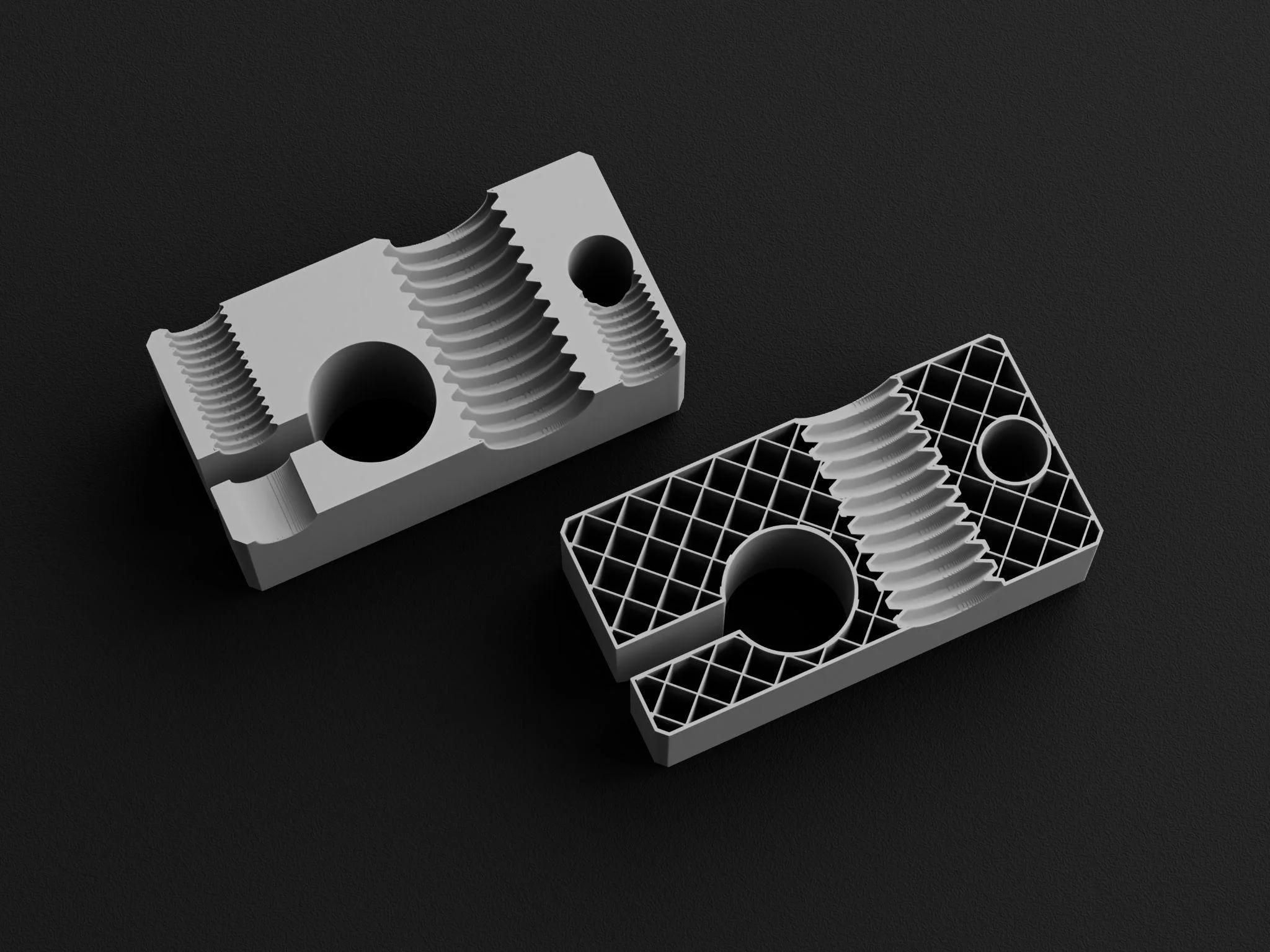
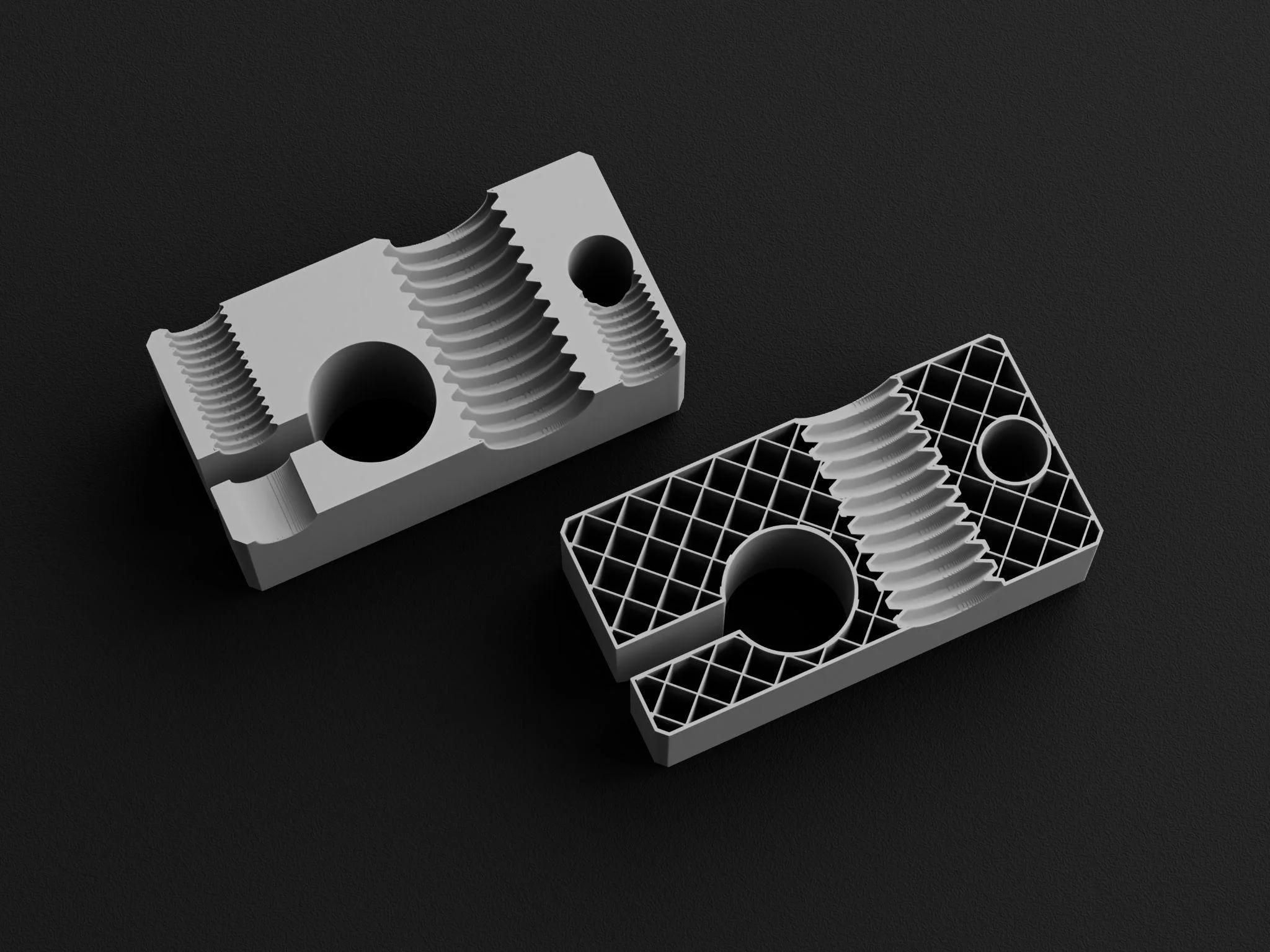
Garden Essentials
How Much Does Infill Affect Strength
Modified: March 7, 2024
Discover how the infill in your garden affects its overall strength. Find out the impacts of different fill options and make informed decisions for a sturdy and durable outdoor space.
(Many of the links in this article redirect to a specific reviewed product. Your purchase of these products through affiliate links helps to generate commission for Storables.com, at no extra cost. Learn more)
Introduction
Welcome to the world of 3D printing, where the possibilities seem virtually endless. From creating intricate designs to manufacturing functional parts, 3D printing has revolutionized the way we approach production. However, one critical aspect that often goes unnoticed is the strength of the printed objects. Strength is crucial, especially when it comes to creating objects that need to withstand external forces or be used in practical applications.
In 3D printing, one of the key factors that contributes to the strength of an object is the infill. Infill refers to the internal structure that fills the empty space within a 3D printed object. It plays a significant role in determining the overall strength and durability of the final print.
In this article, we will explore the various factors that affect the strength of 3D printed objects, with a specific focus on the role of infill. We will delve into the impact of infill density, infill pattern, and infill material on the strength of 3D printed objects. By understanding these factors, you will be able to optimize your prints for maximum strength and durability.
Key Takeaways:
- Infill density, pattern, and material significantly impact the strength of 3D printed objects. Balancing these factors is crucial for creating durable prints that can withstand external forces and meet specific application requirements.
- Achieving optimal strength in 3D printed objects requires a holistic approach, considering factors such as infill density, pattern, and material. By fine-tuning these parameters, you can create strong, durable prints suited for various applications.
Read more: How Much Infill For ABS
Definition of Infill
Infill in 3D printing refers to the internal structure that fills the empty space within a printed object. When you create a 3D model, the printer needs to determine how to fill the hollow areas of the object to provide support and stability. This is where infill comes into play.
The infill can be compared to the framework or backbone of the printed object. It is created by depositing material in a specific pattern or density inside the object, which adds strength and rigidity to the overall structure. Infill is usually represented as a percentage, indicating the amount of space filled within the object. For example, an infill density of 20% means that 20% of the object’s volume is filled with material.
There are different types of infill patterns that can be used, such as grid, honeycomb, triangular, or even custom patterns. Each pattern has its own strengths and weaknesses, and the choice of pattern can significantly impact the strength and performance of the printed object.
Moreover, the infill material used can vary depending on the 3D printing technology and the type of filament being used. Commonly used infill materials include ABS, PLA, Nylon, and PETG. The choice of infill material can affect the overall weight, flexibility, and strength of the printed object.
Now that we have a clear understanding of what infill is, let’s explore why strength is important and how infill plays a crucial role in achieving strong and durable 3D printed objects.
Importance of Strength in 3D Printed Objects
When it comes to 3D printing, strength is a critical factor to consider, especially if you plan to use your printed objects for practical purposes or functional applications. Here are a few reasons why strength is important in 3D printed objects:
Structural Integrity:
Strong 3D printed objects are essential for maintaining structural integrity. Whether it’s a prototype, a tool, or a mechanical component, you want your prints to be able to withstand the stresses and forces they may encounter. Strength ensures that your objects remain stable and functional, avoiding any potential failures or breakages.
Longevity and Durability:
Strong prints are built to last. They can withstand wear and tear, repetitive use, and external forces without losing their shape or functionality. This is particularly important when creating objects that need to endure harsh conditions or repetitive movements.
Read more: How Much Is Infill Percentage
Safety:
If you are printing objects that will be in close contact with human beings, such as medical devices or household items, strength is crucial for ensuring safety. Weak prints can break easily, leading to potential hazards and injuries. By prioritizing strength, you can create objects that are reliable, safe, and capable of withstanding everyday use.
Weight-to-Strength Ratio:
Strong prints do not necessarily mean heavy prints. With an optimal balance of strength and weight, you can create objects that are lightweight yet robust. This is particularly important in applications where weight is a crucial factor, such as aerospace or automotive industries.
Design Flexibility:
Strong prints provide design flexibility, allowing you to create complex shapes and intricate structures without compromising on strength. This opens up endless possibilities for creating unique and innovative designs, pushing the boundaries of what’s achievable with 3D printing technology.
As you can see, the importance of strength in 3D printed objects cannot be overstated. It ensures structural integrity, longevity, safety, and design flexibility. Now, let’s explore the various factors that affect the strength of 3D printed objects, focusing specifically on the role of infill.
Factors Affecting Strength in 3D Printed Objects
When it comes to achieving strong and durable 3D printed objects, several factors come into play. Understanding these factors will help you optimize your prints for maximum strength. Let’s take a closer look at the key factors that affect the strength of 3D printed objects:
Read more: How Does Rain Affect Construction
Layer Adhesion:
The adhesion between layers is critical for achieving strength in 3D printed objects. Proper bonding between layers ensures that the object remains intact and can withstand external forces. Factors such as extrusion temperature, printing speed, and cooling can all influence layer adhesion and, consequently, the overall strength of the print.
Infill Density:
The density of the infill significantly affects the strength of 3D printed objects. Higher infill densities generally result in stronger prints as there is less empty space inside the object. However, increasing infill density also increases material usage and print time. Finding the right balance between infill density and print efficiency is essential.
Infill Pattern:
The pattern used for infill can have a significant impact on the strength of the print. Different infill patterns distribute forces differently and can affect the overall stability and strength of the object. For example, a honeycomb pattern provides excellent strength and rigidity, while a grid pattern allows for more flexibility.
Infill Material:
The choice of infill material plays a vital role in the strength of 3D printed objects. Different materials have varying mechanical properties, such as flexibility, elasticity, and tensile strength. It’s important to select an infill material that matches the requirements of your print, considering factors like load-bearing capacity and environmental conditions.
Read more: How Does Construction Affect Wildlife
Print Settings:
Optimizing the print settings, such as layer height, print temperature, and print speed, can greatly influence the strength of the print. Finding the right balance for each specific object and material is crucial to achieving strong and durable prints.
Post-Processing Techniques:
Post-processing techniques, such as annealing, can enhance the strength of 3D printed objects. Annealing involves subjecting the print to controlled heating and cooling processes, which can improve the material’s internal structure and increase its overall strength and toughness.
By considering these factors and making appropriate adjustments, you can achieve prints that are strong, durable, and well-suited for their intended applications. Now, let’s dive deeper into the role of infill in influencing the strength of 3D printed objects.
Understanding the Role of Infill in Strength
Infill plays a crucial role in determining the strength of 3D printed objects. It acts as the internal support structure, providing stability, rigidity, and impact resistance. By understanding the role of infill, you can optimize your prints for maximum strength. Here are a few key points to consider:
Support and Structural Integrity:
Infill fills the empty space within a printed object, providing support and maintaining the object’s structural integrity. Without infill, the object would be hollow and weak, making it prone to deformation and failure. The internal structure created by the infill helps distribute external forces and prevents the object from collapsing under stress.
Distribution of Forces:
During use, 3D printed objects are subjected to various forces, such as compression, tension, and shear. Infill helps distribute these forces evenly throughout the object, reducing the concentration of stress points. This balanced distribution of forces improves the object’s overall strength and resistance to deformation or breakage.
Increase in Stiffness:
Infill increases the stiffness of the printed object by reducing its flexibility. This is especially important in applications where rigidity is necessary, such as when printing mechanical parts or functional prototypes. With higher infill densities and appropriate infill patterns, the object becomes more resistant to bending or twisting, enhancing its overall strength.
Enhancement of Surface Quality:
Infill also plays a role in improving the surface quality of the printed object. With the right infill pattern and density, the object’s external surfaces become smoother and more even. This is particularly important for aesthetics and for objects that require a polished or finished appearance.
It’s important to note that while a higher infill density generally results in stronger prints, it also increases material usage and print time. Therefore, finding the right balance between infill density, print efficiency, and required strength is essential.
In addition to infill density, other factors such as infill pattern and infill material also influence the strength of the printed object. Different infill patterns distribute forces differently, and the choice of infill material with appropriate mechanical properties can significantly impact the final strength of the print.
By understanding and optimizing these factors, you can ensure that your 3D printed objects are strong, durable, and able to withstand the demands of their intended applications. In the next sections, we will explore the effects of infill density, infill pattern, and infill material on the overall strength of 3D printed objects.
Effects of Infill Density on Strength
The infill density of a 3D printed object has a significant impact on its strength. The density refers to the percentage of the object’s volume that is filled with infill material. Understanding the effects of infill density can help you optimize your prints for the desired strength and durability. Here are the key effects of infill density on the strength of 3D printed objects:
Increased Strength:
Higher infill densities generally result in stronger prints. When the empty space within the object is filled with infill material, it provides additional support and rigidity, increasing the overall strength of the object. This is particularly important for prints that will endure external forces or repetitive use.
Improved Load-Bearing Capacity:
A higher infill density allows the printed object to bear more weight or withstand greater loads. The infill material acts as internal reinforcement, distributing the external forces throughout the object more evenly. This enhances the load-bearing capacity of the print, making it suitable for applications that require structural integrity and stability.
Reduced Risk of Delamination:
Delamination is the separation between layers that can occur in 3D printed objects. By increasing the infill density, the adhesion between layers improves, reducing the risk of delamination. Improved layer adhesion contributes to the overall strength of the print, making it less prone to failure or breakage.
Increased Material Usage and Print Time:
While higher infill densities result in stronger prints, they also lead to increased material usage and longer print times. More infill material is required to fill the object, which can increase the cost of the print. Additionally, longer print times may be needed to achieve the desired infill density. It’s important to strike a balance between strength, material usage, and efficiency.
Read more: How Does Ground Cover Affect Erosion
Impact on Weight and Flexibility:
Higher infill densities can increase the weight of the printed object. This may be a consideration in applications where weight is a critical factor, such as aerospace or robotics. Additionally, higher infill densities can reduce the flexibility of the print, making it stiffer. This can be beneficial in some cases, especially for parts that require rigidity, but it may not be ideal for all applications.
Choosing the right infill density depends on the specific requirements of your print. It’s essential to consider factors such as the intended application, the strength needed, the material being used, and any weight or flexibility constraints. By experimenting with different infill densities and evaluating the resulting strength, you can achieve optimal prints that meet your requirements.
Next, let’s explore the effects of infill pattern on the strength of 3D printed objects, as another significant factor to consider in optimizing your prints for maximum strength and durability.
Effects of Infill Pattern on Strength
The choice of infill pattern in 3D printed objects can significantly impact their strength and performance. Different infill patterns distribute forces and stresses differently, ultimately affecting the overall strength and stability of the print. Understanding the effects of infill pattern can help you optimize your prints for the desired strength and functionality. Here are the key effects of infill pattern on the strength of 3D printed objects:
Strength and Rigidity:
The infill pattern plays a critical role in determining the strength and rigidity of the printed object. Some infill patterns, such as the honeycomb or triangular pattern, provide excellent strength and rigidity due to their evenly distributed internal structure. On the other hand, infill patterns like the grid pattern offer more flexibility. Choosing the right pattern depends on the specific requirements of your print, considering factors such as load-bearing capabilities and the desired level of rigidity.
Impact Resistance:
Different infill patterns also affect the impact resistance of a 3D printed object. Some patterns, such as the gyroid or octet pattern, offer enhanced impact resistance due to their geometric arrangement. This makes them suitable for prints that will undergo sudden or repetitive impacts, increasing the durability and longevity of the object.
Material Usage and Print Time:
The choice of infill pattern can also influence the amount of material used and the print time required. Some patterns, such as solid or grid infill, use more material and take longer to print compared to patterns with higher voids or increased spacing. It’s important to consider the balance between strength, material usage, and print efficiency to optimize your prints accordingly.
Surface Quality and Aesthetics:
Infill patterns can also impact the surface quality and aesthetics of the printed object. Some patterns, such as the rectilinear or concentric pattern, can result in visible lines on the surface that may require additional post-processing to achieve a smoother finish. However, other patterns, such as the adaptive grid or Hilbert curve pattern, can produce a more visually appealing and uniform surface finish.
Printability and Support Removal:
Lastly, the choice of infill pattern may also affect the printability of the object and the ease of support removal. Certain patterns, such as the rectilinear or triangular pattern, are more easily printed and require less support material, simplifying the post-processing and support removal process. However, more complex patterns, such as the Voronoi or organic patterns, may require additional support material and present challenges during printing and cleanup.
Ultimately, the choice of infill pattern depends on the specific requirements of your print, considering factors such as strength, rigidity, impact resistance, material usage, print time, surface quality, and printability. Experimenting with different infill patterns and evaluating their effects on the strength and performance of your prints will help you optimize your designs for improved functionality and durability.
Next, let’s explore the effects of infill material on the strength of 3D printed objects, as another crucial factor in achieving strong and durable prints.
Effects of Infill Material on Strength
The choice of infill material in 3D printed objects can have a significant impact on their strength and overall performance. Different materials possess varying mechanical properties, such as flexibility, elasticity, and tensile strength, which directly influence the strength of the printed object. Understanding the effects of infill material can help you select the appropriate material to optimize the strength and durability of your prints. Here are the key effects of infill material on the strength of 3D printed objects:
Read more: How To Spread Infill Without Infill Machine
Tensile Strength:
The tensile strength of the infill material refers to its ability to resist pulling or stretching forces. Different materials exhibit different tensile strengths, and selecting a material with high tensile strength is crucial for achieving strong prints. Materials like carbon fiber-infused filaments or nylon tend to have higher tensile strengths, making them suitable for applications that require robust and durable prints.
Flexibility and Impact Resistance:
The flexibility and impact resistance of the infill material play an important role in determining the strength of the printed object. Some materials, like TPU (thermoplastic polyurethane), offer high flexibility and elasticity, making them suitable for objects that require impact resistance or the ability to withstand bending or stretching. However, materials that are too flexible may sacrifice some degree of overall strength.
Read more: How Does Rain Affect Construction
Layer Adhesion:
The adhesion between layers is crucial for achieving strong prints. Different infill materials have varying levels of adhesion when printed layer by layer. Materials with good layer adhesion, such as ABS (acrylonitrile butadiene styrene) or PETG (polyethylene terephthalate glycol), tend to result in prints with higher overall strength. Ensuring proper printing parameters and optimizing the adhesion between layers is essential for maximizing the strength of the printed object.
Environmental Factors:
Some infill materials may perform differently under certain environmental factors, such as temperature or humidity. For example, materials like PLA (polylactic acid) may become brittle in cold temperatures, which can affect their overall strength. Considering the intended application and the environmental conditions the printed object will encounter is important in selecting the appropriate infill material to ensure long-term strength and durability.
Weight and Density:
The weight and density of the infill material can also affect the overall strength of the printed object. Lightweight materials like PLA or PETG can contribute to strong prints without adding excessive weight. Balancing the desired strength with weight considerations is important, especially in applications where weight reduction is a critical factor, such as aerospace or automotive industries.
Considering these effects, it is crucial to select an infill material that aligns with your specific requirements for strength, flexibility, impact resistance, layer adhesion, and environmental factors. It’s recommended to test and evaluate different infill materials to find the one that best meets your needs for strong and durable prints.
Now that we have explored the effects of infill density, infill pattern, and infill material on the strength of 3D printed objects, let’s conclude our discussion.
Conclusion
When it comes to 3D printing, achieving strong and durable prints is a paramount goal. The strength of a 3D printed object plays a crucial role in its performance, longevity, and functionality. Throughout this article, we have explored the factors that affect the strength of 3D printed objects, with a specific focus on the role of infill.
We began by defining infill as the internal structure that fills the empty space within a printed object. We discussed the importance of strength in 3D printed objects, highlighting its significance in ensuring structural integrity, longevity, safety, weight-to-strength ratio, and design flexibility.
We then delved into the key factors that affect the strength of 3D printed objects, including layer adhesion, infill density, infill pattern, infill material, print settings, and post-processing techniques. These factors, when optimized, contribute to creating prints that are strong, durable, and able to meet the demands of their intended applications.
Furthermore, we explored the effects of infill density on strength, highlighting how higher infill densities generally result in stronger prints, while considering the trade-offs in material usage and print time. We discussed how the choice of infill pattern influences strength, rigidity, impact resistance, material usage, print time, surface quality, and printability. Additionally, we examined how the choice of infill material affects tensile strength, flexibility, layer adhesion, and performance under specific environmental conditions.
The key takeaway is that achieving optimal strength in 3D printed objects requires a holistic approach. It involves fine-tuning various parameters, such as infill density, infill pattern, and infill material, while considering the specific requirements of each print. It also requires balancing strength with efficiency, aesthetics, and functionality.
By understanding these factors and making informed choices, you can create prints that are strong, durable, and well-suited for their intended applications. Whether you’re prototyping, manufacturing functional parts, or simply bringing your creative ideas to life, optimizing the strength of your 3D printed objects will elevate your prints to new heights.
So, go ahead, experiment, and push the limits of what’s achievable with 3D printing. Embrace the power of infill and unlock the potential for strong, reliable, and impactful prints.
Frequently Asked Questions about How Much Does Infill Affect Strength
Was this page helpful?
At Storables.com, we guarantee accurate and reliable information. Our content, validated by Expert Board Contributors, is crafted following stringent Editorial Policies. We're committed to providing you with well-researched, expert-backed insights for all your informational needs.
0 thoughts on “How Much Does Infill Affect Strength”