Home>Garden Essentials>How Much Is Infill Percentage
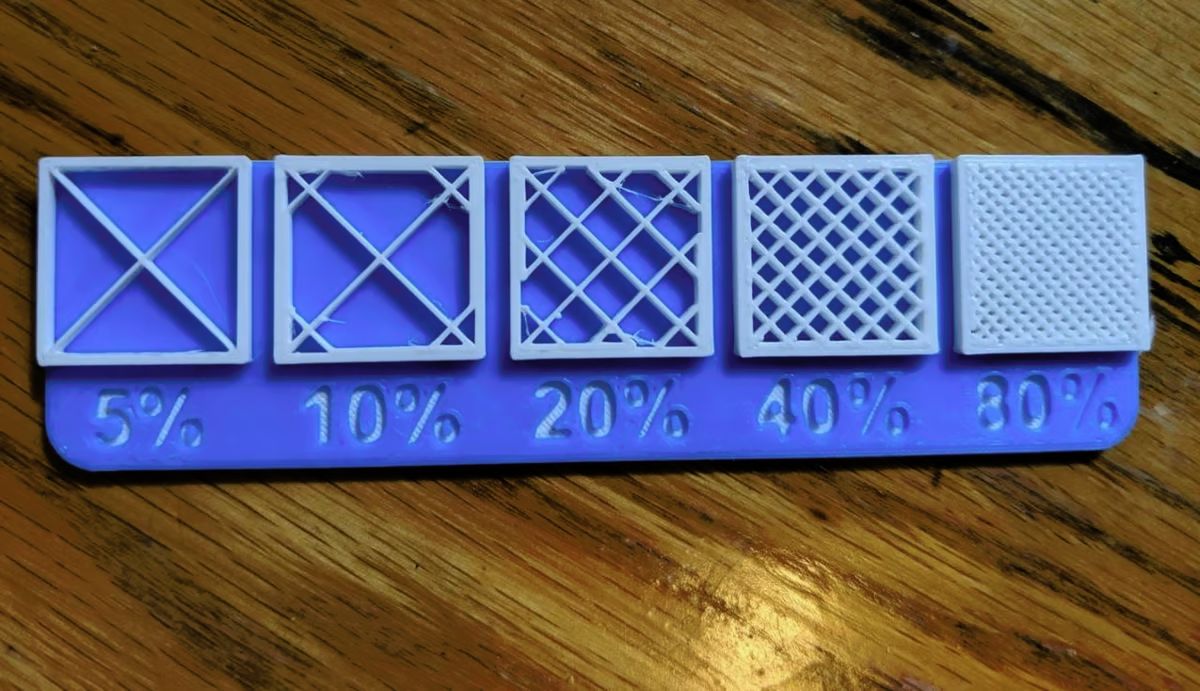
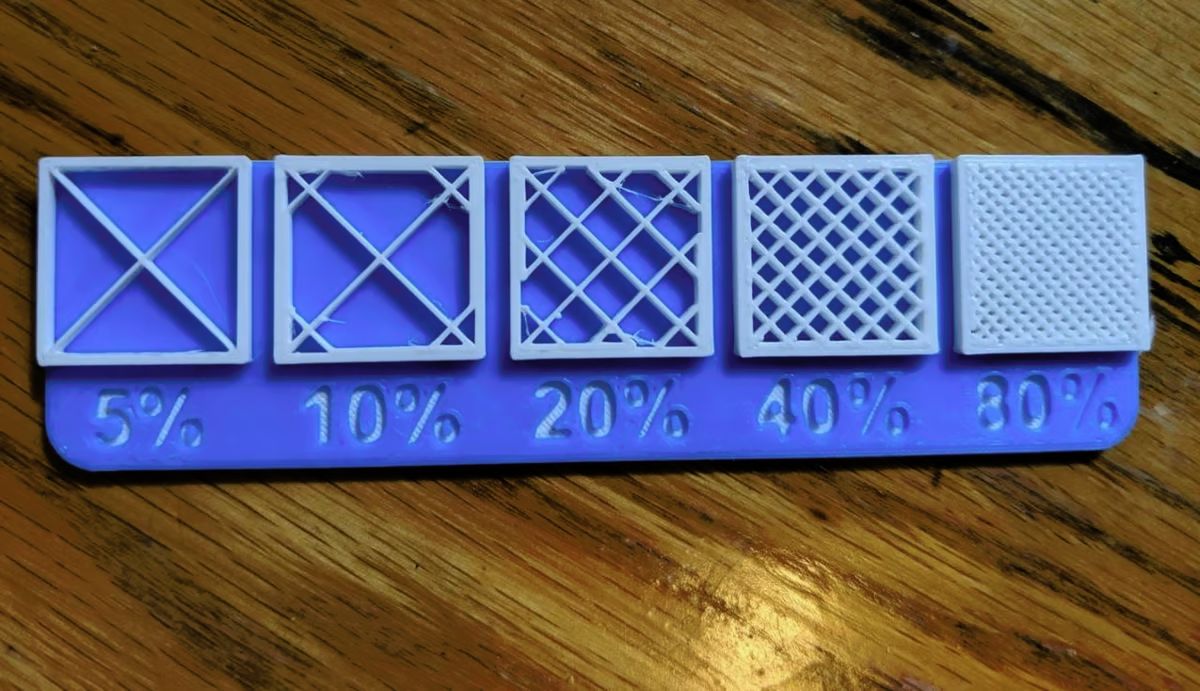
Garden Essentials
How Much Is Infill Percentage
Modified: March 7, 2024
Discover the optimum infill percentage for your garden. Get expert advice on how much infill to use to enhance the beauty and functionality of your outdoor space.
(Many of the links in this article redirect to a specific reviewed product. Your purchase of these products through affiliate links helps to generate commission for Storables.com, at no extra cost. Learn more)
Introduction
Welcome to the world of 3D printing, where intricate designs and functional objects can be brought to life with the help of advanced technology. Whether you are a beginner or an experienced 3D printing enthusiast, you may have come across the term “infill percentage” in your journey. Infill percentage plays a crucial role in optimizing the strength and material usage of 3D printed objects.
Infill percentage refers to the density of the internal structure of a 3D printed object. It determines how much material is used to fill the empty space inside the print, while the rest is occupied by the outer shell. By adjusting the infill percentage, you can control the strength, weight, and durability of your prints.
Understanding the concept and importance of infill percentage is vital to achieving the desired results in your 3D prints. In this article, we will explore the significance of infill percentage, factors that affect it, how to determine the optimal infill percentage, and advanced techniques for infill optimization.
So, let’s dive into the world of infill percentage and unlock the secrets to creating robust and efficient 3D prints!
Key Takeaways:
- Infill percentage in 3D printing determines the internal structure’s density, impacting strength, weight, and material usage. It’s crucial to find the right balance for optimal results.
- By adjusting infill percentage, 3D prints can achieve the desired strength, flexibility, and material efficiency. Experimentation and advanced techniques further enhance the performance and functionality of printed objects.
Read more: Which Infill Percentage To Use
Definition of Infill Percentage
Infill percentage in 3D printing refers to the density of the internal structure of a printed object. It represents the ratio of solid material to empty space inside the printed object. When 3D printing, an object is created by building layers upon layers of material. The infill percentage determines how much of the internal space is filled with material, while the remaining space is occupied by the outer shell.
The infill percentage is measured in percentage values, typically ranging from 0% to 100%. A 0% infill means that the entire object is hollow, with no internal structure, while a 100% infill indicates that the object is entirely filled, leaving no empty space inside. The infill percentage is usually set using slicing software, which generates the G-code instructions for the 3D printer to follow.
The infill pattern refers to the specific pattern in which the internal structure is created. There are various infill patterns available, such as honeycomb, grid, triangular, and cubic, each with its own advantages and drawbacks. The choice of infill pattern can affect the mechanical properties, weight, and printing time of the object.
By adjusting the infill percentage, you can control the balance between strength, weight, flexibility, and material usage in your 3D prints. Higher infill percentages result in stronger prints, but they also consume more material and increase printing time. On the other hand, lower infill percentages reduce material usage and printing time, but may compromise the strength of the object.
Understanding the concept of infill percentage is crucial for optimizing your 3D prints based on the specific requirements of your project. In the following sections, we will explore the importance of infill percentage in 3D printing and how it can be adjusted to achieve the desired results.
Importance of Infill Percentage in 3D Printing
The infill percentage plays a vital role in 3D printing as it directly impacts the strength, weight, and material usage of the printed object. Understanding its importance is crucial for achieving the desired results and optimizing the manufacturing process.
One of the primary benefits of adjusting the infill percentage is optimizing the strength and structural integrity of the printed object. By increasing the infill percentage, more material is used to fill the internal structure, resulting in a stronger and more durable object. This is particularly important for functional parts that require strength, such as mechanical components or structural prototypes.
Conversely, reducing the infill percentage can lead to lighter prints, saving material and reducing printing time. This is beneficial for objects where weight is a concern, such as drones or wearable devices. By finding the right balance between strength and weight, you can create efficient and optimized 3D printed objects.
Another significant advantage of adjusting the infill percentage is the ability to fine-tune the flexibility of the printed object. In some cases, such as objects that require a certain level of pliability or elasticity, a lower infill percentage can provide the desired level of flexibility. On the other hand, increasing the infill percentage can create more rigid and stiff objects.
Moreover, the infill percentage has a direct impact on the material usage during the printing process. Higher infill percentages require more material to fill the internal structure, leading to increased material consumption. This can be a consideration when working with expensive or limited resources. By optimizing the infill percentage, you can reduce material waste and save costs.
Infill percentage also affects the print time. Higher infill percentages result in longer print times, as more material needs to be extruded to fill the internal structure. When time is a factor, reducing the infill percentage can be beneficial, as it shortens the print duration. However, it is essential to strike a balance and consider the impact on strength and structural integrity.
Overall, the infill percentage is a critical parameter in 3D printing that allows for customization and optimization of printed objects. By adjusting the infill percentage, you can control the strength, weight, flexibility, material usage, and printing time to meet the specific requirements of your project.
Factors Affecting Infill Percentage
Several factors can influence the choice of infill percentage in 3D printing. Understanding these factors is essential for determining the optimal infill percentage for your specific project. Let’s explore some of the key considerations:
1. Object Application: The purpose and application of the printed object play a significant role in determining the appropriate infill percentage. Functional parts that require high strength and durability, such as mechanical components or load-bearing structures, may require a higher infill percentage. On the other hand, decorative or lightweight objects may be suitable for a lower infill percentage.
2. Material Characteristics: The type of material used in 3D printing can influence the optimal infill percentage. Different materials have varying strength properties and behave differently under different infill densities. For example, using a flexible filament may require a lower infill percentage to achieve the desired flexibility, while a rigid plastic may need a higher infill percentage for added strength.
3. Printing Time Considerations: Infill percentage directly affects the printing time of 3D objects. Higher infill percentages require more material to be extruded, resulting in longer print times. If time is a constraint, a lower infill percentage can be chosen to reduce the printing duration. However, it is important to weigh this against the potential compromise in strength and structural integrity.
4. Weight Constraints: The weight of the printed object can also be a deciding factor in choosing the infill percentage. For applications where weight reduction is crucial, such as drones or lightweight components, lowering the infill percentage can result in lighter prints. This can help improve overall performance and reduce material usage.
5. Cost Considerations: Material consumption directly affects the cost of 3D printing. Higher infill percentages require more material, which can increase costs. Therefore, it is important to strike a balance between the desired strength and material usage. For cost-sensitive projects, optimizing the infill percentage can help minimize material waste and reduce expenses.
6. Print Resolution: The desired level of detail and resolution can also impact the choice of infill percentage. Higher infill densities can enhance the surface quality and smoothness of the printed object. If achieving a high-quality finish is important, a higher infill percentage may be necessary.
7. Printing Equipment: The capabilities and limitations of the 3D printer itself should also be taken into account. Certain printers may have restrictions on minimum and maximum infill percentages. It is important to consider the printer’s capabilities and adjust the infill percentage accordingly.
By considering these factors and carefully analyzing the requirements of your specific project, you can determine the optimal infill percentage that balances strength, weight, material usage, cost, and other considerations. It may require some trial and error to find the perfect balance, but with experimentation and experience, you can achieve the desired results in your 3D prints.
Determining the Optimal Infill Percentage
Determining the optimal infill percentage for your 3D prints involves finding the right balance between strength, weight, material usage, and other considerations. While there isn’t a one-size-fits-all approach, there are several methods you can use to determine the optimal infill percentage for your specific project. Let’s explore some of these techniques:
- Default Recommendations: Many slicing software programs provide default infill percentage recommendations based on the type of object being printed. These recommendations are a good starting point and may work well for general-purpose prints. However, keep in mind that these defaults are not tailored to the specific requirements of your project, so they may need adjustment.
- Strength Testing: If strength is a critical factor, you can perform strength testing on printed objects with different infill percentages. Create several test prints with varying infill percentages and subject them to stress or load tests to determine the infill percentage that offers optimal strength for your specific application.
- FEM Analysis: Finite Element Method (FEM) analysis is a powerful technique used to simulate the behavior of printed objects under different infill densities. By modeling the object and applying various infill percentages, FEM analysis can help predict the structural integrity and strength of the prints. This method is more advanced and requires knowledge of FEM software.
- Guidelines from Material Manufacturers: Material manufacturers often provide guidelines and recommendations for infill percentages specific to their materials. These guidelines are based on their extensive testing and can be a valuable resource when choosing the infill percentage for your prints. Consider consulting the documentation or contacting the manufacturer for guidance.
- Iterative Approach: Another method is to use an iterative approach by starting with a conservative infill percentage and gradually increasing or decreasing it in subsequent prints. Evaluate the strength, weight, and other properties of each print to determine the optimal infill percentage that satisfies your requirements.
It is worth mentioning that there is no definitive rule or formula for determining the optimal infill percentage. It often depends on the specific requirements of your project, such as strength, weight, cost, and material usage. Experimentation and experience play a significant role in finding the sweet spot that achieves the desired results.
Once you have determined the optimal infill percentage, it is essential to document the settings for future reference. This way, you can reproduce the desired results consistently and save time in future projects.
Remember that infill percentage is just one parameter in the 3D printing process, and it should be considered in conjunction with other settings, such as layer height, printing temperature, and print speed. Finding the right combination of these parameters will help you achieve high-quality prints that meet your specific needs.
By utilizing the techniques mentioned above and understanding the specific requirements of your project, you can determine the optimal infill percentage that strikes the right balance between strength, weight, material usage, and other considerations.
When adjusting the infill percentage for 3D printing, a higher percentage will result in a stronger and denser print, while a lower percentage will save time and material. Consider the balance between strength and efficiency for your specific project.
Read more: How Much Infill For ABS
Common Infill Percentage Recommendations
While determining the optimal infill percentage for your 3D prints depends on several factors, there are some common recommendations that can serve as a starting point. These recommendations provide a general guideline based on the intended use and properties desired in the printed object. Here are some commonly used infill percentage recommendations:
- 10-20%: This infill percentage range is often recommended for decorative or lightweight objects that do not require significant strength. It strikes a balance between minimal material usage and providing some internal support to maintain the structural integrity.
- 30-50%: For most general-purpose prints that require a moderate level of strength and durability, infill percentages between 30% and 50% are commonly used. This range offers a good compromise between material usage and strength, making it suitable for a wide variety of applications.
- 60-80%: If strength is a critical requirement, such as for load-bearing or structural components, infill percentages between 60% and 80% are often recommended. These higher infill percentages provide robust internal support, resulting in strong and durable prints.
- 100%: In some cases, such as when creating solid objects or objects that need the maximum possible strength, a 100% infill percentage may be desired. This means the entire internal space of the object is filled with material, leaving no empty space. However, printing with 100% infill can be time-consuming and consumes a significant amount of material.
- Variable Infill: Another approach is to use variable infill percentages for different sections or layers of the object. This allows for customized strength and weight distribution within a single print. For example, higher infill percentages can be used in critical areas and lower infill percentages in less stressed parts.
It’s important to note that these recommendations are not set in stone and should be adjusted based on the specific requirements of your project. Consider factors such as the application, material properties, weight constraints, and cost considerations when finalizing the infill percentage.
Furthermore, different slicing software programs or manufacturers may have their own recommended infill percentage ranges based on their testing and experience with specific materials. It is worth exploring these recommendations and determining which works best for your particular setup.
Remember that infill percentage is just one aspect of 3D printing, and it should be considered in conjunction with other parameters, such as layer height, printing temperature, and print speed, to achieve the desired results.
By starting with these common infill percentage recommendations as a baseline and adjusting them based on your specific project requirements, you can achieve prints that strike the right balance between strength, weight, and other properties.
Balancing Strength and Material Savings
When determining the infill percentage for your 3D prints, finding the right balance between strength and material savings is crucial. By optimizing this balance, you can achieve strong, functional prints while minimizing material consumption. Here are some strategies to help you strike the ideal balance:
- Evaluate the Application: Consider the intended use of the printed object. If it is a functional part that will undergo stress or strain, prioritize strength and durability. In such cases, opting for a higher infill percentage will help ensure the object can withstand the required forces. On the other hand, for decorative or lightweight objects, you can choose a lower infill percentage to save material while still maintaining adequate structural integrity.
- Consider Material Characteristics: Different 3D printing materials possess unique properties that influence their strength and behavior under different infill densities. Some materials, like PLA, may achieve sufficient strength at lower infill percentages, whereas others, like ABS or nylon, may require higher infill percentages for similar strength. Experimenting with different materials and their corresponding infill recommendations can help you strike the right balance between strength and material savings.
- Optimize Infill Pattern: In addition to adjusting the infill percentage, consider exploring different infill patterns. Some patterns, like honeycomb or gyroid, provide excellent strength and material distribution. They can maximize structural integrity while minimizing material usage. Experimenting with various infill patterns, combined with the appropriate infill percentage, can help you find the optimal balance between strength and material savings for your specific print.
- Utilize Variable Infill: Variable infill allows for different infill percentages within a single print. By strategically placing higher infill percentages in critical areas and lower infill percentages in less stressed regions, you can optimize strength while saving material. This approach is particularly useful for objects with complex geometries or varying load requirements.
- Perform Test Prints: Conducting test prints with different infill percentages can provide valuable insights into the strength and material-saving potential of your designs. Test prints allow you to evaluate the trade-off between strength and material usage firsthand. By comparing and analyzing the results, you can identify the infill percentage that delivers the desired balance for your specific project.
Remember that striking the perfect balance between strength and material savings may require some experimentation and iteration. It is essential to document and record your findings for future reference and to improve your understanding and control over the infill settings for different applications.
By implementing these strategies and considering the specific requirements of your project, you can optimize the infill percentage to achieve strong, functional prints while maximizing material savings. Finding the right balance will not only benefit your prints but also contribute to cost savings and efficient use of resources.
Advanced Techniques for Infill Optimization
While adjusting the infill percentage is a fundamental method for optimizing prints, there are advanced techniques you can employ to further enhance the performance, strength, and functionality of your 3D printed objects. These techniques involve more intricate infill settings and innovative design approaches. Let’s explore some of these advanced techniques:
- Variable Density Infill: Instead of using a single infill percentage throughout the entire print, variable density infill involves adjusting the infill percentage in different sections or layers of the object. This technique allows you to allocate more material and density to areas that require additional strength while reducing material usage in less critical regions. Variable density infill can be accomplished through advanced slicing software or by manually adjusting the infill settings.
- Adaptive Infill: Adaptive infill is a technique where the infill pattern and density are adjusted dynamically based on the geometric complexity and stress distribution within the object. By utilizing algorithms and intelligent software, adaptive infill optimizes the internal structure of the print to provide the necessary strength and support where it’s needed most. This technique is particularly useful for complex objects with varying load requirements.
- Lattice Structures: Lattice structures involve creating intricate internal lattice-like patterns within the object to optimize strength and weight. These structures are designed to distribute forces evenly and eliminate excess material. By incorporating lattice structures in specific areas, you can increase the overall strength of the print while reducing material consumption. Lattice structures can be generated using specialized software or 3D modeling techniques.
- Topology Optimization: Topology optimization is an advanced technique that utilizes computational algorithms to determine the optimal material distribution within a given design space. By defining the desired constraints and objectives, the algorithm generates a lightweight and structurally efficient internal structure. Topology optimization enables you to create organic and complex internal geometries, maximizing strength while minimizing material usage. This technique requires specialized software and expertise.
- Hollowing and Ribbing: Hollowing an object involves removing unnecessary internal material while maintaining the external shell, resulting in lightweight prints. This technique is particularly useful for large objects where material savings are significant. Ribbing, on the other hand, involves incorporating internal reinforcing ribs to improve strength without increasing material usage. Hollowing and ribbing can be achieved through careful design modifications using CAD software.
Implementing these advanced techniques requires a deeper understanding of 3D design, slicing software, and advanced modeling. It is recommended to develop expertise through practice and experimentation. Additionally, advanced infill techniques may also require more processing power and longer computation times.
By utilizing these advanced techniques for infill optimization, you can create 3D prints that excel in strength, functionality, and material efficiency. However, it’s important to assess whether the complexity and additional effort involved in these methods are warranted based on the specific requirements of your project.
Remember to document your settings and techniques for future reference and to continuously refine your skills and knowledge in infill optimization as you explore the exciting possibilities within the realm of 3D printing.
Conclusion
Infill percentage is a vital parameter in 3D printing that directly affects the strength, weight, and material usage of printed objects. Understanding the importance of infill percentage and optimizing it according to your project’s specific requirements is key to achieving optimal results. Throughout this article, we have explored the definition of infill percentage, its importance, factors influencing it, methods to determine the optimal infill percentage, common recommendations, and advanced techniques for infill optimization.
By carefully considering the application, materials, weight constraints, cost considerations, and other factors, you can strike a balance between strength and material savings. Adjusting the infill percentage allows you to tailor the internal structure of your prints, affecting their strength, flexibility, durability, and functionality. Through various techniques such as variable infill, adaptive infill, lattice structures, topology optimization, and hollowing/ribbing, you can further optimize the infill and internal geometry of your prints to maximize their performance and material efficiency.
It is crucial to experiment, iterate, and document your findings to improve your understanding and control over infill optimization. By testing different infill percentages, infill patterns, and advanced techniques, you can gain insights into how they impact the strength, weight, and overall quality of your prints. With experience, you will develop the expertise to achieve the desired balance and create prints that meet your specific needs.
As you embark on your 3D printing journey, continue to explore new advancements, techniques, and materials that can further enhance the infill optimization process. Stay up to date with the latest developments in slicing software, material characteristics, and design methodologies to continuously improve the quality and efficiency of your prints.
So, go ahead and unleash your creativity, optimize your infill percentage, and unlock the full potential of 3D printing. With the right infill settings, you can create robust, functional, and visually stunning objects that showcase the power of this revolutionary technology.
Frequently Asked Questions about How Much Is Infill Percentage
Was this page helpful?
At Storables.com, we guarantee accurate and reliable information. Our content, validated by Expert Board Contributors, is crafted following stringent Editorial Policies. We're committed to providing you with well-researched, expert-backed insights for all your informational needs.
0 thoughts on “How Much Is Infill Percentage”