Home>Garden Essentials>What Is A Good Infill Layer Thickness
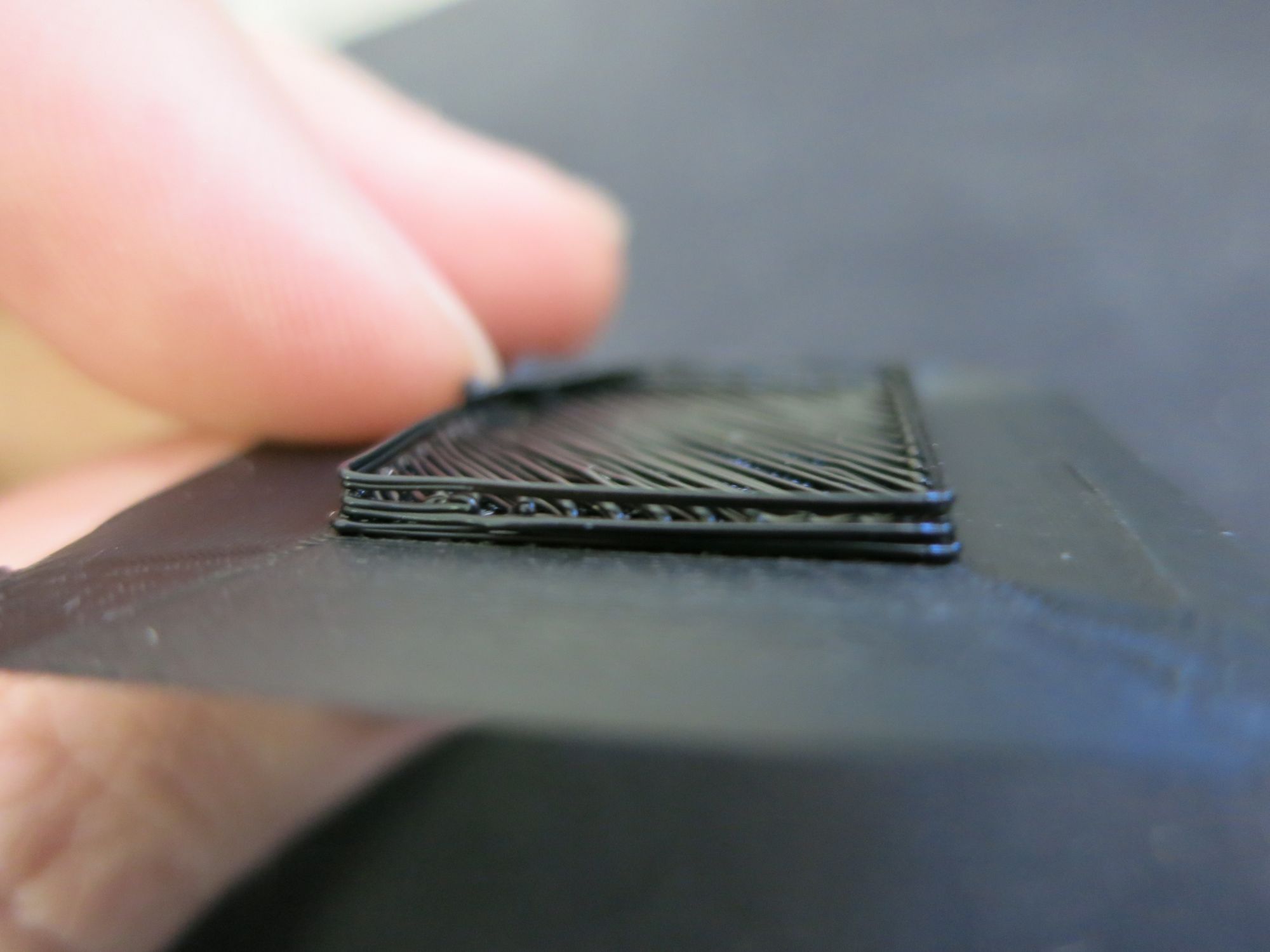
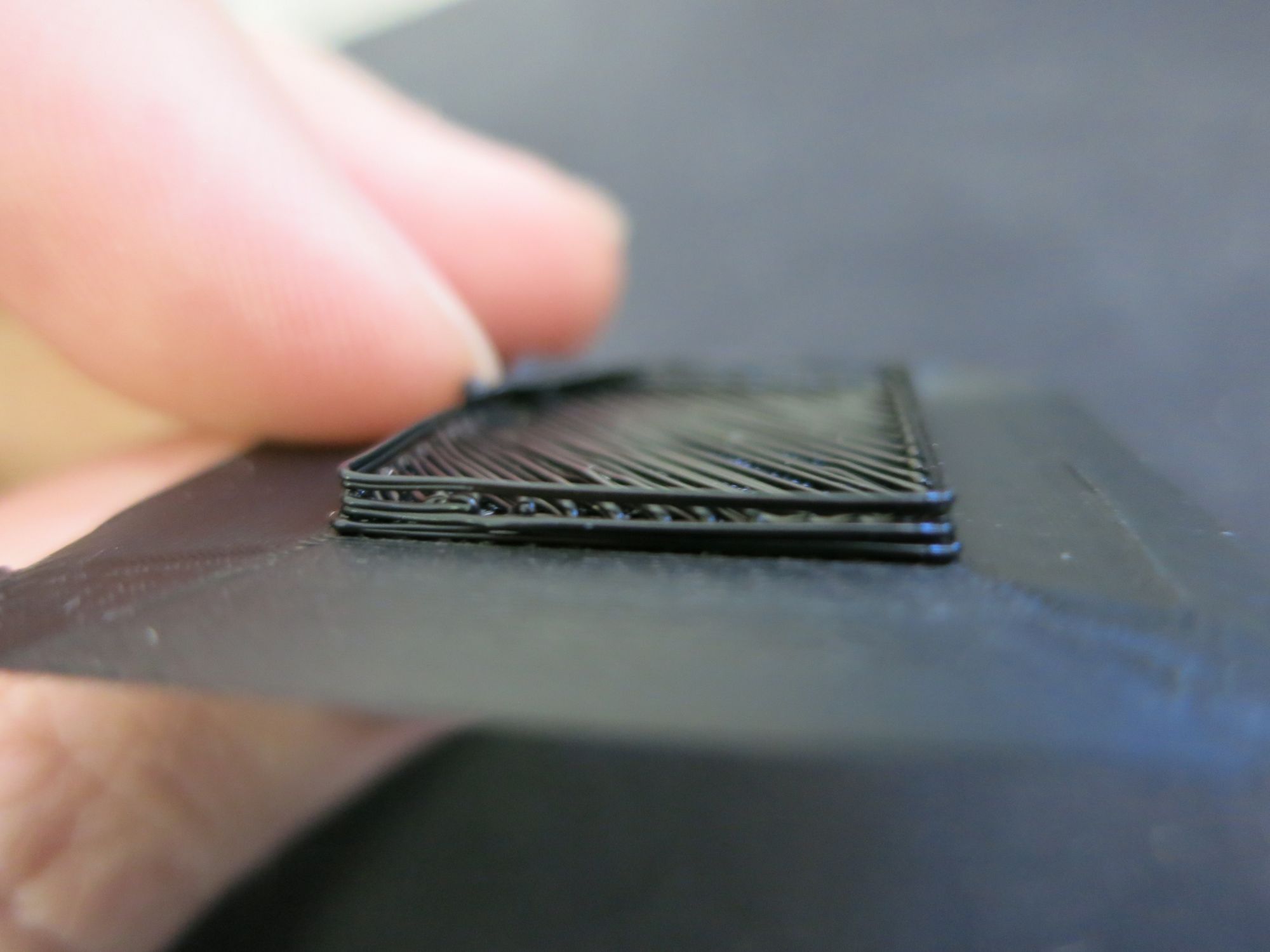
Garden Essentials
What Is A Good Infill Layer Thickness
Modified: March 7, 2024
Find out the ideal garden infill layer thickness for optimal growth and maintenance. Discover the perfect balance for a thriving garden.
(Many of the links in this article redirect to a specific reviewed product. Your purchase of these products through affiliate links helps to generate commission for Storables.com, at no extra cost. Learn more)
Introduction
When it comes to 3D printing, achieving the desired strength and structural integrity of a printed object is crucial. One important factor that contributes to the overall strength of a 3D printed object is the infill layer thickness. The infill layer thickness refers to the thickness of the internal structure or fill pattern inside the printed object. It plays a significant role in determining the mechanical properties, durability, and weight of the printed object.
Infill layer thickness is an essential consideration for 3D printing enthusiasts, hobbyists, and professionals alike. It allows for customization, as adjusting the infill layer thickness can result in different levels of strength and flexibility for specific applications. By optimizing the infill layer thickness, users can strike the perfect balance between strength and material conservation.
In this article, we will delve deeper into the concept of infill layer thickness and its importance in 3D printing. We will explore the factors that affect the choice of infill layer thickness, discuss how to determine the ideal thickness, and highlight the benefits and challenges associated with adjusting this parameter. So, let’s dive in and discover the significance of infill layer thickness in 3D printing.
Key Takeaways:
- Adjusting infill layer thickness in 3D printing can make objects stronger, lighter, and more flexible, but it may also affect print time and surface quality.
- Choosing the right infill layer thickness is crucial for creating high-quality 3D printed objects that meet specific strength, weight, and flexibility requirements.
Read more: What Is A Good Infill Speed In Cura
Importance of Infill Layer Thickness
The infill layer thickness plays a critical role in 3D printing because it directly influences the strength and performance of the printed object. Here are some key reasons why infill layer thickness is important:
- Mechanical Strength: The infill layer provides internal support to the printed object, enhancing its mechanical strength. By adjusting the infill layer thickness, you can customize the strength of the printed object based on its intended use. For example, objects that require high strength, such as mechanical parts or functional prototypes, benefit from a thicker infill layer that provides added stability and rigidity.
- Weight Reduction: In many cases, reducing the weight of a 3D printed object without compromising its strength is desirable. By using a thinner infill layer, you can significantly reduce the amount of material used in the internal structure. This not only results in lighter objects but also reduces material costs, printing time, and energy consumption.
- Flexibility and Elasticity: The infill layer thickness can also affect the flexibility and elasticity of a printed object. Thicker infill layers provide more rigidity, making the object less flexible but more suitable for applications that require stability and minimal deformation. Conversely, thinner infill layers offer increased flexibility, making the printed object suitable for applications where resilience and deformation are desirable, such as in wearable devices or prosthetics.
- Print Speed: Infill layer thickness can have an impact on the overall print duration. Thicker infill layers require fewer passes to complete the internal structure, resulting in faster printing times. This can be beneficial for large-scale production or time-sensitive projects.
Overall, the infill layer thickness is a critical parameter for optimizing the strength, weight, flexibility, and print speed of 3D printed objects. Understanding its importance allows users to fine-tune their prints to suit specific requirements, ensuring the desired performance and durability of the final product.
Factors Affecting Infill Layer Thickness
The choice of infill layer thickness in 3D printing is influenced by several factors. Let’s explore some of the key factors that affect this parameter:
- Print Object’s Purpose: The intended use of the printed object plays a significant role in determining the ideal infill layer thickness. For functional parts or prototypes that require high strength, a thicker infill layer is often preferred. On the other hand, objects that require flexibility or weight reduction may benefit from a thinner infill layer.
- Material Choice: Different 3D printing materials have varying properties and behaviors. Some materials, like PLA, may require a thicker infill layer to achieve optimal strength, while others, like flexible filaments, may require a thinner infill layer for better flexibility. It is important to consider the material’s specific characteristics and manufacturer’s recommendations when determining the infill layer thickness.
- Print Object Size and Geometry: The size and geometry of the print object can also impact the choice of infill layer thickness. Larger objects typically require thicker infill layers to ensure structural stability, while smaller objects may be fine with thinner layers. Complex geometries with intricate details may also require adjustments to the infill layer thickness to maintain print quality and structural integrity.
- Time Constraints: Time-sensitive projects may require faster printing with thicker infill layers to reduce the print duration. On the other hand, projects with more relaxed timelines may allow for thinner infill layers to achieve specific design and performance goals.
- Personal Preference: Ultimately, personal preference and experience can influence the choice of infill layer thickness. Some users may have specific preferences based on past successful prints and their familiarity with certain materials and printer settings.
It is important to note that the choice of infill layer thickness is not a one-size-fits-all approach. Various factors need to be considered to achieve the desired performance and characteristics of the printed object. Experimentation, along with a good understanding of these factors, can help users determine the ideal infill layer thickness for their specific 3D printing projects.
How to Determine the Ideal Infill Layer Thickness
Determining the ideal infill layer thickness for a 3D printing project involves a combination of experimentation and consideration of the desired outcome. Here are some guidelines to help you determine the right infill layer thickness:
- Consider the Object’s Requirements: Start by understanding the purpose and requirements of the printed object. Determine whether it needs to be strong, flexible, lightweight, or have specific performance characteristics.
- Refer to Manufacturer Guidelines: Check the manufacturer’s guidelines and recommendations for the specific 3D printing material you are using. They often provide suggested settings, including recommended infill layer thickness, based on their material’s properties.
- Test Different Infill Percentage: Experiment with various infill percentages along with different layer heights. Start with a low infill percentage and gradually increase it while observing the strength and integrity of the printed object. Keep in mind that increasing the infill percentage will also increase print time and material usage.
- Adjust Infill Layer Thickness: Once you have determined the suitable infill percentage for your project, start adjusting the infill layer thickness. Start with a thicker infill layer, such as 80% of your layer height, and print a test object. Observe the strength, weight, and flexibility of the object. If necessary, gradually decrease the infill layer thickness and retest until the desired outcome is achieved.
- Evaluate Print Quality: Throughout the testing process, closely monitor the print quality and overall appearance of the object. A well-balanced infill layer thickness should result in a smooth surface finish without any visible gaps or artifacts in the internal structure.
It’s important to approach the determination of the ideal infill layer thickness as an iterative process. Take time to analyze and evaluate the different test prints, making adjustments as needed. Each project might require slightly different infill layer thickness based on the specific design and performance requirements.
By following these guidelines and taking the time to fine-tune the infill layer thickness, you can maximize the strength, durability, and performance of your 3D printed object, ensuring that it meets your expectations and requirements.
A good infill layer thickness for 3D printing is typically between 15-30%. This provides a balance between strength and material usage. Experiment with different infill percentages to find the best option for your specific project.
Benefits of Using a Good Infill Layer Thickness
Using a good infill layer thickness in 3D printing offers several important benefits that contribute to the overall quality and functionality of the printed object. Let’s explore some of the key advantages:
- Enhanced Strength: A good infill layer thickness provides internal support to the printed object, resulting in improved strength and structural integrity. By choosing the appropriate infill layer thickness, you can ensure that the object can withstand the intended load or usage without deformation or failure.
- Optimized Weight-to-Strength Ratio: The infill layer thickness directly affects the weight of the printed object. By customizing the infill layer thickness to match the requirements of the project, you can achieve an optimal weight-to-strength ratio. This means that the object will be lightweight while still maintaining the necessary strength to fulfill its purpose.
- Improved Dimensional Accuracy: A well-calibrated infill layer thickness contributes to better dimensional accuracy of the printed object. The infill layer provides internal support that prevents warping or distortion during the printing process, resulting in a more precise and accurate final product.
- Material Conservation: Using the appropriate infill layer thickness allows you to optimize the amount of material used in the internal structure of the printed object. By reducing the infill layer thickness when feasible, you can conserve material and reduce printing costs without sacrificing the overall strength or functionality of the object.
- Customization Flexibility: Adjusting the infill layer thickness provides flexibility for customization based on specific project requirements. Whether you need added strength, flexibility, or weight reduction, you can fine-tune the infill layer thickness to match the desired properties of the printed object.
- Print Speed and Efficiency: Optimizing the infill layer thickness can also lead to faster print speeds. Thicker infill layers require fewer passes to complete the internal structure, resulting in reduced print time. This can be advantageous for large-scale production or time-sensitive projects.
By using a good infill layer thickness, you can achieve 3D printed objects that not only meet the desired strength and performance requirements but also minimize material usage, enhance dimensional accuracy, and reduce printing time. This ensures that your prints are efficient, cost-effective, and of high quality.
Challenges and Limitations of Adjusting Infill Layer Thickness
While adjusting the infill layer thickness in 3D printing offers various benefits, it also comes with its fair share of challenges and limitations. It’s important to be aware of these factors to make informed decisions. Here are some challenges and limitations you may encounter when adjusting infill layer thickness:
- Print Time: Thicker infill layers require more time to print, resulting in longer print durations. If you need to print objects quickly, using thicker infill layers may not be feasible.
- Material Usage: Increasing the infill layer thickness can significantly increase material consumption, leading to higher costs. This is especially important to consider if expensive or exotic materials are being used.
- Structural Integrity: While a thicker infill layer can provide increased strength, it can also result in reduced flexibility. This can be a limitation for certain applications that require both strength and flexibility. Finding the right balance between the two can be challenging.
- Print Surface Quality: Thicker infill layers can result in a more pronounced “grid” pattern on the surface of the printed object. This can detract from the desired surface finish or aesthetics, especially for objects that require a smooth or polished appearance.
- Print Resolution: Adjusting the infill layer thickness can potentially impact the overall print resolution. Thicker infill layers may result in more visible layer lines and reduced fine details, affecting the overall quality of the print.
- Compatibility with Printers and Software: The ability to adjust infill layer thickness can depend on the capabilities of your 3D printer and the software you are using. Some printers or software may have limitations on the range of infill layer thickness options available to users.
It’s important to balance the benefits and limitations when adjusting the infill layer thickness. Consider the specific requirements of your project, the desired outcomes, and the capabilities of your equipment and materials. Keep in mind that experimentation and iterative testing may be necessary to find the optimal infill layer thickness for each unique 3D printing project.
Conclusion
Infill layer thickness is a crucial parameter that significantly influences the strength, weight, flexibility, and overall quality of 3D printed objects. By understanding the importance of infill layer thickness and considering factors such as the object’s purpose, material choice, size and geometry, time constraints, and personal preference, users can determine the ideal infill layer thickness for their specific projects.
Adjusting the infill layer thickness offers numerous benefits, including enhanced strength, optimized weight-to-strength ratio, improved dimensional accuracy, material conservation, customization flexibility, and increased print speed and efficiency. However, there are also challenges and limitations to consider, such as longer print times, increased material usage, potential compromises in structural integrity, surface quality, print resolution, and compatibility with printers and software.
To achieve the desired outcomes and overcome these challenges, it is important to engage in iterative testing and experimentation, monitor print quality, and make adjustments as needed. Striking the right balance between strength, flexibility, weight, and other performance characteristics is key to obtaining high-quality 3D printed objects that meet your particular requirements.
In conclusion, infill layer thickness plays a vital role in the success of 3D printing projects. By understanding its significance, considering the influencing factors, and carefully adjusting this parameter, you can create strong, durable, and customized 3D printed objects that meet your specific needs. So, take the time to explore and optimize your infill layer thickness to unlock the full potential of your 3D printing endeavors.
Frequently Asked Questions about What Is A Good Infill Layer Thickness
Was this page helpful?
At Storables.com, we guarantee accurate and reliable information. Our content, validated by Expert Board Contributors, is crafted following stringent Editorial Policies. We're committed to providing you with well-researched, expert-backed insights for all your informational needs.
0 thoughts on “What Is A Good Infill Layer Thickness”