Home>Renovation & DIY>Tools & Equipment>What Is Sandpaper Made Of
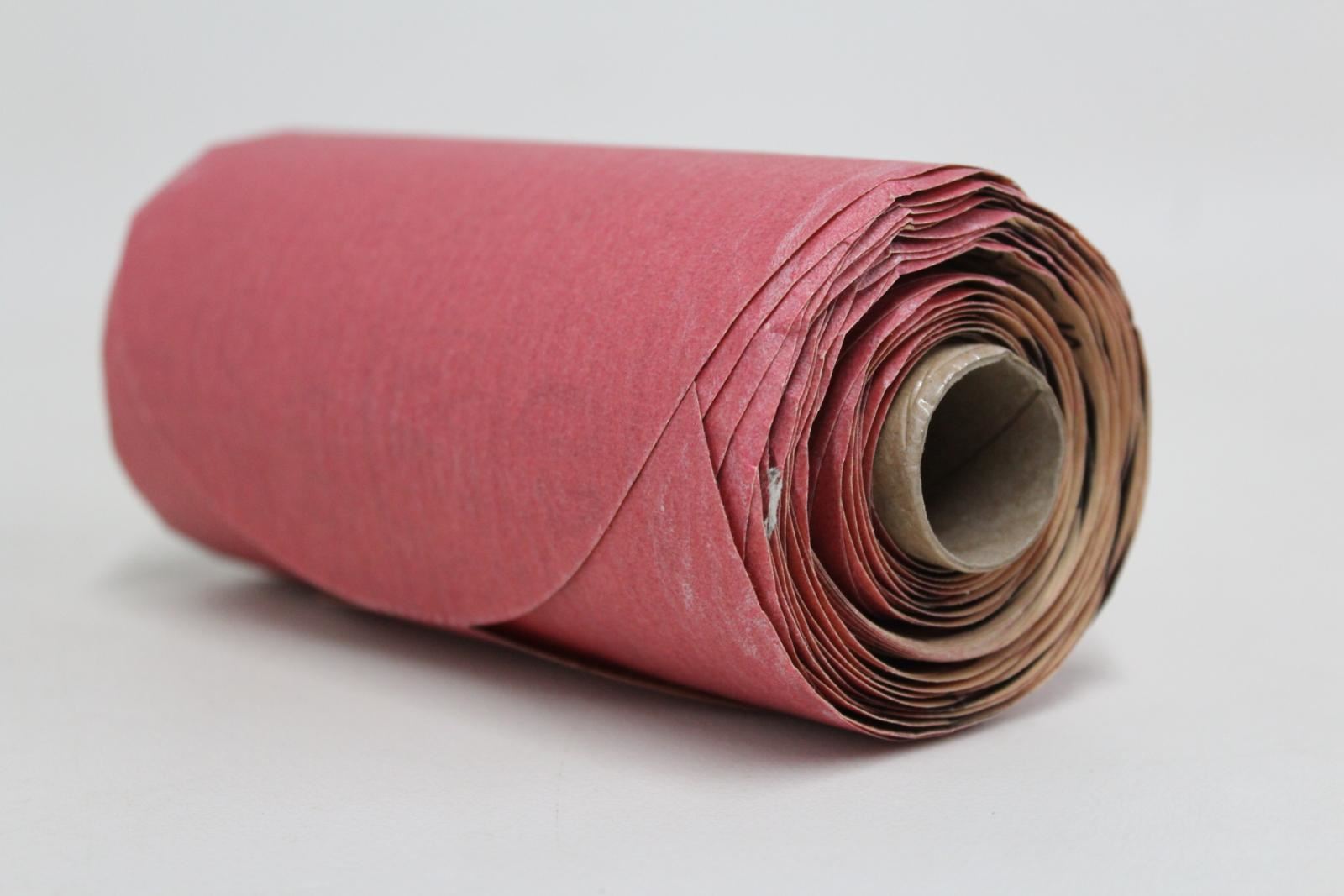
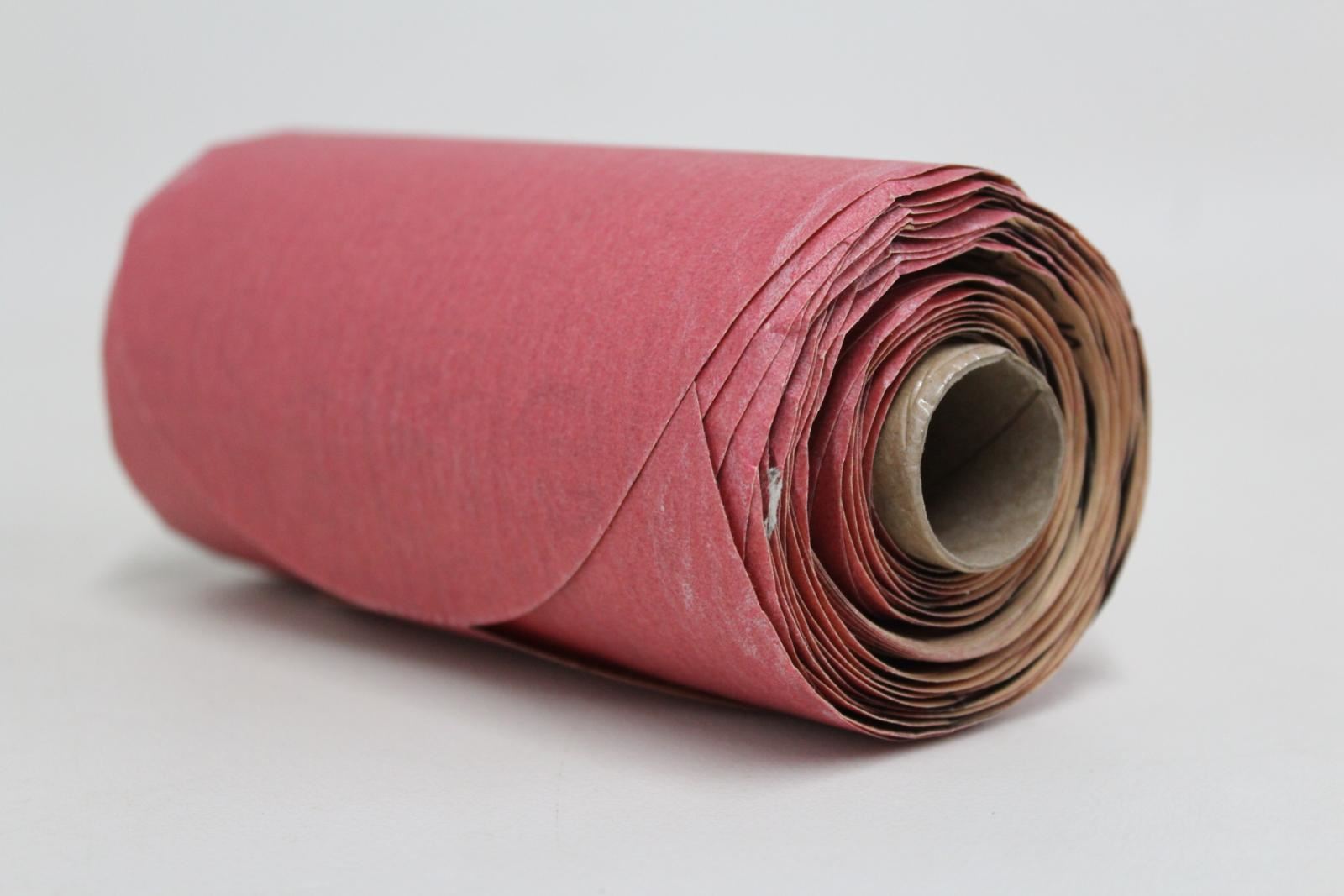
Tools & Equipment
What Is Sandpaper Made Of
Published: December 20, 2023
Discover what sandpaper is made of and its uses in tools and equipment. Learn about the materials and grits used for different applications.
(Many of the links in this article redirect to a specific reviewed product. Your purchase of these products through affiliate links helps to generate commission for Storables.com, at no extra cost. Learn more)
Introduction
Read more: What Is Sandpaper Used For
Introduction
When it comes to woodworking, metalworking, or even DIY home improvement projects, one indispensable tool that often comes to mind is sandpaper. This humble yet versatile tool has been a staple in workshops and households for centuries, aiding in the smoothing, shaping, and refining of various materials. But have you ever wondered what sandpaper is made of, how it came to be, and the intricate components that make it such an effective abrasive tool?
In this comprehensive guide, we will delve into the fascinating world of sandpaper, exploring its history, components, types, manufacturing process, and diverse applications. By the end of this journey, you will have a newfound appreciation for this seemingly simple yet incredibly impactful tool.
History of Sandpaper
Key Takeaways:
- Sandpaper is made of backing material, adhesive, and abrasive particles, working together to smooth and shape surfaces in woodworking, metalworking, and DIY projects.
- Sandpaper has a rich history dating back to ancient China, and its diverse types cater to specific needs, from woodworking to automotive refinishing, making it an essential tool for craftsmen and enthusiasts.
History of Sandpaper
The history of sandpaper can be traced back to ancient times when civilizations used abrasive materials to smooth and polish various surfaces. The concept of sandpaper, as we know it today, can be attributed to the Chinese, who are believed to have used crushed shells and sand adhered to parchment as early as the 13th century. This rudimentary form of sandpaper laid the foundation for the development of modern abrasives.
During the 18th century, the use of sandpaper gained momentum in Europe, particularly in the burgeoning industrial centers. Craftsmen and artisans recognized its efficacy in shaping and refining wood, metal, and other materials. The Industrial Revolution further propelled the production and refinement of sandpaper, leading to the introduction of mechanized manufacturing processes and the use of more diverse abrasive materials.
By the 20th century, sandpaper had become a ubiquitous tool in various industries, from construction and automotive manufacturing to woodworking and metalworking. Its evolution continued with the introduction of synthetic abrasives, which offered enhanced durability and precision. Today, sandpaper remains an essential tool in countless applications, embodying centuries of innovation and refinement.
Components of Sandpaper
Read more: What Is Insulation Made Of
Components of Sandpaper
Sandpaper may appear to be a straightforward tool, but its effectiveness lies in the intricate combination of materials that form its structure. The primary components of sandpaper include the backing material, the adhesive, and the abrasive particles.
Backing Material: The backing material serves as the foundation of the sandpaper, providing stability and support during the sanding process. It can be made of various materials, including paper, cloth, or polyester. Each type of backing material offers distinct advantages, such as flexibility, tear resistance, and durability, catering to different sanding requirements.
Adhesive: The adhesive, also known as the bond, plays a crucial role in securing the abrasive particles to the backing material. It must withstand the friction and heat generated during sanding while maintaining a strong bond with the abrasive. Different adhesives are utilized based on the type of abrasive and the intended application, ensuring optimal adhesion and longevity.
Abrasive Particles: The abrasive particles are the heart of sandpaper, responsible for the actual sanding and material removal. These particles can be made of natural minerals, such as garnet or emery, or synthetic materials like aluminum oxide, silicon carbide, or ceramic. The choice of abrasive material dictates the sandpaper’s suitability for specific tasks, with variations in hardness, sharpness, and durability.
By carefully balancing these components, sandpaper manufacturers create a diverse range of products tailored to different materials and surface treatments. Understanding the interplay of these components is essential for selecting the right sandpaper for a given application, ensuring optimal results and efficiency.
Types of Sandpaper
Types of Sandpaper
Sandpaper is available in a variety of types, each designed to address specific sanding needs and materials. Understanding the distinctions between these types is crucial for achieving desired results and maintaining the integrity of the surfaces being worked on.
1. Based on Backing Material:
- Paper Backing: Commonly used for woodworking and general purpose sanding, paper-backed sandpaper offers flexibility and ease of use. It is available in various weights and grades to accommodate different levels of abrasion.
- Cloth Backing: Cloth-backed sandpaper is prized for its durability and tear resistance, making it suitable for heavy-duty applications, metalworking, and shaping hard materials.
- Fiber or Film Backing: These backings are ideal for fine sanding and finishing work, offering exceptional flexibility and conformability for intricate surfaces.
2. Based on Abrasive Material:
- Aluminum Oxide: Known for its versatility and durability, aluminum oxide sandpaper is widely used for woodworking, metalworking, and general sanding tasks. It is available in various grits to accommodate different levels of abrasiveness.
- Silicon Carbide: This abrasive material is preferred for its exceptional sharpness and hardness, making it suitable for sanding hard and non-ferrous materials, such as glass, stone, and plastic.
- Zirconia Alumina: Offering high-performance sanding capabilities, zirconia alumina sandpaper excels in aggressive material removal and is often used for heavy-duty applications and shaping hard surfaces.
3. Based on Grit Size:
The grit size of sandpaper determines its abrasive coarseness or fineness, influencing the level of material removal and surface finish. Common grit sizes range from coarse (lower grits) for rapid material removal to fine (higher grits) for smooth finishing and polishing.
By familiarizing oneself with the diverse types of sandpaper available, individuals can make informed choices based on the specific requirements of their projects, ensuring efficient and effective sanding results.
Manufacturing Process
Read more: What Is A Trampoline Made Of
Manufacturing Process
The production of sandpaper involves a meticulous process that integrates various materials and technologies to create a versatile and reliable abrasive tool. The manufacturing process encompasses several key stages, each contributing to the quality and performance of the final product.
1. Backing Material Preparation: The manufacturing process begins with the preparation of the backing material, which can be paper, cloth, or other suitable substrates. The backing material undergoes treatment to enhance its strength, flexibility, and tear resistance, ensuring it can withstand the rigors of sanding.
2. Adhesive Application: A specialized adhesive is applied to the backing material, forming a strong and durable bond that will secure the abrasive particles during the sanding process. The adhesive must exhibit resilience to heat and friction, maintaining its integrity under demanding sanding conditions.
3. Abrasive Coating: The abrasive particles, which can be natural minerals or synthetic materials, are precisely coated onto the adhesive-treated backing material. This process requires precision to ensure uniform distribution and secure adhesion of the abrasive, optimizing its cutting performance and longevity.
4. Sizing and Cutting: Once the abrasive coating is applied, the sandpaper undergoes sizing and cutting processes to achieve the desired dimensions and formats. This stage involves precision cutting to create sheets, rolls, discs, or other configurations tailored to specific applications and sanding equipment.
5. Quality Control and Packaging: Quality control measures are implemented to assess the integrity, abrasiveness, and consistency of the manufactured sandpaper. Following rigorous testing, the sandpaper is packaged according to its type, grit size, and intended use, ready to be distributed to workshops, industries, and retail outlets.
By adhering to stringent manufacturing standards and leveraging advanced technologies, sandpaper manufacturers produce a diverse range of high-quality abrasive products that cater to the varying needs of craftsmen, artisans, and industrial professionals.
Uses of Sandpaper
Uses of Sandpaper
Sandpaper finds an extensive array of applications across diverse industries and DIY projects, owing to its versatility and effectiveness in material preparation, finishing, and surface refinement. From woodworking and metalworking to automotive maintenance and home renovations, sandpaper serves as an indispensable tool for achieving smooth, polished, and precisely shaped surfaces.
Woodworking: In woodworking, sandpaper is utilized for shaping, smoothing, and refining wooden surfaces, whether for furniture, cabinetry, or artisanal crafts. It aids in removing imperfections, leveling uneven surfaces, and achieving the desired texture and finish, contributing to the overall aesthetic and quality of the woodwork.
Metalworking: Metalworkers rely on sandpaper for deburring, polishing, and preparing metal surfaces for welding, painting, or coating applications. It facilitates the removal of rust, corrosion, and blemishes, ensuring that metal components exhibit optimal durability and visual appeal.
Automotive Refinishing: The automotive industry extensively utilizes sandpaper for refinishing and restoring vehicle surfaces. Whether for smoothing body panels, preparing surfaces for paint or clear coat application, or addressing imperfections in automotive finishes, sandpaper plays a critical role in maintaining the aesthetic and protective qualities of vehicles.
Home Improvement and Repairs: From sanding drywall during renovations to preparing surfaces for painting or varnishing, sandpaper is a go-to tool for homeowners and DIY enthusiasts. It aids in achieving smooth and uniform surfaces, whether for walls, furniture, or fixtures, enhancing the visual appeal and longevity of home improvements.
Art and Craft Projects: Artists and crafters utilize sandpaper for sculpting, shaping, and refining various materials, including clay, wood, and certain types of plastics. Its precision and control make it an invaluable tool for achieving intricate details and desired textures in artistic creations.
These diverse applications underscore the indispensable nature of sandpaper in numerous industries and creative pursuits, showcasing its pivotal role in material preparation, surface refinement, and the pursuit of quality craftsmanship.
Conclusion
Read more: What Is Cutlery Made Of
Conclusion
As we conclude our exploration of sandpaper, it becomes evident that this seemingly humble tool embodies centuries of innovation, craftsmanship, and practical utility. From its humble origins in ancient China to its indispensable presence in modern workshops and industries, sandpaper has stood the test of time as an essential tool for shaping, refining, and perfecting a myriad of materials and surfaces.
The intricate components of sandpaper, including the backing material, adhesive, and abrasive particles, work in harmony to deliver precise and effective material removal and surface preparation. This synergy allows craftsmen, artisans, and enthusiasts to achieve smooth finishes, precise contours, and polished surfaces across woodworking, metalworking, automotive refinishing, and various DIY projects.
Furthermore, the diverse types of sandpaper, ranging from paper-backed to cloth-backed, and the wide array of abrasive materials and grit sizes, offer tailored solutions for specific applications and materials, empowering individuals to select the most suitable sandpaper for their unique needs.
From the meticulous manufacturing process to the extensive range of uses spanning woodworking, metalworking, automotive refinishing, home improvement, and artistic endeavors, sandpaper remains an indispensable ally in the pursuit of quality craftsmanship, surface refinement, and creative expression.
As we reflect on the enduring legacy of sandpaper, we recognize its role as a silent yet indispensable partner in countless projects and industries, embodying the spirit of precision, innovation, and versatility. Whether in the hands of a seasoned artisan or a passionate DIY enthusiast, sandpaper continues to shape and refine the world around us, leaving behind a legacy of craftsmanship and quality.
Frequently Asked Questions about What Is Sandpaper Made Of
Was this page helpful?
At Storables.com, we guarantee accurate and reliable information. Our content, validated by Expert Board Contributors, is crafted following stringent Editorial Policies. We're committed to providing you with well-researched, expert-backed insights for all your informational needs.
0 thoughts on “What Is Sandpaper Made Of”