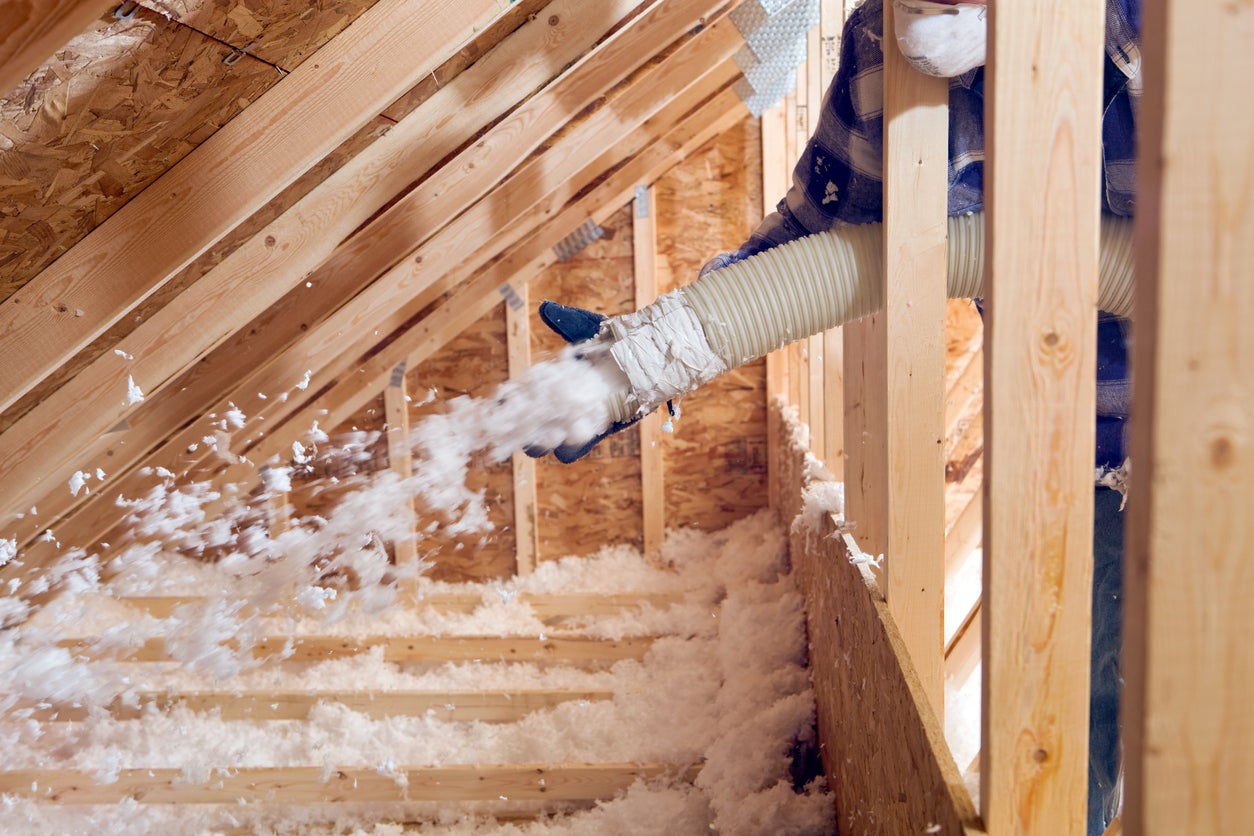
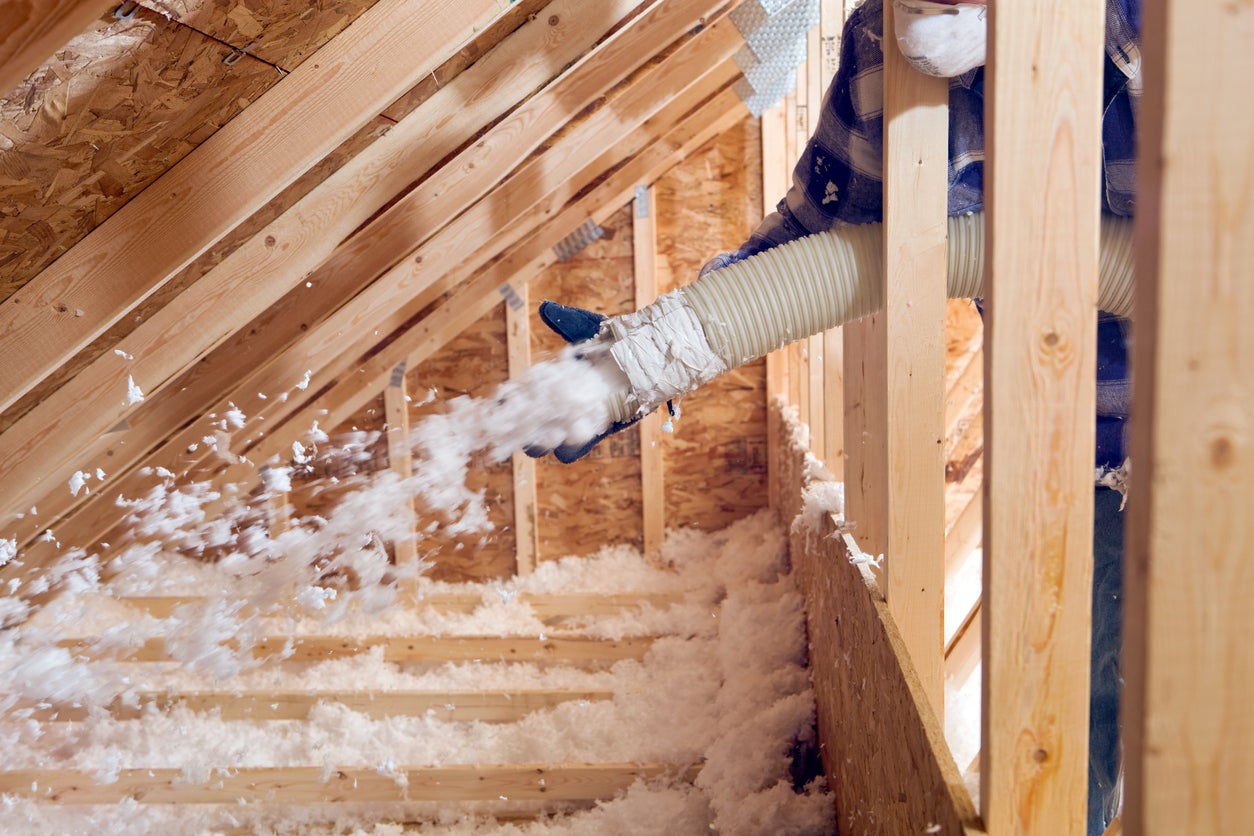
Articles
How Long Does Blown In Insulation Last
Modified: October 19, 2024
Discover how long blown-in insulation typically lasts and get expert advice in our informative articles.
(Many of the links in this article redirect to a specific reviewed product. Your purchase of these products through affiliate links helps to generate commission for Storables.com, at no extra cost. Learn more)
Introduction
Blown-in insulation is a popular choice for homeowners looking to improve the energy efficiency and comfort of their homes. This type of insulation, also known as loose-fill insulation, consists of small particles or fibers that are blown into an attic or wall cavity using specialized equipment. It is an effective way to fill gaps and create a barrier against heat transfer.
While blown-in insulation has numerous benefits, such as reducing energy costs and improving indoor comfort, homeowners may wonder about its lifespan and how long it will continue to provide these benefits. In this article, we will explore the factors that affect the lifespan of blown-in insulation, how long it typically lasts, and signs of deterioration to look out for.
Understanding the lifespan of blown-in insulation can help homeowners make informed decisions about maintenance and replacement to ensure the continued efficiency and effectiveness of their insulation.
Key Takeaways:
- Blown-in insulation, whether fiberglass or cellulose, can typically last for 20 to 30 years or more when installed properly and not subject to excessive moisture, pests, or damage. Proper maintenance and proactive measures can extend its lifespan and ensure optimal energy efficiency.
- Regular inspections, moisture management, and staying informed about energy efficiency standards are essential for maximizing the lifespan of blown-in insulation. By taking proactive measures, homeowners can protect their investment and enjoy long-term energy savings and comfort.
Read more: Who Does Blown-In Insulation Near Me
What is Blown In Insulation?
Blown-in insulation, also known as loose-fill insulation, is a type of insulation material that is used to fill spaces such as attics, walls, and floors. Unlike traditional batt or roll insulation, blown-in insulation is made up of small particles or fibers that are blown into the desired area using specialized equipment.
There are two main types of blown-in insulation: fiberglass and cellulose. Fiberglass blown-in insulation is made from tiny glass fibers that are blown into the space, creating a thermal barrier. Cellulose blown-in insulation is made from recycled paper and treated with fire-retardant chemicals. Both types of blown-in insulation provide excellent thermal insulation and can effectively reduce heat transfer.
The installation process for blown-in insulation involves using a blowing machine that agitates the insulation material and blows it into the designated area. This process ensures that the insulation fills all the nooks and crannies, creating a uniform layer that provides optimal thermal resistance.
Blown-in insulation offers several advantages over other types of insulation. It is highly effective in reducing heat loss and heat gain, making it an excellent choice for improving energy efficiency in homes. It can also fill hard-to-reach areas, such as around pipes, wires, and irregularly shaped spaces, providing better coverage than traditional batt or roll insulation.
Another benefit of blown-in insulation is its ability to resist settling. Over time, some types of insulation may settle, reducing the effectiveness of the insulation layer. Blown-in insulation, however, maintains its integrity and thermal resistance over the long term, ensuring consistent performance.
Overall, blown-in insulation is a versatile and efficient option for homeowners looking to improve the insulation of their homes. Its ability to fill gaps and provide uniform coverage makes it an excellent choice for both new construction and retrofitting older homes.
Factors Affecting the Lifespan of Blown In Insulation
While blown-in insulation is known for its durability, several factors can affect its lifespan. It is important to understand these factors to ensure that your insulation continues to perform optimally for as long as possible. Here are some key factors that can influence the lifespan of blown-in insulation:
- Installation Quality: The quality of the installation plays a crucial role in determining how long blown-in insulation will last. If installed improperly, insulation can become compressed, allowing air gaps to form and reducing its effectiveness. It is essential to hire a professional insulation contractor who has experience in the proper installation of blown-in insulation to ensure its longevity.
- Moisture Exposure: Moisture is a primary enemy of insulation and can significantly reduce its lifespan. If blown-in insulation comes into contact with water due to leaks or excessive humidity, it can degrade and lose its insulating properties. Moisture can also lead to mold or mildew growth, affecting both the insulation and the overall indoor air quality. Proper moisture management, such as addressing leaks and maintaining proper ventilation, is crucial to prolong the lifespan of blown-in insulation.
- Pests and Rodents: Pests and rodents can cause damage to blown-in insulation by nesting or burrowing through it. They can disrupt the integrity of the insulation layer and create air gaps, reducing its effectiveness. Taking measures to prevent pests and rodents from accessing your insulation, such as sealing entry points and using pest deterrents, can help preserve its lifespan.
- Settling: While blown-in insulation is less prone to settling than other types, it can still experience some settling over time. Settling occurs when the insulation particles gradually shift downward, creating gaps and reducing the insulation’s thermal performance. Installing insulation to the recommended thickness and consulting with a professional to ensure proper installation techniques can minimize settling and extend the lifespan of blown-in insulation.
- Exposure to UV Rays: Blown-in insulation installed in attic spaces may be exposed to sunlight through roof vents or skylights. Over time, exposure to UV rays can cause the insulation material to degrade and lose its insulating properties. Using proper attic insulation materials with UV-resistant properties can help mitigate the effects of sun exposure and prolong the lifespan of blown-in insulation.
- Changes in Building Codes and Energy Efficiency Standards: Building codes and energy efficiency standards are constantly evolving. What was once considered adequate insulation may no longer meet current standards. Staying updated with the latest building codes and energy efficiency requirements can help ensure that your blown-in insulation remains effective and meets the necessary standards for optimal lifespan.
By considering these factors and taking the necessary precautions, homeowners can maximize the lifespan of blown-in insulation and enjoy its benefits for many years to come.
Typical Lifespan of Blown In Insulation
The lifespan of blown-in insulation can vary depending on various factors, including the type of insulation material used, the quality of installation, and the maintenance practices employed. However, on average, blown-in insulation can last for several decades.
Fiberglass blown-in insulation, when installed correctly and not subject to excessive moisture or damage, can have a lifespan of 20 to 30 years or more. This type of insulation is durable and resistant to mold, pests, and settling, making it a reliable choice for long-term insulation performance.
Cellulose blown-in insulation, made from recycled paper, can also have a similar lifespan of 20 to 30 years. It is treated with fire-retardant chemicals to enhance its resistance to fire and pests. With proper installation and maintenance, cellulose blown-in insulation can provide effective thermal insulation for many years.
It is important to note that the lifespan of blown-in insulation can be influenced by external factors, such as moisture exposure, pests, and inadequate installation. Regular inspections and maintenance can help identify any issues and address them promptly, prolonging the lifespan of the insulation.
Additionally, changes in building codes and energy efficiency standards may require homeowners to upgrade or add insulation to meet the new requirements. While blown-in insulation may have a long lifespan, it is important to stay informed about any updates in these regulations to ensure that your insulation remains effective and compliant.
If you are unsure about the condition or lifespan of your blown-in insulation, it is advisable to consult with a professional insulation contractor. They can assess the insulation, identify any signs of deterioration, and provide guidance on whether replacement or additional insulation is needed.
Overall, with proper installation, regular maintenance, and adherence to building codes and energy efficiency standards, blown-in insulation can provide reliable thermal insulation for several decades, contributing to energy savings, comfort, and a more sustainable home environment.
Blown-in insulation can last up to 20-30 years if properly installed and maintained. Regular inspections can help identify any issues early on.
Signs of Deterioration in Blown In Insulation
Over time, blown-in insulation can deteriorate or become less effective due to various factors. It is important to be aware of the signs of deterioration so that you can take appropriate action to maintain or replace your insulation. Here are some common signs that indicate the deterioration of blown-in insulation:
- Compacted or Settled Insulation: If you notice that the blown-in insulation appears compressed or settled in certain areas, it may be a sign of inadequate installation or gradual shifting of the insulation material. Compacted or settled insulation may have reduced thermal resistance and should be addressed to maintain optimal insulation performance.
- Moisture Stains or Water Damage: Visible moisture stains or signs of water damage on the surface of the insulation or in the surrounding areas can indicate a problem. Moisture can cause the insulation to degrade, lose its insulating properties, and promote the growth of mold or mildew. Addressing the source of the moisture and replacing the affected insulation is crucial to maintain a healthy and efficient home environment.
- Unwanted Pests or Rodent Activity: Presence of pests or signs of rodent activity, such as droppings or nesting materials, within the insulation may signal damage to the insulation layer. Pests can disrupt the integrity of the insulation, create air gaps, and compromise its effectiveness. Taking immediate action to address pest infestations and replace the affected insulation is necessary to prevent further damage.
- Inconsistent Indoor Temperatures: If you notice significant temperature differences or inconsistencies within your home, it could be a sign that your blown-in insulation is deteriorating. Inadequate insulation performance can result in heat loss or gain, leading to discomfort and increased energy consumption. Consulting with a professional insulation contractor can help determine whether insulation replacement or additional insulation is necessary.
- Drafts or Air Leaks: Blown-in insulation is designed to fill gaps and create an airtight barrier against heat transfer. If you feel drafts or notice air leaks around windows, doors, outlets, or other areas, it may indicate deteriorating or insufficient insulation. Conducting a thorough inspection and repairing any gaps or leaks can help restore the insulation’s effectiveness.
- Old Age or Outdated Insulation: If your blown-in insulation is approaching the end of its expected lifespan or does not meet current building codes and energy efficiency standards, it may be time for replacement or additional insulation. Keeping track of the age of your insulation and staying informed about any updates in regulations will help ensure that your insulation remains effective and efficient.
If you notice any of these signs or have concerns about the condition of your blown-in insulation, it is recommended to consult with a professional insulation contractor. They can assess the insulation, identify any issues, and provide expert advice on whether repair or replacement is needed to maintain optimal insulation performance.
Extending the Lifespan of Blown In Insulation
To maximize the lifespan of blown-in insulation and ensure its long-term effectiveness, proper care and maintenance are essential. Here are some key practices to help extend the lifespan of your blown-in insulation:
- Maintain Proper Moisture Management: Moisture is one of the primary factors that can lead to the deterioration of insulation. Regularly inspect your home for any signs of leaks or areas where moisture may be entering. Promptly address any issues by repairing leaks, improving ventilation, or adding moisture barriers where necessary. Proper moisture management will help preserve the integrity and thermal resistance of your blown-in insulation.
- Seal Air Leaks: Insulation works most effectively when there are no air leaks or drafts that can compromise its performance. Conduct a thorough inspection of your home to identify and seal any air leaks around windows, doors, electrical outlets, and other areas. Properly sealing these gaps will help maintain a consistent temperature and reduce the strain on your insulation.
- Prevent Pest and Rodent Infestations: Pests and rodents can cause damage to insulation by nesting or burrowing through it, creating air gaps and reducing its effectiveness. Take preventative measures to keep pests away from your home, such as sealing entry points and using pest deterrents. Regularly inspect your attic or crawl space for signs of unwanted pests and take immediate action to address any infestations.
- Maintain Adequate Ventilation: Proper ventilation is key to preventing moisture buildup and promoting optimal airflow within your home. Make sure that attic vents, roof vents, and exhaust fans are clear and functioning effectively. Good ventilation will help prevent excess moisture and ensure that your insulation remains dry and efficient.
- Regularly Inspect Insulation: Schedule regular inspections of your blown-in insulation to check for signs of deterioration or damage. Look for any compacted or settled areas, moisture stains, pests, or other issues mentioned earlier. Addressing potential problems early on can help prevent further damage and prolong the lifespan of your insulation.
- Stay Informed About Energy Efficiency Standards: Keep yourself updated with the latest building codes and energy efficiency standards to ensure that your blown-in insulation meets the necessary requirements. Periodically assess the insulation in your home and consult with a professional if upgrades or additional insulation is needed to maintain compliance with these standards.
By following these practices, homeowners can extend the lifespan of their blown-in insulation and ensure optimal energy efficiency and insulation performance. Regular maintenance and proactive measures will help protect your investment in insulation and contribute to a comfortable and energy-efficient home environment.
Conclusion
Blown-in insulation, or loose-fill insulation, is a highly effective and popular option for improving energy efficiency and comfort in homes. Understanding the lifespan of blown-in insulation and the factors that can influence its longevity is crucial for homeowners who want to maximize the performance and longevity of their insulation.
Blown-in insulation, whether fiberglass or cellulose, can typically last for 20 to 30 years or more when installed properly and not subject to excessive moisture, pests, or damage. However, it is important to stay vigilant and be aware of signs of deterioration, such as compacted or settled insulation, moisture stains, pests, inconsistent temperatures, and air leaks.
By applying proper maintenance techniques, homeowners can extend the lifespan of their blown-in insulation. This includes managing moisture effectively, sealing air leaks, preventing pest and rodent infestations, maintaining ventilation, regularly inspecting the insulation, and staying informed about energy efficiency standards.
Regular inspections by professional insulation contractors can also help identify any issues and provide expert advice on maintenance or replacement if necessary. Considering the age of the insulation and staying informed about building codes and energy efficiency standards will ensure that your blown-in insulation remains effective and efficient for years to come.
By investing in blown-in insulation and taking proactive measures to protect and maintain it, homeowners can achieve significant energy savings, improve indoor comfort, and contribute to a more sustainable living environment. With proper care and attention, blown-in insulation can continue to provide thermal insulation benefits for an extended period, making it a worthwhile investment for any homeowner.
Frequently Asked Questions about How Long Does Blown In Insulation Last
Was this page helpful?
At Storables.com, we guarantee accurate and reliable information. Our content, validated by Expert Board Contributors, is crafted following stringent Editorial Policies. We're committed to providing you with well-researched, expert-backed insights for all your informational needs.
0 thoughts on “How Long Does Blown In Insulation Last”