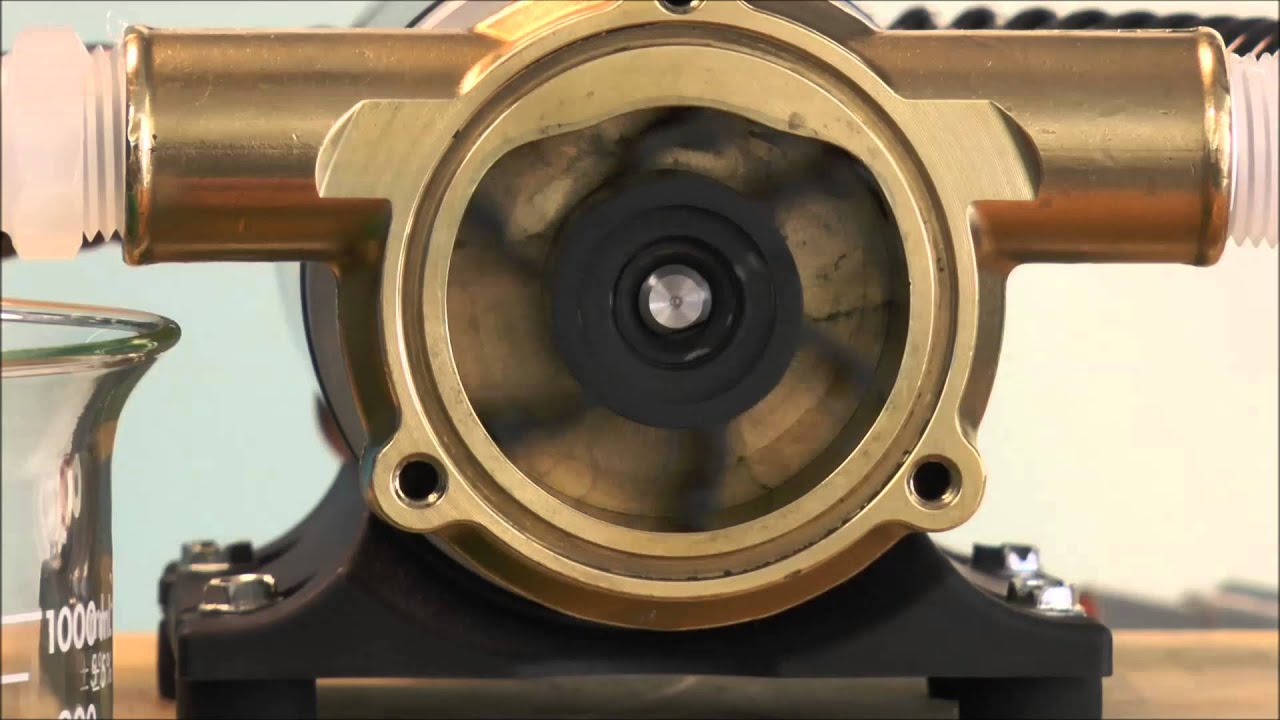
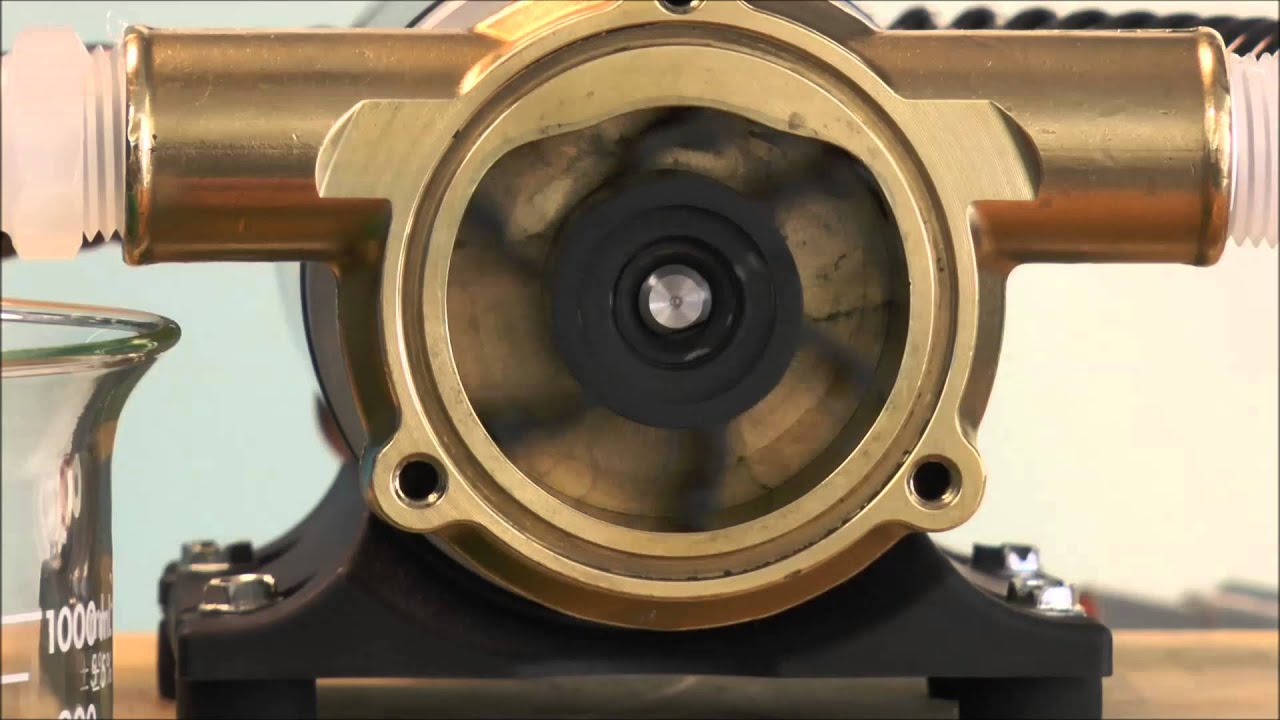
Articles
What Does A Water Pump Impeller Do
Modified: January 8, 2024
Learn about the function and importance of a water pump impeller in this informative article. Find out how it facilitates coolant circulation to prevent engine overheating.
(Many of the links in this article redirect to a specific reviewed product. Your purchase of these products through affiliate links helps to generate commission for Storables.com, at no extra cost. Learn more)
Introduction
Welcome to the world of water pump impellers! If you’ve ever wondered how water is efficiently circulated within a pump, then understanding the role of a water pump impeller is essential. This small but mighty component plays a crucial role in the operation of various water pump systems, from household appliances to industrial machinery.
In this article, we will explore the world of water pump impellers, diving into their definition, function, components, types, and the importance of maintaining them. We will also discuss common issues that can arise with water pump impellers and provide tips for maintaining and replacing them.
By the end of this article, you will have a comprehensive understanding of what a water pump impeller does and how its proper functioning contributes to the smooth operation of water pump systems.
Key Takeaways:
- The water pump impeller is a crucial component that generates fluid flow and pressure within pump systems, impacting efficiency and performance. Regular maintenance and timely replacement are essential to prevent issues and ensure optimal pump operation.
- Different types of water pump impellers, such as open, closed, semi-open, mixed flow, and axial flow, offer distinct advantages for specific pumping applications. Choosing the right impeller type is crucial for optimizing pump performance, efficiency, and reliability.
Read more: How To Change A Water Pump Impeller
Definition of a Water Pump Impeller
A water pump impeller is a rotating component designed to move water or other fluids through a pump system. It is typically a wheel-like structure with curved blades or vanes attached to a central shaft. The impeller is housed within the pump housing and is connected to a motor that provides the rotational power.
The impeller’s primary function is to create a centrifugal force that propels the fluid outwards, increasing its pressure. This pressure difference allows the fluid to be pushed through the pump and into the desired system, whether it is a plumbing system, a cooling system, or an irrigation system.
Impellers are commonly used in various types of pumps, including centrifugal pumps, submersible pumps, and circulation pumps. The design of the impeller, including the number and shape of the blades, is optimized for specific pump applications and fluid properties.
Overall, the water pump impeller is a crucial component that directly affects the efficiency and performance of a pump system. Its design and functionality directly impact the flow rate, pressure, and energy consumption of the system.
Function of a Water Pump Impeller
The function of a water pump impeller is to generate fluid flow and create pressure within a pump system. When the impeller rotates, the curved blades or vanes create a centrifugal force that pushes the fluid outwards. This outward force increases the pressure of the fluid, allowing it to be pumped through the system.
The impeller’s main function is to convert the rotational energy from the motor into kinetic energy for the fluid. As the impeller spins, it transfers its mechanical energy to the fluid, causing it to move from the inlet to the outlet of the pump system.
The fluid enters the pump through the inlet, and as it encounters the spinning impeller, it is accelerated and forced towards the outer edges of the impeller. This acceleration and outward flow cause the pressure to increase, creating the necessary force to move the fluid through the system.
The impeller’s shape, size, and number of blades play a crucial role in determining the flow rate, pressure, and efficiency of the pump system. Different impeller designs are selected based on the specific requirements of the application, such as desired flow rate, fluid viscosity, and system constraints.
In addition to generating fluid flow, water pump impellers also help to circulate and mix the fluid within the system. This is particularly important in applications where heat transfer or chemical reactions are involved. The impeller’s rotational motion creates turbulence and agitation, ensuring proper mixing and distribution of the fluid.
Overall, the function of a water pump impeller is essential for the efficient operation of a pump system. It converts the motor’s rotational energy into fluid movement and pressure, allowing for the transportation of fluids in various applications, ranging from residential plumbing to industrial processes.
Components of a Water Pump Impeller
A water pump impeller consists of several key components that work together to effectively move and propel the fluid through the pump system. These components ensure the impeller’s functionality and enhance its performance. Let’s take a closer look at the main components of a water pump impeller:
- Blades or Vanes: The blades or vanes are the primary component of the impeller. They are curved structures attached to the central hub of the impeller. The design, shape, and number of blades vary depending on the specific application and pump type. The blades are responsible for generating the centrifugal force that propels the fluid outward and creates pressure.
- Hub: The hub is the central part of the impeller that holds the blades together. It provides stability and ensures that the blades are properly attached to the impeller. The hub is usually a solid structure that connects to the impeller shaft.
- Impeller Shaft: The impeller shaft is a rotating component that connects the impeller to the motor. It transmits the rotational power from the motor to the impeller, causing it to spin. The impeller shaft needs to be durable and well-balanced to ensure smooth operation and minimize vibrations.
- Impeller Housing: The impeller housing, also known as the volute or casing, is the enclosure that surrounds the impeller. It guides the flow of the fluid and directs it towards the outlet of the pump. The shape of the impeller housing affects the efficiency of the pump system by optimizing the fluid flow and minimizing energy losses.
- Wear Rings: Some impellers may include wear rings, which are stationary components located on either side of the impeller. Wear rings create a small radial gap between the impeller and the housing, reducing the risk of friction and wear. They help maintain the impeller’s efficiency and improve its lifespan.
The components of a water pump impeller work harmoniously to generate fluid flow and pressure within the pump system. These components undergo various design considerations to ensure optimal performance and longevity. The selection and configuration of these components depend on the specific pump application, fluid properties, and system requirements.
Types of Water Pump Impellers
Water pump impellers come in various types, each designed to suit different pumping applications and fluid properties. The selection of the impeller type depends on factors such as flow rate, pressure requirements, and the nature of the fluid being pumped. Let’s explore some of the most common types of water pump impellers:
- Open Impeller: An open impeller has blades that are not enclosed or covered by any additional structures. It is the simplest impeller design and is commonly used in low-pressure applications. Open impellers are easy to manufacture and maintain, and they allow for handling fluids with high solid content or viscosity. However, open impellers are less efficient compared to other impeller types, as they can create high turbulence and energy loss.
- Closed Impeller: A closed impeller has blades that are enclosed within a housing. This design improves the impeller’s efficiency by reducing turbulence and minimizing energy losses. Closed impellers are commonly used in high-pressure and high-performance applications. They are more complex to manufacture and require precise manufacturing and balancing to ensure optimal performance.
- Semi-Open Impeller: A semi-open impeller has blades that are partially enclosed by a shroud on one side and open on the other. This design allows for handling fluids with a certain amount of solids or abrasives. Semi-open impellers are commonly used in applications where a balance between efficiency and handling debris is required, such as wastewater treatment and solids handling pumps.
- Mixed Flow Impeller: A mixed flow impeller combines elements of both radial flow and axial flow impellers. The blades of a mixed flow impeller are curved, allowing for a combination of radial and axial fluid movement. This impeller type is used in applications where moderate flow rates and medium to high pressures are required, such as irrigation pumps and HVAC systems.
- Axial Flow Impeller: An axial flow impeller moves the fluid parallel to the impeller shaft. It has blades that resemble the shape of a propeller. Axial flow impellers are commonly used in applications where large flow rates and low to moderate pressures are required, such as cooling towers and marine propellers.
Each type of water pump impeller offers distinct advantages and is suitable for specific pumping applications. The selection of the impeller type should consider factors such as the desired flow rate, pressure requirements, fluid properties, and system constraints. Choosing the right impeller type is crucial for optimizing pump performance, efficiency, and reliability.
The water pump impeller is responsible for circulating coolant through the engine to maintain optimal operating temperature. It’s important to regularly inspect and replace a damaged impeller to prevent overheating and engine damage.
Importance of Maintaining a Water Pump Impeller
Maintaining a water pump impeller is essential for ensuring the efficient and reliable operation of a pump system. Neglecting regular maintenance can lead to various issues that can affect the performance and lifespan of the impeller as well as the overall functionality of the pump system. Let’s explore the importance of maintaining a water pump impeller:
- Optimal Pump Performance: The impeller is a crucial component that dictates the flow rate and pressure generated by the pump. Regular maintenance, including cleaning and removing any debris or buildup on the impeller blades, ensures optimal pump performance by reducing friction, increasing fluid flow, and minimizing energy losses.
- Prevention of Clogging: Debris, sediment, or other contaminants can accumulate on the impeller blades, leading to clogging and reduced water flow. Regular maintenance allows for the removal of such obstructions, preventing clogging issues and maintaining a steady flow of water through the pump system.
- Extended Lifespan: Proper maintenance of the impeller, including regular inspection and cleaning, can help extend its lifespan. By keeping the impeller in good condition, you can prevent premature wear, corrosion, and damage, ensuring the impeller’s longevity and avoiding the need for frequent replacements.
- Prevention of System Failures: A poorly maintained water pump impeller can contribute to system failures and breakdowns. If the impeller is not functioning properly, the pump may struggle to provide sufficient water flow or pressure, leading to inefficient performance and potential system malfunctions. Regular maintenance helps identify and address impeller issues before they escalate and cause major problems with the pump system.
- Energy Efficiency: A well-maintained impeller allows the pump system to operate at optimum efficiency, reducing energy consumption. A dirty or damaged impeller can make the pump work harder, consuming more energy to achieve the desired flow rate. By keeping the impeller clean and in good condition, energy efficiency is maintained, leading to cost savings and reduced environmental impact.
In summary, regular maintenance of a water pump impeller is crucial to ensure optimal pump performance, prevent clogging, extend the impeller’s lifespan, prevent system failures, and maintain energy efficiency. By dedicating time and effort to maintaining the impeller, you can maximize the functionality and longevity of your pump system, saving both time and money in the long run.
Common Issues with Water Pump Impellers
Water pump impellers, like any mechanical component, can experience issues over time due to factors such as wear and tear, improper maintenance, or system malfunctions. Identifying and addressing these issues promptly is crucial to prevent further damage and maintain the functionality of the pump system. Let’s explore some common issues that can occur with water pump impellers:
- Erosion and Corrosion: Water impellers are often exposed to abrasive or corrosive fluids, leading to erosion or corrosion of the impeller’s surface. Over time, this can affect the impeller’s efficiency and integrity, resulting in reduced pumping capacity and potential leakage. Regular inspection and maintenance can help identify signs of erosion or corrosion and prompt the necessary repairs or replacements.
- Clogging: Debris, sediment, or other particles in the fluid being pumped can accumulate on the impeller blades, leading to clogging. This can reduce the flow rate and pressure output of the pump, causing inefficient performance and potentially damaging the impeller. Regular cleaning and maintenance can help prevent clogging issues and ensure smooth operation.
- Imbalance: If the impeller is not properly balanced, it can cause vibrations and mechanical stress on the pump system. This can lead to premature wear and tear, decreased efficiency, and even system failures. Regular inspection and balancing of the impeller are necessary to prevent imbalances and maintain stable operation.
- Damage to Blades: The impeller blades can become damaged due to impacts, abrasion, or foreign objects entering the pump system. Damaged blades can cause turbulence, reduced flow rate, and decreased pump efficiency. It is important to regularly inspect the impeller blades for any signs of damage and replace or repair them as needed.
- Wear and Tear: Over time, the continuous rotation and exposure to fluid can cause wear and tear on the impeller’s components. This can include deterioration of the blades, wear on the hub or shaft, and general degradation of the impeller’s surface. Regular maintenance and replacement of worn-out components can prevent further damage and ensure the impeller’s longevity.
It is important to address these common issues promptly to prevent further damage and maintain the functionality and efficiency of the pump system. Regular inspection, maintenance, and timely repairs or replacements are key in keeping the water pump impeller in optimal operating condition.
Signs of a Failing Water Pump Impeller
Identifying signs of a failing water pump impeller is crucial to prevent further damage to the pump system and address any issues promptly. A failing impeller can lead to decreased pump performance, reduced water flow, and potential system malfunctions. Here are some common signs that may indicate a failing water pump impeller:
- Reduced Water Flow: If you notice a significant decrease in the water flow from your pump system, it could be a sign of a failing impeller. The impeller’s blades may be worn down or damaged, hindering its ability to push water effectively through the system. This can result in inadequate water pressure and diminished performance.
- Increased Noise and Vibrations: A failing impeller may cause increased noise and vibrations during pump operation. This can be a result of imbalances or damaged blades that disrupt the smooth rotation of the impeller. Unusual noises or excessive vibrations should be investigated promptly to prevent further damage to the impeller and other components.
- Overheating: A failing impeller can cause the pump system to overheat. If the impeller is not functioning optimally, it may not be able to circulate water effectively, leading to inadequate cooling. Overheating can result in pump inefficiency, system malfunctions, and potential damage to other components.
- Leakage: A failing impeller can contribute to water leakage from the pump system. Damaged blades or worn-out seals can cause fluid to escape, resulting in visible leaks or puddles around the pump. If you notice any signs of leakage, it is important to address them promptly to prevent further damage and loss of water.
- Inconsistent Pressure: If your pump system is experiencing inconsistent water pressure, it could be a sign of a failing impeller. Variations in pressure can occur due to imbalanced or damaged blades, leading to irregular flow rates and pressure output. This can result in inadequate water supply for various applications.
It is important to note that these signs can also be indicative of other pump system issues. Therefore, it is advisable to consult with a professional or experienced technician who can diagnose the specific cause and recommend appropriate solutions based on the observed symptoms.
Regular maintenance and inspection of the water pump impeller can help detect potential issues before they escalate into major problems. By addressing any signs of a failing impeller promptly, you can ensure the smooth and efficient operation of your pump system while minimizing the risk of damage and costly repairs.
Tips for Maintaining and Replacing a Water Pump Impeller
Maintaining and replacing a water pump impeller is essential for the optimal performance and longevity of the pump system. By following these tips, you can ensure that your water pump impeller stays in good condition and functions efficiently:
- Regular Inspection: Conduct regular visual inspections of the impeller, including the blades, hub, and shaft. Look for signs of damage, erosion, corrosion, or wear and tear. Address any issues promptly to prevent further damage and maintain the impeller’s functionality.
- Cleaning: Periodically clean the impeller to remove any debris, sediment, or buildup on the blades. Use a soft brush or a gentle stream of water to remove the particles. Be careful not to damage the blades in the process.
- Balancing: Ensure that the impeller is properly balanced to minimize vibrations and stress on the pump system. If you notice excessive vibrations during operation, consult a professional technician to balance the impeller if necessary.
- Fluid Quality: Use clean and filtered water or fluid in the pump system to reduce the risk of sediment, scale, or abrasive particles that can damage the impeller. Regularly check the fluid quality and ensure proper filtration to protect the impeller from contaminants.
- Replace Damaged Blades: If the impeller blades are damaged, worn out, or bent, replace them promptly. Damaged blades can adversely affect the impeller’s efficiency and performance. Consult the manufacturer’s guidelines or seek professional assistance for proper blade replacement.
- Seal Inspection and Replacement: Inspect the seals around the impeller housing for any signs of leakage or wear. Replace worn-out or damaged seals to prevent fluid leakage and ensure the proper functioning of the impeller.
- Professional Maintenance: At regular intervals, have a professional technician inspect and service the pump system, including the impeller. They can perform more detailed inspections, clean hard-to-reach areas, and conduct necessary repairs or replacements to keep the impeller in optimal condition.
- Consider Manufacturer Guidelines: Follow the manufacturer’s guidelines and recommendations for maintenance, cleaning, and replacement of the impeller. These guidelines provide specific instructions tailored to the type of impeller and pump system, ensuring the best possible maintenance practices.
Remember, proper maintenance and timely replacement of a water pump impeller can prevent costly repairs, maintain pump performance, and prolong the life of your pump system. When in doubt, consult with a professional technician who can provide expert advice and assistance for maintaining or replacing the impeller.
Read more: What Does The Water Pump Do In An Rv
Conclusion
The water pump impeller plays a vital role in the efficient functioning of a pump system. Its ability to generate fluid flow and pressure enables the transportation of water and other fluids in various applications, ranging from residential plumbing to industrial processes.
Understanding the components, function, and types of water pump impellers is crucial for anyone involved in maintaining or operating pump systems. Regular maintenance and inspection of the impeller, along with timely replacements when necessary, are essential to prevent issues such as reduced performance, clogging, and system failures.
By maintaining the impeller, you can optimize pump performance, extend the impeller’s lifespan, and ensure energy efficiency. Regular cleaning, balancing, and inspection can help identify potential issues and address them before they escalate into major problems.
Remember to follow manufacturer guidelines and seek professional assistance when needed. A qualified technician can provide expert advice, guarantee proper maintenance practices, and ensure the longevity and functionality of your pump system.
In conclusion, by understanding the importance of a water pump impeller and implementing proper maintenance and replacement practices, you can maximize the efficiency and reliability of your pump system, allowing for smooth fluid circulation and optimal performance.
Frequently Asked Questions about What Does A Water Pump Impeller Do
Was this page helpful?
At Storables.com, we guarantee accurate and reliable information. Our content, validated by Expert Board Contributors, is crafted following stringent Editorial Policies. We're committed to providing you with well-researched, expert-backed insights for all your informational needs.
0 thoughts on “What Does A Water Pump Impeller Do”