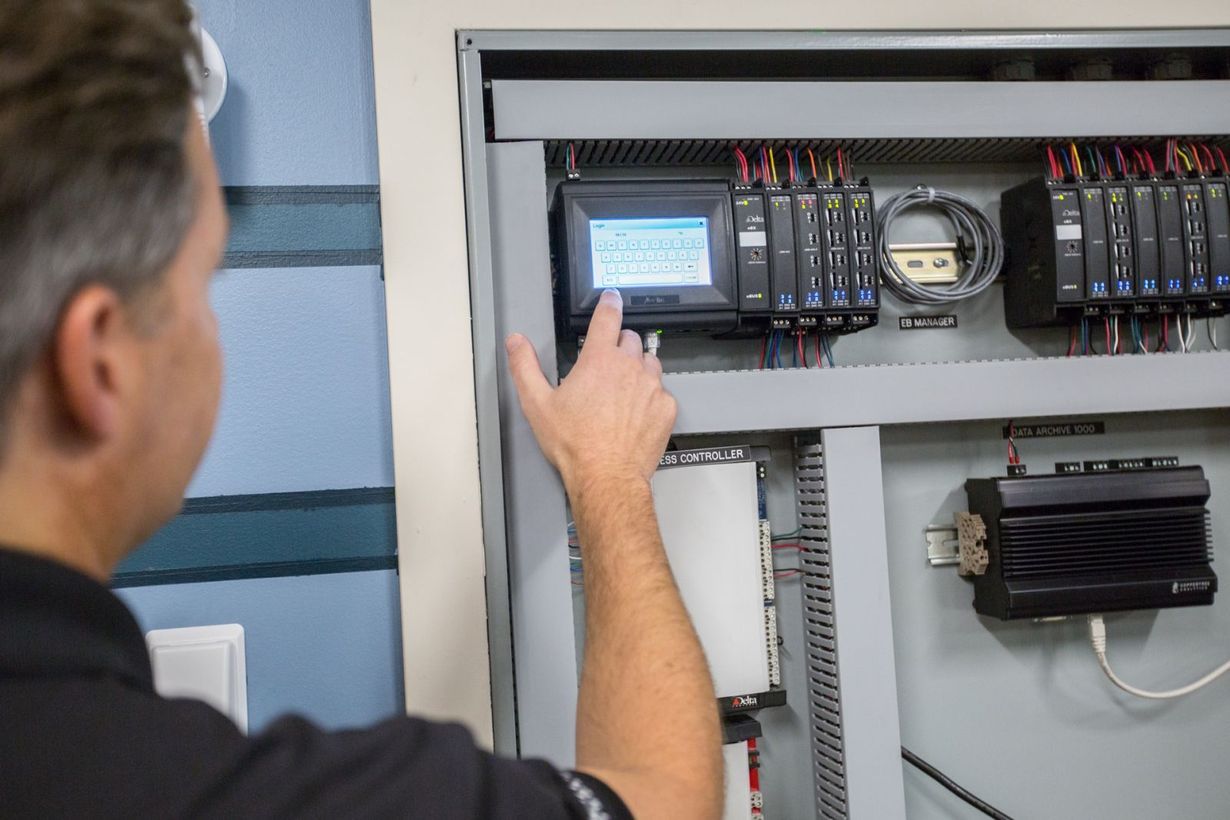
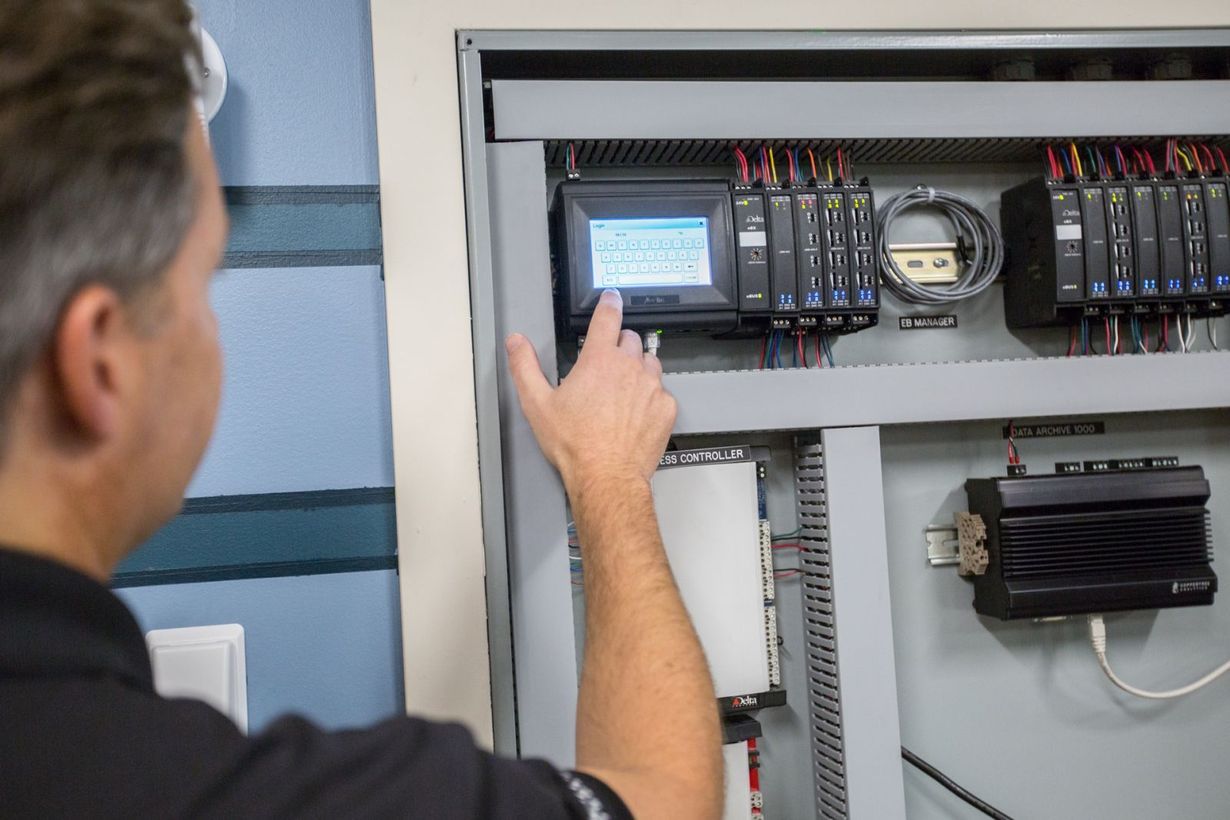
Articles
What Does DDC Stand For In HVAC
Modified: December 7, 2023
Discover what DDC stands for in HVAC with informative articles that explain the benefits and applications of this technology.
(Many of the links in this article redirect to a specific reviewed product. Your purchase of these products through affiliate links helps to generate commission for Storables.com, at no extra cost. Learn more)
Introduction
As technology continues to advance, the field of HVAC (Heating, Ventilation, and Air Conditioning) systems has also evolved. One of the significant advancements in HVAC technology is the implementation of DDC, which stands for Direct Digital Control or sometimes referred to as Direct Digital Communication. DDC not only revolutionizes how HVAC systems are controlled and monitored but also offers numerous benefits in terms of energy efficiency, automation, and ease of operation.
DDC refers to a method of controlling and managing various components and functions of an HVAC system using digital signals. In traditional HVAC systems, control operations were carried out using analog devices and mechanical controls. However, with the introduction of DDC, these analog controls have been replaced by digital devices, enabling more accurate and precise control over HVAC systems.
In this article, we will take a closer look at what DDC stands for in HVAC systems, explore its benefits, understand its components, compare it to traditional controls, and delve into some common DDC terminologies.
Key Takeaways:
- DDC (Direct Digital Control) technology revolutionizes HVAC systems, offering precise control, energy efficiency, and remote accessibility. It replaces analog controls with digital devices, optimizing performance and comfort.
- Understanding DDC terminology is essential for navigating the world of HVAC systems. DDC offers flexibility, integration, and customization, enabling efficient control and energy savings.
Read more: What Does HVAC Do?
Definition of DDC
DDC, or Direct Digital Control, is a method of HVAC system control that involves the use of digital devices and algorithms to regulate and monitor various components and functions. Instead of relying on analog devices and mechanical controls, DDC systems utilize computers, sensors, and software to manage the operations of HVAC systems.
The core principle behind DDC is to convert analog signals from various sensors and devices into digital signals, which can be easily processed, analyzed, and controlled by computer systems. These digital signals provide precise and accurate information about temperature, humidity, pressure, and other parameters, allowing the DDC system to make intelligent decisions and adjustments in real-time.
DDC is not limited to just temperature control but encompasses a wide range of HVAC functions, including air distribution, ventilation, humidity control, and energy management. It offers a more comprehensive and integrated approach to HVAC system control, enabling better optimization of energy consumption, improved comfort levels, and enhanced system performance.
Moreover, DDC systems provide a higher level of automation and customization compared to traditional HVAC controls. With the ability to program and configure various parameters, set schedules, and create sequences of operation, DDC systems allow for more efficient and tailored control strategies. This flexibility not only improves energy efficiency but also simplifies the operation and maintenance of HVAC systems.
In summary, DDC is a digital control method that replaces analog controls in HVAC systems. It utilizes computers, sensors, and software to convert analog signals into digital signals, enabling precise control and monitoring of various HVAC components and functions in real-time.
DDC in HVAC Systems
DDC technology has transformed the way HVAC systems are controlled, providing advanced features and capabilities that enhance energy efficiency, comfort, and control. In HVAC systems, DDC is used to regulate and manage various components such as air handlers, chillers, boilers, pumps, fans, and dampers.
One of the key advantages of DDC in HVAC systems is its ability to provide precise and accurate control. Analog controls often suffer from inaccuracies and limited control range, leading to suboptimal performance and energy waste. With DDC, digital sensors and actuators can precisely measure and adjust parameters such as temperature, humidity, airflow, and pressure, ensuring that the HVAC system operates at the desired setpoints.
Another significant benefit of DDC in HVAC systems is improved energy efficiency. DDC systems can intelligently optimize energy consumption by adjusting setpoints, scheduling equipment operation based on occupancy and demand, and implementing control strategies that minimize waste and unnecessary operation. By continuously monitoring and analyzing the system performance, DDC systems can identify energy-saving opportunities and implement proactive measures to reduce energy usage.
Furthermore, DDC technology enables better integration and communication among different HVAC components. Traditional HVAC systems often operate in isolation, with limited coordination between various components. DDC systems allow for seamless communication and coordination between equipment, ensuring that all components work together efficiently. This integration facilitates better system performance, increased reliability, and reduced maintenance requirements.
DDC also offers remote monitoring and control capabilities, allowing facility managers and technicians to access and control the HVAC system from anywhere. This remote accessibility enables quick troubleshooting, monitoring of equipment status, and adjustment of settings without the need for physical presence. Remote monitoring and control save time and resources, and permit prompt responses to issues or changes in the system.
Overall, DDC technology plays a crucial role in optimizing the performance, energy efficiency, and control of HVAC systems. It enables precise and accurate control, improves energy efficiency, facilitates integration between components, and provides remote monitoring and control capabilities.
Benefits of DDC in HVAC
Implementing DDC in HVAC systems offers a wide range of benefits, making it a preferred choice for many buildings and facilities. Here are some of the key advantages of using DDC technology:
- Energy Efficiency: DDC systems are designed to optimize energy consumption by implementing efficient control strategies. They can adjust setpoints, schedules, and operation modes based on occupancy, demand, and weather conditions, leading to significant energy savings. DDC also enables continuous monitoring and analysis of energy usage, allowing for proactive measures to reduce waste and improve efficiency.
- Improved Comfort: DDC systems provide precise control over temperature, humidity, airflow, and other parameters, ensuring optimal comfort conditions. By accurately maintaining desired setpoints, DDC minimizes temperature fluctuations and eliminates discomfort, enhancing occupant satisfaction and productivity.
- Flexibility and Customization: DDC technology allows for easy programming and configuration of control parameters, schedules, and sequences of operation. This flexibility enables tailored control strategies for different zones or areas within a building, accommodating specific occupancy needs or preferences. Customization also simplifies troubleshooting and adaptation to changes in building usage or requirements.
- Integration and Scalability: DDC systems facilitate seamless integration and communication among various HVAC components, including air handlers, boilers, chillers, and dampers. They can easily connect with building management systems (BMS) and other control systems, enabling comprehensive monitoring and control. DDC systems are also scalable, allowing for the expansion or modification of HVAC systems without significant reconfiguration or hardware changes.
- Remote Monitoring and Control: With DDC, facility managers and technicians can remotely monitor and control the HVAC system, eliminating the need for physical presence. Remote access allows for quick response to issues, adjustment of settings, and proactive maintenance. This feature saves time, reduces costs, and enhances efficiency in managing HVAC systems.
- Enhanced System Performance: DDC technology ensures optimized system performance by continuously monitoring and analyzing various parameters. It can detect anomalies, equipment malfunctions, and performance inefficiencies, triggering alerts or automatically initiating corrective actions. This proactive approach improves reliability, reduces downtime, and extends the lifespan of HVAC equipment.
Overall, DDC technology offers significant benefits in terms of energy efficiency, improved comfort, flexibility, integration, remote accessibility, and enhanced system performance. By utilizing DDC in HVAC systems, building owners and facility managers can achieve optimal control, energy savings, and a comfortable indoor environment.
DDC stands for Direct Digital Control in HVAC systems. It refers to the use of digital technology to control and monitor the operation of heating, ventilation, and air conditioning systems. DDC systems offer improved efficiency and precision in managing building climate control.
Components of DDC System
A DDC system consists of various components that work together to control and monitor the different aspects of an HVAC system. These components include:
- Controllers: The controllers are the heart of the DDC system. They are responsible for processing and executing commands, receiving sensor data, and controlling the operation of HVAC components. The controllers can range from small, localized devices to larger central controllers that manage multiple zones or entire buildings.
- Sensors: Sensors play a crucial role in a DDC system by measuring various parameters such as temperature, humidity, airflow, pressure, and occupancy. These sensors provide the necessary input data to the controllers, enabling them to make informed decisions and adjustments. Common sensors used in DDC systems include temperature sensors, pressure sensors, humidity sensors, and occupancy sensors.
- Actuators: Actuators are devices used to control the operation of HVAC components based on commands from the controllers. They can include motorized dampers, valves, relays, and variable frequency drives (VFDs). Actuators receive signals from the controllers and adjust the position, speed, or flow of the HVAC components to achieve the desired control parameters.
- Communication Networks: DDC systems rely on communication networks to transmit data and commands between the controllers, sensors, and actuators. These networks can be wired or wireless, depending on the specific requirements and layout of the HVAC system. Common communication protocols used in DDC systems include BACnet, Modbus, LonWorks, and Ethernet.
- User Interfaces: User interfaces provide a means for users to interact with the DDC system. They can include graphical interfaces on computer screens, mobile apps, or dedicated control panels. User interfaces allow users to monitor system status, adjust setpoints, view historical data, and receive alerts or notifications.
- Software and Programming: DDC systems rely on software and programming to control and manage the operation of the HVAC system. This includes configuring control strategies, setting schedules, creating sequences of operation, and implementing energy-saving algorithms. Programming can be done using specialized software platforms and programming languages designed for DDC systems.
- Integration with Building Management Systems: DDC systems often integrate with building management systems (BMS) to provide a comprehensive control and monitoring solution. The BMS may include additional features such as energy management, data logging, reporting, and integration with other building systems like lighting or security.
These components work together synergistically to enable precise control, monitoring, and optimization of HVAC systems. Each component plays a critical role in ensuring the efficient and effective operation of the DDC system and the associated HVAC equipment.
Read more: What Does Television Stand For
DDC vs. Traditional HVAC Controls
DDC (Direct Digital Control) systems have revolutionized the field of HVAC controls, offering numerous advantages over traditional analog controls. Here are some key differences between DDC and traditional HVAC controls:
- Precision and Accuracy: DDC systems provide precise and accurate control over HVAC parameters such as temperature, humidity, airflow, and pressure. Analog controls, on the other hand, are more susceptible to inaccuracies, limited control range, and fluctuations. DDC systems utilize digital sensors and actuators, ensuring precise control and eliminating temperature swings and comfort issues.
- Flexibility and Customization: DDC systems offer a high level of flexibility and customization. With DDC, control strategies can be easily programmed and configured to meet specific needs and requirements. This allows for tailored control of different zones or areas within a building, optimizing comfort and energy efficiency. Traditional controls often lack the flexibility and customization options available in DDC systems.
- Energy Efficiency: DDC systems are designed to maximize energy efficiency by implementing advanced control algorithms and optimization strategies. They continuously monitor and adjust HVAC operations based on occupancy, demand, and weather conditions, minimizing energy waste. Traditional controls typically lack the sophisticated algorithms and optimization capabilities of DDC systems, leading to higher energy consumption.
- Integration and Communication: DDC systems facilitate seamless integration and communication among various HVAC components and systems. They can easily connect with building management systems (BMS), allowing for comprehensive monitoring and control. Traditional controls often operate independently and lack the integration capabilities of DDC systems.
- Remote Accessibility: DDC systems offer remote monitoring and control capabilities, allowing facility managers and technicians to access and manage the HVAC system from anywhere. This remote accessibility eliminates the need for physical presence, saves time, and enables quick troubleshooting and adjustment of settings. Traditional controls require on-site access for monitoring and adjustment.
- System Performance and Maintenance: DDC systems continuously monitor and analyze HVAC system performance, allowing for proactive maintenance and optimization. They can detect anomalies, equipment malfunctions, and performance inefficiencies, triggering alerts or automatically initiating corrective actions. Traditional controls often rely on reactive maintenance and lack the proactive monitoring and analysis capabilities of DDC systems.
In summary, DDC systems offer superior precision, customization, and energy efficiency compared to traditional HVAC controls. They facilitate seamless integration, provide remote accessibility, and enhance system performance and maintenance. By utilizing DDC technology, buildings can achieve optimal control, energy savings, and improved comfort for occupants.
Understanding DDC Terminology
When diving into the world of DDC (Direct Digital Control) systems, it’s essential to understand the terminology associated with this technology. Here are some common terms used in DDC systems:
- Controller: The controller is the central device that manages and controls various HVAC components. It receives input from sensors, analyzes the data, and sends commands to actuators to adjust the operation of the system.
- Sensor: Sensors measure different parameters such as temperature, humidity, pressure, and occupancy. They provide input data to the controller, allowing it to make informed control decisions.
- Actuator: An actuator is a device that receives commands from the controller and adjusts the operation of HVAC components accordingly. Examples include motorized dampers, valves, relays, and variable frequency drives (VFDs).
- Setpoint: A setpoint is the desired value or range for a specific parameter such as temperature or humidity. The controller adjusts the system’s operation to maintain the measured value close to the setpoint.
- Control Mode: The control mode determines the method used by the controller to control the HVAC system. Common control modes include proportional control, integral control, and derivative control. These control modes ensure precise and efficient control over the system.
- Sequences of Operation: A sequence of operation refers to a predefined set of steps or actions that dictate the operation of the HVAC system. These sequences define how different components and systems should operate in response to different scenarios or conditions.
- Feedback Control: Feedback control is a control mechanism that relies on sensors to measure the system’s performance and provide feedback to the controller. The controller adjusts the operation based on the feedback received, ensuring the system meets the desired setpoints and achieves optimal performance.
- Demand Control: Demand control involves adjusting the operation of the HVAC system based on the actual demand or occupancy. By monitoring occupancy levels or environmental conditions, the DDC system can dynamically adjust settings to optimize energy usage without sacrificing comfort.
- Override: An override allows manual control over specific settings or operations of the HVAC system. Overrides are typically temporary and can be used to adjust settings or override certain control strategies for special circumstances.
- Trending: Trending refers to the process of collecting and analyzing historical data from sensors and system operations. By analyzing trends over time, facility managers can identify patterns, detect anomalies, and make informed decisions to optimize performance and energy usage.
Understanding these key terms will help you navigate the world of DDC systems and communicate effectively with professionals in the field. By grasping the terminology, you can better understand the functionalities and capabilities of DDC systems and make informed decisions regarding their implementation and operation.
Conclusion
DDC (Direct Digital Control) technology has revolutionized the field of HVAC systems, providing advanced features and capabilities that enhance control, energy efficiency, and comfort. With DDC, analog controls have been replaced by digital devices, enabling precise and accurate control over various HVAC components and functions.
In this article, we explored what DDC stands for in HVAC systems and its significance. We discussed the benefits of using DDC in HVAC, including improved energy efficiency, enhanced comfort, flexibility, integration, and remote accessibility. DDC systems offer a higher level of precision, customization, and automation compared to traditional analog controls. They optimize energy consumption, provide tailored control strategies, and facilitate seamless communication among different components.
We also delved into the components of a DDC system, including controllers, sensors, actuators, communication networks, user interfaces, software, and integration with building management systems. Each component plays a crucial role in enabling the precise control, monitoring, and optimization of HVAC systems.
Furthermore, we discussed some common DDC terminologies, such as setpoint, control mode, sequences of operation, and trending. Understanding these terms is essential for effectively navigating and communicating in the realm of DDC systems.
In conclusion, DDC technology offers numerous advantages in HVAC systems, ranging from energy savings to improved comfort and system performance. By embracing DDC, building owners and facility managers can optimize their HVAC systems, reduce energy consumption, and create a comfortable and efficient indoor environment.
Frequently Asked Questions about What Does DDC Stand For In HVAC
Was this page helpful?
At Storables.com, we guarantee accurate and reliable information. Our content, validated by Expert Board Contributors, is crafted following stringent Editorial Policies. We're committed to providing you with well-researched, expert-backed insights for all your informational needs.
0 thoughts on “What Does DDC Stand For In HVAC”