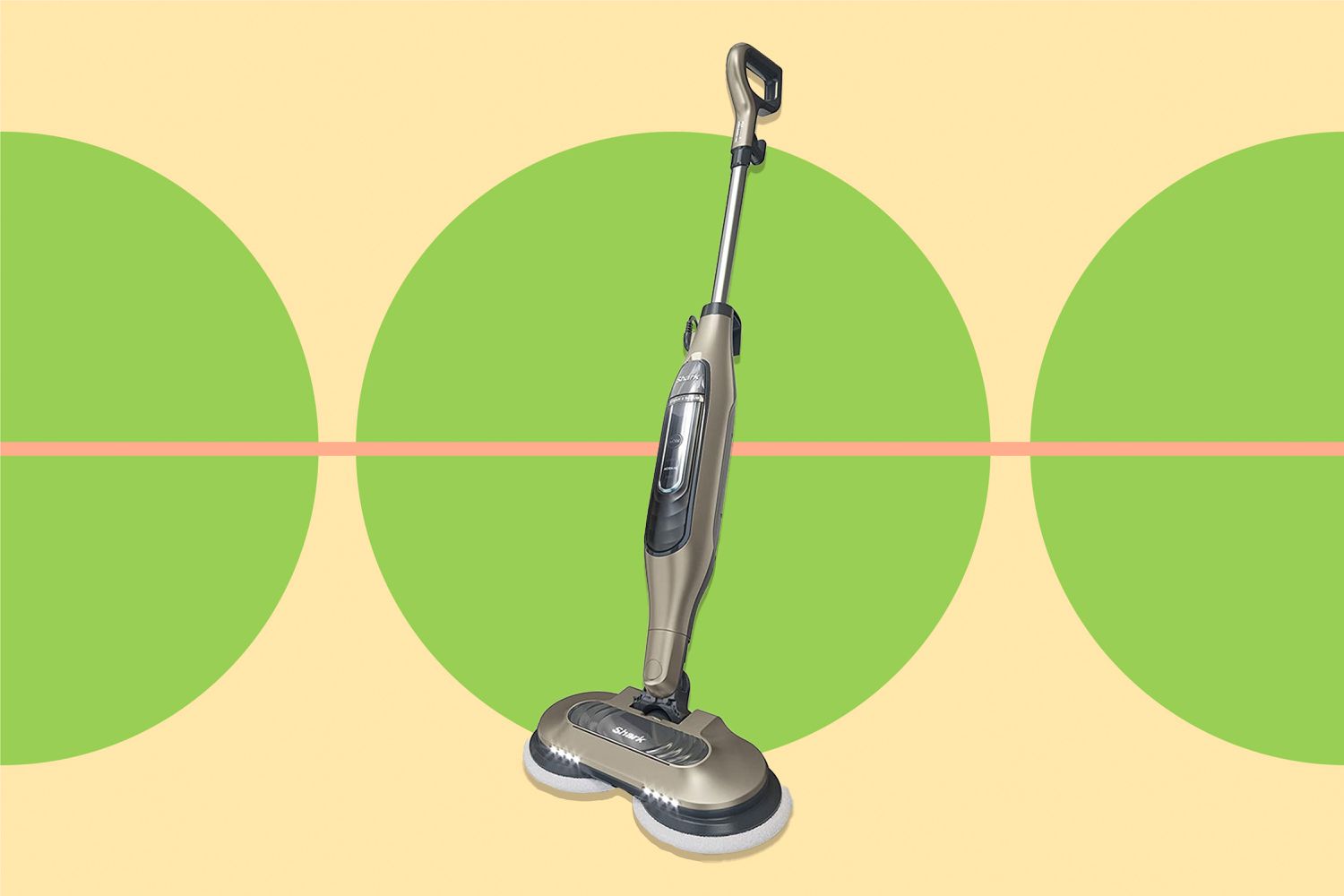
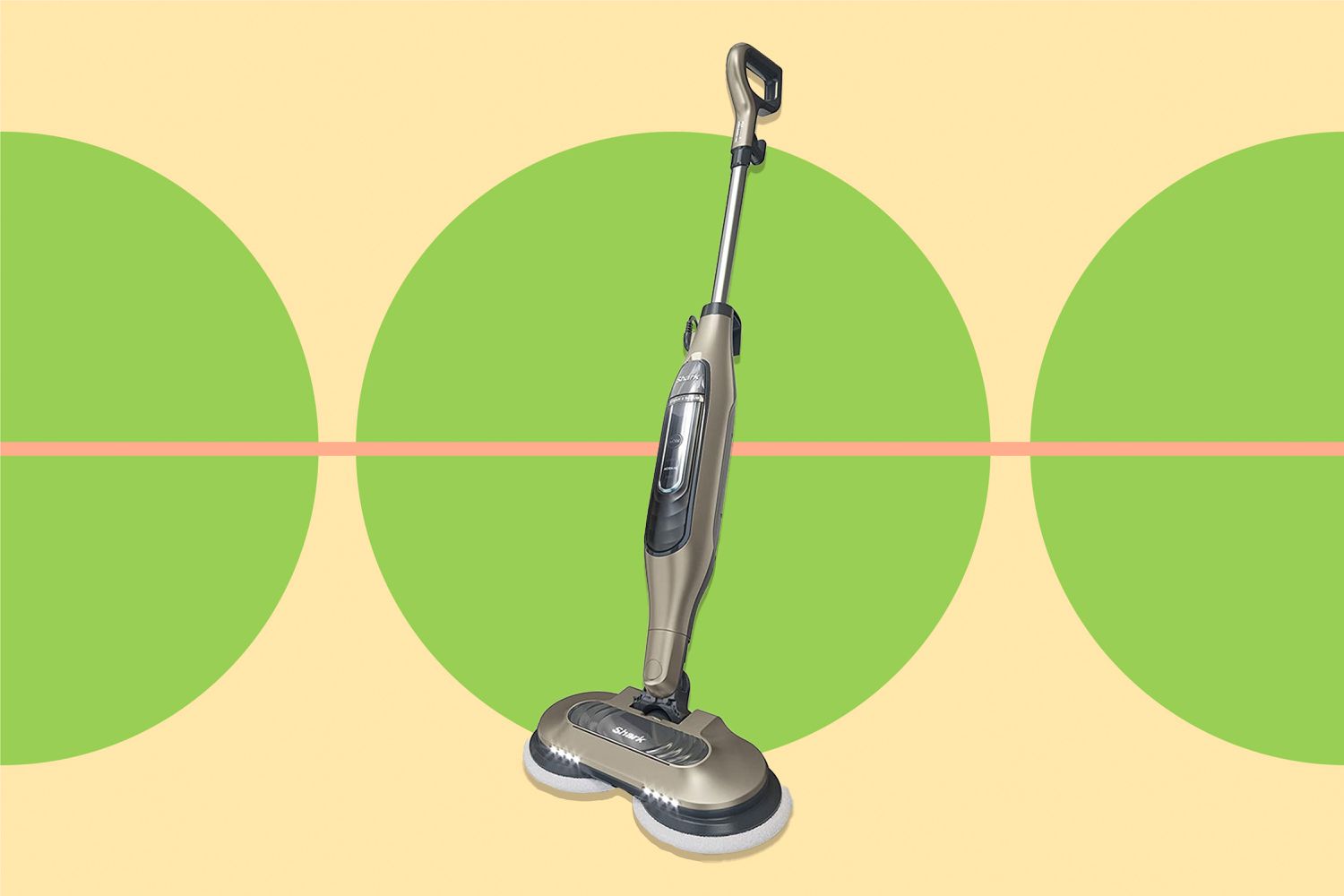
Articles
Why Is My Shark Steamer Not Steaming
Modified: September 2, 2024
Discover why your Shark steamer is not steaming and find helpful articles to troubleshoot and fix the issue.
(Many of the links in this article redirect to a specific reviewed product. Your purchase of these products through affiliate links helps to generate commission for Storables.com, at no extra cost. Learn more)
Introduction
Having a Shark steamer can be a convenient and effective way to clean and sanitize various surfaces in your home. From floors to upholstery, the powerful steam produced by these devices can tackle tough dirt and grime with ease. However, there may be instances where you encounter a problem with your Shark steamer not steaming, leaving you frustrated and wondering what could be causing the issue.
There are several possible reasons why your Shark steamer may not be producing steam as expected. It could be due to issues with the water tank, a clogged nozzle or hose, a malfunctioning heating element, electrical connection problems, activation of the overheating safety feature, or the accumulation of mineral build-up or hard water deposits.
In this article, we will explore these potential causes in detail and provide troubleshooting steps to help you fix a Shark steamer that’s not steaming. By understanding the underlying issues and following the appropriate solutions, you can get your Shark steamer back to its reliable steaming performance and enjoy the benefits of a clean and sanitized home.
Key Takeaways:
- Keep your Shark steamer in top condition by regularly checking the water tank, clearing clogs, and using distilled water to prevent mineral build-up. Proper maintenance ensures consistent steam production for effective cleaning.
- Troubleshoot issues like heating element malfunction, electrical connection problems, and overheating safety feature activation to restore your Shark steamer’s steaming performance. Regular descaling and thorough cleaning are key to preventing future problems.
Read more: Why Is My Conair Steamer Not Steaming
Possible Reasons for Shark Steamer Not Steaming
When your Shark steamer fails to produce steam, it can be frustrating and hinder your cleaning efforts. Understanding the possible reasons behind this issue can help you identify and resolve the problem quickly. Here are some common causes for a Shark steamer not steaming:
- Water Tank Issues: One of the primary reasons for a Shark steamer not steaming is inadequate water in the tank. Ensure that the water tank is filled to the recommended level, as insufficient water can prevent steam generation.
- Clogged Nozzle or Hose: Blockages in the nozzle or hose can obstruct the flow of steam. Debris, mineral deposits, or other particles can accumulate over time, preventing steam from escaping. Cleaning the nozzle and hose thoroughly can help restore proper steaming.
- Heating Element Malfunction: The heating element is responsible for generating the steam in your Shark steamer. If it becomes faulty or damaged, it may not heat up properly, resulting in no steam production. In such cases, the heating element may need to be replaced.
- Electrical Connection Problems: Check the power cord and ensure it is securely plugged in. Faulty electrical connections can disrupt the steamer’s functioning, leading to a lack of steam. Verify that the power source is working correctly and that there are no loose connections.
- Overheating Safety Feature Activated: To prevent damage or injury, many Shark steamers are equipped with an overheating safety feature. If the steamer becomes too hot, this feature automatically shuts off the steam production. In such cases, allow the steamer to cool down before attempting to use it again.
- Mineral Build-up or Hard Water Deposits: Over time, minerals from hard water can build up inside the steamer, clogging the internal components. This can affect the steam generation and cause your Shark steamer to stop producing steam. Regular descaling or using distilled water can help prevent mineral build-up.
Identifying the specific reason why your Shark steamer is not steaming is crucial in finding the appropriate solution. In the following section, we will provide troubleshooting steps to address each of these potential issues, helping you restore the steamer’s steaming performance and get back to your cleaning tasks.
Water Tank Issues
One of the most common reasons for a Shark steamer not steaming is related to water tank issues. It is important to ensure that the water tank is properly filled to the recommended level for optimal steam production. Here are some troubleshooting steps to address water tank issues:
- Check the Water Level: Start by checking the water level in the tank. If it is empty or below the minimum fill line, it will not generate steam. Refill the tank with clean, cold water, ensuring it reaches the appropriate level, but avoid overfilling.
- Verify Water Tank Placement: Ensure that the water tank is properly inserted into the steamer. Sometimes, the tank may not be positioned correctly, leading to steam generation problems. Make sure it is securely attached and properly aligned with the steamer.
- Clean the Water Tank: Over time, debris and mineral deposits can accumulate in the water tank, clogging the steam vents and affecting steam production. Clean the water tank thoroughly with warm soapy water and a soft brush to remove any build-up. Rinse it well and dry it before reattaching it to the steamer.
- Use Distilled Water: If you live in an area with hard water, mineral deposits can accumulate more quickly in the water tank. Using distilled water can help prevent mineral build-up and maintain the steamer’s performance over time. Avoid using tap water or water with high mineral content.
By taking these steps, you can address water tank issues that may be causing your Shark steamer not to produce steam. Checking the water level, ensuring proper tank placement, cleaning the tank regularly, and using distilled water can help maintain the functionality of your steamer and ensure consistent steam generation.
Clogged Nozzle or Hose
A clogged nozzle or hose can significantly impact the steam flow in your Shark steamer, leading to a lack of steam production. If you suspect that a blockage is causing the issue, follow the troubleshooting steps below to clear the clog and restore proper steaming:
- Inspect the Nozzle and Hose: Start by visually inspecting the nozzle and hose for any visible blockages or debris. Look for any signs of dirt, mineral deposits, or other particles that could be obstructing the steam flow.
- Remove the Blockage Manually: If you can see the blockage, try using a brush, a toothpick, or a small wire to gently remove it. Be careful not to damage the nozzle or hose while doing this. Take your time to ensure that you clear the blockage thoroughly.
- Flush the Nozzle and Hose: Fill a bowl or sink with warm water and vinegar solution (equal parts water and vinegar). Submerge the nozzle and hose in the solution and let them soak for about 30 minutes. This will help dissolve any stubborn blockages or mineral deposits.
- Rinse and Dry: After soaking, rinse the nozzle and hose with clean water to remove any vinegar solution. Shake out any excess water and allow them to air dry completely before reattaching them to the steamer.
By following these steps, you can effectively clear any clogs in the nozzle or hose of your Shark steamer. Removing debris, mineral deposits, or other obstructions will restore proper steam flow and resolve the issue of your steamer not steaming. Regular maintenance and cleaning of the nozzle and hose can help prevent clogs from occurring in the future.
Heating Element Malfunction
The heating element in your Shark steamer is responsible for generating the necessary heat to produce steam. If the heating element malfunctions, it can result in a lack of steam production. If you suspect a problem with the heating element, follow these troubleshooting steps to address the issue:
- Check Power Supply: Ensure that your Shark steamer is plugged into a functioning power outlet. Sometimes, a loose connection or a tripped circuit breaker can disrupt the power supply to the heating element, preventing it from heating up. Verify that the power source is working correctly.
- Allow Sufficient Preheating Time: Give your Shark steamer enough time to heat up. Depending on the model, it may require several minutes to reach the optimal temperature for steam production. Refer to the user manual to determine the recommended preheating time for your specific steamer.
- Inspect for Visible Damage: Carefully examine the heating element for any visible signs of damage or wear. Look for burnt wires, frayed connections, or discolored areas. If you notice any abnormalities, it is best to contact the manufacturer or a professional for repair or replacement.
- Verify Warranty Status: If your Shark steamer is still under warranty and you suspect a heating element malfunction, reach out to the manufacturer for assistance. They may be able to provide guidance on troubleshooting or arrange for a repair or replacement if necessary.
If you have tried these troubleshooting steps and continue to experience a heating element malfunction, it is advisable to seek professional assistance. A qualified technician will have the expertise to diagnose the problem accurately and offer the best solution, ensuring that your Shark steamer is back to its normal functioning.
Read more: Shark’s Steam Mop Is On Sale On Amazon
Electrical Connection Problems
Electrical connection problems can hinder the performance of your Shark steamer and result in a lack of steam production. If you suspect that there may be issues with the electrical connection, follow these troubleshooting steps to address the problem:
- Check the Power Cord: Ensure that the power cord of your Shark steamer is securely plugged into a functioning power outlet. Sometimes, a loose or partially inserted plug can disrupt the electrical connection. Verify that the power cord is properly inserted and firmly connected to the outlet.
- Inspect the Power Cord for Damage: Examine the power cord for any signs of damage, such as cuts, frayed wires, or exposed insulation. If you notice any abnormalities in the power cord, it is crucial to discontinue use and contact the manufacturer for a replacement or seek the assistance of a professional to repair it.
- Use a Different Outlet: Try plugging your Shark steamer into a different power outlet to rule out the possibility of a faulty outlet. Sometimes, the power supply from certain outlets may be inadequate, resulting in a lack of steam generation. Make sure to use a properly grounded outlet.
- Check the Circuit Breaker: If the power to your Shark steamer is not turning on at all, check the circuit breaker in your electrical panel. If it has tripped, resetting it may restore power to the appliance. Locate the circuit breaker labeled for the steamer and flip it back to the “on” position.
If you have tried the above troubleshooting steps and are still experiencing electrical connection problems with your Shark steamer, it is advisable to consult a qualified electrician. They will have the expertise to identify and address any electrical issues that may be causing the lack of steam production in your steamer.
Overheating Safety Feature Activated
Many Shark steamers are equipped with an overheating safety feature to prevent damage or injury. If the steamer becomes too hot, this feature will automatically shut off the steam production. If you suspect that the overheating safety feature has been activated, follow these troubleshooting steps to address the issue:
- Allow Time for Cooling: If your Shark steamer suddenly stops producing steam during use, it may have triggered the overheating safety feature. In this case, turn off the steamer and unplug it from the power source. Allow the steamer to cool down for a sufficient amount of time. This can range from a few minutes to several hours, depending on the model and the extent of overheating.
- Check for Blockages or Obstructions: While the steamer is cooling down, inspect the nozzle, hose, and any other steam outlets for any blockages or obstructions. It’s possible that accumulated debris or mineral deposits may be causing the overheating. Clear any blockages or clean the affected areas thoroughly before using the steamer again.
- Verify the Environment: Ensure that you are using your Shark steamer in an appropriate environment. Operating the steamer in extremely high temperatures or high humidity conditions may lead to overheating. If necessary, move to a cooler and well-ventilated area to prevent future overheating issues.
- Inspect for Damage: While the steamer is cooling, take the time to visually inspect its components for any signs of damage or wear. Look for frayed cords, loose connections, or other abnormalities that may contribute to overheating. If you notice any issues, it is recommended to seek professional assistance for repair or replacement.
By following these troubleshooting steps, you can address and resolve the overheating safety feature activation in your Shark steamer. Cooling the steamer, checking for blockages or obstructions, ensuring a suitable environment, and inspecting for damage can help prevent overheating and restore normal steam production.
Mineral Build-up or Hard Water Deposits
Over time, mineral build-up and hard water deposits can accumulate in your Shark steamer, leading to decreased steam production. These deposits can clog the internal components of the steamer and hinder its overall performance. If you suspect that mineral build-up or hard water deposits are causing your steamer not to produce steam, follow these troubleshooting steps to address the issue:
- Descaling Solution: Purchase a descaling solution that is compatible with your Shark steamer. These solutions are specifically designed to dissolve mineral deposits and remove build-up. Follow the instructions provided by the manufacturer for dilution ratios and usage guidelines.
- Run the Descale Cycle: Most Shark steamers have a descale cycle or feature. Fill the water tank with the descaling solution as recommended by the manufacturer. Then, run the steamer in the descale mode, allowing the solution to circulate through the system. This process will help dissolve and flush out any mineral build-up.
- Dismantle and Soak: If the descale cycle alone does not remove all the deposits, you may need to dismantle certain parts of the steamer, such as the nozzle or hose, and soak them in the descaling solution. This will help break down stubborn deposits and restore proper steam flow.
- Rinse Thoroughly: After descaling, rinse all parts of the steamer that came into contact with the descaling solution. Use clean water to ensure that no residue is left behind. If necessary, repeat the rinsing process multiple times to ensure thorough removal of the descaling solution.
- Use Distilled or Filtered Water: To prevent future mineral build-up, consider using distilled or filtered water instead of tap water in your Shark steamer. These types of water have reduced mineral content, minimizing the chances of deposits forming inside the steamer. Check your user manual for any recommendations on water type.
By following these steps, you can effectively remove mineral build-up and hard water deposits from your Shark steamer. Descaling the steamer, running the descale cycle, soaking affected parts, and using distilled or filtered water can help prevent further clogging and restore optimal steam production. Regular descaling maintenance will prolong the lifespan of your steamer and ensure consistent performance.
Check if the water tank is filled and the unit is plugged in. Clean the nozzle and descale the steamer if needed. If the problem persists, contact customer support for further assistance.
Troubleshooting Steps to Fix a Shark Steamer Not Steaming
If you are experiencing issues with your Shark steamer not steaming, there are several troubleshooting steps you can take to address the problem. By following these steps, you can identify the underlying cause and implement the appropriate solution:
- 1. Checking the Water Tank: Ensure that the water tank is properly filled to the recommended level. If the tank is empty or insufficiently filled, it can prevent steam production. Refill the tank with clean, cold water, making sure it reaches the appropriate level.
- 2. Clearing Clogs in the Nozzle or Hose: Inspect the nozzle and hose for any blockages or debris that may be obstructing the steam flow. Clear any visible clogs using a brush, toothpick, or small wire. If necessary, soak the nozzle and hose in warm water and vinegar solution to dissolve stubborn deposits.
- 3. Verifying the Heating Element Functionality: Check the power supply and ensure that the heating element is functioning properly. Make sure the power cord is securely plugged into a functioning outlet. Allow sufficient preheating time for the steamer to reach the optimal steam-producing temperature.
- 4. Ensuring a Proper Electrical Connection: Verify that the power cord is securely connected to the power source. Check for any visible damage to the power cord, such as frayed wires or exposed insulation. Use a different outlet if necessary to rule out a faulty power source.
- 5. Resetting the Overheating Safety Feature: If your steamer suddenly stops producing steam, it may have triggered the overheating safety feature. Turn off the steamer and allow it to cool down for an appropriate amount of time. Inspect for any blockages or obstructions that may have caused the overheating.
- 6. Removing Mineral Build-up or Hard Water Deposits: If mineral deposits are causing the lack of steam production, descale your Shark steamer using a descaling solution. Run the descale cycle, soak affected parts if necessary, and thoroughly rinse all components to remove any residue.
By following these troubleshooting steps, you can identify and resolve the specific issues causing your Shark steamer not to produce steam. It is important to address each potential cause systematically to ensure an optimal solution. Regular maintenance and cleaning of your steamer will help prevent these issues from reoccurring in the future, allowing you to enjoy the full performance of your Shark steamer for years to come.
Read more: How To Clean Shark Steamer
Checking the Water Tank
One of the first troubleshooting steps when your Shark steamer is not steaming is to check the water tank. The water tank plays a crucial role in producing the steam necessary for cleaning. Here are the steps to take when checking the water tank:
- Verify Water Level: Ensure that the water tank is properly filled to the recommended level. If the tank is empty or below the minimum fill line, it will not generate steam. Refill the tank with clean, cold water, making sure it reaches the appropriate level. Avoid overfilling the tank as it can lead to water leakage during operation.
- Check Tank Placement: Verify that the water tank is inserted securely into the steamer. Sometimes, if the tank is not positioned correctly, steam production may be affected. Ensure that it is properly aligned and pushed in all the way to establish a proper connection with the steamer.
- Clean the Water Tank: Over time, debris, mineral deposits, and dirt can accumulate in the water tank, hindering steam production. Clean the water tank regularly to remove any build-up. Empty the tank and wash it with warm soapy water. Use a soft brush or cloth to scrub off any residue. Rinse the tank thoroughly to remove any soap residue and dry it completely before reattaching it to the steamer.
- Use Filtered or Distilled Water: Hard water can contribute to mineral build-up in the water tank. To prevent this, consider using filtered or distilled water in your Shark steamer. These types of water have reduced mineral content, minimizing the chances of deposits forming inside the tank. Check the user manual for any specific recommendations regarding the type of water to use.
By checking the water tank and ensuring proper water level, placement, cleanliness, and water quality, you can address any water-related issues that may be causing your Shark steamer not to steam. Regular maintenance and proper care of the water tank will help optimize steam production and maintain the performance of your steamer over time.
Clearing Clogs in the Nozzle or Hose
If your Shark steamer is not steaming, there may be a clog in the nozzle or hose that is obstructing the steam flow. Clearing these clogs is essential for proper steam production. Follow these steps to clear clogs in the nozzle or hose:
- Inspect the Nozzle and Hose: Begin by visually inspecting the nozzle and hose for any visible blockages or debris. Look for dirt, mineral deposits, or other particles that may be obstructing the steam flow. Pay close attention to the openings and small crevices where clogs are likely to form.
- Remove the Blockage Manually: If you can see the blockage, use a soft brush, toothpick, or a small wire to gently remove it. Be cautious not to damage the nozzle or hose while doing this. Take your time and ensure that you clear the blockage thoroughly. If the clog is stubborn and cannot be easily removed, proceed to the next step.
- Flush the Nozzle and Hose: Fill a bowl or sink with warm water and vinegar solution, creating a mixture of equal parts water and vinegar. Submerge the nozzle and hose in the solution and let them soak for about 30 minutes. The vinegar helps dissolve mineral deposits and loosen stubborn clogs.
- Rinse and Dry: After soaking, remove the nozzle and hose from the solution and rinse them thoroughly with clean water. Ensure that all traces of the vinegar solution and loosened debris are removed. Shake out any excess water and allow the parts to air dry completely before reattaching them to the steamer.
By clearing clogs in the nozzle or hose, you can restore proper steam flow and address the issue of your Shark steamer not steaming. Regular cleaning and maintenance of these components are important to prevent clogs from occurring in the first place. It is recommended to check and clean the nozzle and hose after each use to ensure optimal performance.
Verifying the Heating Element Functionality
If your Shark steamer is not steaming, there may be a malfunction with the heating element. The heating element is responsible for generating the heat required to produce steam. To verify its functionality, follow these steps:
- Check the Power Supply: Ensure that your Shark steamer is securely plugged into a functioning power outlet. Sometimes, a loose or partially inserted plug can disrupt the power supply to the heating element, resulting in no steam production. Verify that the power cord is properly inserted and firmly connected to the outlet.
- Allow Sufficient Preheating Time: Give your Shark steamer enough time to heat up. Depending on the model, it may require several minutes to reach the optimal temperature for steam production. Refer to the user manual for recommended preheating times specific to your steamer. Allow the steamer to heat up before attempting to use it.
- Inspect for Visible Damage: Carefully examine the heating element for any visible signs of damage or wear. Look for burnt wires, frayed connections, or discolored areas. If you notice any abnormalities, it is best to contact the manufacturer for further guidance. They may be able to provide instructions for repair or replacement if necessary.
- Verify Warranty Status: If your Shark steamer is still under warranty and you suspect a heating element malfunction, reach out to the manufacturer for assistance. They may be able to provide troubleshooting guidance or arrange for a repair or replacement if needed. Check your user manual or the manufacturer’s website for warranty information.
Verifying the functionality of the heating element is important in determining the cause of your Shark steamer not steaming. By checking the power supply, allowing sufficient preheating time, inspecting for visible damage, and verifying the warranty status, you can determine the appropriate course of action. If you suspect a heating element malfunction and the steamer is no longer under warranty, it is advisable to consult a professional for repair or replacement.
Ensuring a Proper Electrical Connection
If your Shark steamer is not steaming, it’s important to ensure that there is a proper electrical connection. Electrical connection problems can prevent the steamer from functioning effectively. To ensure a proper electrical connection, follow these steps:
- Check the Power Cord: Verify that the power cord of your Shark steamer is securely plugged into a functioning power outlet. Sometimes, a loose or partially inserted plug can disrupt the electrical connection and result in a lack of steam production. Ensure that the power cord is fully inserted and firmly connected to the outlet.
- Inspect the Power Cord for Damage: Examine the power cord for any signs of damage, such as cuts, frayed wires, or exposed insulation. If you notice any abnormalities in the power cord, it is crucial to discontinue use and contact the manufacturer’s customer service for a replacement or seek the assistance of a qualified technician to repair it. It is important to prioritize safety when dealing with electrical connections.
- Use a Different Outlet: Consider trying a different power outlet to rule out the possibility of a faulty outlet. Sometimes, the power supply from certain outlets may be inadequate, leading to a lack of steam generation. Ensure that the chosen outlet is properly grounded and functioning correctly before connecting your steamer to it.
- Check the Circuit Breaker: If the power to your Shark steamer is not turning on at all, it could be due to a tripped circuit breaker. Locate your electrical panel and check the circuit breaker labeled for the steamer. If it has tripped, flip it back to the “on” position. However, if the circuit breaker continues to trip, it may indicate a more serious electrical problem that requires professional attention.
By ensuring a proper electrical connection, you can address any potential issues that may be causing your Shark steamer not to steam. Checking the power cord, inspecting for damage, using a different outlet, and verifying the circuit breaker can help troubleshoot electrical connection problems. If you are uncertain about any electrical issues or require further assistance, it is always recommended to consult a qualified electrician or contact the manufacturer for guidance.
Read more: How To Steam My Face Without A Steamer
Resetting the Overheating Safety Feature
Many Shark steamers are equipped with a safety feature that automatically shuts off steam production when the steamer becomes too hot. If your Shark steamer stops producing steam suddenly, it is possible that this overheating safety feature has been activated. Resetting the feature can help resolve the issue. Follow these steps to reset the overheating safety feature:
- Turn off the Steamer: If you notice that your Shark steamer has stopped producing steam, immediately turn off the steamer and unplug it from the power source. This will prevent further overheating and ensure your safety during the troubleshooting process.
- Allow Sufficient Cooling Time: Allow the steamer to cool down for an appropriate amount of time. The cooling time can vary depending on the model and the level of overheating. In most cases, a few minutes to an hour should suffice. Avoid attempting to use the steamer until it has reached a safe temperature.
- Inspect for Blockages or Obstructions: While the steamer is cooling down, take the opportunity to inspect the nozzle, hose, and any other steam outlets for any blockages or obstructions. It is possible that accumulated debris or mineral deposits may have caused the overheating. Clear any blockages or clean the affected areas thoroughly with a soft brush or cloth.
- Reset the Steamer: Once the steamer has cooled down and any blockages have been cleared, plug the steamer back into a functioning power outlet. Turn on the steamer as you normally would, following the manufacturer”s instructions. In most cases, this will reset the overheating safety feature, and the steamer should start producing steam again.
By following these steps, you can reset the overheating safety feature on your Shark steamer and address the issue of it not producing steam. It is important to prioritize your safety when dealing with overheating, and allowing the steamer sufficient cooling time is crucial. If the steamer continues to experience overheating or fails to produce steam even after resetting the safety feature, it is advisable to contact the manufacturer for further assistance or consult with a professional technician.
Removing Mineral Build-up or Hard Water Deposits
Over time, mineral build-up and hard water deposits can accumulate in your Shark steamer, hindering its ability to produce steam effectively. These deposits can clog the internal components of the steamer and affect its overall performance. To address this issue and restore optimal steam production, follow these steps to remove mineral build-up and hard water deposits:
- Descaling Solution: Purchase a descaling solution that is compatible with your Shark steamer. These solutions are specifically formulated to dissolve mineral deposits and remove build-up. Follow the manufacturer’s instructions regarding the dilution ratios and usage guidelines.
- Run the Descaling Cycle: Most Shark steamers have a descaling cycle or feature. Fill the water tank with the descaling solution as recommended by the manufacturer. Start the descaling cycle and allow the solution to circulate through the system. This process helps to break down and remove accumulated mineral deposits.
- Dismantle and Soak: In some cases, the descaling cycle alone may not be sufficient to remove stubborn deposits. If necessary, dismantle certain parts of the steamer, such as the nozzle or hose, and soak them in the descaling solution. This helps to further break down the deposits and restore optimal steam flow.
- Rinse Thoroughly: After the descaling process, rinse all parts of the steamer that came into contact with the descaling solution. Use clean water to ensure that no residue is left behind. Thoroughly rinse and flush out all components to remove any remaining descaling solution and loosened mineral deposits.
- Use Distilled or Filtered Water: To prevent future mineral build-up, consider using distilled or filtered water in your Shark steamer. These types of water have reduced mineral content, minimizing the chances of deposits forming inside the steamer. Refer to the user manual for any specific recommendations regarding the type of water to use.
By following these steps to remove mineral build-up and hard water deposits, you can restore optimal steam production in your Shark steamer. Regular descaling maintenance is important to prevent the formation of deposits and maintain the performance of your steamer over time. Ensuring proper water quality and using distilled or filtered water can also help prolong the lifespan of your steamer and minimize the need for frequent descaling.
Conclusion
A Shark steamer not steaming can be a frustrating problem, but with proper troubleshooting steps, you can address and resolve the issue. By understanding the potential causes and implementing the appropriate solutions, you can restore the steaming performance of your Shark steamer.
Throughout this article, we have discussed various possible reasons why your Shark steamer may not be producing steam, including water tank issues, clogged nozzle or hose, heating element malfunction, electrical connection problems, activation of the overheating safety feature, and mineral build-up or hard water deposits.
To troubleshoot these issues, you can check the water tank for proper filling, clear any clogs in the nozzle or hose, verify the functionality of the heating element, ensure a proper electrical connection, reset the overheating safety feature, and remove mineral build-up or hard water deposits. These steps will help you identify and address the specific problem affecting your Shark steamer.
Regular maintenance and cleaning of your Shark steamer are also important to prevent future issues. Keeping the water tank clean, descaling periodically, using distilled or filtered water, and following the manufacturer’s guidelines for maintenance will help optimize the performance and longevity of your steamer.
If you have followed all the troubleshooting steps and your Shark steamer still does not steam, it may be necessary to contact the manufacturer’s customer support or consult with a professional technician for further assistance.
Remember, addressing the problem early and maintaining your Shark steamer properly will ensure that you can enjoy the benefits of efficient and effective cleaning for years to come. Happy steaming!
Frequently Asked Questions about Why Is My Shark Steamer Not Steaming
Was this page helpful?
At Storables.com, we guarantee accurate and reliable information. Our content, validated by Expert Board Contributors, is crafted following stringent Editorial Policies. We're committed to providing you with well-researched, expert-backed insights for all your informational needs.
0 thoughts on “Why Is My Shark Steamer Not Steaming”