Home>diy>Architecture & Design>What Is A Geometric Constraint In CAD
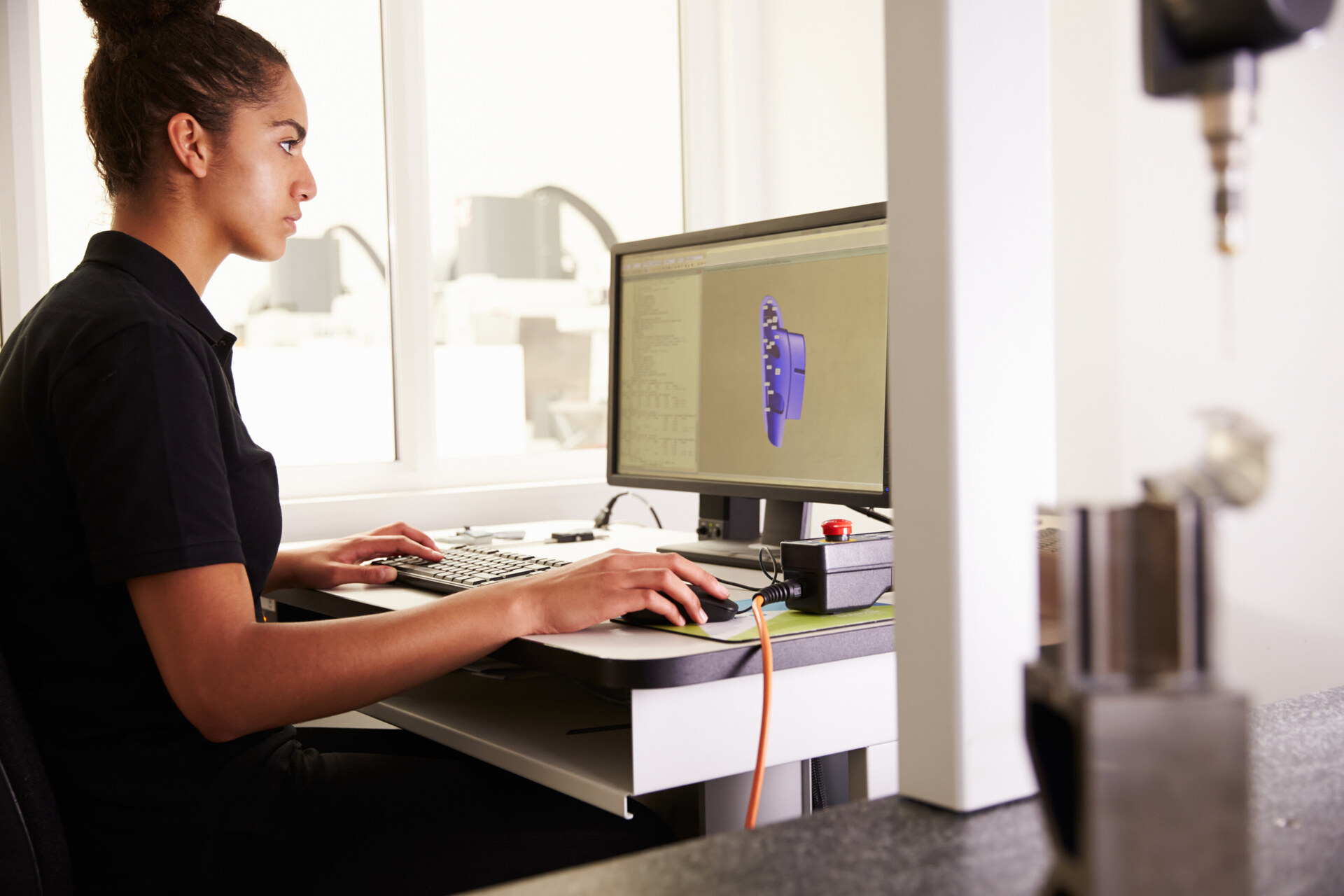
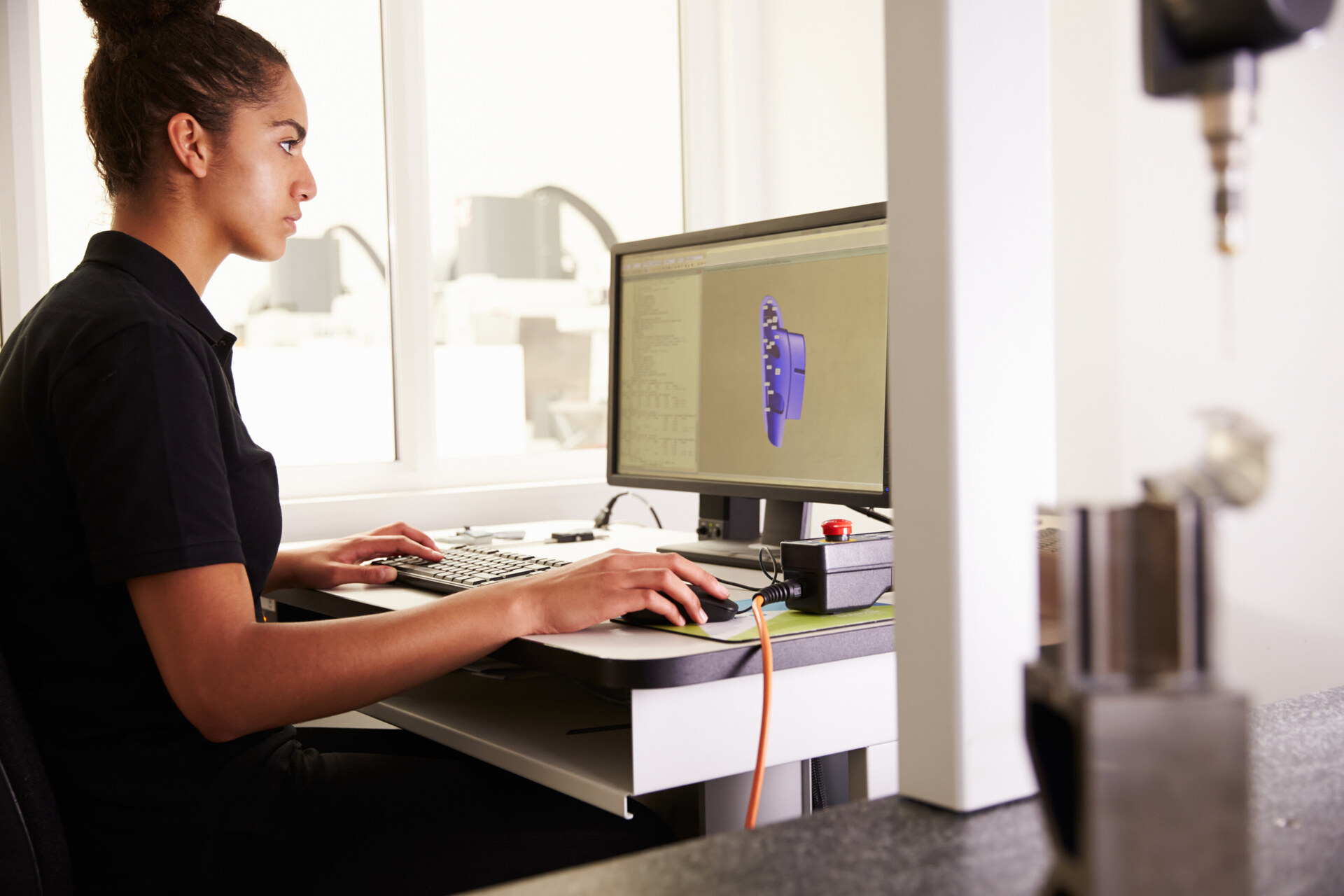
Architecture & Design
What Is A Geometric Constraint In CAD
Modified: December 7, 2023
Discover the role of geometric constraints in CAD software for architecture design. Learn how these limitations shape precision and efficiency in your projects.
(Many of the links in this article redirect to a specific reviewed product. Your purchase of these products through affiliate links helps to generate commission for Storables.com, at no extra cost. Learn more)
Introduction
Welcome to the world of Computer-Aided Design (CAD), where precision and accuracy are crucial for creating high-quality designs. In the realm of CAD, there are various tools and techniques that play a vital role in designing complex structures and models. One such technique is the use of geometric constraints.
Geometric constraints are an essential aspect of CAD software that helps engineers, architects, and designers maintain the integrity and accuracy of their designs. These constraints allow them to define relationships and rules between different elements of the design, ensuring that they adhere to specific geometric properties.
In this article, we will explore the concept of geometric constraints in CAD and examine the different types of constraints that can be applied. We will also discuss the benefits of using geometric constraints in CAD software and provide examples to illustrate their practical application.
So, whether you are a CAD beginner or a seasoned professional, read on to discover the power of geometric constraints and how they enhance the design process.
Key Takeaways:
- Geometric constraints in CAD software ensure precise and accurate designs by controlling the relationships between elements, leading to efficient design iterations and enhanced collaboration among designers, engineers, and stakeholders.
- By applying geometric constraints, designers can create symmetrical shapes, maintain parallel and perpendicular relationships, and optimize designs for specific requirements, resulting in consistent measurements, improved design integrity, and automatic updates across the entire design process.
Read more: What Is CAD?
Definition of Geometric Constraint
Geometric constraints, also known as dimensional constraints, are mathematical relationships that are imposed on geometric elements within a CAD design. These constraints dictate the relative positions, sizes, and orientations of different elements, ensuring that they adhere to specific geometric properties.
By applying geometric constraints, designers can maintain the desired shape, size, and alignment of objects in their design. These constraints act as rules or conditions that restrict the movement or modification of geometric elements, providing a framework for precise and accurate design creation.
Geometric constraints can be categorized into different types based on the properties they control. Some common types of geometric constraints include:
- Horizontal and Vertical Constraints: These constraints ensure that lines or segments remain parallel to the horizontal or vertical axis respectively. This helps in creating straight edges and maintaining alignment in the design.
- Parallel and Perpendicular Constraints: These constraints establish parallel or perpendicular relationships between lines or segments. They are commonly used in creating rectangular shapes or maintaining right angles.
- Equal and Coincident Constraints: These constraints enforce equality or coincidence between points, lines, or endpoints. They are used to create symmetrical designs or ensure alignment between different elements.
- Tangent Constraints: These constraints establish a tangent relationship between curves or circles. They are essential in creating smooth transitions between different curves or maintaining contact between objects.
- Concentric and Collinear Constraints: These constraints ensure that circles or arcs share the same center point or that lines lie along the same straight line. They are useful in creating concentric shapes or maintaining alignment between objects.
These are just a few examples of the many geometric constraints available in CAD software. Each constraint helps designers define precise relationships between geometric elements, allowing for accurate representation of their designs.
Now that we have covered the definition of geometric constraints and some common types, let’s delve into their practical application within CAD software.
Types of Geometric Constraints
Geometric constraints are an integral part of CAD software, offering a wide range of options to ensure the accuracy and integrity of designs. These constraints can be categorized into several types, each serving a specific purpose in controlling the geometry of the design. Let’s explore some of the most commonly used types of geometric constraints:
- Horizontal and Vertical Constraints: These constraints restrict the movement of lines or segments to be parallel to the horizontal or vertical axis, respectively. They ensure that objects maintain a specific orientation in relation to the coordinate system.
- Parallel and Perpendicular Constraints: Parallel constraints enforce lines or segments to remain parallel to each other, while perpendicular constraints ensure that lines form 90-degree angles. These constraints are crucial for creating accurate and aligned structures.
- Equal and Coincident Constraints: Equal constraints ensure that two or more entities have the same length, angle, or radius. Coincident constraints, on the other hand, align different points or lines so that they share the same position. These constraints are fundamental in achieving symmetrical and balanced designs.
- Tangent Constraints: Tangent constraints establish a smooth and continuous transition between curves or circles. They ensure that curves at the point of tangency have a common tangent line, eliminating any abrupt changes in curvature.
- Concentric and Collinear Constraints: Concentric constraints ensure that arcs or circles share the same center point, while collinear constraints enforce lines to lie on the same straight line. These constraints are essential for creating concentric shapes or maintaining alignment between objects.
- Distance Constraints: Distance constraints control the distance between two points, lines, or arcs. They ensure that specific measurements are maintained, allowing for precise positioning and spacing of elements in the design.
- Angle Constraints: Angle constraints define the angle between lines, segments, or arcs. They help maintain specific angular relationships between elements, such as creating triangles or polygons with predetermined angles.
- Symmetry Constraints: Symmetry constraints allow designers to mirror or reflect elements across a given axis or plane. They help achieve balance and harmony in the design by ensuring that one side mirrors the other accurately.
These are just a few examples of the many types of geometric constraints available in CAD software. The wide range of constraints available allows designers to control and manipulate the geometry of their designs with precision and accuracy.
Now that we have covered the types of geometric constraints, let’s explore how these constraints are implemented in CAD software.
Geometric Constraints in CAD Software
CAD software provides a powerful platform for designers to create and manipulate complex designs with ease. One of the key features of CAD software is the ability to apply geometric constraints to control and maintain the desired geometry of a design. Let’s take a closer look at how geometric constraints are implemented in CAD software:
Most CAD software provides an intuitive user interface that allows designers to define and apply geometric constraints to various elements of their design. These elements can include points, lines, arcs, circles, and more. By selecting specific elements and applying constraints, designers can establish relationships and rules that govern the behavior and properties of these elements.
Once a geometric constraint is applied, the CAD software automatically adjusts the position, size, or orientation of the constrained elements based on the defined rules. This real-time feedback enables designers to visualize the impact of the constraints on the design and make necessary adjustments to achieve the desired outcome.
Geometric constraints are often represented visually in CAD software through symbols or indicators that indicate the presence of a constraint. These symbols provide a quick reference for designers to identify the type of constraint applied and its impact on the design.
Furthermore, CAD software allows designers to modify or remove geometric constraints as needed. This flexibility enables iterative design processes, where designers can experiment with different configurations and constraints to arrive at the optimal design solution.
Additionally, CAD software often offers advanced features such as parametric modeling, where the relationships between elements are maintained through mathematical equations. This allows designers to make changes to one element, and the software automatically updates the related elements based on the defined constraints. This parametric approach significantly enhances productivity and streamlines the design iteration process.
Geometric constraints in CAD software play a crucial role in ensuring the accuracy, consistency, and repeatability of designs. They empower designers to create complex and intricate structures with ease, while also maintaining design integrity throughout the entire process.
With a solid understanding of how geometric constraints are implemented in CAD software, let’s explore the benefits of using these constraints in the design process.
A geometric constraint in CAD is a rule that defines the relationship between geometric elements, such as lines, arcs, and points. It helps maintain the intended shape and size of the design, ensuring accuracy and consistency throughout the drawing.
Benefits of Using Geometric Constraints in CAD
Geometric constraints are a powerful tool within CAD software that offer numerous benefits to designers and engineers. Here are some of the key advantages of using geometric constraints in CAD:
- Precision and Accuracy: Geometric constraints ensure that designs adhere to specific geometric properties, leading to precise and accurate representations. Designers can define precise relationships between elements, resulting in consistent measurements, alignments, and angles.
- Efficiency and Time-Saving: By using geometric constraints, designers can easily create and modify designs with a few simple adjustments. Constraints provide a framework for rapid design iterations, reducing the time required for manual adjustments and ensuring quicker turnaround times.
- Improved Design Integrity: Geometric constraints maintain design integrity throughout the entire design process. They prevent unintentional modifications or distortions of elements, ensuring that the design maintains its intended shape, size, and alignment.
- Easy Design Evaluation: Geometric constraints enable designers to evaluate design variations quickly and accurately. By modifying constraint parameters, designers can explore different design options and assess their impact, allowing for informed decision-making.
- Consistency and Replicability: Geometric constraints ensure consistency in designs by enforcing specific rules and relationships. This allows designers to create standardized components or structures that can be easily replicated and reused across multiple projects.
- Enhanced Collaboration: Geometric constraints provide a common language for designers, engineers, and stakeholders to communicate and collaborate effectively. With constraints in place, everyone involved in the design process can understand and interpret the design intent accurately.
- Automatic Updates: Geometric constraints in CAD software often offer parametric modeling capabilities, which automatically update related elements when changes are made. This feature eliminates the need for manual adjustments and ensures that the entire design remains consistent and up to date.
- Error Reduction: Geometric constraints help minimize errors by preventing unintended modifications or misalignments in the design. This reduces the risk of manufacturing or construction errors, resulting in cost savings and improved overall quality.
- Design Optimization: By utilizing geometric constraints, designers can optimize their designs for specific requirements and constraints. They can fine-tune the design parameters to achieve desired outcomes, such as weight reduction, structural stability, or aesthetic appeal.
Overall, the use of geometric constraints in CAD software brings numerous benefits to the design process. From improving precision and efficiency to enhancing collaboration and design optimization, geometric constraints empower designers to create high-quality, accurate, and robust designs.
Now, let’s explore some practical examples of how geometric constraints are applied in real-world CAD designs.
Read more: What Is CAD In Architecture
Examples of Geometric Constraints in CAD
Geometric constraints play a crucial role in CAD software, enabling designers to create intricate and accurate designs. Let’s look at some practical examples of how geometric constraints are applied in real-world CAD designs:
- Rectangular Shape: To create a rectangle, designers can apply parallel and perpendicular constraints to the sides. This ensures that the adjacent sides are parallel, and the opposite sides are perpendicular, resulting in a perfect rectangle.
- Circular Gear: Geometric constraints can be used to design a circular gear with teeth. By applying tangent constraints between the teeth and the base circle, designers can ensure that the teeth smoothly transition from the base circle, allowing for precise meshing with other gears.
- Symmetrical Object: Geometric constraints are helpful in creating symmetrical objects. By applying a mirror or symmetry constraint along a specific axis, designers can ensure that any modifications made to one side of the object are automatically reflected on the other side, maintaining symmetry.
- Concentric Circles: To design concentric circles, designers can apply a concentric constraint, ensuring that the centers of the circles coincide. This constraint allows for the creation of designs with nested or overlapping circular shapes.
- Parallel Lines: Geometric constraints can enforce parallel relationships between lines or segments. This is useful in creating structures such as beams or columns that need to be parallel to each other for stability and aesthetics.
- Dimensional Control: Geometric constraints help maintain specific distances between elements in a design. For example, in architectural designs, constraints can be applied to control the dimensions of doors and windows, ensuring uniformity and compliance with building codes.
- Orthogonal Connections: Geometric constraints can ensure that objects are connected orthogonally at specific points. This is commonly seen in mechanical designs, where two components need to be connected at right angles for proper functionality.
- Equal Lengths: Geometric constraints can enforce equal lengths between different elements, such as sides of a polygon or segments in a truss system. This ensures balanced and consistent designs that meet the required specifications.
These examples illustrate how geometric constraints are applied to achieve precise and accurate designs in various industries. By utilizing the different types of constraints available in CAD software, designers can ensure that their designs adhere to specific geometric properties and meet the desired criteria.
Now that we have explored the examples of geometric constraints, let’s conclude our discussion on the importance of these constraints in CAD.
Conclusion
Geometric constraints are a fundamental aspect of CAD software, empowering designers to create accurate and precise designs across various industries. By utilizing different types of constraints, designers can control the geometry of their designs and ensure adherence to specific geometric properties.
In this article, we explored the definition of geometric constraints, which are mathematical relationships imposed on geometric elements within a CAD design. We discussed the different types of constraints, including horizontal and vertical constraints, parallel and perpendicular constraints, equal and coincident constraints, tangent constraints, concentric and collinear constraints, among others.
We also delved into how geometric constraints are implemented in CAD software, providing designers with an intuitive user interface to define and apply these constraints. The software offers real-time feedback and visualization to help designers assess the impact of constraints on the design and make necessary adjustments.
The benefits of using geometric constraints in CAD are numerous. They promote precision, accuracy, and design integrity while saving time and improving efficiency. Geometric constraints also facilitate collaboration, ease design evaluation, and reduce the occurrence of errors in the design process.
Lastly, we explored practical examples of how geometric constraints are applied in real-world CAD designs. From creating rectangular shapes and symmetrical objects to ensuring parallel lines and concentric circles, the application of geometric constraints enables designers to achieve complex and accurate designs.
In conclusion, the use of geometric constraints is a powerful tool that enhances the capabilities of CAD software and empowers designers to create designs with precision, accuracy, and consistency. By leveraging these constraints, designers can unleash their creativity while maintaining design integrity and achieving optimal outcomes.
So, the next time you embark on a CAD design journey, remember the importance of geometric constraints and how they can elevate your design process to new heights of innovation and excellence.
Frequently Asked Questions about What Is A Geometric Constraint In CAD
Was this page helpful?
At Storables.com, we guarantee accurate and reliable information. Our content, validated by Expert Board Contributors, is crafted following stringent Editorial Policies. We're committed to providing you with well-researched, expert-backed insights for all your informational needs.
0 thoughts on “What Is A Geometric Constraint In CAD”