Home>diy>Building & Construction>How To Keep Construction Costs Down
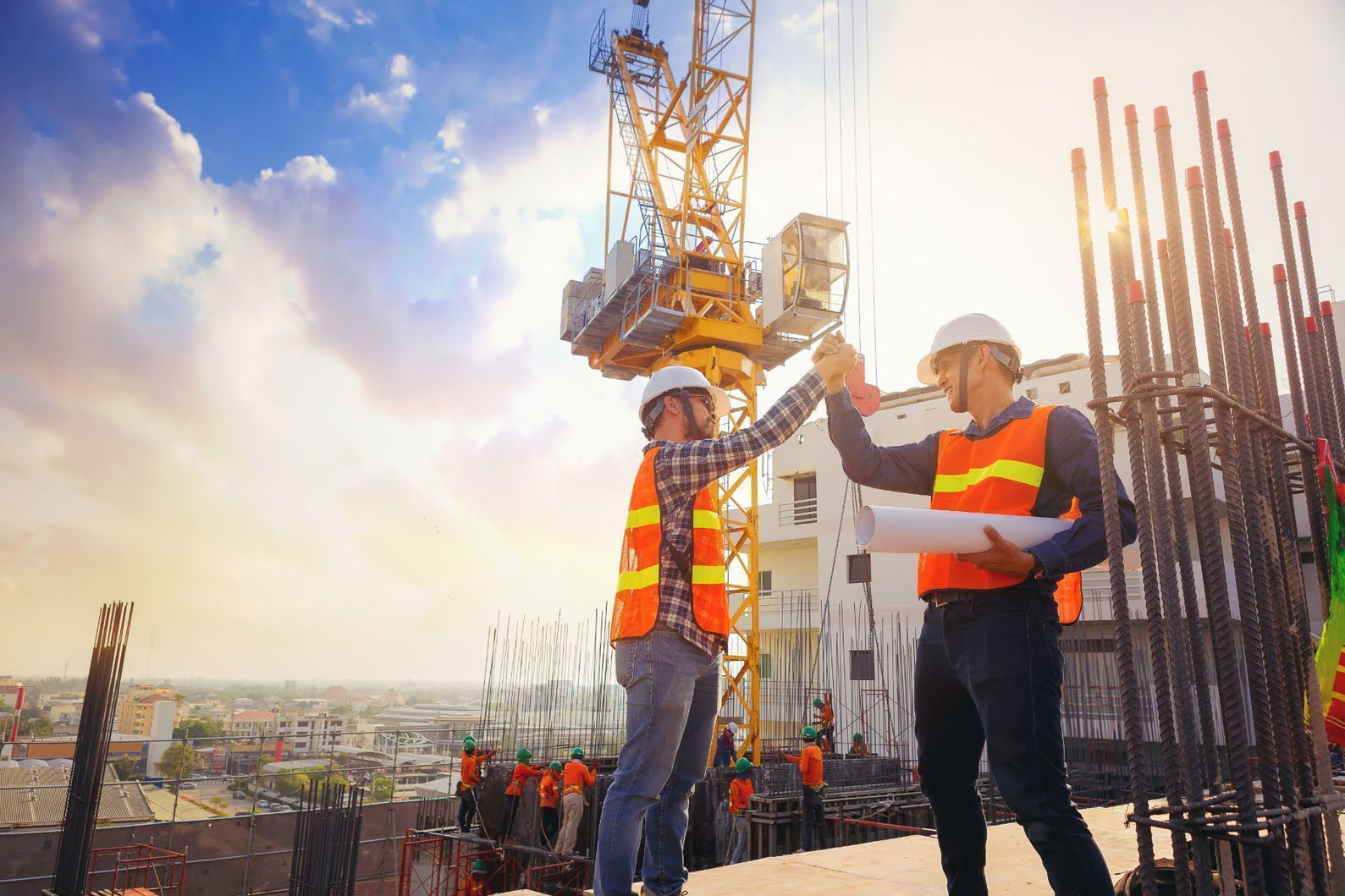
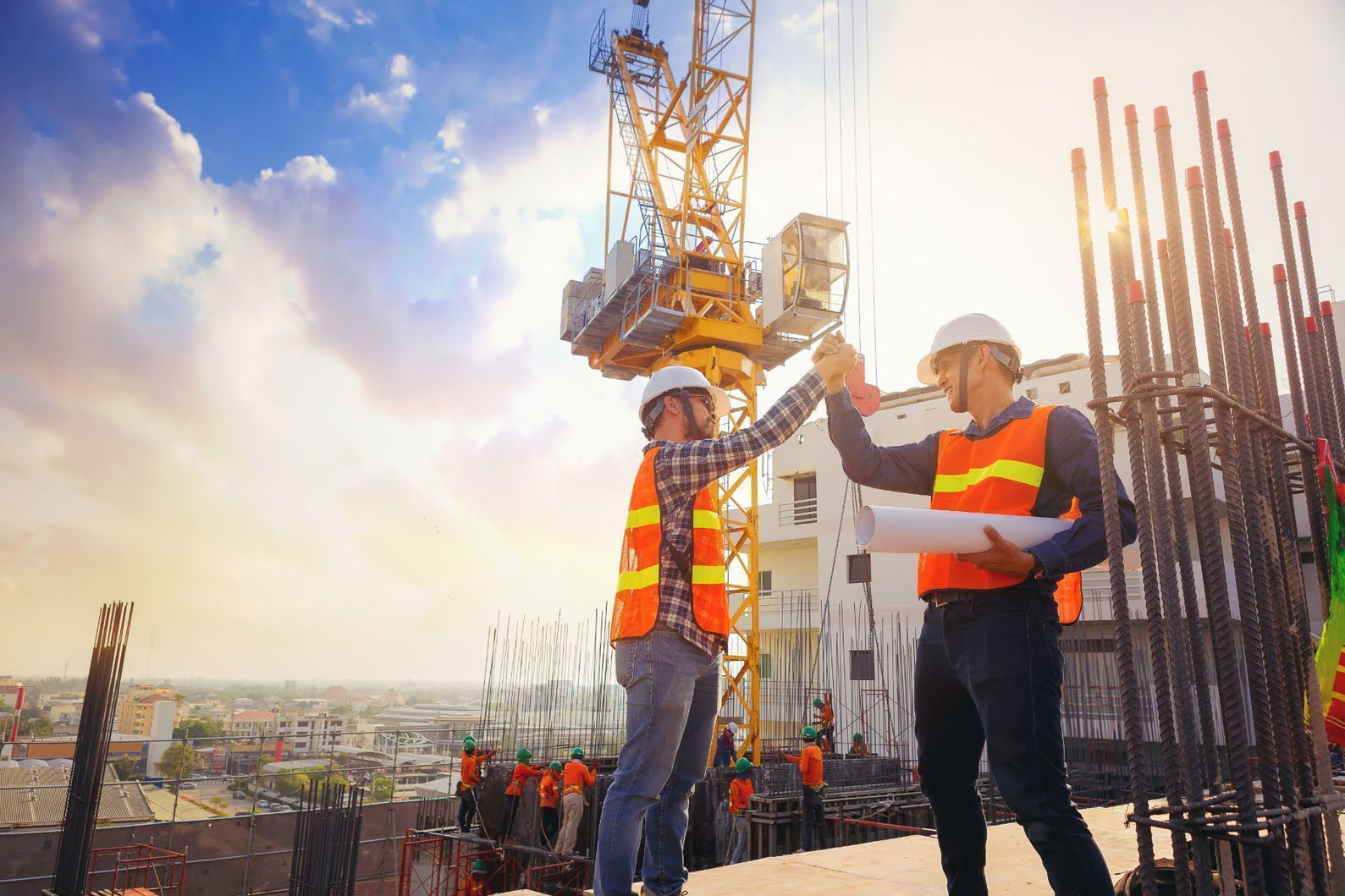
Building & Construction
How To Keep Construction Costs Down
Modified: January 6, 2024
Learn effective strategies to keep building construction costs down and maximize your budget. Discover tips, techniques, and expert advice for cost-saving in construction projects.
(Many of the links in this article redirect to a specific reviewed product. Your purchase of these products through affiliate links helps to generate commission for Storables.com, at no extra cost. Learn more)
Introduction
Construction projects can be complex and costly endeavors. From planning and design to materials, labor, and project management, there are numerous factors that contribute to the overall cost of a construction project. However, with strategic planning and proper cost-saving measures, it is possible to keep construction costs down without compromising on quality or safety.
In this article, we will explore various strategies and techniques that are essential in minimizing construction costs. By implementing these approaches, project managers and contractors can ensure that they stay within budget and deliver successful projects. So, let’s dive into the details and learn how to keep construction costs down.
Key Takeaways:
- Strategic planning and innovative approaches in construction projects can effectively minimize costs without compromising quality or safety. Key strategies include value engineering, efficient communication, and embracing technology and automation.
- Careful material selection, labor management, and proactive issue resolution contribute to cost reduction. Collaboration with contractors, regular inspections, and effective cost tracking are essential for successful cost control in construction projects.
Read more: How To Keep Home Maintenance Costs Down
Planning and Design
One of the critical aspects that can significantly impact construction costs is the planning and design phase. Proper planning and thoughtful design can help identify potential cost-saving measures early on in the project. Here are some key considerations:
- Clear Project Scope: A well-defined project scope helps in avoiding unnecessary changes and scope creep, which can lead to additional expenses. Clearly outline the project objectives, deliverables, and requirements before construction begins.
- Optimize Floor Plans: A well-designed floor plan can maximize space utilization and minimize wasted area. Consider factors such as functionality, flow, and efficiency when designing the layout. This can minimize material wastage and reduce construction time.
- Energy Efficiency: Incorporate energy-efficient designs and sustainable building practices from the start. This can include using energy-saving appliances, efficient insulation, and utilizing natural light and ventilation. Energy-efficient designs can lead to long-term cost savings by reducing utility bills.
- Value Engineering: Value engineering involves reviewing the design and identifying alternative solutions or materials that can provide the same functionality at a lower cost. Engage with architects, engineers, and contractors to explore cost-effective alternatives without compromising on quality.
By investing time and effort into proper planning and design, construction professionals can ensure that the project starts off on the right foot, setting the stage for success while keeping costs under control.
Material Selection and Procurement
Material selection and procurement play a crucial role in the overall cost and quality of a construction project. Making informed decisions in these areas can help minimize costs without compromising on the integrity of the structure. Here are some strategies to consider:
- Research and Compare: Take the time to research different materials and compare their cost, durability, and availability. Consider factors such as maintenance requirements, lifespan, and compatibility with other building components. This will help you make informed choices that meet both budgetary and quality requirements.
- Bulk Purchasing: Buying materials in bulk can often lead to significant cost savings. Work closely with suppliers and negotiate favorable pricing for large quantities of materials. Ensure that the materials are properly stored and handled to prevent any wastage or damage.
- Alternative Materials: Consider using alternative building materials that are cost-effective and readily available. For example, using recycled materials or composite materials can be an environmentally friendly and budget-friendly option. However, always ensure that the alternative materials meet industry standards and regulations.
- Quality Assurance: While cost savings are important, it is equally crucial to prioritize quality. Poor-quality materials may lead to costly repairs and replacements down the line. Conduct proper due diligence, inspect materials before purchasing, and work with reputable suppliers to ensure the quality and durability of the materials.
- Supplier Relationships: Build long-term relationships with reliable suppliers to secure better pricing and service. A good relationship with suppliers can lead to discounts, timely delivery, and access to the latest products or innovations.
By carefully selecting materials and implementing a streamlined procurement process, construction professionals can minimize costs while maintaining high-quality standards in their projects.
Labor Management
Efficient labor management is crucial in keeping construction costs down. Proper planning and effective utilization of labor resources can optimize productivity and reduce expenses. Here are some strategies to consider for effective labor management:
- Workforce Planning: Assess the project requirements and plan the workforce accordingly. Hire an appropriate number of skilled workers to ensure tasks are completed efficiently without overstaffing. Avoid unnecessary overtime, which can lead to increased labor costs.
- Skilled Labor: Invest in hiring skilled laborers who have experience and expertise in their respective trades. Skilled workers can complete tasks more efficiently and effectively, reducing the need for rework and correcting mistakes.
- Training and Development: Provide regular training and development opportunities for the labor force. Enhancing their skills and knowledge can improve productivity and reduce the occurrence of errors or accidents.
- Task Delegation: Assign tasks based on individual strengths and abilities. Delegate responsibilities effectively to ensure that each worker is focused on tasks that align with their skill set. This can improve efficiency and reduce the likelihood of mistakes.
- Effective Communication: Establish clear lines of communication with the labor force. Ensure that instructions and project requirements are clearly communicated, and address any concerns or questions promptly to prevent delays and rework.
- Efficient Time Management: Implement time-tracking systems and ensure that workers are utilizing their time effectively. Minimize downtime by coordinating tasks and activities to maximize productivity throughout the construction process.
By implementing these labor management strategies, construction professionals can ensure optimal utilization of their workforce and effectively manage labor costs, resulting in budgetary savings without compromising on project quality and timelines.
Project Scheduling
Effective project scheduling is vital in keeping construction costs under control. Proper planning and scheduling ensure that tasks are completed in a timely manner, minimizing delays and unnecessary expenses. Here are some strategies to consider for efficient project scheduling:
- Comprehensive Planning: Create a detailed project plan that includes all necessary tasks, milestones, and deadlines. Consider dependencies between tasks and factor in potential delays or unforeseen circumstances.
- Sequence of Work: Determine the optimal sequence of work to streamline the construction process. Start with critical tasks that may affect the entire project schedule and prioritize them accordingly. By sequencing tasks efficiently, you can prevent bottlenecks and minimize downtime.
- Realistic Timeframes: Set realistic timeframes for completing tasks and milestones. Consult with experienced contractors and project managers to accurately estimate the time required for each activity. Avoid overestimating or underestimating, as both can lead to additional costs.
- Resource Allocation: Allocate resources effectively to ensure that each task has the necessary equipment, materials, and labor available when needed. Proper resource management prevents delays caused by waiting for resources to become available and minimizes idle time.
- Contingency Planning: Anticipate potential risks and develop contingency plans for unforeseen events. This will help mitigate the impact on project timelines and costs. Incorporate buffer time in the schedule to account for any unforeseen delays.
- Regular Monitoring and Updates: Continuously monitor the progress of the project and update the schedule as needed. Identify any deviations from the original plan and take corrective actions promptly to keep the project on track. Regular communication with the project team is essential to maintain an accurate and up-to-date schedule.
By implementing effective project scheduling practices, construction professionals can ensure that tasks are completed efficiently, minimizing potential delays and cost overruns. A well-executed schedule helps in optimizing resources, reducing idle time, and improving overall project efficiency.
Read more: How To Keep Artificial Grass Down
Value Engineering
Value engineering is a systematic approach to identify and implement cost-effective solutions without compromising the quality, functionality, and safety of a construction project. It involves analyzing different aspects of a project to find alternative methods, materials, or designs that provide the same or enhanced value at a lower cost. Here are some key strategies for value engineering:
- Collaborative Approach: Involve key stakeholders, such as architects, engineers, contractors, and suppliers, in the value engineering process. Their collective knowledge and expertise can help identify opportunities for cost savings without sacrificing project requirements.
- Cost-Benefit Analysis: Conduct a thorough cost-benefit analysis of various design options or materials. Compare the upfront costs, long-term maintenance costs, durability, and performance to determine the most cost-effective solution.
- Functionality Evaluation: Assess the functionality and performance requirements of the project and explore alternative solutions that meet those requirements at a lower cost. This could involve using different materials, modifying designs, or reevaluating equipment specifications.
- Standardization and Modularization: Standardize components and systems where possible to take advantage of economies of scale. Modular construction techniques can minimize material waste, reduce labor costs, and speed up the construction process.
- Life Cycle Cost Analysis: Consider the long-term costs associated with the project, including operation, maintenance, and replacement. Opting for energy-efficient systems, durable materials, and low-maintenance designs can result in significant cost savings over the life of the project.
- Continuous Improvement: Encourage a culture of continuous improvement and innovation within the project team. Regularly review and reassess processes, designs, and materials to identify opportunities for cost reduction and enhanced efficiency.
Value engineering is not about cutting corners or compromising quality. Instead, it is about finding smarter and more cost-effective solutions that deliver the same or better value. By leveraging value engineering techniques, construction professionals can optimize project costs while meeting the project’s objectives and requirements.
Efficient Communication
Efficient communication is essential in construction projects to minimize misunderstandings, delays, and costly errors. Effective communication ensures that all project stakeholders are aligned, enabling smooth coordination and timely decision-making. Here are some strategies for efficient communication in construction:
- Clear and Concise Communication: Use clear and concise language when communicating project details, requirements, and expectations. Avoid jargon, technical terms, or ambiguous language that could lead to misunderstandings. Clarify any uncertainties promptly to prevent errors or rework.
- Regular Project Meetings: Conduct regular project meetings to provide updates, address concerns, and ensure that everyone is on the same page. Utilize technology such as video conferencing or collaboration tools if team members are located remotely or on different job sites.
- Documented Communication: Document all key project communication in written form, such as meeting minutes, email correspondence, and progress reports. This serves as a reference for future discussions and reduces the chances of miscommunication or memory lapses.
- Listen and Seek Clarification: Actively listen to the concerns and feedback of project team members and stakeholders. Encourage open communication and foster a collaborative environment where everyone feels comfortable asking questions and seeking clarification.
- Effective Team Collaboration: Foster a collaborative atmosphere among the project team members. Encourage regular communication and information sharing, both vertically and horizontally within the organization. This promotes cross-functional collaboration, problem-solving, and avoids duplication of effort.
- Utilize Technology: Leverage construction management software, project management tools, and communication platforms to streamline communication processes. These technologies enable real-time updates, instant messaging, document sharing, and task tracking, enhancing overall efficiency and productivity.
Efficient communication contributes to a well-coordinated construction project, ensuring that all parties are informed, aligned, and equipped to make timely decisions. By promoting clear and open communication channels, construction professionals can minimize costly errors, delays, and rework, ultimately reducing project costs.
Consider using cost-effective materials and construction methods, such as pre-fabricated components or recycled materials, to keep construction costs down.
Regular Inspections and Quality Control
Regular inspections and quality control processes are crucial in construction projects to ensure that work is done according to specifications and industry standards. By maintaining high-quality standards, construction professionals can reduce the risk of rework, warranty claims, and costly remediation. Here are some strategies for effective inspections and quality control:
- Inspection Checklist: Develop a comprehensive inspection checklist that covers all critical aspects of the project. This could include structural integrity, plumbing, electrical systems, HVAC, and finishes. Regularly conduct inspections using the checklist to identify any deficiencies or non-compliance.
- Trained Inspectors: Employ trained inspectors or quality control professionals who have a thorough understanding of construction standards and regulations. Their expertise will enable them to identify any deviations from the specifications and ensure that corrective actions are taken promptly.
- Material Testing: Incorporate material testing and analysis as part of the quality control process. This can include conducting strength tests on concrete, verifying material specifications, and performing quality checks on the sourced materials.
- Documented Procedures: Establish documented procedures and guidelines for quality control inspections. This includes defining the frequency of inspections, who is responsible for conducting them, and how deficiencies should be reported and addressed.
- Third-Party Inspections: Consider engaging third-party inspection agencies or consultants to provide an independent assessment of the construction work. Their unbiased evaluations can provide an extra layer of quality assurance and peace of mind.
- Continuous Improvement: Use inspection findings as an opportunity for continuous improvement. Analyze trends and common issues identified during inspections and take proactive measures to address root causes, improve processes, and enhance project quality.
- Training and Accountability: Provide ongoing training to construction teams on quality control standards, best practices, and the importance of adherence to specifications. Foster a culture of accountability where all team members understand their roles and responsibilities in maintaining quality standards.
Regular inspections and quality control processes not only help identify and rectify deficiencies but also contribute to higher overall construction quality. By proactively addressing quality issues, construction professionals can avoid costly rework, delays, and potential safety hazards, ultimately keeping construction costs in check and ensuring client satisfaction.
Effective Cost Tracking and Management
Effective cost tracking and management are essential in construction projects to keep expenditures in check and prevent budget overruns. By closely monitoring expenses and implementing cost control measures, construction professionals can ensure financial success. Here are some strategies for effective cost tracking and management:
- Establish a Detailed Budget: Develop a detailed and comprehensive budget that outlines all expected costs throughout the project. This should include materials, labor, equipment, permits, insurance, and contingencies. Regularly review and update the budget as the project progresses.
- Track Expenses: Maintain a systematic method for tracking and documenting all project-related expenses, including receipts, invoices, and cost reports. This allows for accurate and up-to-date financial records, making it easier to identify areas of overspending or potential cost-saving opportunities.
- Accurate Cost Estimations: Ensure that cost estimations are as accurate as possible during the pre-construction phase. This includes conducting thorough quantity takeoffs, obtaining competitive bids, and considering historical data from similar projects. Overestimating or underestimating costs can lead to significant budget deviations.
- Procurement Analysis: Regularly analyze procurement activities to identify cost-saving opportunities. Compare prices, negotiate with suppliers for better rates, and explore alternative vendors or materials that offer better value for money.
- Variance Analysis: Conduct regular variance analysis to compare actual project costs against the budgeted amounts. Identify the reasons behind any cost variances and take corrective actions, such as adjusting project plans, reallocating resources, or implementing cost-saving measures.
- Change Order Management: Establish a robust change order management process to handle any modifications or additions to the scope of work. Ensure that change orders are thoroughly reviewed, cost implications are assessed, and proper approvals are obtained before proceeding with the changes.
- Risk Management: Identify potential risks and develop contingency plans to mitigate their impact on project costs. A proactive approach to risk management can help prevent unexpected expenses and minimize financial disruptions.
- Regular Financial Reviews: Conduct regular financial reviews with project stakeholders to assess the project’s financial performance. Use these reviews to address any financial concerns, make necessary adjustments to the budget, and identify strategies for cost reduction.
By implementing effective cost tracking and management practices, construction professionals can maintain control over project expenditures, avoid budget overruns, and optimize financial outcomes. Continuous monitoring and proactive management of costs contribute to the overall success of a construction project.
Read more: How To Keep Outdoor Rugs Down
Minimizing Change Orders
Change orders can significantly impact construction costs, resulting in delays, additional expenses, and potential conflicts with project stakeholders. Minimizing change orders is crucial to keeping projects on track and within budget. Here are some strategies to minimize change orders in construction projects:
- Thorough Planning and Design: Invest time and effort in the planning and design phase to ensure that project requirements are clearly defined and documented. Engage with stakeholders, including clients, architects, and engineers, to align expectations and minimize the need for design changes later on.
- Effective Communication: Establish open lines of communication with all project stakeholders from the start. Regularly communicate project progress, discuss any potential changes or issues, and seek input to proactively address concerns before they escalate into change orders.
- Comprehensive Scope of Work: Develop a comprehensive and detailed scope of work that outlines the project’s objectives, deliverables, specifications, and requirements. Ensure that all parties involved clearly understand and agree upon the scope to minimize misunderstandings and unnecessary changes.
- Thorough Contract Agreements: Create well-defined and comprehensive contract agreements that clearly state the obligations, responsibilities, and limitations of all parties involved. Include specific provisions addressing change orders, including approval processes, cost and schedule impacts, and dispute resolution mechanisms.
- Client Involvement: Actively involve clients throughout the project to ensure that their expectations are understood and integrated into the project scope. Regularly update clients on progress and seek their input to avoid misunderstandings and reduce the likelihood of change orders.
- Change Order Review Process: Implement a standardized change order review process that requires thorough analysis and evaluation before approving any changes. Assess the impact of the proposed change on project costs, schedules, and resources to make informed decisions.
- Value Engineering: Emphasize value engineering techniques during the pre-construction phase to identify cost-saving opportunities and alternatives without compromising project quality. This can reduce the need for design changes later on due to cost concerns.
- Proactive Issue Resolution: Promptly address and resolve any issues or conflicts that arise during the construction process. By addressing concerns proactively, you can prevent small problems from turning into larger ones that necessitate change orders.
By implementing these strategies, construction professionals can minimize change orders, streamline project execution, and reduce costs. Effective planning, communication, and proactive issue resolution are essential to avoiding unnecessary changes and ensuring project success.
Collaboration with Contractors and Subcontractors
Collaboration with contractors and subcontractors is crucial in construction projects to ensure smooth coordination, timely project delivery, and cost control. Building effective relationships and fostering collaboration among all parties involved can lead to improved project outcomes. Here are some strategies for effective collaboration with contractors and subcontractors:
- Early Involvement: Involve contractors and subcontractors early in the project planning stage. Their expertise and input can help identify potential challenges, offer valuable insights, and provide more accurate cost estimates.
- Clear Expectations: Clearly communicate project goals, requirements, and performance expectations to contractors and subcontractors. Establish clear deliverables, timelines, and quality standards, ensuring that all parties are aligned from the beginning.
- Regular Communication: Maintain open lines of communication with contractors and subcontractors throughout the project. Regularly discuss progress, address any concerns, and encourage collaboration to ensure that everyone is working towards the same objectives.
- Collaborative Problem-Solving: Encourage a collaborative approach to problem-solving. When issues arise, involve contractors and subcontractors in finding solutions together. Their input and expertise may lead to innovative and cost-effective resolutions.
- Transparent Documentation: Maintain transparent documentation of project plans, specifications, contracts, and change orders. This establishes clear expectations and provides a reference point for all parties, minimizing misunderstandings and the potential for disputes.
- Regular Site Meetings: Conduct regular site meetings that include all key stakeholders, including contractors, subcontractors, and project managers. These meetings facilitate communication, provide updates on progress, and allow for immediate clarification of any issues or questions.
- Rewarding Performance: Recognize and reward contractors and subcontractors who consistently meet or exceed project requirements. This fosters a positive working relationship and motivates them to continue delivering high-quality work.
- Proactive Issue Resolution: Promptly address any issues or disputes that arise during construction. Work together with contractors and subcontractors to find mutually beneficial solutions that minimize disruptions and mitigate cost implications.
- Payment Terms and Incentives: Establish fair and clearly defined payment terms for contractors and subcontractors. Consider incorporating incentive structures for early completion or cost savings to encourage efficiency and collaboration.
Effective collaboration with contractors and subcontractors promotes a cohesive project team and enables optimal use of resources, resulting in improved project outcomes, reduced costs, and timely delivery. When all parties work together towards a common goal, projects are completed successfully while maintaining budgetary and quality requirements.
Utilizing Technology and Automation
In today’s digital age, leveraging technology and automation can significantly improve construction processes, enhance productivity, and reduce costs. By embracing innovative tools and software, construction professionals can streamline operations and achieve greater efficiency. Here are some ways to effectively utilize technology and automation in construction:
- Building Information Modeling (BIM): BIM technology enables the creation of a digital representation of the project, facilitating effective collaboration, clash detection, and improved decision-making. It helps identify potential conflicts early on, minimizing rework and change orders.
- Construction Management Software: Implement construction management software that integrates various project management aspects, including scheduling, document management, cost tracking, and communication. These platforms provide real-time data, streamline processes, and enhance overall project visibility.
- Drones and Aerial Imaging: Utilize drones for aerial imaging and surveying to gather accurate and up-to-date data about the project site. This technology enables faster surveying, progress monitoring, and site analysis, reducing the need for manual work and improving accuracy.
- Mobile Applications: Equip construction teams with mobile applications that allow them to access project information, document progress, submit reports, and communicate in real-time. This promotes efficient collaboration, eliminates paper-intensive processes, and enhances productivity on-site.
- IoT and Sensor Technology: Internet of Things (IoT) devices and sensors can be used to capture and analyze valuable data during construction, such as equipment usage, environmental conditions, and energy consumption. This data-driven approach enables proactive decision-making, resource optimization, and cost reduction.
- Automated Equipment and Robotics: Incorporate automated equipment and robotics for tasks that are repetitive, time-consuming, or hazardous. Automated processes can improve productivity, reduce labor costs, and enhance safety on the construction site.
- Virtual and Augmented Reality: Utilize virtual and augmented reality technologies for enhanced visualization, simulation, and training purposes. These technologies allow stakeholders to experience the project in a virtual environment, identify design issues, and make informed decisions before construction begins.
- Prefabrication and Modular Construction: Embrace prefabrication and modular construction techniques to improve efficiency, quality control, and cost-effectiveness. These methods involve fabricating components off-site, reducing construction time, minimizing waste, and optimizing resources.
By embracing technology and automation, construction professionals can streamline processes, improve collaboration, minimize errors, and reduce costs. Investing in innovative solutions allows for more efficient project execution, ultimately leading to successful construction projects that meet both budgetary and quality requirements.
Conclusion
In the construction industry, keeping costs down is crucial for project success and profitability. By implementing strategic measures and embracing innovative approaches, construction professionals can effectively minimize expenses without compromising on quality or safety. Throughout the various stages of a construction project, from planning and design to project completion, several key strategies can be employed to achieve cost reduction objectives.
The initial planning and design phase plays a critical role in optimizing costs. Clear project scoping, efficient floor plans, and value engineering techniques help identify cost-saving opportunities while meeting project objectives. Careful material selection and procurement practices ensure the use of quality materials at competitive prices.
Labor management encompasses tasks such as workforce planning, skillful task delegation, effective communication, and training and development. Proper project scheduling, while accounting for contingencies, ensures efficient utilization of resources and minimizes delays and overtime expenses.
Value engineering promotes the exploration of cost-effective alternatives without compromising quality, functionality, or safety. Efficient communication, both within the project team and with contractors and subcontractors, fosters collaboration and avoids misunderstandings that can lead to costly change orders.
Regular inspections and quality control measures guarantee that work is performed to specifications while reducing the risk of rework or costly errors. Effective cost tracking and management practices, along with minimizing change orders, facilitate staying within budget while maintaining financial control.
Lastly, the utilization of technology and automation tools empowers construction professionals to streamline processes, enhance communication, and improve efficiency. This can encompass the adoption of BIM technology, use of construction management software, and incorporation of automated equipment and robotics.
By applying these strategies and embracing innovation, construction professionals can successfully navigate the challenges of cost control in construction projects. Combining sound management practices, effective communication, and the intelligent use of technology, construction projects can be delivered on time, within budget, and to the satisfaction of all stakeholders involved.
Frequently Asked Questions about How To Keep Construction Costs Down
Was this page helpful?
At Storables.com, we guarantee accurate and reliable information. Our content, validated by Expert Board Contributors, is crafted following stringent Editorial Policies. We're committed to providing you with well-researched, expert-backed insights for all your informational needs.
0 thoughts on “How To Keep Construction Costs Down”