Home>diy>Building & Construction>What Is Overhead Cost In Construction
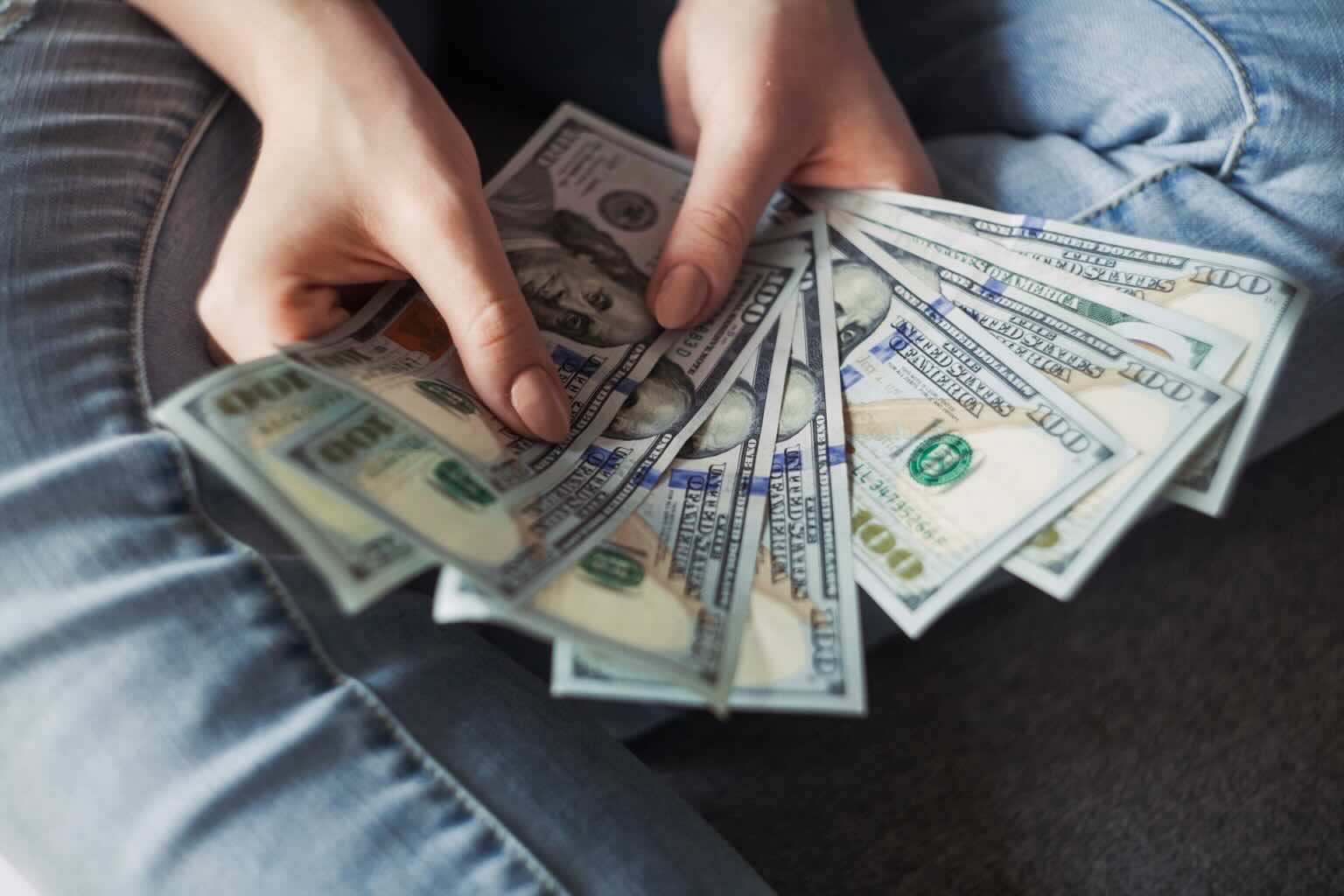
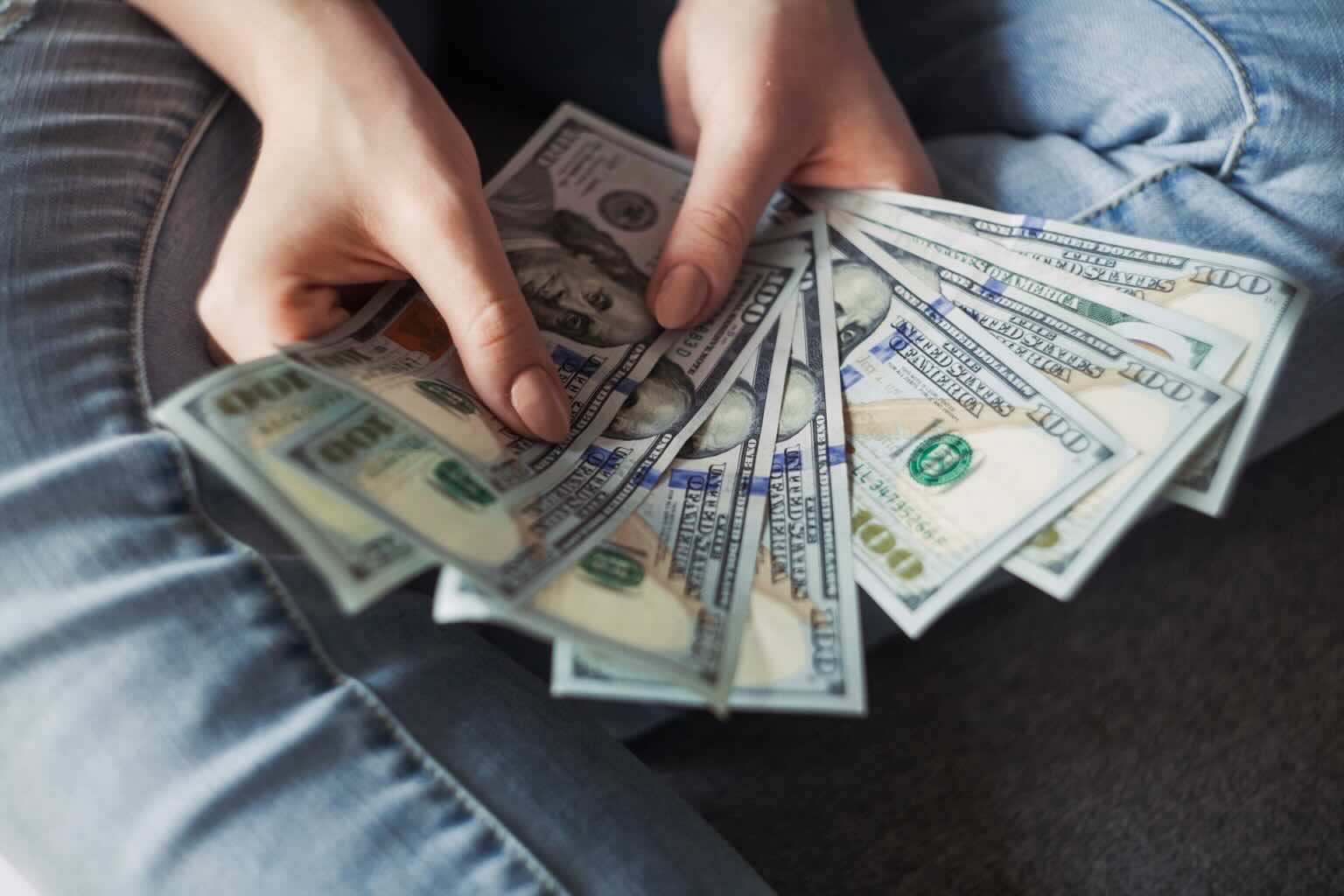
Building & Construction
What Is Overhead Cost In Construction
Modified: January 9, 2024
Learn about overhead costs in building construction and how they impact project budgets. Gain insights into managing and minimizing these expenses for successful construction projects.
(Many of the links in this article redirect to a specific reviewed product. Your purchase of these products through affiliate links helps to generate commission for Storables.com, at no extra cost. Learn more)
Introduction
Welcome to the world of construction, where the art of building meets the science of cost calculation. In the realm of construction projects, there are many factors to consider, from materials and labor to equipment and permits. One crucial component that often gets overlooked is overhead cost.
Overhead cost plays a significant role in construction projects, as it encompasses various expenses not directly related to the production or materials. Understanding and managing overhead cost is essential for construction companies to ensure profitability and successful project completion.
In this article, we will delve into the definition, importance, components, calculation, and management of overhead cost in construction. Whether you are a construction professional, project manager, or simply curious about the inner workings of the industry, this article will provide you with valuable insights.
Key Takeaways:
- Overhead cost in construction encompasses various indirect expenses crucial for a company’s functioning. Accurate estimation, cost monitoring, and prioritizing value-adding activities are essential for effective management.
- Factors influencing overhead cost include project size, location, labor productivity, and market conditions. By adopting innovative practices and efficient resource allocation, construction companies can optimize profitability and project success.
Definition of Overhead Cost
Before we dive into the details, let’s define overhead cost in the context of construction. Overhead cost refers to the expenses incurred by a construction company that are not directly attributable to a specific project or task. These expenses are necessary for the overall operation and management of the company and are shared across multiple projects or activities.
Overhead cost covers a wide range of expenses, including administrative costs, rent, utilities, insurance, taxes, and salaries of non-direct project personnel. It represents the ongoing costs that are incurred regardless of whether a company is actively working on a project.
Unlike direct costs, such as labor and materials directly used in project construction, overhead costs cannot be easily allocated to a specific activity or project since they benefit the overall functioning of the company. However, they are still a vital part of the construction process and need to be accounted for and managed effectively.
Understanding and tracking overhead costs accurately is crucial for construction companies as it allows them to determine the true cost of a project, evaluate its profitability, and make informed decisions about pricing, budgeting, and resource allocation.
Importance of Overhead Cost in Construction
Overhead cost is a critical aspect of construction projects, and its proper management is essential for the success and profitability of construction companies. Here are some reasons why overhead cost is important:
- Accurate Cost Estimation: Including overhead costs in project estimates ensures that the total cost of the project is calculated accurately. By considering both direct costs and overhead costs, construction companies can determine the actual expenses associated with a project and avoid underestimating the budget.
- Determining Project Profitability: Properly accounting for overhead costs allows construction companies to determine the net profit or loss on a project. This information is crucial for making informed decisions about which projects to take on, negotiating contracts, and assessing the financial health of the company.
- Budgeting and Resource Allocation: Understanding overhead costs helps construction companies allocate resources effectively. By knowing the ongoing operating expenses, companies can allocate funds for overhead costs appropriately, ensuring that the necessary resources are available without compromising project budgets.
- Pricing and Competitive Advantage: Accurately accounting for overhead costs allows construction companies to set competitive pricing for their services. Pricing too low may result in losses, while pricing too high can deter potential clients. Properly accounting for overhead costs ensures fair pricing, considering both direct project costs and the company’s overhead expenses.
- Risk Management: Ongoing management of overhead costs helps construction companies identify areas where expenses can be reduced or controlled. This allows companies to mitigate financial risks associated with overhead costs, prevent cost overruns, and maintain profitability.
In summary, overhead costs play a crucial role in construction projects by providing a comprehensive understanding of the true costs involved. Proper management of overhead costs ensures accurate cost estimation, enhances profitability, facilitates budgeting and resource allocation, helps set competitive pricing, and enables effective risk management.
Components of Overhead Cost
Overhead cost in construction comprises various components that are necessary to support the overall functioning of a construction company. Let’s take a closer look at the main components:
- Labor Overhead Cost: This component encompasses the expenses associated with non-direct labor, such as wages and benefits for administrative staff, supervisors, project managers, and support personnel. It also includes training and development costs for employees.
- Materials Overhead Cost: Materials overhead cost includes expenses related to the storage, handling, and transportation of construction materials. This may involve costs for warehouses, material handling equipment, and storage facilities.
- Equipment Overhead Cost: Construction companies often utilize various types of equipment, including heavy machinery, tools, and vehicles. Equipment overhead cost accounts for expenses such as maintenance, repairs, depreciation, and operating costs of these equipment items.
- Subcontractor Overhead Cost: Subcontractor expenses are an essential part of construction projects. This component covers the fees paid to subcontractors for their services, including coordination, management, and any necessary support they provide throughout the construction process.
- General Overhead Cost: General overhead cost includes expenses that are not directly tied to a specific project or task. These may include rent for office space, utilities, insurance premiums, taxes, office supplies, and marketing and advertising expenses.
These components of overhead cost can vary between construction companies based on their size, scope of projects, and organizational structure. It is crucial for construction companies to identify and accurately allocate these costs to ensure proper cost management and profitability.
Labor Overhead Cost
Labor is a fundamental component of construction projects, and labor overhead cost refers to the expenses associated with non-direct labor activities that support the overall functioning of a construction company. It encompasses various aspects of workforce management, including wages, benefits, training, and development. Let’s explore further into the details of labor overhead cost:
1. Wages and Benefits: Labor overhead cost includes the wages and salaries paid to administrative staff, supervisors, project managers, and support personnel who are not directly involved in project construction. These individuals play crucial roles in managing operations, overseeing projects, ensuring compliance, and providing administrative support.
In addition to wages, labor overhead cost also includes benefits such as health insurance, retirement plans, paid time off, and other employee perks. These benefits contribute to the overall cost of labor and must be factored into the calculation of labor overhead expenses.
2. Training and Development: Construction companies invest in the training and development of their employees to enhance their skills, knowledge, and expertise. Labor overhead cost includes expenses related to training programs, workshops, seminars, certifications, and continuing education for employees.
Effective training and development programs help improve the efficiency, productivity, and safety of the workforce. By investing in employee growth, construction companies ensure a skilled and competent workforce, leading to improved project outcomes and overall company success.
3. Employee Support: Labor overhead cost also covers various employee support activities that are necessary for the day-to-day operations of the construction company. This may include HR (human resources) functions, payroll processing, employee relations, and compliance management.
Employee support activities ensure that the workforce is well-managed, motivated, and compliant with legal and regulatory requirements. These activities contribute to the smooth functioning of the company as a whole and are essential for maintaining a healthy work environment.
Overall, labor overhead cost is an important component of overhead expenses in construction. It covers the wages, benefits, training, and development, as well as employee support activities that are crucial for the efficient functioning, management, and growth of a construction company. Effectively managing labor overhead cost ensures a skilled and motivated workforce, which ultimately contributes to the success and profitability of construction projects.
Read more: What Is Considered Overhead In Construction
Materials Overhead Cost
Materials are a critical component of construction projects, and materials overhead cost refers to the expenses associated with various activities related to the storage, handling, and transportation of construction materials. These costs are necessary for the smooth and efficient operation of a construction company. Let’s delve into the details of materials overhead cost:
1. Storage and Warehousing: The storage of construction materials is an essential aspect of any construction project. Materials overhead cost includes expenses related to renting or owning warehouses, storage facilities, or yards to store the construction materials safely. This may also include costs for shelving, pallets, and containers for organization and proper storage.
2. Handling and Transportation: Construction materials need to be handled and transported from suppliers to the construction site. Materials overhead cost accounts for the expenses associated with loading, unloading, and transporting materials using trucks, forklifts, or other equipment. This may also include costs for fuel, maintenance, and insurance for the vehicles used in materials transportation.
3. Inventory Management: Construction companies need to manage their inventory of materials effectively to ensure a continuous supply for projects while minimizing waste and excess. Materials overhead cost includes expenses related to inventory tracking, management systems, inventory audits, and any necessary software or technology used to monitor and control the materials inventory.
4. Loss and Waste: Construction projects can experience material loss or waste due to factors such as damage, theft, or improper handling. Materials overhead cost covers the expenses associated with these losses or waste, including replacements, repairs, and disposal costs. Implementing proper inventory control and waste management strategies can help minimize these costs.
Accurately accounting for materials overhead cost is crucial for construction companies as it allows them to monitor and manage the expenses associated with the storage, handling, transportation, and management of construction materials. Effective management of materials overhead cost ensures that construction projects have a continuous supply of materials, reduces waste and loss, and improves overall project efficiency and profitability.
Equipment Overhead Cost
Equipment is an essential element in construction projects, and equipment overhead cost refers to the expenses associated with the ownership, maintenance, and operation of various types of equipment used in construction. Proper management of equipment overhead cost is crucial for ensuring the efficiency and profitability of construction projects. Let’s explore the details of equipment overhead cost:
1. Equipment Maintenance and Repairs: Construction equipment requires regular maintenance and occasional repairs to keep it in optimal working condition. Equipment overhead cost includes expenses related to routine maintenance, scheduled inspections, and the costs of repairing any breakdowns or malfunctions. This may involve hiring skilled technicians, purchasing replacement parts, or outsourcing maintenance tasks to specialized service providers.
2. Depreciation: Construction equipment has a limited lifespan, and its value depreciates over time due to wear and tear, technological advancements, and market conditions. Equipment overhead cost accounts for the depreciation of equipment, which is the gradual reduction in its value. Companies must allocate a portion of the equipment’s original cost as an overhead expense to account for depreciation.
3. Operating Costs: Construction equipment requires fuel, lubricants, and other consumables to operate. Equipment overhead cost includes expenses associated with the ongoing operation of equipment, such as fuel costs, oil changes, filter replacements, and other consumables required for proper functioning.
4. Insurance and Licensing: Construction equipment often requires insurance coverage to protect against damages, theft, or accidents. Equipment overhead cost includes insurance premiums paid to ensure the equipment is adequately covered. Additionally, licensing fees and permits for operating equipment may also be included in equipment overhead cost.
5. Equipment Financing: In some cases, construction companies may finance the purchase of equipment through loans or leasing arrangements. Equipment overhead cost includes the expenses associated with financing, such as interest payments, lease payments, or lease fees.
Proper management of equipment overhead cost is essential for construction companies as it allows them to allocate resources efficiently, ensure equipment reliability and performance, and make informed decisions regarding equipment acquisition and replacement. Construction companies must carefully evaluate their equipment needs, implement effective maintenance strategies, and consider factors like utilization rates and overall equipment costs to optimize their equipment overhead expenses.
Overhead costs in construction include expenses like office rent, utilities, and administrative salaries. It’s important to accurately calculate and allocate these costs to projects to ensure accurate pricing and profitability.
Subcontractor Overhead Cost
In the construction industry, subcontractors play a vital role in completing projects. Subcontractor overhead cost refers to the expenses associated with hiring and managing subcontractors for specific tasks or specialized services. Proper management of subcontractor overhead cost is essential for ensuring successful project execution. Let’s explore the details of subcontractor overhead cost:
1. Subcontractor Fees: The primary component of subcontractor overhead cost is the fees paid to subcontractors for their services. These fees typically include the subcontractor’s labor and expertise, project management, coordination, and any necessary support they provide throughout the construction process. It is important to establish clear agreements and contracts with subcontractors to define the scope of work and the associated fees.
2. Planning and Coordination: Subcontractor overhead cost also covers the expenses associated with planning and coordinating subcontractor activities. This includes communication, meetings, collaboration, and supervision to ensure that subcontractors are properly aligned with the project schedule and quality standards. It may also involve the use of project management software or tools to facilitate coordination and information sharing.
3. Insurance and Legal Compliance: In many cases, subcontractors need to carry insurance coverage and adhere to legal compliance requirements. Subcontractor overhead cost includes expenses related to verifying insurance coverage, ensuring compliance with safety regulations, and ensuring that subcontractors have the necessary licenses and permits to perform their work. This helps mitigate potential risks and ensures that subcontractors meet industry standards and legal obligations.
4. Documentation and Administration: Subcontractor overhead cost covers the administrative tasks associated with subcontractor management. This includes contract administration, documenting work progress, processing payments for completed work, and maintaining records of subcontractor expenses. Keeping accurate records and documentation ensures transparency and facilitates financial and project management processes.
5. Quality Control and Performance Evaluation: Construction companies must monitor the performance of subcontractors to ensure that they meet quality standards and deliver work to the agreed-upon specifications. Subcontractor overhead cost includes expenses associated with quality control measures, inspections, and performance evaluations. This may involve the use of quality management systems, site visits, and corrective action management processes.
Effective management of subcontractor overhead cost is essential for construction companies to achieve project success. By carefully selecting subcontractors, establishing clear agreements, coordinating activities, ensuring compliance, and monitoring performance, construction companies can optimize the utilization of subcontractors while minimizing risks and costs. Proper management of subcontractor overhead cost contributes to efficient project execution, client satisfaction, and overall profitability.
General Overhead Cost
General overhead cost is a broad category of expenses that are essential for the overall operation and management of a construction company. These expenses are not directly tied to a specific project or task but are necessary to support the company’s day-to-day operations. Let’s explore the details of general overhead cost:
1. Office Rent and Utilities: General overhead cost includes expenses related to office space, such as rent or mortgage payments, utilities (electricity, water, heating), internet, phone lines, and office maintenance. Providing a functional and comfortable office space is vital for managing the administrative functions of a construction company.
2. Insurance and Taxes: Construction companies need insurance coverage to protect against risks associated with their operations, such as liability insurance, property insurance, and workers’ compensation insurance. General overhead cost also includes various taxes imposed by authorities, such as property taxes, payroll taxes, and corporate income taxes.
3. Administrative Staff and Salaries: General overhead cost includes the salaries and benefits of administrative staff who support the day-to-day operations of the company. This includes roles such as office managers, accountants, human resources personnel, and other administrative employees necessary to ensure the smooth functioning of the company.
4. Marketing and Advertising: Construction companies need to invest in marketing and advertising to promote their services, gain new clients, and maintain brand visibility. General overhead cost covers expenses related to marketing campaigns, website development, advertising materials, trade show participation, and other promotional activities.
5. Professional Services: General overhead cost may include expenses related to professional services utilized by the construction company, such as legal services, accounting services, consultancy, and IT support. These services help ensure compliance with regulations, provide expert advice, and support the company’s operational and financial management.
6. Office Supplies and Equipment: General overhead cost includes expenses for office supplies (stationery, printer ink, paper) and equipment (computers, printers, copiers, furniture) necessary for day-to-day office operations. These items are essential for maintaining an efficient and productive work environment.
Proper management of general overhead cost is crucial for construction companies as it directly impacts the company’s overall financial health and profitability. By accurately budgeting and controlling these expenses, construction companies can optimize their operational efficiency, allocate resources effectively, and ensure the smooth functioning of the company as a whole.
Read more: What Is Overhead And Profit In Construction
Calculation of Overhead Cost
Calculating overhead cost in construction involves determining the indirect expenses that are necessary for the overall operation of a construction company. While the specific method may vary depending on the company and project, there are general approaches to consider. Let’s explore the calculation of overhead cost:
1. Identify Direct Costs: Start by identifying the direct costs associated with a construction project. These costs include labor, materials, equipment, and direct subcontractor expenses directly attributable to the project.
2. Determine Indirect Costs: Next, identify the various indirect costs that are not directly tied to any specific project but are necessary for the operation of the company. These may include administrative salaries, rent, utilities, insurance, taxes, marketing expenses, office supplies, and other general overhead costs.
3. Allocate Indirect Costs: Allocate the identified indirect costs to the project. There are different methods to allocate overhead costs, such as percentage allocation based on direct costs, labor hours, or square footage. The chosen method should reflect the company’s specific circumstances and provide a fair representation of the indirect costs associated with each project.
4. Determine Overhead Rate: Calculate the overhead rate by dividing the total indirect costs by the chosen allocation base. For example, if the total indirect costs amount to $100,000 and the allocation base is the total direct labor cost of $500,000, the overhead rate would be 20% ($100,000 / $500,000).
5. Apply Overhead Rate: Apply the determined overhead rate to the direct costs of each project to determine the overhead cost. Multiply the direct costs (such as labor, materials, and equipment) by the overhead rate (e.g., 20%) to obtain the overhead cost for each project.
Calculating the overhead cost accurately allows construction companies to determine the total cost of each project, evaluate its profitability, and make informed decisions about pricing, budgeting, and resource allocation. It is essential to review and adjust the overhead rate periodically to account for changes in the company’s expenses and industry conditions.
Effective management of overhead cost requires careful monitoring, cost control measures, and regular review of expenses to identify areas for potential cost savings. By accurately calculating and effectively managing overhead cost, construction companies can optimize their financial performance and improve the overall success of their projects.
Factors Influencing Overhead Cost
Several factors can influence the overhead cost in construction projects. These factors vary depending on the specific circumstances of each project and the construction company involved. Understanding and considering these factors is crucial for accurate cost estimation and effective management of overhead expenses. Let’s explore some of the key factors influencing overhead cost:
1. Size and Complexity of the Project: The size and complexity of a construction project can significantly impact the overhead cost. Larger and more complex projects often require additional administrative staff, coordination efforts, and resources, resulting in higher overhead expenses than smaller, straightforward projects.
2. Project Location: The geographical location of a project can influence the overhead cost due to variations in local labor rates, material availability, and transportation costs. Construction companies operating in high-cost areas may have higher overhead expenses compared to those in relatively lower-cost regions.
3. Project Duration: The duration of a project can affect overhead cost. Longer projects may require sustained overhead expenses, such as rental costs, insurance premiums, and ongoing administrative support. However, shorter projects may also have their own set of challenges, requiring compressed scheduling and intensified coordination efforts.
4. Labor Productivity: The productivity of the labor force can impact the overhead cost of a project. Factors such as worker efficiency, skill level, training, and experience can influence labor productivity. Higher productivity can result in reduced labor hours and lower overall overhead expenses.
5. Regulatory Requirements: Compliance with various regulatory requirements can affect overhead cost. Construction companies must spend resources on ensuring compliance with safety regulations, environmental regulations, licensing requirements, and building codes. Non-compliance or inadequate compliance can lead to potential legal issues and increased costs.
6. Market Conditions: Market conditions, including supply and demand dynamics, can influence overhead cost. Fluctuations in material prices, labor rates, and subcontractor availability can impact the overall cost of construction projects. Construction companies must monitor and adapt to market conditions to effectively manage overhead expenses.
7. Company Size and Structure: The size and organizational structure of a construction company can also influence overhead cost. Large companies may have higher overhead expenses due to the need for a more extensive administrative and management structure. Additionally, the incorporation of multiple divisions or branches can add to the overall overhead cost.
8. Technology and Innovation: The adoption of technology and innovative practices can impact overhead cost. Utilizing advanced project management software, mobile applications, and automation tools can improve efficiency, reduce administrative overhead, and streamline processes, potentially leading to cost savings.
These are just some of the factors that can influence overhead cost in construction projects. It is important for construction companies to carefully analyze and consider these factors when estimating and managing overhead expenses. By understanding these influencing factors, construction companies can make informed decisions, effectively control costs, and optimize their financial performance.
Control and Management of Overhead Cost
Effective control and management of overhead cost is crucial for construction companies to optimize profitability, ensure project success, and maintain a competitive edge. By adopting the right strategies and practices, construction companies can minimize unnecessary expenses and maximize the value of their resources. Here are some approaches to control and manage overhead cost:
1. Accurate Cost Estimation: Start by accurately estimating the overhead cost during the project planning phase. Consider all the components of overhead cost discussed earlier, such as labor, materials, equipment, subcontractors, and general overhead. Thoroughly analyze historical data, industry averages, and project-specific factors to determine realistic overhead expenses.
2. Cost Monitoring and Tracking: Implement systems and processes to monitor and track overhead expenses throughout the project lifecycle. Regularly review financial reports, budget vs. actual analyses, and project management software to identify any deviations or potential cost overruns. This allows for proactive measures to be taken to address issues promptly.
3. Prioritize Value-Adding Activities: Focus on activities that directly contribute value to the projects and the company. Eliminate or minimize non-value-adding tasks and non-essential expenses. Continuously assess and optimize processes to improve efficiency and reduce waste, such as streamlining paperwork, minimizing rework, and optimizing resource allocation.
4. Negotiate Contracts and Subcontracts: When engaging subcontractors or suppliers, negotiate contracts that clearly define the scope of work, pricing, and responsibilities. Seek competitive bids and carefully evaluate proposals to ensure fair pricing and cost-effectiveness. Regularly review and monitor subcontractor performance to ensure that they adhere to agreed-upon deliverables and quality standards.
5. Controlled Purchasing and Inventory Management: Establish a robust purchasing and inventory management system to control material costs. Maintain accurate and up-to-date records of materials and supplies, carefully plan and time purchases, and negotiate favorable terms with suppliers. Minimize waste and surplus by implementing proper storage and handling procedures and regularly auditing inventory levels.
6. Efficient Resource Allocation: Ensure resources, including labor and equipment, are allocated efficiently, taking into consideration project needs and skill requirements. Optimize workforce utilization by matching personnel expertise and experience to project requirements. Regularly review equipment usage and consider renting or leasing equipment when practical instead of outright purchases.
7. Continuous Improvement and Innovation: Foster a culture of continuous improvement and encourage innovation within the company. Embrace technology and automation tools that can streamline processes, reduce administrative tasks, and enhance productivity. Regularly evaluate and implement new practices, techniques, and technologies that can lead to cost savings and improved efficiency.
8. Benchmarking and Best Practices: Benchmark against industry standards and best practices to gauge the company’s performance and identify areas for improvement. Study successful construction companies and learn from their approaches to overhead cost control and management. Participate in industry associations and networking events to share knowledge and experiences with peers.
By implementing these strategies, construction companies can effectively manage and control overhead cost, which ultimately contributes to increased profitability, improved project outcomes, and sustained business success. A proactive and disciplined approach to overhead cost management can provide a significant competitive advantage in the construction industry.
Conclusion
Overhead cost is a critical aspect of construction projects that encompasses various indirect expenses necessary for the overall functioning of a construction company. Understanding and effectively managing overhead cost is essential for construction companies to ensure profitability, accurate cost estimation, and successful project completion.
In this article, we explored the definition of overhead cost and its importance in construction. We discussed the components of overhead cost, including labor overhead cost, materials overhead cost, equipment overhead cost, subcontractor overhead cost, and general overhead cost. Each component plays a crucial role in the overall overhead expenses of a construction project.
We also examined the factors influencing overhead cost, such as the size and complexity of the project, project location, labor productivity, regulatory requirements, market conditions, company size, and technology adoption. Understanding these factors allows construction companies to accurately estimate and manage overhead expenses.
To effectively control and manage overhead cost, construction companies should adopt strategies such as accurate cost estimation, cost monitoring and tracking, prioritizing value-adding activities, negotiation of contracts and subcontracts, controlled purchasing and inventory management, efficient resource allocation, continuous improvement, and benchmarking against industry standards.
By implementing these strategies and practices, construction companies can optimize the utilization of their resources, minimize unnecessary expenses, and maximize profitability. Effective control and management of overhead cost contribute to improved project outcomes, enhanced competitiveness, and sustained success in the construction industry.
In conclusion, understanding, tracking, and managing overhead cost are vital for construction companies’ financial health and project success. By prioritizing cost control measures, embracing innovation, and continuously improving processes, construction companies can thrive in an ever-evolving industry, ensuring long-term sustainability and profitability.
Frequently Asked Questions about What Is Overhead Cost In Construction
Was this page helpful?
At Storables.com, we guarantee accurate and reliable information. Our content, validated by Expert Board Contributors, is crafted following stringent Editorial Policies. We're committed to providing you with well-researched, expert-backed insights for all your informational needs.
0 thoughts on “What Is Overhead Cost In Construction”