Home>diy>Building & Construction>What Does As-Builts Mean In Construction
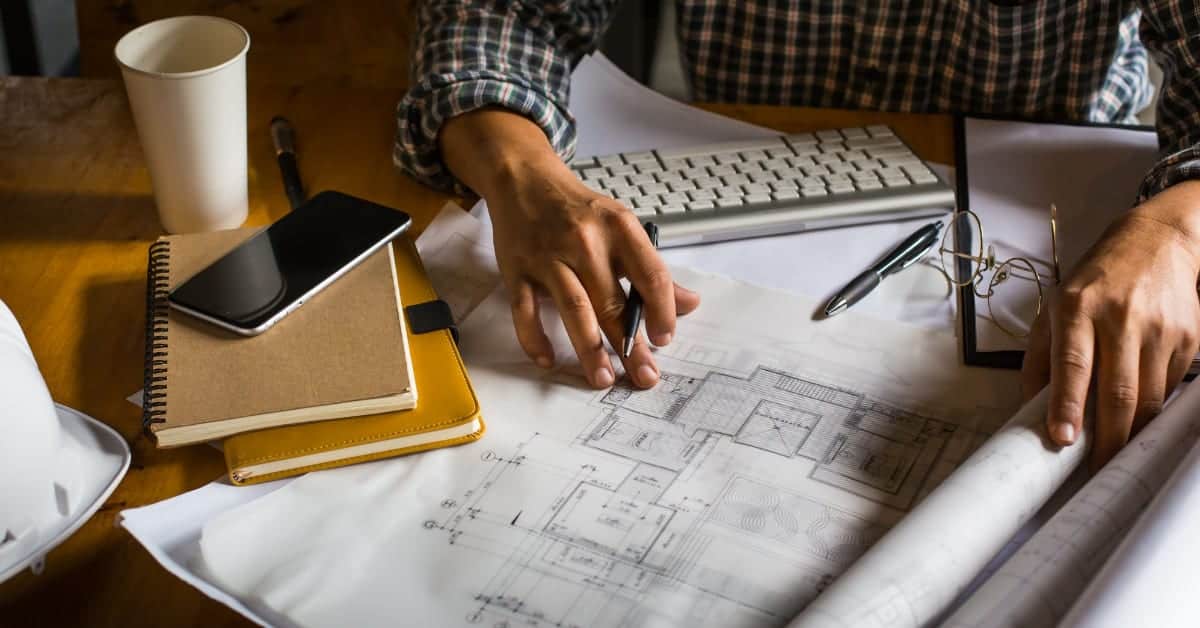
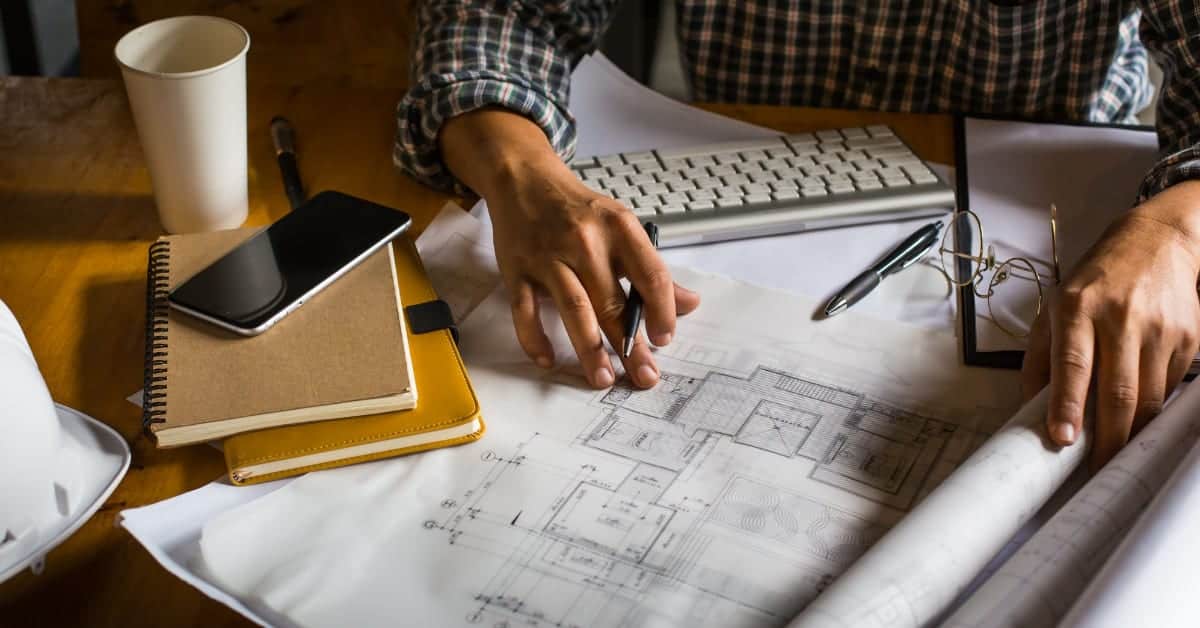
Building & Construction
What Does As-Builts Mean In Construction
Modified: January 23, 2024
Discover the meaning of "as-builts" in building construction. Explore how these documents play a vital role in recording and updating crucial information.
(Many of the links in this article redirect to a specific reviewed product. Your purchase of these products through affiliate links helps to generate commission for Storables.com, at no extra cost. Learn more)
Introduction
Welcome to the fascinating world of construction. Building projects involve a complex process with multiple stakeholders, intricate designs, and countless moving parts. In this dynamic and ever-evolving industry, it is crucial to have accurate and up-to-date documentation to ensure the success of the project.
One critical aspect of construction project documentation is the concept of “As-Builts.” In simple terms, As-Builts refer to the final set of drawings or documents that represent the actual construction of a building or structure after completion. These drawings are a vital resource for architects, engineers, contractors, and facility managers, providing valuable information about the project’s as-built condition.
In this article, we will delve deeper into the definition, importance, process, benefits, and challenges associated with As-Builts in the construction industry. By gaining a comprehensive understanding of this concept, we can appreciate its significance and implement best practices to optimize project management.
Key Takeaways:
- As-Builts are crucial in construction, providing accurate documentation of as-built conditions, facilitating efficient project management, and ensuring long-term sustainability, compliance, and successful outcomes.
- Despite challenges, best practices such as early incorporation, standardized formats, technology utilization, and regular updates maximize the usability and value of As-Built documentation, mitigating risks and enhancing collaboration.
Read more: What Is As-Built In Construction
Definition of As-Builts
As-Builts are the final set of drawings, plans, and documents that accurately represent the completed construction project. They are a comprehensive record of the actual built conditions, capturing any changes or modifications made during the construction process. As-Builts provide a detailed and accurate representation of the project’s final state, showcasing the exact locations, dimensions, and specifications of various components within the building or structure.
As-Built drawings can include architectural, structural, mechanical, electrical, and plumbing plans, among others, depending on the complexity of the project. These drawings are typically created through a combination of site verification, field surveys, and coordination with the project team.
The purpose of As-Builts is to document any deviations from the original plans or specifications, such as changes made during construction, unforeseen site conditions, or variations from the initial design. These deviations are marked on the As-Built drawings using industry-standard symbols and notations, ensuring that anyone reviewing the documentation can easily identify the differences between the original plans and the as-built condition.
It’s important to note that As-Builts are not just simple “redline” drawings that indicate deviations. They are comprehensive documents that accurately portray the final state of the construction project, providing an invaluable resource for future reference, maintenance, renovations, or facility management.
While As-Builts are primarily associated with the completion of a project, they can also include revisions and updates made to the drawings during the lifespan of a building. Any modifications, renovations, or additions made after the initial construction should be accurately documented and incorporated into the As-Built drawings, ensuring a complete and accurate record of the building’s history.
Importance of As-Builts in Construction
As-Builts play a vital role in the construction industry, serving as a reliable source of information and documentation for various stakeholders involved in a project. Here are some key reasons why As-Builts are important:
- Accurate Record of Changes: Construction projects often undergo modifications, changes, and unforeseen adjustments during the building process. As-Builts provide an accurate record of these changes, capturing the deviations from the original plans. This information is crucial for future reference, troubleshooting, and maintenance purposes.
- Documentation of Site Conditions: As-Builts document the actual as-built conditions of the construction project, including any variations or discrepancies discovered during the construction process. This information is valuable for understanding the existing infrastructure, identifying potential issues, and ensuring compliance with codes and regulations.
- Facility Management and Maintenance: As-Builts serve as a comprehensive resource for facility managers and maintenance teams. They provide detailed information about the building’s layout, mechanical systems, electrical components, and plumbing infrastructure. This documentation enables effective maintenance planning, repairs, and renovations, saving time and resources in the long run.
- Legal and Insurance Purposes: As-Builts serve as legal documents that accurately represent the completed construction project. They can be used as evidence in case of disputes or claims, ensuring that all parties have a clear understanding of the project’s as-built condition. Additionally, As-Builts provide valuable information for insurance purposes, helping assess risks and determine coverage.
- Efficient Renovations and Retrofitting: As-Builts provide a foundation for future renovations, expansions, or retrofitting of the building. By having accurate documentation of the existing conditions, architects, engineers, and contractors can plan and execute modifications more efficiently, minimizing disruptions and optimizing the use of resources.
Overall, As-Builts are critical for ensuring accurate and reliable documentation of a construction project’s as-built condition. They provide valuable information for project stakeholders, facility managers, maintenance teams, legal purposes, and future renovations. As-Builts enhance project management, reduce risks, and support the long-term functionality and maintenance of the building.
Process of Creating As-Builts
The process of creating As-Builts involves several key steps to accurately capture and document the actual as-built conditions of a construction project. Here is an overview of the typical process:
- Site Verification: The initial step of creating As-Builts involves physically visiting the construction site to verify the built conditions. This includes conducting site surveys, measurements, and inspections to compare the actual construction with the original plans.
- Collecting Field Data: During the site verification process, field data is collected through various methods, such as laser scanning, photogrammetry, or manual measurements. Advanced technologies like 3D scanners and drones can be used to capture accurate measurements and images of the existing structure.
- Reviewing Original Plans: The next step is to review the original plans and specifications of the project. This helps identify any deviations or changes made during construction and serves as a reference point for comparing the as-built conditions.
- Documenting Deviations: Once the field data and original plans have been reviewed, any deviations or changes from the original plans are documented on the As-Built drawings. This includes marking modifications, additions, removals, and any variations discovered during site verification.
- Updating Drawings: After documenting the deviations, the As-Built drawings are updated to accurately reflect the actual construction. This involves revising the plans, dimensions, and specifications to match the as-built conditions captured during the site verification process.
- Review and Approval: The updated As-Built drawings are reviewed by the project team, including architects, engineers, contractors, and other relevant stakeholders. Any discrepancies or clarifications are addressed, and necessary revisions are made before final approval.
- Issuing As-Builts: Once the As-Built drawings have been reviewed and approved, they are finalized and issued to the project team. These drawings serve as the official record of the project’s as-built conditions and are used for future reference, maintenance, renovations, and facility management.
The process of creating As-Builts requires close collaboration among the project team, including architects, engineers, contractors, and surveyors. Effective communication and coordination are crucial to ensure accurate documentation of the as-built conditions and a smooth transition from construction to facility management.
By following a systematic process and utilizing technologies, such as laser scanning or 3D modeling, the creation of As-Builts can be streamlined, providing an accurate representation of the completed project and facilitating effective project management.
Benefits of Using As-Builts in Construction
Utilizing As-Builts in the construction industry offers numerous benefits throughout the lifecycle of a building project. Here are some key advantages of using As-Builts:
- Accurate Documentation: As-Builts provide an accurate record of the actual as-built conditions, capturing any changes or modifications made during construction. This documentation ensures that all stakeholders have access to reliable and up-to-date information about the project’s final state.
- Effective Project Management: As-Builts serve as a reference for project management, allowing the project team to compare actual construction with the original plans. This helps identify any deviations, assess the impact on the project, and make informed decisions to ensure successful completion.
- Facility Maintenance and Management: As-Builts are a valuable resource for facility managers and maintenance teams. They provide accurate information about the building’s infrastructure, systems, components, and layouts. This knowledge facilitates effective maintenance planning, repairs, and renovations, ultimately extending the lifespan of the building.
- Streamlined Renovations and Retrofits: When modifications or renovations are required, As-Builts act as a foundation for efficient planning. By having an accurate record of the existing conditions, architects, engineers, and contractors can design and execute renovations more effectively, minimizing disruptions and optimizing resource utilization.
- Improved Communication and Collaboration: As-Builts serve as a common reference point for all project stakeholders. They facilitate communication and collaboration among architects, engineers, contractors, and other team members, ensuring a shared understanding of the project’s as-built conditions and reducing errors and misunderstandings.
- Compliance and Regulatory Requirements: Accurate As-Builts help ensure compliance with building codes, regulations, and legal requirements. By documenting any changes made during construction and incorporating them into the As-Built drawings, construction projects can meet regulatory standards and avoid potential legal issues.
- Cost and Time Savings: Utilizing As-Builts can result in cost and time savings throughout the project lifecycle. By having accurate documentation of the as-built conditions, construction teams can avoid rework, make more informed decisions, and streamline the construction process, ultimately reducing delays and minimizing costs.
Overall, the benefits of using As-Builts in construction are extensive, ranging from accurate documentation and improved project management to efficient facility maintenance, streamlined renovations, and compliance with regulations. Incorporating As-Builts into construction processes is crucial for achieving successful outcomes and long-term sustainability in the built environment.
As-builts in construction refer to the final set of drawings that reflect the actual conditions of the project. They are crucial for future renovations or maintenance.
Examples of As-Builts in Construction Projects
As-Builts are an essential part of construction projects, providing valuable insights into the as-built conditions of a building or structure. Here are a few examples of how As-Builts are used in different construction projects:
- Residential Construction: When constructing a residential property, As-Builts become crucial for documenting the exact placement of electrical outlets, plumbing fixtures, and HVAC systems. This documentation helps homeowners and contractors in the future when they need to locate and maintain these systems or make renovations to the property.
- Commercial Buildings: In the construction of office buildings, shopping malls, or hotels, As-Builts play a vital role in accurately documenting the layout and installation of various systems. This includes electrical wiring, fire suppression systems, water lines, and the positioning of structural elements. As-Builts ensure that the building’s infrastructure is correctly represented and can be easily accessed for maintenance or future expansion.
- Industrial Facilities: Industrial construction projects, such as manufacturing plants or warehouses, rely on As-Builts to document the intricate layout of heavy machinery, conveyors, and production lines. Accurate As-Builts with precise measurements and equipment specifications allow facility managers to optimize production workflows, plan for equipment upgrades or replacements, and ensure compliance with safety regulations.
- Infrastructure Projects: Large-scale infrastructure projects, such as bridges, roads, or tunnels, also benefit from As-Builts. These drawings document the actual dimensions, alignment, and construction details, ensuring that the built infrastructure matches the design specifications. As-Builts provide a valuable reference for future inspections, maintenance, and repair work, ensuring the safety and longevity of these structures.
- Historical Restoration: As-Builts are crucial in historical restoration projects where the goal is to preserve the authenticity and historical accuracy of a building. By creating accurate As-Builts, historians, architects, and restoration experts can understand and document the original construction techniques, materials used, and architectural details. As-Builts serve as a valuable resource in ensuring that the restoration work aligns with the building’s historical significance.
These are just a few examples of how As-Builts are utilized in construction projects. Whether it’s a residential, commercial, industrial, or infrastructure project, As-Builts serve as integral documents that accurately capture the actual as-built conditions. They provide a detailed and reliable reference for future maintenance, renovations, and historical preservation, ensuring the long-term success and integrity of the built environment.
Challenges and Limitations of As-Builts
While As-Builts are valuable in construction projects, there are certain challenges and limitations that need to be considered. Here are a few common challenges associated with As-Builts:
- Accuracy and Completeness: One of the main challenges is ensuring the accuracy and completeness of the As-Built documentation. Human error, misinterpretation of measurements, or missed changes during site verification can lead to discrepancies between the As-Builts and the actual as-built conditions. It is crucial to conduct thorough field surveys and validation checks to minimize inaccuracies.
- Timeliness: Creating accurate As-Builts requires time and effort, which can be a challenge, especially if there are tight project schedules or limited resources. Delays in the creation and approval of As-Builts can hinder the timely completion of a project, impacting subsequent phases of construction or facility management.
- Complexity of Information: As-Builts include a vast amount of information, ranging from architectural plans to electrical and plumbing layouts. Managing and organizing this complex information can be challenging, particularly when different disciplines and systems are involved. Proper documentation and a well-structured database are necessary to ensure easy retrieval and utilization of the As-Built information.
- Changes and Retrofits: As-Builts primarily capture the as-built conditions at the completion of a construction project. However, buildings often undergo changes, renovations, and retrofits throughout their lifespan. Keeping the As-Builts up-to-date with these modifications can be challenging, requiring ongoing documentation and revision of the drawings.
- Technology Limitations: While advanced technologies like laser scanning and 3D modeling have revolutionized the creation of As-Builts, there are still limitations. The cost of these technologies, the complexity of data processing, and the learning curve associated with their implementation can pose challenges for smaller projects or less technologically advanced teams.
- Communication and Collaboration: As-Builts involve multiple stakeholders, including architects, engineers, contractors, and facility managers. Effective communication and collaboration among these parties are essential to ensure the accuracy and completeness of the As-Built documentation. Challenges can arise when there are breakdowns in communication, misunderstandings, or discrepancies in the interpretation of the as-built conditions.
Despite these challenges and limitations, it is important to understand and address them proactively to maximize the benefits of As-Builts. By implementing proper quality control processes, utilizing technology effectively, fostering collaboration, and updating As-Builts regularly, these challenges can be mitigated, ensuring that the documentation accurately represents the actual as-built conditions of a construction project.
Best Practices for Managing As-Builts
Effectively managing As-Built documentation is crucial to ensure its accuracy, accessibility, and usability throughout the lifecycle of a construction project. Here are some best practices for managing As-Builts:
- Start Early: As-Builts should be considered from the start of a construction project. Incorporate As-Built requirements and processes into the project timeline, ensuring that the necessary resources and expertise are allocated for accurate documentation.
- Standardize Drawing Formats: Establish clear standards for As-Built drawings, including symbols, notations, and drawing conventions. This ensures consistency and easy interpretation of the documentation by all stakeholders involved in the project.
- Implement Quality Control Checks: Conduct regular quality control checks throughout the As-Built creation process. This involves reviewing and verifying the accuracy and completeness of the information captured during field surveys and site verifications.
- Utilize Technology: Leverage advanced technologies, such as laser scanning, 3D modeling, and Building Information Modeling (BIM), to streamline the creation and management of As-Builts. These technologies enhance accuracy, speed up data collection, and facilitate collaboration among project teams.
- Establish a Document Management System: Implement a robust document management system to organize and store the As-Built documentation. Utilize digital platforms or cloud-based solutions to ensure easy access, searchability, version control, and efficient collaboration.
- Update As-Builts Regularly: As-Builts should be updated regularly to reflect any changes, modifications, or renovations made to the building or structure. Establish a process for updating the drawings promptly when modifications occur, ensuring that the documentation remains accurate and relevant.
- Ensure Communication and Collaboration: Foster effective communication and collaboration among the project team, including architects, engineers, contractors, and facility managers. Establish clear channels of communication and regular meetings to discuss As-Built updates, revisions, and any discrepancies that may arise.
- Train and Educate Team Members: Provide training and education to project team members on the importance of As-Builts and the proper procedures for creating and managing them. This ensures that everyone involved understands the significance of accurate documentation and follows the established processes.
- Share and Archive As-Builts: Share the final As-Built documentation with relevant stakeholders, such as facility managers, maintenance teams, and future owners of the building. Additionally, establish an archival system to safely store the As-Builts for future reference, ensuring their availability throughout the lifespan of the construction project.
By implementing these best practices, construction projects can effectively manage As-Built documentation, ensuring accuracy, accessibility, and usability. Proper planning, standardized processes, utilization of technology, regular updates, and strong communication among team members contribute to the success of As-Built management and its long-term value for the project.
Conclusion
As-Builts are an essential component of construction projects, capturing the accurate as-built conditions of a building or structure. They provide valuable documentation that serves as a reference for project management, facility maintenance, renovations, compliance, and historical preservation.
Throughout this article, we’ve explored the definition, importance, process, benefits, challenges, and best practices associated with As-Builts in the construction industry. As-Builts offer accurate documentation of changes, facilitate efficient project management, enable effective facility maintenance, streamline renovations and retrofits, ensure compliance, and result in cost and time savings.
However, it is important to acknowledge the challenges and limitations of As-Builts, such as accuracy, completeness, timeliness, complexity, technology limitations, and communication issues. By being aware of these challenges and implementing best practices, construction projects can mitigate risks and maximize the usability and value of As-Built documentation.
In conclusion, incorporating As-Builts into construction processes is crucial for accurate record-keeping, enhanced collaboration, and efficient project and facility management. By capturing the as-built conditions and maintaining updated documentation, construction projects can achieve long-term sustainability, compliance, and successful outcomes in the ever-evolving construction industry.
Frequently Asked Questions about What Does As-Builts Mean In Construction
Was this page helpful?
At Storables.com, we guarantee accurate and reliable information. Our content, validated by Expert Board Contributors, is crafted following stringent Editorial Policies. We're committed to providing you with well-researched, expert-backed insights for all your informational needs.
0 thoughts on “What Does As-Builts Mean In Construction”