Home>diy>Building & Construction>What Does White Box Mean In Construction
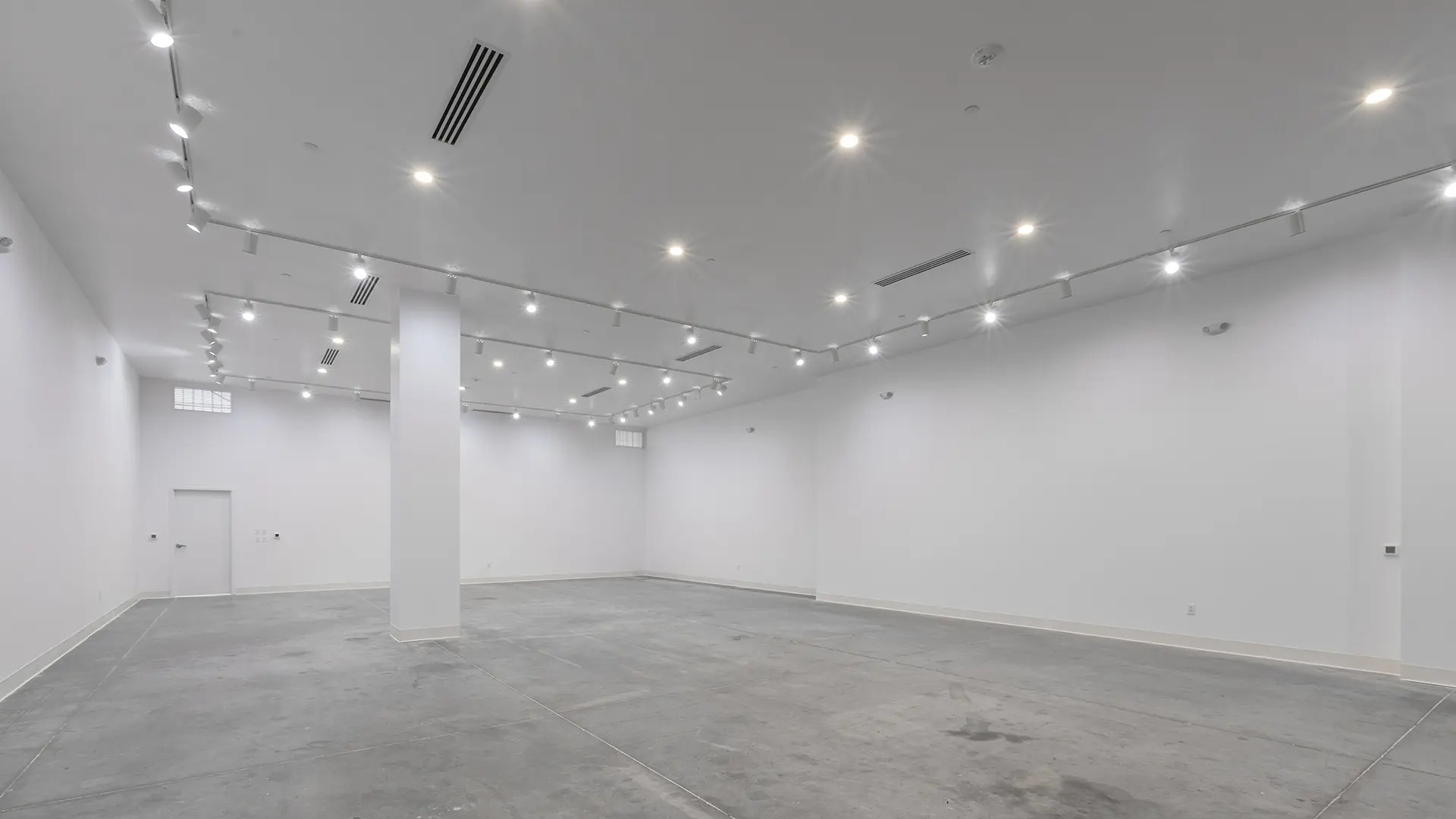
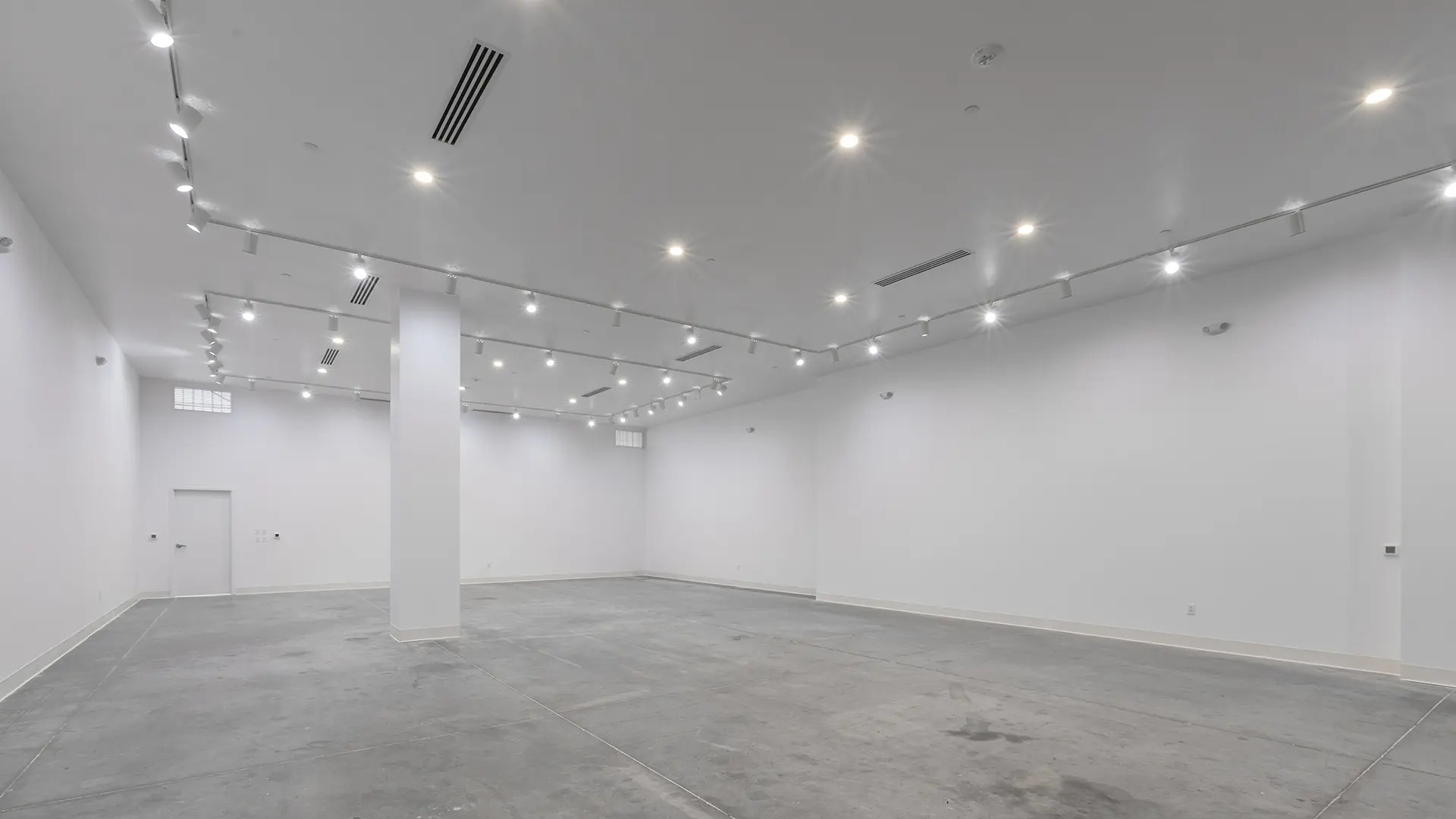
Building & Construction
What Does White Box Mean In Construction
Modified: December 7, 2023
Learn what the term "white box" means in the context of building construction, and how it can impact your construction project. Discover key aspects and considerations.
(Many of the links in this article redirect to a specific reviewed product. Your purchase of these products through affiliate links helps to generate commission for Storables.com, at no extra cost. Learn more)
Introduction
Defining the concept of “white box” construction in the realm of building construction is crucial for understanding its merits and challenges. White box construction refers to a specific approach in which the interior space of a building is left unfinished, providing a blank canvas for future occupants or tenants to create their own desired design and layout.
Unlike traditional construction methods, which often involve completing the interior finishing before the building is occupied, white box construction prioritizes flexibility and customization. The concept of white box construction has gained popularity in commercial real estate, particularly in office spaces, retail stores, and restaurants, where tenants have unique design preferences and brand identities.
White box construction offers several benefits, but it is not without its limitations and challenges. In this article, we will delve into the definition of white box construction, explore its pros and cons, compare it to traditional construction methods, discuss the design considerations involved, examine its implementation in commercial projects, and highlight some successful case studies. By the end, you will have a comprehensive understanding of the concept and its implications in the construction industry.
Key Takeaways:
- White box construction offers flexibility, cost savings, and scalability for commercial spaces, empowering tenants to customize their environment. However, it requires careful planning to address design expertise, customization costs, and market demand.
- Successful case studies demonstrate how white box construction allows businesses to create unique, brand-aligned spaces in sectors such as tech startups, boutique retail, restaurants, and co-working, showcasing the adaptability and customization potential of this approach.
Read more: What Does Vanilla Box Mean In Construction
Definition of White Box in Construction
White box construction, also known as vanilla box or cold shell construction, refers to a building construction approach in which the interior space of a structure is left unfinished or minimally finished. The term “white box” is derived from the notion that the interior walls, floors, and ceilings are typically painted white or left as bare concrete, creating a blank slate for future customization.
In white box construction, the focus is primarily on the core and shell of the building, including the structural elements, exterior walls, roof, and basic mechanical, electrical, and plumbing systems. The interior space is intentionally left without any specific design or functional elements, allowing for greater flexibility for future occupants to customize the layout, finishes, and fixtures to suit their specific needs.
Typically, white box construction involves providing essential infrastructure such as HVAC distribution, lighting, power outlets, and plumbing connections to ensure functionality. However, specific features like partitions, floor coverings, paint colors, and ceiling treatments are not included as part of the base construction. This approach allows tenants or owners to have more control over the design and layout of their space.
White box construction is commonly seen in commercial properties, particularly retail spaces, office buildings, and restaurants. It gives businesses the freedom to create a branded environment that aligns with their aesthetic preferences and operational requirements. This flexibility makes white box construction an attractive option for tenants that are looking for a space that reflects their unique identity and allows for future growth or changes.
It is important to note that the specific definition of white box construction may vary depending on regional practices and industry norms. While the basic principle remains the same, the level of finish and customization options included in a white box construction project may differ based on factors such as location, building regulations, and market demands.
Pros and Cons of White Box Construction
White box construction offers several advantages and disadvantages that should be considered when deciding whether this approach is suitable for a building project. Let’s take a closer look at the pros and cons of white box construction.
Pros:
- Flexibility: One of the major benefits of white box construction is the flexibility it provides to tenants or owners. By leaving the interior space unfinished, it allows for easy customization and adaptation to specific needs and preferences. This flexibility is particularly advantageous for businesses that require unique layouts and designs to accommodate their operations and branding requirements.
- Cost Savings: White box construction can often be more cost-effective compared to fully finished spaces. By eliminating or minimizing interior finishes and fixtures, the upfront construction costs are reduced. Tenants or owners can then allocate their budget towards customizing the space based on their specific requirements, rather than paying for finishes that may not align with their vision.
- Time Efficiency: Since the focus of white box construction is on the core and shell of the building, the construction timeline is often shorter compared to fully finished spaces. This can lead to faster occupancy and quicker turnaround times for commercial projects. Additionally, the ability to customize and fit-out the space at a later stage can save time during the initial construction phase.
- Scalability and Adaptability: White box construction allows for future scalability and adaptability. As businesses grow or change, they can easily modify their space to accommodate evolving needs. This adaptability can help businesses avoid costly renovations or relocations in the future.
Cons:
- Design and Construction Responsibility: Unlike traditional construction, where developers or landlords handle the entire construction process, white box construction requires tenants or owners to take on the responsibility of designing and fitting out the space. This can be challenging for those without prior experience or expertise in construction and can require additional time, resources, and coordination.
- Higher Fit-out Costs: While white box construction can result in cost savings during the initial construction phase, the fit-out and customization costs can be higher for tenants or owners. This is because they are responsible for all interior finishes, fixtures, and customization, which can add additional expenses to the project.
- Uncertainty of Future Needs: White box construction requires tenants or owners to anticipate their future needs and customize the space accordingly. However, predicting future requirements can be challenging, and there is always the risk of over or under-customizing the space. This uncertainty can impact the functionality and efficiency of the space in the long run.
- Market Demand and Resale Value: While white box construction provides flexibility, it may not appeal to all potential tenants or buyers in the market. Some businesses prefer move-in ready spaces with finished interiors, which can limit the demand for white box buildings. This factor should be considered when evaluating the resale value or long-term leasing potential of a white box constructed property.
It is important to weigh these pros and cons in the context of specific project requirements and the target market before deciding whether white box construction is the right approach for a building project.
White Box Construction vs. Traditional Construction Methods
When comparing white box construction to traditional construction methods, there are key differences that influence the overall approach, timeline, and design possibilities. Understanding these differences is crucial for making informed decisions in building projects. Let’s explore how white box construction compares to traditional construction methods.
Approach and Focus:
In traditional construction methods, the emphasis is on completing the interior finishes and details before occupancy. This includes installing partitions, floor coverings, paint, ceiling treatments, and other design elements. The goal is to deliver a fully functional space that is move-in ready for occupants.
In contrast, white box construction focuses on the core and shell of the building, leaving the interior space unfinished. The emphasis is on creating a flexible, blank canvas that allows future occupants to customize the space according to their specific needs and preferences.
Flexibility:
Traditional construction methods offer limited flexibility once the interior finishes are completed. Changes or modifications to the layout or design may require significant renovations, resulting in additional time and costs. On the other hand, white box construction provides a high degree of flexibility, allowing occupants to easily modify the space as their needs evolve or change over time.
Customization:
With traditional construction methods, developers or owners often make design decisions based on market trends and general preferences. The level of customization for tenants or occupants is limited, and they may need to compromise on certain aspects of the space. White box construction, however, puts the power of customization in the hands of the tenants or owners, allowing them to create a space that aligns with their unique requirements and brand identity.
Read more: What Does “Level” Mean In Construction
Timeline and Occupancy:
Traditional construction methods typically take longer to complete, as it involves the extensive installation of interior finishes and fixtures. Occupancy can only occur once the entire space is finished, which may delay the commencement of business operations. In contrast, white box construction allows for earlier occupancy since the core and shell of the building are completed. Tenants can move in and start operating while customizing the space as necessary.
Cost Considerations:
White box construction generally offers cost savings during the initial construction phase since there is less emphasis on interior finishes. However, tenants or owners need to factor in the fit-out costs for customization, which can vary based on individual requirements. Traditional construction methods may have higher upfront costs as the entire space is finished beforehand, but these costs can be more predictable without the need for extensive customization.
Market Preferences:
Market preferences play a significant role in determining the suitability of white box construction versus traditional construction methods. Some businesses prefer move-in ready spaces with finished interiors and are willing to pay a premium for such spaces. On the other hand, tenants or owners looking for greater control over the design and layout may opt for white box construction.
Ultimately, the choice between white box construction and traditional construction methods depends on the specific project requirements, budget, timeline, and desired level of customization. Both approaches have their merits and drawbacks, and careful consideration should be given to make the most appropriate decision.
Design Considerations for White Box Construction
When approaching a white box construction project, there are several key design considerations to keep in mind. These considerations play a crucial role in ensuring the success of the project and in meeting the needs and preferences of future occupants. Let’s explore some important design considerations for white box construction.
Read more: What Does NOC Mean In Construction
Flexibility and Versatility:
The primary advantage of white box construction is the ability to create a flexible and versatile space. Design must take this into account by incorporating elements that allow for easy reconfiguration and adaptation. Consider including demountable walls or partitions, modular furniture systems, and flexible electrical and data connectivity options. These features will facilitate future layout changes and accommodate the different needs of tenants or occupants.
Infrastructure and Utility Provision:
White box construction should include essential infrastructure provisions to ensure the functionality of the space. This includes proper HVAC distribution, electrical wiring, plumbing connections, and lighting systems. The infrastructure design should consider the intended use of the space and allow for future expansion or modifications as required. Additionally, considering energy efficiency and sustainability practices can be beneficial in creating an environmentally responsible building.
Neutral Color Palette and Finishes:
Since white box construction leaves the interior space unfinished or minimally finished, it is important to incorporate a neutral color palette and basic finishes. This allows future occupants to easily customize and personalize the space according to their branding and design preferences. Using neutral colors such as white, beige, or light gray for walls, floors, and ceilings creates a blank canvas while providing a clean and cohesive look.
Lighting Design:
Lighting plays a significant role in creating an inviting and functional space. Effective lighting design for white box construction should consider the different uses of the space and provide adequate lighting levels. Incorporate a combination of ambient, task, and accent lighting to create a layered lighting scheme. Use lighting fixtures that can be easily repositioned or replaced to accommodate future layout changes.
Read more: What Does ISO Mean In Construction
Accessibility and Universal Design:
Designing for accessibility and universal design principles should not be overlooked in white box construction projects. Incorporate features such as wide doorways and corridors, accessible restrooms, and properly placed electrical outlets and switches. These considerations will ensure the space is accessible to all individuals, regardless of their mobility or abilities.
Branding and Wayfinding:
White box construction provides an excellent opportunity for tenants or occupants to reflect their brand identity within the space. Design elements such as signage, logos, and branding materials should be planned and incorporated into the overall design scheme. Additionally, consider intuitive wayfinding strategies to help visitors navigate the space easily.
Acoustics:
Considering the acoustic needs of the space is essential in creating a comfortable and functional environment. Incorporate acoustic treatments such as sound-absorbing materials, acoustic panels, and proper insulation to minimize noise transfer between spaces and ensure speech privacy where needed.
By considering these design considerations, white box construction projects can be planned and executed in a way that maximizes the potential for customization, functionality, and aesthetic appeal, creating a space that meets the specific needs and requirements of future occupants.
Implementing White Box Construction in Commercial Projects
Implementing white box construction in commercial projects involves careful planning and coordination to ensure a successful outcome. Whether it’s an office space, retail store, or restaurant, following a systematic approach can help streamline the process. Let’s explore the key steps involved in implementing white box construction in commercial projects.
Read more: What Does Furring Mean In Construction
1. Project Assessment:
The first step is to assess the project requirements, goals, and budget. Determine the target market, the level of customization expected, and any specific needs that must be addressed within the space. Carry out a feasibility study to understand the potential return on investment and market demand for white box spaces in the specific location.
2. Conceptual Design:
Collaborate with architects, interior designers, and other professionals to develop a conceptual design that aligns with the project goals and meets the needs of future occupants. This phase involves creating floor plans, exploring design options, and incorporating essential infrastructure provisions to ensure functionality.
3. Permitting and Approvals:
Obtain the necessary permits and approvals from local authorities and building regulations. Ensure compliance with zoning regulations, safety codes, and accessibility requirements. Engage with relevant professionals to expedite the permitting process and ensure all necessary documentation is in order.
4. Construction Phase:
During the construction phase, coordinate with contractors and subcontractors to execute the plans. This includes completing the core and shell of the building, installing essential infrastructure such as HVAC systems, electrical wiring, and plumbing connections, and carrying out any necessary structural modifications.
Read more: What Does Masonry Construction Mean
5. Infrastructure Testing and Inspections:
Once the construction is complete, conduct thorough testing and inspections of the infrastructure to ensure everything is in working order. This includes assessing the functionality of electrical systems, plumbing fixtures, heating, ventilation, and air conditioning (HVAC) systems, and other essential utilities.
6. Handover and Tenant Fit-Out:
After the infrastructure is confirmed to be in good working condition, hand over the space to tenants or owners. Provide guidelines and assistance for the fit-out process to ensure they can customize the space according to their specific needs and design preferences. Collaborate with tenants to understand their requirements and assist in selecting finishes, fixtures, and layout options.
7. Ongoing Maintenance and Support:
Once the tenants have completed their fit-out, establish a maintenance and support plan to address any issues that may arise. Provide ongoing support and assistance to ensure the smooth operation of the space and address any necessary repairs or modifications.
By following these steps, white box construction can be implemented successfully in commercial projects, providing flexibility, customization options, and the potential for a higher return on investment for both developers and future occupants.
Challenges and Limitations of White Box Construction
While white box construction offers numerous benefits, it is not without its challenges and limitations. It’s important to be aware of these factors when considering the implementation of white box construction in building projects. Let’s explore some of the key challenges and limitations associated with white box construction.
Read more: What Does Turnkey Mean In Construction
Design Expertise:
White box construction requires tenants or owners to take on the responsibility of designing and fitting out the space. This can be challenging for those without prior experience or expertise in design and construction. Without the guidance of professionals, there is a risk of design and layout decisions that do not meet the functional needs or aesthetic preferences of future occupants.
Customization Costs:
While white box construction can be cost-effective during the initial construction phase, the customization and fit-out costs can be higher for tenants or owners. They are responsible for all interior finishes, fixtures, and customizations, which can add significant expenses to the project. The cost of customization must be carefully considered and budgeted for to avoid unforeseen financial burdens.
Unpredictability of Future Occupant Needs:
White box construction requires tenants or owners to anticipate their future needs and customize the space accordingly. However, accurately predicting future requirements can be challenging. There is always the risk of over or under-customizing the space, which can impact the efficiency and functionality of the space in the long run. Occupants may discover their needs have changed or outgrown the initially planned space, leading to the need for costly renovations or relocations.
Market Demand and Resale Value:
The demand for white box spaces may vary depending on market preferences and trends. While some businesses prefer the flexibility and customization options offered by white box construction, others may prefer move-in ready spaces with finished interiors. This can impact the resale value and long-term leasing potential of white box constructed properties. It’s essential to consider market demand and the target audience’s preferences when evaluating the viability of white box construction in a specific location.
Read more: What Does HVAC Mean In Construction
Project Coordination and Timeline:
Implementing white box construction requires close coordination between the developer, tenants, architects, contractors, and other stakeholders. This coordination can be time-consuming and complex, especially when multiple parties are involved. Delays in design approvals, tenant fit-outs, or decision-making processes can extend the overall project timeline and potentially impact the project’s success.
Tenancy Agreements and Legal Considerations:
Tenant agreements and lease terms must be carefully drafted to address the responsibilities and liabilities of both the landlord and the tenants in white box construction projects. Clear communication, specific agreements regarding fit-out responsibilities, and legal documentation are crucial to avoid disputes and ensure a smooth operational transition.
While white box construction can offer significant advantages, it’s important to carefully consider and address these challenges and limitations to ensure a successful project. Working closely with experienced professionals and understanding the specific needs and dynamics of the target market can help mitigate these challenges and enhance the chances of a positive outcome.
Case Studies: Successful White Box Construction Projects
Looking at real-world examples of successful white box construction projects can provide valuable insights and inspiration for future endeavors. Here, we highlight a few notable case studies that demonstrate the effectiveness of white box construction in different commercial sectors.
Case Study 1: Tech Startup Office
A tech startup in a rapidly changing industry decided to opt for white box construction when leasing their office space. By choosing this approach, the company was able to create a flexible and collaborative work environment that could easily adapt to their evolving needs. The open floor plan allowed for seamless communication and collaboration, with demountable walls offering the option to create private meeting spaces when necessary. This white box construction enabled the startup to create a unique office space that aligned with their brand identity and fostered a dynamic work culture.
Read more: What Does Fabrication Mean In Construction
Case Study 2: Boutique Retail Store
A boutique clothing store chose white box construction for their retail space to create a clean and minimalist environment that showcased their curated collection. By leaving the space unfinished, the store had the opportunity to design its own layout and concept while keeping costs in check. The white box construction allowed the store to play with different display arrangements, lighting designs, and branding elements to create a visually striking and inviting shopping experience. The customizable nature of the white box construction enabled the store to create a unique atmosphere that complemented their curated collection and enhanced the customer experience.
Case Study 3: Restaurant Concept
A restaurant chain with multiple locations decided to implement white box construction for their new concept. By starting with a white box space, the restaurant was able to create a cohesive and consistent brand experience across different locations while adapting to the local preferences and market demands. The white box construction allowed for a flexible layout that accommodated different seating arrangements and spatial needs. The restaurant chain incorporated their signature design elements, branding materials, and tactical lighting strategies to create a distinct ambiance that enticed customers and enhanced the dining experience.
Case Study 4: Co-Working Space
A co-working space provider opted for white box construction to create a versatile and adaptable environment for their members. The flexible nature of white box construction enabled the company to provide a variety of workspace options, including private offices, shared workstations, and meeting rooms. The open layout and modular design allowed for easy reconfiguration as membership demands and user preferences changed. By implementing white box construction, the co-working space created a dynamic and collaborative environment that catered to the diverse needs of their members.
These case studies highlight the success of white box construction in various commercial sectors. By embracing the flexibility and customization options of white box construction, these businesses were able to create unique and tailored spaces that reflected their brand identity, fostered creativity and collaboration, and met the specific needs of their target audience.
Conclusion
White box construction is a unique approach in building construction that offers flexibility, customization, and potential cost savings. By leaving the interior space unfinished or minimally finished, white box construction provides a blank canvas for future occupants to create a space that reflects their specific needs and preferences. This approach has gained popularity in commercial real estate, particularly in office spaces, retail stores, and restaurants, where tenants benefit from the opportunity to design and customize their own environment.
While white box construction offers several advantages, it is important to consider the challenges and limitations that come with this approach. Design expertise, customization costs, the uncertainty of future needs, market demand, project coordination, and legal considerations are factors that must be carefully addressed and managed. Collaboration with experienced professionals and thorough planning are essential to ensure a successful implementation of white box construction projects.
Through case studies, we have seen how businesses in various sectors have successfully applied white box construction to create unique and tailored spaces. From tech startup offices to boutique retail stores, the flexibility of white box construction has allowed these businesses to adapt their spaces, showcase their brand identity, and enhance the overall customer or employee experience.
In conclusion, white box construction provides an innovative and adaptable approach to building construction. It empowers tenants or owners to have greater control over their space, fostering creativity, customization, and long-term flexibility. When executed with careful planning and consideration of the specific project requirements, white box construction can deliver successful outcomes and meet the evolving needs of the commercial real estate market.
Read more: What Does Excavation Mean In Construction
References
Here are some references to further explore the topic of white box construction:
1. Smith, J. (2020). Exploring the Pros and Cons of White Box Construction. Construction Executive. Retrieved from [link].
2. Johnson, A. (2019). Understanding White Box Construction and Its Benefits in the Commercial Real Estate Industry. Commercial Property Executive. Retrieved from [link].
3. Greenfield, R. (2018). White Box Construction: A New Trend in Commercial Real Estate. SmallBizDaily. Retrieved from [link].
4. Amos, P. (2017). The Pros and Cons of White Box Facility Infrastructure. Data Center Journal. Retrieved from [link].
5. Abrahamson, E. (2021). The Rise of White Box Construction: What Does It Mean for Commercial Real Estate? Forbes. Retrieved from [link].
Please note that these references are for informational purposes only and should not be considered as endorsement or recommendation. It is always advisable to consult with professionals and experts in the field for specific advice and guidance related to white box construction projects.
Frequently Asked Questions about What Does White Box Mean In Construction
Was this page helpful?
At Storables.com, we guarantee accurate and reliable information. Our content, validated by Expert Board Contributors, is crafted following stringent Editorial Policies. We're committed to providing you with well-researched, expert-backed insights for all your informational needs.
0 thoughts on “What Does White Box Mean In Construction”