Home>Articles>What Is The Ideal Co2 Ne Pressure Setting For A Kegerator
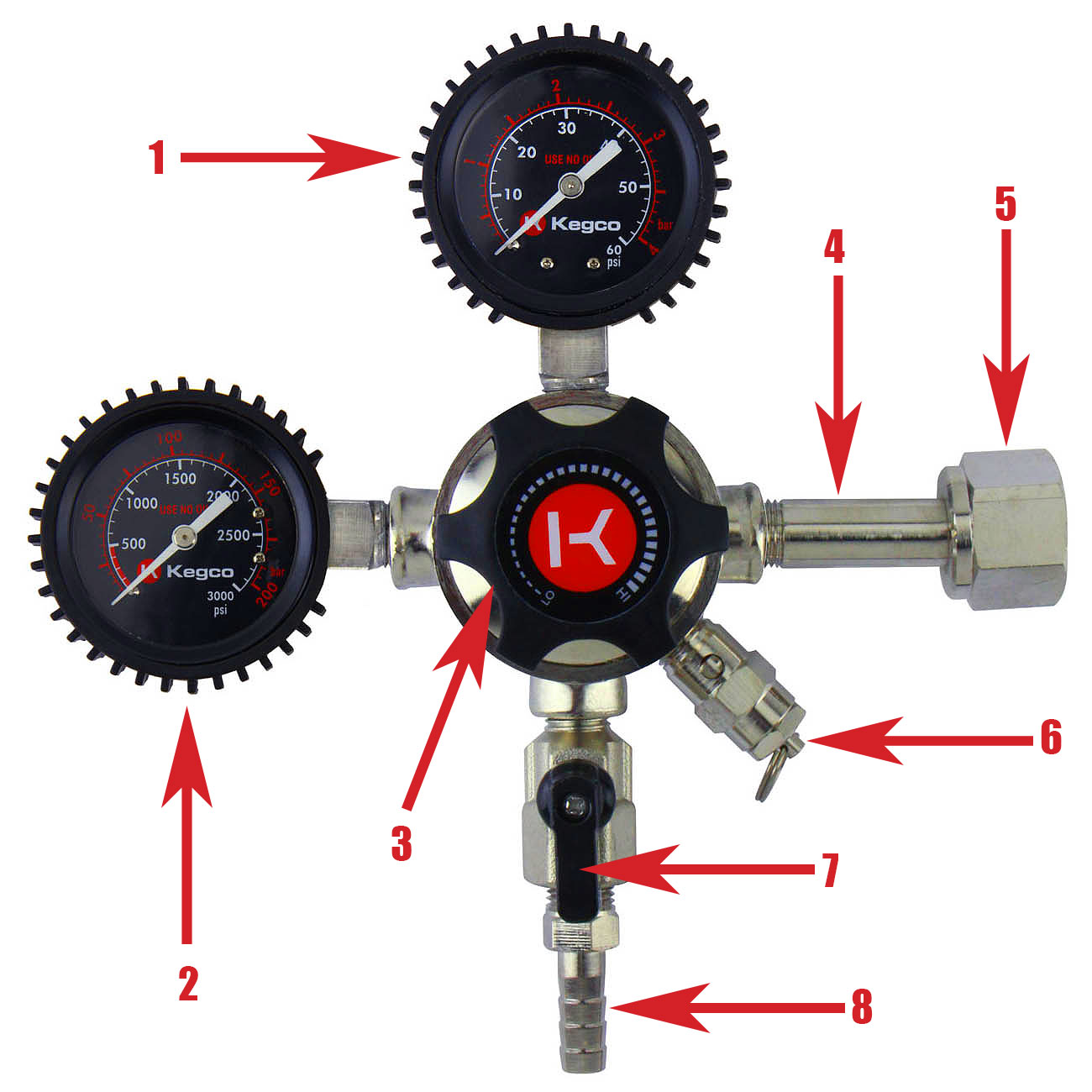
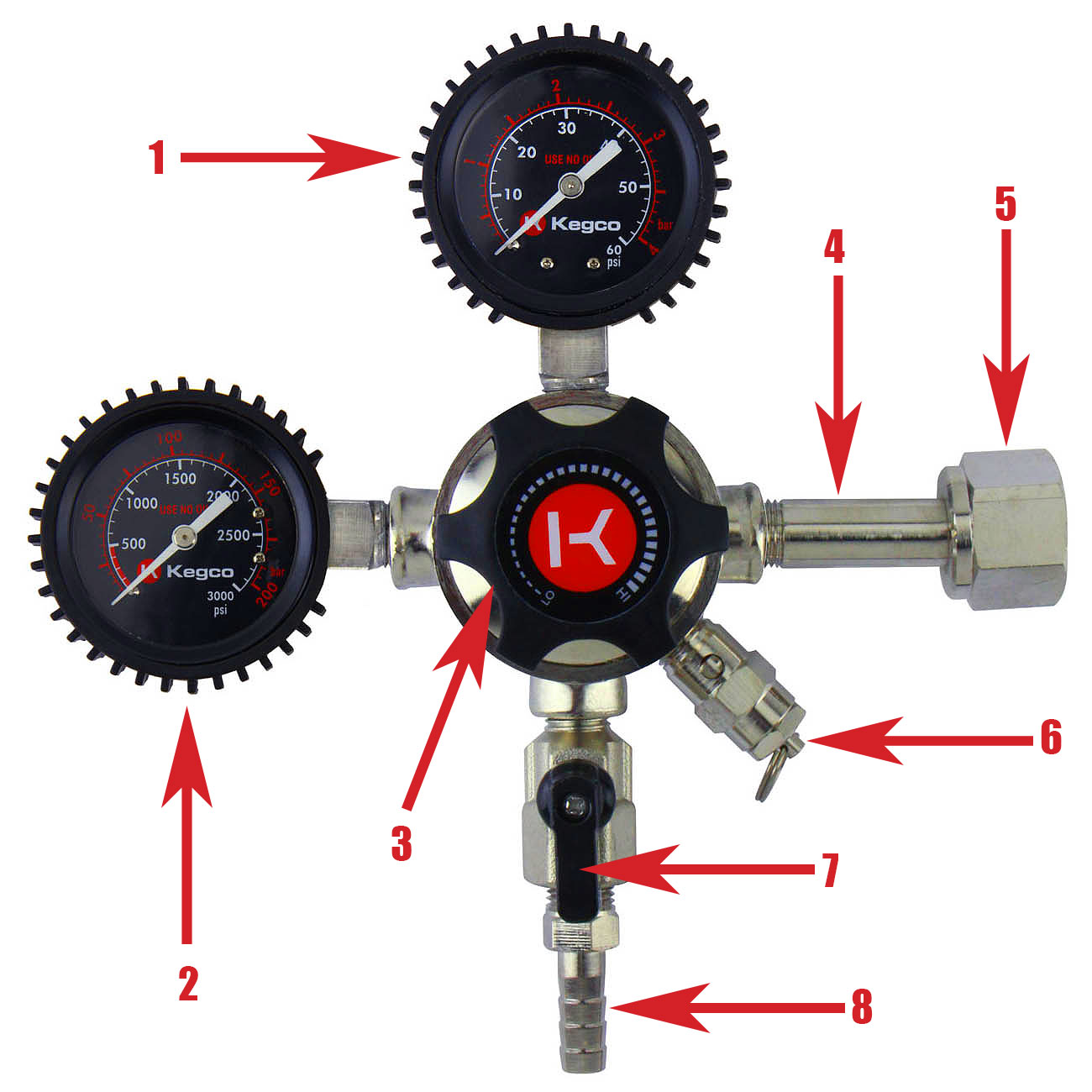
Articles
What Is The Ideal Co2 Ne Pressure Setting For A Kegerator
Modified: August 24, 2024
Discover the ideal CO2 pressure for your kegerator setup with our informative articles. Get expert advice and maintain the perfect carbonation for your draft beer.
(Many of the links in this article redirect to a specific reviewed product. Your purchase of these products through affiliate links helps to generate commission for Storables.com, at no extra cost. Learn more)
Introduction
Welcome to the world of kegerators, where beer enthusiasts can enjoy their favorite brews on tap, right in the comfort of their own homes. However, to achieve that perfect pour and optimal carbonation, it’s crucial to understand and regulate the CO2 pressure in your kegerator.
CO2 pressure plays a vital role in carbonating and dispensing beer from a kegerator. Too much pressure can result in over-carbonated, foamy beer, while too little pressure can lead to under-carbonated, flat beer.
In this article, we will dive into the details of CO2 pressure for kegerators. We will explore the factors that affect CO2 pressure, discuss the ideal pressure settings, provide tips on adjusting and maintaining pressure, as well as troubleshoot common issues that may arise.
So, whether you are a homebrewer or a beer enthusiast looking to master the art of pouring draft beer, understanding CO2 pressure in your kegerator is essential for achieving that perfect pint.
Key Takeaways:
- Mastering CO2 pressure is crucial for perfect draft beer at home. Understand factors, adjust pressures, and troubleshoot issues for an optimal pouring experience.
- Ideal CO2 pressure ranges for carbonation and dispensing ensure a balanced pour. Experiment, adjust, and maintain pressures for the perfect pint every time.
Read more: How To Build A Co2 Kegerator
Understanding CO2 Pressure for Kegerators
CO2 pressure is a critical factor in the carbonation and dispensing process of beer in kegerators. It determines the amount of carbonation dissolved in the beer and regulates the flow of beer from the keg to the tap. To effectively understand CO2 pressure in kegerators, let’s break it down into two key components: carbonation pressure and dispensing pressure.
Carbonation Pressure
Carbonation pressure refers to the pressure at which CO2 is added to the beer to achieve optimal carbonation levels. When a keg is initially filled, the beer is typically flat, lacking the desired amount of carbonation. To carbonate the beer, CO2 is forced into the keg under pressure.
The carbonation process is influenced by several factors, including temperature and desired carbonation level. Generally, the colder the beer, the higher the pressure needed to achieve proper carbonation. Different beer styles may also require varying carbonation levels, which can be achieved by adjusting the pressure accordingly.
Dispensing Pressure
Dispensing pressure, on the other hand, refers to the pressure required to push the carbonated beer from the keg to the tap. This pressure needs to be carefully controlled to ensure a steady flow of beer without excessive foaming or loss of carbonation.
Dispensing pressure is affected by factors such as the length and diameter of the beer lines, the height and temperature of the kegerator, and the desired pouring rate. These variables impact the resistance to flow and must be considered when determining the ideal dispensing pressure.
By understanding and adjusting both carbonation and dispensing pressures, you can achieve the perfect balance of carbonation and a smooth pour, enhancing the overall beer-drinking experience.
Factors Affecting CO2 Pressure
Several factors can influence the CO2 pressure in a kegerator. Understanding these factors is crucial for maintaining the desired carbonation levels and a consistent flow of beer. Let’s take a closer look at the key factors that can affect CO2 pressure:
Read more: How Adjust Co2 Kegerator
Temperature
Temperature plays a significant role in CO2 pressure regulation. As temperature increases, CO2 becomes more soluble in beer, leading to an increase in pressure. Conversely, as temperature decreases, CO2 becomes less soluble, resulting in a decrease in pressure. It is important to monitor and control the temperature of the kegerator to maintain the desired carbonation level and pressure.
Degree of Carbonation
The desired level of carbonation for different beer styles can vary. Beers with higher carbonation levels require higher CO2 pressures, while beers with lower carbonation levels require lower pressures. Understanding the specific carbonation requirements for each beer style is essential to set the appropriate CO2 pressure.
Keg Volume
The volume of beer remaining in the keg can impact the CO2 pressure. As the beer is consumed, the pressure inside the keg decreases. It is important to monitor the beer level and adjust the CO2 pressure accordingly to ensure consistent carbonation and dispensing pressure throughout the life of the keg.
Beer Line Length and Diameter
The length and diameter of the beer lines can affect the resistance to flow and impact the required dispensing pressure. Longer lines or lines with smaller diameters create more resistance, necessitating higher pressures for proper beer flow. Conversely, shorter lines or larger diameter lines require lower pressures. It is crucial to consider the specific characteristics of the beer lines when setting the optimal CO2 pressure for dispensing.
Read more: Where To Get Co2 For A Kegerator
Kegerator Elevation and Ambient Temperature
The elevation of the kegerator and the ambient temperature can influence CO2 pressure. Higher elevations and warmer ambient temperatures tend to decrease the pressure, while lower elevations and cooler temperatures increase the pressure. These factors should be taken into account when adjusting the CO2 pressure to achieve the desired carbonation and dispensing results.
By considering and adjusting these factors accordingly, you can maintain the appropriate CO2 pressure for your kegerator and ensure optimal carbonation and dispensing performance for a perfect beer drinking experience.
Ideal CO2 Pressure for Kegerators
Setting the ideal CO2 pressure for your kegerator is crucial to maintain the perfect carbonation and dispensing experience. While the specific pressure may vary depending on factors such as beer style and personal preference, there are generally accepted guidelines to help you achieve the desired results. Here are some considerations for determining the ideal CO2 pressure:
Carbonation Pressure
The carbonation pressure is crucial for achieving the desired level of carbonation in your beer. The ideal carbonation pressure typically ranges between 8 and 14 pounds per square inch (psi). However, this can vary depending on the beer style and your personal preference. Lighter beers, such as lagers, usually require higher pressures, while darker and heavier beers, like stouts, may require lower pressures. It’s important to refer to the specific recommendations for each beer style and adjust accordingly.
Dispensing Pressure
The dispensing pressure is essential for ensuring a smooth and controlled flow of beer without excessive foaming or loss of carbonation. The ideal dispensing pressure is typically between 6 and 12 psi. However, this can also vary based on factors like the length and diameter of the beer lines, the temperature of the kegerator, and personal preference. Start with a lower pressure and gradually increase until you achieve the desired flow rate and carbonation levels.
Read more: What Size Co2 Tank For A Kegerator Nostalgia
Trial and Error
While there are general guidelines for CO2 pressure, it’s important to note that every kegerator setup and beer style may require slight adjustments. Achieving the perfect CO2 pressure may involve some trial and error. Start with the recommended pressures mentioned above, and then make slight adjustments based on taste and carbonation levels. Take note of the changes made and their impact on the beer’s flavor and carbonation so that you can fine-tune your kegerator setup over time.
Remember, the ideal CO2 pressure is a balance between carbonation and dispensing. It should deliver a properly carbonated beer while ensuring a smooth pour with minimal foaming. Keep in mind that personal preference plays a role in determining the ideal pressure, so don’t be afraid to experiment until you find the perfect settings for your kegerator.
By understanding the guidelines for carbonation and dispensing pressures and making adjustments based on experimentation and taste, you can find the ideal CO2 pressure for your kegerator, allowing you to enjoy a perfectly carbonated and delicious draft beer at home.
How to Adjust CO2 Pressure in a Kegerator
Adjusting the CO2 pressure in your kegerator is key to achieving optimal carbonation and dispensing. Whether you need to increase or decrease the pressure, here are the steps to effectively adjust the CO2 pressure:
Step 1: Evaluate the Current Pressure
Before making any adjustments, it’s important to understand the current CO2 pressure in your kegerator. Use a pressure gauge or regulator to measure the existing pressure. This will serve as a baseline for any adjustments you plan to make.
Step 2: Determine the Desired Pressure
Consider the desired carbonation and dispensing pressures for your specific beer style and personal preference. Consult brewing guidelines or resources for recommended pressure ranges. This will help you determine the target pressure for your kegerator.
Read more: How To Change Co2 Tank In Kegerator
Step 3: Adjust the Regulator
Locate the CO2 regulator on your kegerator, which is typically attached to the CO2 tank. Using the appropriate tools, adjust the regulator by turning the adjustment screw or dial. Turning clockwise will increase the pressure, while turning counterclockwise will decrease it.
Step 4: Monitor the Pressure and Carbonation
After making adjustments to the regulator, allow some time for the pressure to stabilize and the carbonation to adjust. Check the pressure gauge or regulator periodically to ensure it matches the desired pressure. Additionally, regularly check the carbonation level of the beer by pouring a small sample and assessing its carbonation levels and taste.
Step 5: Fine-Tune as Needed
If the pressure is not quite right or if the carbonation is not to your liking, continue to make small adjustments to the regulator. Remember to wait for the pressure to stabilize after each adjustment before assessing the carbonation and taste. Repeat this process until you achieve the desired carbonation and dispensing results.
It’s important to note that adjustments to the CO2 pressure should be made gradually. Small changes are easier to control and allow for better fine-tuning. It’s always better to make minor adjustments over time rather than large, abrupt changes that can result in over-carbonation or excessive foaming.
By following these steps and taking your time to make precise adjustments, you can effectively adjust the CO2 pressure in your kegerator, ensuring optimal carbonation and a smooth, enjoyable pour every time you pour a refreshing glass of draft beer.
Maintaining CO2 Pressure in a Kegerator
Once you have set the ideal CO2 pressure in your kegerator, it’s important to maintain that pressure to ensure consistent carbonation and dispensing. Here are some tips for maintaining CO2 pressure in your kegerator:
Read more: How To Fix Co2 Leak In Kegerator
1. Regularly Monitor Pressure
Check the pressure gauge or regulator on a regular basis to ensure that the CO2 pressure is within the desired range. Make it a routine to inspect the pressure every time you use the kegerator or at least once a week to catch any fluctuations or potential issues early on.
2. Check for Leaks
Leaks can cause a drop in CO2 pressure and affect carbonation levels. Periodically inspect all connections, including the CO2 tank, regulator, and beer lines, for any signs of leaks. Use a solution of soapy water and apply it to the connections; if bubbles appear, there is a leak present. Tighten any loose connections or replace faulty parts to maintain a consistent CO2 pressure.
3. Maintain Proper Temperature
Temperature plays a crucial role in CO2 pressure regulation. Ensure that the kegerator is set at the appropriate temperature for your beer style, typically between 36°F and 40°F (2°C to 4°C). Fluctuations in temperature can affect CO2 solubility and consequently the pressure. Regularly check and adjust the temperature settings to maintain consistency.
4. Avoid Excessive Foam
Excessive foam can result from improper CO2 pressure or incorrect pouring techniques. Foam causes a drop in pressure and can lead to under-carbonation. To avoid excessive foam, ensure that the CO2 pressure is set within the recommended range and use proper pouring techniques, such as tilting the glass and gradually straightening it as you pour.
Read more: How To Use A Kegerator Co2 Regulator
5. Perform Regular Maintenance
Regularly clean the beer lines, taps, and connectors to prevent buildup of residue and bacteria. Dirty lines can impact the flow of beer and affect carbonation. Follow the manufacturer’s instructions for cleaning and sanitizing your kegerator components to maintain optimal performance.
6. Keep Spare CO2 Tanks
It’s always a good idea to keep spare CO2 tanks on hand in case of emergencies or unexpected pressure drops. Having a backup tank ensures that you can quickly replace it and maintain consistent pressure. Additionally, consider keeping a spare regulator and other essential parts to avoid any prolonged downtime.
By regularly monitoring pressure, checking for leaks, maintaining proper temperature, avoiding excessive foam, performing routine maintenance, and having spare CO2 tanks available, you can effectively maintain CO2 pressure in your kegerator. This will help ensure that your beer is consistently carbonated and ready to be enjoyed at its best.
Common Issues and Troubleshooting CO2 Pressure
While maintaining CO2 pressure in a kegerator is generally straightforward, there are some common issues that can arise. Here are a few troubleshooting tips to help you address these problems:
1. Low Carbonation
If you notice that your beer has low carbonation levels, it could be due to insufficient CO2 pressure. Check the pressure gauge or regulator to ensure that the pressure is set within the recommended range. If the pressure is too low, adjust the regulator to increase the pressure gradually. Monitor the carbonation levels and taste after making adjustments to find the optimal pressure for your beer.
2. Foamy Beer
Excessive foam is a common issue that can be caused by several factors. One potential cause is having too high of a CO2 pressure. To troubleshoot this, reduce the pressure gradually until you reach a point where the beer pours smoothly without excessive foam. Additionally, make sure to use proper pouring techniques, such as tilting the glass and gradually straightening it as you pour, to minimize foam formation.
3. Inconsistent Pressure
If you notice that the CO2 pressure in your kegerator is fluctuating or inconsistent, it could be due to a leak. Inspect all connections, including the CO2 tank, regulator, and beer lines, for any signs of leaks. Tighten any loose connections or replace faulty parts. If the issue persists, consider using a solution of soapy water to identify the exact location of the leak. Once identified, address the leak promptly to maintain consistent pressure.
4. Pressure Drops
If the CO2 pressure drops unexpectedly, it could be due to an empty or malfunctioning CO2 tank. Check the CO2 tank to ensure that it is not empty. If it is, replace it with a full tank. If the tank is full and there are still pressure drops, it could be a problem with the regulator or a leak. Inspect the regulator for any issues and check all connections for leaks. Replace any faulty parts as needed.
5. High Carbonation
If your beer is over-carbonated and has excessive carbonation levels, it may be due to too high of a CO2 pressure. Check the pressure gauge or regulator and gradually reduce the pressure until the desired carbonation levels are achieved. However, be cautious not to lower the pressure too quickly or too much, as this could result in flat beer. Make small adjustments and monitor the carbonation levels and taste to find the right balance.
By troubleshooting these common CO2 pressure issues and taking steps to address them promptly, you can ensure a smooth and consistent carbonation experience in your kegerator. Remember to always refer to the specific guidelines for your beer style and make adjustments gradually to achieve the desired results.
Read also: 8 Amazing Co2 Tank For Kegerator For 2024
Conclusion
Mastering CO2 pressure in your kegerator is an essential skill for any beer enthusiast or homebrewer. By understanding the factors that affect CO2 pressure, setting the ideal pressure levels, and knowing how to adjust and maintain them, you can enjoy a perfectly carbonated and properly poured draft beer every time.
Carbonation and dispensing pressures play a crucial role in achieving the right balance of carbonation and controlling the flow of beer. It’s important to consider factors such as temperature, beer style, keg volume, and beer line length when determining the ideal pressure settings.
Adjusting CO2 pressure requires careful monitoring, gradual adjustments, and occasional troubleshooting. Regularly checking the pressure, inspecting for leaks, and maintaining proper temperature are key to a consistent carbonation experience. Additionally, staying aware of common issues like low carbonation, foamy beer, inconsistent pressure, pressure drops, and high carbonation can help you troubleshoot problems and address them promptly.
Remember that finding the ideal CO2 pressure is a process of trial and error, influenced by personal preference and specific beer styles. Take your time to make adjustments gradually and monitor the carbonation levels and taste to fine-tune your kegerator setup over time.
By following the guidelines and tips in this article, you can become an expert in regulating CO2 pressure in your kegerator. With your newly acquired knowledge and skills, you can pour the perfect pint, impress your friends, and elevate your beer-drinking experience to the next level. Cheers!
Frequently Asked Questions about What Is The Ideal Co2 Ne Pressure Setting For A Kegerator
Was this page helpful?
At Storables.com, we guarantee accurate and reliable information. Our content, validated by Expert Board Contributors, is crafted following stringent Editorial Policies. We're committed to providing you with well-researched, expert-backed insights for all your informational needs.
0 thoughts on “What Is The Ideal Co2 Ne Pressure Setting For A Kegerator”