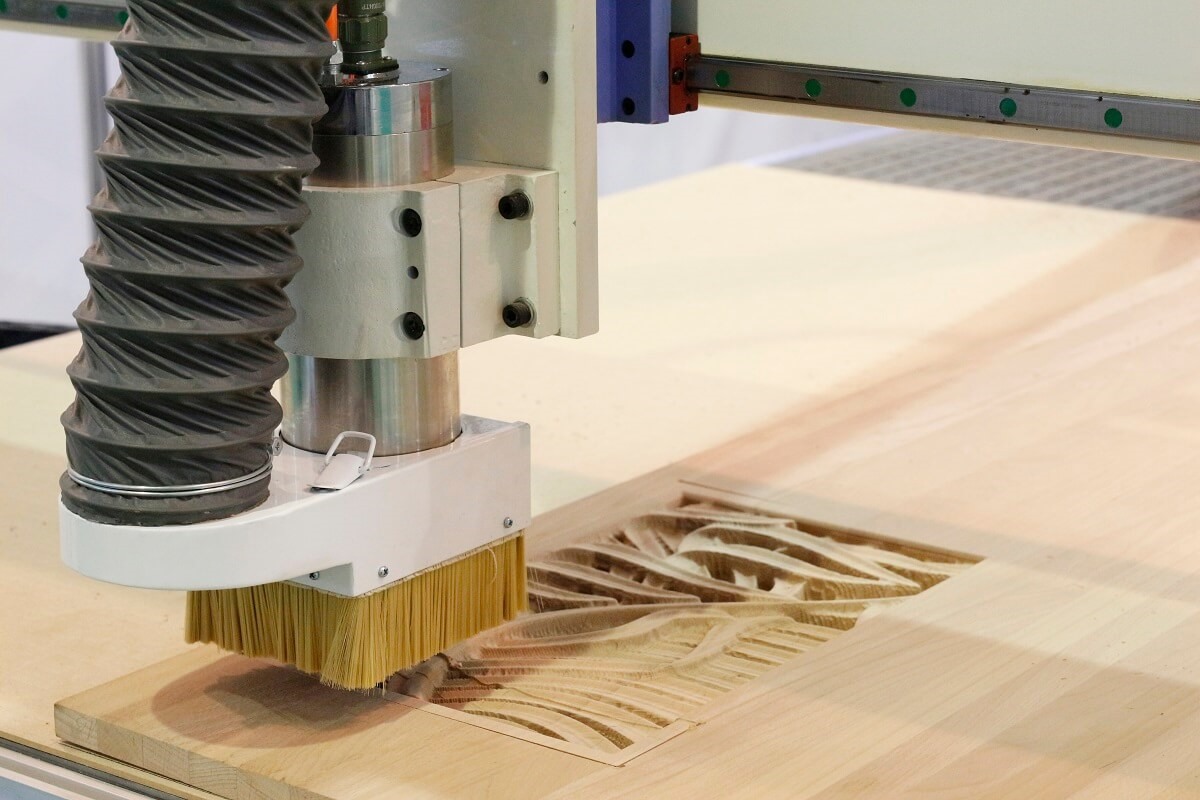
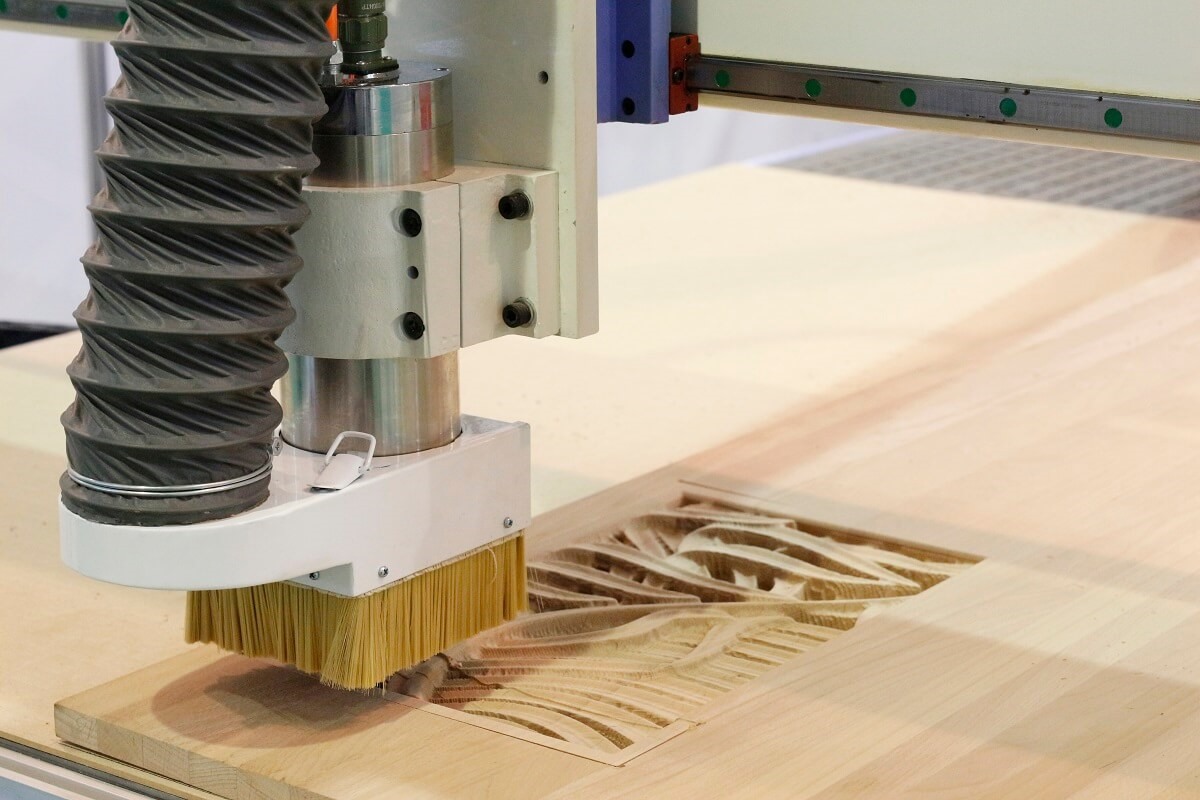
Articles
What Is Cnc In Woodworking
Modified: October 29, 2024
Discover articles about CNC in woodworking and explore its applications, benefits, and techniques. Gain insights into this innovative technology for precision woodworking.
(Many of the links in this article redirect to a specific reviewed product. Your purchase of these products through affiliate links helps to generate commission for Storables.com, at no extra cost. Learn more)
Introduction
Welcome to the world of woodworking, where creativity meets precision. In the traditional woodworking process, craftsmen have relied on their skill and expertise to shape and create beautiful pieces of furniture and decorative items. However, with the advent of technology, a new tool has emerged that is revolutionizing the woodworking industry – CNC (Computer Numerical Control). In this article, we will explore what CNC is, its applications in woodworking, and the advantages it offers.
CNC is a technology that uses computer programs to control the movement of cutting tools and machinery with high precision. It replaces the manual labor involved in woodworking with automated processes, making it easier and more efficient to produce intricate designs and complex shapes. This technology has transformed the woodworking industry, allowing craftsmen to push the boundaries of their creativity and produce unique pieces that were once only possible through hours of manual labor.
When it comes to woodworking, CNC machines have become an essential tool in many workshops. These machines can perform a wide range of tasks, from cutting and carving to drilling and shaping, all with incredible accuracy and consistency. It eliminates the need for multiple tools and repetitive manual actions, saving time and effort.
So, what are the advantages of using CNC in woodworking? First and foremost, precision is key in woodworking, and CNC machines excel in this aspect. They can cut and shape materials with incredible accuracy, ensuring that the final product meets the exact specifications and design requirements. Whether it’s creating intricate patterns or replicating complex designs, CNC machines deliver consistent results every time.
Another significant advantage of CNC in woodworking is efficiency. The automated nature of CNC machines allows for faster production times and increased productivity. Tasks that would have taken hours or even days to complete manually can now be done in a fraction of the time with CNC. This not only helps woodworkers meet deadlines but also opens up possibilities for scaling their business and taking on more projects.
CNC machines also offer versatility in woodworking. With the ability to work with different materials, such as wood, plastics, and even metals, woodworkers have the flexibility to explore new design options and experiment with various materials. This opens up a whole new world of possibilities and expands the creative horizons of woodworkers.
Key Takeaways:
- CNC technology revolutionizes woodworking by offering precision, efficiency, and versatility. It empowers woodworkers to create intricate designs, streamline production, and push the boundaries of creativity, transforming the industry.
- Woodworkers can maximize the potential of CNC technology by focusing on precision design, tool selection, and continuous learning. Embracing safety measures and balancing technical expertise with creativity are essential for mastering CNC woodworking.
Read more: What Is Woodworking
What is CNC?
CNC, short for Computer Numerical Control, is a technology that utilizes computer software and controls to automate the movement and operation of cutting tools and machinery. It has revolutionized various industries, including woodworking, by streamlining the production process and increasing precision.
At its core, CNC involves the use of a computer program known as CAD (Computer-Aided Design) to create a design or blueprint of the desired woodwork. The CAD software allows craftsmen to create intricate designs and precise measurements, providing a visual representation of the final product. Once the design is completed, it is transferred to CAM (Computer-Aided Manufacturing) software, which translates the design into machine-readable instructions.
These instructions, often referred to as G-code, contain precise coordinates and commands that guide the CNC machine in executing the desired woodworking tasks. The CNC machine’s computerized control system then interprets the G-code and initiates the appropriate movements of the cutting tools and machinery to shape and carve the wood according to the design specifications.
Unlike traditional woodworking methods that rely on manual labor, CNC technology offers a host of advantages. One of the key benefits is the high level of precision and accuracy that CNC machines can achieve. By eliminating human error and ensuring consistent movements and measurements, CNC machines can produce complex and intricate designs with incredible detail and accuracy.
Moreover, CNC machines offer increased productivity and efficiency. Once the design is programmed into the software, the CNC machine can carry out repetitive tasks with speed and consistency. This allows woodworkers to complete projects in less time and with greater precision, ultimately increasing their productivity and output.
In addition to precision and efficiency, CNC technology also allows for greater design versatility. With the ability to create complex shapes, curves, and intricate patterns, CNC machines unlock new creative possibilities for woodworkers. They can experiment with unique designs, incorporate intricate details, and explore new woodworking techniques that were previously challenging or time-consuming to achieve manually.
CNC machines also offer enhanced safety features. With automated processes, woodworkers can minimize the risk of accidents and injuries. The machines are equipped with sensors and emergency stop buttons to ensure the safety of operators and prevent any mishaps.
Overall, CNC technology has revolutionized the woodworking industry by combining automation, precision, and versatility. It has become an indispensable tool for woodworkers, enabling them to push the boundaries of their creativity and craftsmanship while streamlining production and improving efficiency.
CNC in Woodworking
CNC technology has made a significant impact on the woodworking industry, transforming the way woodworkers approach their craft. From small workshops to large-scale manufacturing facilities, CNC machines have become a staple tool in woodworking. Let’s explore how CNC is used in woodworking and the benefits it brings to the industry.
One of the primary applications of CNC in woodworking is precision cutting and carving. CNC machines excel at cutting intricate shapes, carving complex patterns, and creating precise joints. Whether it’s producing furniture components, decorative carvings, or architectural elements, CNC technology enables woodworkers to achieve a level of precision and detail that would be challenging to attain manually.
CNC machines are especially beneficial in the production of repetitive woodworking tasks. Instead of manually reproducing the same design or shape multiple times, woodworkers can program the CNC machine to complete the task with accuracy and consistency. This not only saves time but also ensures that each piece is identical, making it ideal for mass production and maintaining quality standards.
Moreover, CNC technology allows woodworkers to explore unique design possibilities. With the ability to work with complex shapes and patterns, CNC machines enable the creation of intricate details and customized designs. Woodworkers can experiment with different styles, textures, and decorative elements, pushing the boundaries of their creativity and delivering highly customized pieces.
Another advantage of CNC in woodworking is its efficiency in material usage. CNC machines optimize the cutting process by minimizing waste and maximizing the utilization of the material. The precise cutting capabilities of CNC machines ensure that each cut is accurate and strategic, reducing material wastage and potentially lowering production costs.
CNC technology has also significantly improved the speed of production in woodworking. Manual labor can be time-consuming, especially for complex designs or large-scale projects. By automating the woodworking process, CNC machines can work much faster, increasing production capacity and meeting tight deadlines.
Additionally, CNC machines offer enhanced safety measures in woodworking. With automated processes, woodworkers can minimize the risk of accidents and injuries. The machines are equipped with safety features such as emergency stop buttons and sensors that detect any anomalies or obstructions, ensuring a safer working environment.
Overall, CNC technology has revolutionized the woodworking industry by streamlining production, increasing precision, and unlocking new design possibilities. It has become an essential tool for woodworkers, enabling them to deliver high-quality, customized pieces efficiently. As the woodworking industry continues to evolve, CNC machines will continue to play a vital role in shaping the future of woodworking.
Advantages of CNC in Woodworking
CNC (Computer Numerical Control) technology has brought numerous advantages to the woodworking industry. From increased precision to improved productivity, CNC machines have revolutionized the way woodworkers approach their craft. Let’s delve into the key advantages of using CNC in woodworking.
1. Precision and Accuracy: CNC machines are unparalleled in their ability to consistently produce precise and accurate results. The automated nature of CNC eliminates human error and ensures that each piece is cut, shaped, and carved with exact measurements. This level of precision allows woodworkers to create intricate designs and tight-fitting joints that would be challenging to achieve by hand.
2. Efficiency and Time Savings: CNC machines are incredibly efficient, enabling woodworkers to complete projects in a fraction of the time it would take using traditional methods. Once the design is programmed into the machine, it can execute tasks with remarkable speed and consistency. This increased efficiency translates to higher productivity, allowing woodworkers to take on more projects and meet tighter deadlines.
3. Repetitive and Mass Production: For projects that require the production of multiple identical pieces, CNC is a game-changer. Woodworkers can program the CNC machine to replicate designs and shapes accurately, eliminating the need for manual reproduction. This makes CNC ideal for mass production, ensuring consistent quality and reducing labor-intensive tasks.
4. Design Versatility: CNC machines offer endless design possibilities in woodworking. They can effortlessly create intricate patterns, complex curves, and customized shapes. Woodworkers can experiment with unique designs and push the boundaries of their creativity, incorporating intricate details that were once challenging to achieve manually. The versatility provided by CNC machines opens up new doors for innovation and customization in woodworking.
5. Material Optimization: One of the significant advantages of CNC in woodworking is its ability to optimize material usage. CNC machines are programmed to cut with precision, minimizing waste and maximizing the utilization of the material. This not only reduces material costs but also contributes to environmental sustainability by reducing the overall waste generated in the woodworking process.
6. Enhanced Safety: CNC machines offer improved safety features compared to traditional woodworking tools. They are equipped with safety mechanisms such as emergency stop buttons and sensors that detect any anomalies or obstructions. These features help reduce the risk of accidents and injuries, providing a safer working environment for woodworkers.
7. Consistency and Quality Control: With CNC, the quality of the finished product is consistent from piece to piece. Each item produced adheres precisely to the programmed design, ensuring uniformity and adherence to desired specifications. CNC machines eliminate variations that can occur with manual techniques, resulting in high-quality, precision-made woodworking pieces.
Overall, the advantages of using CNC in woodworking are undeniable. From precision and efficiency to design versatility and enhanced safety, CNC machines have revolutionized the industry. They have enabled woodworkers to achieve outstanding results, increase productivity, and deliver high-quality, customized pieces that were once only possible through labor-intensive manual processes.
Types of CNC Machines in Woodworking
CNC (Computer Numerical Control) machines have become an integral part of the woodworking industry, offering a wide range of capabilities to woodworkers. From cutting and shaping to carving and milling, different types of CNC machines cater to various woodworking needs. Let’s explore some of the most common types of CNC machines used in woodworking.
1. CNC Routers: CNC routers are one of the most versatile machines in woodworking. They are widely used for cutting, shaping, and carving wood. CNC routers use spinning router bits to remove material and create intricate designs with high precision. These machines can handle a wide range of woodworking tasks, making them suitable for both small-scale workshops and large-scale production facilities.
2. CNC Mills: CNC mills, also known as machining centers, are specialized machines used for precision cutting, drilling, and milling operations. They use rotating cutting tools to remove material from the workpiece and create complex shapes and detailed designs. CNC mills are commonly used for producing precision components and intricate parts, making them indispensable in woodworking industries that require high accuracy and fine details.
3. CNC Lathes: CNC lathes are primarily used for turning operations in woodworking. They rotate the workpiece while a cutting tool shapes the material into the desired form. CNC lathes are ideal for producing cylindrical shapes, such as table legs, balusters, and decorative columns. These machines offer excellent precision and efficiency in creating symmetrical designs and repetitive shapes.
4. CNC Plasma Cutters: CNC plasma cutters are used for cutting through metal materials, such as steel or aluminum, in woodworking. These machines use high-temperature plasma jets to melt through the metal, creating precise cuts and shapes. While primarily used for metalwork, CNC plasma cutters can also be utilized in woodworking to create metal components or decorative elements to enhance wooden structures.
5. CNC Laser Cutters: CNC laser cutters are versatile machines that use laser beams to cut and engrave materials. In woodworking, they are used to create intricate designs, precise cuts, and decorative etchings. CNC laser cutters are ideal for working with various materials, including wood, acrylic, and leather. They provide excellent control and detail in cutting and engraving designs onto wooden surfaces.
6. CNC Panel Saws: CNC panel saws are designed for precise and efficient cutting of large wooden panels or sheets. These machines are equipped with a horizontal cutting blade that can be programmed to cut materials to specific dimensions and shapes. CNC panel saws are widely used in the manufacturing of cabinetry, furniture, and other wooden structures that require accurate and consistent cuts.
7. CNC Drill Presses: CNC drill presses are specialized machines used for drilling holes in woodworking projects. These machines offer precise drilling capabilities, ensuring consistent hole placements and depths. CNC drill presses are often used in the production of furniture, cabinets, and other wooden products that require precise hole alignments.
These are just a few examples of the types of CNC machines used in woodworking. Each machine offers unique capabilities and applications, allowing woodworkers to achieve intricate designs, precise cuts, and efficient production. By harnessing the power of CNC technology, woodworkers can take their craftsmanship to new heights and unlock a world of creative possibilities.
When working with CNC in woodworking, always double-check your design and tool paths before cutting to avoid any costly mistakes. It’s important to have a thorough understanding of the software and machine capabilities to ensure precision and efficiency in your projects.
Read more: What Is A Planer In Woodworking
CNC Software for Woodworking
CNC (Computer Numerical Control) software plays a crucial role in the operation and programming of CNC machines in woodworking. It allows woodworkers to design, visualize, and control the movements of the cutting tools with precision. Let’s explore some of the common types of CNC software used in woodworking and their key features.
1. CAD (Computer-Aided Design) Software: CAD software is used to create detailed designs and blueprints of woodworking projects. It provides a platform for woodworkers to digitally design and visualize their ideas before sending them to the CNC machine for production. CAD software allows for precise measurements, accurate dimensions, and the creation of complex shapes and patterns. It is the foundation for CNC programming and serves as the starting point for generating the machine-readable instructions.
2. CAM (Computer-Aided Manufacturing) Software: CAM software translates the designs created in CAD software into machine-readable instructions, known as G-code. It determines the toolpaths, speeds, and feeds required for the CNC machine to carry out each operation. CAM software optimizes the machining process by calculating the most efficient toolpaths and generating the necessary tool motion commands. It plays a crucial role in ensuring that the CNC machine executes the woodworking tasks accurately and efficiently.
3. Nesting Software: Nesting software is specifically designed for optimizing material usage in CNC woodworking projects. It allows woodworkers to arrange the pieces to be cut on the material sheet, minimizing waste and maximizing material utilization. Nesting software assists in positioning and orienting the designs to achieve the most efficient cutting layout. By optimizing material consumption, nesting software helps reduce costs and improve sustainability in woodworking projects.
4. Simulation Software: Simulation software allows woodworkers to visualize and simulate the machining process before running it on the CNC machine. It provides a virtual environment where woodworkers can see a preview of the cutting, carving, and shaping operations. Simulation software helps identify any potential issues or collisions that may occur during the machining process, allowing for adjustments and optimizations before starting production. It helps to ensure the safety and accuracy of the CNC operations while minimizing the risk of errors and material wastage.
5. ERP (Enterprise Resource Planning) Software: ERP software is used for overall project management, including inventory control, scheduling, and tracking of woodworking projects. It provides a centralized system for managing materials, monitoring production progress, and tracking costs. ERP software integrates with CNC machines to streamline the workflow, improve productivity, and provide real-time insights into project status and performance.
These are just a few examples of the CNC software used in woodworking. The development of specialized software packages for CNC machines in woodworking has greatly simplified the programming process and improved efficiency. With the right combination of CAD, CAM, nesting, simulation, and ERP software, woodworkers can optimize designs, automate tasks, minimize waste, and improve overall productivity in their CNC woodworking operations.
Common Applications of CNC in Woodworking
CNC (Computer Numerical Control) technology has revolutionized the woodworking industry, offering endless possibilities for woodworkers to create intricate designs, precise cuts, and customized pieces. Let’s explore some of the common applications of CNC in woodworking that have transformed the way woodworkers approach their craft.
1. Furniture Manufacturing: CNC machines have become invaluable in the production of furniture. From cutting and shaping wooden components to creating intricate details and joinery, CNC technology streamlines the manufacturing process. It allows woodworkers to produce consistent, high-quality furniture pieces efficiently and at scale.
2. Cabinetry and Millwork: CNC machines are widely used in the production of cabinetry and millwork. They excel at cutting precise joints, creating intricate panel designs, and carving details on cabinet doors and moldings. CNC technology ensures that each piece is accurately shaped and fits together seamlessly, resulting in visually stunning and functional cabinetry and millwork.
3. Decorative Carvings and Inlays: CNC machines offer unmatched precision and control in creating decorative carvings and inlays. Whether it’s intricate patterns, ornate designs, or custom logos, CNC technology allows woodworkers to achieve detailed and intricate carvings with ease. This makes it ideal for creating decorative elements that add a touch of elegance and uniqueness to woodworking projects.
4. Sign Making: CNC machines have transformed the sign-making industry. Woodworkers can create custom signs with precision-cut letters, intricate designs, and even 3D relief carvings. CNC technology enables woodworkers to produce eye-catching, professional-grade signs that stand out in both commercial and residential settings.
5. Architectural Woodworking: CNC machines are used extensively in architectural woodworking. From intricate wooden moldings to detailed door and window frames, CNC technology allows woodworkers to create precise and custom architectural elements. CNC machines enable them to replicate intricate historical designs or bring innovative concepts to life with ease and accuracy.
6. Artistic Sculptures: CNC technology has opened up new avenues for artistic expression in woodworking. Woodworkers can create intricate and elaborate sculptures using CNC machines. The precision and control offered by CNC allow artists to unleash their creativity and sculpt wood into complex shapes and forms that were once painstakingly challenging to achieve manually.
7. Musical Instruments: CNC machines have found their way into the production of musical instruments. Whether it’s guitars, violins, or drums, CNC technology ensures precise cuts, perfect fret placement, and intricate detailing. This allows woodworkers to create instruments that not only sound amazing but also have exceptional craftsmanship and aesthetic appeal.
These are just a few examples of the common applications of CNC in woodworking. The possibilities are virtually endless. CNC technology has given woodworkers the ability to bring their visions to reality with greater precision, efficiency, and versatility. It has transformed woodworking from a labor-intensive craft to a streamlined and innovative art form.
Tips for Using CNC in Woodworking
Using CNC (Computer Numerical Control) technology in woodworking requires a combination of technical knowledge, creativity, and attention to detail. To make the most out of CNC machines and achieve exceptional results, here are some tips to keep in mind:
1. Design with Precision: One of the essential aspects of CNC woodworking is designing with precision. Invest time in creating detailed and accurate CAD designs that account for material thickness, tool diameter, and cutting paths. Double-check measurements and dimensions to ensure that the final product matches your vision.
2. Choose the Right Tooling: Selecting the appropriate cutting tools is crucial for achieving the desired results. Consider the type of wood, the intricacy of the design, and the desired finish when choosing cutting bits, drills, or carving tools. Using the right tooling will ensure clean cuts, smooth finishes, and overall better performance.
3. Optimize Tool Paths: Efficient tool paths can significantly enhance productivity and minimize cutting time. Utilize CAM software to optimize tool paths based on your specific project and desired outcomes. Consider strategies such as climb cutting, ramping, and varying cut depths to maximize efficiency and minimize unnecessary tool movements, reducing the wear and tear on cutting bits.
4. Test and Fine-tune: Before running a full-scale production, it’s a good practice to run a test cut or prototype to fine-tune your CNC settings. This allows you to identify any issues, such as tool chatter, improper depths, or incorrect speeds, and make adjustments before committing to larger production runs. Testing and fine-tuning help optimize the quality and efficiency of your CNC woodworking projects.
5. Secure and Prepare the Material: Proper material preparation and secure clamping are necessary for accurate and safe machining. Ensure that the material is straight, flat, and properly sized before starting the CNC process. Take time to secure the material firmly in place using appropriate clamps that won’t interfere with the CNC machine’s movements. This will help prevent material shift and ensure precise cuts and carvings.
6. Pay Attention to Dust and Chip Control: Woodworking can generate a significant amount of dust and chips, which can affect the accuracy and performance of the CNC machine. Implement effective dust collection systems to keep the workspace clean and avoid debris from interfering with the machine’s movements or damaging the electronics. Regularly clean and maintain the CNC machine to prevent dust and chips from building up.
7. Practice Safety Measures: Safety should always be a top priority when working with CNC machines. Familiarize yourself with the machine’s safety features, such as emergency stop buttons and safety interlocks, and follow all recommended safety guidelines. Always wear appropriate personal protective equipment (PPE), such as safety glasses and hearing protection. Regularly inspect and maintain the machine to ensure safe and reliable operation.
8. Continuous Learning and Improvement: CNC woodworking is a constantly evolving field. Stay updated with the latest advancements, software upgrades, and techniques. Attend workshops, seminars, or online courses to enhance your knowledge and skills. Embrace continuous learning and experimentation to unlock new possibilities and refine your CNC woodworking expertise.
By following these tips, you can maximize the potential of CNC technology in woodworking and achieve exceptional results. Remember to balance technical precision with your creativity, and don’t hesitate to experiment and push the boundaries of your craft. CNC woodworking offers endless opportunities, and with practice, you can master this powerful tool and create extraordinary woodworking projects.
Conclusion
CNC (Computer Numerical Control) technology has revolutionized the woodworking industry, empowering woodworkers to achieve precision, efficiency, and creativity like never before. With the ability to automate tasks, create intricate designs, and streamline production, CNC machines have become an essential tool in modern woodworking.
Through CNC technology, woodworkers can produce high-quality furniture, intricate carvings, customized designs, and architectural elements with unparalleled precision. The combination of CAD and CAM software enables them to transform their ideas into detailed digital designs and translate them into machine-readable instructions. This level of precision and control allows woodworkers to push the boundaries of their creativity and deliver exceptional craftsmanship.
Not only does CNC technology offer precision, but it also enhances efficiency and productivity. By automating tasks that would otherwise be time-consuming, woodworkers can complete projects faster and take on more work. CNC machines can replicate designs precisely, enabling consistent production and minimizing human error. The optimization of material usage further contributes to increased efficiency by reducing waste.
CNC machines have vastly expanded the possibilities in woodworking. Woodworkers can now create intricate carvings, detailed inlays, and complex shapes that were once challenging to achieve manually. They can experiment with different styles and push their creative boundaries, offering a wide range of customized options to their clients.
However, it’s important to note that CNC technology is just a tool, and it requires the skill and expertise of woodworkers to fully harness its potential. Collaborating with the machine rather than relying solely on its capabilities is crucial. Woodworkers must continue to develop their knowledge and skills, adapt to new software updates, and continuously refine their craft to fully leverage the benefits of CNC in woodworking.
In conclusion, CNC technology has transformed the woodworking industry, revolutionizing the way woodworkers approach their craft. Whether it is precision cutting, intricate detailing, or streamlining production processes, CNC machines empower woodworkers to achieve exceptional results. By embracing the opportunities brought by CNC technology and combining it with their passion and expertise, woodworkers can continue to push the boundaries of creativity, deliver high-quality craftsmanship, and shape the future of woodworking.
Frequently Asked Questions about What Is Cnc In Woodworking
Was this page helpful?
At Storables.com, we guarantee accurate and reliable information. Our content, validated by Expert Board Contributors, is crafted following stringent Editorial Policies. We're committed to providing you with well-researched, expert-backed insights for all your informational needs.
0 thoughts on “What Is Cnc In Woodworking”