Home>Articles>What Is The Function Of The Brushes And Commutators In An Electric Motor?
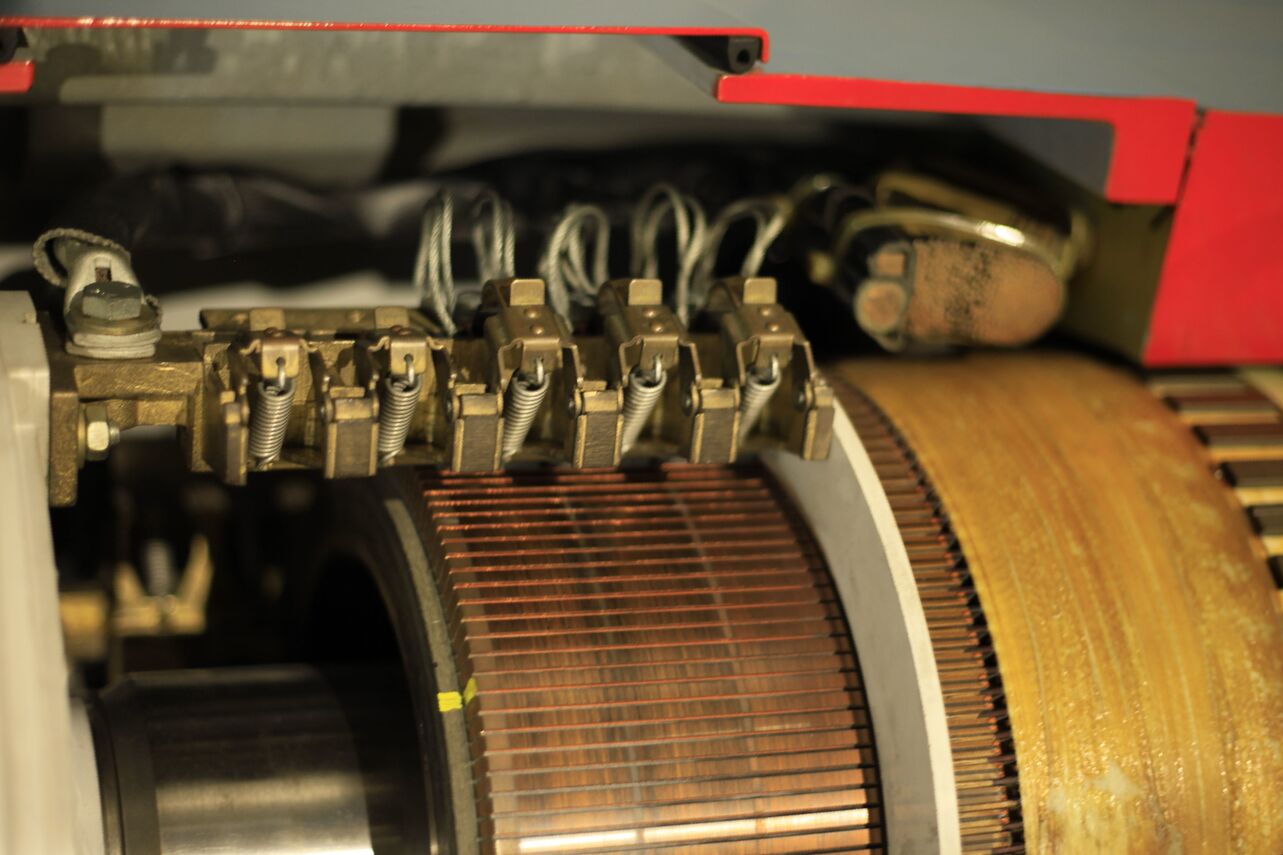
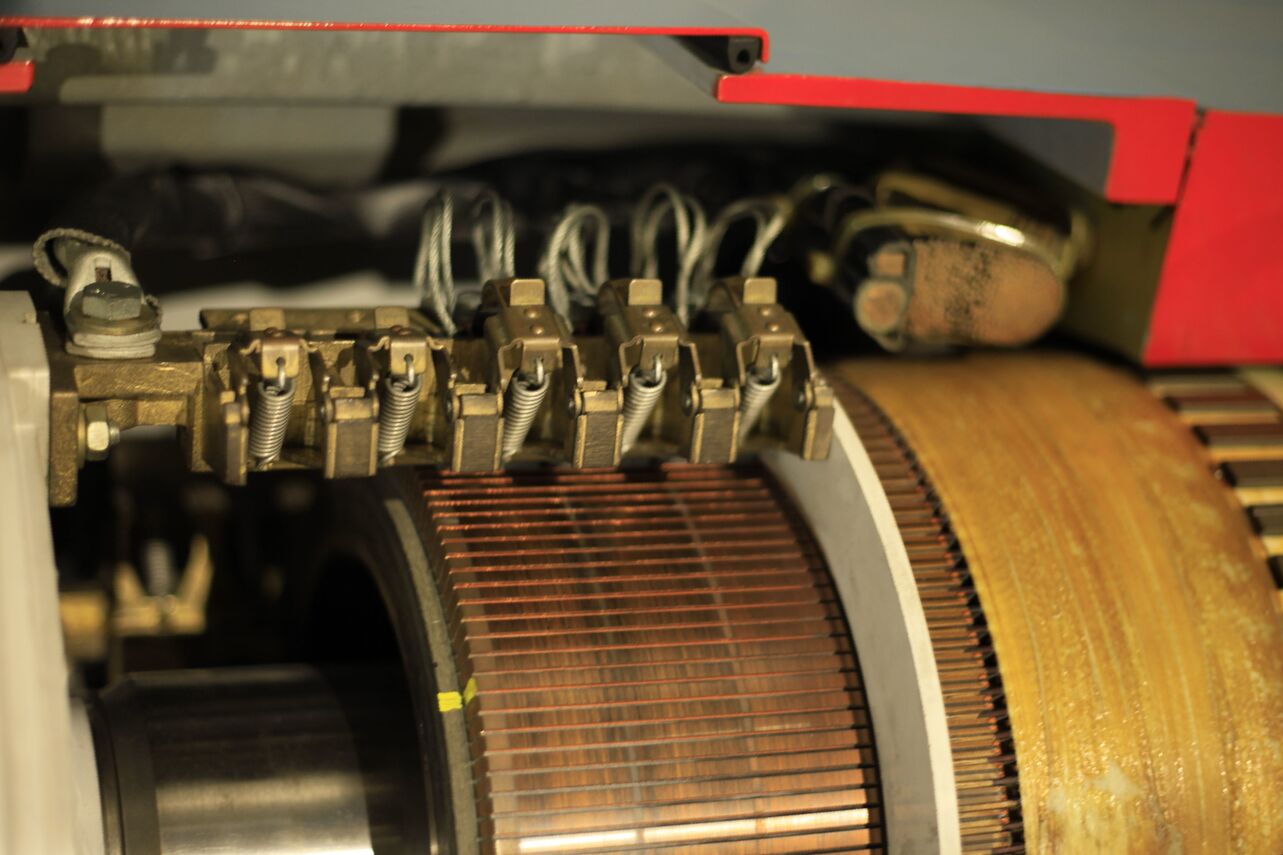
Articles
What Is The Function Of The Brushes And Commutators In An Electric Motor?
Modified: December 7, 2023
Discover the key differences between a brush and a commutator in an electric motor in this informative article. Gain insights on their functions and significance.
(Many of the links in this article redirect to a specific reviewed product. Your purchase of these products through affiliate links helps to generate commission for Storables.com, at no extra cost. Learn more)
Introduction
Electric motors play a crucial role in various industries and everyday applications. They are widely used in appliances, vehicles, machinery, and many other devices to convert electrical energy into mechanical energy. One of the key components of an electric motor is the brush and the commutator. These two components work together to ensure the smooth and efficient operation of the motor.
Understanding the function and comparison between a brush and a commutator is essential for those involved in the design, maintenance, and repair of electric motors. In this article, we will delve into the working principle of an electric motor and explore the roles of brushes and commutators in this dynamic system. We will also discuss the factors affecting their performance and provide insights on how to optimize their functionality.
So, let’s dive into the fascinating world of electric motors and explore the functions and features of brushes and commutators!
Key Takeaways:
- Brushes and commutators are essential components in electric motors, with brushes maintaining electrical connection and regulating speed, while commutators convert AC to DC and control current direction.
- Factors such as material quality, brush pressure, alignment, and maintenance significantly impact the performance of brushes and commutators, emphasizing the importance of proper care and attention to ensure optimal motor functionality.
Working Principle of an Electric Motor
Before we delve into the functions of brushes and commutators, let’s first understand the basic working principle of an electric motor. At its core, an electric motor converts electrical energy into mechanical energy to generate rotational motion.
An electric motor consists of two key components: the stator and the rotor. The stator is the stationary part that houses the winding, while the rotor is the rotating part that carries the output shaft. The stator typically contains multiple electromagnets, which are coils of wire wound around an iron core. These electromagnets create a rotating magnetic field when energized.
The rotor, on the other hand, consists of a series of conductive bars or coils mounted on an iron core. These conductive elements are free to rotate within the magnetic field generated by the stator. When an electric current is passed through the conductors, it creates a magnetic field around them, which interacts with the magnetic field of the stator.
According to the principles of electromagnetism, when two magnetic fields interact, a force is exerted on the conductors. This force causes the rotor to rotate, converting electrical energy into mechanical energy. The rotation of the rotor is what drives the machinery or device connected to the motor.
To ensure the smooth and continuous rotation of the rotor, it is essential to maintain the flow of current in the conductors as they pass through the magnetic field. This is where brushes and commutators come into play, functioning as critical components in the operation of an electric motor.
Now that we have a basic understanding of the working principle of an electric motor, let’s dive deeper into the functions of brushes and commutators and explore their individual roles in this sophisticated machine.
Function of a Brush in an Electric Motor
In an electric motor, the brush serves as a critical component that facilitates the transfer of electrical current between the power source and the rotating rotor. The primary function of the brush is to maintain a constant electrical connection with the commutator, allowing the flow of current to power the motor.
When the electric current is supplied to the motor, it enters the stationary part of the motor, known as the stator, which houses the brushes. The brushes are typically made of carbon or graphite, as these materials have excellent electrical conductivity and can withstand the mechanical forces and high temperatures generated during motor operation.
As the rotor rotates, it comes into contact with the brushes, establishing an electrical contact through the commutator. The commutator is a cylindrical device that consists of a series of copper segments or bars insulated from each other. The brushes make contact with these segments, which are connected to the armature winding.
As the rotor rotates, the brushes slide over the segments of the commutator, allowing electrical current to flow from the power source to the armature winding. This current creates the magnetic field necessary for the motor’s operation. The brushes ensure a continuous flow of current, maintaining a constant connection with the commutator as the rotor rotates.
The brushes in an electric motor also play a crucial role in regulating the speed and controlling the direction of rotation. By changing the position of the brushes on the commutator, the timing and sequencing of the current flow can be adjusted, resulting in variations in motor speed and direction.
Additionally, the brushes help in dissipating heat generated during motor operation. As the electrical current flows through the brushes, they experience friction and heat up. This heat needs to be dissipated to prevent damage to the brushes and other motor components. To facilitate heat dissipation, the brushes are often designed to have good thermal conductivity and are sometimes equipped with cooling systems.
In summary, the function of brushes in an electric motor includes maintaining a constant electrical connection with the commutator, ensuring the flow of current to power the motor, regulating motor speed and direction, and aiding in heat dissipation. Without brushes, the efficient and reliable operation of electric motors would not be possible.
Function of a Commutator in an Electric Motor
Within an electric motor, the commutator serves a vital function in converting the alternating current (AC) flowing through the armature winding into a unidirectional current (DC) that drives the motor’s rotation. The commutator allows for the continuous and controlled flow of current to the armature winding, ensuring the smooth operation of the motor.
The armature winding consists of coils of wire that are wound around the rotor, the rotating part of the motor. As the rotor spins, it passes over the stationary brushes that make contact with the segments of the commutator, which are connected to the armature winding. The commutator consists of a series of copper bars or segments that are electrically insulated from each other.
The function of the commutator is twofold. First, it acts as a mechanical switch, continuously reversing the direction of current flow in the armature winding as the rotor rotates. This reversal is necessary because the magnetic field generated by the stator’s electromagnets changes in polarity as the rotor spins. By reversing the current flow in the armature winding, the commutator ensures that the interaction between the field generated by the rotor and the stator remains constant, resulting in a steady rotational motion.
Secondly, the commutator facilitates the conversion of AC into DC. When the brushes make contact with the segments of the commutator, the electrical current flows into the armature winding. As the rotor rotates, the commutator segments and brushes establish temporary connections, allowing the current to flow in one direction. This conversion from AC to DC is crucial for many applications, as most devices and machinery operate on DC power.
The commutator accomplishes the conversion process by creating a series of closed circuits. As the rotor spins, the brushes make contact with different commutator segments, opening and closing specific circuits. This controlled action ensures that the current flows in one direction, creating a continuous flow of power to the armature winding.
Furthermore, the commutator helps in maintaining a constant connection with the brushes as they slide over the segments. Its design ensures that the brushes maintain contact even as the motor experiences vibrations and mechanical stresses during operation. This reliable connection is crucial for the efficient and uninterrupted transfer of power between the power source and the motor.
In summary, the function of the commutator in an electric motor includes reversing the direction of current flow in the armature winding, converting AC to DC, establishing temporary connections with the brushes, and maintaining a reliable contact with the brushes as the motor operates. The commutator is a key component that enables the controlled flow of current, ensuring the smooth and efficient rotation of the motor.
A brush and a commutator in an electric motor both play a crucial role in transferring electrical energy to mechanical energy. The brush makes direct contact with the commutator to ensure a continuous flow of current, allowing the motor to function efficiently.
Comparison between a Brush and a Commutator
While both the brush and the commutator are essential components in an electric motor, there are distinct differences in their functions and characteristics. Let’s explore the key points of comparison between these two components:
1. Function: The brush serves as a bridge between the power source and the commutator, maintaining a continuous electrical connection and facilitating the flow of current to power the motor. On the other hand, the commutator is responsible for converting the alternating current (AC) into direct current (DC) and reversing the direction of current flow in the armature winding as the rotor rotates.
2. Composition: Brushes are typically made of carbon or graphite due to their excellent electrical conductivity and ability to withstand high temperatures and mechanical stresses. Commutators, on the other hand, are constructed with segmented copper bars or segments that are electrically insulated from each other.
3. Contact: Brushes make physical contact with the commutator segments, sliding over them as the rotor rotates. This continuous contact ensures a reliable electrical connection. In contrast, the commutator segments are stationary and do not move, providing fixed points for the brushes to make contact.
4. Movement: Brushes move along the commutator as the rotor spins, maintaining contact and allowing for the transfer of electrical current. In contrast, the commutator remains stationary and does not move during motor operation.
5. Maintenance: Brushes undergo wear and tear due to friction and heat generated during motor operation. Regular inspection and replacement are necessary to ensure optimal performance. Commutators, on the other hand, require periodic cleaning and maintenance to remove build-up and ensure smooth operation.
6. Heat Dissipation: Brushes play a role in dissipating heat generated during motor operation. Their composition and design allow for effective heat transfer and help prevent damage to the brushes and other motor components. Commutators, while not specifically designed for heat dissipation, can also contribute to heat distribution within the motor.
7. Size and Shape: Brushes are typically small and compact, designed to make contact with specific areas of the commutator. Commutators come in various shapes and sizes depending on the motor’s requirements, but they are generally larger and more robust.
In summary, while the brush and commutator work together in an electric motor, their functions, composition, and characteristics differ significantly. The brush acts as a conductor, maintaining contact and facilitating the transfer of electrical current, while the commutator converts AC to DC and regulates the direction of the current flow. Both components are vital for the efficient operation of the motor, and their proper maintenance and care are essential for optimal performance.
Read more: How To Replace Brushes In Electric Motor
Factors Affecting the Performance of a Brush and a Commutator in an Electric Motor
The performance of both the brush and the commutator in an electric motor can be influenced by various factors. Understanding these factors is crucial for maintaining the efficiency and longevity of these components. Here, we will explore the key factors that can affect their performance:
1. Material Quality: The quality of the materials used for the brush and the commutator greatly impacts their performance. High-quality materials with excellent electrical conductivity, thermal conductivity, and resistance to wear are essential. Carbon or graphite brushes with the right composition and copper segments with proper insulation contribute to reliable performance.
2. Brush Pressure: The pressure exerted by the brushes on the commutator affects their performance. Adequate brush pressure ensures sufficient contact for the transfer of electrical current. However, excessive pressure can increase friction and wear, while insufficient pressure may result in poor electrical connection.
3. Brush Alignment: Proper alignment of the brushes on the commutator is crucial for optimal performance. Misalignment can lead to uneven contact, increased friction, and potential damage to the commutator segments. Regular inspection and adjustment of brush alignment are necessary to avoid these issues.
4. Brush Composition: The composition of the brush determines its electrical and thermal conductivity, as well as its ability to withstand mechanical stresses. Different motor applications may require specific brush compositions to meet the demands of the operating conditions.
5. Commutator Maintenance: Regular maintenance of the commutator is essential for optimal performance. Build-up of dirt, dust, or carbon deposits on the commutator can disrupt the contact with the brushes, resulting in poor electrical conductivity and potential arcing. Routine cleaning and inspection are necessary to ensure the smooth operation of the commutator.
6. Current Load: The current load placed on the motor affects the performance of both the brush and the commutator. Higher current loads result in increased heat generation and mechanical stress, which can impact the wear rate of the brushes and the integrity of the commutator segments. Ensuring that the motor is operated within its rated current limits is important to prevent premature failure.
7. Operating Conditions: The environmental conditions in which the motor operates can affect the performance of the brush and the commutator. Factors such as temperature, humidity, and the presence of contaminants can influence their performance. Extreme temperatures, excessive moisture, or the presence of abrasive particles can accelerate wear and compromise the integrity of these components.
8. Lubrication: Proper lubrication of the brushes and the commutator is vital for reducing friction, heat generation, and wear. Using suitable lubricants helps to maintain smooth operation and prolong the lifespan of the components.
To ensure optimal performance, it is crucial to consider these factors and implement appropriate maintenance practices. Regular inspection, cleaning, and replacement of worn brushes or damaged commutator segments are essential steps in maximizing the performance and longevity of these critical components in an electric motor.
Conclusion
The brush and commutator are integral components of an electric motor, working in harmony to ensure its efficient and reliable operation. The brush serves as a bridge between the power source and the commutator, maintaining a continuous electrical connection and facilitating the flow of current to power the motor. Meanwhile, the commutator converts alternating current (AC) into direct current (DC) and reverses the direction of current flow in the armature winding as the rotor rotates.
The performance of the brush and the commutator can be influenced by various factors, such as material quality, brush pressure, alignment, composition, and commutator maintenance. Additionally, the current load, operating conditions, and proper lubrication play critical roles in their performance.
To ensure optimal performance, it is crucial to regularly inspect, clean, and replace worn brushes or damaged commutator segments. The use of high-quality materials, proper alignment, and appropriate brush pressure are essential for their efficient functioning. Maintaining the commutator’s cleanliness and ensuring it is operating within its rated current limits are also important factors to consider.
By understanding the functions and factors affecting the performance of brushes and commutators, those involved in the design, maintenance, and repair of electric motors can optimize their functionality, prolong their lifespan, and enhance the overall efficiency of the motor.
In conclusion, the brush and commutator work together as a crucial duo in the intricate machinery of an electric motor. Their proper maintenance, alignment, and quality ensure the smooth and efficient conversion of electrical energy into mechanical energy. The continuous development and improvement of brushes and commutators contribute to the advancement and reliability of electric motors, powering a wide range of industries and applications around the world.
Frequently Asked Questions about What Is The Function Of The Brushes And Commutators In An Electric Motor?
Was this page helpful?
At Storables.com, we guarantee accurate and reliable information. Our content, validated by Expert Board Contributors, is crafted following stringent Editorial Policies. We're committed to providing you with well-researched, expert-backed insights for all your informational needs.
0 thoughts on “What Is The Function Of The Brushes And Commutators In An Electric Motor?”