Home>diy>Building & Construction>How To Calculate The Construction Productivity Rate
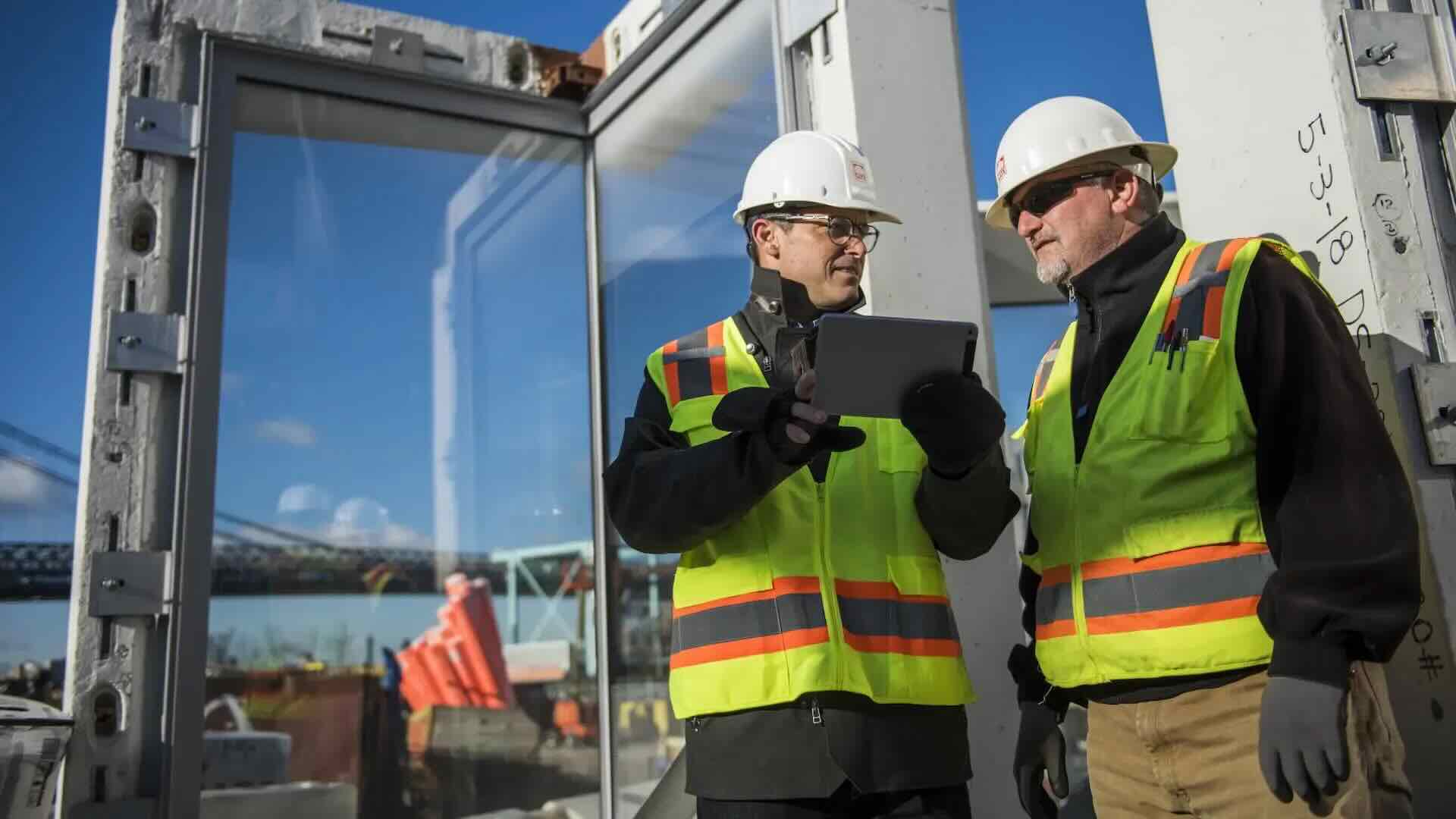
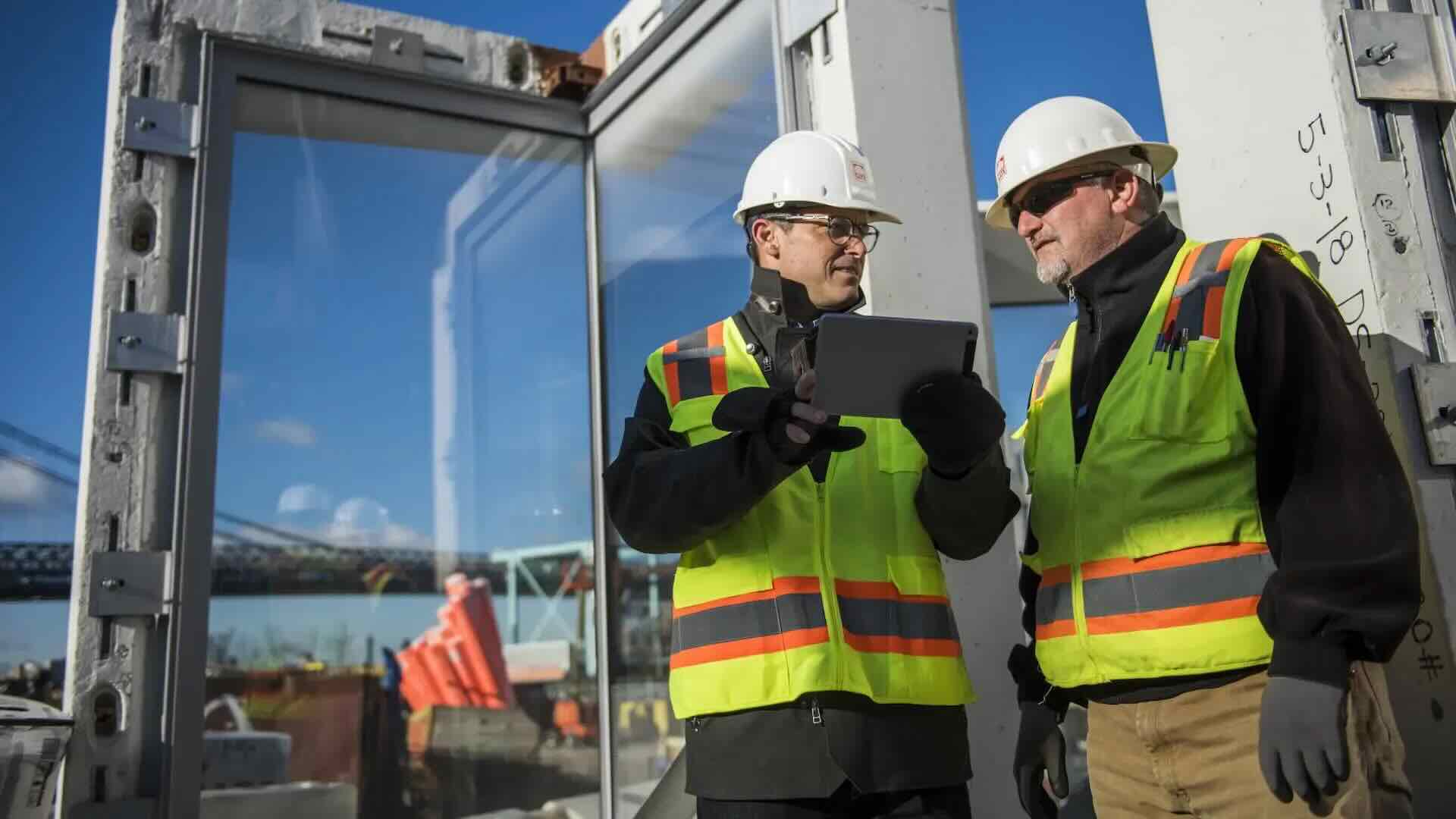
Building & Construction
How To Calculate The Construction Productivity Rate
Modified: January 24, 2024
Learn how to calculate production rate in building construction. Discover efficient methods and formulas to optimize productivity on construction sites.
(Many of the links in this article redirect to a specific reviewed product. Your purchase of these products through affiliate links helps to generate commission for Storables.com, at no extra cost. Learn more)
Introduction
In the world of construction, efficiency and productivity are paramount. Project managers, contractors, and stakeholders all have a vested interest in completing construction projects in a timely manner and within budget. One crucial factor that directly impacts the project’s timeline and cost is the production rate.
The production rate in construction refers to the amount of work that can be completed in a specific period of time. It is essentially the rate at which tasks, activities, or work units are accomplished. Calculating the production rate enables construction professionals to estimate project timelines, allocate resources, and make informed decisions that optimize efficiency and productivity.
Understanding how to calculate production rate is not only essential for adequately planning a construction project but also for monitoring and controlling its progress. By tracking the actual production rate against the planned rate, project managers can identify and address any deviations early on, ensuring that the project stays on track.
This article aims to provide a comprehensive guide on how to calculate production rate in construction. We will explore the significance of production rate, the factors influencing it, the steps involved in its calculation, and the benefits of accurate production rate estimation. So, let’s delve deeper into this crucial aspect of construction management.
Key Takeaways:
- Accurately calculating the production rate in construction is essential for efficient project planning, optimized resource allocation, improved cost control, early issue identification, increased productivity, client satisfaction, and improved decision-making.
- Understanding how to calculate the production rate empowers construction professionals to make informed decisions, optimize resource utilization, and ensure the successful completion of construction projects, contributing to overall project success and client satisfaction.
Read more: How To Calculate The Construction Area
Definition of Production Rate
Before we dive into the intricacies of calculating production rate in construction, it’s important to have a clear understanding of what it actually entails.
The production rate is a measure of how much work or output can be achieved within a specific time frame. It is typically expressed as a quantity per unit of time, such as cubic yards of concrete poured per hour or linear feet of piping installed per day.
In the context of construction, the production rate refers to the pace at which construction activities are completed or the amount of work that can be accomplished within a given time period. It is influenced by various factors, including the complexity of the task, the skill level of the workers, the availability of resources, and the efficiency of the construction processes.
The production rate in construction is a critical metric for project planning, as it helps determine the estimated time required to complete a project. Additionally, it serves as a benchmark for evaluating and improving productivity throughout the construction process.
By accurately estimating and monitoring the production rate, construction professionals can make informed decisions regarding resource allocation, scheduling, and project management. It enables them to set realistic project timelines, optimize the use of available resources, and identify potential bottlenecks or areas for improvement.
It’s important to note that the production rate can vary from one construction project to another, as each project has its own unique characteristics and requirements. Factors such as project scope, site conditions, weather conditions, and the availability of skilled labor and equipment can all impact the production rate.
Now that we have a clear understanding of what production rate means in the context of construction, let’s explore why calculating it is of utmost importance.
Importance of Calculating Production Rate in Construction
The calculation of production rate holds great significance in the construction industry. It plays a vital role in project planning, resource management, and overall project success. Let’s explore the key reasons why calculating production rate is important:
- Accurate Project Planning: Calculating production rate helps project managers create realistic project schedules and timelines. By knowing how much work can be accomplished within a specific time frame, they can allocate resources effectively and set achievable milestones. This ensures that the project is completed on time and within budget.
- Resource Allocation: Understanding the production rate allows for efficient allocation of resources. By knowing the pace of work, project managers can determine the number of workers, equipment, and materials required to meet specific project goals. This helps avoid over- or under-utilization of resources, optimizing productivity and minimizing costs.
- Budget Control: Calculating production rate helps in estimating labor and material costs accurately. By knowing the quantity of work that can be completed within a given timeframe, project managers can budget accordingly, avoiding unexpected expenses and ensuring financial stability throughout the project.
- Identifying Bottlenecks: Monitoring the production rate allows for early identification of potential bottlenecks or inefficiencies in the construction process. By comparing the actual production rate with the planned rate, project managers can pinpoint areas that require improvement, address issues promptly, and keep the project on track.
- Quality Control: Calculating production rate is not only about speed and efficiency but also about maintaining quality standards. By monitoring the production rate, project managers can ensure that the work is being done to the required quality levels. This helps in delivering a high-quality end product that meets client expectations.
- Performance Evaluation: The production rate serves as a benchmark for evaluating the performance of workers, subcontractors, and the overall construction team. By comparing the actual production rate against the planned rate, project managers can identify areas of excellence and areas for improvement. This information can then be utilized in performance reviews and training programs.
Overall, calculating the production rate is crucial for effective project management, resource optimization, and cost control. It enables construction professionals to make informed decisions, improve productivity, and ensure the successful completion of construction projects. Now that we understand the importance of production rate calculation, let’s explore the factors that can impact it.
Factors Affecting Production Rate
Several factors can influence the production rate in construction. It is important for project managers and construction professionals to consider these factors when estimating and calculating the production rate. Let’s take a closer look at some of the key factors that can affect production rate:
- Worker Skill and Efficiency: The skill level and efficiency of the construction workforce can have a significant impact on the production rate. Experienced and well-trained workers are likely to complete tasks more quickly and accurately, resulting in a higher production rate. On the other hand, inexperienced or inadequately trained workers may take longer to complete tasks and may be more prone to errors, leading to a lower production rate.
- Availability of Resources: The availability of resources, such as materials, equipment, and machinery, can greatly influence the production rate. Insufficient or delayed availability of resources can cause delays and hinder productivity. Conversely, having an ample supply of resources and well-maintained equipment can enhance the production rate and overall efficiency.
- Project Complexity: The complexity of the construction project can impact the production rate. Projects that require intricate design details, complex coordination, or specialized construction techniques may take longer to complete, resulting in a lower production rate. Projects with simple designs and straightforward processes, on the other hand, tend to have a higher production rate.
- Site Conditions: The conditions of the construction site can affect the production rate. Factors such as weather conditions, accessibility, site layout, and restrictions can impact construction activities. Extreme weather conditions, site congestion, or limited access to the site can slow down work progress and lower the production rate.
- Availability of Skilled Labor: The availability of skilled labor is crucial for maintaining a high production rate. Insufficient skilled labor or a shortage of specific trades can hamper productivity and prolong project timelines. On the other hand, having a skilled and experienced workforce can expedite construction activities and increase the production rate.
- Efficiency of Construction Processes: The efficiency of the construction processes and workflows can significantly influence the production rate. Streamlined processes, well-defined workflows, and effective project management practices can optimize productivity and enhance the production rate. Conversely, inefficient processes, lack of coordination, and frequent rework can decrease the production rate.
These factors are not exhaustive, and other project-specific factors may also affect the production rate. It is crucial for project managers to analyze these factors and make adjustments to their estimates and plans accordingly. Additionally, understanding how to accurately calculate the production rate is essential to ensuring efficient resource allocation and project management. In the next section, we will explore the steps involved in calculating the production rate in construction.
Steps to Calculate Production Rate in Construction
Calculating the production rate in construction requires a systematic approach that takes into account the relevant factors and measurements. By following these steps, project managers can estimate the production rate with greater accuracy. Let’s explore the steps involved in calculating the production rate:
- Define the Work Unit: Start by identifying the specific work unit that you want to measure. This could be tasks such as pouring concrete, installing pipes, or laying bricks.
- Determine the Quantity of Work: Next, determine the quantity of work completed within a specific timeframe. This could be measured in terms of volume, length, or area, depending on the nature of the work unit. For example, if measuring concrete pouring, it could be cubic yards of concrete poured per hour.
- Calculate the Timeframe: Determine the timeframe over which the work was completed. This could be an hour, a day, a week, or any other relevant time period.
- Divide the Quantity by the Timeframe: Divide the quantity of work completed by the timeframe to get the average production rate per unit of time. For example, if 100 cubic yards of concrete were poured in 4 hours, the average production rate would be 25 cubic yards per hour.
- Consider Efficiency and Factors Affecting Production: Take into account the efficiency of the workforce and the factors that can affect the production rate, such as worker skill level, resource availability, project complexity, and site conditions. Adjust the calculated average production rate accordingly to reflect the expected productivity.
- Consider Variations and Improvement Opportunities: Analyze any variations in the production rate based on different factors and conditions. Identify areas for improvement and implement strategies to optimize productivity and increase the production rate.
It’s important to note that the steps mentioned above provide a general framework for calculating the production rate. The specific measurements, units, and calculations may vary depending on the nature of the construction task and the project requirements.
Additionally, it is recommended to track the actual production rate continuously and compare it with the planned rate to ensure that the project stays on track. This will provide valuable insights into the project’s progress and help identify any deviations or areas for improvement.
Now that we understand the steps involved in calculating the production rate, let’s put this knowledge into practice with an example calculation.
To calculate production rate in construction, divide the total quantity of work by the total labor hours. This will give you the production rate in units per hour.
Read more: How To Calculate A Construction In Progress
Example Calculation
Let’s walk through an example to illustrate how to calculate the production rate in construction.
Suppose we have a construction project that involves installing electrical wiring. Our goal is to determine the production rate in terms of linear feet of wiring installed per hour.
First, we define the work unit as the installation of electrical wiring.
Next, we need to determine the quantity of work completed within a specific timeframe. Let’s assume that in a 4-hour period, 800 linear feet of wiring were successfully installed.
To calculate the production rate, we divide the quantity of work (800 linear feet) by the timeframe (4 hours).
Production Rate = Quantity of Work / Timeframe = 800 linear feet / 4 hours = 200 linear feet per hour.
Based on this calculation, the average production rate for the installation of electrical wiring is 200 linear feet per hour.
However, it’s important to consider the efficiency of the workforce and any factors that can influence the production rate. For example, if the workforce is inexperienced or if there are challenges such as inaccessible areas or complex wiring configurations, we may need to adjust the production rate to reflect the expected productivity.
By continuously monitoring the actual production rate and making improvements where necessary, project managers can ensure that the project stays on track and productivity is maximized.
Now that we have seen an example of calculating the production rate, let’s explore some limitations and considerations to keep in mind.
Limitations and Considerations
While calculating the production rate in construction can provide valuable insights, it is important to be aware of its limitations and consider certain factors. Here are some limitations and considerations to keep in mind:
- Variability: The production rate can vary based on factors such as worker skill level, project complexity, resource availability, and site conditions. It is important to account for these variations and adjust the production rate calculation accordingly.
- Changing Conditions: Construction projects are dynamic, and conditions can change over time. External factors such as weather conditions, unexpected delays, or design changes can impact the production rate. Regularly reassessing and recalculating the production rate based on the current conditions is essential.
- Data Accuracy: The accuracy of the production rate calculation relies on the accuracy of the data collected. It is important to ensure that the quantity of work completed and the timeframe for calculation are accurately recorded to obtain reliable results.
- Realistic Expectations: The calculated production rate represents an average based on the quantity of work completed within a specific timeframe. It is important to set realistic expectations and consider the limitations and constraints of the project. Unrealistic productivity goals can lead to burnout, quality issues, or inefficiencies.
- Technology and Process Improvements: Calculating the production rate is based on the current processes and technologies utilized. However, advancements in construction technologies and process improvements can significantly increase productivity over time. It is important to continuously explore and implement innovative solutions to enhance the production rate.
- Worker Collaboration: The production rate is influenced not only by individual worker productivity but also by the collaboration and coordination among the construction team. Effective communication, teamwork, and a positive work environment can improve productivity and subsequently increase the production rate.
- Learning Curve: For new projects or processes, there may be a learning curve for workers to become efficient and accustomed to the specific tasks. The production rate may be lower initially but can improve as workers gain experience and familiarity with the work.
Considering these limitations and factors is crucial for accurately assessing and utilizing the production rate calculations in construction. By recognizing these considerations, project managers can make informed decisions, set realistic goals, and effectively manage construction projects.
Next, let’s explore the benefits of accurately calculating the production rate in construction.
Benefits of Accurate Production Rate Calculation
Accurately calculating the production rate in construction offers several benefits that can positively impact project management, resource allocation, and overall project success. Let’s explore some of the key benefits:
- Enhanced Project Planning: Accurate production rate calculations provide project managers with valuable insights for effective project planning. They can set realistic project schedules, allocate resources appropriately, and establish achievable milestones. This ensures that projects are completed on time and within budget.
- Optimized Resource Allocation: By understanding the production rate, project managers can effectively allocate resources such as labor, equipment, and materials. They can ensure that the right resources are available at the right time, avoiding shortages or overutilization. This leads to improved productivity, reduced costs, and minimized project delays.
- Improved Cost Control: Accurate production rate calculations allow for better cost control in construction projects. By understanding the pace of work, project managers can estimate labor and material costs more accurately. This enables them to prepare realistic budgets, monitor expenses effectively, and avoid unexpected cost overruns.
- Early Identification of Issues: Monitoring the actual production rate against the planned rate helps project managers identify any deviations or issues early on. This allows them to take corrective measures promptly, preventing delays and ensuring that the project stays on track. It also provides an opportunity to address inefficiencies, improve processes, and enhance overall productivity.
- Increased Productivity: Accurately calculating the production rate enables construction professionals to identify areas for improvement and implement strategies to enhance productivity. By setting targets based on achievable production rates, workers can be motivated to work efficiently, resulting in increased productivity, streamlined processes, and improved performance.
- Client Satisfaction: Accurate production rate calculation directly impacts the timely completion of construction projects. Meeting project timelines and delivering projects on time enhances client satisfaction and builds a positive reputation for the construction company. Satisfied clients are more likely to provide referrals and repeat business in the future.
- Improved Decision-Making: Having accurate production rate calculations provides project managers with valuable data for informed decision-making. They can evaluate the impact of design changes, resource reallocation, or process improvements on the production rate. This helps in making sound decisions that maximize productivity, minimize risks, and optimize project outcomes.
By leveraging the benefits of accurate production rate calculations, construction professionals can effectively manage projects, improve resource utilization, control costs, and deliver high-quality results. It fosters efficiency, productivity, and client satisfaction, ultimately contributing to the success of construction projects.
Now, let’s wrap up our discussion on calculating production rate in construction.
Conclusion
Calculating the production rate in construction is a crucial aspect of project management and resource allocation. It allows project managers to estimate project timelines, allocate resources effectively, and make informed decisions that optimize efficiency and productivity. By understanding the factors influencing the production rate and following a systematic approach, construction professionals can accurately estimate and monitor the pace of work.
Throughout this article, we explored the definition of production rate and its significance in construction. We discussed the importance of calculating the production rate for effective project planning, resource allocation, and budget control. Additionally, we examined the key factors that can affect the production rate, such as worker skill level, resource availability, and project complexity.
We then delved into the steps involved in calculating the production rate, emphasizing the need to define the work unit, determine the quantity of work, calculate the timeframe, and consider efficiency and influencing factors. We also highlighted the limitations and considerations associated with production rate calculations, such as variations in productivity, changing conditions, and data accuracy.
Accurately calculating the production rate provides several benefits, including enhanced project planning, optimized resource allocation, improved cost control, early issue identification, increased productivity, client satisfaction, and improved decision-making. By leveraging these benefits, construction professionals can successfully manage projects, meet timelines, control costs, and deliver high-quality results.
In conclusion, calculating the production rate in construction is an essential tool for efficient project management. By accurately estimating and monitoring the pace of work, construction professionals can make informed decisions, optimize resource utilization, and ensure the successful completion of construction projects.
So, whether you are a project manager, contractor, or stakeholder in the construction industry, understanding how to calculate the production rate can significantly contribute to the success of your projects. Embrace the power of accurate production rate calculations and unlock the potential to maximize productivity and achieve project goals.
Frequently Asked Questions about How To Calculate The Construction Productivity Rate
Was this page helpful?
At Storables.com, we guarantee accurate and reliable information. Our content, validated by Expert Board Contributors, is crafted following stringent Editorial Policies. We're committed to providing you with well-researched, expert-backed insights for all your informational needs.
0 thoughts on “How To Calculate The Construction Productivity Rate”