Home>diy>Building & Construction>What Does Fabrication Mean In Construction
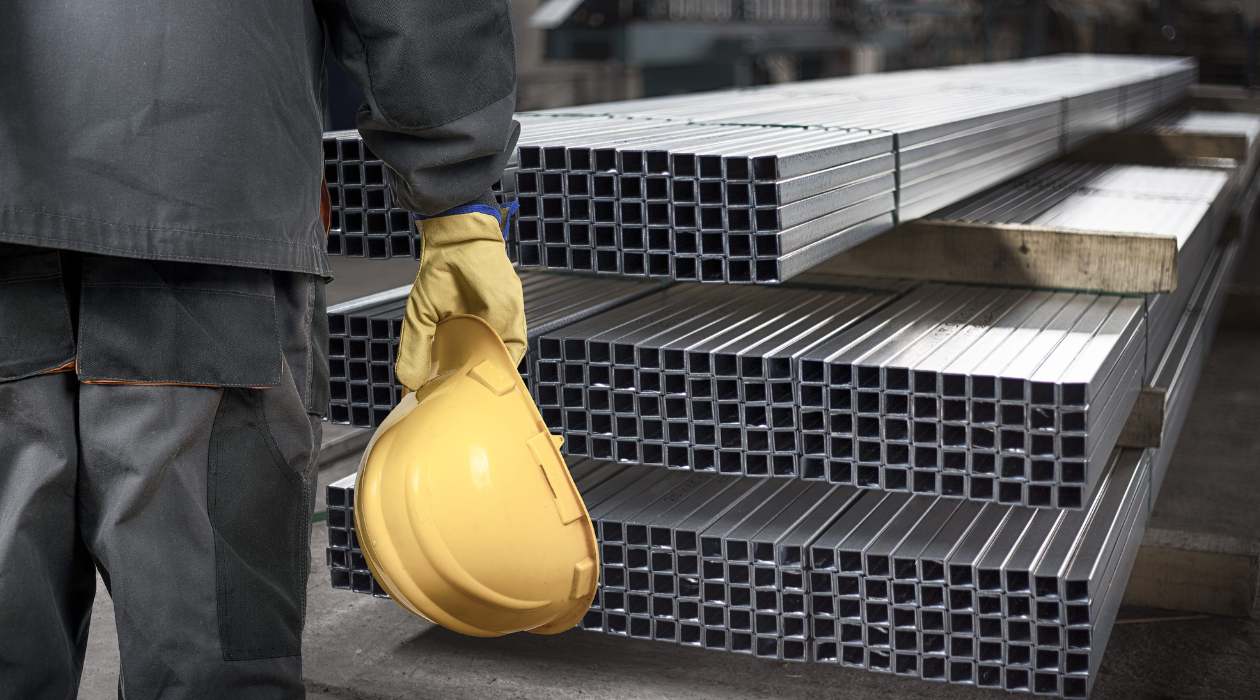
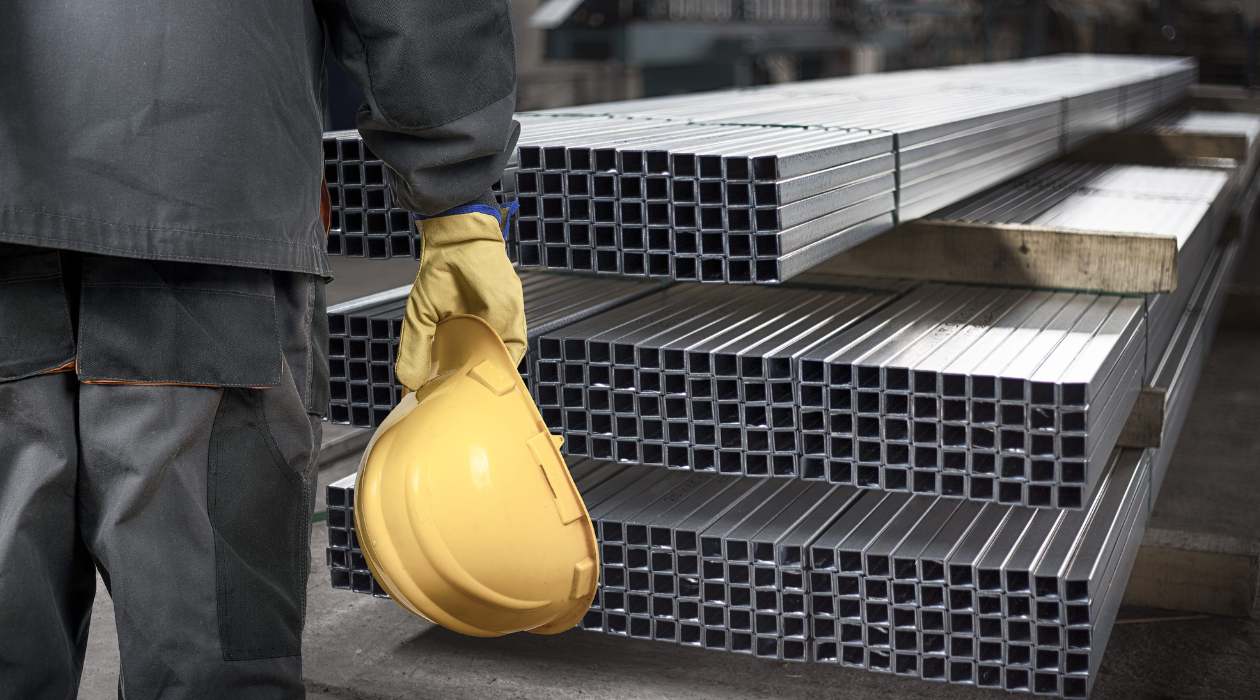
Building & Construction
What Does Fabrication Mean In Construction
Modified: October 18, 2024
Find out what the term "fabrication" means in the context of building construction and how it plays a crucial role in the construction process.
(Many of the links in this article redirect to a specific reviewed product. Your purchase of these products through affiliate links helps to generate commission for Storables.com, at no extra cost. Learn more)
Introduction
In the world of construction, the process of fabrication plays a crucial role in bringing architectural designs to life. Fabrication involves the creation of components or structures by combining various raw materials, such as metal, wood, or concrete, through cutting, shaping, and assembling processes.
With advancements in technology and increased demand for sustainable and efficient construction methods, fabrication has become an integral part of the construction industry. It allows for precision engineering, customization, and faster construction times, leading to cost savings and enhanced project outcomes.
In this article, we will delve into the meaning of fabrication in construction, explore its importance, discuss different types of fabrication processes, highlight the advantages and challenges involved, examine recent innovations, present case studies of successful implementation, and provide insights into future trends.
So let’s dive in and uncover the world of fabrication in construction.
Key Takeaways:
- Fabrication in construction involves creating precise components, offering customization, cost savings, and enhanced safety. It revolutionizes project efficiency and quality control, shaping the future of construction projects.
- Recent innovations in fabrication, such as BIM, robotic fabrication, and 3D printing, have transformed the industry. Successful case studies showcase fabrication’s effectiveness, while future trends promise further innovation, efficiency, and sustainability in construction.
Definition of Fabrication in Construction
Fabrication in construction refers to the process of creating components or structures by manipulating and combining raw materials. It involves various techniques, such as cutting, bending, welding, and assembling, to manufacture parts that will be used in the construction of buildings, bridges, roads, and other infrastructure projects.
The raw materials used in fabrication can vary depending on the desired end product. The most commonly used materials include metals (such as steel and aluminum), wood, concrete, and composite materials. These materials are transformed through fabrication processes to meet design specifications and project requirements.
Fabrication is often carried out in specialized facilities known as fabrication shops or workshops. These facilities are equipped with machinery, tools, and skilled workers who are trained in the specific techniques required for various fabrication processes.
The goal of fabrication in construction is to produce high-quality, durable, and precise components that can be easily incorporated into the overall construction project. This requires careful planning, expertise in material selection, and adherence to design specifications and building codes.
Fabrication in construction is not limited to creating small components; it can also involve the production of large-scale structures. For example, in the construction of bridges, fabrication may include creating beams, girders, and trusses, which are then transported to the construction site for assembly.
The fabrication process in construction involves several stages, including material procurement, preparation, cutting and shaping, assembly or joining, and finishing. Each stage requires specialized knowledge, skills, and equipment to ensure the final product meets design requirements and passes quality control standards.
Overall, fabrication in construction is a vital process that enables the efficient and precise creation of components and structures necessary for building construction. It combines artistry, engineering principles, and advanced technology to transform raw materials into functional and aesthetically pleasing elements of the built environment.
Importance of Fabrication in Construction
Fabrication plays a crucial role in the construction industry and offers several key benefits. Let’s explore why fabrication is important in construction:
- Precision Engineering: Fabrication allows for precise cutting, shaping, and assembly of components, ensuring that each piece fits together perfectly. This precision engineering improves the overall quality and functionality of the construction project.
- Customization: Fabrication offers immense flexibility in terms of customization. It allows architects and engineers to design and create unique components tailored to specific project requirements, ensuring both functionality and aesthetics are met.
- Efficiency and Time Savings: The use of fabrication methods enables construction projects to be completed more efficiently and within shorter timeframes. Prefabricated components can be fabricated off-site and then transported to the construction site for installation, minimizing on-site labor and reducing construction time.
- Cost Savings: Fabrication can result in significant cost savings due to reduced on-site labor, improved project efficiency, and better utilization of materials. In addition, the ability to customize components can lead to optimized designs and material usage, further reducing costs.
- Quality Control: Fabrication allows for rigorous quality control throughout the manufacturing process, ensuring that each component meets the required standards and specifications. This helps minimize the risk of on-site errors and inconsistencies, improving the overall quality of the construction project.
- Enhanced Safety: Fabrication can contribute to improved safety in construction projects. By prefabricating components off-site, potential hazards and risks associated with on-site construction activities are reduced. This helps create a safer working environment for construction workers.
Overall, the importance of fabrication in construction cannot be overstated. It provides the means to achieve precision, customization, efficiency, cost savings, and quality control in the construction process. By leveraging fabrication techniques, construction projects can be completed more effectively, resulting in higher quality structures that meet the specific needs and requirements of each project.
Types of Fabrication Processes in Construction
There are several different types of fabrication processes used in the construction industry. Each process is unique and suited for specific materials and project requirements. Let’s explore some common types of fabrication processes:
- Structural Steel Fabrication: This process involves the fabrication of steel components used in structural frameworks, such as beams, columns, and trusses. Structural steel fabrication typically includes cutting, drilling, welding, and assembly to create large-scale structural elements.
- Precast Concrete Fabrication: Precast concrete fabrication involves the creation of precast components, such as walls, slabs, and architectural elements, in a controlled environment. The precast components are manufactured off-site and then transported to the construction site for installation.
- Wood Fabrication: Wood fabrication is commonly used in construction for creating wooden structures and components. This process involves cutting, shaping, and assembling wood pieces to form beams, columns, trusses, panels, and decorative elements.
- Sheet Metal Fabrication: Sheet metal fabrication refers to the creation of components from thin metal sheets, such as steel, aluminum, or copper. This process involves cutting, bending, welding, and assembling the metal sheets to produce various components, including ductwork, enclosures, and architectural features.
- Composite Fabrication: Composite fabrication involves the combination of different materials, such as carbon fiber, fiberglass, and resin, to create lightweight and high-strength components. This process is commonly used in industries where weight reduction and durability are essential, such as aerospace and marine construction.
- Glass Fabrication: Glass fabrication encompasses processes, such as cutting, grinding, drilling, and tempering, to create glass components, including windows, doors, facades, and decorative glass elements. Glass fabrication requires precision and specialized techniques to ensure the desired transparency, strength, and visual aesthetics.
It is worth mentioning that many fabrication processes can be combined to create intricate and complex components. For example, a construction project may require the integration of both steel and concrete fabrication techniques to produce a composite structure.
Each type of fabrication process requires specific knowledge, skills, and equipment. Expertise and experience in these processes are crucial for achieving the desired results in terms of quality, precision, and efficiency.
Overall, the diverse range of fabrication processes available in construction enables the creation of a wide variety of components and structures, catering to the unique needs and specifications of each project.
Advantages of Fabrication in Construction
Fabrication brings numerous advantages to the construction industry, revolutionizing the way buildings and infrastructure projects are designed and constructed. Let’s explore some key advantages of fabrication in construction:
- Cost Savings: Fabrication can lead to significant cost savings in construction projects. The off-site fabrication of components allows for better material utilization and reduced wastage. Additionally, the streamlined process and efficient use of resources help minimize labor costs, as skilled workers can focus on the fabrication process instead of time-consuming on-site construction tasks.
- Increased Project Efficiency: Fabrication improves project efficiency by reducing construction time and enhancing productivity. Prefabricated components can be manufactured in parallel with site preparation, leading to faster project completion. The use of standardized fabrication techniques and quality control ensures consistent and predictable results, minimizing delays and rework.
- Improved Quality Control: Fabrication allows for stringent quality control measures to be implemented throughout the manufacturing process. Off-site fabrication in controlled environments allows for better monitoring and adherence to design specifications. This helps to minimize errors and ensures that each component meets the necessary quality standards, resulting in a higher-quality end product.
- Flexibility in Design and Customization: Fabrication offers unparalleled flexibility in design and customization. Architects and engineers can create complex and unique components that cater to specific project requirements. This allows for the realization of innovative designs, diverse architectural styles, and the incorporation of sustainable features, enhancing the overall aesthetic appeal and functional performance of the project.
- Enhanced Safety: Fabrication promotes improved safety conditions in construction projects. By prefabricating components off-site, potential hazards and risks associated with on-site construction activities are reduced. This includes minimizing the need for working at heights, reducing exposure to weather-related hazards, and implementing standardized safety protocols in fabrication facilities.
- Environmental Benefits: Fabrication can have positive environmental impacts. The controlled manufacturing environment allows for better recycling and waste management practices. Additionally, the use of prefabricated components reduces on-site construction waste and noise pollution, minimizing the project’s carbon footprint.
The advantages of fabrication in construction contribute to improved project outcomes, including cost-effectiveness, faster completion times, higher quality standards, and enhanced safety measures. Fabrication has become an essential component of modern construction practices, providing a range of benefits that drive innovation, efficiency, and sustainability in the industry.
Fabrication in construction refers to the process of creating structural components off-site, such as steel beams or precast concrete panels. This can help save time and improve quality control on the construction site.
Read more: What Does Turnkey Mean In Construction
Challenges and Limitations of Fabrication in Construction
While fabrication brings significant benefits to the construction industry, it also presents certain challenges and limitations that need to be addressed. Let’s explore some common challenges and limitations of fabrication in construction:
- Design Complexity: Highly complex designs and unique architectural features can pose challenges in fabrication. The fabrication process must be carefully planned and executed to ensure that intricate components are manufactured accurately and efficiently.
- Transportation and Logistics: Fabricated components need to be transported from the fabrication facility to the construction site. The transportation logistics, including size constraints, weight limitations, and coordination with transportation providers, can present challenges, especially for large-scale or heavy components.
- Limited Flexibility: Although fabrication offers customization, there may be limitations in terms of flexibility during the construction phase. Changes or modifications to fabricated components may be more difficult and costly to implement compared to on-site construction, where adjustments can be made more readily.
- Skilled Workforce: Fabrication requires a skilled workforce with expertise in specific fabrication processes. However, there is a shortage of skilled workers in certain regions, which can result in delays or compromised quality if not addressed adequately.
- Site Constraints and Integration: Incorporating fabricated components into the construction site can present challenges when dealing with existing structures or site-specific conditions. Retrofitting or integrating prefabricated elements requires careful planning, coordination, and expertise.
- Cost Considerations: While fabrication can result in cost savings, the initial investment in equipment, facilities, and training can be significant. This may not be feasible or economical for smaller-scale construction projects or for organizations that do not have a consistent pipeline of projects to justify the investment.
- Quality Control: Maintaining quality control throughout the fabrication process requires rigorous inspection and adherence to standards. The quality of fabricated components heavily relies on the expertise and diligence of the fabrication team. Failure to meet quality requirements can result in rework, delays, and compromised project outcomes.
- Material Limitations: Different fabrication processes have limitations in terms of the materials that can be effectively used. Certain materials may not be suitable for fabrication due to their properties, cost, or availability. It is crucial to select the appropriate materials that align with the project design and performance requirements.
Addressing these challenges and limitations requires careful planning, collaboration, and expertise. It is essential to conduct thorough assessments, establish clear communication channels between stakeholders, and invest in training and development to overcome these challenges and maximize the benefits of fabrication in construction projects.
Recent Innovations in Construction Fabrication
The construction industry has witnessed significant advancements and innovations in fabrication techniques and technologies in recent years. These innovations have revolutionized the way buildings and infrastructure projects are designed, fabricated, and constructed. Here are some notable recent innovations in construction fabrication:
- Building Information Modeling (BIM): BIM is a digital modeling technology that allows for the creation and management of detailed 3D models of buildings and construction projects. BIM has transformed the fabrication process by enabling seamless collaboration between architects, engineers, and fabricators. It allows for the integration of design, fabrication, and construction data, improving accuracy, coordination, and efficiency throughout the project lifecycle.
- Robotic Fabrication: Robots are increasingly being used in fabrication processes, automating tasks such as cutting, welding, and assembling. Robotic fabrication offers precision, speed, and repeatability, reducing human error and enhancing efficiency. Robotic arms and advanced algorithms enable the fabrication of complex geometries, resulting in unique architectural designs and structural elements.
- 3D Printing: 3D printing, also known as additive manufacturing, has revolutionized the fabrication process. It allows for the direct creation of 3D objects layer by layer, using materials such as concrete, plastics, and metals. 3D printing offers the potential for cost-effective and faster fabrication, especially for intricate and customized components. It also enables the use of sustainable materials and reduces material wastage.
- Prefabrication and Modular Construction: Prefabrication and modular construction have gained popularity due to their speed, cost-effectiveness, and sustainability. This approach involves the manufacturing of building components off-site in controlled environments, allowing for faster project completion and reduced on-site disruption. Prefabrication and modular construction enable higher quality control, efficient material usage, and improved sustainability through the integration of renewable energy systems and green building practices.
- Collaborative Design and Fabrication Platforms: Collaborative platforms and cloud-based software have transformed the way design and fabrication teams work together. These platforms facilitate real-time collaboration, communication, and sharing of design and fabrication data, enhancing coordination and reducing errors. They enable seamless integration between architects, engineers, fabricators, and contractors, resulting in streamlined processes and improved project outcomes.
- Advanced Materials: The development and use of advanced materials have expanded the possibilities in construction fabrication. Examples include high-strength concrete, fiber-reinforced polymers, and composites. These materials offer improved performance, durability, and sustainability, enabling the creation of lighter and stronger structures.
These recent innovations in construction fabrication have transformed the industry, emphasizing efficiency, precision, sustainability, and customization. By embracing these technologies and techniques, the construction industry continues to push boundaries and deliver innovative projects that meet evolving demands and challenges.
Case Studies: Successful Implementation of Fabrication in Construction Projects
Several construction projects have successfully implemented fabrication techniques, showcasing the benefits and potential of this approach. Let’s explore some noteworthy case studies:
- One World Trade Center: The iconic One World Trade Center in New York City is a prime example of successful fabrication implementation. Fabrication played a crucial role in the construction of the building’s steel frame, comprised of more than 42,000 tons of steel components. The off-site fabrication of the steel allowed for precise manufacturing and efficient installation, resulting in the completion of the tower on schedule and within budget.
- Offsite Construction of Hospitals: Many healthcare facilities have embraced fabrication methods to expedite construction timelines and improve project efficiency. For instance, the Royal Adelaide Hospital in Australia used off-site modular construction for the delivery of patient rooms, bathrooms, and corridors. This approach significantly reduced on-site construction time and disruption, allowing the hospital to be operational more quickly.
- London Olympic Velodrome: The London Olympic Velodrome, designed for the 2012 Summer Olympics, utilized advanced fabrication techniques for its iconic roof structure. The roof was constructed using over 1800 steel sections, which were precisely fabricated off-site and then assembled on-site. This approach allowed for efficient construction and created the distinctive curved roof design that is now an architectural focal point.
- Modular Construction of Student Housing: Modular construction has gained traction in the construction of student housing projects. Universities and institutions have leveraged modular fabrication to create high-quality and cost-effective accommodations for students. One notable example is the University of California, Berkeley, where prefabricated modules were used to construct student housing units quickly and efficiently, meeting the growing demand for on-campus residences.
- Airport Terminal Expansion: Fabrication has been instrumental in airport terminal expansions, providing rapid construction and minimal disruption to ongoing operations. The Hong Kong International Airport Terminal 1 expansion project utilized off-site fabrication techniques for various components, including structural steel frames and precast concrete panels. This approach allowed for seamless integration with the existing terminal while minimizing construction time.
These case studies demonstrate the successful implementation of fabrication in construction projects of varying scale and complexity. The utilization of fabrication techniques, such as off-site construction, modular fabrication, and precise steel fabrication, has resulted in improved project outcomes, including cost savings, accelerated construction timelines, and enhanced quality and safety.
These success stories highlight the potential and effectiveness of fabrication methods in achieving efficient, sustainable, and innovative construction projects.
Future Trends and Outlook for Fabrication in Construction
The field of fabrication in construction is continuously evolving, driven by technological advancements and the need for more efficient and sustainable construction methods. Here are some future trends and outlook for fabrication in construction:
- Advanced Robotics and Automation: The use of advanced robotics and automation in fabrication processes is expected to increase. Collaborative robots, machine learning algorithms, and artificial intelligence will enhance efficiency and precision in fabrication. Robots will be capable of performing complex tasks, such as 3D printing, welding, and assembly, reducing reliance on manual labor and improving the overall productivity of the construction industry.
- Scaling Up 3D Printing: 3D printing, or additive manufacturing, is poised to transform the construction industry. Large-scale 3D printers will become more prevalent, capable of fabricating entire buildings or major components on-site. This technology offers the potential to reduce construction time, improve design freedom, and minimize material waste, leading to a more sustainable and cost-effective construction process.
- Integration of Internet of Things (IoT): The integration of IoT devices and sensors in fabricated components will enable real-time monitoring of structural health, energy efficiency, and maintenance needs. This data-driven approach will enable predictive maintenance, optimize building performance, and enhance the lifespan of constructed assets.
- Sustainable and Green Fabrication: There will be an increasing focus on sustainable and green fabrication practices. This includes the use of eco-friendly materials, energy-efficient processes, and recycling and waste reduction measures. Fabrication techniques will aim to minimize the environmental impact of construction, aligning with global efforts to combat climate change and promote sustainable development.
- Modular Construction and Plug-and-Play Systems: Modular construction will continue to gain traction, driven by the need for faster and more efficient project delivery. Plug-and-play systems, where fabricated components can be easily interconnected and reconfigured, will allow for adaptable and scalable construction, enabling buildings to evolve and respond to changing needs over time.
- Integration of Augmented Reality (AR) and Virtual Reality (VR): AR and VR technologies will revolutionize the fabrication process by enabling immersive visualization, simulation, and training. Fabricators will be able to visualize the end product in a virtual environment and identify design flaws or constructability issues before fabrication begins. This will result in improved accuracy, reduced rework, and enhanced collaboration among project stakeholders.
The future of fabrication in construction holds immense potential for innovation, efficiency, and sustainability. Embracing these future trends will enable the construction industry to overcome existing challenges, optimize project outcomes, and deliver buildings and infrastructure that are safer, more resilient, and environmentally friendly.
Read more: What Does “Level” Mean In Construction
Conclusion
Fabrication has become an essential process in the construction industry, offering numerous benefits and shaping the future of construction projects. It enables precise engineering, customization, and cost savings while improving project efficiency, quality control, and safety. The different types of fabrication processes, including structural steel, precast concrete, wood, sheet metal, composite, and glass fabrication, provide a wide range of options to meet project requirements.
Recent innovations in fabrication techniques have further transformed the industry. Building Information Modeling (BIM), robotic fabrication, 3D printing, prefabrication, and collaborative design platforms have revolutionized the way buildings are designed, fabricated, and constructed. These advancements have resulted in faster construction timelines, cost savings, enhanced quality, and sustainability.
Successful case studies around the world highlight the effectiveness of fabrication in various construction projects, including skyscrapers, hospitals, stadiums, student housing, and airport terminals. These case studies showcase the ability of fabrication to deliver projects on schedule, within budget, and with improved project outcomes.
The future of fabrication in construction holds even more promise, with trends such as advanced robotics, 3D printing, IoT integration, sustainable practices, modular construction, and augmented reality shaping the industry. These trends will foster innovation, efficiency, customization, and sustainability in construction projects.
In conclusion, fabrication plays a crucial role in the construction industry, providing the means to create precise components and structures. By embracing fabrication techniques and adopting future trends, the construction industry can achieve cost-effective, sustainable, and innovative projects that meet the evolving demands and challenges of the built environment.
Frequently Asked Questions about What Does Fabrication Mean In Construction
Was this page helpful?
At Storables.com, we guarantee accurate and reliable information. Our content, validated by Expert Board Contributors, is crafted following stringent Editorial Policies. We're committed to providing you with well-researched, expert-backed insights for all your informational needs.
0 thoughts on “What Does Fabrication Mean In Construction”