Home>diy>Building & Construction>What Does GMP In Construction Mean
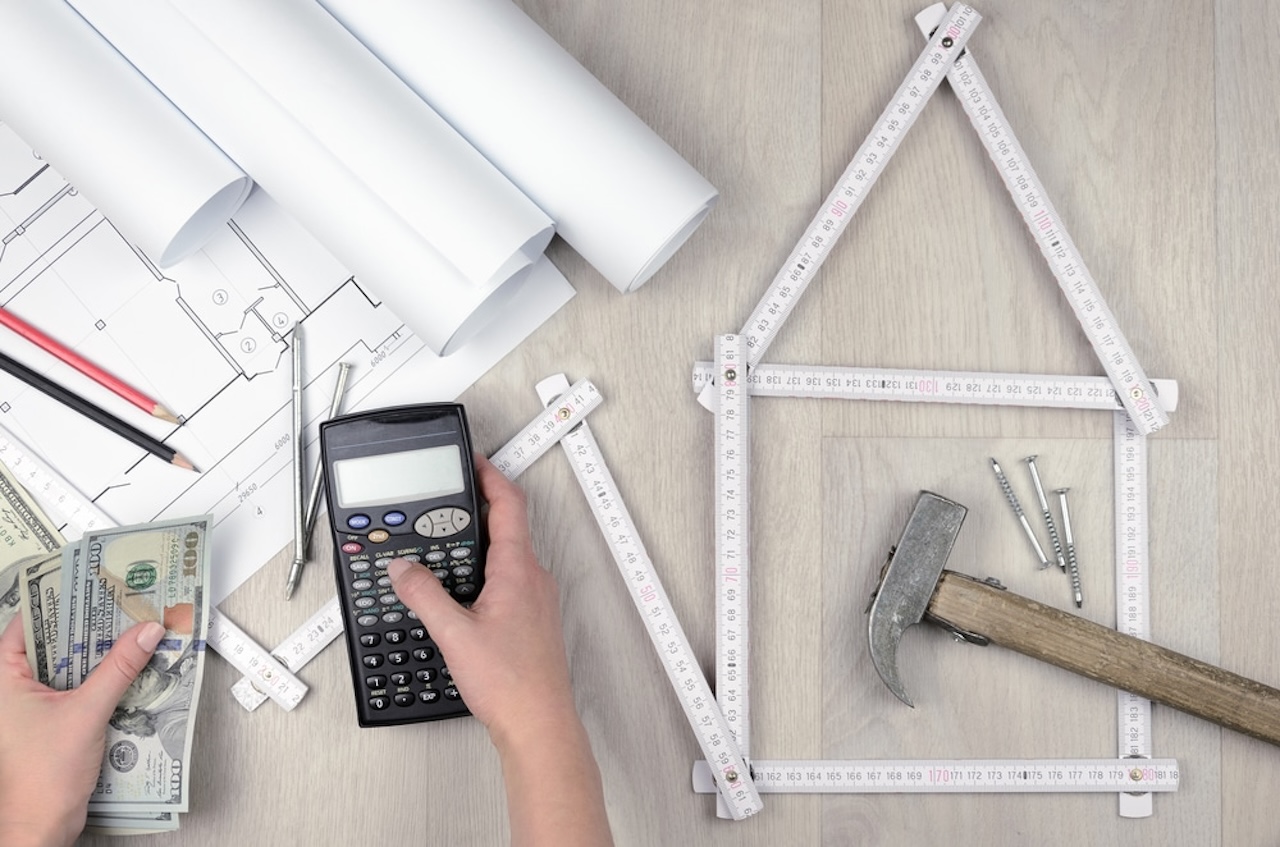
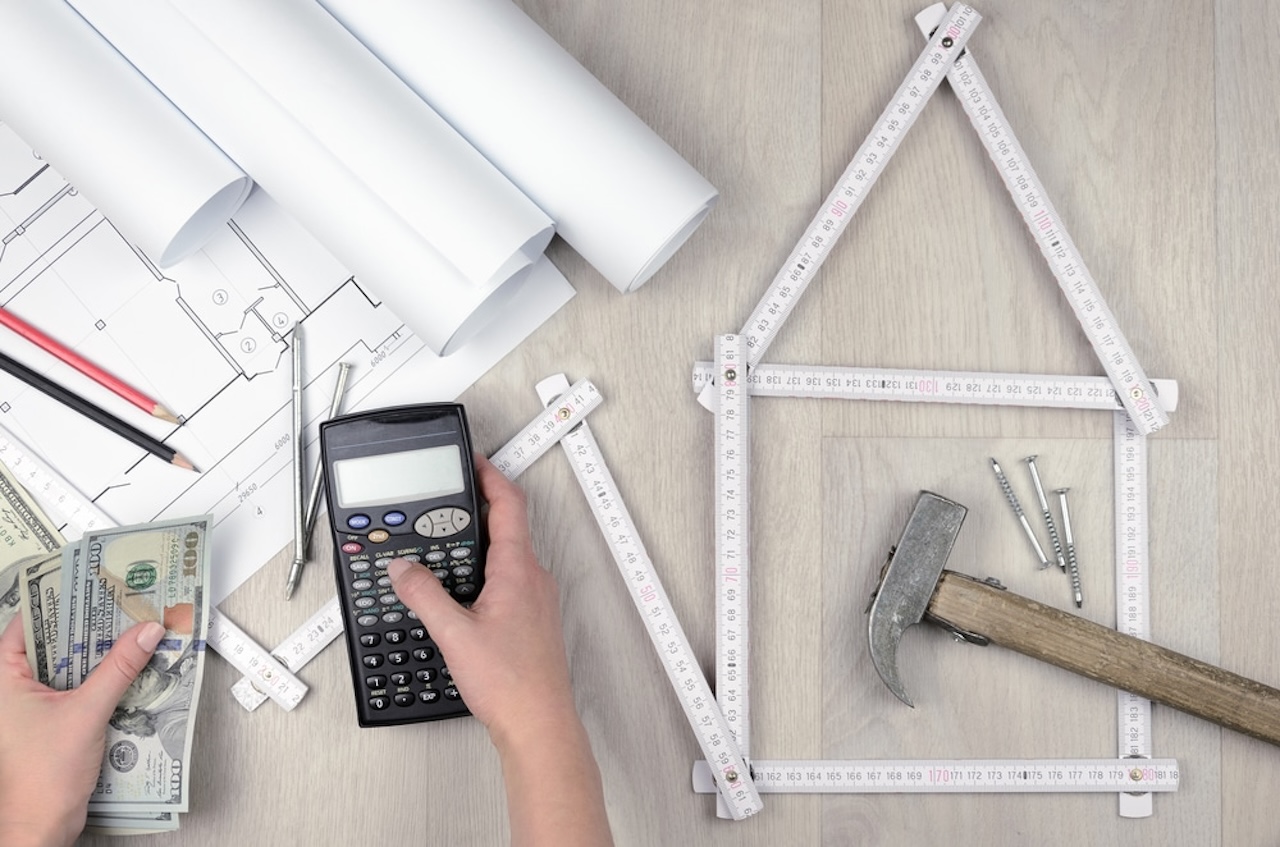
Building & Construction
What Does GMP In Construction Mean
Modified: February 25, 2024
Discover the meaning of GMP in construction and how it impacts building-construction processes. Gain insights into its importance and implementation.
(Many of the links in this article redirect to a specific reviewed product. Your purchase of these products through affiliate links helps to generate commission for Storables.com, at no extra cost. Learn more)
Introduction
Welcome to the world of construction! Building and construction projects play a significant role in shaping our infrastructure and society. From towering skyscrapers to intricate road networks, construction projects are a manifestation of human ingenuity and engineering excellence. However, behind every successful construction project lies a complex web of planning, coordination, and execution.
In the construction industry, it is crucial to ensure that projects are carried out with the highest standards of quality, safety, and efficiency. This is where GMP, or Good Manufacturing Practice, in construction comes into play. GMP in construction refers to a set of guidelines and protocols that ensure the quality and consistency of construction projects. It outlines the best practices to be followed by construction professionals to meet regulatory requirements and deliver projects that meet or exceed client expectations.
While GMP is commonly associated with manufacturing industries such as pharmaceuticals or food production, its principles can be adapted and applied to construction projects. The aim is to establish a systematic approach that guarantees the quality of materials, workmanship, and project management, leading to successful project outcomes.
In this article, we will delve deeper into the concept of GMP in construction, exploring its definition, purpose, benefits, key principles, implementation steps, challenges, and best practices. Whether you are a construction professional, project owner, or simply curious about the construction industry, this article will provide valuable insights into the world of GMP in construction.
Key Takeaways:
- GMP in construction ensures high-quality, safe, and efficient project outcomes by emphasizing standardization, quality assurance, and compliance with regulations. It benefits clients, construction companies, and the industry as a whole.
- Implementing GMP in construction comes with challenges such as resistance to change, project complexity, and cost constraints. Overcoming these challenges through proactive planning, education, and best practices is crucial for successful GMP compliance.
Read more: What Is GMP Construction
Definition of GMP in Construction
In the construction industry, GMP stands for Good Manufacturing Practice. While GMP is traditionally associated with manufacturing industries, such as pharmaceuticals or food production, it has gained traction in the construction sector as well. GMP in construction refers to a set of guidelines and protocols that ensure the quality, consistency, and integrity of construction projects.
At its core, GMP in construction encompasses a systematic approach to project planning, execution, and control. It emphasizes the use of standardized processes, quality materials, proper documentation, and adherence to regulatory standards and best practices.
GMP in construction encompasses all stages of a project, from the initial design and pre-construction phase to construction activities, and ultimately project completion. It covers various aspects, including project management, quality control, safety procedures, worker training, and documentation.
The primary goal of implementing GMP in construction is to ensure that the constructed facilities meet or exceed the required quality standards. By following GMP principles, construction professionals can mitigate risks, prevent costly rework, enhance project efficiency, and deliver high-quality outcomes.
GMP in construction not only benefits the project itself but also extends to the stakeholders involved. Clients benefit from having confidence in the quality of the end product, leading to increased satisfaction. Construction companies that adhere to GMP standards can enhance their reputation, improve client relationships, and ultimately achieve a competitive advantage in the industry.
Overall, GMP in construction serves as a framework that promotes excellence and quality in the construction industry, ensuring that projects are built to withstand the test of time, meeting the needs and expectations of clients and regulators alike.
Purpose of GMP in Construction
The purpose of implementing GMP (Good Manufacturing Practice) in construction is to ensure that construction projects are executed with the highest standards of quality, consistency, safety, and efficiency. It provides a structured framework that sets guidelines and protocols to be followed by construction professionals throughout the project lifecycle.
One of the primary purposes of GMP in construction is to ensure the quality of the constructed facilities. GMP principles emphasize the use of quality materials, proper workmanship, and adherence to industry standards and regulations. By implementing GMP, construction projects are less prone to defects, errors, and rework, resulting in a final product that meets or exceeds the desired quality standards.
Another purpose of GMP in construction is to promote consistency and standardization. GMP principles establish a set of documented processes and procedures that provide a reliable and uniform approach to project planning, execution, and control. This consistency helps to minimize variations and uncertainties, leading to smoother project outcomes and improved stakeholder satisfaction.
Safety is also a crucial aspect of GMP in construction. Construction sites are inherently hazardous, and it is essential to implement robust safety measures to protect workers and mitigate risks. GMP guidelines incorporate safety protocols, training requirements, and the use of appropriate personal protective equipment (PPE) to ensure a safe working environment. By prioritizing safety, GMP in construction helps prevent accidents, injuries, and potential legal issues.
Efficiency and productivity are key objectives of GMP in construction. By establishing standardized processes and best practices, GMP helps streamline project workflows, minimizing delays, and optimizing resource utilization. Efficient construction practices not only result in cost savings and timely project completion but also contribute to overall client satisfaction.
Furthermore, GMP in construction serves as a means of quality assurance and regulatory compliance. Many construction projects are subject to industry-specific regulations and codes. GMP provides a framework to ensure that projects adhere to these regulations, helping construction companies avoid legal challenges and potential fines.
In summary, the purpose of GMP in construction is to ensure that projects are executed with the highest level of quality, consistency, safety, and efficiency. It fosters client satisfaction, minimizes risks, promotes standardization, and enhances project outcomes. By adhering to GMP guidelines, construction professionals can deliver projects that meet regulatory requirements, exceed client expectations, and contribute to the overall advancement of the construction industry.
Benefits of Implementing GMP in Construction Projects
Implementing GMP (Good Manufacturing Practice) in construction projects offers several significant benefits, improving project outcomes and enhancing the overall construction process. From better quality control to improved efficiency, the advantages of GMP in construction are vast. Here are some key benefits:
1. Enhanced Quality Control: GMP ensures that construction projects are executed using high-quality materials and proper workmanship. By implementing quality control measures, such as inspections and checks, GMP helps prevent defects, errors, and non-compliance with industry standards. This results in a final product that meets or exceeds the desired quality standards.
2. Reduced Rework and Costs: Through its focus on quality and standardized processes, GMP minimizes the need for rework and corrective actions. This reduces project costs, including the expenses associated with fixing errors, replacing faulty materials, and dealing with project delays. GMP helps construction companies save time and money, resulting in improved profitability.
3. Improved Safety: GMP in construction prioritizes safety protocols and procedures. By implementing robust safety measures and providing adequate training, GMP helps prevent accidents, injuries, and fatalities on construction sites. This not only protects workers but also reduces potential legal issues and associated costs.
4. Streamlined Project Workflows: GMP promotes standardized processes and best practices, leading to streamlined project workflows. By establishing clear guidelines and protocols, GMP helps remove uncertainties and variations in project execution, resulting in smoother project outcomes. This improves communication, coordination, and collaboration among project stakeholders.
5. Enhanced Client Satisfaction: Clients benefit greatly from GMP implementation as it ensures that projects are delivered with high quality, consistency, and safety. By meeting or exceeding client expectations, GMP helps build trust and enhances client satisfaction. Satisfied clients are more likely to provide positive referrals and repeat business, contributing to the success and reputation of construction companies.
6. Compliance with Regulations and Standards: Many construction projects are subject to specific industry regulations and codes. GMP in construction ensures compliance with these regulations, reducing the risk of legal challenges and associated fines. By following GMP standards, construction companies demonstrate their commitment to regulatory compliance.
7. Competitive Advantage: Implementing GMP sets construction companies apart from their competitors. GMP certification or adherence to GMP guidelines provides a competitive advantage, as it demonstrates a commitment to quality, safety, and efficiency in project execution. This can help attract new clients, enhance the company’s reputation, and open doors to new business opportunities.
Overall, the benefits of implementing GMP in construction projects extend to all stakeholders involved. From improved project quality and safety to streamlined workflows and enhanced client satisfaction, GMP helps construction companies deliver successful projects while maintaining compliance with industry regulations and best practices.
Key Principles of GMP in Construction
GMP (Good Manufacturing Practice) in construction is based on several key principles that guide construction professionals in adhering to the highest standards of quality, consistency, and safety. These principles serve as a foundation for implementing and maintaining GMP in construction projects. Let’s explore some of the key principles:
1. Standardization: Standardization is a fundamental principle of GMP in construction. It emphasizes the use of standardized processes, procedures, and practices throughout the project lifecycle. This ensures consistency and minimizes variations, leading to predictable project outcomes.
2. Quality Assurance: Quality assurance is at the core of GMP in construction. It focuses on ensuring that projects are executed with the highest level of quality, meeting or exceeding the desired standards. Quality assurance involves quality control measures, inspections, and checks to identify and address any potential defects or deviations.
3. Documentation: Proper documentation is essential in GMP in construction. It involves creating and maintaining thorough and accurate records of project activities, including design documents, specifications, test reports, and change orders. Documentation allows for traceability, facilitates communication, and ensures accountability throughout the project.
4. Risk Management: GMP in construction incorporates risk management as an integral part of project planning and execution. It involves identifying potential risks, assessing their impact, and implementing appropriate control measures to mitigate or minimize those risks. Risk management helps prevent accidents, delays, and costly rework in construction projects.
5. Compliance with Regulations: GMP in construction emphasizes compliance with industry regulations, codes, and standards. It ensures that construction projects meet the required legal and regulatory requirements. By adhering to these requirements, construction professionals demonstrate their commitment to responsible and ethical practices.
6. Continuous Improvement: Continuous improvement is a key principle of GMP in construction. It involves regularly reviewing and evaluating project processes, identifying areas for improvement, and implementing corrective actions to enhance performance. Continuous improvement drives innovation, efficiency, and the overall advancement of the construction industry.
7. Stakeholder Collaboration: GMP in construction recognizes the importance of collaborative efforts among project stakeholders. It emphasizes effective communication, coordination, and collaboration among architects, engineers, contractors, subcontractors, and clients. By fostering collaboration, GMP ensures a shared understanding of project goals and facilitates a smooth project execution process.
8. Training and Competency: GMP in construction promotes training and competency development among construction professionals. It emphasizes the importance of ongoing training and skills development to ensure that individuals involved in construction projects have the necessary knowledge and expertise to perform their roles effectively.
These key principles of GMP in construction provide a guiding framework for construction professionals to follow. By embracing these principles, construction companies can ensure the highest level of quality, consistency, and safety throughout their projects, leading to successful outcomes and client satisfaction.
GMP in construction stands for Guaranteed Maximum Price, which is a contract between the owner and the contractor that sets a limit on the total cost of the project. This helps to provide cost certainty and minimize the risk of budget overruns.
Steps to Implement GMP in Construction Projects
Implementing GMP (Good Manufacturing Practice) in construction projects requires careful planning, coordination, and adherence to specific steps. These steps help construction professionals establish a framework for effectively implementing and maintaining GMP principles. Here are the key steps to implement GMP in construction projects:
1. Familiarize Yourself with GMP Principles: Before implementing GMP, it is essential to gain a thorough understanding of the principles and guidelines involved. Research and familiarize yourself with the key concepts, industry standards, and regulatory requirements related to GMP in construction.
2. Assess Current Processes and Procedures: Conduct an initial assessment of your current construction processes and procedures. Evaluate how closely they align with GMP principles. Identify areas where improvements can be made to enhance quality, consistency, and safety in your projects.
3. Develop Standard Operating Procedures (SOPs): Develop comprehensive Standard Operating Procedures (SOPs) based on GMP principles. These SOPs should outline the step-by-step processes to be followed at each stage of the project, from design to completion. SOPs should cover aspects such as planning, material selection, quality control, documentation, safety protocols, and communication.
4. Establish Documentation Practices: Implement robust documentation practices to ensure proper record-keeping and traceability throughout the project. Establish protocols for documenting design decisions, specifications, change orders, material test reports, inspection reports, and other relevant project documents. Maintain clear and organized records to facilitate transparency and accountability.
5. Implement Quality Control Measures: Incorporate quality control measures into your project workflows. Develop inspection and testing procedures to verify the quality of materials and workmanship. Conduct regular inspections at critical stages of the project to identify any deviations or non-compliance and take appropriate corrective actions.
6. Prioritize Safety: Safety should be a top priority in GMP implementation. Establish comprehensive safety protocols and procedures to protect workers and mitigate risks in construction projects. Conduct regular safety training for all personnel involved in the project and provide them with the necessary personal protective equipment (PPE).
7. Train and Educate Personnel: Conduct training programs to educate your staff about GMP principles and the specific SOPs and procedures you have established. Ensure that they understand the importance of GMP in construction and are trained to follow the prescribed processes and protocols.
8. Monitor and Measure Performance: Continuously monitor and measure the performance of your construction projects against the established GMP standards. Use Key Performance Indicators (KPIs) to assess project quality, adherence to SOPs, safety records, and client satisfaction. Regularly review performance data to identify areas for improvement.
9. Foster Continuous Improvement: Embrace a culture of continuous improvement within your organization. Encourage feedback from project teams and stakeholders, and use it to identify opportunities for enhancing processes, addressing challenges, and implementing best practices. Make adjustments to your SOPs and procedures based on lessons learned from previous projects.
10. Ensure Regulatory Compliance: Lastly, ensure that your construction projects comply with all relevant industry regulations, codes, and standards. Stay updated with the latest regulatory changes and incorporate them into your GMP implementation. Regularly review and audit your projects to ensure ongoing compliance.
By following these steps, construction professionals can successfully implement GMP in their projects, ensuring the highest standards of quality, consistency, safety, and client satisfaction.
Challenges in Implementing GMP in Construction
Implementing GMP (Good Manufacturing Practice) in construction projects can present unique challenges and complexities. It requires a concerted effort from all stakeholders involved. Recognizing and addressing these challenges is essential to ensure successful GMP implementation. Here are some common challenges in implementing GMP in construction:
1. Resistance to Change: A significant challenge in implementing GMP in construction is resistance to change. Construction professionals may be accustomed to traditional practices and may be hesitant to adopt new processes and procedures. Overcoming this resistance requires effective communication, training, and a clear explanation of the benefits of GMP implementation.
2. Lack of Awareness and Education: GMP may be a relatively new concept in the construction industry. Lack of awareness and education about GMP principles and their relevance to construction can hinder successful implementation. Providing adequate training and education to construction professionals about GMP and its benefits is crucial to overcome this challenge.
3. Complexity of Construction Projects: Construction projects are inherently complex, involving multiple stakeholders, diverse activities, and various regulatory requirements. The complexity of projects can make it challenging to implement GMP consistently across all stages of the project. It requires meticulous planning, coordination, and effective project management to ensure GMP principles are followed throughout.
4. Cost and Time Constraints: Implementing GMP in construction may involve additional costs and time requirements. It may require investing in quality materials, implementing additional quality control measures, and conducting training programs. Balancing these requirements with project budgets and timelines can be challenging. Construction companies need to carefully plan and budget for GMP implementation to minimize cost and schedule impacts.
5. Lack of Standardization in the Industry: The construction industry lacks standardized processes and practices compared to other industries. The absence of standardized approaches may pose challenges when implementing GMP and establishing uniform procedures across different projects and organizations. Encouraging industry-wide collaboration and promoting the adoption of standardized practices can help address this challenge.
6. Subcontractor Management: Construction projects often involve subcontractors who may have their own practices and procedures. Ensuring that subcontractors align with the GMP principles and adhere to established procedures can be a challenge. Effective subcontractor management, including clear communication, training programs, and contract agreements, is crucial to maintain GMP standards across all project stakeholders.
7. Scaling GMP for Different Project Sizes: GMP implementation needs to be scalable to accommodate projects of different sizes and complexities. What works for small-scale projects may not be suitable for large-scale projects and vice versa. Developing flexible procedures and tools that can be tailored to different project sizes is essential to address this challenge.
8. Continuous Compliance and Monitoring: Ensuring ongoing compliance with GMP principles throughout the project lifecycle can be challenging. It requires continuous monitoring, inspections, and compliance audits. Having a dedicated team responsible for monitoring compliance and implementing corrective actions is essential to maintain GMP standards.
While these challenges may seem daunting, they can be overcome with proper planning, education, communication, and stakeholder engagement. Addressing these challenges proactively is crucial to successfully implement GMP in construction projects and reap the benefits of quality, consistency, and stakeholder satisfaction.
Best Practices for Ensuring GMP Compliance in Construction Projects
Ensuring compliance with GMP (Good Manufacturing Practice) principles in construction projects requires the adoption of best practices that promote quality, consistency, and safety. By implementing these best practices, construction professionals can maintain GMP compliance throughout the project lifecycle. Here are some key best practices:
1. Establish a GMP Implementation Plan: Develop a comprehensive GMP implementation plan that outlines roles, responsibilities, and timelines for adopting GMP principles in construction projects. This plan should incorporate all stages of the project, from design to completion, and include procedures for documentation, quality control, safety, and training.
2. Promote Collaboration and Communication: Foster collaboration and communication among project stakeholders to ensure alignment with GMP principles. Encourage regular meetings and open communication channels to address any issues, share best practices, and maintain consistent adherence to GMP standards. Effective communication builds a shared understanding and commitment to GMP compliance.
3. Implement Robust Quality Control Measures: Develop and implement robust quality control measures to monitor and maintain compliance with GMP standards. Conduct inspections, tests, and audits at critical stages of the project to verify the quality of materials, workmanship, and adherence to specifications. Establish procedures for non-conformance management and corrective actions when deviations are identified.
4. Invest in Training and Education: Provide comprehensive training and education programs to ensure that all personnel involved in the project understand GMP principles and their relevance to construction. Training should cover topics such as quality control, safety protocols, documentation practices, and regulatory compliance. Regular refresher courses can help reinforce GMP knowledge and ensure ongoing compliance.
5. Maintain Comprehensive Documentation: Establish robust documentation practices to ensure proper record-keeping and traceability. Maintain clear and organized records of project activities, including design documents, specifications, change orders, inspection reports, and test records. Documenting deviations, corrective actions, and lessons learned helps identify areas for improvement and ensures regulatory compliance.
6. Conduct Regular Audits and Reviews: Regularly conduct audits and reviews to assess GMP compliance throughout the project. These audits should include a comprehensive evaluation of processes, practices, and documentation. Use the findings to identify gaps and implement corrective actions to maintain and improve GMP compliance.
7. Engage and Monitor Subcontractors: Ensure that subcontractors align with GMP principles and follow established procedures. Clearly communicate GMP requirements to subcontractors, including quality control measures, documentation practices, and safety protocols. Regularly monitor subcontractor performance, provide feedback, and address any non-compliance promptly.
8. Foster Continuous Improvement: Continuously strive for improvement by fostering a culture of continuous improvement within the organization. Encourage feedback from project teams and stakeholders and use it to identify opportunities for enhancing processes, addressing challenges, and implementing best practices. Regularly review and update SOPs and procedures based on lessons learned from previous projects.
9. Stay Updated with Regulations and Industry Standards: Keep abreast of the latest industry regulations, codes, and standards relevant to GMP compliance in construction. Regularly review and update procedures and practices to ensure ongoing compliance. Engage with industry associations and participate in relevant conferences and training programs to stay informed about industry best practices.
10. Utilize Technology and Digital Tools: Leverage technology and digital tools to streamline GMP compliance in construction projects. Utilize construction management software, project documentation tools, and quality control apps to enhance communication, documentation, and data management. These tools can improve efficiency, accuracy, and accessibility of GMP-related processes.
By adopting these best practices, construction professionals can ensure GMP compliance in their projects, promoting quality, consistency, and safety throughout the construction process, and ultimately achieving successful project outcomes.
Conclusion
Implementing GMP (Good Manufacturing Practice) in construction projects is crucial for ensuring the highest standards of quality, consistency, and safety. By following the key principles of GMP and implementing best practices, construction professionals can enhance project outcomes and deliver successful projects that meet or exceed client expectations.
GMP in construction encompasses a systematic approach to project planning, execution, and control. It emphasizes standardization, quality assurance, documentation, and compliance with regulations. By establishing comprehensive SOPs, implementing quality control measures, and prioritizing safety, construction projects can significantly benefit from GMP implementation.
The benefits of GMP in construction are numerous. It enhances quality control, reduces rework and costs, improves safety, streamlines project workflows, enhances client satisfaction, ensures regulatory compliance, and provides a competitive advantage in the industry.
However, implementing GMP in construction does come with challenges. Resistance to change, lack of awareness, project complexity, cost constraints, and subcontractor management are some of the common challenges that need to be overcome. By addressing these challenges proactively and following established best practices, construction professionals can navigate the path towards successful GMP compliance.
To ensure GMP compliance in construction projects, it is essential to establish a GMP implementation plan, promote collaboration and communication, implement robust quality control measures, invest in training and education, maintain comprehensive documentation, conduct regular audits and reviews, engage and monitor subcontractors, foster continuous improvement, stay updated with regulations, and leverage technology and digital tools.
In conclusion, GMP in construction is a valuable framework that promotes excellence, quality, and safety in construction projects. By implementing GMP, construction professionals can enhance project outcomes, mitigate risks, and build a reputation for delivering high-quality projects. GMP compliance not only benefits the construction industry but also contributes to the advancement of infrastructure and society as a whole.
Frequently Asked Questions about What Does GMP In Construction Mean
Was this page helpful?
At Storables.com, we guarantee accurate and reliable information. Our content, validated by Expert Board Contributors, is crafted following stringent Editorial Policies. We're committed to providing you with well-researched, expert-backed insights for all your informational needs.
0 thoughts on “What Does GMP In Construction Mean”