Home>diy>Building & Construction>What Does PO Mean In Construction
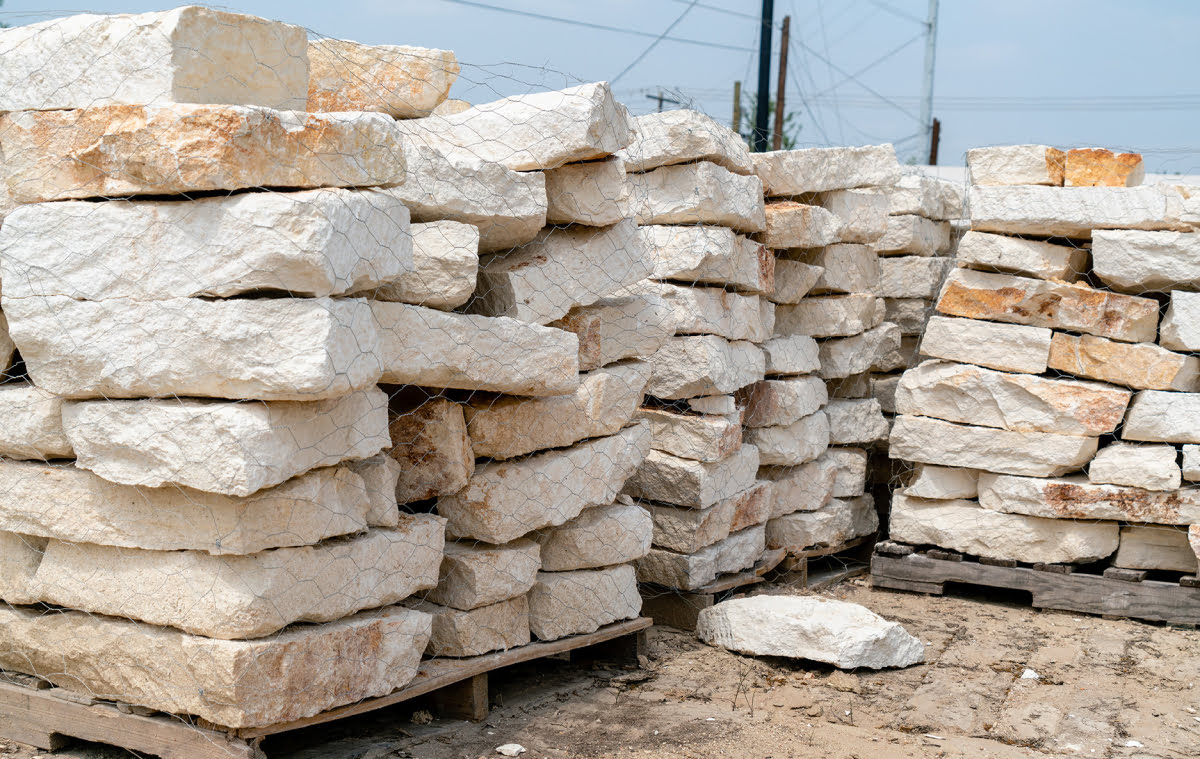
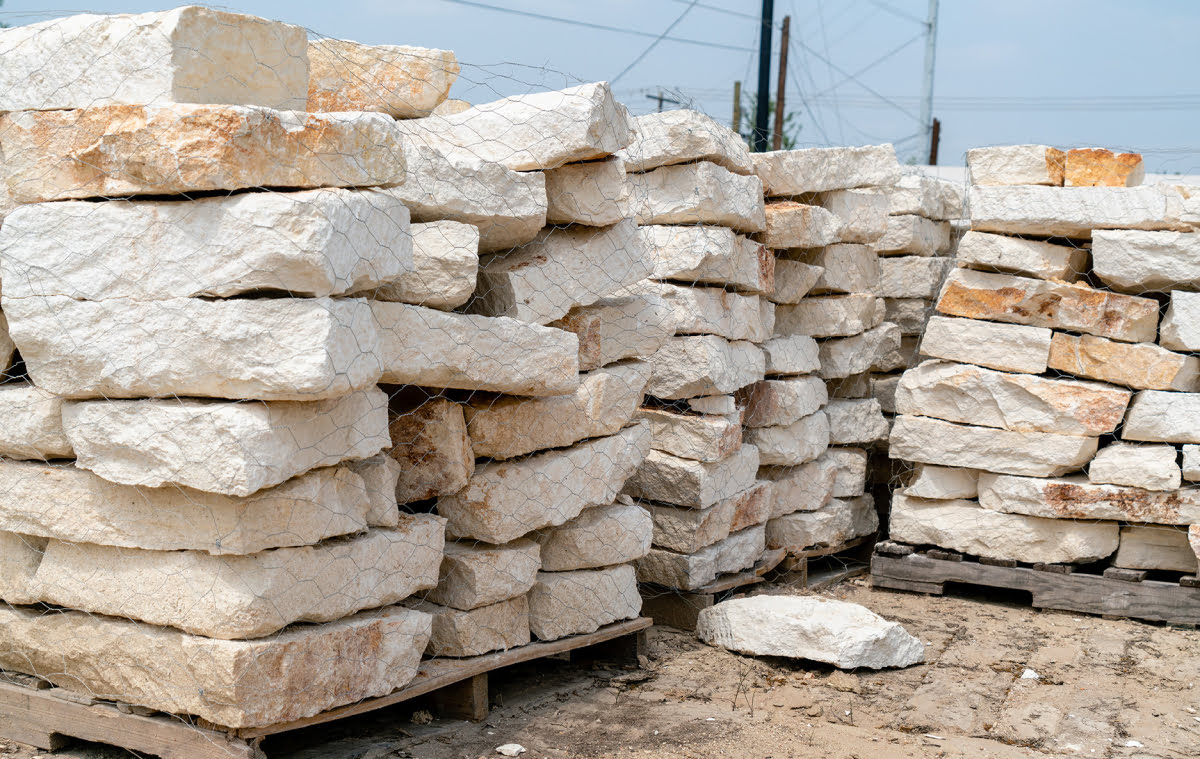
Building & Construction
What Does PO Mean In Construction
Modified: December 7, 2023
Discover the meaning of "PO" in construction and how it is related to building-construction industry. Learn about its significance and common usage.
(Many of the links in this article redirect to a specific reviewed product. Your purchase of these products through affiliate links helps to generate commission for Storables.com, at no extra cost. Learn more)
Introduction
Welcome to the world of construction, where the process of building structures and transforming visions into reality takes place. In this dynamic industry, there are various terms and acronyms that are commonly used. One such acronym is PO, which stands for Purchase Order. But what does PO mean in construction, and why is it important?
In the construction industry, a purchase order (PO) is a legal document used to initiate and authorize the purchase of goods or services. It serves as a formal agreement between a buyer and a supplier, setting out the details of the transaction, including the quantity, price, delivery date, and terms of payment.
Construction projects involve numerous subcontractors, suppliers, and vendors, each responsible for providing different materials, equipment, and services. Managing these procurement processes efficiently is crucial to ensure the smooth execution of projects, as well as maintaining cost control and transparency.
By implementing a systematic purchase order process, construction companies can streamline their purchasing activities, reduce errors and misunderstandings, and enhance project management and financial control. In this article, we will explore the purpose of purchase orders in construction, their importance, the process involved, and the benefits they bring to construction projects.
So, let’s dive deeper into the world of purchase orders in construction and unravel the significance behind the acronym PO.
Key Takeaways:
- Purchase Orders (POs) are crucial in construction, serving as formal agreements between buyers and suppliers. They streamline procurement, enhance cost control, and provide valuable documentation for auditing and compliance purposes.
- Implementing best practices, such as standardizing the PO process, utilizing e-procurement systems, and fostering supplier collaboration, is essential for effective PO management in construction. Addressing challenges like resistance to change and complex supplier relationships is key to successful implementation.
Definition of PO in Construction
In the construction industry, a Purchase Order (PO) is a document that serves as a formal agreement between a buyer and a supplier for the procurement of goods or services. It outlines the specific details of the transaction, including the quantity, price, delivery date, and terms of payment. The PO acts as a legally binding contract, ensuring that both parties understand and agree upon the terms and conditions of the purchase.
Construction projects involve a complex network of subcontractors, suppliers, and vendors, each responsible for providing different materials, equipment, or services. The use of purchase orders helps to streamline the procurement process, ensuring that all parties are on the same page and that goods and services are obtained efficiently and cost-effectively.
When a construction company or project manager needs to purchase materials or services, they generate a purchase order to initiate the transaction. The PO typically includes essential information such as the company’s name and address, the supplier’s name and contact details, a unique PO number, a description of the items or services being procured, and the agreed-upon terms and conditions.
Once the purchase order is generated, it is sent to the supplier or vendor. They review the details provided, including the quantity, price, and delivery date, and confirm their acceptance of the order. This process helps to ensure that both parties are in agreement before proceeding with the purchase.
Once the supplier accepts the purchase order, it serves as a reference document throughout the procurement process. It helps to track the progress of the order, facilitates communication between the buyer and supplier, and serves as a paper trail for accounting and auditing purposes.
Overall, the purchase order is a crucial document in construction projects, as it helps to establish transparency, ensure accuracy in procurement, and maintain a record of all transactions related to materials and services acquired for the project.
Purpose of PO in Construction
The primary purpose of Purchase Orders (POs) in the construction industry is to establish a clear and formal agreement between the buyer and the supplier for the procurement of goods or services. POs serve several important purposes that benefit both parties involved in the transaction.
One of the key purposes of a PO is to provide a detailed description of the items or services being purchased. By specifying the quantity, quality, and specifications of the materials or equipment required, the PO ensures that there is no confusion or ambiguity about what is being ordered. This clarity helps to prevent errors or misunderstandings and ensures that the buyer receives the exact items they need for the construction project.
Another purpose of a PO is to establish the agreed-upon terms and conditions of the purchase. This includes outlining the price per unit, the total cost, the payment terms, and the delivery date. By clearly documenting these details in the PO, both parties are aware of their rights and obligations, reducing the risk of disputes or disagreements later on.
Additionally, a PO serves as a control mechanism for managing project costs. By requiring a purchase order for each procurement, construction companies can evaluate the necessity and cost of the items or services before committing to the purchase. This helps to prevent overspending and improves financial management throughout the project.
POs also play a crucial role in inventory management and tracking. When a purchase order is issued, it enables companies to update their inventory records, ensuring that they have accurate information on the availability of materials or equipment. This allows for better planning and scheduling, as well as preventing unnecessary delays or disruptions in the construction process.
Furthermore, POs provide a means of accountability and documentation for auditing purposes. By keeping a record of all purchase orders issued and received, companies can demonstrate their compliance with internal and external regulations. This is especially important for larger construction projects, where transparency and accountability are key considerations.
In summary, the purpose of a PO in construction is to establish a formal agreement between the buyer and supplier, provide clarity on the items or services being purchased, outline the terms and conditions of the transaction, control project costs, enable inventory management, and ensure accountability and compliance. By implementing a robust purchase order process, construction companies can streamline their procurement activities and improve project management efficiency.
Importance of PO in Construction Projects
Purchase Orders (POs) play a crucial role in the successful execution of construction projects. They bring several benefits and are of significant importance in ensuring transparency, accountability, and efficient project management. Let’s explore why POs are so vital in the construction industry.
First and foremost, POs provide a clear and formal agreement between the buyer and the supplier. By documenting the details of the purchase, including the quantity, price, delivery date, and terms of payment, POs help to establish a mutual understanding and expectation between the parties involved. This ensures that both the buyer and supplier are on the same page regarding the transaction, reducing the chances of misunderstandings or disputes.
One of the key advantages of using POs is that they facilitate better cost control in construction projects. By requiring a PO for each procurement, construction companies can track and monitor their expenses in a systematic manner. The PO acts as a reference document for budgeting and accounting purposes, allowing for better financial management and preventing overspending.
Another significant benefit of POs is that they streamline the procurement process. In construction, multiple subcontractors, suppliers, and vendors are involved, and managing these relationships can be complex. POs help to standardize and simplify the purchasing activities by ensuring that all parties follow a consistent and documented process. This leads to greater efficiency in acquiring the necessary materials, equipment, and services for the project.
POs also enhance project planning and scheduling. By specifying the required items and delivery dates in the purchase order, construction companies can better schedule their activities. They can plan for the arrival of materials or equipment, coordinate with subcontractors, and ensure that the project progresses smoothly without delays or disruptions.
Moreover, POs serve as a control mechanism for quality assurance. When items are ordered through a PO, construction companies can outline the required specifications and standards. This helps to ensure that the materials or equipment procured meet the necessary quality criteria. By specifying these requirements upfront, the risk of receiving subpar or unsuitable items is minimized.
Lastly, POs provide an essential documentation trail for auditing and compliance purposes. They serve as evidence of the transactions made, demonstrating that proper protocols and procedures were followed. This documentation is valuable during audits, inspections, and legal disputes, as it helps companies prove their adherence to regulations, contractual obligations, and financial accountability.
In summary, the use of POs in construction projects is of utmost importance. They establish clear agreements, support cost control, streamline procurement, aid in project planning, ensure quality assurance, and provide essential documentation for auditing and compliance purposes. By implementing effective PO processes, construction companies can enhance transparency, accountability, and overall project management efficiency.
PO Process in Construction
The Purchase Order (PO) process in construction involves several steps to ensure a smooth and efficient procurement of goods or services. Let’s take a closer look at the typical PO process in the construction industry.
1. Identify the Need: The first step is to identify the need for a purchase. This can be done by the project manager or relevant personnel who determines the materials, equipment, or services required for the construction project.
2. Request for Quotations (RFQ): Once the need is identified, the next step is to gather quotations from potential suppliers or vendors. The RFQ contains information on the required items, specifications, quantities, and delivery dates. Suppliers submit their quotes based on these requirements.
3. Evaluation and Selection: After receiving the quotes, the project team evaluates and compares them to determine the best-fit supplier. Factors such as price, quality, reputation, delivery capabilities, and past performance are taken into consideration during the evaluation process.
4. Negotiation: If necessary, negotiations take place with the selected supplier to finalize the terms and conditions of the purchase. This includes discussing pricing, delivery schedules, payment terms, and any other relevant details to ensure both parties are aligned.
5. Generation of Purchase Order: Once the negotiations are complete, a purchase order is generated. The PO includes details such as the company’s name and address, supplier’s name, a unique PO number, item descriptions, quantities, pricing, delivery dates, terms of payment, and any special instructions or conditions.
6. Approval: The purchase order is then sent for internal approval within the company. This step ensures that the purchase is authorized by the appropriate personnel and aligns with the project’s budget and requirements.
7. Sending the PO: Once the PO is approved, it is sent to the selected supplier. The supplier reviews the PO and acknowledges acceptance, confirming their commitment to fulfill the order as per the specified terms and conditions.
8. Order Fulfillment: The supplier processes the order and delivers the goods or services according to the agreed-upon terms. They may provide updates on the status of the delivery or any changes that may affect the order.
9. Receiving and Inspection: Upon the receipt of the ordered items or services, the construction team inspects them for quality, quantity, and compliance with the specifications outlined in the PO. Any discrepancies or issues are documented and addressed with the supplier.
10. Invoicing and Payment: Once the delivered items or services are accepted, the supplier generates an invoice based on the agreed-upon terms. The construction company verifies the invoice against the PO and processes payment in a timely manner.
11. Documentation and Record-Keeping: Throughout the PO process, all relevant documents, including the PO, RFQ, supplier quotations, and invoices, are recorded and maintained for future reference, audits, and compliance purposes.
The PO process in construction ensures that the procurement of materials, equipment, and services follows a systematic and controlled approach, allowing for better project management, cost control, and accountability.
PO in construction stands for Purchase Order. It is a document issued by a buyer to a seller, outlining the details of the materials or services to be purchased. It is important for tracking and ensuring the correct items are delivered.
Benefits of Using PO in Construction
The use of Purchase Orders (POs) in construction projects brings several benefits, contributing to improved procurement processes, project management efficiency, and cost control. Let’s explore the key advantages of using POs in the construction industry.
1. Clarity and Accuracy: POs provide a clear and detailed description of the materials, equipment, or services being procured. By specifying the quantity, quality, and specifications in the PO, both the buyer and supplier have a clear understanding of what is being ordered. This clarity helps to prevent errors, misunderstandings, and disputes, ensuring the correct items are obtained.
2. Cost Control: By requiring a PO for each procurement, construction companies can effectively monitor and control project costs. POs enable better budgeting and financial management, ensuring that purchases align with the project’s budget. This helps prevent overspending, improves cash flow management, and enhances overall cost control throughout the project.
3. Streamlined Procurement: The use of POs streamlines the procurement process by establishing a standardized and documented procedure. This helps to simplify and organize purchasing activities, enabling more efficient communication between the buyer and supplier. By following a consistent process, construction companies can save time and effort, reducing potential errors and delays in procurement.
4. Better Planning and Scheduling: POs play a crucial role in project planning and scheduling. By specifying delivery dates in the PO, construction companies can better coordinate their activities. They can schedule the arrival of materials or equipment, coordinate with subcontractors, and ensure seamless project execution. This leads to improved efficiency and timely completion of the construction project.
5. Quality Assurance: POs assist in ensuring quality assurance in construction projects. By specifying the required specifications and standards in the PO, construction companies can ensure that the materials or equipment procured meet the necessary quality criteria. This helps minimize the risk of receiving subpar or unsuitable items, reducing the chances of rework or project delays.
6. Documentation and Auditing: POs provide a vital documentation trail for auditing and compliance purposes. They serve as evidence of the transactions made, demonstrating that proper protocols and procedures were followed. The documentation helps construction companies comply with internal and external auditing requirements, contractual agreements, and regulatory standards.
7. Dispute Resolution: In case of any discrepancies or issues with the purchase, POs serve as a reference document for dispute resolution. They provide a clear record of the agreed-upon terms and conditions, facilitating communication between the buyer and supplier. This helps to resolve conflicts or disagreements in a more efficient and effective manner, avoiding misunderstandings and potential legal disputes.
In summary, the use of POs in construction projects brings numerous benefits, including clarity and accuracy in procurement, cost control, streamlined processes, improved planning and scheduling, quality assurance, effective documentation for audits, and enhanced dispute resolution. By implementing a robust PO process, construction companies can optimize project management, reduce risks, and ensure a smoother and more successful project execution.
Challenges in Implementing PO in Construction
While Purchase Orders (POs) offer numerous benefits in construction projects, there are also several challenges that construction companies may encounter when implementing PO processes. Understanding and addressing these challenges is crucial to ensure the effective use of POs. Let’s explore some of the common challenges in implementing PO in construction.
1. Resistance to Change: One of the significant challenges is the resistance to change from employees and stakeholders. Implementing PO processes may require adjustments to existing workflows and systems. Resistance can arise due to a lack of understanding, fear of disruption, or reluctance to adapt to new practices. Addressing this challenge requires effective communication, training, and involving key stakeholders in the implementation process.
2. Complex Supplier Relationships: Construction projects often involve multiple subcontractors, suppliers, and vendors. Maintaining effective relationships with these stakeholders can be challenging, especially when implementing PO processes. Suppliers may have their own procurement systems in place, and aligning them with the buyer’s PO requirements can be complex. Building strong relationships, open communication channels, and collaborative partnerships are key to overcoming this challenge.
3. Limited Technological Infrastructure: Many construction companies still rely on manual or outdated systems for procurement processes. This lack of technological infrastructure can hinder the efficient implementation and management of POs. Limited access to computer systems, lack of integration with other project management software, and inadequate training can pose significant challenges. Investing in modern procurement and project management systems can help address these challenges and improve the effectiveness of PO implementation.
4. Inaccurate Data and Documentation: Inaccurate data and documentation can disrupt the smooth implementation of PO processes. Errors in PO creation, incomplete information, or delays in updating receipt and inspection records can lead to confusion and potential disputes. Emphasizing the importance of accurate and timely data entry, implementing quality control measures, and providing training on proper documentation practices can mitigate this challenge.
5. Non-compliance and Unauthorized Purchases: Another challenge is ensuring compliance with the PO process and preventing unauthorized purchases. Employees may bypass the PO system for urgent or unplanned purchases, which can lead to uncontrolled spending and a lack of transparency. Implementing proper authorization protocols, establishing clear purchasing guidelines, and enforcing compliance measures can help overcome this challenge and ensure that all purchases go through an approved PO process.
6. Communication and Coordination: Effective communication and coordination between different departments, project teams, and suppliers are essential for successful PO implementation. Miscommunication, delays in approvals, or lack of collaboration can lead to confusion and disrupt the procurement cycle. Fostering a culture of clear and open communication, establishing efficient approval workflows, and utilizing collaboration tools can help address this challenge.
7. Training and Education: Lastly, the lack of training and education on PO processes can hinder their successful implementation. Employees may not have a clear understanding of the purpose, benefits, and procedures related to POs. Providing comprehensive training programs, emphasizing the importance of POs, and ensuring continuous education can help overcome this challenge and promote effective PO implementation.
Addressing these challenges requires a combination of clear communication, training, technological advancements, and stakeholder collaboration. By proactively tackling these challenges, construction companies can successfully implement PO processes and reap the benefits they offer in terms of cost control, efficiency, and transparency in procurement.
Best Practices for Managing PO in Construction
The effective management of Purchase Orders (POs) is crucial in the construction industry to ensure smooth procurement processes, cost control, and efficient project management. Implementing best practices can help construction companies optimize their PO management. Let’s explore some of the key best practices for managing POs in construction.
1. Standardize PO Process: Establish a standardized PO process that defines clear guidelines and procedures for creating, approving, and managing POs. This ensures consistency and streamlines the procurement workflow across different projects and teams within the organization.
2. Implement E-Procurement Systems: Utilize e-procurement systems or software to automate and digitize the PO management process. These systems allow for efficient creation, tracking, and management of POs, reducing manual paperwork and enabling real-time visibility into procurement activities.
3. Define Purchase Approval Levels: Establish clear approval levels within the organization based on the value or nature of the purchase. This ensures that the appropriate personnel review and authorize POs based on their assigned authority levels, minimizing the risk of unauthorized purchases and ensuring compliance.
4. Periodic Supplier Evaluation: Regularly evaluate and assess the performance of suppliers based on factors such as product quality, on-time delivery, and customer service. This evaluation helps in identifying reliable and efficient suppliers, which can optimize the procurement process and strengthen the supply chain.
5. Implement Budget Control Measures: Integrate budget controls within the PO system to monitor and control project costs. This ensures that POs align with the project’s budget and prevents overspending. Establishing budget thresholds, alerts, and reporting mechanisms can help monitor expenditure and enable better financial control.
6. Maintain Accurate Data and Documentation: Ensure accurate data entry and documentation throughout the PO management process. This includes capturing all relevant information such as item descriptions, quantities, pricing, and delivery dates. Accurate data and documentation provide a reliable audit trail and facilitate effective decision-making.
7. Foster Strong Internal Communication: Establish clear lines of communication between project managers, procurement teams, and other relevant stakeholders involved in the PO process. Effective communication ensures that all parties are aligned and informed about the status of POs, changes in requirements, and any potential delays or issues.
8. Train and Educate Employees: Provide comprehensive training and education to employees involved in the PO process. This includes educating them on the best practices, procedures, and importance of adhering to the PO management guidelines. Continuous training ensures that employees are equipped with the knowledge and skills necessary for effective PO management.
9. Conduct Regular Reviews and Audits: Periodically review and audit the PO management process to identify areas for improvement and ensure compliance with established protocols. Regular reviews help identify any potential bottlenecks, issues, or gaps in the process and enable implementation of corrective measures.
10. Foster Supplier Collaboration: Build strong relationships and foster collaboration with suppliers. Develop open lines of communication, establish performance expectations, and conduct regular meetings to discuss opportunities for improvement and address any issues or concerns that may arise.
By implementing these best practices, construction companies can enhance the management of POs and optimize the procurement process. This leads to better project planning, cost control, supplier management, and overall project success.
Conclusion
Purchase Orders (POs) play a critical role in the construction industry, serving as formal agreements between buyers and suppliers for the procurement of goods or services. POs facilitate clarity, transparency, and efficiency in procurement processes, contributing to effective project management and cost control. Understanding the definition, purpose, and process of POs is essential for construction companies to leverage their benefits and overcome associated challenges.
POs bring numerous advantages to construction projects. They establish clear agreements, ensure accurate documentation, and provide a control mechanism for managing costs. POs streamline procurement processes, enhance planning and scheduling, and contribute to quality assurance. Additionally, they serve as valuable documentation for auditing and compliance purposes, enabling companies to adhere to regulations and demonstrate financial accountability.
However, implementing PO processes in construction can present challenges. Resistance to change, complex supplier relationships, limited technological infrastructure, and accurate data management are obstacles that need to be addressed. Effective communication, training, and education are key to overcoming these challenges and ensuring successful PO implementation.
To effectively manage POs in construction, best practices should be implemented. Standardizing the PO process, utilizing e-procurement systems, defining purchase approval levels, and implementing budget control measures are some essential practices. Accurate data and documentation, strong internal communication, training and education, regular reviews and audits, and fostering supplier collaboration also contribute to effective PO management.
In conclusion, POs are vital in construction projects for establishing clear agreements, ensuring transparency, and optimizing procurement processes. By implementing best practices and addressing associated challenges, construction companies can leverage the benefits of POs to streamline operations, enhance project management, and achieve successful project outcomes.
Frequently Asked Questions about What Does PO Mean In Construction
Was this page helpful?
At Storables.com, we guarantee accurate and reliable information. Our content, validated by Expert Board Contributors, is crafted following stringent Editorial Policies. We're committed to providing you with well-researched, expert-backed insights for all your informational needs.
0 thoughts on “What Does PO Mean In Construction”