Home>diy>Building & Construction>What Is Considered Overhead In Construction
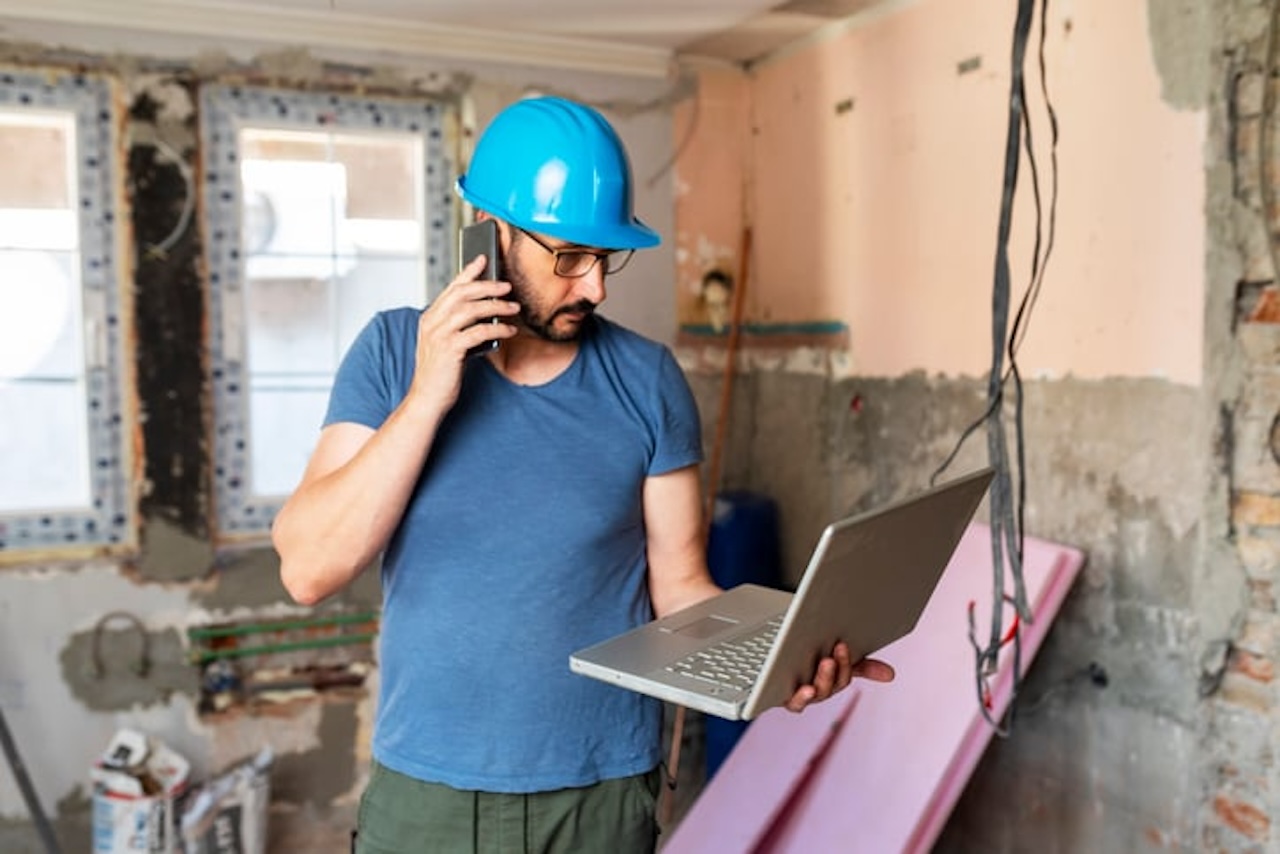
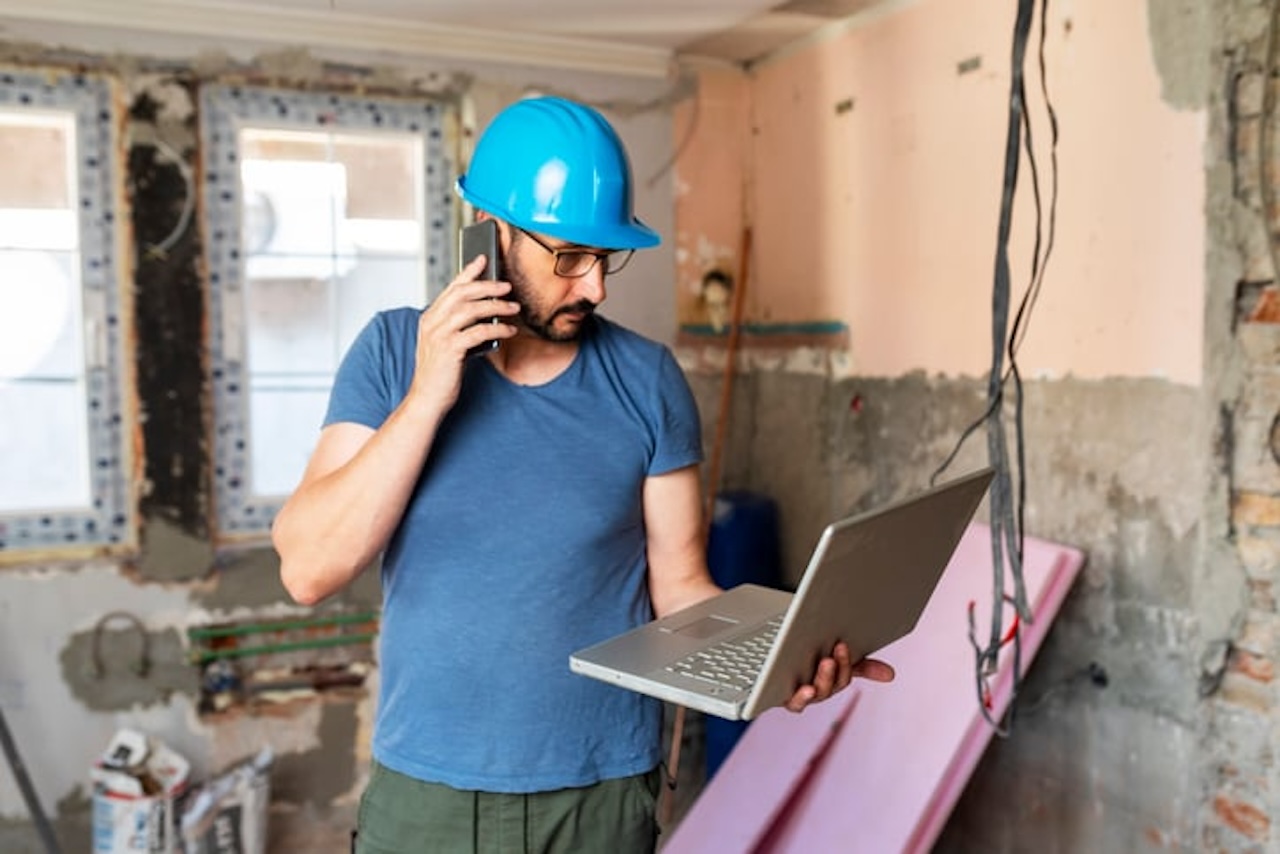
Building & Construction
What Is Considered Overhead In Construction
Modified: January 24, 2024
Learn about what is considered overhead in construction and its impact on building-construction projects. Essential information for contractors and project managers.
(Many of the links in this article redirect to a specific reviewed product. Your purchase of these products through affiliate links helps to generate commission for Storables.com, at no extra cost. Learn more)
Introduction
Welcome to the world of construction, where every project requires careful planning, precision, and efficient management. As an integral factor in the success of any construction project, overhead costs play a crucial role in determining its financial viability. Understanding what is considered overhead in construction and how to manage it effectively is essential for contractors, project managers, and anyone involved in the construction industry.
Overhead costs, also known as indirect costs, are the expenses incurred by a construction company that are not directly attributable to a specific project or job. These costs are necessary for the overall operation of the business and are incurred regardless of the number of projects currently being undertaken. They include expenses like rent, utilities, payroll taxes, insurance, office supplies, and equipment maintenance.
Managing construction overhead costs is vital for maintaining profitability and financial stability in the industry. By effectively monitoring and controlling overhead expenses, construction companies can optimize their operations, improve cash flow, and enhance their competitive edge. In this article, we will delve deeper into the concept of overhead in construction, explore some examples of overhead costs, and discuss strategies to reduce these costs without compromising quality or efficiency.
Whether you are a contractor, project manager, or investor, understanding how overhead costs impact the construction process is crucial for effective decision-making and project success. So, let’s dive into the world of construction overhead and discover ways to streamline and optimize your construction operations.
Key Takeaways:
- Overhead costs in construction encompass various indirect expenses, from office rent to insurance, impacting financial stability and project viability. Effective monitoring and reduction strategies are vital for profitability and competitiveness.
- Strategies to reduce overhead costs in construction include streamlining operations, negotiating contracts, embracing technology, and optimizing resource allocation. Balancing cost reduction with quality and safety is essential for long-term success.
Read more: What Is Overhead Cost In Construction
Definition of Overhead in Construction
In the construction industry, overhead refers to the indirect costs incurred by a company that are not directly attributed to a specific project. These costs are necessary for the overall functioning and management of the construction business. While it may be tempting to focus solely on the direct costs of labor, materials, and equipment, overhead costs are equally important in determining the financial health and profitability of a construction company.
Construction overhead costs can be categorized into three main areas: administrative overhead, project overhead, and general overhead. Administrative overhead includes expenses related to office operations, such as rent, utilities, insurance, office supplies, and salaries of administrative staff. These costs are necessary for the day-to-day management and administrative functions of the construction company.
Project overhead costs, on the other hand, are specific to individual construction projects. They include expenses like project management fees, permits and licenses, job site trailers, temporary facilities, safety equipment, and project-specific insurance costs. These costs are directly related to the successful planning, execution, and completion of a specific project.
General overhead costs encompass the expenses that are not directly tied to a specific project, nor solely related to office operations. Examples of general overhead costs include executive salaries, marketing expenses, professional fees, accounting and legal services, and general office maintenance. These costs support the overall functioning and growth of the construction company.
It is important to note that overhead costs are not fixed. They can vary based on the size and complexity of the construction company, the type of projects undertaken, and the overall economic conditions. Additionally, as construction companies grow and undertake more projects, their overhead costs may increase due to the need for larger office spaces, additional administrative staff, and enhanced marketing efforts.
Understanding the various categories of overhead costs in construction is essential for accurately estimating project budgets, determining pricing for proposals, and assessing the financial feasibility of construction projects. By effectively managing and controlling overhead costs, construction companies can enhance their profitability, improve financial stability, and stay competitive in the industry.
Examples of Construction Overhead Costs
Construction overhead costs encompass various expenses that are necessary for the operation and management of a construction company. Here are some common examples of construction overhead costs:
- Office Rent and Utilities: This includes the cost of leasing office space, utilities like electricity, water, internet, and property taxes.
- Office Equipment and Supplies: Expenses related to office furniture, computers, printers, software, stationery, and other supplies needed for day-to-day operations.
- Salaries and Benefits: Compensation for administrative staff, project managers, accounting personnel, and other support staff, including benefits such as health insurance and retirement contributions.
- Insurance: General liability insurance, workers’ compensation insurance, and other types of coverage to protect the business and employees from unforeseen events.
- Professional Services: Accounting, legal, and consulting fees incurred for professional advice and assistance.
- Marketing and Advertising: Costs associated with promoting the construction company’s services, including website development, advertising campaigns, and industry memberships.
- Vehicle Expenses: Fuel, maintenance, and insurance for construction company vehicles used for transportation and site visits.
- Equipment Maintenance: Repairs, servicing, and maintenance of construction equipment to ensure their optimal functionality and longevity.
- Permits and Licenses: Expenses related to obtaining necessary permits, licenses, and certifications required to carry out construction work legally.
- Safety and Training: Costs associated with safety equipment, safety training programs, and certifications to ensure compliance with safety regulations.
These are just a few examples of construction overhead costs. It is important for construction companies to identify and track all relevant expenses to accurately calculate overhead and incorporate it into project budgets and pricing strategies. By understanding and managing these overhead costs effectively, construction companies can achieve better financial control, improve profitability, and ensure the successful completion of projects.
Calculation and Allocation of Overhead in Construction
Calculating and allocating overhead costs accurately is essential for proper budgeting, estimating project costs, and determining pricing for construction projects. While the specific methods may vary between companies, here are some common approaches to calculate and allocate overhead in construction:
1. Direct Cost Percentage Method: This method involves calculating overhead as a percentage of direct costs. The company determines a fixed percentage that represents the expected ratio of overhead costs to direct costs. For example, if the estimated overhead percentage is 20% and the total direct costs for a project are $100,000, then the overhead allocation would be $20,000.
2. Labor Hours Method: In this method, the company calculates overhead costs based on the total labor hours worked on a project. The overhead rate is determined by dividing the total overhead costs by the total labor hours. This rate is then applied to the labor hours for each project to allocate overhead costs accordingly.
3. Square Footage Method: This method is commonly used in construction companies where office space is a significant component of overhead costs. The company determines the total square footage of its office space and assigns a specific dollar value per square foot as the overhead rate. The allocated overhead for a project is then calculated based on the square footage of the designated project office area.
4. Activity-Based Costing (ABC) Method: This method involves identifying key activities or cost drivers that contribute to overhead costs and allocating them based on their usage. For example, if equipment maintenance is a significant overhead cost, the company may allocate these costs based on the usage hours of each piece of equipment on a project.
5. Historical Data Method: Using historical data, construction companies can analyze their past projects to determine the average overhead costs relative to direct costs. This historical ratio can then be applied to future projects to allocate overhead costs based on estimated direct costs.
Regardless of the method used, it is important for construction companies to regularly review and adjust their overhead allocation methods to ensure that they accurately reflect the current business operations and market conditions. This ensures that overhead costs are properly allocated to each project, allowing for better cost control, accurate pricing, and increased profitability.
When considering overhead costs in construction, be sure to include expenses such as insurance, permits, utilities, and office expenses. These costs can add up and should be factored into project budgets.
Factors Affecting Overhead Costs in Construction
In the construction industry, several factors contribute to the variation and magnitude of overhead costs. Understanding these factors is crucial for effectively managing and controlling overhead expenses. Here are some of the key factors that can influence overhead costs in construction:
1. Size of the Construction Company: The size of a construction company directly impacts its overhead costs. Larger companies typically have higher overhead costs due to the need for larger office spaces, a larger administrative staff, and more extensive resources to manage multiple projects simultaneously.
2. Type and Complexity of Projects: The nature and complexity of the construction projects undertaken by a company can significantly impact overhead costs. More complex projects require specialized expertise, additional project management, and administrative support, leading to higher overhead expenses.
3. Geographic Location: The geographic location of a construction company can influence overhead costs. Operating in areas with higher costs of living, higher taxes, or stricter regulations can increase overhead expenses.
4. Seasonality: Construction companies often experience seasonal fluctuations in business activity. During peak seasons, when numerous projects are underway, overhead costs may increase due to the need for additional resources and temporary staff to handle the higher workload.
5. Economic Conditions: The overall economic conditions, such as inflation rates and interest rates, can impact overhead costs. Inflation can cause increases in office rent, utilities, and material costs, leading to higher overhead expenses for construction companies.
6. Technology and Equipment: The level of technology and equipment used by a construction company can affect overhead costs. Advanced technology and modern equipment can increase initial capital investment, maintenance costs, and the need for specialized training, resulting in higher overhead expenses.
7. Safety Regulations and Compliance: Construction companies need to comply with various safety regulations and provide a safe working environment for their employees. Costs associated with safety equipment, training, and compliance measures can contribute to overhead expenses.
8. Business Overhead Policies: The specific policies and practices implemented by a construction company can impact overhead costs. For example, outsourcing certain administrative functions or implementing cost-saving measures like energy-efficient practices can help reduce overhead expenses.
9. Market Competitiveness: The level of competition in the construction industry can affect overhead costs. In highly competitive markets, companies may lower profit margins by reducing overhead expenses to win bids, while in less competitive markets, companies may have more flexibility in pricing to cover higher overhead costs.
By being aware of these factors, construction companies can make informed decisions, implement effective strategies, and control overhead costs more efficiently. Regular monitoring and evaluation of these factors will enable construction companies to adapt and optimize their operations to maintain profitability and competitiveness.
Read more: What Is Overhead And Profit In Construction
Importance of Monitoring and Controlling Overhead in Construction Projects
Monitoring and controlling overhead costs is a critical aspect of managing construction projects effectively. Here are several reasons why it is important to prioritize the monitoring and control of overhead in construction:
1. Financial Stability: By monitoring and controlling overhead costs, construction companies can maintain financial stability. Overhead expenses can quickly escalate if not properly managed, eroding profit margins and potentially putting the company at risk. Controlling overhead costs ensures that the company remains financially sound, even during challenging times.
2. Accurate Cost Estimation: Properly monitoring overhead costs allows for more accurate cost estimation during project bidding and proposal stages. Understanding and including overhead costs in project estimates helps to avoid underestimating expenses and ensures that projects are priced competitively while still maintaining profitability.
3. Maximize Profitability: Effective control of overhead costs directly impacts a construction company’s profitability. By reducing unnecessary overhead expenses and optimizing resources, the company can improve its profit margins and overall financial performance.
4. Competitive Advantage: Controlling overhead costs can provide a competitive advantage in the construction industry. By being able to offer more competitive pricing without sacrificing quality, construction companies can win more projects and gain a stronger foothold in the market.
5. Efficient Resource Allocation: By monitoring overhead costs, construction companies can identify areas where resources are being underutilized or wasted. This enables them to reallocate resources more efficiently, thereby optimizing productivity and reducing unnecessary expenditures.
6. Project Viability: Carefully monitoring and controlling overhead costs helps ensure the financial viability of construction projects. By accurately estimating overhead expenses and factoring them into project budgets, companies can avoid cost overruns and potential project delays caused by insufficient funding.
7. Cash Flow Management: Effective control of overhead costs improves cash flow management within a construction company. By reducing unnecessary expenses and eliminating waste, companies can better allocate funds for critical project needs, pay vendors and suppliers on time, and maintain a healthy cash flow cycle.
8. Sustainability: Monitoring and controlling overhead costs contribute to the long-term sustainability of a construction company. By implementing cost-saving measures, energy-efficient practices, and sustainable strategies, companies can reduce overhead expenses, minimize their environmental impact, and promote responsible construction practices.
Overall, monitoring and controlling overhead costs in construction projects are essential for maintaining financial stability, maximizing profitability, and gaining a competitive edge in the industry. By implementing effective strategies, leveraging technology, and continually evaluating and adjusting overhead practices, construction companies can optimize their operations and lay the foundation for long-term success.
Strategies to Reduce Overhead Costs in Construction
Reducing overhead costs is a key objective for construction companies seeking to improve profitability and maintain a competitive edge. Here are some effective strategies that can help reduce overhead costs in the construction industry:
- Streamline Operations: Analyze and review current workflow processes to identify areas of inefficiency or redundancy. Streamline operations by implementing lean construction principles, optimizing work schedules, and eliminating unnecessary steps in the project management and administrative processes.
- Negotiate Contracts: Negotiate with suppliers, subcontractors, and vendors to secure better pricing and terms. Consider long-term contracts or strategic partnerships to leverage volume discounts and reduce procurement costs.
- Optimize Resource Allocation: Continuously assess resource utilization, including labor, equipment, and materials. Optimize resource allocation to ensure that they are effectively utilized across multiple projects, avoiding underutilization or wastage.
- Implement Technology: Embrace digital tools and construction management software to automate processes, improve communication, and reduce unnecessary paperwork. Automation can streamline tasks, enhance efficiency, and reduce the need for manual labor, thus reducing overhead costs.
- Energy Efficiency: Implement energy-efficient practices within the office and on construction sites. This can include using energy-efficient lighting, insulation, HVAC systems, and equipment. By reducing energy consumption, companies can lower utility bills and reduce overhead costs.
- Outsource Non-Core Functions: Consider outsourcing non-core functions such as accounting, payroll, and IT services. Outsourcing these tasks can reduce administrative overhead and free up internal resources to focus on core competencies.
- Invest in Employee Training: Provide training and professional development opportunities to employees. Well-trained and skilled employees are more productive, leading to increased efficiency and reduced labor costs.
- Implement Cost Control Measures: Regularly monitor and control project expenses, reviewing budgets and identifying cost-saving opportunities. Implement effective cost control measures like strict inventory management, waste reduction initiatives, and proactive monitoring of expenses.
- Review Insurance Coverage: Regularly review insurance coverage to ensure appropriate levels of coverage and evaluate competitive rates. Insurance costs can be a significant overhead expense, and periodic reviews can help identify potential savings without compromising protection.
- Collaborate and Share Resources: Explore opportunities for collaboration with other construction companies or subcontractors. Share resources, such as equipment or office space, to reduce capital investment and rental costs.
It is important to note that reducing overhead costs should not come at the expense of quality or safety. The goal is to find the right balance between cost reduction and maintaining the necessary resources and standards to ensure project success and client satisfaction.
By implementing these strategies and continuously evaluating and adjusting overhead practices, construction companies can optimize their operations, reduce costs, and improve their overall profitability.
Conclusion
Managing and controlling overhead costs is a critical aspect of running a successful construction business. By understanding what is considered overhead in construction and implementing strategies to monitor and reduce these costs, companies can enhance their financial stability, improve profitability, and gain a competitive advantage in the industry.
In the construction industry, overhead costs include various indirect expenses necessary for the overall operation and management of a construction company. These costs can range from office rent and utilities to salaries, insurance, and marketing expenses. It is important to accurately calculate and allocate overhead costs to ensure accurate project budgeting, pricing, and profitability.
Factors such as the size of the company, project complexity, economic conditions, and geographic location can influence overhead costs. Construction companies must identify these factors and continuously evaluate their impact on overhead to implement effective cost-saving measures.
Monitoring and controlling overhead costs yield numerous benefits. It enhances financial stability, enables accurate cost estimation, maximizes profitability, and improves resource allocation. It also provides a competitive advantage, ensures project viability, optimizes cash flow management, and promotes long-term sustainability.
Several strategies can be employed to reduce overhead costs in the construction industry. These include streamlining operations, negotiating contracts, optimizing resource allocation, leveraging technology, implementing energy-efficient practices, outsourcing non-core functions, investing in employee training, implementing cost control measures, reviewing insurance coverage, and collaborating and sharing resources.
By implementing these strategies and adapting to market conditions, construction companies can effectively control and reduce overhead costs without compromising quality and safety. Regular evaluation, adjustment, and continuous improvement are essential to ensure ongoing success and profitability.
In conclusion, effective management and control of overhead costs in construction projects are crucial for financial stability, profitability, and competitiveness. With a focus on reducing waste, optimizing resources, and embracing efficient practices, construction companies can navigate the industry successfully and achieve long-term success.
Frequently Asked Questions about What Is Considered Overhead In Construction
Was this page helpful?
At Storables.com, we guarantee accurate and reliable information. Our content, validated by Expert Board Contributors, is crafted following stringent Editorial Policies. We're committed to providing you with well-researched, expert-backed insights for all your informational needs.
0 thoughts on “What Is Considered Overhead In Construction”