Home>Furniture & Design>Interior Design Trends>How To Shape Glass
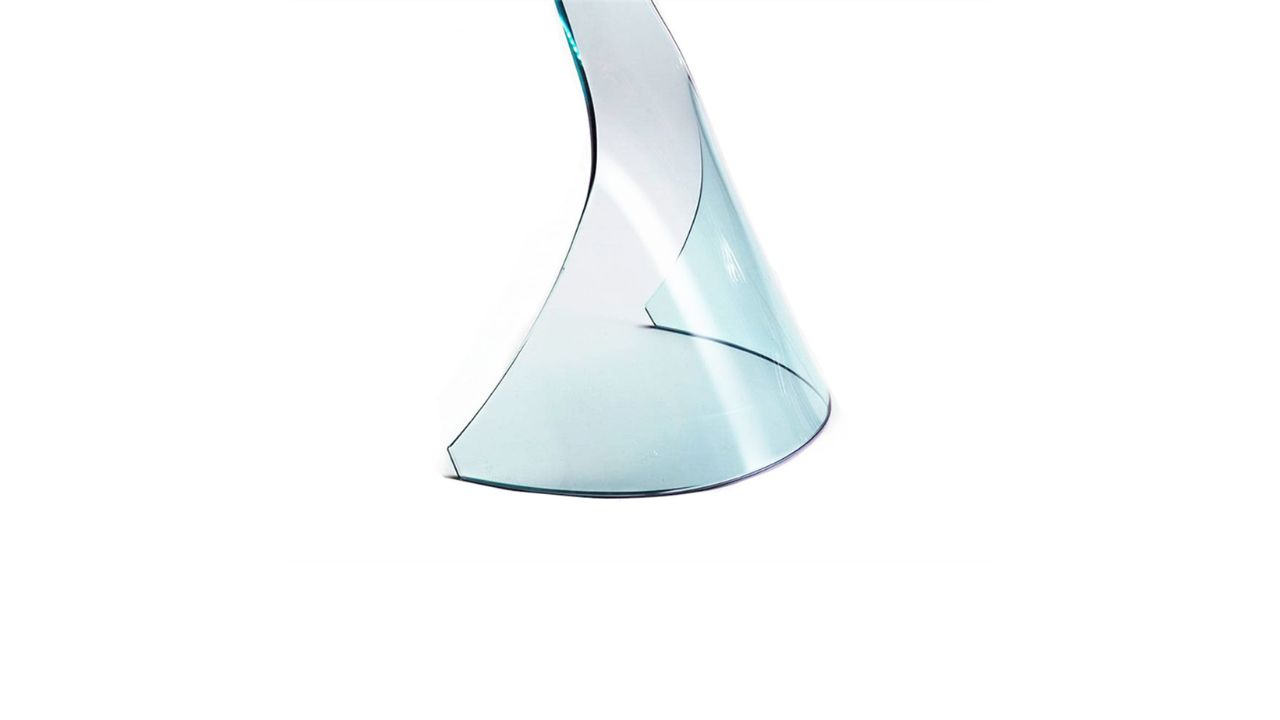
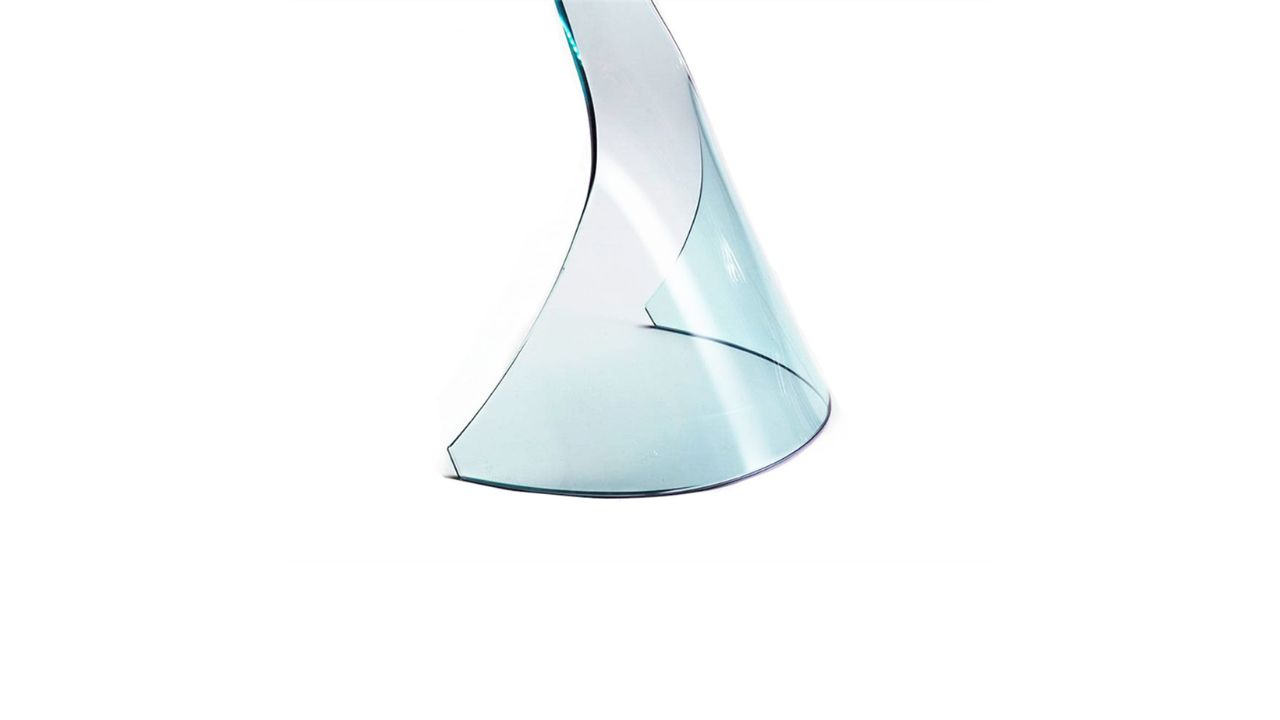
Interior Design Trends
How To Shape Glass
Modified: February 18, 2024
Discover the latest interior design trends with our guide on how to shape glass. Elevate your space with modern glass design ideas and techniques.
(Many of the links in this article redirect to a specific reviewed product. Your purchase of these products through affiliate links helps to generate commission for Storables.com, at no extra cost. Learn more)
Introduction
Shaping glass is a fascinating and intricate process that requires precision, skill, and an understanding of the unique properties of this versatile material. Whether you are a seasoned artisan or an enthusiastic DIY enthusiast, mastering the art of shaping glass opens up a world of creative possibilities. From crafting exquisite glassware to creating custom-designed windows, the ability to shape glass empowers individuals to bring their artistic visions to life.
The process of shaping glass involves a delicate balance of artistry and technical expertise. Each step, from selecting the right type of glass to applying the appropriate shaping techniques, contributes to the final outcome. Understanding the behavior of glass under different conditions and knowing how to manipulate it effectively are essential aspects of this craft.
In this comprehensive guide, we will delve into the intricacies of shaping glass, exploring the properties of glass that influence the shaping process, the tools and equipment needed to execute various shaping techniques, and the crucial safety precautions to ensure a secure working environment. Additionally, we will outline the step-by-step process of shaping glass, from initial preparation to the finishing and polishing stages.
By gaining insight into the art of shaping glass, you will not only expand your creative horizons but also develop a profound appreciation for the beauty and versatility of this remarkable material. Whether you aspire to create stunning glass sculptures, intricate stained glass designs, or functional glassware, the knowledge and skills acquired through this guide will serve as a valuable foundation for your glass-shaping endeavors. Let's embark on this captivating journey into the world of glass shaping and unlock the potential to transform ordinary glass into extraordinary works of art.
Key Takeaways:
- Shaping glass requires understanding its properties, using specialized tools, and prioritizing safety. It’s a meticulous process that transforms raw glass into stunning, purposeful creations.
- The art of shaping glass involves precision, artistry, and meticulous craftsmanship. From cutting and grinding to finishing and polishing, it’s a captivating journey of transforming glass into refined, elegant creations.
Read more: How Is Glass Shaped
Understanding the Properties of Glass
Glass, a material with a rich history dating back thousands of years, possesses unique properties that distinguish it from other substances. Understanding these properties is fundamental to the process of shaping glass effectively.
Transparency and Optical Clarity
One of the most distinctive features of glass is its transparency, allowing light to pass through and creating a sense of openness and luminosity. This property makes glass an ideal medium for creating visually captivating objects, such as decorative ornaments, intricate sculptures, and architectural elements like windows and skylights. The optical clarity of glass enables it to transmit and refract light, adding a dynamic dimension to any space.
Strength and Fragility
Glass exhibits a remarkable combination of strength and fragility. While it can withstand significant compressive forces, it is susceptible to shattering upon impact or when subjected to tensile stress. This duality of strength and fragility necessitates careful handling and precise shaping techniques to harness the material's resilience while mitigating the risk of breakage.
Thermal Responsiveness
The behavior of glass is profoundly influenced by changes in temperature. When heated, glass becomes malleable, allowing artisans to shape it into intricate forms. Conversely, rapid cooling can induce internal stresses, potentially leading to fractures. This thermal responsiveness underscores the importance of controlled heating and cooling processes during glass shaping, ensuring the integrity of the final product.
Chemical Inertness
Glass is chemically inert, meaning it does not react with most substances. This property makes it an excellent choice for containing and preserving various liquids and solids, as well as for creating laboratory equipment and medical instruments. The inert nature of glass also contributes to its durability, making it resistant to corrosion and degradation over time.
Versatility and Aesthetic Appeal
The versatility of glass as a creative medium is unparalleled. It can be shaped into an array of forms, from delicate filigree to bold, sculptural compositions. Its ability to assume diverse textures, colors, and finishes further expands the possibilities for artistic expression. Whether used in traditional or contemporary contexts, glass captivates with its aesthetic allure, adding a touch of elegance and sophistication to any environment.
By comprehending these inherent properties of glass, artisans and enthusiasts can navigate the intricacies of shaping this remarkable material with precision and insight, unlocking its full potential to inspire and enchant.
Tools and Equipment Needed
The art of shaping glass requires a specialized set of tools and equipment designed to facilitate precise manipulation and transformation of this unique material. From cutting and grinding to shaping and polishing, each stage of the glass-shaping process demands the use of specific instruments tailored to the intricacies of working with glass.
Glass Cutter
A fundamental tool in glass shaping, the glass cutter features a small, hardened steel wheel that scores the surface of the glass, enabling controlled separation along the scored line. This essential implement comes in various designs, including handheld cutters and precision oil-fed cutters, each suited to different applications and levels of precision.
Read more: Why Is A Martini Glass Shaped The Way It Is
Glass Grinder
To refine and shape glass edges, a glass grinder equipped with diamond-coated bits is indispensable. This versatile tool allows artisans to meticulously smooth rough edges, create intricate bevels, and achieve precise contours, enhancing the overall aesthetic and safety of the glasswork.
Glass Kiln
For projects involving glass fusing, slumping, or shaping through controlled heating, a glass kiln is essential. This specialized oven provides a controlled environment for heating glass to specific temperatures, enabling artisans to achieve desired forms and textures through careful manipulation of the glass's thermal properties.
Glassblowing Tools
In the realm of glassblowing, a distinct set of tools, including blowpipes, punties, jacks, and shears, are utilized to shape molten glass into exquisite, freeform creations. These tools enable artisans to manipulate the molten glass with precision, creating intricate patterns, textures, and sculptural forms.
Safety Gear
Given the inherent risks associated with working with glass, appropriate safety gear is paramount. Safety glasses, gloves, and protective clothing shield artisans from potential hazards, such as glass shards and heat-related injuries, ensuring a secure working environment.
Read more: How To Shape Brass With Hand Tools
Lapping and Polishing Equipment
To achieve a flawless, lustrous finish on glass surfaces, lapping and polishing equipment, such as lap wheels, polishing pads, and cerium oxide, are employed. These tools enable artisans to refine the glass's surface, removing imperfections and enhancing its visual appeal.
Cutting and Shaping Templates
Precision cutting and shaping templates aid in achieving consistent, accurate dimensions and shapes during the glass-cutting and shaping process. These templates serve as guides for creating intricate designs and ensuring uniformity across multiple glass components.
Miscellaneous Tools
Additional tools, including glass saws, grozing pliers, and UV glue curing lamps, cater to specific shaping and assembly requirements, offering versatility and precision in executing diverse glass-shaping techniques.
By assembling a comprehensive array of tools and equipment tailored to the intricacies of glass shaping, artisans and enthusiasts can embark on their creative endeavors with confidence, precision, and a commitment to excellence. Each tool plays a vital role in shaping glass, empowering individuals to bring their artistic visions to fruition with finesse and ingenuity.
Safety Precautions
Ensuring a safe working environment is paramount when engaging in the art of shaping glass. The inherent fragility of glass, coupled with the potential risks associated with cutting, grinding, and handling heated glass, underscores the critical importance of adhering to stringent safety precautions. By implementing comprehensive safety measures, artisans and enthusiasts can mitigate hazards and safeguard their well-being throughout the glass-shaping process.
Read more: How To Shape A Pool Cue Tip With Sandpaper
Protective Gear
Prior to commencing any glass-shaping activities, it is imperative to don appropriate protective gear. Safety glasses with side shields provide essential eye protection, shielding against potential splinters, shards, and abrasive particles generated during cutting and grinding processes. Additionally, wearing cut-resistant gloves minimizes the risk of lacerations and punctures, particularly when handling sharp glass edges and utilizing cutting tools. Furthermore, donning long-sleeved clothing and closed-toe shoes offers added protection against accidental contact with glass fragments and hot surfaces, reducing the likelihood of injuries.
Ventilation and Respiratory Protection
Effective ventilation is crucial when working with glass, especially during grinding and polishing stages where fine glass particles may become airborne. Adequate ventilation systems or the use of respirators equipped with appropriate filters help mitigate the inhalation of glass dust, ensuring respiratory health and minimizing potential long-term health risks associated with prolonged exposure to airborne glass particles.
Workspace Organization
Maintaining a well-organized workspace is essential for minimizing accidents and promoting efficient glass-shaping processes. Clearing work surfaces of clutter and unnecessary obstructions reduces the risk of accidental falls and injuries. Additionally, ensuring that tools and equipment are properly stored when not in use prevents potential tripping hazards and promotes a safe, unobstructed working environment.
Handling Hot Glass
When working with heated glass, whether in a kiln or through glassblowing techniques, exercising caution and employing heat-resistant gloves are imperative. Proper handling of hot glass minimizes the risk of burns and thermal injuries, ensuring the safety of the artisan throughout the shaping and manipulation of molten or heated glass.
Read more: What Is The Shape Of A Brick
First Aid Preparedness
In the event of minor cuts, abrasions, or other injuries, having a well-equipped first aid kit readily accessible in the workspace is essential. Basic first aid supplies, including adhesive bandages, antiseptic ointment, and sterile gauze, enable prompt and effective treatment of minor injuries, promoting a safe and responsive approach to addressing unexpected mishaps.
By prioritizing safety precautions and integrating them into every facet of the glass-shaping process, artisans and enthusiasts can cultivate a secure and conducive environment for their creative endeavors. Embracing a safety-first mindset not only safeguards against potential hazards but also fosters a culture of responsible and conscientious glass shaping, ensuring a fulfilling and risk-aware approach to this captivating art form.
Steps for Shaping Glass
Shaping glass is a meticulous and multi-faceted process that encompasses a series of precise steps, each contributing to the transformation of raw glass into refined, purposeful creations. Whether crafting intricate stained glass panels, sculpting elegant glassware, or shaping bespoke architectural elements, the following steps outline a comprehensive approach to shaping glass with finesse and expertise.
-
Design and Preparation: The journey of shaping glass begins with conceptualization and meticulous planning. Define the desired form, dimensions, and aesthetic attributes of the glass object or structure. Prepare detailed sketches or digital renderings to serve as a blueprint for the shaping process. Select the appropriate type of glass based on the intended application, considering factors such as transparency, strength, and thermal properties.
-
Glass Cutting: Using a glass cutter, score the selected glass sheet along the predetermined lines, ensuring precision and accuracy. Employ cutting templates or guides to achieve consistent dimensions and shapes. Carefully apply controlled pressure to create clean, straight cuts or intricate curves, depending on the design requirements.
-
Grinding and Shaping: After cutting the glass components, utilize a glass grinder equipped with diamond-coated bits to refine the edges and shape the glass to the desired contours. This step involves meticulous attention to detail, as artisans gradually smooth rough edges, create beveled surfaces, and achieve precise angles, enhancing both the visual appeal and safety of the glasswork.
-
Heating and Forming (Optional): For projects involving glass fusing, slumping, or glassblowing, controlled heating and forming processes are employed. In a glass kiln, carefully heat the glass to specific temperatures, allowing it to fuse together, slump into molds, or assume freeform shapes through controlled manipulation. In the case of glassblowing, molten glass is shaped using specialized tools and techniques, requiring exceptional skill and dexterity.
-
Assembly and Finishing: Assemble the individual glass components, employing UV-curing adhesives or traditional soldering techniques for stained glass applications. Ensure precise alignment and secure bonding to create a cohesive, structurally sound composition. Following assembly, employ lapping and polishing equipment to refine the glass surfaces, removing imperfections and achieving a flawless, lustrous finish.
-
Quality Inspection: Thoroughly examine the shaped glass object or structure, scrutinizing for any imperfections, irregularities, or structural weaknesses. Verify that the dimensions, angles, and surface finishes align with the initial design specifications. Address any discrepancies through additional grinding, shaping, or polishing as necessary, ensuring the highest standards of craftsmanship and quality.
By meticulously adhering to these steps, artisans and enthusiasts can navigate the complexities of shaping glass with precision and artistry, culminating in the realization of stunning, purposeful glass creations that captivate and inspire. Each step represents a pivotal stage in the transformative journey from raw glass to refined artistry, embodying the dedication and expertise required to master the craft of shaping glass.
Finishing and Polishing Techniques
The final stages of shaping glass involve meticulous attention to detail and the application of specialized finishing and polishing techniques to refine the glass surfaces, enhance visual clarity, and achieve a flawless, lustrous finish. These critical steps not only contribute to the aesthetic appeal of the glasswork but also ensure the integrity and quality of the final product.
Read more: How To Shape Brass With Hand Tools
Lapping and Polishing Equipment
Lapping and polishing equipment, including lap wheels, polishing pads, and cerium oxide, play a pivotal role in refining the surfaces of shaped glass components. The lapping process involves the use of abrasive materials, such as diamond-embedded laps, to gradually remove imperfections and irregularities from the glass surfaces. This meticulous approach results in the creation of smooth, uniform surfaces, setting the stage for the subsequent polishing phase.
Polishing pads, often impregnated with fine abrasive compounds, are employed to further enhance the optical clarity and luster of the glass. By systematically progressing through increasingly finer grades of polishing pads, artisans achieve a mirror-like finish, imbuing the glass with a captivating sheen and brilliance. Cerium oxide, a rare-earth compound renowned for its exceptional polishing properties, is frequently utilized to achieve unparalleled levels of clarity and shine, particularly in the context of precision optical glass and decorative glassware.
Read more: How To Shape Metal With Hand Tools
Precision and Finesse
The application of finishing and polishing techniques demands precision and finesse, as artisans meticulously navigate the glass surfaces, ensuring uniformity and flawlessness. Each stroke of the polishing pad or lap wheel contributes to the gradual refinement of the glass, gradually eradicating imperfections and blemishes. This meticulous approach is underpinned by a commitment to achieving the highest standards of craftsmanship, elevating the glasswork to a level of unparalleled visual sophistication and elegance.
Visual Inspection and Quality Assurance
Following the application of finishing and polishing techniques, a comprehensive visual inspection is conducted to scrutinize the glass surfaces for any remaining imperfections or irregularities. This meticulous examination ensures that the glass exhibits a pristine, unblemished appearance, free from any visual distortions or surface defects. Any discrepancies are promptly addressed through targeted polishing or lapping, reaffirming the dedication to delivering glasswork of uncompromising quality and visual allure.
The Artistry of Refinement
The artistry of refinement inherent in finishing and polishing techniques elevates the glass shaping process to a realm of unparalleled sophistication and visual splendor. Each meticulously polished surface reflects the dedication and expertise invested in shaping and transforming raw glass into exquisite, refined creations. The culmination of these techniques is a testament to the fusion of technical mastery and artistic vision, resulting in glasswork that captivates with its luminous clarity and impeccable finish.
By embracing the intricacies of finishing and polishing techniques, artisans and enthusiasts infuse their glass creations with a timeless elegance and allure, showcasing the transformative power of precision and artistry in the realm of glass shaping.
Conclusion
In conclusion, the art of shaping glass is a captivating fusion of technical expertise, artistic vision, and meticulous craftsmanship. From understanding the inherent properties of glass to mastering the intricacies of cutting, grinding, and shaping, this comprehensive guide has illuminated the multifaceted journey of transforming raw glass into refined, purposeful creations.
The properties of glass, including its transparency, strength, thermal responsiveness, and chemical inertness, form the foundation upon which the art of shaping glass is built. By comprehending these properties, artisans and enthusiasts gain a profound appreciation for the unique characteristics of glass and the ways in which they influence the shaping process.
The tools and equipment essential for shaping glass serve as indispensable allies, empowering individuals to execute precise cuts, refine edges, and achieve intricate forms with finesse and accuracy. From glass cutters and grinders to kilns and lapping equipment, each tool plays a pivotal role in shaping glass, enabling artisans to bring their creative visions to life.
Safety precautions, an integral aspect of the glass-shaping process, underscore the commitment to fostering a secure and conducive working environment. By prioritizing protective gear, ventilation, workspace organization, and first aid preparedness, artisans and enthusiasts uphold a safety-first mindset, ensuring the well-being of all involved in the glass-shaping endeavor.
The step-by-step process of shaping glass, encompassing design and preparation, cutting, grinding, heating and forming, assembly, and quality inspection, provides a comprehensive roadmap for navigating the complexities of glass shaping. Each step represents a pivotal stage in the transformative journey from raw glass to refined artistry, embodying the dedication and expertise required to master the craft of shaping glass.
The final stages of finishing and polishing techniques elevate the glass shaping process to a realm of unparalleled sophistication and visual splendor. Through meticulous refinement and visual inspection, artisans imbue their glass creations with a timeless elegance and allure, showcasing the transformative power of precision and artistry in the realm of glass shaping.
In essence, the art of shaping glass transcends the boundaries of craftsmanship, embodying a harmonious blend of technical mastery and artistic expression. Whether crafting intricate stained glass panels, sculpting elegant glassware, or shaping bespoke architectural elements, the journey of shaping glass is a testament to the transformative potential of this remarkable material. By embracing the intricacies of glass shaping, artisans and enthusiasts unlock a world of creative possibilities, where raw glass evolves into extraordinary works of art that captivate and inspire.
Frequently Asked Questions about How To Shape Glass
Was this page helpful?
At Storables.com, we guarantee accurate and reliable information. Our content, validated by Expert Board Contributors, is crafted following stringent Editorial Policies. We're committed to providing you with well-researched, expert-backed insights for all your informational needs.
0 thoughts on “How To Shape Glass”