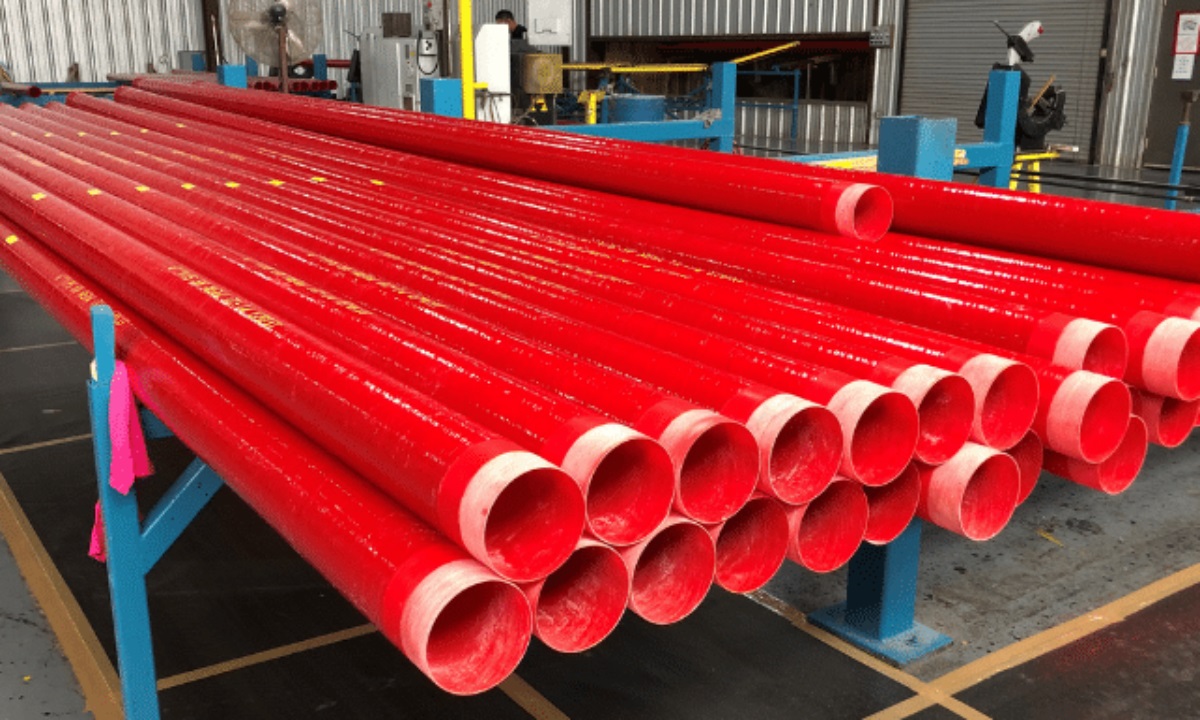
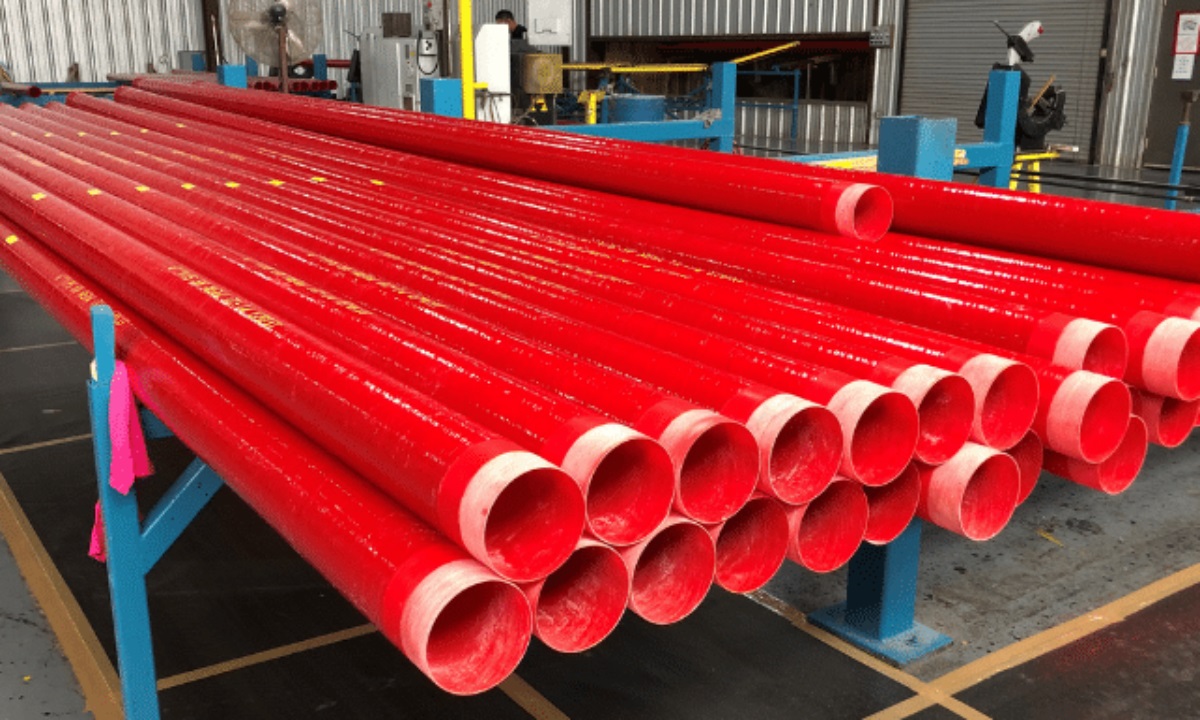
Articles
How Heavy Is Fiberglass Conduit
Modified: October 20, 2024
Learn about the weight of fiberglass conduit in our informative articles. Find out how this durable material compares to other options.
(Many of the links in this article redirect to a specific reviewed product. Your purchase of these products through affiliate links helps to generate commission for Storables.com, at no extra cost. Learn more)
Introduction
Fiberglass conduit is a versatile and durable solution for electrical and telecommunications installations. It offers a range of benefits, including corrosion resistance, high strength, and ease of installation. One important aspect to consider when choosing a conduit material is its weight.
In this article, we will explore the weight of fiberglass conduit and its significance in various applications. We will discuss the properties of fiberglass conduit, factors affecting its weight, and compare it to other conduit materials. Additionally, we will highlight the benefits of using lightweight fiberglass conduit and explore its wide-ranging applications.
Whether you are an electrical contractor, engineer, or someone interested in infrastructure installations, understanding the weight of fiberglass conduit is crucial for making informed decisions.
Key Takeaways:
- Lightweight fiberglass conduit offers ease of handling, simplified installation, and cost savings. Its non-conductive, corrosion-resistant, and durable nature makes it ideal for various applications, from industrial facilities to transportation infrastructure.
- Fiberglass conduit’s significantly lighter weight compared to metal and PVC options provides practical advantages, including reduced strain on installers, faster installation times, and lower transportation costs. Its versatility and efficiency make it a reliable choice for protecting electrical and communication systems.
Read more: How To Work With Fiberglass Tape
What is Fiberglass Conduit?
Fiberglass conduit, also known as fibreglass reinforced polymer (FRP) conduit, is a type of conduit made from a composite material consisting of resin and glass fibers. It is designed to provide a protective pathway for electrical cables, wires, and other communication infrastructure.
The manufacturing process of fiberglass conduit involves impregnating glass fibers with a resin matrix, usually made of polyester or vinyl ester. This combination results in a lightweight but highly durable material that offers excellent resistance to corrosion, UV radiation, and chemical exposure.
Unlike traditional conduit materials such as metal or PVC, fiberglass conduit boasts exceptional strength-to-weight ratio, making it a preferred choice in various applications where weight plays a crucial role.
Due to its non-conductive nature, fiberglass conduit is an ideal solution for protecting electrical cables in environments where conductivity can pose a safety risk. It also eliminates the need for grounding, providing additional convenience during installation.
Furthermore, fiberglass conduit is available in a range of shapes and sizes to accommodate different installation requirements. It can be found in various forms, including rigid conduit, conduit fittings, elbows, and conduit bodies.
Overall, fiberglass conduit is an innovative and reliable choice for electrical and communication infrastructure due to its exceptional durability, non-conductivity, and versatility.
Properties of Fiberglass Conduit
Fiberglass conduit possesses a unique set of properties that make it an advantageous choice for electrical and telecommunications installations. Here are some key properties of fiberglass conduit:
1. Corrosion Resistance: Fiberglass conduit is highly resistant to corrosion caused by moisture, chemicals, and other environmental factors. This property ensures a longer lifespan and reduces the need for frequent maintenance or replacement.
2. Non-Conductivity: Unlike metal conduits, fiberglass conduit is non-conductive, making it an excellent choice for applications where electrical insulation is required. It eliminates the risk of electrical shock and prevents interference or signal loss in communication cables.
3. High Strength: Despite its lightweight nature, fiberglass conduit exhibits exceptional strength. It has a high tensile strength, which means it can withstand significant tension without breaking or deforming. This property makes fiberglass conduit suitable for demanding installations, such as underground or overhead applications.
4. Flexibility: Fiberglass conduit is flexible, allowing for easy bending and maneuvering during installation. This flexibility reduces the need for additional fittings and simplifies the routing of cables, saving time and effort.
5. UV Resistance: Fiberglass conduit is designed to resist the damaging effects of UV radiation from the sun. It does not degrade or become brittle when exposed to prolonged sunlight, ensuring its longevity and performance in outdoor applications.
6. Fire Resistance: Fiberglass conduit has excellent fire-resistant properties. It does not support combustion and has a high ignition temperature, making it ideal for installations where fire safety is a priority.
7. Chemical Resistance: Fiberglass conduit is resistant to a wide range of chemicals, including acids, alkalis, and solvents. This property allows it to withstand exposure to harsh environments, such as chemical processing plants or industrial facilities.
8. Low Thermal Conductivity: Fiberglass conduit has a low thermal conductivity, which means it does not easily transfer heat. This property helps protect cables from overheating and minimizes the risk of thermal damage.
Overall, the unique combination of corrosion resistance, non-conductivity, high strength, flexibility, and other properties makes fiberglass conduit an excellent choice for a variety of electrical and telecommunications applications. Its durable and reliable nature ensures optimal performance and longevity in various environmental conditions.
Weight of Fiberglass Conduit
One of the key advantages of fiberglass conduit is its lightweight nature. Compared to other conduit materials like metal or PVC, fiberglass conduit offers a significantly lower weight, making it easier to handle and install.
The weight of fiberglass conduit can vary based on several factors, including the diameter, thickness, and length of the conduit. Generally, fiberglass conduit is much lighter than traditional conduit materials, making it a preferred choice in applications where weight is a critical consideration.
The weight of fiberglass conduit is typically measured in pounds per linear foot (lb/ft) or kilograms per meter (kg/m). The exact weight will depend on the specific product and manufacturer, as well as any additional fittings or accessories included.
On average, fiberglass conduit weighs approximately 0.25-0.5 pounds per linear foot, or 0.37-0.74 kilograms per meter. This makes it significantly lighter than metal conduit, which can weigh around 1-2 pounds per linear foot, or 1.49-2.98 kilograms per meter. PVC conduit falls somewhere in between, typically weighing around 0.4-0.8 pounds per linear foot, or 0.6-1.19 kilograms per meter.
The reduced weight of fiberglass conduit offers numerous benefits. Firstly, it simplifies transportation and handling, allowing for easier maneuverability on the job site. This can lead to increased efficiency and productivity during installation.
Additionally, the lightweight nature of fiberglass conduit reduces the strain and physical exertion required during installation. It makes it easier for installers to carry and position the conduit, minimizing the risk of strain-related injuries and making the overall installation process more comfortable.
Furthermore, the reduced weight of fiberglass conduit can also have cost-saving implications. The lighter weight means fewer resources are required for transportation, resulting in lower shipping costs. It also enables more efficient use of labor, as installers can work more quickly and with less effort.
Overall, the lightweight nature of fiberglass conduit offers practical advantages in terms of ease of handling, installation efficiency, and cost-effectiveness. Its reduced weight makes it an appealing choice for infrastructure projects where weight considerations are key.
Factors Affecting the Weight of Fiberglass Conduit
The weight of fiberglass conduit can vary depending on several factors. Understanding these factors is essential for selecting the appropriate conduit for your specific application. Here are some key factors that can affect the weight of fiberglass conduit:
1. Diameter: The diameter of the fiberglass conduit greatly influences its weight. As the diameter increases, the weight of the conduit tends to increase as well. Larger diameter conduit requires more material, which adds to its overall weight. Conversely, smaller diameter conduit is lighter due to the lesser amount of material needed.
2. Wall Thickness: The thickness of the walls of fiberglass conduit can also impact its weight. Thicker-walled conduit will be heavier compared to conduit with thinner walls. The thickness of the walls is usually determined based on the application and the required level of strength and durability.
3. Length: The length of the fiberglass conduit is a significant factor in determining its weight. Longer lengths of conduit will inherently weigh more than shorter lengths. When planning an installation, it is important to consider the total length of conduit required and its impact on transportation and handling.
4. Reinforcement: Fiberglass conduit can be reinforced with additional layers or materials to enhance its strength and durability. The presence of reinforcing layers, such as extra glass fibers or structural bracing, can increase the weight of the conduit.
5. Accessories and Fittings: The weight of the fiberglass conduit may also be affected by any accessories or fittings attached to it. This includes elbows, connectors, couplings, and other fittings required for routing and connecting the conduit system. These additional components can add to the overall weight of the conduit.
6. Manufacturing Standards: Different manufacturers may produce fiberglass conduit with varying densities or resin-to-fiber ratios. These variations in manufacturing standards can result in differences in weight. It is important to check the specifications provided by the manufacturer to ensure consistency and accuracy in weight calculations.
7. Temperature Variation: Extreme temperature variations can cause slight changes in the weight of fiberglass conduit. Expansion and contraction due to temperature fluctuations can result in minimal weight variations but are typically negligible for most applications.
It is important to consider these factors when determining the weight requirements for your specific project. By understanding the factors that influence the weight of fiberglass conduit, you can make informed decisions and select the most suitable conduit for your application.
When determining the weight of fiberglass conduit, consider the diameter and wall thickness, as these factors will significantly impact the overall weight of the conduit. Additionally, be sure to account for any additional components, such as fittings or connectors, when calculating the total weight of the conduit system.
Read more: How To Whiten A Fiberglass Bathtub
Comparison of Fiberglass Conduit Weight to Other Conduit Materials
When choosing a conduit material, it is essential to consider the weight as it can impact transportation, installation, and overall project costs. Fiberglass conduit stands out in terms of its lightweight nature compared to other common conduit materials. Let’s compare the weight of fiberglass conduit to other popular options:
1. Metal Conduit: Metal conduit, such as galvanized steel or aluminum, is known for its strength and durability. However, it tends to be much heavier than fiberglass conduit. While the weight can vary depending on the specific type and diameter of metal conduit, it typically weighs around 1-2 pounds per linear foot (1.49-2.98 kilograms per meter). This weight can make metal conduit more challenging to transport and maneuver during installation.
2. PVC Conduit: PVC conduit is a popular choice due to its affordability and ease of installation. It offers a middle-ground option in terms of weight. PVC conduit is lighter than metal conduit but heavier than fiberglass conduit. On average, PVC conduit weighs around 0.4-0.8 pounds per linear foot (0.6-1.19 kilograms per meter). While still lighter than metal conduit, the weight of PVC conduit can make it slightly more cumbersome to handle and install compared to fiberglass conduit.
3. HDPE Conduit: High-density polyethylene (HDPE) conduit is another lightweight alternative to fiberglass. HDPE conduit is a plastic-based solution that offers several benefits, including resistance to corrosion, UV radiation, and impact. The weight of HDPE conduit can vary depending on its diameter and wall thickness. On average, HDPE conduit weighs around 0.2-0.7 pounds per linear foot (0.3-1.04 kilograms per meter), making it comparable to or slightly lighter than fiberglass conduit.
4. EMT Conduit: Electrical metallic tubing (EMT) is a lightweight steel conduit commonly used in electrical installations. It is lighter than rigid metal conduit but heavier than fiberglass conduit. The weight of EMT conduit varies based on its diameter, with an average weight of around 0.3-0.7 pounds per linear foot (0.45-1.04 kilograms per meter).
Compared to these other materials, fiberglass conduit stands out for its exceptionally low weight. Fiberglass conduit typically weighs around 0.25-0.5 pounds per linear foot (0.37-0.74 kilograms per meter). Its lightweight nature offers advantages in terms of ease of handling, reduced strain on installers, and lower transportation costs.
The reduced weight of fiberglass conduit also contributes to faster installation times, as it can be easily maneuvered and positioned. This can result in increased efficiency and productivity on the job site.
Overall, the weight comparison highlights the superior lightweight characteristics of fiberglass conduit, making it an appealing choice for various electrical and telecommunications applications.
Benefits of Using Lightweight Fiberglass Conduit
Lightweight fiberglass conduit offers several significant benefits, making it an ideal choice for a wide range of electrical and telecommunications applications. Here are the key advantages of using lightweight fiberglass conduit:
1. Ease of Handling: The lightweight nature of fiberglass conduit makes it much easier to handle compared to heavier conduit materials such as metal or PVC. Installers can transport and maneuver the conduit more effortlessly, reducing physical strain and fatigue. This ease of handling improves overall installation efficiency and reduces the risk of injuries.
2. Simplified Installation: The reduced weight of fiberglass conduit simplifies the installation process. It is easier to position and secure in place, allowing for faster and more straightforward installations. Furthermore, the lightweight nature of fiberglass conduit eliminates the need for heavy machinery or equipment to move and lift it, further streamlining the installation process.
3. Cost Savings: Lightweight fiberglass conduit can lead to cost savings in various ways. The reduced weight means lower transportation costs, as less fuel and resources are needed to transport the conduit. Additionally, the ease of installation results in shorter labor times, reducing labor costs. Overall, the cost savings associated with lightweight fiberglass conduit contribute to a more budget-friendly solution.
4. Non-Conductivity: Fiberglass conduit is non-conductive, making it an excellent choice for applications where electrical insulation is crucial. It eliminates the risk of electrical shock and prevents interference or signal loss in communication cables. The non-conductive nature of fiberglass conduit provides added safety and reliability in electrical installations.
5. Corrosion Resistance: Fiberglass conduit offers exceptional resistance to corrosion, even in harsh environmental conditions. It does not rust, corrode, or deteriorate when exposed to moisture, chemicals, or UV radiation. This longevity ensures that the conduit maintains its structural integrity over time, protecting the cables and wiring within.
6. Flexibility: Lightweight fiberglass conduit is designed to be flexible, allowing for easy bending and routing during installation. It can navigate around obstacles and follow complex pathways, saving time and effort. The flexibility of fiberglass conduit makes it versatile and adaptable to various installation scenarios.
7. Low Maintenance: Fiberglass conduit requires minimal maintenance compared to traditional conduit materials. Its resistance to corrosion and degradation means less upkeep and fewer repairs over time. This low maintenance requirement translates to cost savings and reduced downtime in electrical systems.
8. Durability: Despite its lightweight nature, fiberglass conduit is highly durable. It offers exceptional strength and can withstand impact, vibration, and environmental stressors. This durability ensures the longevity and reliability of the conduit system, reducing the need for frequent replacements.
In summary, the benefits of using lightweight fiberglass conduit include ease of handling, simplified installation, cost savings, non-conductivity, corrosion resistance, flexibility, low maintenance, and durability. These advantages make fiberglass conduit an excellent choice for a wide range of applications, providing long-term performance, reliability, and safety.
Applications of Fiberglass Conduit
Fiberglass conduit is a versatile solution that finds extensive use in various electrical and telecommunications applications. Its unique properties and lightweight nature make it ideal for a wide range of installations. Here are some common applications of fiberglass conduit:
1. Industrial Facilities: Fiberglass conduit is widely used in industrial environments, including factories, plants, and refineries. Its corrosion resistance and durability make it suitable for protecting electrical cables and wiring in harsh chemical and high-moisture areas.
2. Commercial Buildings: Fiberglass conduit is commonly employed in commercial buildings such as offices, retail spaces, and hospitals. Its lightweight nature simplifies installation in complex building structures and tight spaces. Additionally, its non-conductive properties provide an extra level of safety in these high-traffic environments.
3. Motorway Communications: Along highways and motorways, fiberglass conduit is utilized for routing communication cables, fiber optics, and surveillance systems. Its UV resistance prevents degradation from exposure to sunlight, ensuring long-lasting performance in outdoor installations.
4. Data Centers: Data centers demand reliable cable management systems, and fiberglass conduit meets these requirements. Its non-conductive, corrosion-resistant properties, along with its ease of handling and flexibility, make it an ideal choice for protecting critical data and communication cables.
5. Renewable Energy Projects: Fiberglass conduit is commonly used in renewable energy projects, such as wind farms and solar power installations. Its resistance to environmental factors, including UV radiation and temperature fluctuations, ensures the long-term integrity of the conduit system and reliable power transmission.
6. Transportation Infrastructure: Fiberglass conduit plays a vital role in transportation infrastructure projects, including subway systems, railways, and airports. Its lightweight nature facilitates easy and quick installation, even in challenging environments. Fiberglass conduit helps protect electrical wiring and communication systems essential for transportation operations.
7. Water Treatment Plants: Water treatment facilities rely on fiberglass conduit for its resistance to corrosive chemicals and moisture. It ensures reliable electrical wiring and communication systems in these critical infrastructure facilities.
8. Underground Installations: Fiberglass conduit is commonly used for underground installations, such as burying electrical cables or fiber optics. Its durability and corrosion resistance make it an excellent choice for protecting cabling and wiring from moisture and soil conditions.
9. Marine and Offshore Applications: In marine and offshore environments, fiberglass conduit is highly sought after due to its resistance to saltwater, chemicals, and harsh weather conditions. It is commonly used to protect electrical systems on ships, offshore platforms, and marinas.
10. Hazardous Areas: Fiberglass conduit is often preferred in areas classified as hazardous, such as oil and gas facilities or chemical plants. Its non-conductive and corrosion-resistant properties provide an added level of safety, reducing the risk of electrical incidents.
These are just a few examples of the diverse applications of fiberglass conduit. Its lightweight nature, durability, non-conductivity, and corrosion resistance make it a reliable choice in numerous industries and infrastructure installations. Fiberglass conduit continues to provide a cost-effective and efficient solution for protecting electrical and communication systems.
Conclusion
Fiberglass conduit offers a lightweight and durable solution for electrical and telecommunications installations. Its unique properties, including corrosion resistance, non-conductivity, and flexibility, make it an ideal choice for various applications. Understanding the weight of fiberglass conduit is crucial for making informed decisions when selecting conduit materials.
In this article, we explored the properties of fiberglass conduit, factors affecting its weight, and compared its weight to other conduit materials. Fiberglass conduit stands out for its significantly lighter weight compared to metal conduit, PVC conduit, and other options. The lightweight nature of fiberglass conduit offers numerous benefits, including ease of handling, simplified installation, cost savings, non-conductivity, corrosion resistance, flexibility, low maintenance, and durability.
Fiberglass conduit finds applications in a wide range of industries and infrastructure projects. From industrial facilities to commercial buildings, motorway communications to data centers, renewable energy projects to transportation infrastructure, and more, fiberglass conduit is a reliable choice for protecting electrical cables and communication systems.
In conclusion, fiberglass conduit is a versatile and efficient solution that provides long-term performance, reliability, and safety. Its lightweight nature simplifies installation, reduces strain on installers, and offers cost savings. The corrosion resistance and non-conductive properties of fiberglass conduit ensure the protection of electrical systems in various environmental conditions.
Whether you are an electrical contractor, engineer, or someone interested in infrastructure installations, understanding the advantages of lightweight fiberglass conduit is essential. By choosing fiberglass conduit, you can ensure a durable and reliable conduit system that meets the specific needs of your project.
Frequently Asked Questions about How Heavy Is Fiberglass Conduit
Was this page helpful?
At Storables.com, we guarantee accurate and reliable information. Our content, validated by Expert Board Contributors, is crafted following stringent Editorial Policies. We're committed to providing you with well-researched, expert-backed insights for all your informational needs.
0 thoughts on “How Heavy Is Fiberglass Conduit”