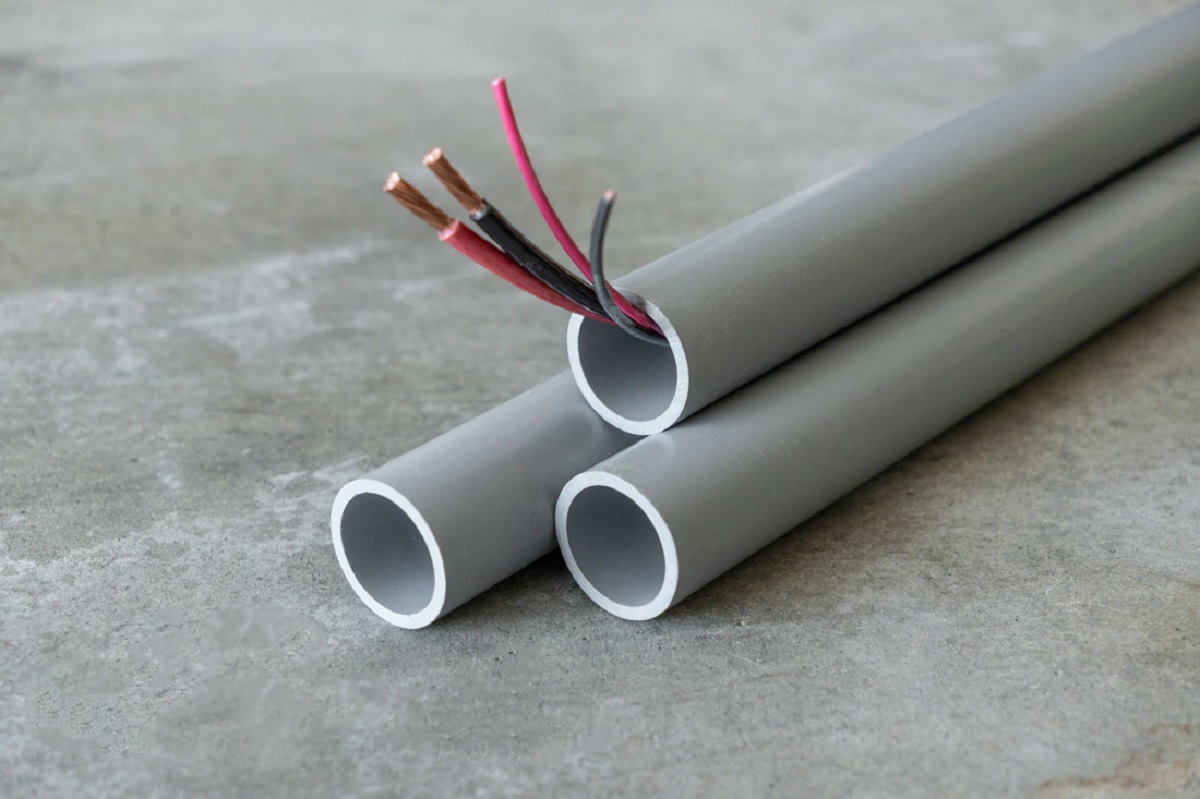
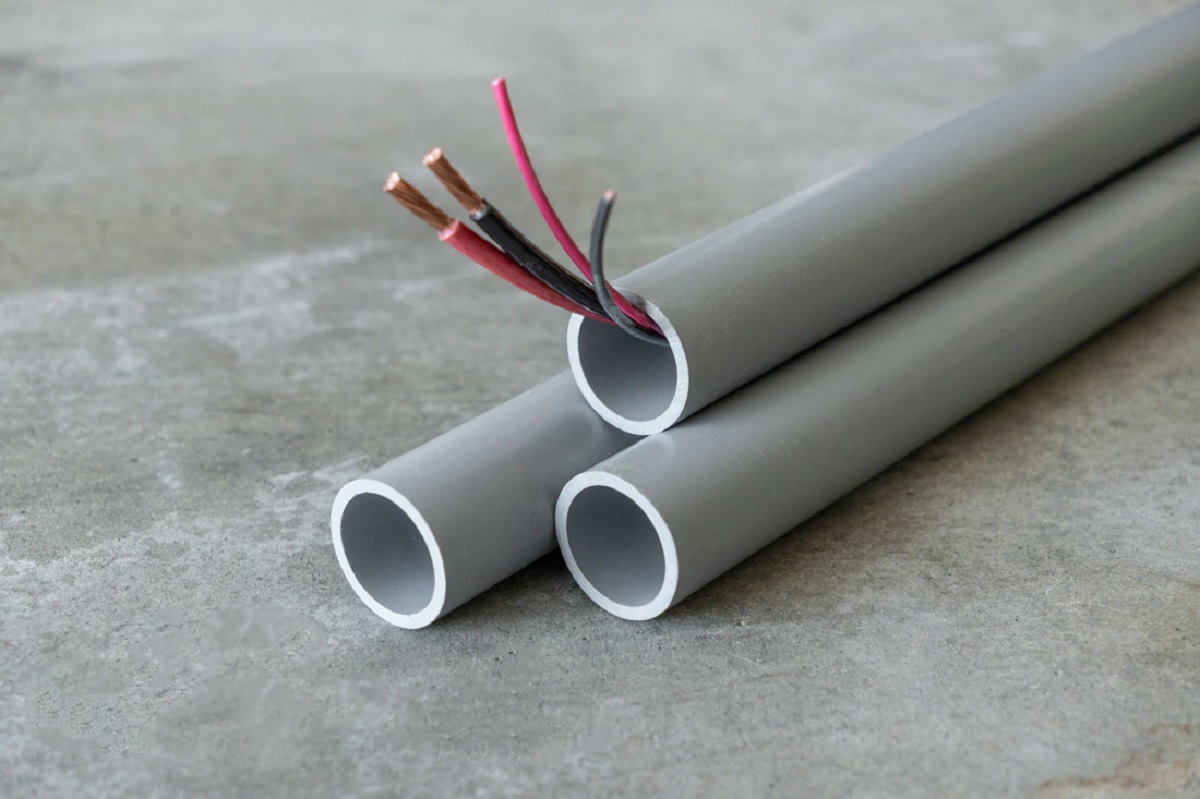
Articles
What Type Of Wire Should Be Used In Conduit
Modified: February 22, 2024
Discover the best type of wire to use in conduit with our informative articles. Find the right information and tips for all your wiring needs.
(Many of the links in this article redirect to a specific reviewed product. Your purchase of these products through affiliate links helps to generate commission for Storables.com, at no extra cost. Learn more)
Introduction
Choosing the right type of wire for conduit is crucial to ensure the safety and efficiency of electrical installations. Conduit is a protective tubing system used to encase electrical wires and cables, providing a barrier against physical damage, moisture, and other environmental factors. It is widely used in residential, commercial, and industrial settings to route and protect electrical wiring.
When it comes to selecting the appropriate wire for conduit, several factors should be taken into consideration. These factors include the environment in which the conduit will be installed, the type of electrical load the wire will be carrying, and the cost-effectiveness of the wire. In this article, we will discuss the different types of wire that are suitable for use in conduit, with a focus on copper and aluminum wire.
Copper wire is the most commonly used type of wire in conduit applications. It offers excellent conductivity, corrosion resistance, flexibility, and durability. Copper wire is available in two main forms: solid copper wire and stranded copper wire. Solid copper wire consists of a single, solid strand of copper, while stranded copper wire is made up of multiple smaller strands twisted together.
Aluminum wire is another option for conduit installations. While it is less commonly used than copper wire, aluminum wire offers several advantages, such as its lighter weight and lower cost. Similar to copper wire, aluminum wire is available in both solid and stranded forms.
It is important to note that the selection of wire for conduit should comply with the electrical code and regulations in your area. This ensures that the wiring system meets safety standards and reduces the risk of electrical hazards.
In the following sections, we will delve deeper into the different types of copper and aluminum wire suitable for use in conduit. We will discuss their characteristics, advantages, and applications. Additionally, we will explore other important considerations when selecting wire for conduit installations. By the end of this article, you will have a comprehensive understanding of the wire options available and be better equipped to make an informed decision for your specific electrical installation needs.
Key Takeaways:
- Choosing the right wire for conduit, whether copper or aluminum, is crucial for safety and efficiency. Factors such as conductor material, wire size, insulation, and compliance with electrical codes must be carefully considered to ensure a reliable electrical system.
- Copper wire, available in solid and stranded forms, offers excellent conductivity and durability, while aluminum wire provides a lightweight and cost-effective alternative. Considering environmental conditions, voltage drop, and code compliance is essential for optimal performance and safety.
Read more: When To Use Conduit For Electrical Wiring
Understanding Conduits
Conduits are an essential component of electrical wiring systems, providing a protective pathway for electrical cables and wires. They come in various materials, including metal (such as steel or aluminum) and non-metal (such as PVC or fiberglass). The choice of conduit material depends on factors such as the application, environment, and specific requirements of the electrical installation.
The main purpose of conduits is to protect the electrical wires from damage. This can include physical damage due to impact, exposure to moisture, chemicals, or extreme temperatures. By enclosing the wires within a conduit, they are shielded from these potential hazards, reducing the risk of electrical failures, shorts, or fires. Conduits also help to organize and route the wires in a neat and structured manner, facilitating maintenance and future installations.
Conduits come in different forms, including rigid conduits, flexible conduits, and liquid-tight conduits. Rigid conduits, made of metal or PVC, are commonly used in commercial and industrial applications where durability is a key consideration. Flexible conduits, often made of metal or plastic, provide added flexibility and are suitable for applications where the wiring needs to be routed around corners or in tight spaces. Liquid-tight conduits are designed to prevent the ingress of liquid or moisture into the electrical system and are used in outdoor or wet locations.
It is important to choose the appropriate size of conduit for the wires being installed. The conduit should have enough space to accommodate the wires comfortably without damaging them or impeding their performance. The National Electrical Code (NEC) provides guidelines on the conduit sizing based on the number and gauge of wires being installed.
In addition to protecting the wires, conduits also play a role in grounding the electrical system. Metal conduits can act as a grounding pathway, providing an additional layer of safety by helping to dissipate any stray currents and preventing electrical shocks. Grounding is crucial for electrical systems to protect equipment and occupants from electrical faults or surges.
Overall, conduits are a crucial part of electrical installations, providing protection, organization, and safety. Understanding the different types of conduits available and their intended applications is essential in selecting the most suitable conduit for your electrical wiring project. Additionally, choosing the right type of wire to be used within the conduit is equally important, as it ensures optimal performance and compliance with safety standards.
Factors to Consider when Choosing Wire for Conduit
When selecting the wire to be used in conduit, it is important to consider several factors to ensure the safety and efficiency of the electrical installation. These factors include:
- Conductor Material: The material of the conductor plays a significant role in the wire’s performance. The most commonly used conductor materials for wiring are copper and aluminum. Copper offers better conductivity and is more resistant to corrosion, making it ideal for most conduit applications. Aluminum, on the other hand, is lighter, more affordable, and can be a suitable alternative for certain installations.
- Wire Size: The size of the wire, measured in gauge or AWG (American Wire Gauge), is crucial in determining its current-carrying capacity. The current load of the wire must match the electrical load it will be carrying. Choosing the correct wire size helps minimize voltage drop, which can affect the efficiency and performance of electrical devices.
- Insulation Type: The insulation material and type of wire should be appropriate for the intended application and environment. Common insulation types include PVC, thermoplastic, and rubber. The insulation should provide proper protection against moisture, heat, and chemicals, depending on the installation location.
- Conduit Type and Size: The type and size of the conduit being used will determine the capacity and space available for the wire. The wire size should be compatible with the conduit size to ensure a proper fit and prevent issues such as wire jamming or overheating.
- Environmental Factors: Consider the environmental conditions in which the wire will be installed. Factors such as temperature extremes, humidity, exposure to chemicals, or outdoor elements should be taken into account. Some wires are specifically designed for harsh environments, offering enhanced protection and durability.
- Installation Method: The method of wire installation, whether it is in a conduit or directly secured, can impact the choice of wire. Conduit installations may require specific types of wire with added flexibility or durability to withstand the bending and pulling forces during installation.
- Code Compliance: It is vital to adhere to local electrical codes and regulations when selecting wire for conduit installations. Codes ensure the safety of electrical systems and should never be compromised. Consulting with a licensed electrician or referencing the National Electrical Code (NEC) can provide guidance on compliance requirements.
By considering these factors, you can make an informed decision when choosing the appropriate wire for your conduit installation. It is crucial to prioritize safety, efficiency, and compliance with electrical standards to ensure a reliable and long-lasting electrical system.
Types of Wire Suitable for Conduit
There are various types of wire suitable for use in conduit, each with its own characteristics and applications. The two primary types of wire commonly used in conduit installations are copper wire and aluminum wire. Let’s explore each of these types in more detail:
Copper Wire
Copper wire is the most popular choice for wiring installations, including conduit applications. It is valued for its high conductivity, corrosion resistance, flexibility, and durability. Copper wire is available in two main forms: solid copper wire and stranded copper wire.
Solid Copper Wire
Solid copper wire consists of a single, solid strand of copper. It is commonly used for smaller wires and in situations where a rigid, secure connection is required. The solid construction makes it less prone to breakage and offers excellent electrical conductivity. However, solid copper wire is less flexible compared to its stranded counterpart, which can make it challenging to work with when routing through conduit bends.
Stranded Copper Wire
Stranded copper wire is made up of multiple smaller strands of copper wire twisted together. This construction provides greater flexibility, making it easier to handle and route through conduit systems. Stranded copper wire is commonly used for larger gauge wires and installations that require increased flexibility. It is also less likely to break under repeated bending or vibration. The strands of wire help distribute the electrical load evenly, reducing the risk of hotspots and improving overall performance. However, stranded copper wire is generally more expensive than solid copper wire due to the additional manufacturing process.
Read more: What Type Of Toothbrush Should I Use
Aluminum Wire
Aluminum wire is an alternative to copper wire in conduit applications. It is lighter in weight and more affordable, making it a popular choice in certain circumstances. Aluminum wire is available in both solid and stranded forms, similar to copper wire.
Solid Aluminum Wire
Solid aluminum wire consists of a single, solid strand of aluminum. It is commonly used for smaller wires and in applications where weight reduction is a priority. However, solid aluminum wire is less conductive than copper wire, which can result in higher resistance and voltage drops. It is important to carefully consider the electrical load and consult local electrical codes before selecting solid aluminum wire for conduit installations.
Stranded Aluminum Wire
Stranded aluminum wire is made up of multiple smaller strands of aluminum wire twisted together. It offers better flexibility and improved conductivity compared to solid aluminum wire. Stranded aluminum wire is commonly used for larger gauge wire applications and installations that require increased flexibility and reduced voltage drop.
When selecting between copper and aluminum wire for conduit installations, it is crucial to consider factors such as cost, electrical load requirements, flexibility, and electrical code compliance. Consulting with a licensed electrician can provide further guidance on the most suitable wire type for your specific application.
Copper Wire
Copper wire is widely regarded as the gold standard in electrical wiring due to its exceptional conductivity, durability, and corrosion resistance. It is the most commonly used type of wire for conduit installations and is valued for its long lifespan and reliability. Copper wire is available in two main forms: solid copper wire and stranded copper wire.
Solid Copper Wire
Solid copper wire consists of a single, solid strand of copper. It is typically used for smaller gauge wires, such as those used in residential wiring or low-power applications. Solid copper wire offers excellent electrical conductivity, allowing for efficient transmission of electrical current. Its single-strand construction provides a secure and rigid connection, making it ideal for applications that require stability and minimal movement.
One of the key advantages of solid copper wire is its resistance to breakage. The solid construction makes it less prone to damage during installation and over time, ensuring a reliable and long-lasting electrical connection. Solid copper wire also has a higher resistance to vibration and mechanical stress, making it suitable for applications where durability is a priority.
One potential drawback of solid copper wire is its lack of flexibility. Solid wire does not have the same bending capabilities as stranded wire, which can make it challenging to route through conduit systems with tight bends or corners. Care must also be taken during installation to prevent sharp bends that can damage or deform solid copper wire. However, the rigidity of solid copper wire can also be an advantage in situations where a fixed, secure connection is required.
Stranded Copper Wire
Stranded copper wire is made up of multiple smaller strands of copper wire that are twisted together. This construction provides increased flexibility compared to solid copper wire, making it easier to handle and route through conduit systems. Stranded copper wire is commonly used for larger gauge wires and in applications that require flexibility, such as installations with numerous bends or where wire movement may occur.
The strands in stranded copper wire distribute the electrical load more evenly, reducing the risk of hotspots and improving the overall performance of the wire. The increased surface area from the stranded construction also enhances the wire’s ability to dissipate heat, which is particularly beneficial in high-current applications.
Stranded copper wire is less prone to breakage under repeated bending or vibration, making it more suitable for applications with frequent movement or mechanical stress. It is also easier to terminate, as the individual strands can be separated to create a secure connection. However, it is worth noting that stranded copper wire is generally more expensive than solid copper wire due to the additional manufacturing process.
Overall, copper wire, whether solid or stranded, is a superior choice for conduit installations due to its excellent electrical conductivity, durability, and corrosion resistance. It is essential to consider factors such as wire size, load requirements, flexibility, and electrical code compliance when selecting the appropriate copper wire for your specific application.
Read more: What Is Conduit Used For
Solid Copper Wire
Solid copper wire, also known as single-strand copper wire, is a type of electrical wire made up of a single, solid strand of copper. It is widely used in various electrical applications, including conduit installations. Solid copper wire offers several advantages and is valued for its conductivity, durability, and versatility.
Conductivity
Copper is renowned for its high electrical conductivity, making solid copper wire an excellent choice for electrical wiring. Copper has one of the best conductive properties among common metals, allowing for efficient transmission of electrical current. The low resistance of solid copper wire minimizes voltage drops, ensuring optimal electrical performance and reducing energy losses in the system.
Durability
One of the key benefits of solid copper wire is its durability. The solid construction of the wire lends it strength and resistance to breakage, making it suitable for a wide range of applications. Solid copper wire can withstand mechanical stress and maintain its structural integrity even in challenging environments. This durability ensures a reliable and long-lasting electrical connection.
Secure Connection
The single-strand construction of solid copper wire provides a secure and rigid connection. It creates a stable electrical pathway, minimizing the risk of loose or unreliable connections. This makes solid copper wire ideal for applications where a fixed and secure connection is essential, such as in conduit installations.
Read more: What Size Conduit For 6/3 Wire
Compatibility
Solid copper wire is compatible with a variety of termination methods, making it versatile and easy to work with. It can be connected using screws, crimp connectors, or wire nuts, providing flexibility in installations. Additionally, solid copper wire can be used with both copper and aluminum connectors, making it compatible with a wide range of electrical components.
Limitations
While solid copper wire offers numerous advantages, it does have a few limitations. Its lack of flexibility can make it challenging to route through conduit systems with tight bends or corners. Sharp bends should be avoided during installation to prevent damage or deformation of the wire. It is essential to carefully plan and measure the desired path to ensure a smooth and efficient installation.
In summary, solid copper wire is an excellent choice for conduit installations, offering high conductivity, durability, and a secure connection. Its solid construction provides stability and reliability in electrical wiring systems. However, its lack of flexibility should be considered when planning the installation route. By choosing solid copper wire, you can ensure a reliable and efficient electrical connection for your conduit installations.
Stranded Copper Wire
Stranded copper wire is a type of electrical wire composed of multiple smaller strands of copper that are twisted or braided together. It is widely used in various electrical applications, including conduit installations. Stranded copper wire offers unique advantages and is valued for its flexibility, durability, and versatility.
Flexibility
One of the key benefits of stranded copper wire is its flexibility. The multiple strands of wire that make up the cable allow it to bend and twist more easily compared to solid copper wire. This increased flexibility makes stranded copper wire highly versatile and suitable for installations that require extensive wire routing, such as conduit systems with tight bends or corners. The flexibility of stranded copper wire also allows for easy installation in areas with limited space.
Read more: What Size Conduit For A 4-Gauge Wire
Resistance to Breakage
The stranded construction of the wire provides enhanced resistance to breakage. The multiple smaller strands distribute the stress and strain more evenly, reducing the risk of individual strands breaking. This characteristic makes stranded copper wire highly durable and suitable for applications that involve movement or mechanical stress, such as conduit installations that may experience vibration or bending forces.
Ease of Termination
Stranded copper wire is easy to terminate due to its composition. The individual strands can be separated and joined using various termination methods, such as crimping, soldering, or using wire nuts. This flexibility in termination options makes stranded copper wire compatible with a wide range of electrical connectors, providing convenience and ease of installation.
Improved Conductivity
The multiple strands in stranded copper wire increase its surface area, resulting in improved conductivity compared to solid copper wire. This increased contact area allows for better current flow and helps to reduce resistance and voltage drops in electrical systems. The enhanced conductivity of stranded copper wire makes it suitable for applications that require higher current-carrying capacities.
Vibration Resistance
Due to its stranded construction, this type of wire is known for its vibration resistance. The individual strands are able to absorb and dissipate vibrations more effectively, reducing stress on the wire and minimizing the likelihood of failures caused by vibrations. This makes stranded copper wire ideal for applications where vibrations are common, such as in machinery or outdoor installations.
Overall, stranded copper wire offers numerous advantages for conduit installations. Its flexibility, resistance to breakage, ease of termination, improved conductivity, and vibration resistance make it a preferred choice in various electrical applications. It provides a reliable and durable solution for routing and protecting electrical cables and wires within conduit systems.
Read more: What Size Conduit For 12/2 Wire
Aluminum Wire
Aluminum wire is an alternative to copper wire for conduit installations. While less commonly used than copper wire, aluminum wire offers several advantages, including its light weight, cost-effectiveness, and versatility. It is available in both solid and stranded forms, making it suitable for various electrical applications.
Solid Aluminum Wire
Solid aluminum wire is composed of a single, solid strand of aluminum. It is often used for smaller gauge wires in low-voltage applications where weight reduction is a priority. Solid aluminum wire is significantly lighter than copper wire, making it easier to handle and install. This weight advantage can be especially beneficial in large-scale electrical projects where the quantity of wire being used is substantial.
However, solid aluminum wire has a higher resistance compared to copper wire, which can result in increased voltage drops and reduced electrical conductivity. Consequently, solid aluminum wire is typically used in applications that have lower power demands and longer wire runs, as it may not handle high current loads as effectively as copper wire.
Stranded Aluminum Wire
Stranded aluminum wire consists of multiple smaller strands of aluminum wire twisted or braided together. It offers similar advantages to stranded copper wire, such as increased flexibility and improved conductivity. The multiple strands in stranded aluminum wire enhance its ability to carry current and reduce the risk of voltage drops.
Stranded aluminum wire is commonly used for larger gauge wire applications that require both flexibility and higher current-carrying capacity. Its stranded construction allows for easier installation, particularly in conduit systems with bends or corners. Stranded aluminum wire is suitable for a range of applications, including residential, commercial, and industrial installations.
Advantages and Considerations
Aluminum wire offers several advantages over copper wire. It is generally more cost-effective, making it a budget-friendly option for electrical installations. Additionally, aluminum has a superior corrosion resistance, making it suitable for outdoor or high-humidity environments where corrosion is a concern.
However, there are some considerations when using aluminum wire. The differences in conductivity and expansion properties between aluminum and copper can lead to compatibility issues when connecting aluminum wire to copper terminals. To ensure a reliable connection, specialized connectors designed for use with aluminum wire should be used, along with anti-oxidant compounds to prevent corrosion. It is crucial to follow proper installation techniques and consult local electrical codes and regulations when working with aluminum wire.
In summary, aluminum wire offers a lightweight, cost-effective alternative to copper wire for conduit installations. Solid aluminum wire is lighter and suitable for low-power applications, while stranded aluminum wire provides increased flexibility and higher current-carrying capacity. Care must be taken to address compatibility issues with aluminum wire, but when installed correctly and in accordance with local codes, aluminum wire can provide a reliable and efficient electrical connection.
Read more: What Is Blue Conduit Used For
Solid Aluminum Wire
Solid aluminum wire is a type of electrical wire that consists of a single, solid strand of aluminum. It serves as an alternative to solid copper wire and is used in various electrical applications, including conduit installations. Solid aluminum wire offers a unique set of characteristics and benefits.
Lightweight
One of the primary advantages of solid aluminum wire is its light weight. Aluminum is significantly lighter than copper, making it easier to handle, transport, and install. This weight advantage can be particularly beneficial in large-scale electrical projects where the quantity of wire being used is substantial. Additionally, the lightweight nature of solid aluminum wire can help reduce strain on supporting structures and minimize overall installation costs.
Cost-Effective
Another significant advantage of solid aluminum wire is its cost-effectiveness. Aluminum is generally less expensive than copper, making it a budget-friendly option for electrical installations. This cost advantage can be especially beneficial when undertaking projects with long wire runs, where the cost savings of using aluminum wire can add up significantly.
Corrosion Resistance
While aluminum has a lower conductivity compared to copper, it possesses excellent corrosion resistance properties. Aluminum naturally forms a layer of oxide on its surface, which protects it against environmental elements and prevents corrosion. This corrosion resistance makes solid aluminum wire suitable for outdoor or high-humidity environments where moisture and other corrosive substances may be present.
Read more: What Is Red Conduit Used For
Considerations
When utilizing solid aluminum wire, it is important to consider a few factors. Due to aluminum’s lower conductivity compared to copper, solid aluminum wire has a higher resistance, which can lead to increased voltage drops and potential power losses. As a result, solid aluminum wire is generally recommended for low-power applications or applications with longer wire runs.
In addition, when connecting solid aluminum wire to copper terminals, it is crucial to address compatibility issues. The differences in expansion properties between aluminum and copper can lead to loosening or separation of connections over time. Proper installation techniques, along with specialized connectors designed for use with aluminum wire, should be employed to ensure a reliable and secure connection. The use of anti-oxidant compounds can also help prevent corrosion and enhance the longevity of the connection.
Furthermore, it is essential to consult local electrical codes and regulations when working with solid aluminum wire. These guidelines provide specific requirements for the proper installation and usage of aluminum wire to ensure safety and compliance.
In summary, solid aluminum wire offers advantages such as its lightweight nature, cost-effectiveness, and corrosion resistance. While it may have a higher resistance compared to copper, making it more suitable for low-power applications, proper installation techniques and adherence to local electrical codes can ensure a reliable and efficient electrical connection using solid aluminum wire.
Stranded Aluminum Wire
Stranded aluminum wire is a type of electrical wire that consists of multiple smaller strands of aluminum twisted or braided together. It offers a versatile and flexible alternative to solid aluminum wire in conduit installations. Stranded aluminum wire has several advantages and is used in a variety of electrical applications.
Flexibility
One of the key advantages of stranded aluminum wire is its flexibility. The multiple strands of aluminum wire allow for easier bending and maneuvering compared to solid aluminum wire. This flexibility makes stranded aluminum wire suitable for conduit systems with tight bends, corners, or installations that require extensive wire routing. The flexibility of stranded aluminum wire also simplifies installation in areas with limited space.
Conductivity
The stranded construction of the wire provides enhanced conductivity compared to solid aluminum wire. The multiple smaller strands increase the total surface area, allowing for better current flow and reducing the risk of voltage drops. The improved conductivity of stranded aluminum wire makes it suitable for applications that require higher current-carrying capacities.
Read more: What Is A Conduit Body Used For
Strength and Durability
Stranded aluminum wire offers increased strength and durability as compared to solid aluminum wire. The individual strands distribute stress and strain more evenly, reducing the risk of breakage under mechanical stress. This characteristic makes stranded aluminum wire suitable for applications that involve movement or vibration, such as conduit installations exposed to external vibrations or frequent bending.
Read more: What Size Conduit For 6/3 Wire
Compatibility
Stranded aluminum wire is compatible with a wide range of termination methods and electrical connectors. It allows for easier installation and termination due to the flexibility and separability of the individual strands. This compatibility enhances the versatility of stranded aluminum wire and makes it suitable for various electrical applications.
Read more: What Is Red Conduit Used For
Considerations
When working with stranded aluminum wire, it is crucial to follow proper installation techniques and adhere to local electrical codes. The differences in conductivity and expansion properties between aluminum and copper require special considerations when connecting stranded aluminum wire to copper terminals. Specialized connectors designed explicitly for use with stranded aluminum wire should be employed, along with anti-oxidant compounds to prevent corrosion and maintain a reliable connection. Consulting with a professional electrician can provide guidance on the proper installation practices and ensure compliance with electrical codes.
In summary, stranded aluminum wire offers flexibility, improved conductivity, strength, and compatibility, making it a versatile option for conduit installations. Its flexibility allows for easy routing in tight spaces or around bends, while its conductivity and strength make it suitable for various electrical applications. By following proper installation practices and code compliance, stranded aluminum wire can provide a reliable and efficient electrical connection for your conduit installations.
Other Considerations for Wire Selection in Conduit
When selecting wire for conduit installations, there are additional factors to consider beyond the type and material of the wire. These considerations can impact the safety, efficiency, and overall performance of the electrical system. Here are some key factors to keep in mind:
Read more: What Size Conduit For 10/2 Wire
Wire Insulation
The type and quality of wire insulation are crucial in ensuring the safety and protection of the wire within the conduit. Different insulation materials offer varying levels of resistance to temperature, moisture, chemicals, and abrasion. It is important to choose wire with insulation appropriate for the specific installation environment and requirements to prevent damage or degradation of the wire over time.
Wire Ampacity
The ampacity, or current-carrying capacity, of the wire is a critical consideration. It is necessary to select wire that can handle the expected electrical load without exceeding its maximum ampacity. Oversized wires can be costlier and more challenging to install, while undersized wires can lead to voltage drop, overheating, and potential hazards. Consult the National Electrical Code (NEC) or a qualified electrician to determine the appropriate wire size for your specific application.
Voltage Drop
Voltage drop occurs when the voltage decreases due to the resistance of the wire. It is important to minimize voltage drop to ensure the proper functioning of electrical devices and equipment. Longer wire runs and higher current loads can result in more significant voltage drops. Carefully consider the wire size, conductor material, and specific installation requirements to mitigate voltage drop and maintain electrical efficiency.
Environmental Conditions
The environmental conditions in which the wire will be installed can significantly impact its performance and longevity. Factors such as extreme temperatures, moisture, humidity, chemicals, and exposure to UV rays should be considered. Some wire types, such as those with special insulation or coatings, are better suited for harsh or specific environmental conditions. Choose wire that is designed to withstand the anticipated environmental factors to ensure its durability and reliability.
Code Compliance
It is essential to adhere to local electrical codes and regulations when selecting wire for conduit installations. These codes ensure the safety and standardization of electrical systems. Compliance with electrical codes may include considerations such as wire type, ampacity, insulation rating, grounding requirements, and proper installation methods. Failure to comply with electrical codes can result in safety hazards, failed inspections, and potential legal consequences. Always consult the NEC or a licensed electrician to ensure you meet the necessary requirements.
By considering these other factors alongside wire type and material, you can make informed decisions and select the most suitable wire for your conduit installations. Taking these considerations into account will help ensure the safety, efficiency, and compliance of your electrical system, providing you with peace of mind and reliable performance.
Conclusion
Choosing the right wire for conduit is crucial for a safe, efficient, and reliable electrical installation. The selection of wire involves considering factors such as conductor material, wire size, insulation type, conduit size, environmental conditions, and compliance with electrical codes. The two primary types of wire suitable for conduit installations are copper wire and aluminum wire.
Copper wire, available in solid and stranded forms, is widely used and valued for its excellent conductivity, durability, and corrosion resistance. Solid copper wire offers a secure and rigid connection, making it suitable for applications that require stability. On the other hand, stranded copper wire provides increased flexibility, making it easier to route through conduit systems with bends or corners.
Aluminum wire, available in solid and stranded forms as well, offers advantages including its lighter weight, cost-effectiveness, and corrosion resistance. Solid aluminum wire is lighter and suitable for low-power applications, while stranded aluminum wire provides flexibility and higher current-carrying capacity.
Other important considerations when selecting wire for conduit installations include factors such as wire insulation, ampacity, voltage drop, environmental conditions, and compliance with electrical codes. Ensuring proper insulation, ampacity matching, and minimizing voltage drop are critical for optimal electrical performance. Additionally, considering the environmental conditions and complying with electrical codes ensure safety and longevity.
Ultimately, making informed decisions based on these considerations will lead to a reliable and efficient electrical system. Consultation with a licensed electrician or referencing the National Electrical Code (NEC) can provide valuable guidance and ensure compliance with local regulations.
In conclusion, the selection of wire for conduit is a critical aspect of any electrical installation. By understanding the different types of wire available and considering factors such as conductor material, wire size, insulation, environmental conditions, and code compliance, you can make the best choice for your specific application. Whether it is copper wire or aluminum wire, ensuring a safe and efficient electrical system will provide peace of mind and reliable performance for years to come.
Frequently Asked Questions about What Type Of Wire Should Be Used In Conduit
Was this page helpful?
At Storables.com, we guarantee accurate and reliable information. Our content, validated by Expert Board Contributors, is crafted following stringent Editorial Policies. We're committed to providing you with well-researched, expert-backed insights for all your informational needs.
0 thoughts on “What Type Of Wire Should Be Used In Conduit”