Home>Articles>Why Did My Ryobi Pressure Washer Stopped Working
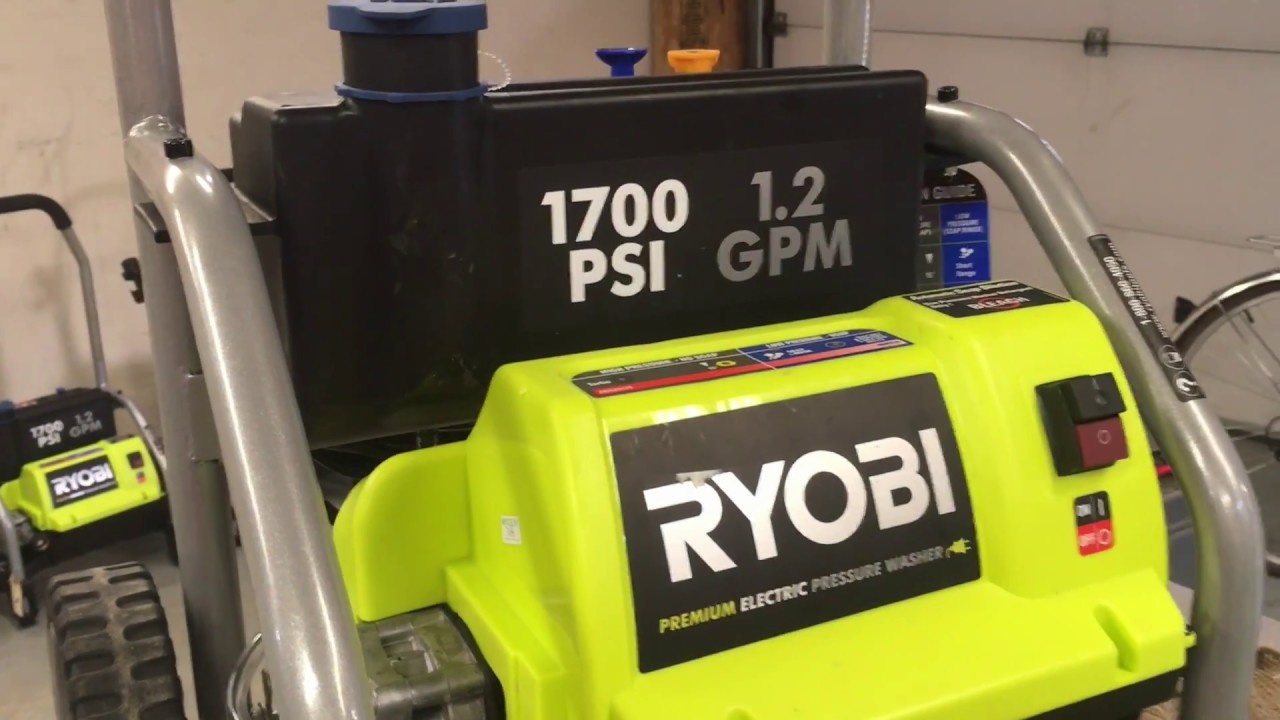
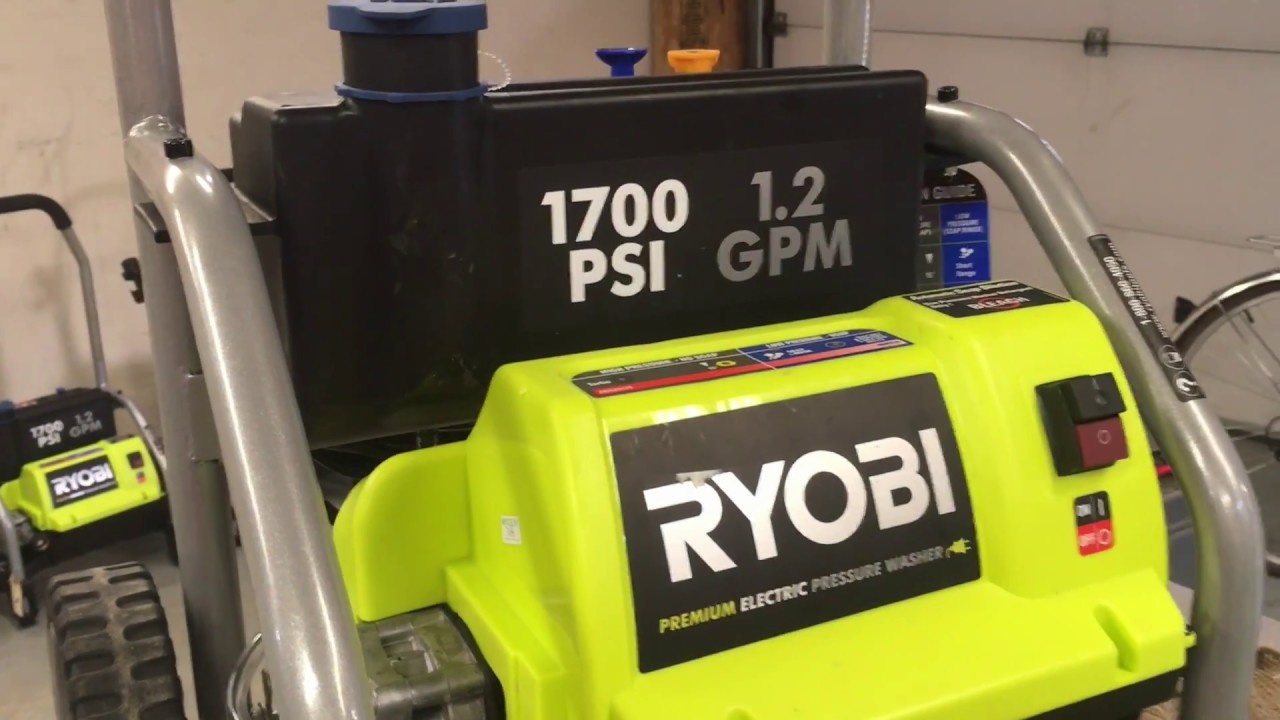
Articles
Why Did My Ryobi Pressure Washer Stopped Working
Modified: February 28, 2024
Explore our informative articles on why your Ryobi pressure washer may have suddenly stopped working. Find troubleshooting tips and solutions to get it back up and running efficiently.
(Many of the links in this article redirect to a specific reviewed product. Your purchase of these products through affiliate links helps to generate commission for Storables.com, at no extra cost. Learn more)
Introduction
Pressure washers are powerful tools used for cleaning a variety of surfaces, from driveways and decks to vehicles and outdoor furniture. They make the task of removing dirt, grime, and stains much easier and more efficient. However, if your Ryobi pressure washer suddenly stops working, it can be frustrating and leave you wondering what went wrong.
There could be several reasons why your Ryobi pressure washer stopped working. In this article, we will explore the common causes for this issue and provide troubleshooting steps to help you fix the problem.
Before we dive into the possible causes, it’s important to note that Ryobi pressure washers are known for their durability and reliability. However, like any mechanical device, they can experience malfunctions or breakdowns due to various factors. By understanding these potential issues and performing the necessary troubleshooting steps, you can get your Ryobi pressure washer up and running again in no time.
Key Takeaways:
- Keep your Ryobi pressure washer running smoothly by checking power supply, cleaning the nozzle, ensuring proper water supply, and addressing pump, trigger gun, wand, and motor issues through regular maintenance and troubleshooting.
- If your Ryobi pressure washer stops working, follow the troubleshooting steps to identify and resolve common issues such as power supply problems, nozzle blockages, water supply issues, pump failures, trigger gun or wand problems, and motor malfunctions. Regular maintenance is key to preventing issues and ensuring optimal performance.
Read more: Why Did My Blender Stop Working
Common Causes for Ryobi Pressure Washers to Stop Working
When your Ryobi pressure washer stops working, it can be frustrating, but with a little troubleshooting, you can often identify and resolve the issue. Here are some common causes for Ryobi pressure washers to stop working:
- Power Supply Issues: One of the first things to check when your pressure washer is not working is the power supply. Make sure the power cord is securely plugged into a functioning outlet and that the circuit breaker or fuse has not tripped. If the power supply is not the issue, move on to the next potential cause.
- Blocked or Clogged Nozzle: A clogged nozzle can cause a loss of pressure or complete loss of water flow. Inspect the nozzle for any debris or blockages and clean it thoroughly. If the nozzle is damaged or worn out, it may need to be replaced.
- Water Supply Problems: Insufficient water supply can also cause a pressure washer to stop working. Ensure that the water source is turned on and supplying enough water to the unit. Check for any kinks or blockages in the hose that may be restricting water flow. Additionally, make sure the water inlet filter is clean and not clogged.
- Pump Failure: The pump is a vital component of a pressure washer, and if it fails, the machine will not work properly. If you suspect pump failure, check for any leaks or unusual noises coming from the pump. The pump may need to be repaired or replaced by a professional.
- Trigger Gun or Wand Issues: Faulty trigger guns or wands can prevent a pressure washer from working correctly. Inspect the trigger gun and wand for any damage or leaks. If necessary, replace these components to restore the proper function of the pressure washer.
- Unresponsive Motor: If your pressure washer’s motor is not running, it could be due to various issues. Check the power supply to ensure it is reaching the motor. If the motor is receiving power but still not working, it may be a sign of motor failure and require repair or replacement.
Identifying the cause of your Ryobi pressure washer not working is the first step in troubleshooting and resolving the issue. By narrowing down the possibilities, you can focus your efforts on the specific area that needs attention. In the next section, we will discuss the steps you can take to fix a stopped Ryobi pressure washer.
Power Supply Issues
One of the most common causes for a Ryobi pressure washer to stop working is power supply issues. Before assuming there’s a major problem with your pressure washer, it’s crucial to ensure that it’s receiving adequate power. Here are a few steps to troubleshoot power supply issues:
- Check the Power Cord: Ensure that the power cord is securely plugged into a functioning electrical outlet. Sometimes, the connection may become loose or disconnected, resulting in a loss of power. Wiggle the power cord gently to see if it’s properly connected.
- Inspect the Circuit Breaker or Fuse: If the power cord is properly connected, check the circuit breaker or fuse that controls the outlet. It’s possible that it may have tripped or blown, cutting off power to the pressure washer. Reset the circuit breaker or replace the fuse if necessary.
- Try a Different Outlet: If the circuit breaker or fuse seems to be working fine, try plugging the pressure washer into a different outlet. There’s a possibility that the original outlet may be faulty and not providing proper power supply.
- Consider the Extension Cord Length: If you’re using an extension cord to power your pressure washer, make sure it’s the appropriate length and gauge size. Using an extension cord that’s too long or too thin can cause a voltage drop, leading to power issues. Refer to the manufacturer’s guidelines for the recommended cord length and gauge for your specific pressure washer model.
- Check for Disconnected Wires: It’s possible that there may be a loose or disconnected wire within the pressure washer’s electrical system. Inspect the wiring connections, particularly around the power switch and motor, and ensure that all wires are securely connected. If you notice any loose or disconnected wires, consult a professional for repair or consider contacting Ryobi customer service for assistance.
By following these steps, you can determine if power supply issues are the cause of your Ryobi pressure washer not working. If you’ve ruled out power supply problems and your pressure washer still isn’t functioning correctly, it’s time to move on to the next potential cause: blocked or clogged nozzle.
Blocked or Clogged Nozzle
Another common cause for a Ryobi pressure washer to stop working is a blocked or clogged nozzle. Over time, debris, dirt, and mineral deposits can accumulate in the nozzle, obstructing the water flow and reducing the pressure. Here are a few steps to troubleshoot and clean a blocked or clogged nozzle:
- Turn Off the Pressure Washer: Before inspecting or cleaning the nozzle, always ensure that the pressure washer is turned off and the trigger gun is in the locked position. This is to prevent any accidental spraying or injuries.
- Remove the Nozzle: Depending on your Ryobi pressure washer model, the nozzle may screw off or require a quick-release mechanism. Carefully remove the nozzle from the end of the wand or lance by twisting or releasing it.
- Inspect the Nozzle: Examine the nozzle for any visible blockages or debris. You can use a flashlight or magnifying glass if necessary.
- Clean the Nozzle: If there are any blockages or debris in the nozzle, use a fine needle or a nozzle cleaning tool to carefully remove the obstructions. Be gentle to avoid damaging the nozzle. Alternatively, you can soak the nozzle in a solution of warm water and vinegar to dissolve mineral deposits.
- Rinse and Reattach the Nozzle: Once the nozzle is cleaned, rinse it thoroughly with water to remove any remaining debris or cleaning solution. Then, reattach the nozzle to the wand or lance and ensure it is securely in place.
- Test the Pressure Washer: Turn on the pressure washer and squeeze the trigger to check if the nozzle is now providing the proper water flow and pressure. If you notice an improvement, the blocked or clogged nozzle was likely the cause of the issue.
Regularly inspecting and cleaning the nozzle can help maintain the efficiency and performance of your Ryobi pressure washer. By ensuring that the nozzle is clear of any obstructions, you can prevent potential issues and keep your pressure washer running smoothly.
If cleaning the nozzle doesn’t resolve the problem and your Ryobi pressure washer continues to have issues, it’s time to move on to the next potential cause: water supply problems.
Water Supply Problems
Water supply problems can also cause a Ryobi pressure washer to stop working. Insufficient water flow or pressure can affect the performance of the pressure washer and result in issues. Here are some steps to troubleshoot and address water supply problems:
- Check the Water Source: Ensure that the water source, such as a faucet or hose, is turned on and providing an adequate water supply. It’s possible that the water supply may have been inadvertently shut off or restricted.
- Inspect the Hose: Examine the hose for any kinks, bends, or obstructions that may be restricting water flow. Straighten out any kinks and ensure that the hose is not being compressed or squeezed by heavy objects.
- Clear Hose Blockages: If there are any blockages or debris in the hose, remove the hose from the pressure washer and flush it out with water. You can also use a high-pressure stream of water or a long, flexible brush to manually clear any obstructions.
- Check the Water Inlet Filter: Most pressure washers, including Ryobi models, are equipped with a water inlet filter to capture dirt and debris from entering the unit. Check the filter for any clogs or blockages and clean it if necessary. Refer to the user manual for instructions on how to remove and clean the water inlet filter.
- Ensure Proper Hose Diameter: Using a hose with a diameter smaller than recommended by the manufacturer can restrict water flow and affect the pressure washer’s performance. Make sure that you are using a hose with the appropriate diameter for your Ryobi pressure washer model.
- Consider Water Source Distance: If you’re using a long water hose or drawing water from a distant source, it may result in decreased water pressure. To resolve this issue, try reducing the distance between the water source and the pressure washer or use a larger diameter hose to allow for better water flow.
By troubleshooting and addressing water supply problems, you can ensure that your Ryobi pressure washer is receiving an adequate water flow and pressure to function properly. Once you have ruled out water supply issues, it’s time to move on to the next potential cause: pump failure.
Read more: Why Did My Electric Toothbrush Stop Working
Pump Failure
A pump failure is a more critical issue that can cause a Ryobi pressure washer to stop working. The pump is responsible for pressurizing the water and delivering it through the nozzle at high pressure. Here are some signs of pump failure and steps to troubleshoot this issue:
Signs of Pump Failure:
- Loss of pressure or low water flow
- Unusual noises coming from the pump
- Leaking water or oil from the pump
- Inconsistent or intermittent pressure
Troubleshooting Steps:
- Inspect for Leaks: Check the pump for any visible leaks or signs of oil or water leakage. Leaks may indicate a damaged seal or gasket, which can lead to pump failure. If leaks are detected, the pump may need to be repaired or replaced by a professional.
- Check for Unusual Noises: Pay attention to any unusual noises coming from the pump, such as grinding, rattling, or squealing sounds. These noises can indicate a problem with the pump’s internal components. In such cases, it’s best to contact a professional for repair or replacement.
- Inspect the Pump Inlet: The pump’s inlet, where the water enters the pump, can sometimes become clogged with debris. Remove the water inlet hose and inspect the filter screen or valve for any blockages. Clean or replace the filter screen as needed.
- Test Pump Performance: Run the pressure washer and observe the performance of the pump. If the pressure is inconsistent or significantly reduced, it may be a sign of pump failure. In such cases, it is recommended to consult a professional or contact Ryobi customer service to arrange for repair or replacement.
- Follow Maintenance Schedule: Regular maintenance, such as changing the oil, inspecting seals, and keeping the pump clean, can help prevent pump failure. Refer to the user manual for the recommended maintenance schedule and procedures for your Ryobi pressure washer model.
Pump failure is a more complex issue that may require professional assistance. If troubleshooting steps do not resolve the problem, it is advisable to seek help from a qualified technician or contact Ryobi customer service for further guidance.
Next, we’ll explore another potential cause for a stopped Ryobi pressure washer: trigger gun or wand issues.
Trigger Gun or Wand Issues
Issues with the trigger gun or wand can also cause a Ryobi pressure washer to stop working properly. The trigger gun is responsible for controlling the water flow, while the wand directs the water stream. Here are some common trigger gun and wand issues and steps to troubleshoot them:
Common Trigger Gun and Wand Issues:
- Leaking or dripping trigger gun
- Blocked or clogged wand nozzle
- Trigger gun not engaging or releasing properly
- Damage or wear on trigger gun or wand components
Troubleshooting Steps:
- Inspect for Leaks: Check the trigger gun for any leaks or drips. Inspect the O-rings, seals, and connections for any damage or wear. If there are any visible issues, replace the faulty parts or consider replacing the trigger gun altogether.
- Clear Wand Nozzle Blockages: If the water flow from the wand nozzle is weak or inconsistent, there may be a blockage. Remove the nozzle from the wand and clean it thoroughly, ensuring that no debris or obstructions are present. If the nozzle is damaged or worn out, replace it with a new one.
- Check Trigger Gun Operation: Test the trigger gun to ensure it engages and releases properly. If you are experiencing difficulties with the trigger gun, it may need to be repaired or replaced.
- Inspect Components: Examine the trigger gun and wand for any signs of damage, such as cracks or fractures. If there are any visible issues, it is recommended to replace the damaged components to maintain the proper functioning of the pressure washer.
- Follow Proper Maintenance: Regularly inspect and clean the trigger gun and wand, especially after each use. Lubricate any moving parts and ensure proper storage to prevent damage or wear over time.
By troubleshooting trigger gun and wand issues, you can ensure that they are functioning correctly and allowing for proper water flow and control. If you have followed these steps and are still experiencing difficulties with the trigger gun or wand, it may be necessary to seek professional assistance or contact Ryobi customer service for further guidance.
Now, let’s proceed to the final potential cause for a stopped Ryobi pressure washer: motor issues.
Unresponsive Motor
If your Ryobi pressure washer’s motor is unresponsive, it can prevent the machine from working altogether. The motor is responsible for powering and driving the pump, generating the necessary pressure for the water flow. Here are some troubleshooting steps to address motor-related issues:
Signs of Motor Issues:
- The motor does not start or turn on
- The motor runs but does not produce enough power
- Unusual noises or vibrations coming from the motor
- The motor gets excessively hot
Troubleshooting Steps:
- Check the Power Supply: Ensure that the power cord is properly connected and that the outlet is functioning correctly. Test the outlet with another device to confirm that it is providing power. If the power supply is not the issue, move to the next step.
- Inspect for Tripped Safety Features: Some pressure washers have built-in safety features, such as thermal overload protection or low oil shutdown. Check for any tripped safety switches or indicators and follow the instructions in the user manual to reset them.
- Check Oil Level: Verify that the motor has sufficient oil. Low oil levels can cause the motor to malfunction or shut down. Refer to the user manual for instructions on checking and adding oil to the motor.
- Inspect Motor Components: Examine the motor for any visible damage, loose connections, or worn-out parts. Ensure all connections are secure and tighten any loose components. If you notice any significant damage or wear, it may be necessary to consult a professional for repair or replacement.
- Test Motor Capacitor: A faulty motor capacitor can prevent the motor from starting or operating at full power. Consult the user manual or contact Ryobi customer service for guidance on how to test and replace the capacitor if needed.
- Seek Professional Help: If the motor continues to be unresponsive after performing these troubleshooting steps, it is recommended to seek professional assistance. A certified technician can diagnose and repair more complex motor issues.
The motor is a critical component of the pressure washer, and diagnosing and fixing motor-related problems may require specialized knowledge and expertise. If you are unsure or uncomfortable performing the troubleshooting steps, it’s best to consult a professional or contact Ryobi customer service for assistance.
Now that we have covered the common causes for a Ryobi pressure washer to stop working, let’s summarize the troubleshooting steps in the next section.
Check the water supply and make sure it’s turned on and flowing properly. Also, check the power source and make sure it’s connected and working. If these are both okay, it may be a problem with the pump or motor that needs professional attention.
Troubleshooting Steps to Fix a Stopped Ryobi Pressure Washer
If your Ryobi pressure washer has stopped working, it can be frustrating, but don’t worry. By following these troubleshooting steps, you can identify and resolve the issue. Here are the steps to fix a stopped Ryobi pressure washer:
- Check Power Supply and Connections: Ensure the power cord is securely plugged into a functioning outlet. Check the circuit breaker or fuse to make sure it hasn’t tripped. Consider using the appropriate extension cord if needed.
- Inspect and Clean the Nozzle: Remove the nozzle and inspect it for any blockages or debris. Clean the nozzle thoroughly using a fine needle or nozzle cleaning tool.
- Ensure Proper Water Supply: Confirm that the water source is turned on and providing sufficient water flow. Check the hose for any kinks, blockages, or leaks. Clean the water inlet filter as necessary.
- Test and Repair the Pump: Check for any leaks, unusual noises, or visible damage on the pump. Inspect the pump inlet for blockages. If necessary, consult a professional for pump repair or replacement.
- Examine and Fix Trigger Gun or Wand Issues: Inspect the trigger gun for leaks and ensure it engages and releases properly. Clean the wand nozzle and replace it if damaged. Replace any damaged trigger gun or wand components.
- Troubleshoot and Repair Motor Issues: Ensure the power supply is reaching the motor. Check for tripped safety features, verify the oil level, and inspect motor components for damage. Test and replace the motor capacitor if necessary. Seek professional help if the motor remains unresponsive.
By following these troubleshooting steps, you can often identify and fix the issues causing your Ryobi pressure washer to stop working. However, if you’re unable to resolve the problem or if you are uncomfortable performing the troubleshooting steps yourself, it is always recommended to seek professional assistance or contact Ryobi customer service for further guidance.
Remember to refer to your Ryobi pressure washer’s user manual for model-specific instructions and recommendations. Regular maintenance and care can also help prevent issues and keep your pressure washer operating smoothly for years to come.
Hopefully, with the help of this guide, you will be able to get your Ryobi pressure washer back in working condition and ready to tackle your next cleaning project!
Happy pressure washing!
Read more: Why Did My Kitchenaid Mixer Stop Working
Check Power Supply and Connections
When your Ryobi pressure washer stops working, the first step in troubleshooting is to check the power supply and connections. Power supply issues can often be the cause of the problem. Here are the steps to check the power supply and connections:
- Inspect the Power Cord: Start by examining the power cord of your Ryobi pressure washer. Ensure that it is securely plugged into a functioning electrical outlet. Sometimes, the connection between the power cord and the outlet may become loose, resulting in a loss of power. Gently wiggle the power cord to check for a secure connection.
- Check the Circuit Breaker or Fuse: If the power cord is properly connected, the next step is to check the circuit breaker or fuse that controls the outlet. It is possible that the circuit breaker may have tripped or the fuse may have blown, cutting off the power supply to the pressure washer. Locate the circuit breaker panel or fuse box and inspect it. If you find a tripped circuit breaker, simply reset it. If you find a blown fuse, replace it with a new one of the same rating.
- Try a Different Outlet: If you have confirmed that the power cord and the circuit breaker/fuse are not the issue, try plugging your pressure washer into a different electrical outlet. Sometimes, the original outlet may have an underlying problem, such as a wiring issue or a faulty connection, which is causing the power failure. By trying a different outlet, you can determine if the issue is specific to the original outlet or if it persists regardless of the outlet used.
- Consider Using an Extension Cord: If you are using an extension cord to power your Ryobi pressure washer, make sure it is the appropriate length and gauge size. Using an extension cord that is too long or has a lower gauge rating than recommended can result in a voltage drop, leading to insufficient power supply to the pressure washer. Refer to the user manual or manufacturer’s guidelines to determine the correct extension cord specifications for your particular pressure washer model.
- Inspect for Disconnected or Damaged Wires: In some cases, a power supply issue may be caused by a loose or disconnected wire within the pressure washer’s electrical system. Inspect the power supply connections, including the power switch and motor connections, to ensure all wires are securely connected. If you notice any loose or disconnected wires, consult a professional for repair or contact Ryobi customer service for assistance.
By following these steps to check the power supply and connections of your Ryobi pressure washer, you can identify and resolve power-related issues. If, after checking the power supply, your pressure washer continues to have problems, it’s time to move on to the next troubleshooting step to further diagnose the issue.
Inspect and Clean the Nozzle
When your Ryobi pressure washer stops working, a clogged or blocked nozzle could be the culprit. Over time, dirt, debris, and mineral deposits can accumulate in the nozzle, obstructing the water flow and reducing the pressure. To address this issue, follow these steps to inspect and clean the nozzle:
- Turn Off the Pressure Washer: Before inspecting or cleaning the nozzle, always ensure that the pressure washer is turned off and the trigger gun is in the locked position. This step will prevent any accidental spraying and keep you safe during the cleaning process.
- Remove the Nozzle: Depending on your Ryobi pressure washer model, the nozzle can either screw off or require a quick-release mechanism. Carefully remove the nozzle from the end of the wand or lance by twisting it counterclockwise or releasing the latch, following the manufacturer’s instructions.
- Inspect the Nozzle: Once the nozzle is removed, inspect it for any visible blockages or debris. Examine the nozzle openings and the inside for any signs of clogs or obstructions. Often, you can visually identify dirt or debris buildup that is hindering the water flow.
- Clean the Nozzle: If you find any blockages or debris in the nozzle, it’s time to clean it. Begin by using a fine needle or pin to gently dislodge any stubborn particles or deposits from the nozzle openings. Be careful not to damage the nozzle while doing this. Alternatively, you can soak the nozzle in a solution of warm water and mild detergent to dissolve any dirt or mineral buildup. Use a small brush or toothbrush to scrub away stubborn deposits. Rinse the nozzle thoroughly with clean water.
- Inspect the Wand or Lance: While the nozzle is removed, take the opportunity to inspect the wand or lance for any blockages or debris. Check the inside of the wand or lance for any clogs and clean them out if necessary.
- Reattach the Nozzle: After cleaning, make sure the nozzle is completely dry before reattaching it to the end of the wand or lance. Align the nozzle and twist it clockwise or secure it according to the manufacturer’s instructions.
- Test the Pressure Washer: With the nozzle securely attached, turn on the pressure washer and squeeze the trigger to test the water flow and pressure. If the water flow is improved, and the pressure washer is working properly again, the clogged or blocked nozzle was the likely cause of the issue.
Regularly inspecting and cleaning the nozzle is essential to maintain optimal performance and prevent clogs that can hinder your Ryobi pressure washer. By following these steps, you can effectively clean the nozzle and restore proper water flow and pressure. If the issue persists after cleaning the nozzle, move on to the next troubleshooting step to further diagnose the problem.
Ensure Proper Water Supply
Adequate water supply is essential for the proper functioning of your Ryobi pressure washer. If your pressure washer is not receiving sufficient water flow, it may fail to operate correctly. Follow these steps to ensure a proper water supply:
- Check the Water Source: Begin by ensuring that the water source, such as a faucet or hose, is turned on and supplying water. Sometimes, the water supply may have been inadvertently shut off or restricted, so it’s important to verify that it’s open and flowing.
- Inspect the Hose: Examine the hose connected to your pressure washer for any kinks, bends, or obstructions that may be restricting water flow. Straighten out any kinks or twists in the hose, ensuring that it’s not being compressed or squeezed by heavy objects or furniture.
- Clear Hose Blockages: If you notice any blockages or debris in the hose, remove it from the pressure washer and flush it out with clean water. You can use a high-pressure stream of water or a long, flexible brush to manually clear any obstructions within the hose.
- Check the Water Inlet Filter: Many pressure washers, including Ryobi models, are equipped with a water inlet filter. This filter captures dirt, debris, and other contaminants from entering the pressure washer and causing damage. Locate the water inlet filter, usually near the water inlet connection, and inspect it for any clogs or blockages. If necessary, carefully remove the filter and clean it under running water. Make sure the filter is thoroughly dry before reattaching it to the pressure washer.
- Ensure Proper Hose Diameter: Using a hose with an incorrect diameter can result in insufficient water flow to the pressure washer. Check the manufacturer’s recommendations for the appropriate hose diameter for your Ryobi pressure washer model. Using the correct hose diameter will ensure optimal water flow and pressure.
- Consider Water Source Distance: If you’re drawing water from a distant source or using a long hose, it can affect the water pressure reaching your pressure washer. Consider reducing the distance between the water source and the pressure washer, if possible. Alternatively, a larger diameter hose may be required to compensate for the increased distance and maintain adequate water flow.
By following these steps to ensure a proper water supply, you can eliminate any issues related to insufficient water flow to your Ryobi pressure washer. Adequate water supply is crucial for the optimal performance of the pressure washer, as it directly impacts the water pressure and cleaning effectiveness. If the problem persists after addressing the water supply, proceed to the next step of troubleshooting to identify and resolve any potential issues.
Test and Repair the Pump
If your Ryobi pressure washer is not working, a potential cause could be a malfunctioning pump. The pump is responsible for pressurizing the water and delivering it through the nozzle at high pressure. Follow these steps to test and repair the pump:
- Inspect the Pump: Start by visually inspecting the pump for any visible issues. Look for leaks, cracks, or unusual noises coming from the pump. If you notice any signs of damage or wear, it may indicate a problem with the pump that needs to be addressed.
- Check the Pump Inlet: The pump inlet, where the water enters the pump, can sometimes become clogged with debris. Start by removing the water inlet hose and inspecting the filter screen or valve for any blockages. Clean the filter screen or valve by rinsing it with clean water or using a soft brush to remove any debris.
- Test the Pump: With the water inlet hose and the filter screen or valve reattached, turn on the pressure washer and squeeze the trigger on the spray wand to activate the pump. Listen for any unusual noises or vibrations coming from the pump. If the pump is not working or is not generating sufficient pressure, it may require repair or replacement.
- Check for Pump Leaks: Look for any signs of water or oil leakage from the pump. Leaks may indicate a damaged seal or gasket, which can impact the pump’s performance. If you detect leaks, it’s best to contact a professional or Ryobi customer service for assistance with repairing or replacing the pump.
- Consult a Professional: If you’re unable to identify or resolve the issue on your own, it’s recommended to consult a professional technician or contact Ryobi customer service. They will have the expertise to diagnose and repair more complex pump problems.
- Follow Maintenance Guidelines: Regular maintenance is crucial for the longevity and performance of your pressure washer’s pump. Follow the maintenance guidelines outlined in the user manual, including changing the pump oil, inspecting seals and valves, and keeping the pump clean.
By following these steps, you can test and repair the pump of your Ryobi pressure washer. However, if you are uncertain about performing these steps or if the pump issues persist, it’s recommended to seek professional assistance. A qualified technician can accurately diagnose the problem and provide the necessary repairs or guidance on replacement options.
Proper maintenance and care will help extend the life of your pressure washer’s pump, ensuring its optimal performance for years to come.
Read more: Why Did My Air Fryer Stop Working
Examine and Fix Trigger Gun or Wand Problems
If your Ryobi pressure washer is not working properly, issues with the trigger gun or wand could be the cause. The trigger gun controls the water flow, and the wand directs the water stream. Follow these steps to examine and fix trigger gun or wand problems:
- Inspect for Leaks: Check the trigger gun for any signs of leaks or dripping. Inspect the connections, O-rings, and seals for any damage or wear and replace them if necessary. Properly seated and functioning seals are essential for a leak-free operation.
- Ensure Proper Trigger Gun Operation: Test the trigger gun by squeezing and releasing the trigger. The trigger should engage smoothly and release without any sticking or hesitation. If the trigger is not engaging or releasing properly, it may require adjustment or replacement. Consult the user manual or contact Ryobi customer service for guidance on how to address trigger gun issues.
- Inspect the Wand Nozzle: Examine the nozzle at the end of the wand for any blockages or debris. A clogged nozzle can lead to reduced water flow or inconsistent spray patterns. Remove the nozzle and clean it thoroughly using a fine needle or nozzle cleaning tool. If the nozzle is damaged or worn out, replace it with a new one.
- Check for Damage or Wear: Inspect the trigger gun and wand for any visible damage, such as cracks or fractures. Similarly, check the wand for any signs of wear, such as bent or damaged sections. If you notice any significant damage or wear, it may be necessary to replace the affected parts to ensure proper functioning.
- Follow Proper Maintenance: Regularly clean and lubricate the trigger gun and wand to keep them in good working condition. After each use, rinse them with clean water and remove any debris or dirt. Lubricate any moving parts according to the manufacturer’s instructions to prevent stiffness or corrosion.
- Replace Faulty Components: If you’ve identified specific issues with the trigger gun or wand that cannot be repaired, it may be necessary to replace the faulty components. Consult the user manual or contact Ryobi customer service to find replacement parts that are compatible with your specific pressure washer model.
By examining and addressing trigger gun or wand problems, you can restore proper water control and spray functionality to your Ryobi pressure washer. Regular inspection, maintenance, and timely replacement of worn or damaged components are key to ensuring the long-term performance of these parts.
If you have followed these steps and are still experiencing difficulties with the trigger gun or wand, it may be best to seek professional assistance or contact Ryobi customer service for further guidance.
Troubleshoot and Repair Motor Issues
If your Ryobi pressure washer’s motor is not functioning properly, it can prevent the machine from working effectively. The motor is responsible for powering the pump and generating the necessary pressure for water flow. Follow these steps to troubleshoot and repair motor issues:
- Check the Power Supply: Ensure that the power supply is reaching the motor. Make sure the power cord is properly connected and that the outlet is providing power. If there is a power switch on the pressure washer, ensure it is in the “on” position.
- Inspect for Tripped Safety Features: Some pressure washers have built-in safety features such as thermal overload protection or low oil shutdown. Check if any safety switches or indicators have tripped. Follow the instructions in the user manual to reset them if necessary.
- Check the Oil Level: Verify that the motor has sufficient oil. Low oil levels can lead to motor malfunctions or shutdowns. Refer to the user manual for instructions on checking and adding oil to the motor. Use the recommended type and amount of oil.
- Inspect Motor Components: Examine the motor for any visible damage, loose connections, or worn-out parts. Ensure all connections are secure and tighten any loose components. If you notice significant damage or wear, it may be necessary to consult a professional for repair or consider contacting Ryobi customer service for further assistance.
- Test the Motor Capacitor: The motor capacitor is essential for starting and running the motor. A faulty capacitor can prevent the motor from starting or operating at full power. If you suspect an issue with the capacitor, consult the user manual or contact Ryobi customer service for guidance on how to test and replace it if necessary.
- Consider Professional Assistance: If you have followed these steps and are still experiencing motor issues, it may be best to seek professional assistance. A professional technician will have the expertise and tools to diagnose and repair more complex motor problems.
Regular maintenance, including checking the power supply, oil levels, and motor components, can prevent motor issues and prolong the life of your Ryobi pressure washer. Following the manufacturer’s recommendations for maintenance and care is key.
If you are unfamiliar or uncomfortable with troubleshooting or repairing the motor yourself, it is recommended to consult a professional technician or contact Ryobi customer service for guidance and support.
Remember, safety is of utmost importance when working with electrical components. Always ensure the pressure washer is turned off and unplugged before inspecting or repairing the motor.
By following these steps, you can identify and address motor issues to get your Ryobi pressure washer running smoothly again.
Conclusion
When your Ryobi pressure washer stops working, it can be frustrating and inconvenient. However, by understanding the common causes and following the troubleshooting steps outlined in this article, you can identify and resolve the issue. From power supply problems to nozzle blockages, water supply issues, pump failures, trigger gun or wand problems, and motor malfunctions, each potential cause has been addressed with helpful guidance for diagnosis and repair.
Remember, it’s essential to follow the manufacturer’s guidelines outlined in the user manual specific to your Ryobi pressure washer model. Regular maintenance, including proper cleaning, lubrication, and replacement of worn parts, can prevent issues and extend the life of your pressure washer.
If you have exhausted all troubleshooting steps and are still unable to resolve the problem, it may be best to seek professional assistance. Qualified technicians and Ryobi customer service can provide expertise to diagnose, repair, or provide additional guidance tailored to your specific situation.
By being proactive and addressing issues promptly, you can ensure that your Ryobi pressure washer remains in optimal working condition, providing you with reliable performance and efficient cleaning for years to come.
Thank you for reading this comprehensive troubleshooting guide for resolving issues with your Ryobi pressure washer. We hope this article has been helpful in assisting you with getting your pressure washer back up and running smoothly. Happy cleaning!
Frequently Asked Questions about Why Did My Ryobi Pressure Washer Stopped Working
Was this page helpful?
At Storables.com, we guarantee accurate and reliable information. Our content, validated by Expert Board Contributors, is crafted following stringent Editorial Policies. We're committed to providing you with well-researched, expert-backed insights for all your informational needs.
0 thoughts on “Why Did My Ryobi Pressure Washer Stopped Working”