Home>diy>Building & Construction>What Does “FFE” Mean In Construction
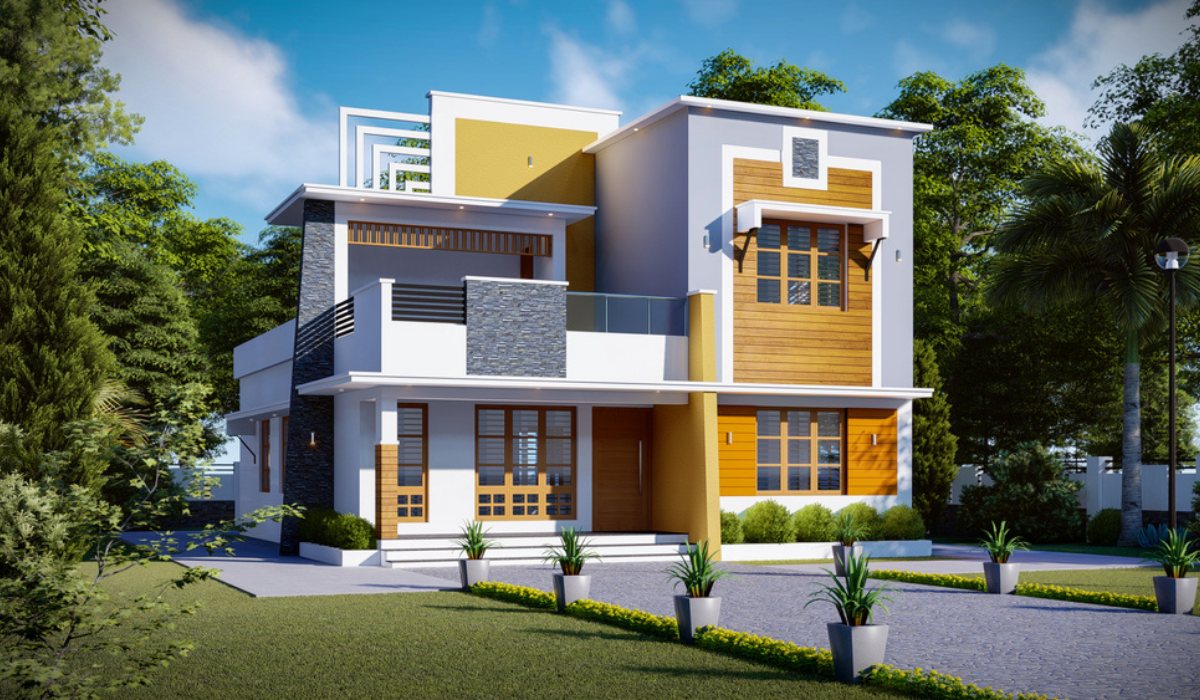
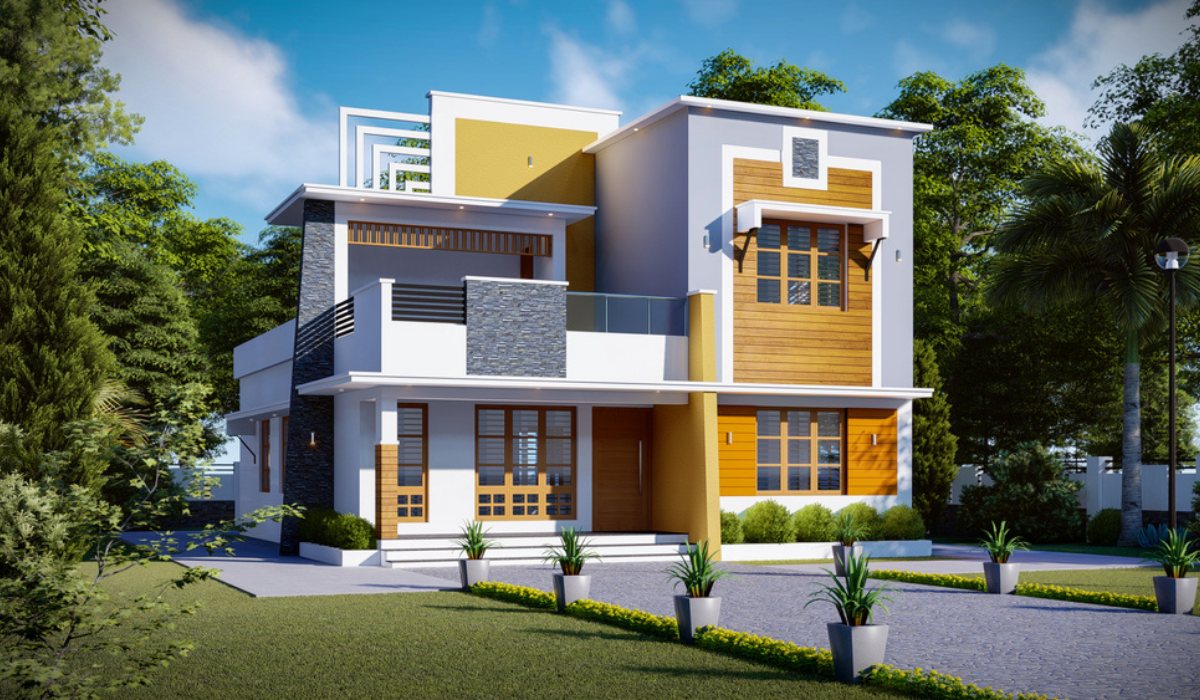
Building & Construction
What Does “FFE” Mean In Construction
Modified: September 1, 2024
Discover the meaning of "FFE" in construction and its significance in building-construction. Find out how it affects the design and functionality of a structure.
(Many of the links in this article redirect to a specific reviewed product. Your purchase of these products through affiliate links helps to generate commission for Storables.com, at no extra cost. Learn more)
Introduction
When it comes to construction projects, there are numerous terms and acronyms that are commonly used in the industry. One such acronym is “FFE,” which stands for “Furniture, Fixtures, and Equipment.” While this term may seem straightforward, its meaning and implications in construction can vary depending on the context in which it is used.
Understanding what FFE encompasses is crucial for both construction professionals and clients alike. In this article, we will delve into the meaning of FFE in the construction industry, explore its common interpretations, discuss its importance in construction projects, address the challenges involved in implementing FFE, and provide best practices for managing FFE effectively.
So, if you’re curious about what FFE means in construction and want to gain a deeper understanding of its significance, read on!
Key Takeaways:
- FFE, which stands for “Furniture, Fixtures, and Equipment,” is crucial in construction for creating comfortable spaces, ensuring functionality, and managing costs effectively.
- Managing FFE involves early involvement of specialists, thorough research, effective communication, and careful budget planning to streamline the process and ensure successful project delivery.
Understanding FFE in Construction
In the construction industry, “FFE” stands for “Furniture, Fixtures, and Equipment.” These three components play a crucial role in the completion of any construction project, regardless of its scale or purpose.
Let’s break down the meaning of each component:
- Furniture: This refers to the movable objects that are used to support human activities in a built environment. It includes items such as desks, chairs, tables, cabinets, and shelving units. Furniture helps create functional and comfortable spaces within a building.
- Fixtures: Fixtures are permanent elements that are attached or installed in a building. They include things like lighting fixtures, sinks, faucets, toilets, and built-in storage units. Fixtures are essential for the functionality and aesthetics of a space.
- Equipment: Equipment refers to the machinery, tools, appliances, and other devices necessary for the operation or use of a building. It can include items such as kitchen appliances, HVAC systems, elevators, security systems, and audiovisual equipment.
Together, FFE encompasses everything from the furnishings and finishing touches to the essential machinery and equipment needed for a building to serve its intended purpose.
It’s important to note that the inclusion of FFE in a construction project can vary based on the project’s scope and requirements. For example, an office building may require extensive furniture and fixtures for workstations, meeting rooms, and common areas. However, a warehouse facility may only require specific equipment for its operations.
Now that we have a clear understanding of what FFE entails, let’s explore the different interpretations and implications of FFE in construction.
Common Interpretations of FFE
In the construction industry, the term “FFE” can be interpreted in multiple ways, depending on the perspective of the project stakeholders. Here are the two most common interpretations:
- Physical Interpretation: From a physical standpoint, FFE refers to the tangible items that are installed or placed within a building. This includes furniture, fixtures, and equipment that are essential for the functionality and aesthetics of the space. Construction professionals, architects, and interior designers often focus on this interpretation to ensure that the necessary elements are incorporated into the design and construction process.
- Financial Interpretation: FFE can also be viewed from a financial perspective, especially when it comes to project budgeting and cost estimation. In this interpretation, FFE represents the specific components that contribute to the overall project cost. By identifying and estimating the cost of furniture, fixtures, and equipment, project owners and financial managers can effectively allocate resources and plan for procurement.
Both interpretations are important in the construction process. While the physical interpretation ensures that the necessary elements are considered during design and construction, the financial interpretation helps project stakeholders manage costs and make informed decisions regarding procurement and budget allocation.
It’s worth noting that the interpretation of FFE can vary from project to project and from industry to industry. For example, in a hospital construction project, FFE may include specialized medical equipment not typically found in other building types. Similarly, in a retail store construction project, FFE may include display shelves, cash registers, and point-of-sale systems.
Now that we understand the common interpretations of FFE, let’s explore the importance of FFE in construction projects.
Importance of FFE in Construction Projects
Furniture, Fixtures, and Equipment (FFE) play a crucial role in the success and functionality of construction projects. Here are some key reasons why FFE is important:
- User Experience: FFE directly impacts the experience of the building occupants. Comfortable and functional furniture enhances productivity in office spaces, while well-designed fixtures and equipment provide convenience and efficiency. Attention to FFE ensures that the constructed space meets the needs and expectations of its occupants.
- Aesthetics and Branding: FFE contributes to the overall aesthetics and branding of a building. The right choice of furniture and fixtures can create a particular ambiance and style that aligns with the project’s purpose and target audience. This helps in creating a positive impression and reinforcing the identity of the space.
- Functionality and Efficiency: Properly selected fixtures and equipment ensure that a building functions smoothly and efficiently. From plumbing fixtures in a bathroom to specialized equipment in a laboratory, FFE enables the building to serve its intended purpose effectively. Attention to functionality reduces operational issues and enhances user experience.
- Regulatory Compliance: FFE is often subject to specific regulations and standards. In certain industries, such as healthcare or hospitality, there are strict requirements for equipment, furnishings, and fixtures to comply with safety, health, and accessibility guidelines. Adhering to these regulations ensures the building is legally compliant and provides a safe environment for its occupants.
- Budget and Cost Control: Taking FFE into account during the early stages of a construction project enables accurate budgeting and cost control. By identifying and estimating the costs of furniture, fixtures, and equipment, project owners can allocate resources effectively and prioritize spending. It also helps in preventing delays and cost overruns during the procurement phase.
Considering the importance of FFE in construction projects is essential for the successful completion and long-term functionality of the built environment. By carefully planning and integrating FFE, project stakeholders can optimize user experience, ensure compliance, and create a space that aligns with the project’s objectives and brand image.
Next, let’s explore the challenges involved in implementing FFE and how to overcome them effectively.
“FFE” in construction stands for “Furniture, Fixtures, and Equipment.” It refers to the movable items in a building, such as desks, chairs, and appliances.
Challenges in Implementing FFE
While Furniture, Fixtures, and Equipment (FFE) are integral to construction projects, implementing them can come with certain challenges. Here are some common challenges that arise during the FFE implementation process:
- Coordination and Communication: Coordinating and communicating among various stakeholders, including architects, designers, contractors, suppliers, and clients, can be challenging. Each party has different roles and responsibilities, and ensuring effective communication and collaboration is crucial for a successful FFE implementation.
- Procurement and Lead Times: Procuring FFE items involves extensive research, evaluation of suppliers, and negotiating contracts. Additionally, lead times for manufacturing, shipping, and delivery can vary for different items. Coordinating these timelines and ensuring timely procurement can be a challenge, especially for large-scale projects and when working with international suppliers.
- Budget Constraints: FFE can significantly impact the overall project budget. Cost considerations can pose challenges when trying to balance the desired quality, functionality, and aesthetics within the available budget. It requires careful planning, value engineering, and effective cost management strategies.
- Compatibility and Integration: Ensuring compatibility and seamless integration of FFE components within the building design and infrastructure can be challenging. Conflicts may arise between functionality, space requirements, and existing systems. Coordinating MEP (Mechanical, Electrical, and Plumbing) details and ensuring proper installation and integration are vital for a successful implementation.
- Changing Design Requirements: Design requirements for FFE items can change during the course of a project. This can be due to modifications requested by the client or evolving industry standards. Adapting to these changes while balancing cost, time, and quality can pose challenges and requires effective change management.
Overcoming these challenges requires proactive planning, effective project management, and close collaboration among the project team. Regular communication, building strong relationships with suppliers, carefully analyzing the budget, anticipating design changes, and implementing contingency plans are key strategies for successful FFE implementation.
Now that we’ve explored the challenges, let’s move on to discussing best practices for managing FFE in construction projects.
Read more: What Does NOC Mean In Construction
Best Practices for Managing FFE
Effectively managing Furniture, Fixtures, and Equipment (FFE) in construction projects requires careful planning, organization, and attention to detail. Here are some best practices to help streamline the FFE management process:
- Early Involvement: Involve FFE specialists, such as interior designers, furniture consultants, and equipment suppliers, early in the project. Their expertise can contribute to better space planning, timely procurement, and seamless integration of FFE elements within the building design.
- Comprehensive Scope Definition: Clearly define the scope of FFE and its associated deliverables. Specify the required quantity, quality, and functionality of furniture, fixtures, and equipment in project documentation, contracts, and specifications. This helps ensure clarity and reduces the potential for misunderstandings during procurement.
- Thorough Research and Evaluation: Conduct thorough research and evaluation of potential suppliers, manufacturers, and contractors for FFE items. Consider factors such as their reputation, past project experience, product quality, lead times, and pricing. Request and review samples, specifications, and warranties to make informed decisions.
- Budget Planning and Tracking: Develop a detailed budget plan specifically for FFE. Estimate the costs accurately, considering procurement, installation, and any associated fees or taxes. Regularly track and monitor the FFE budget to ensure it remains within allocated limits. Utilize cost management techniques, such as value engineering, to optimize costs without sacrificing quality.
- Effective Communication and Collaboration: Foster open and regular communication among all project stakeholders involved in FFE implementation. Maintain a collaborative environment where information, updates, and changes are shared promptly. Utilize technology tools, such as project management software, to facilitate communication, document sharing, and tracking of progress.
- Quality Assurance: Implement a robust quality assurance process for FFE items. Establish clear quality standards, conduct inspections, and verify compliance with relevant codes, regulations, and project requirements. Regularly communicate with suppliers and manufacturers to address any quality concerns or issues that may arise.
- Documenting and Providing Specifications: Clearly document and provide detailed specifications for each FFE item. Include information regarding dimensions, materials, finishes, installation requirements, warranties, and maintenance instructions. This ensures consistent understanding among all stakeholders and helps in managing expectations.
- Change Management: Anticipate and plan for potential design changes or modifications related to FFE. Establish change management protocols to effectively handle and track any requested changes. Assess the impacts on schedule, budget, and quality before implementing the changes, and communicate them clearly to all relevant stakeholders.
Implementing these best practices helps streamline the management of FFE, improves project coordination, ensures quality, and minimizes potential delays or budget overruns. By proactively managing FFE, construction projects can achieve successful outcomes that meet client expectations and provide functional and aesthetically pleasing spaces.
Now, let’s wrap up our discussion on FFE in construction projects.
Conclusion
Understanding the significance of Furniture, Fixtures, and Equipment (FFE) in construction projects is essential for achieving successful outcomes. FFE encompasses the tangible elements that contribute to the functionality, aesthetics, and user experience of a built environment.
Throughout this article, we explored the meaning of FFE, its common interpretations, and the importance of considering FFE in construction projects. We also discussed the challenges that arise during the implementation of FFE and provided best practices for effectively managing FFE.
From enhancing user experience and creating a cohesive design to ensuring compliance with regulations and managing costs, FFE plays a critical role in constructing spaces that align with the project’s objectives and meet the needs of its occupants.
Effectively managing FFE requires early involvement of specialists, comprehensive scope definition, thorough research and evaluation, budget planning and tracking, effective communication and collaboration, quality assurance, and implementing proper change management protocols.
By implementing these best practices, construction professionals can streamline the FFE management process, mitigate risks, and ensure successful project delivery. The integration of FFE elements in construction projects contributes to the overall functionality, efficiency, and satisfaction of the end-users.
In conclusion, being knowledgeable about FFE in construction enables the construction industry to create spaces that are not just structurally sound but also aesthetically pleasing, functional, and tailored to the needs of the end-users. By understanding the importance, challenges, and best practices associated with FFE, construction projects can reach new heights of success.
Frequently Asked Questions about What Does "FFE" Mean In Construction
Was this page helpful?
At Storables.com, we guarantee accurate and reliable information. Our content, validated by Expert Board Contributors, is crafted following stringent Editorial Policies. We're committed to providing you with well-researched, expert-backed insights for all your informational needs.
0 thoughts on “What Does “FFE” Mean In Construction”