Home>Technology>Smart Home Devices>How To Improve Adhesion In A 3D Printer
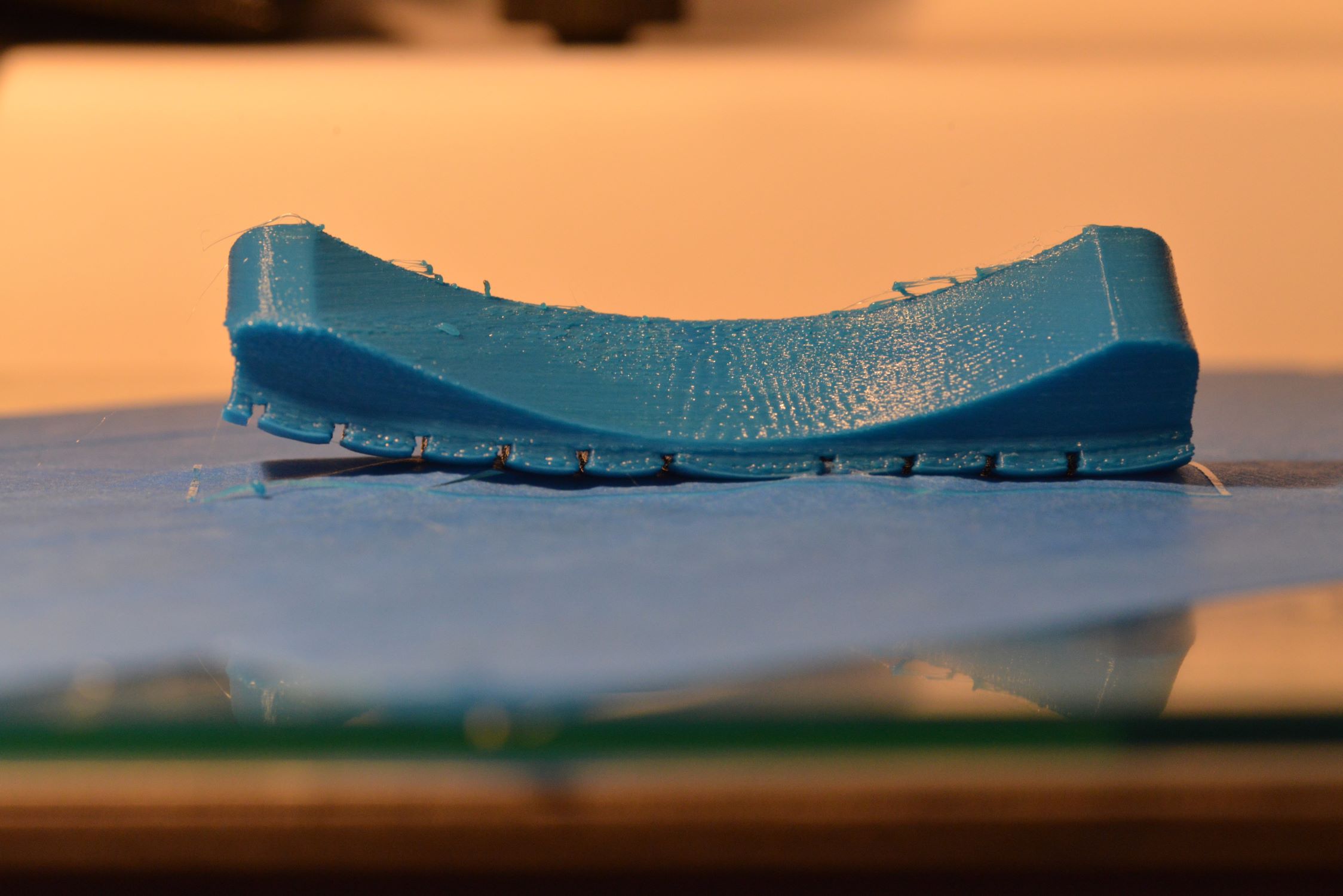
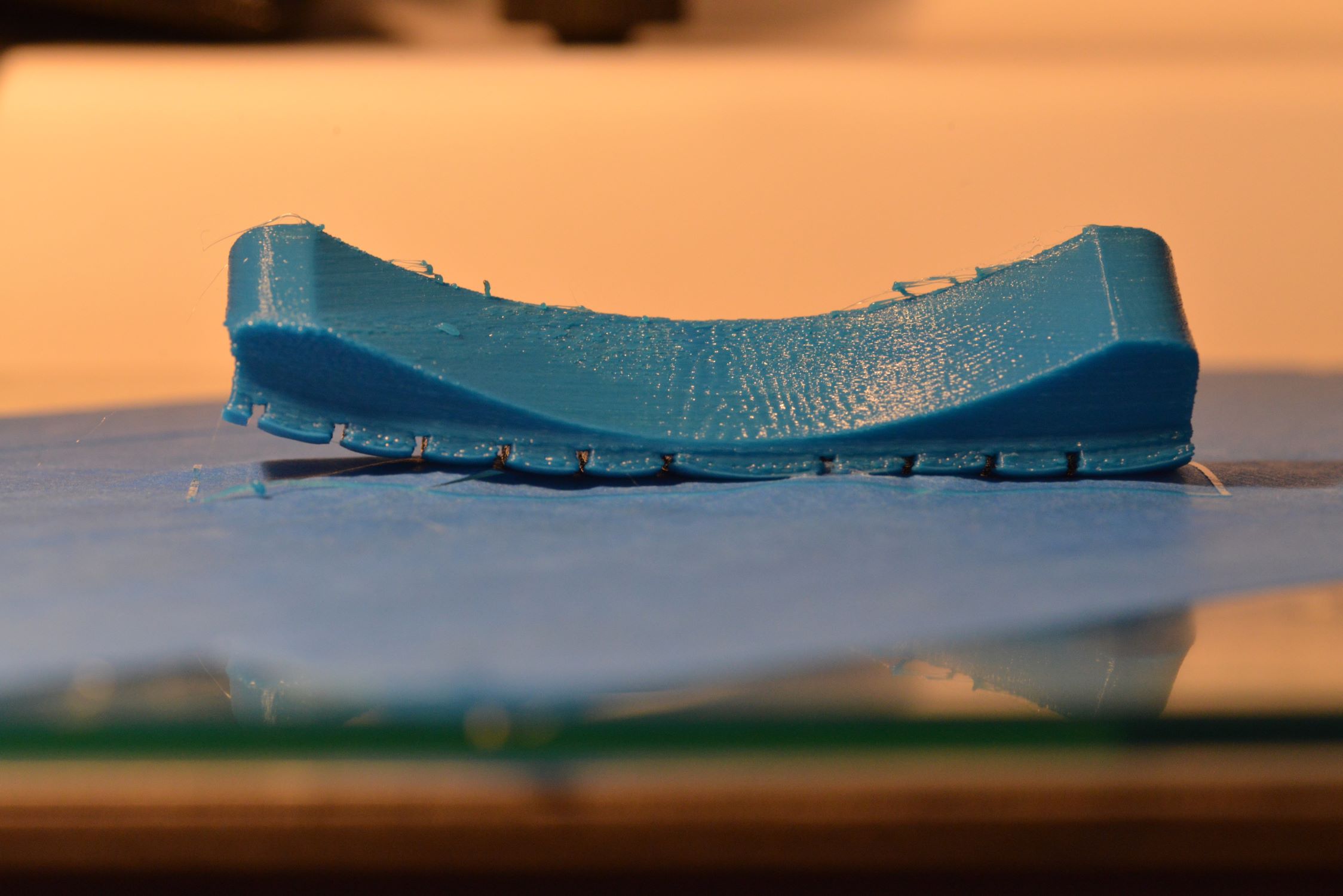
Smart Home Devices
How To Improve Adhesion In A 3D Printer
Modified: August 20, 2024
Learn how to enhance adhesion in your 3D printer for better results. Discover the best tips and tricks for optimizing your smart home devices.
(Many of the links in this article redirect to a specific reviewed product. Your purchase of these products through affiliate links helps to generate commission for Storables.com, at no extra cost. Learn more)
Introduction
Welcome to the exciting world of 3D printing! Whether you’re a seasoned enthusiast or a newcomer to the realm of additive manufacturing, one of the most crucial aspects of successful 3D printing is adhesion. Achieving optimal adhesion between the 3D printing material and the build surface is essential for producing high-quality prints with precise details and smooth finishes. In this comprehensive guide, we’ll delve into the intricacies of adhesion in 3D printing, explore the factors that influence it, address common adhesion problems, and provide valuable tips for enhancing adhesion to elevate the quality of your 3D prints.
Understanding the dynamics of adhesion and implementing effective strategies to improve it can significantly impact the overall 3D printing experience, leading to enhanced print reliability and consistency. So, let’s embark on this enlightening journey to unravel the secrets of optimizing adhesion in a 3D printer!
Key Takeaways:
- Proper adhesion is crucial in 3D printing for creating high-quality prints. Factors like material type, surface preparation, and temperature significantly impact adhesion and print success.
- Common adhesion problems, such as warped prints and poor first layer adhesion, can be overcome by implementing strategies like proper bed leveling, surface cleaning, and optimized printing temperatures.
Read more: What Is An Extruder On A 3D Printer
Understanding Adhesion in 3D Printing
In the realm of 3D printing, adhesion refers to the bond between the 3D printing material, such as filament or resin, and the build surface of the 3D printer. This bond is critical as it ensures that the printed layers adhere firmly to the build platform throughout the printing process, ultimately determining the quality and accuracy of the final print.
Adhesion is especially vital during the initial layers of the printing process, as these foundational layers serve as the base upon which subsequent layers are deposited. If the initial layers do not adhere properly to the build surface, it can result in print defects, warping, or even detachment of the print from the build platform, leading to print failures.
Several key factors contribute to the adhesion process in 3D printing, including the type of printing material, the composition and condition of the build surface, the printing temperature, and the presence of additional adhesion aids such as bed adhesives or coatings. Understanding the interplay of these factors is essential for achieving optimal adhesion and ensuring successful 3D prints.
By comprehending the significance of adhesion and its underlying mechanisms, 3D printing enthusiasts can make informed decisions regarding print settings, material selection, and surface preparation, ultimately leading to improved print adhesion and overall print quality. Now, let’s explore the factors that influence adhesion in 3D printing and delve deeper into the intricacies of this fundamental aspect of the 3D printing process.
Factors Affecting Adhesion
Several critical factors play a pivotal role in determining the adhesion quality in 3D printing. Understanding these factors is essential for optimizing adhesion and achieving successful print outcomes. Let’s explore the key elements that influence adhesion in the 3D printing process:
- Printing Material: The type and composition of the printing material significantly impact adhesion. Different materials, such as PLA, ABS, PETG, and TPU, have distinct adhesion characteristics based on their adhesion to various build surfaces and their susceptibility to warping.
- Build Surface: The build surface, often referred to as the print bed, plays a crucial role in adhesion. Common build surface materials include glass, aluminum, PEI sheets, and specialized build surfaces like BuildTak. The surface texture, cleanliness, and temperature management are vital factors influencing adhesion.
- Printing Temperature: The extruder and bed temperatures impact the material’s adhesion to the build surface. Maintaining the recommended temperatures for the specific printing material is essential for promoting adhesion and preventing warping or delamination.
- Layer Height and First Layer Settings: Proper calibration of the initial layer height and printing speed is crucial for ensuring adequate material deposition and adhesion during the first layer of the print. Fine-tuning these settings can significantly enhance adhesion and overall print quality.
- Adhesion Aids: Additional adhesion aids, such as adhesive sprays, glue sticks, or specialized bed adhesives, can be used to improve adhesion, especially for challenging materials or intricate prints. These aids create a temporary bond between the print material and the build surface, promoting better adhesion.
- Environmental Conditions: Factors such as ambient temperature, humidity levels, and airflow in the printing environment can influence adhesion. Controlling these environmental variables can help maintain consistent adhesion performance across different printing sessions.
By considering and optimizing these factors, 3D printing enthusiasts can effectively address adhesion challenges and elevate the quality and reliability of their prints. Now that we’ve explored the factors affecting adhesion, let’s delve into common adhesion problems encountered in 3D printing and discover effective solutions to overcome these challenges.
Clean the print bed with isopropyl alcohol before starting a new print to remove any oils or debris that could affect adhesion.
Common Adhesion Problems
Despite the advancements in 3D printing technology, adhesion issues can still arise, leading to frustrating print failures and suboptimal print quality. Understanding the common adhesion problems encountered in 3D printing is crucial for implementing targeted solutions and improving print outcomes. Let’s explore some of the typical adhesion challenges faced by 3D printing enthusiasts:
- Warped Prints: Warping occurs when the printed object’s corners or edges lift or curl upwards during the printing process, leading to a distorted final shape. This problem is often attributed to uneven cooling, inadequate bed adhesion, or excessive temperature differentials within the print.
- Poor First Layer Adhesion: Inadequate adhesion during the first layer of the print can result in uneven or detached initial layers, compromising the structural integrity of the entire print. Factors such as improper bed leveling, insufficient bed adhesion aids, or incorrect printing temperatures can contribute to this issue.
- Print Detachment: Print detachment occurs when the printed object partially or completely separates from the build surface during the printing process. This issue can be caused by insufficient bed adhesion, improper cooling settings, or excessive mechanical stress on the print due to rapid movements of the 3D printer’s components.
- Adhesion to Specialty Materials: Certain specialty materials, such as flexible filaments or composite materials, may pose unique adhesion challenges due to their specific material properties. These materials may require tailored adhesion strategies to ensure successful prints.
- Print Imperfections: Adhesion problems can manifest as visible imperfections on the print surface, such as gaps, layer misalignments, or rough textures. These imperfections can detract from the overall print quality and aesthetic appeal of the final object.
Identifying and addressing these common adhesion problems is essential for enhancing the reliability and consistency of 3D prints. By implementing targeted solutions and proactive measures, 3D printing enthusiasts can overcome these challenges and elevate the overall print quality. Now, let’s delve into valuable tips and strategies for improving adhesion in 3D printing to achieve exceptional print outcomes.
Tips for Improving Adhesion
Enhancing adhesion in 3D printing is a multifaceted endeavor that involves optimizing various aspects of the printing process and implementing effective strategies to promote strong and consistent adhesion between the print material and the build surface. Here are valuable tips and techniques for improving adhesion in 3D printing:
- Proper Bed Leveling: Ensuring that the build surface is precisely leveled is crucial for establishing uniform adhesion across the entire print area. Regular bed leveling maintenance is essential for preventing adhesion inconsistencies and print defects.
- Surface Preparation: Cleaning the build surface thoroughly and, if necessary, applying adhesion aids such as glue sticks, adhesive sprays, or specialized bed adhesives can significantly enhance adhesion, especially for materials prone to adhesion challenges.
- Optimized Printing Temperature: Adhering to the recommended extruder and bed temperatures specified for the printing material is essential for promoting proper adhesion and mitigating the risk of warping or delamination during the print.
- First Layer Calibration: Fine-tuning the first layer height, printing speed, and extrusion flow rate can improve the initial layer’s adhesion and contribute to the overall print stability and quality.
- Enclosed Print Environment: Creating a controlled and enclosed printing environment can help regulate ambient temperature and minimize drafts, contributing to more consistent adhesion performance, especially for materials sensitive to temperature fluctuations.
- Adhesion Enhancement Products: Utilizing specialized build surfaces, such as PEI sheets or BuildTak, can provide enhanced adhesion for specific materials. Additionally, experimenting with different adhesion aids can help identify the most effective solutions for challenging prints.
- Print Cooling Management: Optimizing the cooling settings, particularly for materials prone to warping, can help maintain proper adhesion while preventing overheating and deformation during the printing process.
- Adaptive Raft or Brim Structures: Implementing raft or brim structures in the print settings can provide additional adhesion support, especially for prints with intricate geometries or limited surface contact with the build platform.
By incorporating these tips into the 3D printing workflow and adapting them to specific printing materials and models, enthusiasts can significantly enhance adhesion and elevate the overall print quality. Now that we’ve explored these valuable tips, let’s conclude our journey by summarizing the key insights and emphasizing the importance of prioritizing adhesion in 3D printing.
Read more: Where To Put A 3D Printer
Conclusion
Adhesion is a fundamental aspect of 3D printing that profoundly influences the quality, reliability, and success of printed objects. By gaining a comprehensive understanding of adhesion and the factors that impact it, 3D printing enthusiasts can navigate the intricacies of the printing process with confidence and precision. From the type of printing material and build surface characteristics to temperature management and adhesion enhancement techniques, every facet of adhesion plays a crucial role in shaping the outcome of 3D prints.
Addressing common adhesion problems and implementing targeted solutions, such as proper bed leveling, surface preparation, and optimized printing parameters, empowers enthusiasts to overcome challenges and consistently achieve exceptional print adhesion. Furthermore, the utilization of adhesion aids and the strategic management of environmental and cooling factors contribute to a more robust and reliable adhesion performance across diverse printing scenarios.
As 3D printing continues to evolve and expand into various industries and creative endeavors, the significance of adhesion remains paramount. By embracing the tips and techniques for improving adhesion, enthusiasts can elevate their printing capabilities, enhance print quality, and unlock the full potential of their 3D printers.
In essence, prioritizing adhesion in 3D printing is not merely a technical consideration but a foundational principle that underpins the art and science of additive manufacturing. By honing adhesion expertise and integrating best practices into the printing workflow, enthusiasts can embark on a journey of innovation and craftsmanship, bringing their digital designs to life with precision, reliability, and excellence.
So, as you embark on your next 3D printing venture, remember that adhesion is the cornerstone of your printing success, and by mastering its nuances, you pave the way for a world of limitless creative possibilities in the realm of additive manufacturing.
Frequently Asked Questions about How To Improve Adhesion In A 3D Printer
Was this page helpful?
At Storables.com, we guarantee accurate and reliable information. Our content, validated by Expert Board Contributors, is crafted following stringent Editorial Policies. We're committed to providing you with well-researched, expert-backed insights for all your informational needs.
0 thoughts on “How To Improve Adhesion In A 3D Printer”