Home>Articles>How Can The Direction Of Rotation Of A DC Electric Motor Be Changed?
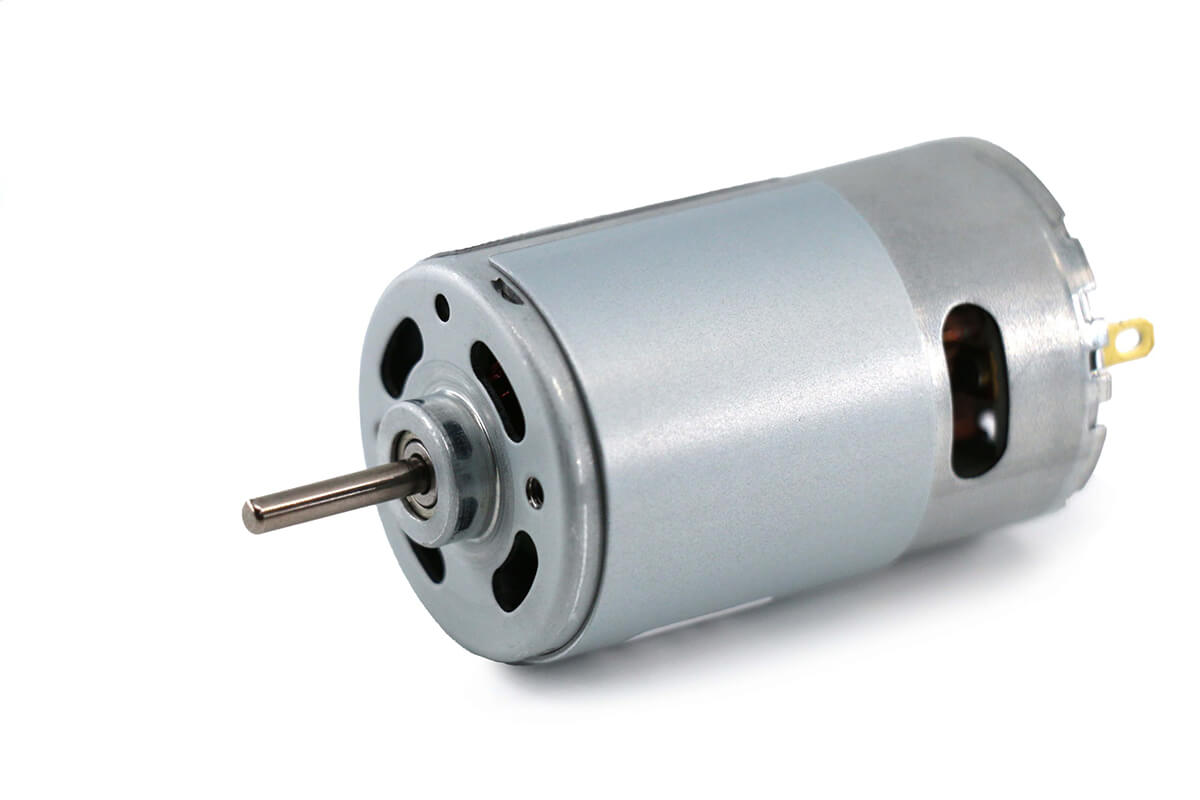
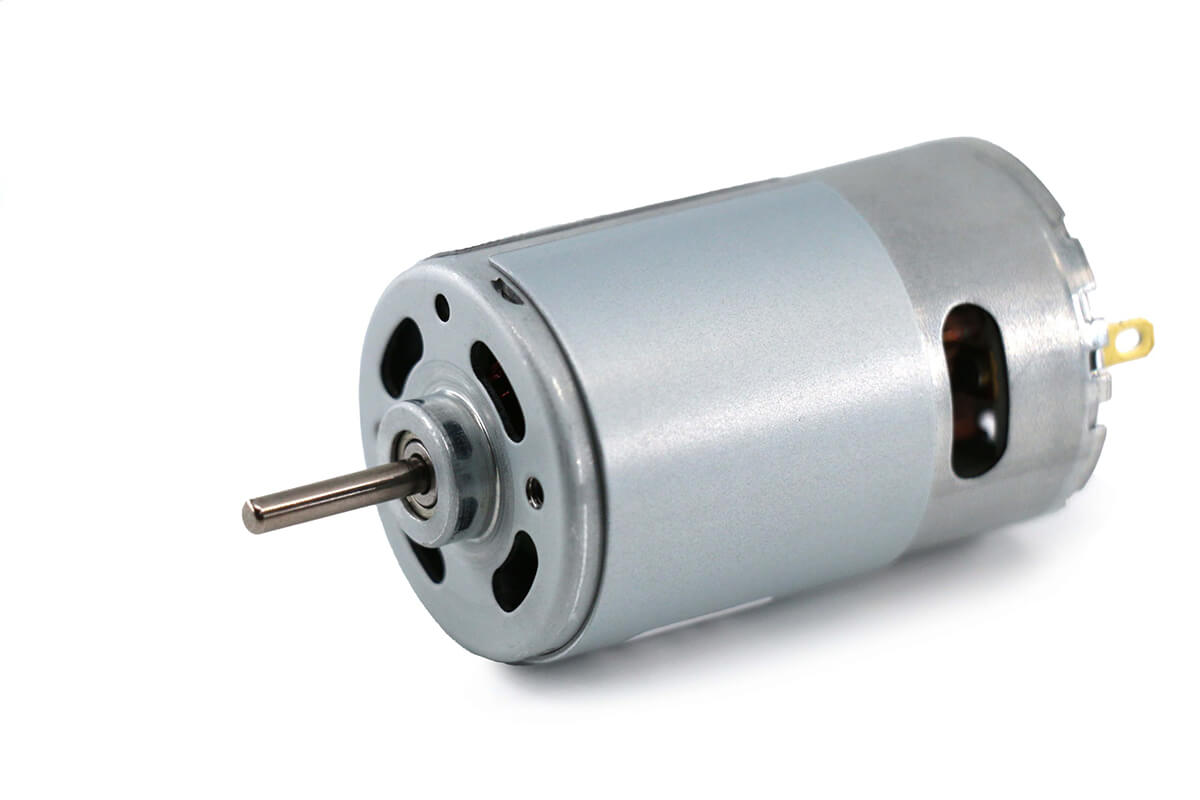
Articles
How Can The Direction Of Rotation Of A DC Electric Motor Be Changed?
Modified: December 7, 2023
Discover helpful articles on changing the direction of rotation in DC electric motors. Explore step-by-step guides and tips for efficient motor control.
(Many of the links in this article redirect to a specific reviewed product. Your purchase of these products through affiliate links helps to generate commission for Storables.com, at no extra cost. Learn more)
Introduction
Direct Current (DC) electric motors are widely used in various applications, ranging from small household appliances to large industrial machinery. These motors have the unique ability to convert electrical energy into mechanical energy through the use of electromagnetic principles. One of the key aspects of DC motors is their ability to change the direction of rotation, allowing for versatile applications and control.
In this article, we will explore the different methods to change the direction of rotation in a DC electric motor. Understanding these methods is crucial for individuals involved in maintenance, repairs, or even those who simply want to gain a deeper understanding of how DC motors operate.
Before diving into the various methods, let’s quickly examine how the direction of rotation is determined in a DC electric motor. The rotation of a DC motor is influenced by the interaction between the magnetic fields generated by the stator (stationary part) and the armature (rotating part) of the motor. Depending on the polarity and configuration of these magnetic fields, the motor will rotate either clockwise or counterclockwise.
Changing the direction of rotation in a DC motor is essential in many applications. For example, in a robotic arm, the ability to reverse the motor’s rotation allows for precise control and movement in different directions. Similarly, in a conveyor belt system, reversing the motor’s rotation can facilitate the movement of materials in both forward and reverse directions.
Now that we have established the importance of changing the direction of rotation in a DC motor, let’s explore the common methods used to achieve this.
Key Takeaways:
- Understanding the Direction of Rotation
In a DC electric motor, the direction of rotation is determined by the interaction of magnetic fields and current flow. Methods like reversing power supply polarity and swapping armature leads can effectively change the rotation direction. - Versatile Methods for Changing Rotation
From reversing power supply polarity to using mechanical reversing switches and electronic speed controllers, there are versatile methods to change the direction of rotation in DC electric motors. Each method offers unique advantages and considerations based on specific motor types and applications.
Read more: How Does A Dc Electric Motor Work
Understanding the Direction of Rotation in DC Electric Motors
Before delving into the methods of changing the direction of rotation in a DC electric motor, it is crucial to grasp the underlying principles that determine the motor’s rotation. This understanding will help us comprehend how the different methods manipulate these principles to achieve the desired outcome.
In a DC electric motor, the direction of rotation depends on the alignment and interaction of magnetic fields. The motor is composed of two fundamental components: the stator and the armature. The stator, which remains stationary, consists of permanent magnets or electromagnets that create a magnetic field. The armature, on the other hand, is the moving part and typically comprises a coil of wire known as the rotor, which produces a magnetic field when an electric current passes through it.
When an electric current flows through the armature, a magnetic force is generated, causing the armature’s magnetic field to interact with the stator’s magnetic field. The resulting interaction determines the direction of rotation of the DC motor. Specifically, the direction of the current flow and the polarity of the magnetic fields play a vital role in determining the direction in which the armature rotates.
In a basic DC motor, the armature is connected via brushes and commutator segments. The brushes facilitate the flow of current from an external power supply to the armature, while the commutator segments ensure that the current reverses its direction every half-revolution of the armature. This reversal of current flow maintains the magnetic field’s polarity, resulting in continuous rotation in the same direction.
To understand the direction of rotation, consider a simple example. Suppose the current enters the armature through the positive brush and exits through the negative brush. In this configuration, the magnetic force created in the armature interacts with the stator’s magnetic field, causing the armature to rotate in one direction, let’s say clockwise. Now, if the current flow is reversed, with the current entering through the negative brush and exiting through the positive brush, the magnetic force reverses as well, resulting in a counterclockwise rotation of the armature.
It is important to note that the actual direction of rotation may vary depending on the specific design and construction of the DC motor. Therefore, it is crucial to consult the motor’s manual or documentation to determine the default direction of rotation.
With a solid understanding of how the direction of rotation is determined in a DC electric motor, we can now explore the different methods used to change this direction. Through the manipulation of electrical connections or mechanical components, these methods enable us to reverse or adjust the rotation to suit specific applications.
Common Methods to Change the Direction of Rotation
There are several methods available to change the direction of rotation in a DC electric motor. These methods provide flexibility and control in various applications. Let’s explore some of the most common methods below:
1. Reversing the Power Supply Polarity: One of the simplest ways to change the direction of rotation is by reversing the polarity of the power supply. This involves swapping the positive and negative terminals of the power source connected to the motor. By reversing the flow of current, the magnetic force generated in the armature and its interaction with the stator’s magnetic field cause the motor to rotate in the opposite direction.
2. Swapping the Armature Leads: Another method to change the rotation direction is by swapping the armature leads. This requires disconnecting the armature from the power supply and interchanging the connections of the positive and negative leads. This effectively reverses the current flow within the armature, resulting in a reverse rotation of the motor.
3. Using a Mechanical Reversing Switch: Some DC motors come equipped with a built-in mechanical reversing switch. This switch allows the user to manually change the direction of rotation by simply flipping the switch. When the switch is activated, it alters the internal connections of the motor, effectively reversing the current flow and changing the rotation direction.
4. Using an Electronic Speed Controller (ESC): Electronic Speed Controllers (ESCs) are commonly used in applications such as RC vehicles. These controllers not only regulate the speed of the motor but also provide the option to reverse the rotation direction. By programming the ESC accordingly, the user can change the motor’s rotation with the push of a button or a control signal.
5. Reconfiguring the Brush Connections: In certain types of DC motors, such as brushed motors, the direction of rotation can be changed by reconfiguring the brush connections. By swapping the brush leads, the motor’s current flow and magnetic field relationships are altered, resulting in a reversal of the rotation direction.
These methods offer versatile options to change the direction of rotation in a DC electric motor. Depending on the specific motor design, application requirements, and available control mechanisms, one or more of these methods may be used.
It is essential to follow proper safety guidelines and consult the motor’s documentation or manufacturer’s instructions when applying any of these methods to ensure correct and safe operation.
In the next sections, we will explore each method in detail, providing step-by-step instructions and considerations for implementing these changes effectively.
Method 1: Reversing the Power Supply Polarity
One of the simplest and most straightforward methods to change the direction of rotation in a DC electric motor is by reversing the polarity of the power supply. This method involves swapping the positive and negative terminals of the power source connected to the motor.
To implement this method, follow these steps:
- First, ensure that the motor is disconnected from any power source to avoid any accidental electrical shock.
- Identify the power supply terminals connected to the motor. Typically, these are labeled as positive (+) and negative (-) or have distinct color-coding.
- Using proper safety precautions, carefully disconnect the wires or connectors from the power supply terminals.
- Now, swap the connections. Connect the wire that was originally connected to the positive terminal to the negative terminal of the power supply, and vice versa.
- Double-check all connections to ensure they are secure and properly tightened.
- Once you have completed the reversal of the power supply polarity, you can now reapply power and observe the motor’s rotation direction.
It is important to note that reversing the power supply polarity may be a suitable method for some applications but not for all. Certain systems or components connected to the motor may not be compatible with reverse rotation. Therefore, it is essential to consider the overall system requirements and potential consequences before applying this method.
Additionally, it is crucial to follow proper safety procedures and adhere to manufacturer’s guidelines when working with electrical connections. If you are uncertain or uncomfortable performing this procedure, it is recommended to seek assistance from a qualified professional.
By simply reversing the polarity of the power supply, you can effectively change the direction of rotation in a DC electric motor, providing versatility and control in various applications.
Method 2: Swapping the Armature Leads
Another method to change the direction of rotation in a DC electric motor is by swapping the armature leads. This method involves disconnecting the motor’s armature from the power supply and interchanging the connections of the positive and negative leads.
To implement this method, follow these steps:
- Ensure that the motor is disconnected from any power source to prevent potential electrical hazards.
- Locate the armature leads connected to the motor. These leads are typically connected to the brush terminals of the motor.
- Using appropriate safety measures, carefully disconnect the armature leads from the brush terminals.
- Once the leads are disconnected, swap their positions. Connect the lead that was originally connected to the positive brush terminal to the negative brush terminal, and vice versa.
- Ensure that all connections are secure and properly fastened.
- Now, you can reconnect the motor to the power supply and observe the direction of rotation.
Swapping the armature leads effectively reverses the current flow within the armature, resulting in a change in the direction of rotation of the motor. It is a simple and effective method, especially for motors with easily accessible brush terminals.
However, it is important to note that this method may not be suitable for all motor designs. Some motors have complex internal structures, making it difficult or impractical to access and swap the armature leads. In such cases, it is best to consult the motor’s documentation or seek guidance from the manufacturer.
As always, exercise caution and follow safety procedures when working with electrical connections. If you are uncertain about performing this procedure, it is recommended to consult a qualified professional.
By swapping the armature leads, you can quickly and easily change the direction of rotation in a DC electric motor, providing versatility and control in various applications.
To change the direction of rotation of a DC electric motor, simply reverse the polarity of the power supply by swapping the connections to the motor’s terminals. This can be done by switching the wires or using a polarity-reversing switch.
Read more: How To Reverse An Electric Motor Rotation
Method 3: Using a Mechanical Reversing Switch
Another method commonly used to change the direction of rotation in a DC electric motor is by utilizing a mechanical reversing switch. This method involves the use of a switch that allows manual control over the motor’s rotation direction.
To implement this method, follow these steps:
- Ensure that the motor is disconnected from any power source to avoid any potential electrical hazards.
- Locate a suitable mechanical reversing switch compatible with your motor. These switches are often designed specifically for DC motor applications and can be found in electrical supply stores.
- Carefully install the reversing switch according to the manufacturer’s instructions. This may involve making the necessary electrical connections and mounting the switch securely.
- Once the reversing switch is installed, connect the motor’s power supply to the switch, following the manufacturer’s instructions for wiring.
- Now, you can operate the mechanical reversing switch to change the motor’s rotation direction. Usually, the switch will have two positions, allowing you to toggle between forward and reverse rotation.
The mechanical reversing switch provides a convenient and reliable method to manually change the direction of rotation in a DC electric motor. It allows for quick and easy control, making it suitable for applications where frequent changes in rotation direction are required.
It is important to note that not all motors come equipped with a built-in mechanical reversing switch. In such cases, an external reversing switch can be added to the motor circuit to achieve the desired functionality. Again, it is crucial to consult the motor’s documentation or seek guidance from the manufacturer to ensure compatibility and proper installation.
Ensure that you follow proper safety procedures and guidelines when working with electrical connections. If you are uncertain or unfamiliar with the installation of a reversing switch, it is recommended to seek assistance from a qualified professional.
By utilizing a mechanical reversing switch, you can easily and manually change the direction of rotation in a DC electric motor, providing precise control in various applications.
Method 4: Using an Electronic Speed Controller (ESC)
Using an Electronic Speed Controller (ESC) is another effective method to change the direction of rotation in a DC electric motor. ESCs are commonly used in applications such as RC vehicles, drones, and robotic systems. These controllers not only regulate the speed of the motor but also provide the option to reverse the rotation direction.
To implement this method, follow these steps:
- Ensure that the motor is disconnected from any power source to prevent potential electrical hazards.
- Select an appropriate ESC that is compatible with your motor and meets the power and control requirements of your application.
- Follow the manufacturer’s instructions to properly install the ESC, making the necessary electrical connections and ensuring secure mounting of the controller.
- Connect the motor to the ESC following the manufacturer’s instructions for wiring. Typically, the motor wires are connected to the ESC’s output terminals.
- Ensure that the ESC is properly calibrated and programmed according to the motor specifications and desired control settings.
- Once the ESC is installed and calibrated, you can use the control interface (such as a remote control or programming software) to change the rotation direction of the motor. This can usually be achieved by flipping a switch, selecting a menu option, or sending a specific command signal based on the ESC’s programming.
Using an ESC provides a convenient and versatile method to not only change the direction of rotation but also regulate the motor’s speed. This is particularly useful in applications where precise control and dynamic movement are required.
It is important to note that not all motors are compatible with ESCs, as certain motors may require specific controllers or speed control mechanisms. Therefore, it is essential to check the motor’s documentation or consult the manufacturer to ensure compatibility and proper operation.
When working with ESCs and making electrical connections, adhere to proper safety precautions and guidelines. If you are unfamiliar with the installation or programming of an ESC, it is recommended to seek assistance from someone experienced or knowledgeable in this area.
By utilizing an Electronic Speed Controller (ESC), you can easily and precisely change the direction of rotation in a DC electric motor, providing versatile control in a wide range of applications.
Method 5: Reconfiguring the Brush Connections
In certain types of DC motors, such as brushed motors, another method to change the direction of rotation is by reconfiguring the brush connections. This method involves swapping the brush leads of the motor, effectively altering the current flow and magnetic field relationships, resulting in a reversal of the rotation direction.
To implement this method, follow these steps:
- Disconnect the motor from any power source to prevent potential electrical hazards.
- Identify the brush terminals of the motor. These terminals are typically connected to the commutator segments and the brushes.
- Carefully remove the connections of the brush leads from the terminals. Take note of the original connection configuration for reference.
- Swap the brush leads, connecting the lead that was originally connected to the positive brush terminal to the negative brush terminal, and vice versa.
- Ensure that all connections are secure and properly tightened.
- Reconnect the motor to the power source and observe the direction of rotation.
Reconfiguring the brush connections effectively changes the relationship between the current flow within the armature and the magnetic field, resulting in a reverse direction of rotation. This method is commonly used in brushed motors, which have a simple commutator and brush design that allows for easy access to the brush terminals.
Note that not all motors are compatible with reconfiguring the brush connections to change direction. Certain motors may have fixed or non-adjustable brush configurations, making this method impractical or not possible. Therefore, it is crucial to consult the motor’s documentation or manufacturer’s recommendations to ensure compatibility.
When working with electrical connections, always follow proper safety procedures and guidelines. If you are uncertain or uncomfortable performing this procedure, it is recommended to seek assistance from a qualified professional.
By reconfiguring the brush connections, you can effectively change the direction of rotation in a DC electric motor, providing flexibility and control in various applications.
Conclusion
Changing the direction of rotation in a DC electric motor is a crucial aspect in many applications that require versatile control and precise movements. Throughout this article, we have explored various methods to achieve this, providing insights into how each method manipulates the motor’s electrical and mechanical components.
We began by understanding the basic principles that determine the direction of rotation in a DC electric motor, highlighting the importance of magnetic fields and current flow. From there, we delved into five common methods to change the rotation direction:
1. Reversing the Power Supply Polarity: By swapping the positive and negative terminals of the power supply, the motor’s rotation direction can be reversed.
2. Swapping the Armature Leads: Interchanging the connections of the positive and negative leads of the motor’s armature changes the current flow and, subsequently, the rotation direction.
3. Using a Mechanical Reversing Switch: Employing a mechanical reversing switch allows for manual control of the rotation direction by toggling between forward and reverse settings.
4. Using an Electronic Speed Controller (ESC): ESCs not only regulate motor speed but also offer the flexibility to change the rotation direction through programming or control interfaces.
5. Reconfiguring the Brush Connections: In certain types of motors, reconfiguring the brush connections alters the current flow and magnetic field relationships to achieve a change in rotation direction.
Each method has its own advantages and considerations depending on the motor type, application requirements, and available control mechanisms. It is important to carefully evaluate these factors before selecting the appropriate method.
Remember to always prioritize safety when working with electrical components. Following proper procedures and consulting the motor’s documentation or seeking professional guidance can help ensure safe and effective implementation of these methods.
In conclusion, the ability to change the direction of rotation in a DC electric motor offers flexibility, control, and adaptability in various applications. By understanding and utilizing the methods discussed in this article, you can confidently manipulate the rotation direction to meet your specific needs.
Frequently Asked Questions about How Can The Direction Of Rotation Of A DC Electric Motor Be Changed?
Was this page helpful?
At Storables.com, we guarantee accurate and reliable information. Our content, validated by Expert Board Contributors, is crafted following stringent Editorial Policies. We're committed to providing you with well-researched, expert-backed insights for all your informational needs.
0 thoughts on “How Can The Direction Of Rotation Of A DC Electric Motor Be Changed?”