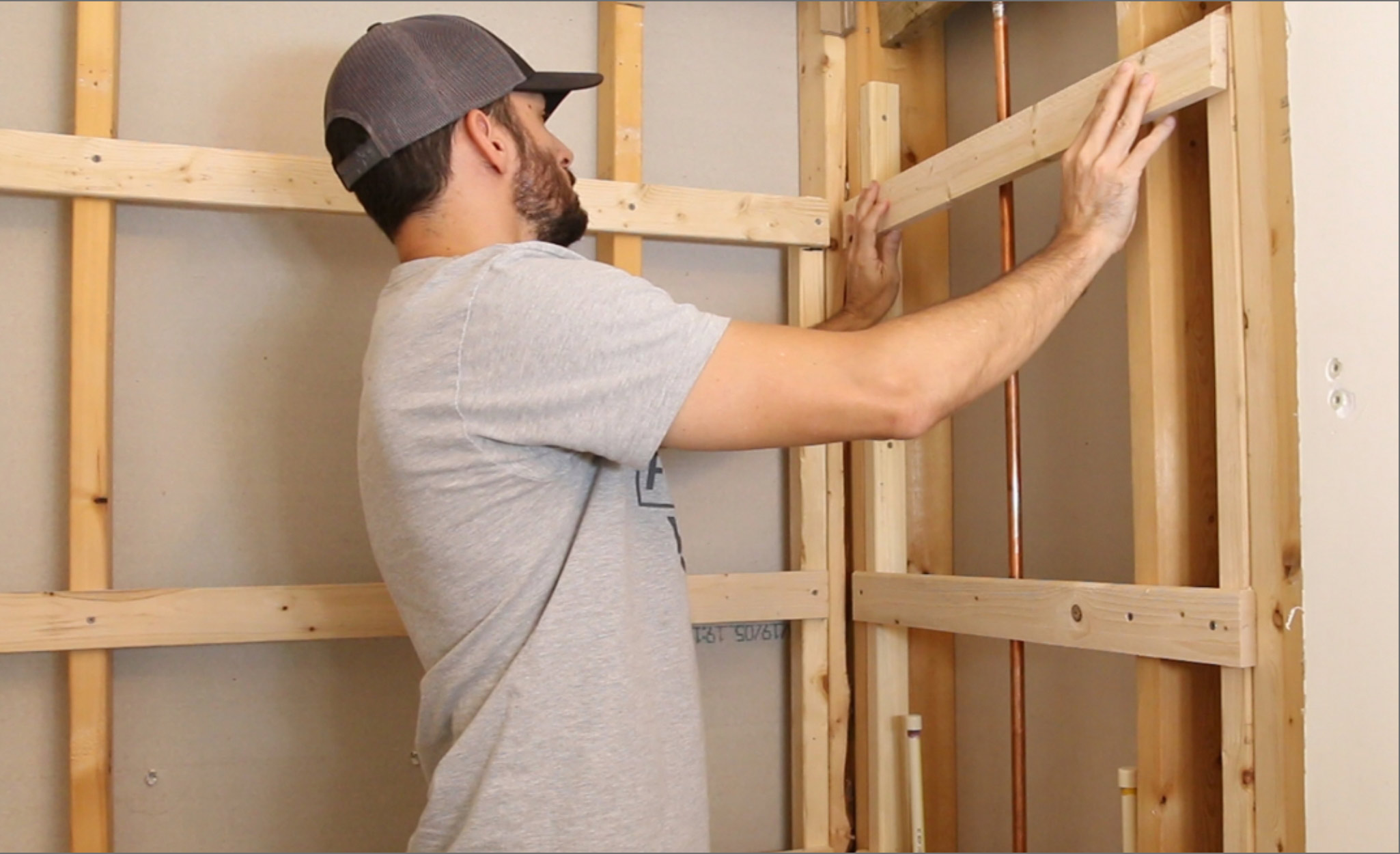
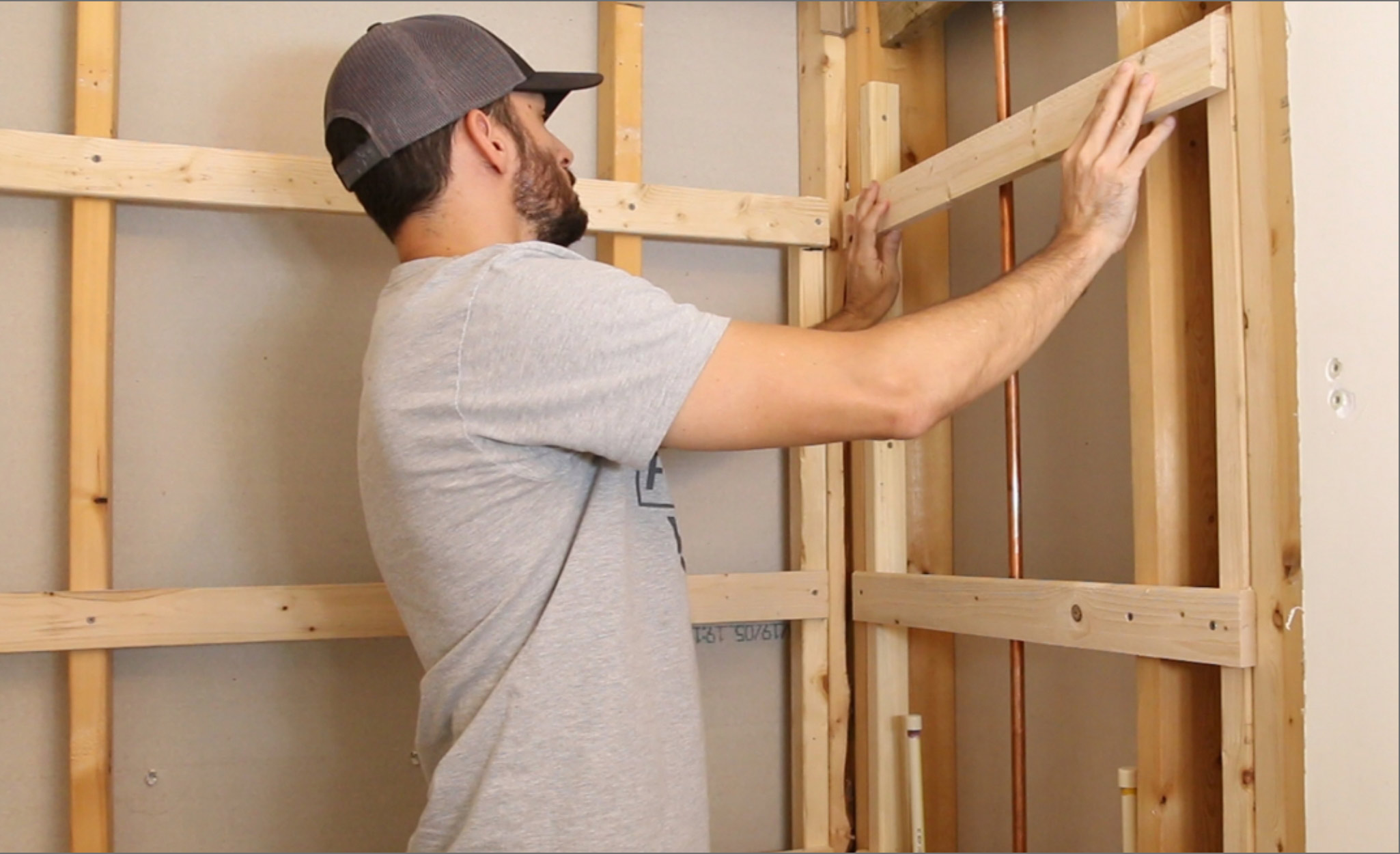
Articles
How Thick Is A Plumbing Wall
Modified: January 6, 2024
Discover the ideal thickness for plumbing walls and gain valuable insights with our comprehensive articles.
(Many of the links in this article redirect to a specific reviewed product. Your purchase of these products through affiliate links helps to generate commission for Storables.com, at no extra cost. Learn more)
Introduction
When it comes to plumbing installations, one often overlooked but crucial aspect is the thickness of plumbing walls. The thickness of plumbing walls plays a significant role in ensuring the structural integrity, durability, and safety of plumbing systems. Understanding the importance of plumbing wall thickness and the factors that influence it is essential for both homeowners and professionals in the plumbing industry.
In this article, we will delve into the world of plumbing wall thickness and explore the various factors that affect it. We will also discuss the minimum thickness requirements and the common materials used for plumbing walls. Additionally, we will highlight the potential problems that can arise from having thin walls and provide some tips for determining wall thickness.
Whether you are planning a new plumbing installation or looking to upgrade an existing one, having a solid understanding of plumbing wall thickness will enable you to make informed decisions and ensure that your plumbing system is robust and efficient.
Key Takeaways:
- Plumbing wall thickness is crucial for structural integrity, durability, and safety. Factors like material, water pressure, and building codes influence thickness, so consulting professionals and adhering to regulations is essential.
- Thin plumbing walls can lead to structural weakness, vulnerability to damage, reduced insulation, and maintenance challenges. Prioritize determining optimal wall thickness by considering material selection, load requirements, and professional guidance.
Read more: How Thick Are Glass Walls
Understanding Plumbing Walls
Plumbing walls refer to the partitions or barriers used to contain or enclose pipes, fixtures, and other components of a plumbing system. These walls serve several purposes, including providing support, protecting the plumbing system, and facilitating maintenance and repairs. Understanding the different types of plumbing walls and their components is essential for proper plumbing system design and installation.
There are various types of plumbing walls commonly used in residential and commercial buildings. The most common types include load-bearing walls, non-load-bearing walls, and wet walls.
Load-bearing walls carry the weight of the building’s structure, including the floors, walls, and roof. These walls are typically made of sturdy materials, such as concrete, brick, or solid timber, and are designed to bear the load imposed upon them. Load-bearing walls are essential for maintaining the structural integrity of the building and should not be altered or removed without professional consultation.
Non-load-bearing walls, on the other hand, do not carry any structural load and are primarily used to define the layout and structure of rooms. These walls are usually made of lighter materials, such as timber studs or metal frames, and are easier to install and modify. Non-load-bearing walls can be added, removed, or reconfigured more easily, making them ideal for flexible interior design.
Wet walls are specialized plumbing walls that house the pipes and fixtures for a specific plumbing system, such as a bathroom or kitchen. These walls are designed to conceal and protect the plumbing components while providing access for maintenance and repairs. Wet walls are often constructed using moisture-resistant materials, such as cement board or waterproof drywall, to prevent water damage.
Plumbing walls also have various components that contribute to their functionality and performance. Some of these components include insulation, vapor barriers, soundproofing materials, and access panels.
Insulation is commonly installed within plumbing walls to prevent heat loss or transfer, improving the energy efficiency of the building. Insulation also helps prevent freezing of pipes in colder climates and reduces noise transmission between rooms.
Vapor barriers are often added to plumbing walls to control the movement of moisture and prevent condensation. These barriers help maintain a dry and comfortable indoor environment, reducing the risk of mold or mildew growth.
Soundproofing materials, such as acoustic insulation or resilient channels, can be incorporated into plumbing walls to minimize the transmission of sound between rooms, providing a more peaceful and private living or working environment.
An important element of plumbing walls is access panels. These panels are strategically placed to provide convenient access to plumbing components, making maintenance, inspections, and repairs easier. Access panels should be properly installed and sealed to maintain the integrity of the plumbing system and prevent water or moisture penetration.
Understanding the different types and components of plumbing walls is crucial for designing, constructing, and maintaining an efficient and reliable plumbing system. It ensures that the system is structurally sound, adequately protected, and easily accessible for necessary maintenance and repairs.
Factors Affecting Thickness
The thickness of plumbing walls is not arbitrary; it is determined by several factors that influence the overall performance and durability of the plumbing system. These factors must be carefully considered during the design and installation process to ensure the walls are of adequate thickness.
1. Material of the Plumbing Wall:
The type of material used for the plumbing wall significantly affects its thickness. Different materials have varying strength characteristics and load-bearing capacities. For example, a concrete wall can withstand more pressure compared to a drywall partition. The material chosen should be able to support the weight of plumbing fixtures, pipes, and any potential loads imposed on the wall.
2. Water Pressure:
The water pressure within the plumbing system can put stress on the walls. Higher water pressure requires thicker walls to prevent any potential leaks or bursts. It’s essential to consider the maximum water pressure that the pipes will encounter regularly and design the walls accordingly.
3. Pipe Diameter and Material:
The size and material of the pipes within the plumbing system impact the required wall thickness. Larger diameter pipes may require thicker walls to provide sufficient support and stability. Additionally, the material of the pipes, such as copper, PVC, or galvanized steel, can affect the overall load-bearing capacity and flexibility of the system, which should be taken into account when determining wall thickness.
4. Building Codes and Regulations:
Building codes and regulations set by local authorities play a vital role in determining the minimum thickness requirements for plumbing walls. These regulations ensure that the walls meet specific safety standards and can withstand anticipated loads and pressures. It is essential to consult the relevant building codes and regulations to ensure compliance and avoid any potential legal or safety issues.
5. Location and Environmental Factors:
The location and environmental conditions of the building can impact the required wall thickness. For example, buildings in seismic zones or areas prone to hurricanes or heavy snowfall may require thicker walls to withstand the potential impact. Similarly, buildings in extremely hot or cold climates may need thicker walls to provide proper insulation and prevent pipe damage due to temperature fluctuations.
6. Future Expansion or Modifications:
Consideration should be given to potential future expansion or modifications of the plumbing system. If there is a possibility of adding additional fixtures or extending the system, it is advisable to account for these changes in the initial wall thickness design. This proactive approach ensures that the walls can accommodate future modifications without compromising their integrity or requiring major structural alterations.
By taking into account these factors, plumbing professionals can determine the appropriate thickness for the walls of a plumbing system. Ensuring the walls are of sufficient thickness helps guarantee the long-term performance, durability, and safety of the plumbing system, minimizing the risk of leaks, structural damage, and costly repairs.
Minimum Thickness Requirements
The minimum thickness requirements for plumbing walls are established by building codes and regulations to ensure the structural integrity and safety of the plumbing system. These requirements vary depending on the type of wall, location, and other factors that may influence the load-bearing capacity and durability of the wall.
1. Load-Bearing Walls:
Load-bearing plumbing walls are subjected to the weight of the building’s structure and must be able to support the imposed loads. The minimum thickness requirements for load-bearing walls are typically determined based on engineering calculations and local building codes. These requirements may also take into account the type of material used for the wall, the height of the building, and other factors related to structural stability.
2. Non-Load-Bearing Walls:
Non-load-bearing plumbing walls are primarily used for room partitioning and do not carry any structural loads. These walls can be thinner compared to load-bearing walls but must still meet the minimum thickness requirements set by building codes. The thickness requirements for non-load-bearing walls may be based on factors like fire resistance, soundproofing, and the type of material used.
3. Wet Walls:
Wet walls, which house the plumbing components for a specific system like a bathroom or kitchen, require additional considerations. The minimum thickness requirements for wet walls are often determined by plumbing codes and regulations, which aim to ensure sufficient space for pipe installation, insulation, and accessibility for maintenance and repairs. Moisture resistant materials and proper sealing techniques may also be required to prevent water damage.
It’s important to note that the minimum thickness requirements set by building codes are meant to provide a baseline for safety and compliance. Depending on specific circumstances, such as the presence of heavy fixtures or anticipated loads, it may be necessary or advisable to exceed these minimum requirements to ensure optimal performance and longevity of the plumbing walls.
When planning a plumbing installation, it is crucial to consult local building codes and regulations to ensure compliance with the minimum thickness requirements. Engaging the services of a qualified plumbing professional or consulting with an engineer can help determine the appropriate thickness for the plumbing walls while considering factors specific to the project.
By adhering to the minimum thickness requirements, plumbing professionals can ensure that the walls of a plumbing system provide the necessary support, protection, and accessibility, contributing to the overall effectiveness and safety of the plumbing installation.
The typical thickness of a plumbing wall is 4-6 inches. However, it can vary depending on the type of building and the specific plumbing requirements. Always consult a professional plumber or contractor for accurate measurements and installation.
Common Materials Used for Plumbing Walls
Choosing the right material for plumbing walls is essential to ensure durability, strength, and longevity of the plumbing system. Different materials offer varying properties and benefits, allowing for flexibility in design, installation, and maintenance. Here are some of the common materials used for plumbing walls:
1. Concrete:
Concrete is a popular choice for load-bearing plumbing walls due to its strength and durability. It can withstand significant pressure and provide excellent structural integrity. Concrete walls are typically constructed using concrete blocks or poured concrete, making them resistant to moisture, fire, and pests. They are ideal for commercial buildings or areas with higher loads or increased safety requirements.
2. Brick:
Brick walls have been used for centuries, offering a timeless appeal and excellent strength. Brick is a natural and sustainable material, providing thermal insulation and soundproofing properties. Brick walls are commonly used for both load-bearing and non-load-bearing plumbing walls, adding character and aesthetic value to residential and commercial spaces.
3. Metal Studs:
Metal studs, primarily made of steel, are lightweight and versatile, making them suitable for both load-bearing and non-load-bearing plumbing walls. They are easy to install, provide flexibility in design, and are resistant to fire, moisture, and pests. Metal studs offer advantages such as being non-combustible, termite-proof, and having better sound reduction properties compared to other materials.
4. Wood Framing:
Wood framing, often made of kiln-dried lumber, is a common choice for non-load-bearing plumbing walls. Wood is readily available, cost-effective, and easy to work with. Wood framing offers thermal insulation properties and can be used in various architectural styles. However, it is important to choose pressure-treated or moisture-resistant wood to prevent fungal growth or damage due to moisture exposure.
5. Drywall:
Drywall, also known as gypsum board or plasterboard, is frequently used for non-load-bearing plumbing walls. It is made from a layer of gypsum sandwiched between two layers of paper. Drywall is cost-effective, easy to install, and provides a smooth surface for painting or wallpapering. However, drywall is not moisture-resistant and should not be used in wet areas unless appropriate waterproofing measures are taken.
6. Cement Board:
Cement board, also called tile backer board, is a moisture-resistant material commonly used for wet walls in bathrooms or kitchens. It is made of a combination of cement and reinforcing fibers, providing excellent resistance to moisture, mold, and mildew. Cement board is an ideal substrate for tile installations and offers enhanced stability and durability in areas prone to water exposure.
When selecting the material for plumbing walls, it is essential to consider the specific requirements of the project, such as load-bearing capacity, moisture resistance, fire rating, and aesthetic preferences. Consulting with a professional plumber or contractor can help determine the most suitable material for the plumbing walls based on these factors and ensure a successful and long-lasting plumbing installation.
Read more: How Thick Is A Brick Wall
Potential Problems with Thin Walls
Having thin walls in a plumbing system can lead to various issues that can compromise its performance, durability, and safety. It is essential to understand the potential problems associated with thin walls to take necessary precautions and ensure the long-term integrity of the plumbing installation. Here are some of the common problems that can arise from having thin walls:
1. Structural Weakness:
Thin walls lack the necessary thickness to provide adequate structural support. They may not be able to withstand the weight of plumbing fixtures, pipes, and potential pressure or loads imposed on the wall. This can lead to sagging, shifting, or even collapse of the plumbing system, risking damage to the surrounding structure.
2. Increased Vulnerability to Damage:
Thin walls are more susceptible to damage from external forces, such as impact or vibration. They may crack or chip easily, leading to water leaks, pipe rupture, or even flooding. Thin walls are also less resistant to temperature fluctuations, which can cause expansion and contraction of pipes, leading to potential pipe bursts.
3. Reduced Insulation and Soundproofing:
Thinness in the walls can compromise insulation properties, affecting energy efficiency and comfort. Thin walls provide less thermal insulation, resulting in heat loss or gain, reduced energy savings, and potentially higher utility bills. Additionally, thin walls may not effectively block out noise, leading to lower levels of soundproofing between rooms.
4. Limited Space for Pipe Installation and Maintenance:
Thin walls may not provide sufficient space for proper pipe installation and maintenance access. This can make it challenging to route pipes correctly, install fittings, or perform necessary repairs and inspections. Inadequate space can increase the risk of damage to the pipes and hinder the ability to address issues efficiently.
5. Increased Risk of Leaks and Water Damage:
Thin walls are more prone to cracks, holes, or weak points, increasing the risk of water leaks. Small leaks can go unnoticed for extended periods, leading to water damage, mold growth, and structural issues. Thin walls also have less capacity to contain and redirect water from potential leaks, further exacerbating the damage caused.
6. Difficulty in Upgrades or Modifications:
Thin walls may pose challenges when upgrading or modifying the plumbing system. Adding additional fixtures or making changes to the system may be more complicated or require major structural alterations. Thin walls limit flexibility and can lead to increased project costs and disruptions to the plumbing system.
It is crucial to address these potential problems associated with thin walls by ensuring proper wall thickness during the initial design and construction stages. Working with qualified professionals and following building codes and regulations can help mitigate these issues and ensure a robust and reliable plumbing system.
By avoiding thin walls and opting for appropriate wall thickness, the plumbing system can maintain its structural integrity, resist damage, improve energy efficiency, and minimize the risk of costly repairs or disruptions in the future.
Tips for Determining Wall Thickness
Determining the appropriate wall thickness for plumbing systems is crucial to ensure their performance, durability, and safety. While there are specific factors to consider, here are some tips to help you determine the optimal wall thickness:
1. Consult Building Codes and Regulations:
Building codes and regulations provide guidelines and minimum requirements for wall thickness based on factors such as load-bearing capacity, water pressure, and material specifications. Consult the relevant codes and regulations to ensure compliance and to get a foundation for determining the appropriate wall thickness.
2. Assess Project Scope and Load Requirements:
Evaluate the project’s scope and the anticipated loads the plumbing system will bear. Consider factors such as the number of fixtures, water pressure, and any potential future modifications. This assessment will help determine the minimum thickness requirements and if additional thickness is needed to accommodate the specific project requirements.
3. Consider Material Selection:
The choice of material greatly influences wall thickness. Different materials have varying load-bearing capacities and strength characteristics. Determine the material best suited for your plumbing system, considering factors such as structural demands, water resistance, and fire rating. Consult professionals or industry experts to identify the most suitable material for your specific needs.
4. Engage Professional Guidance:
Seek the advice of experienced plumbers, contractors, or engineers who specialize in plumbing installation and design. Professionals can provide valuable insights based on their expertise and experience, helping you determine the optimal wall thickness based on project requirements, local regulations, and industry best practices.
5. Conduct Structural Analysis:
If the plumbing system involves significant structural loads or unique challenges, consider engaging a structural engineer to perform a thorough analysis. This analysis assesses factors such as static and dynamic loads, seismic considerations, and potential impacts from nearby structures. The engineer will provide recommendations and determine the appropriate wall thickness based on the analysis.
6. Prioritize Accessibility and Maintenance:
Ensure there is sufficient space within the walls for pipe installation, maintenance access, and potential repairs. Adequate accessibility reduces the likelihood of damage during installation, facilitates troubleshooting, and allows for routine upkeep. Plan for access panels or other means of easy access to the plumbing components, taking into account the thickness required to accommodate these features.
7. Seek Multiple Opinions:
When determining wall thickness, it’s valuable to consult multiple professionals or experts in the field. Different perspectives can provide additional insights and help validate your decision-making process. Engaging with experts from different disciplines, such as plumbing, structural engineering, and architecture, can provide a well-rounded perspective on wall thickness requirements.
By following these tips, you can make informed decisions about the appropriate wall thickness for your plumbing system. Taking into account local regulations, project scope, material selection, and professional advice will ensure a robust and reliable plumbing installation that meets safety standards and performs optimally for years to come.
Conclusion
Understanding the importance of plumbing wall thickness is essential for ensuring the integrity, durability, and safety of plumbing systems. By considering factors such as material selection, load requirements, and compliance with building codes and regulations, you can determine the optimal wall thickness for your plumbing installation.
Thin walls can lead to various problems, including structural weakness, increased vulnerability to damage, reduced insulation and soundproofing, limited space for maintenance access, and an increased risk of leaks and water damage. It is crucial to avoid these issues by choosing the appropriate wall thickness and material for your specific needs.
Consulting with professionals in the plumbing industry, including plumbers, contractors, engineers, and architects, can provide valuable insights and ensure compliance with relevant regulations and best practices. Their expertise can help you navigate the complexities of determining wall thickness and make informed decisions that enhance the performance and longevity of your plumbing system.
By prioritizing wall thickness and considering factors such as load-bearing capacity, water pressure, material selection, and accessibility for maintenance, you can mitigate potential problems and create a robust plumbing installation. Taking a proactive approach to wall thickness will contribute to the efficiency, reliability, and safety of your plumbing system, ultimately providing peace of mind for homeowners and ensuring the smooth operation of commercial and residential buildings.
Remember, plumbing wall thickness is not an aspect to overlook. By investing time and effort in determining the appropriate thickness, you are laying a solid foundation for a plumbing system that will serve you well for years to come.
Frequently Asked Questions about How Thick Is A Plumbing Wall
Was this page helpful?
At Storables.com, we guarantee accurate and reliable information. Our content, validated by Expert Board Contributors, is crafted following stringent Editorial Policies. We're committed to providing you with well-researched, expert-backed insights for all your informational needs.
0 thoughts on “How Thick Is A Plumbing Wall”