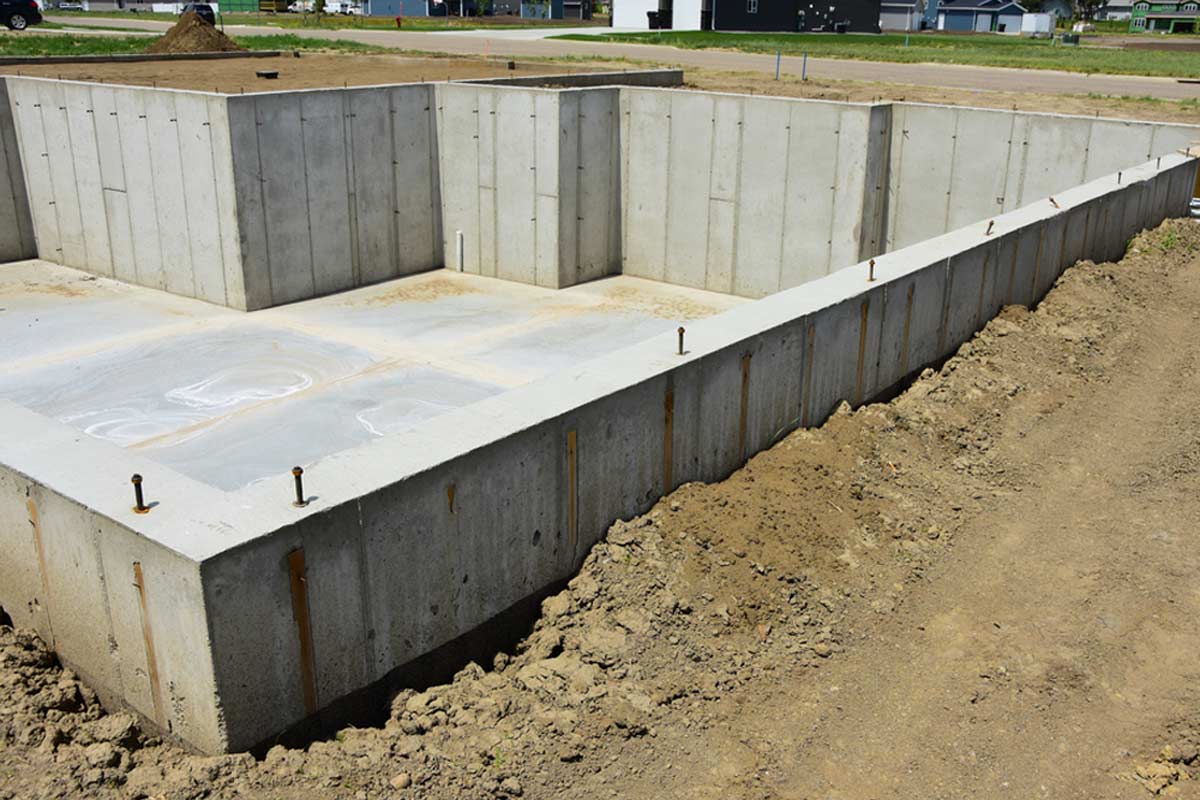
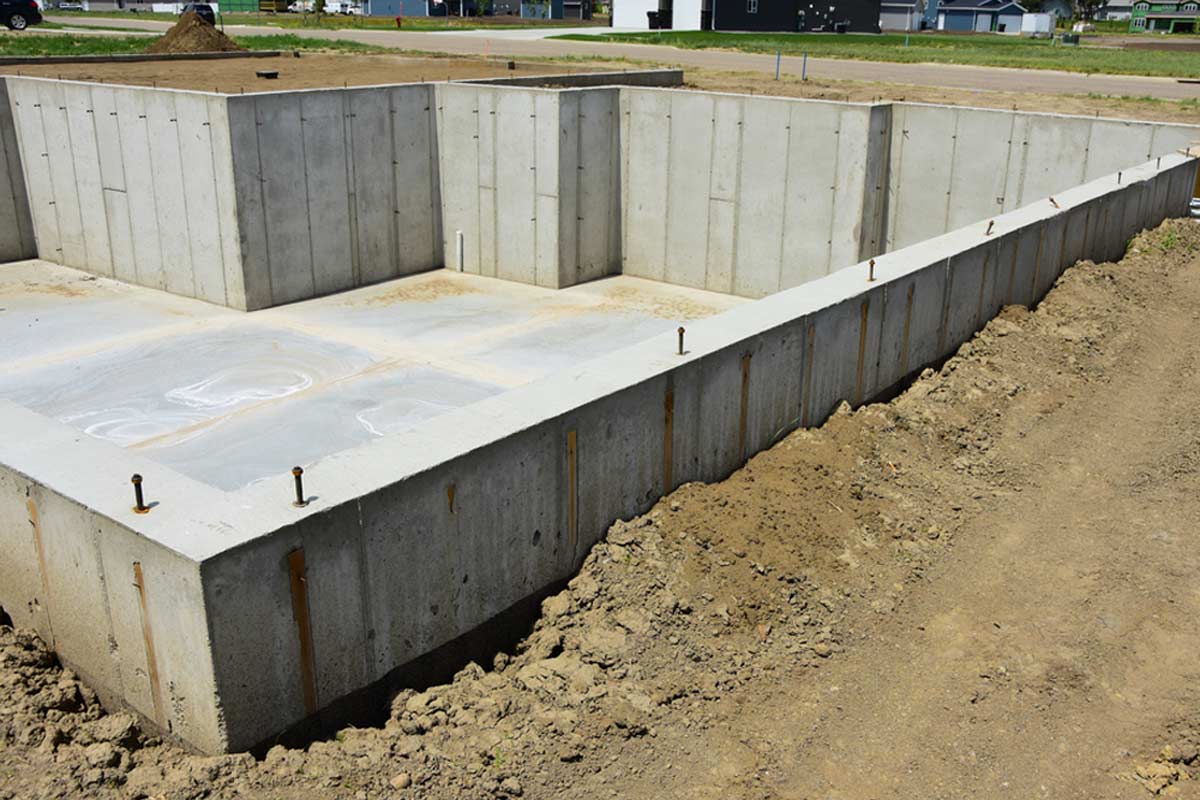
Articles
How Thick Are Poured Basement Walls
Modified: December 7, 2023
Discover the ideal thickness of poured basement walls in our informative articles. Find out how to ensure durability and strength for your construction projects.
(Many of the links in this article redirect to a specific reviewed product. Your purchase of these products through affiliate links helps to generate commission for Storables.com, at no extra cost. Learn more)
Introduction
When it comes to constructing a durable and structurally sound basement, the thickness of poured basement walls plays a crucial role. Basement walls are responsible for providing support to the entire structure above and protecting the interior from moisture intrusion. Therefore, understanding the factors that affect the thickness of these walls is essential for ensuring a solid foundation for any building.
The thickness of poured basement walls depends on several factors, including the construction materials, building codes and regulations, and specific requirements of the project. By adhering to these guidelines, builders can create a basement that is strong, reliable, and meets the necessary standards.
In this article, we will explore the factors that affect the thickness of poured basement walls, the regulations stipulated by building codes, and the options available for different project requirements. Additionally, we will discuss the importance of reinforcement and structural integrity, as well as consider the considerations for insulation and waterproofing. Lastly, we will weigh the benefits and drawbacks of opting for thicker basement walls, helping you make an informed decision for your construction project.
Key Takeaways:
- The thickness of poured basement walls is influenced by soil conditions, building height, water table levels, and building codes. Thicker walls offer increased strength and protection but come with higher construction costs and design limitations.
- Proper reinforcement, insulation, and waterproofing are crucial for durable and energy-efficient basement walls. Collaboration with experts and adherence to building codes ensure a stable and protected foundation for any building.
Read more: How Thick Is Basement Concrete Floor
Factors Affecting Thickness of Poured Basement Walls
The thickness of poured basement walls is determined by several factors that are crucial for maintaining the structural integrity and longevity of the building. Understanding these factors is essential for builders, as it enables them to construct a basement that meets the specific requirements and ensures the safety of the structure.
1. Soil Conditions: The type and condition of the soil surrounding the basement play a significant role in determining the thickness of the walls. If the soil has poor stability or high water content, thicker walls may be required to resist external pressure and prevent any potential damage.
2. Building Height: The height of the building above the basement also influences the thickness of the walls. Taller structures exert more load on the foundation, requiring additional wall thickness to bear the weight and distribute the load evenly.
3. Water Table Level: The level of the water table in the area where the building is constructed can impact the thickness of the basement walls. Areas with a high water table may require thicker walls to prevent water infiltration and protect the basement from water damage.
4. Building Codes and Regulations: Building codes and regulations provide specific guidelines for the minimum required thickness of poured basement walls. These codes ensure that the walls can withstand the expected loads and meet safety standards. Compliance with these regulations is essential to ensure the structural integrity of the building.
5. Type of Construction Materials: The type of materials used in the construction of the basement walls can impact their thickness. Different materials have different load-bearing capacities and strength properties, which may require adjustments in thickness to ensure structural stability.
6. Adjacent Structures: If the building is located near existing structures, the proximity may influence the thickness of the basement walls. The walls need to be thick enough to prevent any potential damage to neighboring properties and maintain the safety of the site.
7. Use of Basement Space: The intended use of the basement space also affects the thickness of the walls. If the basement will be utilized for storage, recreational purposes, or as habitable living space, additional thickness may be necessary to provide proper insulation, soundproofing, and fire resistance.
By considering all these factors, builders can determine the ideal thickness for the poured basement walls and ensure the stability, durability, and safety of the structure. It is essential to consult with structural engineers and adhere to building codes and regulations to meet the required standards for construction.
Building Codes and Regulations
Building codes and regulations play a critical role in the construction industry by establishing minimum standards for the design, construction, and maintenance of buildings. These codes are developed and enforced by local, state, and national authorities to ensure the safety, health, and welfare of the public. When it comes to determining the thickness of poured basement walls, builders must adhere to the guidelines set forth by these codes and regulations.
Building codes typically provide specific requirements for the minimum thickness of poured basement walls based on various factors such as the type of construction, the height of the building, and the specific use of the basement space. These requirements are designed to ensure that the walls are strong enough to withstand anticipated loads, resist external pressures, and provide adequate protection against environmental elements, such as water intrusion.
The International Building Code (IBC) is one of the most widely adopted codes in the United States. It provides comprehensive guidelines for the construction of buildings, including specifications for foundation walls. According to the IBC, the minimum thickness of poured basement walls should be determined based on factors such as the type of soil, the height of the structure, and the intended use of the basement space.
In addition to the IBC, local building departments may have additional requirements, known as amendments, that builders must comply with. These amendments are tailored to address specific local conditions and considerations. Therefore, it is crucial for builders to review and understand the building codes and regulations of the specific jurisdiction where the construction project is taking place.
To ensure compliance with building codes and regulations, it is recommended to work with a qualified structural engineer or design professional. These experts have a deep understanding of the applicable codes and can provide guidance on the appropriate thickness of poured basement walls based on the specific project requirements. By working closely with professionals and following building codes, builders can ensure the safety, durability, and legal compliance of the constructed basement walls.
It is essential to note that building codes and regulations are subject to periodic updates and revisions. Therefore, it is crucial to stay updated and informed about any changes that may impact the design and construction of poured basement walls. Consulting with local building authorities and industry professionals will help ensure that the construction project is up to date with the latest codes and regulations.
Common Thickness Options
When it comes to poured basement walls, there are several common thickness options that builders can choose from based on the specific project requirements and local building codes. These options provide a range of wall thicknesses to ensure structural integrity, stability, and resistance to external pressures. Here are some of the common thickness options for poured basement walls:
1. 8 inches: An 8-inch thick poured basement wall is one of the most common options for residential construction. It provides adequate strength and stability in most cases and meets the minimum thickness requirements of many building codes. This thickness is suitable for low-rise structures and basements that will be used for general storage or recreational purposes.
2. 10 inches: A 10-inch thick poured basement wall offers increased structural strength and is often used for taller buildings or areas with unstable soil conditions. This thickness provides extra stability and resistance to external pressures, making it more suitable for buildings with multiple stories or large loads.
3. 12 inches: A 12-inch thick poured basement wall is considered a heavy-duty option and is commonly used for commercial and industrial buildings. This thickness provides maximum strength and can withstand higher loads and pressures. It is often required for structures with high water tables or significant lateral forces.
It is important to note that these thickness options are general guidelines, and the specific requirements may vary depending on factors such as the building height, soil conditions, and local building codes. It is crucial to consult with a structural engineer or design professional to determine the appropriate thickness based on the specific project parameters.
In addition to the primary thickness of the basement walls, allowances should also be made for additional layers of insulation, waterproofing membranes, and reinforcement materials. These elements not only provide thermal efficiency and moisture protection but also add to the overall thickness of the basement walls.
It should be noted that using thicker basement walls will increase the overall cost of the construction project due to the additional materials and labor involved. Therefore, it is important to carefully consider the structural requirements, soil conditions, and building codes to determine the most appropriate thickness option that balances cost-effectiveness and structural integrity.
By selecting the right thickness for poured basement walls, builders can ensure the stability, safety, and durability of the structure while complying with the relevant building codes and regulations.
Factors to Consider When Determining Thickness
Determining the appropriate thickness for poured basement walls is a crucial step in ensuring the structural integrity and longevity of the building. Several factors need to be taken into consideration to determine the optimal wall thickness. By considering these factors, builders can make informed decisions and construct basements that meet the specific requirements of the project. Here are some important factors to consider when determining the thickness of poured basement walls:
1. Soil Conditions: The type and stability of the soil surrounding the basement play a significant role in determining wall thickness. Soil conditions that are prone to settlement, expansive clay, or high water content may require thicker walls to provide adequate support and prevent potential damage.
2. Building Height: The height of the building above the basement affects the load and pressure exerted on the walls. Taller buildings typically require thicker walls to withstand the increased load and provide sufficient structural support throughout the height of the structure.
3. Adjacent Structures: If the building is located near existing structures, it is important to consider their proximity when determining wall thickness. Thicker walls may be necessary to minimize the risk of damage to neighboring properties and ensure the safety of the entire site.
4. Water Table Level: The level of the water table in the area can impact the thickness of basement walls. Higher water tables may require thicker walls to prevent water infiltration and protect against hydrostatic pressure.
5. Building Codes and Regulations: Compliance with local building codes and regulations is essential. These codes provide minimum requirements for wall thickness to ensure the safety and structural integrity of the building. Familiarize yourself with the specific codes applicable to your area and incorporate them into your decision-making process.
6. Intended Use of the Basement: Consider how the basement space will be used to determine the required wall thickness. If the basement will be utilized for habitable living space, additional thickness may be needed to provide proper insulation, soundproofing, and fire protection.
7. Structural Stability: Evaluate the structural requirements of the building. This includes considering factors such as wind loads, seismic activity, and anticipated forces on the walls. Thicker walls may be necessary to provide the necessary strength and stability under these conditions.
8. Budget and Cost Considerations: While thickness is important for structural integrity, it is also essential to consider budget constraints. Thicker walls generally require more materials and labor, which can increase construction costs. Striking a balance between structural requirements and budget limitations is crucial.
By carefully assessing these factors and consulting with structural engineers or design professionals, builders can determine the optimal thickness for poured basement walls. This ensures the walls can withstand anticipated loads, provide the necessary structural support, and comply with building codes and regulations.
Poured basement walls are typically 8 to 10 inches thick, but can be thicker for added strength or in areas with high water tables. Always consult local building codes for specific requirements.
Read more: How Thick Is A Brick Wall
Reinforcement and Structural Integrity
Ensuring the reinforcement and structural integrity of poured basement walls is essential for creating a strong and durable foundation. Reinforcement materials, such as steel rebar or fiber reinforcement, are commonly used to enhance the strength and stability of the walls. These reinforcements help distribute the loads and reinforce the concrete, preventing cracking and structural failure. Here are some key considerations regarding reinforcement and structural integrity for poured basement walls:
1. Reinforcement Materials: Steel rebar is the most commonly used reinforcement material for poured basement walls. These steel bars are placed within the forms or molds before pouring the concrete. The rebar adds tensile strength to the walls, enhancing their ability to resist external forces. Fiber reinforcement is an alternative option that incorporates synthetic fibers, such as polypropylene or glass, into the concrete mix. Fiber reinforcement can provide additional crack control and improve the overall durability of the walls.
2. Placement and Spacing: The placement and spacing of reinforcement materials are crucial in ensuring their effectiveness. The rebar or fiber reinforcement should be evenly distributed throughout the entire wall and adequately spaced to provide sufficient support and resistance to bending forces.
3. Design Considerations: The design of the reinforcement system should be based on the specific structural requirements and anticipated loads. This includes factors such as the height of the walls, soil conditions, and any other external forces that the walls may experience. Consultation with a structural engineer is crucial to determine the appropriate reinforcement design for the specific project.
4. Reinforcement Cover: The reinforcement materials should be adequately covered by the concrete to protect them from corrosion and provide the necessary bond with the concrete. The cover thickness should meet the requirements specified by building codes and regulations to ensure the longevity and performance of the reinforcement system.
5. Construction Techniques: Proper construction techniques are crucial in maintaining the integrity of the reinforcement and the overall quality of the poured basement walls. Adequate consolidation and compaction of the concrete, as well as proper curing methods, are essential to minimize the risk of voids, shrinkage, and other potential issues that could compromise the structural integrity of the walls.
By incorporating appropriate reinforcement materials, following proper design protocols, and employing effective construction techniques, builders can ensure the structural integrity and stability of poured basement walls. These measures provide the necessary strength and durability to withstand anticipated loads, resist external pressures, and maintain the long-term stability of the entire structure.
Insulation and Waterproofing Considerations
Insulation and waterproofing are essential considerations when it comes to poured basement walls. These aspects play a crucial role in ensuring energy efficiency, preventing moisture intrusion, and maintaining a comfortable and dry environment within the basement space. Here are some important factors to consider when it comes to insulation and waterproofing for poured basement walls:
1. Insulation: Proper insulation is key to enhancing energy efficiency and minimizing heat loss or gain through the basement walls. Insulating the walls helps regulate the indoor temperature, reduce energy consumption, and provide a more comfortable living environment. Common insulation materials used for basement walls include foam boards, spray foam insulation, or rigid foam insulation. The thickness and type of insulation will depend on factors such as local climate, budget, and specific project requirements.
2. Vapor Barrier: A vapor barrier, also known as a moisture barrier or vapor retarder, helps prevent the transmission of moisture from the soil into the basement walls. This barrier is typically installed on the exterior side of the basement walls before backfilling. It prevents moisture infiltration and protects the insulation and interior finishes from water damage, mold, and mildew growth.
3. Waterproofing: Waterproofing is crucial to protect the basement space from water penetration and potential water damage. A variety of waterproofing techniques and materials can be used, such as waterproofing membranes and coatings, drainage systems, and sump pumps. These measures help divert and manage water away from the foundation, ensuring a dry and water-free basement environment.
4. Condensation Management: Condensation can be a concern within basement spaces. Proper insulation and ventilation measures can help manage condensation by reducing moisture buildup and minimizing the risk of mold and mildew growth. Adequate ventilation systems, such as vents or exhaust fans, can help remove excess moisture and maintain optimal air quality within the basement.
5. Sealing and Caulking: Ensuring proper sealing and caulking around windows, doors, utility penetrations, and any other openings in the basement walls is essential to prevent air and water leakage. These openings can be potential entry points for moisture, drafts, and pests. Sealing and caulking them properly helps maintain the integrity of the insulation and waterproofing systems.
It is crucial to consider local building codes and regulations when implementing insulation and waterproofing measures for poured basement walls. Compliance with these requirements ensures that the insulation and waterproofing systems meet the necessary standards for efficiency, safety, and performance.
Consulting with professionals experienced in insulation and waterproofing systems is highly recommended. These experts can provide guidance on the most suitable materials, techniques, and thicknesses for insulation and waterproofing, ensuring the longevity, comfort, and protection of the basement space.
Benefits and Drawbacks of Thicker Walls
Thicker walls for poured basements have both benefits and drawbacks. Builders should carefully evaluate these factors when determining the appropriate wall thickness for their construction projects. Here are some of the benefits and drawbacks associated with thicker basement walls:
Benefits:
- Increased Structural Strength: Thicker walls provide increased structural strength, making them better able to withstand external pressures and loads. They are more resistant to cracking, bending, and other types of damage, resulting in a more solid and durable foundation.
- Enhanced Protection: Thicker walls offer better protection against potential issues such as water infiltration, moisture damage, and soil movement. They can better resist hydrostatic pressure and provide a stronger barrier against moisture intrusion, ensuring a dry and safe basement environment.
- Improved Insulation: Thicker walls allow for more space to incorporate insulation. This enhances energy efficiency by minimizing heat loss or gain. Proper insulation helps maintain a comfortable temperature within the basement, reduces energy consumption, and lowers utility costs.
- Soundproofing: Thicker walls can provide better sound insulation, reducing sound transmission between different areas of the basement and the rest of the building. This can contribute to a more peaceful and private living or working environment.
Drawbacks:
- Increased Construction Costs: Thicker walls require more materials and more labor, resulting in higher construction costs. The additional expenses associated with thicker walls should be carefully considered within the overall project budget.
- Reduced Usable Space: Thicker walls can result in a reduction of usable space within the basement. The added thickness reduces the interior dimensions, potentially limiting the available square footage for storage, living, or recreational purposes.
- More Excavation and Backfilling: Thicker walls require more extensive excavation and backfilling during the construction process. This additional work can increase project timelines and costs, especially if there are challenging soil conditions or site constraints.
- Design Limitations: Thicker walls may have design limitations, especially when it comes to architectural details such as window openings, door frames, or structural connections. The increased thickness can impact the overall aesthetic and design flexibility of the basement space.
Based on project requirements, budget constraints, and specific site conditions, builders should carefully weigh the benefits and drawbacks of thicker walls to make an informed decision. It is advisable to consult with a structural engineer or design professional to ensure the selected wall thickness aligns with structural requirements, local building codes, and overall project objectives.
Conclusion
Determining the appropriate thickness for poured basement walls is a critical aspect of creating a structurally sound and durable foundation. By considering various factors such as soil conditions, building height, and local building codes, builders can make informed decisions that ensure the stability, safety, and longevity of the structure. Thicker walls offer benefits such as increased structural strength, enhanced protection against water intrusion and moisture damage, improved insulation, and soundproofing. However, they also come with drawbacks, including higher construction costs, reduced usable space, and design limitations. Finding the right balance between these factors is essential when determining the ideal wall thickness.
Builders must also consider reinforcement and structural integrity, insulation, and waterproofing when constructing poured basement walls. Proper reinforcement materials and placement, as well as attention to insulation and waterproofing measures, contribute significantly to the overall strength, energy efficiency, and protection of the basement space. Compliance with local building codes and regulations ensures that the constructed walls meet the required standards for safety, performance, and functionality.
Collaborating with structural engineers and design professionals is highly recommended. Their expertise and knowledge can guide builders in making informed decisions throughout the construction process, from determining the optimal wall thickness to implementing proper reinforcement, insulation, and waterproofing techniques. By carefully considering these factors and collaborating with experts, builders can ensure the successful construction of poured basement walls that offer long-lasting stability, protection, and comfort.
In conclusion, poured basement walls are a critical component of any building’s foundation. Taking into account factors such as soil conditions, building height, and local building codes is essential when determining the appropriate thickness. Additionally, ensuring reinforcement and structural integrity, as well as implementing proper insulation and waterproofing measures, is crucial for creating a structurally sound and energy-efficient basement space. By incorporating these considerations, builders can construct poured basement walls that provide a solid foundation for the entire structure, offering durability, long-term stability, and a comfortable and protected environment.
Frequently Asked Questions about How Thick Are Poured Basement Walls
Was this page helpful?
At Storables.com, we guarantee accurate and reliable information. Our content, validated by Expert Board Contributors, is crafted following stringent Editorial Policies. We're committed to providing you with well-researched, expert-backed insights for all your informational needs.
0 thoughts on “How Thick Are Poured Basement Walls”