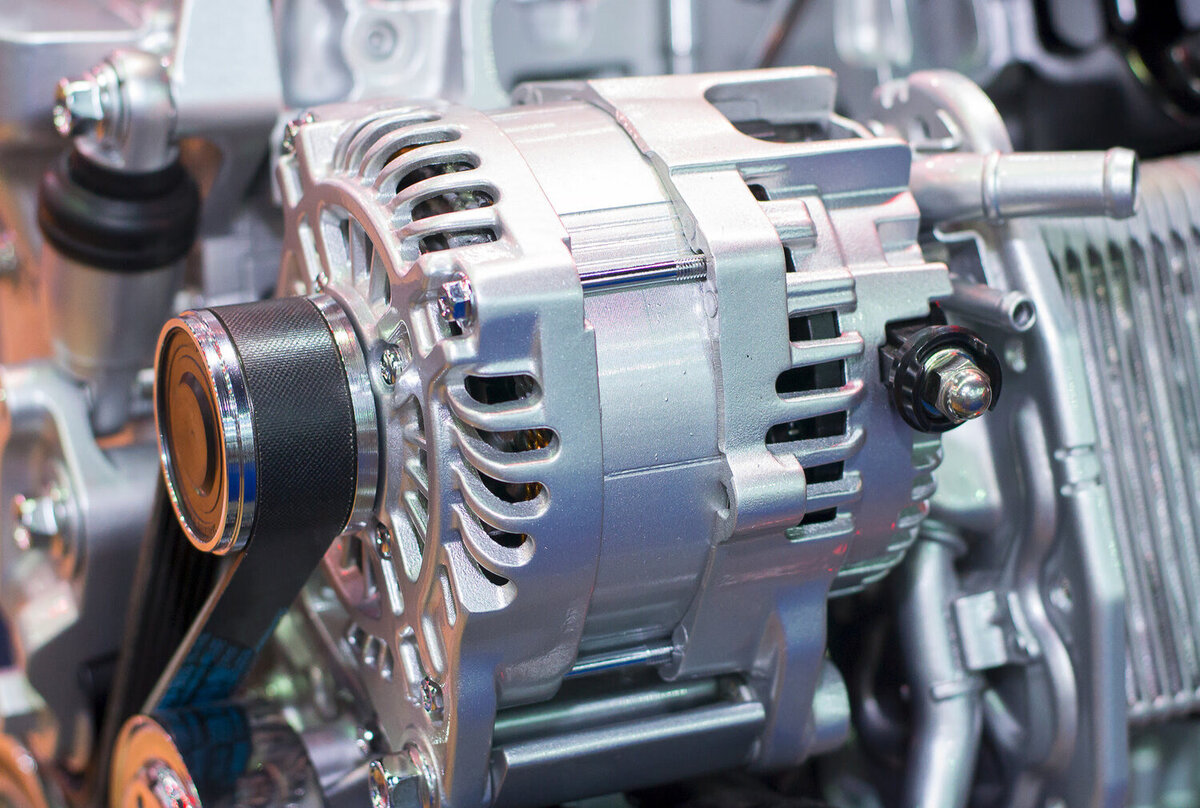
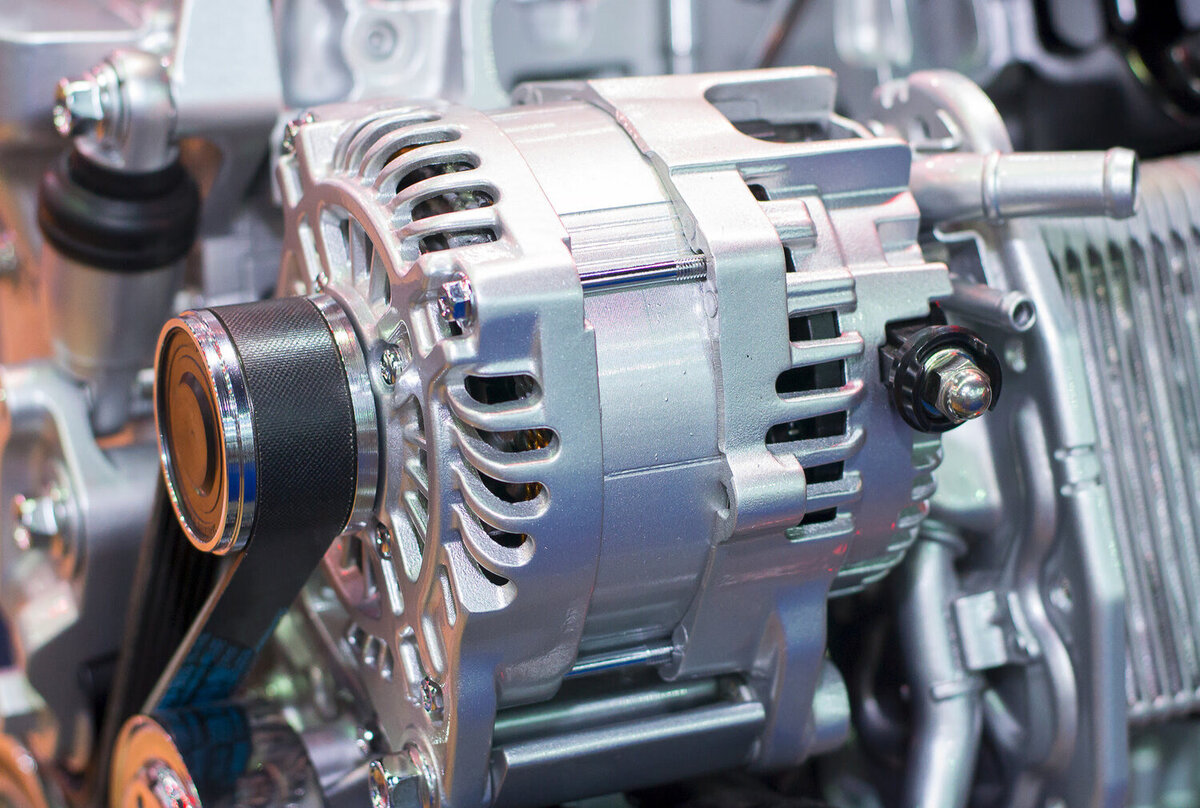
Articles
How To Reduce Electric Motor Noise
Modified: January 9, 2024
Learn effective strategies and techniques to reduce electric motor noise with these informative articles. Enhance your understanding and find practical solutions to minimize noise levels.
(Many of the links in this article redirect to a specific reviewed product. Your purchase of these products through affiliate links helps to generate commission for Storables.com, at no extra cost. Learn more)
Introduction
Electric motors are a vital component in various industries, powering everything from machinery to appliances. However, one common issue that arises with electric motors is noise. Motor noise can be disruptive, annoying, and can even indicate underlying problems with the motor’s function. In this article, we will explore the causes of electric motor noise and provide strategies to reduce it.
Understanding the factors that contribute to motor noise is crucial in finding effective solutions. By diagnosing and addressing the root causes, you can not only reduce noise but also improve the overall efficiency and longevity of your electric motors.
In the following sections, we will discuss the various causes of electric motor noise, how to determine the source of the noise, and strategies to minimize and control it. Let’s dive in!
Key Takeaways:
- Addressing the root causes of electric motor noise, such as vibrations, electromagnetic forces, and inadequate maintenance, can significantly reduce noise levels and improve operational efficiency.
- Implementing strategies like vibration isolation, noise enclosure, and proper lubrication can create a quieter working environment, enhance motor performance, and prolong its lifespan.
Read more: How To Reduce The Speed Of An Electric Motor
Understanding Electric Motor Noise
Electric motor noise refers to the sound produced by the operation of electric motors. This noise can range from a low hum to a high-pitched whine, depending on the type of motor and its specific characteristics. Understanding the factors that contribute to motor noise is essential in effectively addressing and reducing it.
There are several key factors that influence electric motor noise:
- Mechanical Components: The physical components of the motor, such as the rotor and stator, can generate noise when they interact or vibrate during operation.
- Electromagnetic Forces: Electric motors rely on electromagnetic forces to generate rotational motion. These forces can produce vibrations and audible noise.
- Airflow and Cooling: Motors that require cooling often have fans or other mechanisms to circulate air. The movement of air can contribute to noise generation.
- External Factors: Environmental conditions, such as temperature and humidity, can affect the operation of electric motors and contribute to noise.
It’s important to note that some level of noise is inherent in the operation of electric motors. However, excessive noise can be an indication of underlying issues that may require attention.
By understanding the causes of electric motor noise, you can better identify the source of the problem and take appropriate measures to reduce or eliminate it.
Causes of Electric Motor Noise
Electric motor noise can have various causes, each contributing to different types and levels of noise. Identifying the specific cause of the noise is crucial in implementing effective solutions to reduce or eliminate it. Let’s explore some common causes of electric motor noise:
- Vibrations: Vibrations are a significant source of motor noise. These vibrations can originate from imbalances in the rotor or other mechanical components, misalignment, or worn bearings.
- Electromagnetic Forces: The operation of electric motors involves the creation of electromagnetic fields and forces. These forces can lead to mechanical vibrations and noise, especially if there are uneven magnetic fields or interactions between the rotor and stator.
- Airflow and Cooling: Motors with cooling systems, such as fans or vents, can generate noise as the airflow creates turbulence. Unusual or excessive noise from the cooling system may indicate issues with fan balance or obstructions in the airflow.
- Mechanical Friction: Friction between moving parts, such as bearings and shafts, can cause noise. This friction may result from inadequate lubrication, worn or damaged components, or misalignment.
- Eccentricity: Eccentricity refers to an imbalance in the rotation of the rotor. This imbalance can result in vibration and noise during operation.
- Electrical Noise: Electrical noise can be transmitted from the power supply or other electrical equipment to the motor, leading to audible noise. This can be caused by improper grounding, electromagnetic interference, or faulty electrical components.
It’s important to note that these causes are not mutually exclusive, and multiple factors can contribute to motor noise simultaneously. Proper diagnosis and identification of the specific causes are essential in implementing effective noise reduction strategies.
In the next section, we will discuss how to determine the source of electric motor noise, which is a crucial step in developing an effective noise reduction plan.
Determining the Source of Motor Noise
Before implementing any noise reduction strategies, it is important to accurately determine the source of the motor noise. Identifying the root cause will allow you to target specific areas for improvement and implement the most effective solutions. Here are some steps to help you determine the source of motor noise:
- Inspect the Motor: Start by visually inspecting the motor for any obvious signs of damage or loose components. Look for any loose screws, bolts, or connections that could be causing vibrations or noise.
- Listen and Observe: Run the motor and listen carefully to the noise it produces. Pay attention to the type of noise (e.g., humming, grinding, rattling) and its intensity. Take note of any specific conditions or actions that seem to exacerbate or alleviate the noise.
- Isolate the Noise: Use your senses to try to pinpoint the exact location of the noise. Use your hand to touch different parts of the motor while it is running (be cautious of moving parts). Listen for changes in noise intensity as you touch different areas. This can help identify the specific component or area responsible for the noise.
- Perform Diagnostic Tests: If the source of the noise is not immediately apparent, you may need to conduct further diagnostic tests. These tests can include vibration analysis, thermal imaging, or current and voltage analysis. These tests can help identify abnormalities and potential causes of the noise.
- Consult an Expert: If you’re unable to determine the source of the motor noise or if the noise indicates a more serious issue, it is advisable to consult a professional or an electric motor expert. They can provide specialized knowledge and equipment to accurately diagnose the problem and recommend appropriate solutions.
By carefully assessing and identifying the source of motor noise, you can take targeted measures to address the underlying issues and minimize or eliminate the noise.
In the next section, we will explore various strategies to reduce electric motor noise, allowing for quieter and more efficient motor operation.
Strategies to Reduce Electric Motor Noise
Reducing electric motor noise is crucial to create a quieter and more comfortable working environment while maintaining efficient operation. Here are several strategies you can implement to minimize motor noise:
- Vibration Isolation: Use vibration isolation mounts or pads to reduce the transfer of vibrations from the motor to surrounding structures. These mounts absorb the vibrations and prevent them from causing noise.
- Noise Enclosure or Soundproofing: Constructing a noise enclosure or using soundproofing materials around the motor can help contain and dampen the noise. These measures create a physical barrier that prevents noise from spreading and minimizes its impact.
- Balancing and Alignment: Properly balance the motor rotor and ensure alignment of all components. Imbalances or misalignments can result in vibrations and noise during operation. Regular maintenance and adjustment can help minimize these issues.
- Lubrication and Maintenance: Adequate lubrication of bearings and other moving parts is essential for reducing friction and noise. Regularly inspect and maintain the motor to ensure smooth operation and minimize noise due to mechanical wear and tear.
- Electrical Filtering and Grounding: Install appropriate electrical filters and grounding techniques to minimize electrical noise that can be transmitted to the motor. Good grounding helps reduce electromagnetic interference and eliminates noise caused by electrical faults.
- Using Anti-Vibration Mounts: Install anti-vibration mounts on the motor and any auxiliary equipment to further isolate and absorb vibrations. These mounts reduce the transmission of vibrations and minimize noise.
- Noise Damping Materials: Apply noise-damping materials, such as foam or rubber, to the motor or surrounding components. These materials absorb sound waves and reduce noise propagation.
It is important to note that the effectiveness of each strategy may vary depending on the specific motor and noise characteristics. It may be necessary to combine multiple approaches or consult with experts to find the most appropriate solutions for your specific situation.
Implementing these strategies can significantly reduce motor noise, increase workplace comfort, and improve overall operational efficiency.
Now that we have explored the various strategies, we can conclude our discussion.
Read more: How To Reduce HVAC Noise
Vibration Isolation
Vibration isolation is an effective strategy to reduce electric motor noise by minimizing the transmission of vibrations from the motor to surrounding structures. By isolating the motor and preventing vibrations from propagating, you can significantly reduce the noise produced during motor operation.
There are several methods you can employ to achieve vibration isolation:
- Vibration Isolation Mounts: These specialized mounts are designed to absorb and dampen vibrations. They are typically made of rubber or other resilient materials that can effectively isolate the motor from the surrounding environment. Vibration isolation mounts are available in various designs and sizes to suit different motor applications.
- Vibration Isolation Pads: Similar to mounts, vibration isolation pads are made of resilient materials that absorb vibrations. These pads can be placed between the motor and its mounting surface to minimize the transfer of vibrations.
- Damped Motor Mounting Systems: Some motors come equipped with built-in vibration isolation systems. These systems utilize damping techniques, such as viscoelastic materials or special mounting designs, to absorb and dissipate vibrations.
When implementing vibration isolation measures, it is important to consider the specific requirements of your motor and its application. Factors such as motor size, weight, and operating conditions will determine the most suitable vibration isolation solution.
To ensure effective vibration isolation, follow these steps:
- Identify the vibration source: Determine the specific component or area of the motor that is generating the vibrations.
- Choose appropriate isolation mounts or pads: Select vibration isolation mounts or pads that are designed to handle the weight and vibrations of your motor.
- Proper installation: Follow the manufacturer’s guidelines for installing the vibration isolation mounts or pads. Ensure that they are securely attached and properly aligned.
- Inspect and maintain: Regularly inspect the mounts or pads to ensure they are in good condition. Replace worn or damaged mounts to maintain optimal vibration isolation.
Vibration isolation can greatly reduce motor noise and minimize the impact of vibrations on surrounding structures. By implementing this strategy, you can create a quieter work environment while promoting the longevity and efficient operation of your electric motor.
Noise Enclosure or Soundproofing
Another effective strategy for reducing electric motor noise is through the use of a noise enclosure or soundproofing techniques. This approach involves creating a physical barrier around the motor to contain and dampen the noise it generates.
Here are some methods to implement noise enclosure or soundproofing:
- Enclosure: Constructing a noise enclosure around the motor can help to contain the noise and prevent it from spreading to the surrounding area. The enclosure can be made of sound-absorbing materials such as acoustic panels or insulation boards. Ensure that the enclosure has sufficient ventilation to prevent overheating of the motor.
- Soundproofing Materials: Apply sound-absorbing materials to the interior surfaces of the enclosure, such as foam or mass-loaded vinyl. These materials absorb sound waves and reduce noise propagation.
- Sealing: Ensure that the noise enclosure is properly sealed to prevent sound leakage. Use weatherstripping or gaskets to seal any gaps or openings.
When implementing noise enclosure or soundproofing measures, consider the following guidelines:
- Evaluate the motor’s operating conditions: Determine if the motor requires additional cooling or ventilation to prevent overheating within the enclosure.
- Choose sound-absorbing materials: Select materials with appropriate noise reduction coefficients (NRC) to effectively absorb and dampen the motor noise.
- Consider access for maintenance: Design the enclosure with removable panels or doors to provide easy access for inspection and maintenance of the motor.
- Acoustic resonance considerations: Address any potential acoustic resonance issues that may occur within the enclosure by implementing measures such as acoustic damping or adding Helmholtz resonators.
Implementing a noise enclosure or soundproofing techniques can significantly reduce the noise emitted by the motor and create a more peaceful working environment. However, it’s important to remember that proper ventilation and maintenance should be considered to ensure the motor’s optimal performance.
By utilizing noise enclosure or soundproofing methods, you can lower the impact of motor noise on your working environment and enhance overall productivity and comfort.
Ensure proper alignment of the motor and its components to reduce vibration and noise. Use vibration isolation mounts and consider adding sound insulation to the motor housing. Regular maintenance and lubrication can also help reduce noise.
Balancing and Alignment
Balancing and alignment are essential aspects of maintaining smooth motor operation and minimizing noise. Imbalances or misalignments can lead to excessive vibrations, resulting in increased noise levels. By ensuring proper balancing and alignment, you can significantly reduce motor noise and enhance its performance.
Here are the steps to achieve optimal balancing and alignment:
- Balancing: Balancing refers to the process of distributing the mass of the motor’s rotating components evenly. Unbalanced rotors can cause significant vibrations and noise during operation. To balance the rotor, you can use precision instruments such as a balancing machine, which identifies the areas where additional weight needs to be added or removed to achieve balance. Properly balanced rotors result in smoother motor operation and reduced noise.
- Alignment: Misalignment between the motor’s rotor and the driven equipment can also contribute to noise generation. Proper alignment ensures that the rotating components are correctly positioned, minimizing vibrations and noise. Use alignment tools such as laser alignment devices to align the motor shaft with the driven equipment accurately. By achieving precise alignment, you can reduce motor noise and extend the lifespan of both the motor and the driven equipment.
Regular maintenance and inspection are crucial in maintaining balance and alignment over time. Here are some additional tips to consider:
- Scheduled Maintenance: Implement a routine maintenance schedule to check for any signs of imbalance or misalignment. Regular inspections will allow you to identify and address issues before they escalate.
- Lubrication: Inadequate lubrication can lead to increased friction, which in turn can cause imbalances, misalignment, and noise. Ensure that all moving parts are properly lubricated according to the manufacturer’s recommendations.
- Professional Assistance: If you are unsure about the balancing or alignment process, it is advisable to seek assistance from a professional technician or a service provider with expertise in motor maintenance and repair.
By addressing any imbalances or misalignments, you can significantly reduce motor noise and enhance its overall performance. Proper balance and alignment not only reduce noise but also help prevent excessive wear and tear on the motor’s components, leading to increased longevity and reliability.
In the next section, we will discuss the importance of lubrication and maintenance in reducing motor noise.
Lubrication and Maintenance
Lubrication and maintenance play a crucial role in reducing electric motor noise and ensuring optimal performance. Inadequate lubrication or neglecting regular maintenance can lead to increased friction and wear, resulting in excessive noise and potential motor failure. Here’s how proper lubrication and maintenance can help minimize motor noise:
- Lubrication: Adequate lubrication is essential to reduce friction between moving components inside the motor. Friction can generate noise and cause premature wear and tear. Follow the manufacturer’s recommendations for lubrication type and intervals to ensure smooth operation and minimize noise. Regularly check and replenish lubricants to maintain optimal levels.
- Maintenance Inspections: Implement a routine maintenance program to inspect the motor for any signs of wear, damage, or loose components. Pay attention to parts such as bearings, shafts, and couplings that can contribute to noise if not properly maintained. Tighten any loose screws or bolts, and replace worn-out parts promptly.
- Cleaning: Regular cleaning of the motor’s external surfaces and fan blades is necessary to prevent dust and debris buildup. Accumulated debris can disrupt proper airflow, leading to increased noise. Use compressed air or a soft brush to remove dirt and debris from the motor’s cooling system.
- Bearing Maintenance: Bearings are critical components that can contribute to motor noise if not properly maintained. Regularly inspect bearings for signs of wear and lubricate them as recommended. If you notice any unusual noise or vibration coming from the bearings, consider replacing them to avoid further damage.
- Temperature Monitoring: Motors operating at high temperatures can generate increased noise due to expanded components and decreased lubrication effectiveness. Monitor motor temperature and ensure it stays within recommended operating limits. Adequate ventilation and cooling systems can help maintain optimal temperatures.
- Professional Servicing: For complex maintenance procedures or when encountering persistent noise issues, it is recommended to consult a professional electric motor service provider. They have the expertise and specialized equipment to conduct thorough inspections, diagnose problems, and perform any necessary repairs or adjustments.
By prioritizing lubrication and maintenance practices, you can proactively reduce motor noise, extend its lifespan, and prevent costly breakdowns. Regular care and attention to the motor’s condition will help ensure smooth operation and a quieter working environment.
Now that we have covered lubrication and maintenance, let’s move on to the importance of electrical filtering and grounding in reducing motor noise.
Read more: How To Reduce Projector Fan Noise
Electrical Filtering and Grounding
Electrical noise can contribute to motor noise and interfere with its proper operation. Implementing effective electrical filtering and grounding techniques can help minimize noise caused by electrical issues. By addressing the electrical factors associated with motor noise, you can create a quieter and more stable motor operation. Here’s how to reduce motor noise through electrical filtering and grounding:
- Electrical Filtering: Electrical noise can be introduced through the power supply or other electrical devices in the vicinity of the motor. Implementing appropriate electrical filters can help mitigate this noise. Install surge protectors or line filters to filter out electromagnetic interference (EMI) and high-frequency noise. These filters block or redirect noise signals, resulting in smoother power delivery and reduced motor noise. Consult with an electrical engineer or specialist to determine the most suitable filters for your specific motor and noise requirements.
- Grounding: Proper grounding is crucial for minimizing electrical noise. It involves providing an efficient path for current to return to the earth, ensuring stable electrical operation. Poor or inadequate grounding can result in stray currents and electromagnetic interference, leading to increased motor noise. Maintain a solid and low-resistance ground connection for both the motor and the electrical system. Conduct regular inspections to verify the integrity of the grounding system, including grounding conductors, electrodes, and connections.
- Shielding: Shielding involves enclosing sensitive electrical components or cables in a conductive material to prevent the transmission of external electromagnetic interference. Shielding can help reduce noise that may be caused by nearby electrical equipment or power cables. Utilize shielded cables, grounded shielding materials, or metal enclosures to shield vulnerable electrical components or wiring within the motor system.
- Proper Wiring: Ensure that the motor’s electrical connections are properly wired and secured. Loose or improper wiring can introduce noise and cause electrical issues that contribute to motor noise. Use appropriate wire gauge and follow wiring diagrams or manufacturer’s guidelines to ensure correct and secure connections.
Implementing electrical filtering and grounding measures can significantly reduce electrical noise and its associated motor noise. By addressing these electrical factors, you can enhance the stability and efficiency of motor operation while promoting quieter performance.
In the next section, we will explore the use of anti-vibration mounts to reduce motor noise.
Using Anti-Vibration Mounts
Anti-vibration mounts are a practical and effective solution for reducing electric motor noise by isolating and absorbing vibrations. These mounts provide a buffer between the motor and its mounting surface, preventing the transmission of vibrations and minimizing noise. Here’s how using anti-vibration mounts can help reduce motor noise:
- Vibration Isolation: Anti-vibration mounts are designed to isolate the motor from the surrounding structure, minimizing the transfer of vibrations. They are typically made of resilient materials such as rubber or neoprene, which absorb and dampen vibrations generated during motor operation. This isolation helps prevent vibrations from spreading to nearby surfaces, reducing noise.
- Easy Installation: Anti-vibration mounts are relatively straightforward to install. They are typically designed with pre-drilled holes or mounting patterns, making it easy to attach them to the motor and the mounting surface. Ensure that the mounts are properly aligned and securely fastened for optimal vibration isolation and noise reduction.
- Improved Stability: By using anti-vibration mounts, you can enhance the stability of the motor during operation. These mounts help reduce vibrations that can lead to imbalances or misalignments, which in turn contribute to increased noise levels. The improved stability provided by the mounts promotes smoother motor operation and reduces noise generation.
- Versatility: Anti-vibration mounts are available in various shapes, sizes, and load-bearing capacities to suit different motor types and applications. Whether you have a small motor for household appliances or a larger motor for industrial machinery, there are anti-vibration mounts available to accommodate your specific needs.
- Regular Maintenance: Inspect the anti-vibration mounts regularly to ensure they remain in good condition. Over time, these mounts may wear out or deteriorate, leading to reduced effectiveness in vibration isolation. Replace worn or damaged mounts promptly to maintain optimal noise reduction capabilities.
When utilizing anti-vibration mounts, consider the specific requirements of your motor and the surrounding environment. Factors such as the motor’s weight, size, and vibration characteristics should be taken into account when selecting the appropriate mounts.
By incorporating anti-vibration mounts into your motor installation, you can effectively reduce motor noise and create a quieter working environment. Additionally, these mounts help prolong the lifespan of the motor by minimizing vibrations and excessive strain on its components.
In the last section, we will discuss the use of noise damping materials to further reduce motor noise.
Noise Damping Materials
Noise damping materials are an effective solution for reducing electric motor noise by absorbing and dampening sound waves. These materials act as barriers to noise propagation, helping to create a quieter working environment. Here’s how using noise damping materials can help reduce motor noise:
- Sound Absorption: Noise damping materials, such as foam, rubber, or mass-loaded vinyl, are designed to absorb sound waves. When strategically placed around the motor or its surrounding components, these materials help to reduce noise by converting sound energy into heat energy.
- Material Selection: Choose noise damping materials with high noise reduction coefficients (NRC) to effectively absorb a wide range of frequencies. Consider the specific noise characteristics of your motor and select materials accordingly.
- Placement: Install noise damping materials on the interior surfaces of the motor or any components that may amplify noise. Common areas to apply the materials include motor housings, enclosures, or panels that are in direct contact with noise-generating elements. Ensure proper coverage and secure attachment to maximize noise reduction.
- Multi-Layering: For increased effectiveness, consider using multiple layers of noise damping materials. Layering different materials with varying densities can help disrupt the transmission of sound waves and provide additional noise reduction.
- Noise Pathways: Identify and address potential noise pathways that may bypass the noise damping materials. Seal any gaps, joints, or openings that may allow noise to escape or enter the motor’s surroundings.
- Compatibility: Ensure that the noise damping materials selected are compatible with the motor’s operating conditions. Consider factors such as temperature, humidity, and exposure to chemicals or vibrations that may affect the performance of the materials over time.
It’s important to note that noise damping materials should be used in conjunction with other noise reduction strategies for optimal results. Combining vibration isolation, noise enclosure, and proper maintenance with noise damping materials can provide comprehensive noise reduction solutions for electric motors.
Regularly inspect the noise damping materials to ensure they remain in good condition and replace them if degraded or damaged. Proper maintenance and replacement of these materials will help maintain their effectiveness in reducing motor noise over time.
By incorporating noise damping materials into your motor system, you can significantly reduce noise levels and create a quieter and more comfortable working environment.
Now that we have explored the strategies to reduce electric motor noise, let’s conclude our discussion.
Conclusion
Electric motor noise can be a nuisance in various industrial and commercial settings. Excessive motor noise not only disrupts productivity but can also indicate underlying problems with the motor’s functioning. Fortunately, there are several effective strategies to reduce electric motor noise and create a quieter working environment.
Understanding the factors that contribute to motor noise is crucial in implementing the right solutions. Vibrations, electromagnetic forces, airflow, and external factors can all play a role in generating motor noise. By accurately determining the source of the noise, whether it’s mechanical, electrical, or environmental, you can take targeted measures to address the problem.
We explored several strategies to reduce electric motor noise:
- Vibration Isolation: Using anti-vibration mounts or pads to minimize vibrations and prevent their transmission to surrounding structures.
- Noise Enclosure or Soundproofing: Constructing a noise enclosure or applying soundproofing materials to contain and dampen motor noise.
- Balancing and Alignment: Achieving proper balance and alignment of motor components to reduce vibrations and noise.
- Lubrication and Maintenance: Ensuring adequate lubrication and routine maintenance to minimize friction and prevent excessive noise.
- Electrical Filtering and Grounding: Implementing electrical filters and proper grounding to reduce noise caused by electrical issues.
- Using Anti-Vibration Mounts: Installing anti-vibration mounts to isolate the motor and absorb vibrations, thus reducing noise.
- Noise Damping Materials: Applying noise damping materials to absorb sound waves and minimize noise propagation.
Each strategy addresses specific aspects of motor noise and should be employed based on the specific requirements and characteristics of your motor system.
Remember, regular maintenance, inspections, and prompt repairs are essential to keeping your motor in optimal condition and minimizing noise. Be sure to follow manufacturers’ guidelines and consult professionals when needed.
By implementing these strategies, you can effectively reduce electric motor noise, improve workplace comfort, and enhance overall operational efficiency.
Now it’s time to put these strategies into action and enjoy a quieter, more productive environment for your electric motor systems.
Frequently Asked Questions about How To Reduce Electric Motor Noise
Was this page helpful?
At Storables.com, we guarantee accurate and reliable information. Our content, validated by Expert Board Contributors, is crafted following stringent Editorial Policies. We're committed to providing you with well-researched, expert-backed insights for all your informational needs.
0 thoughts on “How To Reduce Electric Motor Noise”