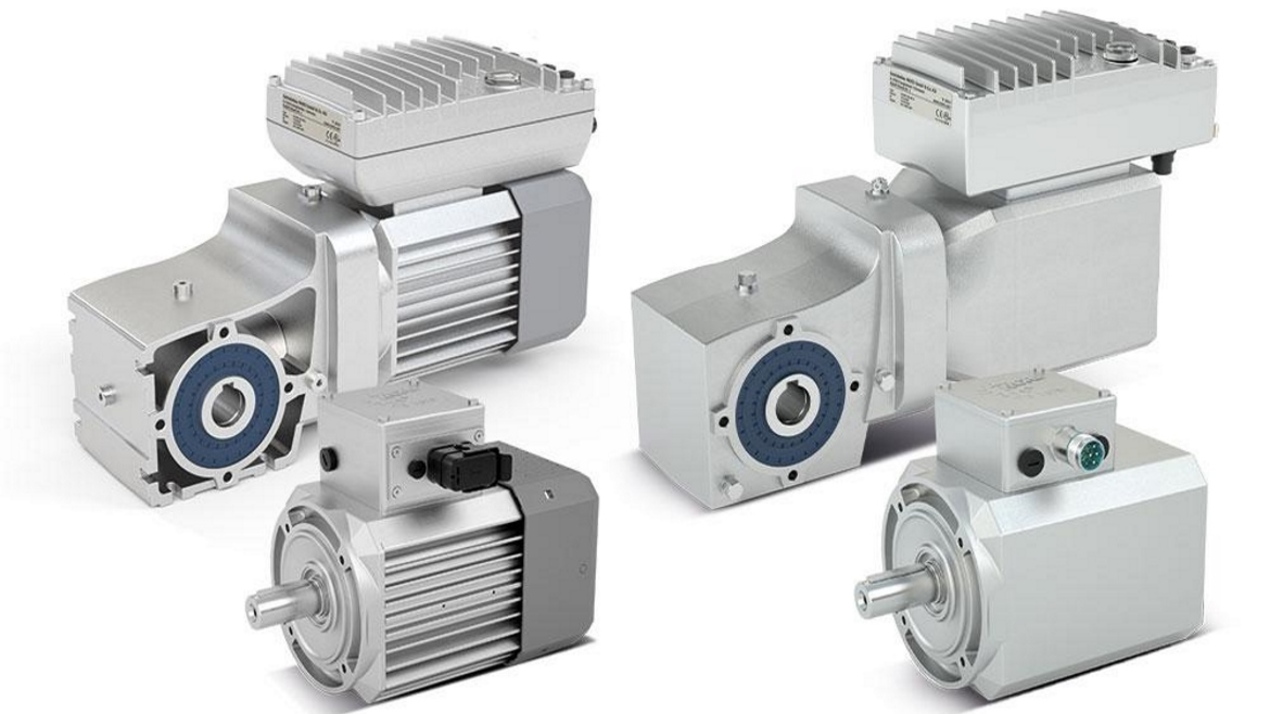
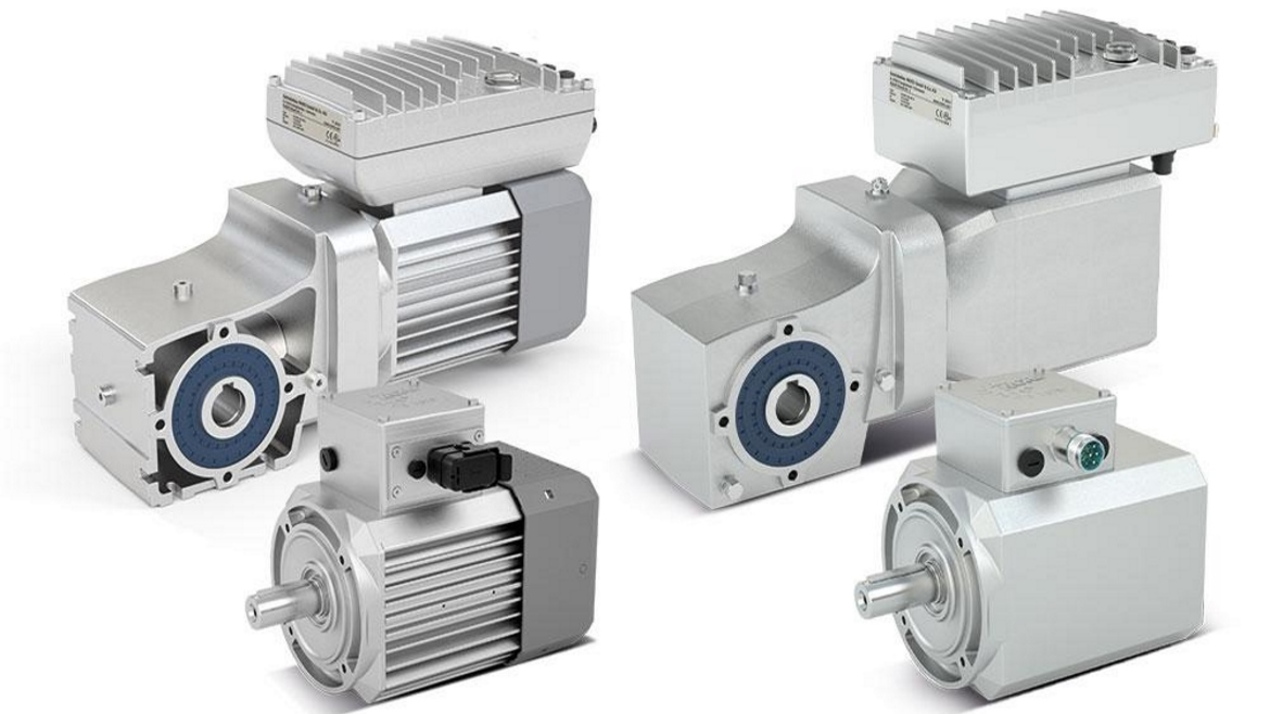
Articles
How to Size An Electric Motor
Modified: December 7, 2023
Discover expert articles on how to properly size an electric motor for your specific needs. Learn about the factors to consider and get valuable insights from industry professionals.
(Many of the links in this article redirect to a specific reviewed product. Your purchase of these products through affiliate links helps to generate commission for Storables.com, at no extra cost. Learn more)
Introduction
Welcome to the world of electric motor sizing! Whether you’re an engineer, a DIY enthusiast, or simply someone who wants to learn more about electric motors, understanding how to properly size an electric motor is essential. Sizing an electric motor involves determining the appropriate motor size and power output to match the requirements of a specific application.
Electric motors are used in a wide range of industries and applications, from powering heavy machinery in manufacturing plants to driving pumps in irrigation systems. Choosing the right electric motor size ensures optimal performance, energy efficiency, and longevity of the motor.
In this article, we will delve into the intricacies of electric motor sizing, highlighting the factors to consider, providing a step-by-step guide, and addressing various application-specific considerations. By the end, you’ll have a comprehensive understanding of how to effectively size an electric motor for your specific needs.
So, whether you’re looking to replace an existing motor, upgrade your equipment, or embark on a new project, let’s dive in and discover the secrets to successful electric motor sizing.
Key Takeaways:
- Properly sizing an electric motor is crucial for optimal performance, energy efficiency, and longevity. Understanding application requirements, considering environmental factors, and consulting experts are key to successful motor sizing.
- Avoid common mistakes in electric motor sizing, such as underestimating power requirements, ignoring torque demand, and disregarding environmental conditions. Accurate calculations, expert advice, and careful consideration lead to effective motor selection.
Read more: How To Build A Electric Motor
Understanding Electric Motor Sizing
Electric motor sizing involves determining the appropriate motor size and power output to ensure optimal performance in a given application. It is crucial to understand the fundamental concepts and factors involved in electric motor sizing to make informed decisions. Let’s explore these key aspects.
Power Requirement: The first step in sizing an electric motor is to determine the power requirement of the application. This includes considering factors such as the load type (constant or variable), operating conditions (continuous or intermittent), and any peak loads that the motor may need to handle.
Torque Demand: Torque is the rotational force required to overcome resistance and is crucial in selecting the motor size. Calculating the torque demand involves considering factors such as the load inertia, acceleration time, and desired speed of the motor.
Speed Control: Depending on the application, you may need to consider the speed control capability of the motor. Some applications require precise speed control, while others may require variable speed options. Choosing a motor with the appropriate speed control features is essential.
Operating Environment: The operating environment, including factors such as temperature, humidity, vibration, and dust, can impact the motor’s performance and lifespan. It is important to choose a motor that is suitable for the specific environmental conditions in which it will operate.
Efficiency and Energy Savings: Selecting a motor with high efficiency can lead to significant energy savings. Look for motors with high efficiency ratings (usually indicated by the motor’s efficiency class) to minimize energy consumption and reduce operating costs.
Space Constraints: Consider the physical dimensions of the motor and compare them to the available space in your application. Ensure that the motor can be easily installed and maintained within the given space constraints.
Cost Considerations: The cost of the motor should also be taken into account. Balance the features and capabilities required for your application with the available budget to choose the most cost-effective option.
By understanding these key aspects of electric motor sizing, you can make informed decisions and select the right motor for your specific application. In the next section, we will provide a step-by-step guide to assist you in the motor sizing process.
Factors to Consider in Electric Motor Sizing
When sizing an electric motor, several factors need to be taken into consideration to ensure optimal performance and efficiency. Let’s explore the key factors that should be considered during the electric motor sizing process.
Application Requirements: The specific requirements of the application should be thoroughly understood. Consider factors such as the load type, operating conditions, desired speed, and torque requirements. This will help determine the power and performance characteristics needed from the motor.
Power Supply: The available power supply voltage and frequency are important considerations. Ensure that the motor’s rated voltage and frequency match the power supply specifications to ensure proper operation.
Motor Type: There are various types of electric motors available, including induction motors, synchronous motors, and brushed or brushless DC motors. Each motor type has its own characteristics and advantages, so select the type that best suits your application requirements.
Efficiency and Energy Savings: Consider the motor’s efficiency rating to maximize energy savings. Look for motors with high efficiency, indicated by the motor’s efficiency class rating. This will help reduce operating costs over the motor’s lifespan.
Load Profile: Analyze the load profile of the application. Determine if the load is constant or variable, and if there are any peak load requirements. This information will aid in selecting a motor with the appropriate power and torque capabilities.
Environmental Conditions: Consider the environmental conditions in which the motor will operate. Factors such as temperature, humidity, dust, and vibration can affect the motor’s performance and lifespan. Choose a motor that is designed to withstand the specific environmental conditions.
Mounting and Installation: Evaluate the mounting options and installation requirements of the motor. Ensure that the motor can be easily installed in the available space and that the mounting method is suitable for the application.
Budget: Consider the cost of the motor and balance it with the features and capabilities required for the application. Select a motor that meets your budget while also providing the necessary performance and reliability.
Future Considerations: Anticipate any future changes or expansions to the application that may require additional power or torque. It is beneficial to choose a motor with some margin, allowing for future growth.
By considering these factors during the electric motor sizing process, you can ensure that the selected motor is well-matched to the application requirements, leading to optimal performance, energy efficiency, and longevity. In the next section, we will provide a step-by-step guide to assist you in sizing your electric motor effectively.
Step-by-Step Guide for Electric Motor Sizing
Sizing an electric motor may seem complex, but by following a systematic approach, you can simplify the process. Here is a step-by-step guide to help you size your electric motor effectively:
- Determine the Application Requirements: Begin by understanding the specific requirements of the application. Consider factors such as the load type, operating conditions, desired speed, and torque requirements. This will provide the baseline for selecting the motor.
- Calculate the Power Requirement: Calculate the power requirement of the application. This involves determining the power needed to drive the load, considering factors such as the load weight, distance, and any additional factors affecting power consumption. The power requirement will help determine the motor’s power output.
- Define the Torque Demand: Calculate the torque demand of the application. This involves considering factors such as load inertia, acceleration time, and desired speed. The torque demand will aid in selecting a motor with sufficient torque capability to overcome the resistance and drive the load.
- Select the Motor Type: Based on the application requirements, choose the appropriate motor type. Consider factors such as efficiency, speed control capabilities, and compatibility with the power supply. Induction motors are commonly used for general-purpose applications, while synchronous motors may be suitable for applications that require precise speed control.
- Consult Motor Manufacturer’s Data Sheets: Refer to the motor manufacturer’s data sheets to gather information about the motor’s specifications, performance characteristics, and efficiencies. This information will help you narrow down your options and make an informed decision.
- Compare with Motor Selection Software: Utilize motor selection software or online tools provided by motor manufacturers to further refine your selection. These tools allow you to input the application parameters and obtain motor recommendations based on the specific requirements.
- Consider Environmental Factors: Take into account the environmental conditions in which the motor will operate. Consider factors such as temperature, humidity, dust, and vibration. Ensure that the selected motor is designed to handle these conditions and provide reliable performance.
- Evaluate Space Constraints: Assess the available space for installing the motor. Consider the physical dimensions of the motor and ensure that it can be comfortably accommodated within the given constraints.
- Review Budget Constraints: Compare the cost of the selected motors and ensure that they fit within your budget. Consider the long-term benefits and operating costs associated with higher efficiency motors, as they may offset the initial investment through energy savings.
- Make the Final Selection: Based on the application requirements, motor specifications, environmental factors, space constraints, and budget considerations, make the final selection of the electric motor that best suits your needs.
By following this step-by-step guide, you can effectively size your electric motor and ensure that it meets the specific requirements of your application. Remember to consult experts and motor manufacturers for any additional guidance or assistance. In the next section, we will discuss specific considerations for different types of applications.
When sizing an electric motor, consider the load requirements, operating conditions, and any potential future expansion. It’s important to choose a motor that can handle the required torque and speed for optimal performance.
Considerations for Different Types of Applications
Electric motor sizing considerations can vary depending on the type of application you are working with. Different applications have unique requirements, load characteristics, and operating conditions. Let’s explore some specific considerations for different types of applications:
- Industrial Applications: In industrial applications such as manufacturing plants, it is crucial to consider the load profile, duty cycle, and start-up torque requirements. These applications often involve heavy machinery and require motors with high torque capabilities.
- Commercial Applications: Commercial applications such as HVAC systems, refrigeration units, and commercial pumps require motors that are efficient and reliable. Consider the load demand, operating conditions, and energy efficiency requirements when selecting a motor for these applications.
- Agricultural Applications: Agricultural applications such as irrigation systems and farming equipment require motors that can handle continuous operation and variable loads. Consider the power requirements, duty cycle, and environmental conditions specific to the agricultural environment.
- Residential Applications: Residential applications such as home appliances and small machines require motors that are cost-effective, energy-efficient, and compact in size. Consider the power requirements, space constraints, and noise level requirements for these applications.
- Automotive Applications: Electric motors in automotive applications, such as electric vehicles and hybrid cars, need to be lightweight, high-performing, and energy-efficient. Consider the power requirements, weight restrictions, and efficiency ratings when selecting motors for automotive applications.
- Pump Applications: Pump applications require motors that can handle varying load conditions and provide consistent flow rates. Consider the specific pump characteristics, such as head and flow rate requirements, when sizing motors for pump applications.
- Fan Applications: Fan applications, such as HVAC systems and industrial fans, require motors that can handle the load fluctuations and provide precise speed control. Consider the airflow requirements, pressure differentials, and noise level restrictions when selecting motors for fan applications.
- Conveyor Applications: Conveyor systems require motors that can deliver sufficient torque to move the load smoothly and handle start-up and braking conditions. Consider the load weight, conveyor length, and operating conditions when sizing motors for conveyor applications.
- Specialized Applications: Some applications may have unique requirements, such as high precision, hazardous environments, or specific regulations. In these cases, consult experts and specialized motor manufacturers to ensure compliance and optimal performance.
Remember that these considerations are not exhaustive, and it is important to analyze the specific requirements and characteristics of your application. Consulting with experts and motor manufacturers can provide valuable insights and recommendations specific to your application type. In the next section, we will discuss common mistakes to avoid in electric motor sizing.
Read more: How To Grease Electric Motor
Common Mistakes to Avoid in Electric Motor Sizing
Sizing an electric motor is a critical process that requires careful consideration of various factors. However, it is common for people to make mistakes that can lead to suboptimal motor performance or even motor failure. Avoiding these common mistakes is essential. Let’s explore some of the most common mistakes to avoid in electric motor sizing:
- Underestimating the Power Requirement: One of the most common mistakes is underestimating the power requirement of the application. Failing to accurately calculate the power demand can result in an undersized motor that cannot adequately drive the load or handle peak power requirements.
- Ignoring the Torque Demand: Neglecting to consider the torque demand of the application can lead to motor overheating, excessive wear, and premature failure. It is important to accurately calculate the torque required to overcome resistance and accelerate the load, ensuring the motor is capable of providing sufficient torque.
- Not Considering Efficiency: Overlooking the efficiency rating of the motor can result in higher operating costs and energy wastage. Choosing a motor with lower efficiency may save money upfront but can lead to higher long-term costs. Always consider the efficiency rating and opt for motors with higher efficiency.
- Disregarding Environmental Conditions: Failing to consider the environmental conditions in which the motor will operate can lead to motor failure or reduced lifespan. Factors such as temperature, humidity, dust, and vibration can significantly impact motor performance. Choose a motor that is designed to withstand the specific environmental conditions present in your application.
- Ignoring Duty Cycle: Some applications have intermittent operating cycles or varying load demands. Ignoring the duty cycle of the application can lead to selecting an underpowered motor or one that cannot handle the intermittent load requirements. Analyze the duty cycle and select a motor that can handle the load demands effectively.
- Not Consulting Motor Manufacturer’s Data Sheets: The motor manufacturer’s data sheets provide valuable information about the motor’s specifications, performance curves, and application guidelines. Failing to review these data sheets can result in selecting a motor that is not suitable for the specific application requirements.
- Not Considering Future Expansion: Neglecting to consider future growth or expansion of the application can result in selecting a motor that is barely capable of meeting the current requirements. Leave some margin for future load increases or expandability to avoid the need for frequent motor replacements.
- Incorrectly Matching Motor and Load: Mismatching the motor and load can lead to inefficiencies, motor overheating, and premature failures. It is important to ensure that the motor’s characteristics, such as torque, speed, and power rating, align with the load’s requirements.
- Not Seeking Expert Advice: Electric motor sizing can be complex, and seeking expert advice can help avoid common pitfalls and ensure proper motor selection. Consulting with motor manufacturers, engineers, or experienced professionals can provide valuable insights and guidance throughout the sizing process.
By being aware of these common mistakes and taking the necessary precautions, you can avoid unnecessary complications and ensure the successful sizing of your electric motor. Careful consideration of the application requirements, accurate calculations, and collaboration with experts will help you select the most suitable motor for your specific needs. In the next section, we will conclude our discussion on electric motor sizing.
Conclusion
Sizing an electric motor is a crucial step in ensuring optimal performance and efficiency in various applications. By understanding the factors involved, following a step-by-step guide, and avoiding common mistakes, you can successfully size an electric motor that meets your specific requirements.
Throughout this article, we explored the important considerations in electric motor sizing, such as understanding the application requirements, calculating power and torque demands, considering environmental factors, and evaluating space and budget constraints. We discussed specific considerations for different types of applications and highlighted common mistakes to avoid.
Remember that electric motor sizing is not a one-size-fits-all process. Each application has unique requirements and characteristics that must be taken into account. Consulting with experts, utilizing motor manufacturer’s data sheets, and utilizing motor selection software can provide valuable insights and guidance specific to your application.
Properly sizing an electric motor is crucial for achieving optimal performance, energy efficiency, and longevity. An undersized motor may struggle to meet the load demands, while an oversized motor can lead to wasted energy and unnecessary costs. By carefully considering the power, torque, efficiency, environmental conditions, and future expansion requirements, you can select the right motor for your specific needs.
In summary, electric motor sizing requires attention to detail, accurate calculations, and an understanding of the specific application requirements. Take the time to carefully assess your needs, consult experts, and make informed decisions. By doing so, you can ensure that your electric motor operates at its best, providing reliable and efficient performance for your application.
Frequently Asked Questions about How To Size An Electric Motor
Was this page helpful?
At Storables.com, we guarantee accurate and reliable information. Our content, validated by Expert Board Contributors, is crafted following stringent Editorial Policies. We're committed to providing you with well-researched, expert-backed insights for all your informational needs.
0 thoughts on “How to Size An Electric Motor”