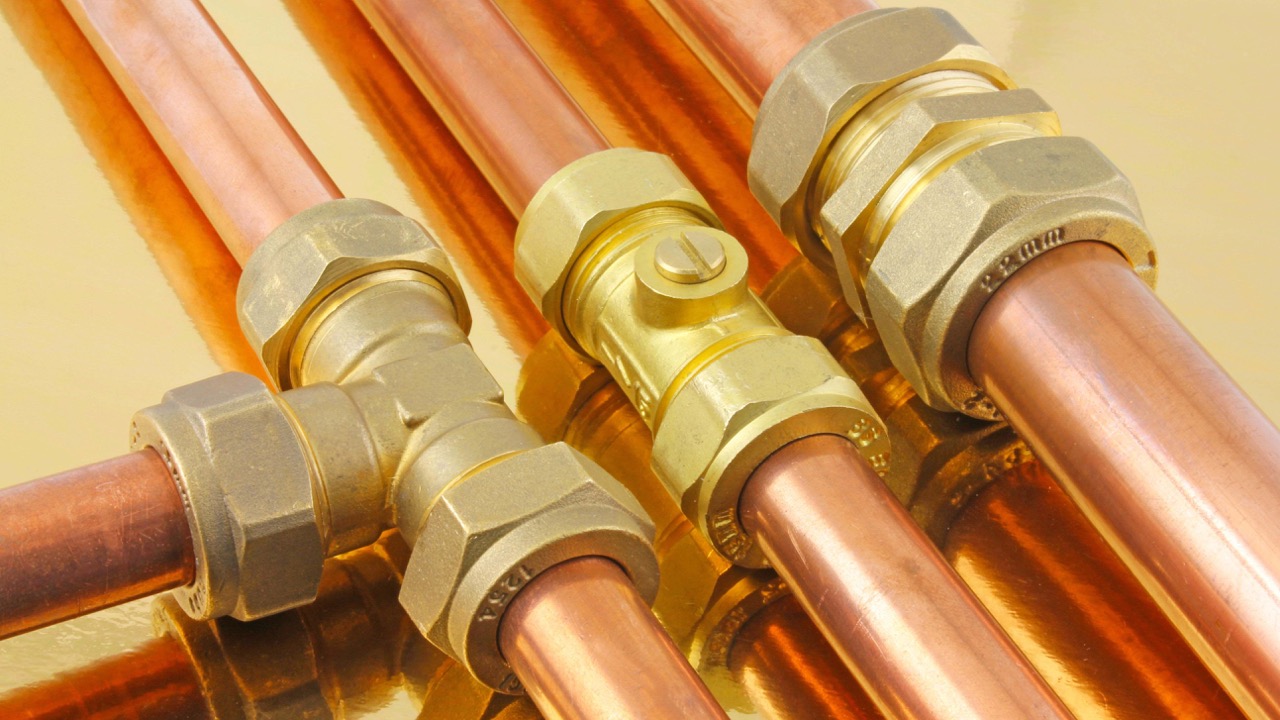
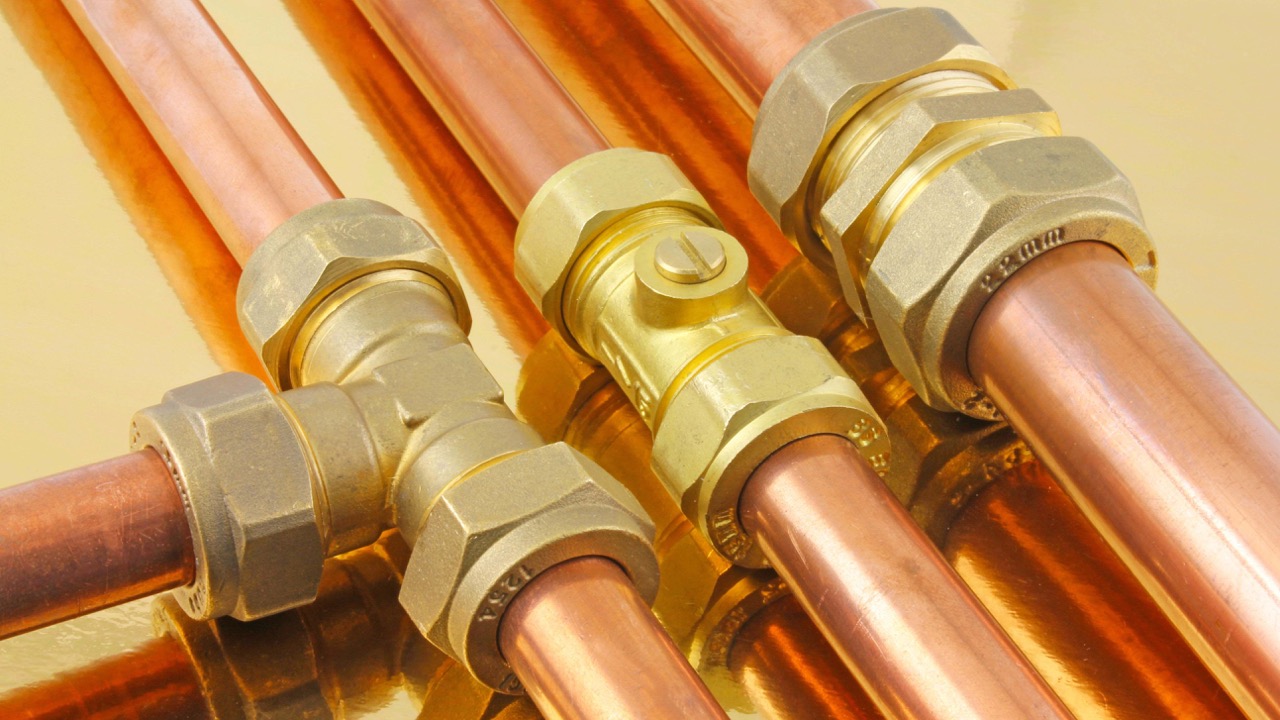
Articles
What Is A Compression Fitting In Plumbing
Modified: January 8, 2024
Learn about compression fittings in plumbing articles. Discover what they are and how they are used in various plumbing applications.
(Many of the links in this article redirect to a specific reviewed product. Your purchase of these products through affiliate links helps to generate commission for Storables.com, at no extra cost. Learn more)
Introduction
When it comes to plumbing installations and repairs, one of the essential components is a compression fitting. Compression fittings play a crucial role in connecting pipes, valves, and fixtures in a secure and leak-free manner. Understanding what compression fittings are and how they work can help you make informed decisions when it comes to your plumbing needs.
Compression fittings are fittings used in plumbing systems to create tight and reliable connections between pipes or tubes. These fittings consist of three main components: the compression nut, the compression ring (also known as a ferrule), and the compression fitting body. Together, these components work in harmony to create a watertight seal, preventing leaks and ensuring smooth water flow.
Compression fittings are commonly made of materials such as brass, copper, or stainless steel, which are known for their durability and corrosion-resistant properties. The choice of material depends on the specific plumbing application and the type of pipes being connected.
Now that we have a basic understanding of compression fittings, let’s explore how they work in more detail.
Key Takeaways:
- Compression fittings are essential for creating leak-free connections in plumbing systems. Their versatility, reusability, and ability to withstand high and low-pressure applications make them a reliable choice for both DIY enthusiasts and professional plumbers.
- While compression fittings offer numerous benefits, it’s important to consider potential drawbacks such as installation complexity and maintenance requirements. Regular inspections, proper tightening, and addressing any leaks or damaged components are crucial for ensuring their longevity and performance.
Read more: What Are Fittings In Plumbing
Definition of Compression Fitting
A compression fitting is a type of plumbing fitting used to connect two pipes or tubes together. The term “compression” refers to the method by which the fitting creates a tight seal between the pipes, preventing leaks and ensuring a secure connection.
Compression fittings consist of three main components: the compression nut, compression ring (or ferrule), and the compression fitting body. The fitting body is the central piece that houses the ends of the pipes to be joined. The compression nut is then threaded onto the fitting body, compressing the ring or ferrule against the pipes to create a seal.
The compression ring or ferrule is a small, circular piece that fits around the pipe’s exterior. As the compression nut is tightened, it presses the ring or ferrule against the pipe, causing it to deform slightly and create a secure connection. This deformation results in the compression fitting’s ability to ensure a watertight seal without the need for soldering or welding.
It’s important to note that the compression nut should be tightened securely, but not excessively. Over-tightening the compression nut can lead to damage or deformation of the components, compromising the integrity of the fitting and potentially causing leaks.
Compression fittings are widely used in various plumbing applications, including connecting pipes to fixtures, valves, or appliances. They are particularly useful in situations where disassembly is required for maintenance or repairs, as they provide a reliable and reusable connection.
Now that we understand the definition and components of compression fittings, let’s dive deeper into how they work.
How Compression Fittings Work
Compression fittings work on the principle of compression, as the name suggests. The design of these fittings allows for a secure and leak-free connection between pipes or tubes. Let’s take a closer look at the working mechanism of compression fittings:
- The first step in using a compression fitting is to prepare the pipes or tubes that need to be joined. This typically involves cutting the pipe ends to ensure they are clean, smooth, and free from any burrs or debris.
- Once the pipes are prepared, the compression fitting body is inserted into one end of the pipe. It is important to ensure that the fitting body is fully inserted for a proper connection.
- A compression ring or ferrule is then placed over the exterior of the pipe, positioned against the fitting body.
- The compression nut is threaded onto the fitting body, applying pressure to the compression ring or ferrule, which in turn compresses against the pipe.
- As the compression nut is tightened, the compression ring or ferrule deforms slightly, creating a seal between the pipe and the fitting body. This deformation creates a mechanical grip on the pipe, preventing any leakage.
The compression fitting’s compression nut must be tightened securely, but not excessively. Over-tightening can lead to damage or distortion of the fitting components, compromising the seal and potentially causing leaks.
One of the advantages of compression fittings is their reusability. If the need arises to disconnect the pipes, the compression nut can be loosened and the fitting easily removed. The compression ring or ferrule may need to be replaced if it becomes deformed or damaged during disassembly.
Compression fittings provide a reliable and convenient solution for joining pipes in plumbing systems. The compression seal creates a tight connection without the need for soldering or welding, making them suitable for both DIY enthusiasts and professional plumbers alike.
Now that we have explored how compression fittings work, let’s move on to discuss the different types of compression fittings available.
Types of Compression Fittings
Compression fittings come in various types to accommodate different plumbing needs. Each type of compression fitting is designed for specific applications, materials, and pipe sizes. Here are some common types of compression fittings:
- Straight Compression Fittings: This is the most basic type of compression fitting. It consists of a compression nut, compression ring, and fitting body, allowing for a straight connection between two pipes.
- Reducing Compression Fittings: These fittings are used when you need to connect pipes of different sizes. They have a larger fitting body on one side and a smaller fitting body on the other, accommodating the varied pipe sizes.
- Elbow Compression Fittings: Elbow compression fittings are designed for making 90-degree bends in plumbing systems. They allow for smooth directional changes in the pipework, maintaining a secure connection.
- Tee Compression Fittings: Tee compression fittings are used when branching off a main pipe into two or more directions. These fittings have a T-shaped body, allowing for multiple connections.
- Union Compression Fittings: Union compression fittings are used when the need for disassembly and reassembly arises. They have a nut and two separate fitting bodies, allowing for easy removal without disturbing the connected pipes.
Compression fittings are available in different materials to suit various plumbing needs. Brass compression fittings are commonly used due to their durability, corrosion resistance, and strength. However, there are also compression fittings available in materials like copper, stainless steel, and plastic, offering flexibility and compatibility with different pipe materials.
The choice of compression fitting depends on factors such as the type of plumbing system, the pipe material, and the specific application. It’s important to select the appropriate type and size of compression fitting to ensure a proper and secure connection.
Now that we have explored the types of compression fittings, let’s discuss the advantages they offer for plumbing installations.
Advantages of Compression Fittings
Compression fittings offer several advantages that make them a popular choice in plumbing installations. Let’s explore some of the key benefits:
- Leak-Free Connection: One of the primary advantages of compression fittings is their ability to create a tight and reliable connection. The compression ring or ferrule, when properly installed, creates a secure seal that prevents leaks, ensuring the integrity of the plumbing system.
- No Need for Heat or Welding: Unlike soldering or welding joints, compression fittings enable you to create connections without the need for heat or welding equipment. This makes installations easier, especially for DIY enthusiasts who may not have specialized tools.
- Easy Disassembly and Reusability: Compression fittings allow for easy disassembly, making them ideal for situations that require maintenance or repairs. You can simply loosen the compression nut and remove the fitting without causing damage or needing to replace any components. This reusability factor can be cost-effective in the long run.
- Versatility: Compression fittings are versatile and compatible with various pipe materials, including copper, brass, PVC, and more. They can be used in a wide range of plumbing applications, from connecting pipes to fixtures and appliances to creating complex plumbing systems with different fittings.
- Adjustability: Compression fittings offer some adjustability during installation. The compression nut can be tightened or loosened to ensure a proper fit, even if the pipe ends are slightly off in size or alignment. This flexibility allows for minor adjustments, saving time and effort.
Due to these advantages, compression fittings are widely used in residential, commercial, and industrial plumbing systems. They provide a reliable and efficient solution for creating connections that withstand both high and low-pressure applications.
However, it’s important to consider the potential drawbacks of compression fittings as well, which we will discuss in the next section.
When using compression fittings in plumbing, make sure to properly measure and cut the pipe to ensure a secure and leak-free connection. It’s also important to use the correct size and type of compression fitting for the specific application.
Read more: What Is A Street Elbow Fitting In Plumbing
Disadvantages of Compression Fittings
While compression fittings offer numerous benefits, it’s important to consider their potential disadvantages before incorporating them into your plumbing system. Here are some of the key drawbacks of compression fittings:
- Installation Complexity: Compared to other types of fittings, compression fittings can be slightly more complex to install. Care must be taken to ensure the compression nut is tightened properly, but not overly tightened, to avoid damaging the components or causing leakage.
- Potential for Weakening: Over time, the repeated tightening and loosening of compression fittings can weaken the fitting and its components. If not properly maintained or if excessive force is used during installation, the compression ring or ferrule can become deformed or damaged, resulting in compromised connections.
- Compatibility with Certain Pipe Materials: While compression fittings are compatible with various pipe materials, their effectiveness may depend on the specific material being used. Some materials, such as plastic pipes, may require additional considerations or specific compression fittings designed for that material.
- Cost Comparison: In some cases, compression fittings may be more expensive compared to other types of fittings, such as sweat or push-to-connect fittings. Depending on the scale of the plumbing project, the cost difference may be a factor to consider.
- Space Limitations: Compression fittings require space for the compression nut and fitting body. In tight or confined spaces, it may be challenging to install or remove compression fittings, making them less ideal for certain applications with limited access.
Despite these drawbacks, compression fittings continue to be widely used in plumbing systems due to their reliability and ease of maintenance. It’s important to weigh the advantages and disadvantages based on your specific plumbing needs before making a decision.
Now that we have examined the advantages and disadvantages of compression fittings, let’s dive into some common uses of these fittings in plumbing applications.
Common Uses of Compression Fittings in Plumbing
Compression fittings are versatile and find applications in various plumbing systems and installations. Here are some common uses of compression fittings:
- Pipe Connections: Compression fittings are commonly used to connect pipes in plumbing systems. Whether it’s joining two sections of copper pipes, connecting plastic pipes to fixtures, or bridging different pipe materials, compression fittings ensure a secure and leak-free connection.
- Fixture Installations: Compression fittings are widely used when installing fixtures such as faucets, showers, and toilets. These fittings provide a reliable connection between the fixture and the water supply lines, ensuring proper water flow and preventing leaks.
- Valve Connections: Compression fittings play a crucial role in connecting valves to pipes. Whether it’s a shutoff valve, pressure reducing valve, or control valve, compression fittings provide a secure connection that allows for easy installation and future maintenance.
- Appliance Hookups: Compression fittings are commonly used for connecting appliances, such as dishwashers, washing machines, and water heaters, to the plumbing system. These fittings ensure a tight and leak-free connection between the appliance and the water supply lines.
- Irrigation Systems: Compression fittings are widely used in irrigation systems, connecting pipes and tubing to sprayers, sprinkler heads, or drip lines. The reliability and adjustability of compression fittings make them suitable for various irrigation applications.
- Pipe Repairs: Compression fittings are often used in pipe repair scenarios. Whether it’s fixing a leaking joint or replacing a damaged section of pipe, compression fittings provide a convenient and effective solution without the need for extensive dismantling or welding.
These are just a few examples of the common uses of compression fittings in plumbing. Their versatility, reliability, and ease of installation make them an essential component in various plumbing applications.
Now that we understand the common uses of compression fittings, let’s move on to discussing the installation process of compression fittings.
Installation Process of Compression Fittings
The installation of compression fittings requires precision and attention to ensure a proper connection. Here is a step-by-step guide on how to install compression fittings:
- Prepare the Pipes: Cut the pipes to the required length and ensure that the ends are clean, smooth, and free from any burrs or debris. This will help create a solid connection.
- Slide on the Compression Nut: Slide the compression nut onto the pipe, followed by the compression ring or ferrule. Make sure that the tapered side of the compression ring or ferrule faces towards the fitting body.
- Insert the Pipe into the Fitting: Insert the pipe into the fitting body, pushing it all the way in until it reaches the stop inside the fitting body. This ensures a proper connection and prevents leaks.
- Tighten the Compression Nut: Use a wrench or adjustable pliers to tighten the compression nut onto the fitting body. Start by hand, and then use the wrench to secure the compression nut. Avoid over-tightening, as this can damage the components or cause leaks. Ensure a snug fit without excessive force.
- Check for Leaks: Once the compression fitting is tightened, turn on the water supply and check for any signs of leaks. Keep an eye on the connection for a few minutes to ensure a secure and leak-free connection.
It’s important to follow the manufacturer’s instructions and guidelines specific to the compression fittings you are using, as installation processes may vary depending on the type and brand. Some compression fittings may require additional steps or considerations.
If you need to disassemble the compression fitting in the future for repairs or maintenance, loosen the compression nut, remove the pipe, and inspect the compression ring or ferrule. Replace any damaged or deformed components before reassembling the fitting.
Regular inspection and maintenance of compression fittings can help identify any potential issues and ensure the longevity of the connections.
Now that we have covered the installation process of compression fittings, let’s move on to discussing the maintenance and troubleshooting of these fittings.
Maintenance and Troubleshooting of Compression Fittings
Maintaining compression fittings is essential to ensure their optimal performance and prevent any potential issues. Here are some maintenance tips and troubleshooting techniques for compression fittings:
- Regular Inspections: Periodically inspect the compression fittings for any signs of leaks, corrosion, or damage. Check the compression nut and the compression ring or ferrule for any wear or deformation. Replace any faulty or damaged components immediately.
- Tightening/Retightening: Over time, compression fittings may require retightening to maintain a secure connection. Use an adjustable wrench to tighten the compression nut slightly if you notice any minor leaks. Be careful not to over-tighten, as it may damage the components.
- Keep Fittings Clean: Ensure that the fittings are free from debris, corrosion, or mineral build-up. Use a brush or cloth to clean the compression nut, fitting body, and compression ring or ferrule. A clean surface helps create a better seal and prevents leaks.
- Inspect Compression Rings/Ferrules: Check the compression rings or ferrules for any signs of wear or damage. If they appear deformed or cracked, it is crucial to replace them before reassembling the compression fitting.
- Proper Pipe Preparation: When installing compression fittings, make sure to properly prepare the pipe ends. Ensure that they are clean, smooth, and free from burrs. This helps create a solid and tight-fitting connection.
- Addressing Leaks: If you notice a leak around a compression fitting, first check if the compression nut is properly tightened. If tightening the nut does not resolve the issue, disassemble the fitting and inspect the compression ring or ferrule. Replace any damaged or worn components and reassemble the fitting.
- Proper Pipe Alignment: Ensure that the pipes are aligned properly before tightening the compression nut. Misaligned pipes can cause leaks or result in a weak connection. Adjust the pipes as necessary to achieve proper alignment.
By following these maintenance practices and troubleshooting techniques, you can ensure the longevity and proper functioning of compression fittings in your plumbing system.
In case you encounter persistent leaks or issues with compression fittings, it may be helpful to consult a professional plumber who can inspect and address the problem effectively.
Now that we have covered the maintenance and troubleshooting aspects, let’s conclude our discussion on compression fittings.
Read more: How To Loosen Plumbing Fittings
Conclusion
Compression fittings are vital components in plumbing systems, providing secure and leak-free connections between pipes, fixtures, and appliances. They offer several advantages, such as easy installation, reusability, versatility, and a reliable method of creating watertight seals.
Understanding the working mechanism, types, and installation process of compression fittings can help you make informed decisions when it comes to your plumbing needs. Whether you are connecting pipes, installing fixtures, or repairing a leak, compression fittings offer a convenient and effective solution.
However, it’s important to be aware of the potential drawbacks and to carry out regular maintenance to ensure optimal functionality of compression fittings. Regular inspections, proper tightening, and addressing any leaks or damaged components are essential for their longevity and performance.
If you encounter any persistent issues or are unsure about the installation or maintenance of compression fittings, consulting a professional plumber can provide the expertise needed to troubleshoot and resolve any problems.
In conclusion, compression fittings are reliable connectors that play a crucial role in ensuring the efficiency and integrity of plumbing systems. By understanding their benefits, installation process, and maintenance requirements, you can confidently utilize compression fittings for your plumbing needs.
Remember to always follow the manufacturer’s instructions and guidelines specific to the compression fittings you are using to ensure proper installation and usage.
With the knowledge gained from this article, you are now well-equipped to make informed decisions when it comes to using compression fittings in your plumbing projects.
Frequently Asked Questions about What Is A Compression Fitting In Plumbing
Was this page helpful?
At Storables.com, we guarantee accurate and reliable information. Our content, validated by Expert Board Contributors, is crafted following stringent Editorial Policies. We're committed to providing you with well-researched, expert-backed insights for all your informational needs.
0 thoughts on “What Is A Compression Fitting In Plumbing”