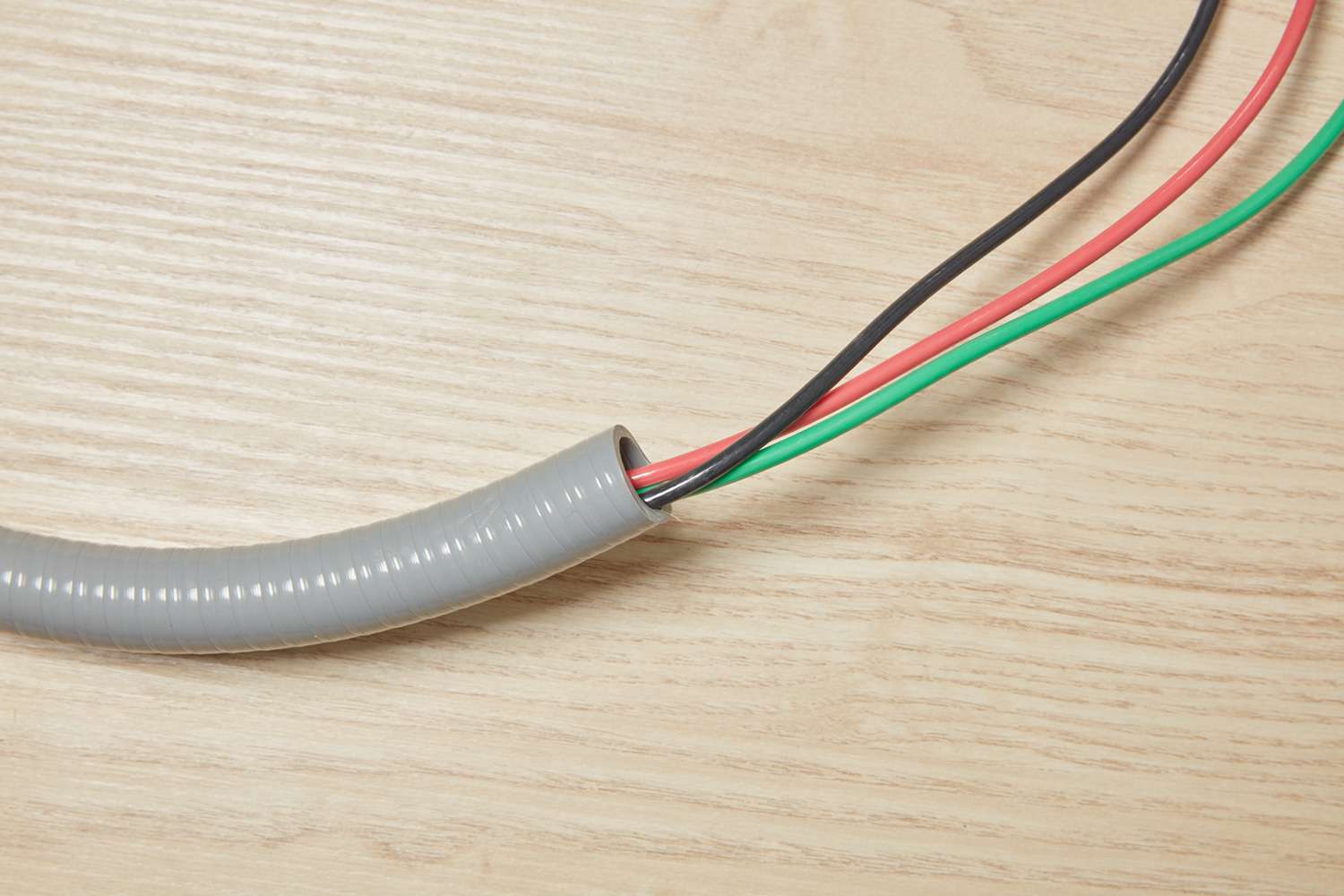
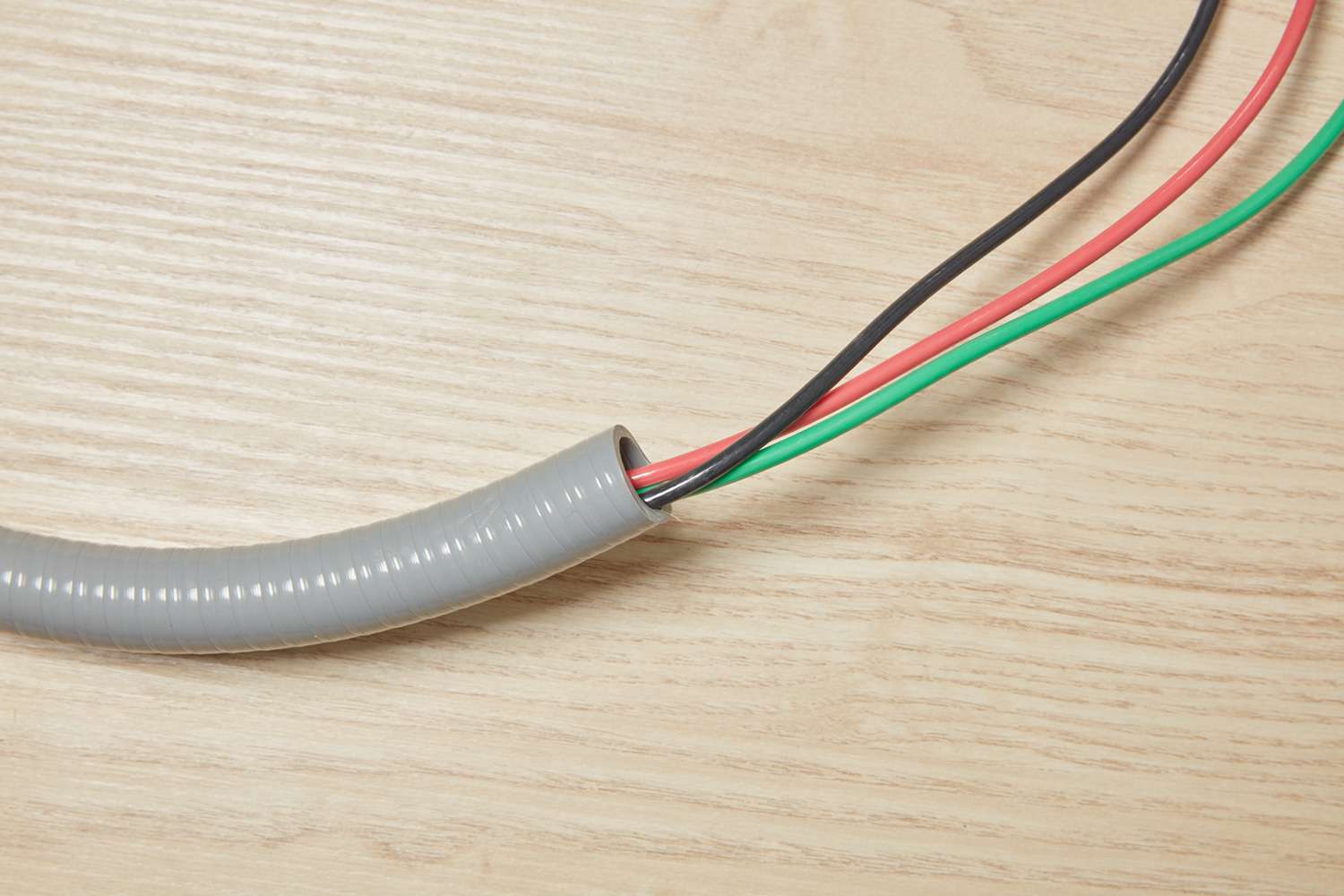
Articles
What Is An Electrical Wire
Modified: October 19, 2024
Learn about electrical wires in our collection of informative articles. Gain insights on types, sizes, and uses of wires in various electrical applications.
(Many of the links in this article redirect to a specific reviewed product. Your purchase of these products through affiliate links helps to generate commission for Storables.com, at no extra cost. Learn more)
Introduction
Electrical wire plays a crucial role in our daily lives, delivering power and electricity to different devices and systems. Whether it’s your home, office, or industrial building, electrical wire is the backbone of the electrical infrastructure. Understanding what an electrical wire is and its different aspects is essential for anyone working in the field of electrical engineering or even for homeowners looking to understand their electrical system better.
An electrical wire, simply put, is a conductive material that allows the flow of electricity from one point to another. It acts as a medium through which electrical energy is transmitted. These wires are composed of various materials and come in different types and sizes, each serving a specific purpose.
In this article, we will explore the different types of electrical wire, their uses, and some safety precautions associated with them. So let’s dive in and unravel the world of electrical wires.
Key Takeaways:
- Electrical wire is a versatile and essential component of our daily lives, providing power to residential, commercial, and industrial systems. Understanding its types, conductor materials, and safety precautions is crucial for safe and efficient electrical installations.
- Proper electrical wire sizing is critical for ensuring the safety and efficiency of an electrical system. Factors such as current carrying capacity, voltage drop, wire length, and environmental conditions must be considered to maintain functional and safe electrical systems.
Read more: What Is 4 Wire Electrical Wire
Definition of Electrical Wire
Electrical wire, also known as electrical cable or conductor, is a flexible or rigid structure made up of one or more conductive materials. It is designed to transmit electrical energy from one point to another within an electrical system. The wire acts as a pathway for electrons to flow, allowing the transfer of electric current to power electrical devices, appliances, and systems.
The most commonly used conductive materials in electrical wires include copper and aluminum. These materials have excellent conductivity properties, allowing for efficient electrical transmission.
Electrical wires are available in various sizes, referred to as wire gauges. The gauge of the wire determines its current-carrying capacity, with larger gauge numbers representing thinner wire diameters. Thicker wires are typically used for higher current applications, while thinner wires are suitable for lower power devices.
The construction of electrical wires involves several layers. The innermost layer is the conductor, which is the core material responsible for carrying the electrical current. It is surrounded by insulation, which acts as a protective barrier to prevent contact with other conductive materials or external factors that may cause electrical shock or short circuits.
Depending on the application, electrical wires may also have additional layers, such as a sheath or jacket. The sheath provides further protection and durability, especially in outdoor or harsh environments.
It is important to note that electrical wires are not limited to just solid or single-stranded structures. They can also be composed of multiple strands or bundles of thinner wires, known as stranded wires. The choice between solid or stranded wire depends on factors such as flexibility, durability, and the specific electrical application.
In summary, electrical wires are essential components of any electrical system, serving as the conduits for electricity to flow and power various devices. They are made up of conductive materials, have different gauges and layers, and are designed to safely transmit electrical energy throughout a system.
Types of Electrical Wire
Electrical wires come in various types, each designed for specific applications and environments. Understanding the different types of electrical wire is essential in selecting the most suitable wire for a particular electrical installation. Let’s explore some common types of electrical wire:
Solid Wire
Solid wire, also known as single-strand wire, is made up of a single, solid conductor. It is rigid and less flexible compared to stranded wire. Solid wire is commonly used in residential and commercial electrical wiring, particularly for permanent installations within walls and electrical panels. Its solid structure provides excellent conductivity and is less susceptible to damage, making it ideal for long-term applications.
Stranded Wire
Stranded wire consists of multiple strands of smaller conductors twisted together to form a flexible wire. The strands can be made from the same material or a combination of different materials. Stranded wire offers increased flexibility, making it suitable for applications that require frequent bending or movement. It is commonly used in appliances, vehicles, and electronic equipment.
Read more: What Is Electrical Wire Made Of
Insulated Wire
Insulated wire is any type of wire that has an additional layer of insulation around the conductor. The insulation provides electrical and mechanical protection, preventing contact with other conductive materials and reducing the risk of electrical shocks and short circuits. Common insulation materials include PVC (Polyvinyl Chloride) and Thermoplastic. Insulated wire is used in various electrical applications, including wiring systems, fixtures, and appliances.
Bare Wire
Bare wire refers to a wire without any insulation or protective covering. It is typically made of copper or aluminum and is primarily used in grounding systems or in situations where insulation is not required or prohibited. Bare wire is commonly used for grounding electrical circuits to ensure safety and provide a path for excess electrical current to dissipate.
Conductor Materials
Electrical wires are available in different conductor materials to suit various applications and environments. The two most commonly used materials are:
- Copper wire: Copper is known for its excellent conductivity and corrosion resistance. It is the preferred choice for most electrical wiring installations due to its superior electrical properties and durability.
- Aluminum wire: Aluminum is a lightweight and cost-effective alternative to copper. It is commonly used in large-scale electrical transmission and distribution systems. However, aluminum wire has a lower conductivity compared to copper and requires proper installation techniques to mitigate potential issues.
Keep in mind that the type of wire selected depends on factors such as the application requirements, environmental conditions, and specific electrical codes and regulations.
Understanding the different types of electrical wire is crucial in maintaining a safe and efficient electrical system. By selecting the appropriate wire type for each application, you can ensure reliable and long-lasting electrical installations.
Solid Wire
Solid wire, also known as single-strand wire, is a type of electrical wire that consists of a single, solid conductor. It is made from a single piece of metal, usually copper or aluminum, and is commonly used in various electrical applications.
One of the key characteristics of solid wire is its rigidity and lack of flexibility. Due to its solid structure, it is not as pliable as stranded wire. However, this rigidity makes solid wire more suitable for permanent installations, where the wire does not need to be moved or bent frequently.
One of the primary advantages of solid wire is its excellent conductivity. The absence of gaps between strands allows for efficient flow of electrical current, resulting in minimal resistance. This is especially important in applications where high conductivity is required, such as in electrical panels, outlets, and switches.
Another benefit of solid wire is its durability and resistance to damage. The solid conductor is less prone to breakage or fraying compared to stranded wire. This makes it suitable for installations that require long-term reliability, such as inside walls or in concealed electrical wiring.
Due to its rigid nature, solid wire is commonly used in residential and commercial electrical wiring. It is often used for permanent installations, such as running wires through walls, ceilings, and floors. Solid wire is also commonly found in electrical panels, circuit breakers, and outlets.
It is important to note that solid wire is not recommended for applications that involve frequent bending or movement. Its lack of flexibility may make it more susceptible to stress and potential breakage in such situations. For applications that require flexibility, stranded wire is the preferred choice.
In summary, solid wire is a single-strand electrical wire that offers excellent conductivity, durability, and reliability. It is commonly used for permanent installations where flexibility is not a requirement. Its rigidity and solid structure make it suitable for a wide range of residential and commercial electrical applications.
Read more: What Is Red In Electrical Wire
Stranded Wire
Stranded wire is a type of electrical wire that is composed of multiple smaller strands of conductive material twisted together. Unlike solid wire, which consists of a single, solid conductor, stranded wire offers increased flexibility and bendability, making it more suitable for certain applications.
The strands in stranded wire are typically made of copper or aluminum, which are excellent conductors of electricity. The number of strands and their thickness can vary, depending on the wire gauge and intended use. The strands are twisted together to create a cohesive and flexible wire structure.
The main advantage of stranded wire is its flexibility. The individual strands allow the wire to bend and flex more easily, making it ideal for applications that require movement or frequent bending. This flexibility makes stranded wire easier to work with during installations and allows for easier routing of wires around corners or through tight spaces.
In addition to improved flexibility, stranded wire offers other benefits as well. The multiple strands reduce the overall resistance of the wire, resulting in lower voltage drops and better transmission of electrical current. This makes stranded wire suitable for applications that involve higher currents or longer wire runs.
Stranded wire is commonly used in a variety of electrical applications. For example, it is often found in household appliances, automotive wiring, electronic devices, and portable cords. It is also commonly used in situations where vibrations or movement may occur, such as in machinery or robotics.
When selecting stranded wire, it is important to consider the wire gauge and the number of strands. Thicker wire gauges are suitable for applications that require higher current carrying capacity, while thinner gauges are used for lower power applications. The number of strands can affect the flexibility of the wire, with more strands generally providing greater flexibility.
Overall, stranded wire offers improved flexibility and bendability compared to solid wire. It is a popular choice for applications that require movement, vibrations, or flexibility. Its ability to transmit electrical current efficiently makes it well-suited for various electrical and electronic applications.
Insulated Wire
Insulated wire is a type of electrical wire that has an additional layer of insulation around the conductor. The insulation serves as a protective barrier, preventing contact with other conductive material and reducing the risk of electrical shock or short circuits. Insulated wire is commonly used in a wide range of electrical applications, providing safety and reliability.
The insulation layer on the wire is typically made of materials such as PVC (Polyvinyl Chloride), Thermoplastic, or Rubber. These materials offer excellent electrical insulation properties and protect the conductor from the surrounding environment.
One of the primary purposes of insulation is to prevent electrical contact with objects or individuals. The insulation layer acts as a barrier, preventing the flow of electricity to unintended areas or surfaces. This is particularly important in applications where wires are exposed, such as power outlets, switches, and electrical cords.
Insulated wire also provides mechanical protection to the conductor. It helps safeguard the wire from damage due to bending, abrasion, or environmental factors. The insulation layer can resist moisture, chemicals, and temperature variations, prolonging the lifespan of the wire and ensuring its performance.
There are various types of insulated wire available, each designed for specific applications. For instance, building wire is used for electrical installations in residential and commercial buildings. It is typically color-coded for easy identification and comes in different ratings based on voltage and current capacity.
Automotive wire, on the other hand, is specifically designed for use in vehicles, with insulation that is resistant to heat, oil, and other automotive fluids. This wire is often marked with specific specifications, such as SAE (Society of Automotive Engineers) ratings.
Insulated wire is also commonly used in appliances, where the conductors need to be protected from external factors. Whether it’s a refrigerator, washing machine, or computer, insulated wires ensure the safe and reliable operation of these electrical devices.
When working with insulated wire, it is important to choose the appropriate wire size and insulation type for the specific application. This ensures compatibility with the electrical load and environment, preventing any safety hazards or performance issues.
In summary, insulated wire provides essential protection for electrical conductors, preventing electrical shocks, short circuits, and damage. The insulation layer acts as a barrier, safeguarding the conductor and enhancing the safety and reliability of electrical installations. Proper selection and use of insulated wire are crucial in maintaining a safe electrical system.
Bare Wire
Bare wire, as the name suggests, is a type of electrical wire that does not have any insulation or protective covering on its conductor. It is a bare metal wire that is commonly made of copper or aluminum.
Bare wire is primarily used in specific electrical applications where insulation is not necessary or prohibited. One of the most common uses of bare wire is in grounding systems. In electrical systems, grounding is a vital safety measure that helps redirect electrical faults and excess current to the earth, preventing electrical shocks and equipment damage.
In grounding applications, bare wire is typically installed as a grounding conductor. It provides a low-resistance path for excess electrical current to flow into the earth, helping to protect people, devices, and structures from electric faults and surges.
Another notable application of bare wire is in overhead power lines. For long-distance transmission and distribution of electricity, bare aluminum conductors are often used due to their lightweight nature. The absence of insulation reduces weight and cost, allowing for cost-effective power transmission over long distances.
It is worth noting that while bare wire has its specific uses, it requires careful installation and maintenance. Without the protection of insulation, bare wire is more susceptible to environmental factors, such as moisture and corrosion. Proper installation techniques, such as secure fastening and periodic inspection, are essential for maintaining the integrity and safety of bare wire installations.
Additionally, it’s important to adhere to local electrical codes and regulations when working with bare wire. These codes outline specific guidelines for installation methods, wire sizing, and safety requirements to ensure compliance and mitigate potential risks.
When working with bare wire, it’s crucial to take appropriate safety precautions. Protective equipment, such as gloves and insulating tools, should be used to prevent electrical shock or accidental contact with live parts. It’s also important to ensure that bare wire installations are properly grounded and that any connections are secure and corrosion-resistant.
In summary, bare wire is an electrical wire without any insulation or protective covering on the conductor. It is commonly used in grounding systems and overhead power lines. While it has specific applications, caution should be exercised during installation and maintenance to ensure safety and compliance with electrical codes and regulations.+
Conductor Materials
Electrical wires are available in different conductor materials, each offering unique characteristics and suitability for specific applications. The two most commonly used conductor materials in electrical wiring are copper and aluminum.
Read more: What Is A White Electrical Wire
Copper Wire
Copper wire is widely regarded as the standard conductor material for electrical applications. Copper is known for its excellent electrical and thermal conductivity, making it highly efficient in the transmission of electrical current. It has low resistance, which minimizes energy losses and ensures efficient power distribution.
In addition to its superior conductivity, copper wire exhibits excellent corrosion resistance and high mechanical strength. This combination of properties makes copper wire highly durable, capable of withstanding harsh environments and prolonged use without deterioration in performance. Copper wiring is commonly used in residential, commercial, and industrial applications, from household wiring to industrial machinery.
Copper wire also offers flexibility, making it easier to work with during installation. It can be easily bent, twisted, and routed through tight spaces, allowing for greater versatility in wiring applications. The flexibility of copper wire reduces the risk of breakage or damage during installation and ensures a secure and reliable connection.
Aluminum Wire
Aluminum wire is an alternative conductor material used in certain electrical applications. It is lighter in weight and more cost-effective compared to copper wire, making it a suitable option for long-distance transmission and distribution systems. Aluminum wire is commonly used in overhead power lines, where its lightweight nature helps reduce strain on supporting structures.
While aluminum wire offers advantages in terms of cost and weight, it has a higher resistance compared to copper wire. This resistance results in higher energy losses and can potentially lead to more significant voltage drops. Therefore, aluminum wire requires larger wire sizes or more substantial conductors to achieve the same current-carrying capacity as copper wire. Proper installation techniques, such as ensuring secure connections and using specialized aluminum-compatible connectors, are crucial for the safe and effective use of aluminum wire.
It is important to note that compatibility issues may arise when connecting copper and aluminum wiring. The dissimilar metals can lead to galvanic corrosion, which can compromise the integrity of the connections over time. To address this, special connectors known as “Al/Cu” or “CO/ALR” connectors are used to eliminate the risk of corrosion and ensure reliable connections between copper and aluminum wire.
In summary, copper and aluminum are the most commonly used conductor materials in electrical wiring. Copper wire offers excellent electrical and thermal conductivity, durability, and flexibility, making it the preferred choice for most electrical applications. Aluminum wire, on the other hand, is lighter and more cost-effective, making it suitable for long-distance power transmission. Proper installation techniques and consideration of compatibility issues are essential when working with these conductor materials to ensure safe and efficient electrical systems.
Copper Wire
Copper wire is one of the most widely used conductor materials in electrical wiring. It is valued for its exceptional conductivity, durability, and versatility, making it the preferred choice for a wide range of applications.
One of the key advantages of copper wire is its excellent electrical conductivity. Copper is highly conductive, allowing electrical current to flow through the wire with minimal resistance. This low resistance results in efficient transmission of electricity, reducing energy loss and ensuring reliable power delivery. The high conductivity of copper also facilitates faster and more efficient heat dissipation, enhancing the overall performance and longevity of electrical systems.
In addition to its conductivity, copper wire exhibits impressive mechanical properties. It is highly ductile and malleable, which means it can be easily shaped and formed without breaking. This flexibility makes copper wire easy to handle and install, allowing for smooth and efficient wiring processes. The malleability of copper wire also enables it to withstand bending and twisting without compromising its structural integrity.
Copper wire is also known for its exceptional durability and resistance to corrosion. Copper has a natural resistance to moisture, chemicals, and atmospheric elements, ensuring long-term reliability even in harsh environments. Its resistance to corrosion allows copper wire to maintain its electrical performance over extended periods, minimizing the risk of insulation damage or electrical failures.
Furthermore, copper wire is highly compatible with various insulation materials, making it suitable for both residential and commercial applications. Its compatibility ensures secure and reliable insulation, protecting the wire from external factors and reducing the risk of electrical shock or short circuits.
Due to its superior conductivity and durability, copper wire is commonly used in a wide range of electrical installations. It is widely employed in residential buildings for wiring systems, electrical outlets, switches, and lighting fixtures. In commercial and industrial applications, copper wire is used for power distribution, electrical machinery, communication systems, and more.
Copper wire is also a preferred choice in industries where high reliability and performance are crucial, such as aerospace, telecommunications, and automotive sectors. Its excellent electrical properties and proven track record make it an indispensable component in these demanding applications.
In summary, copper wire is highly regarded for its exceptional conductivity, durability, and versatility. Its superior electrical and mechanical properties make it the preferred choice for a wide range of electrical applications, from residential wiring to industrial installations. The reliability, longevity, and superior performance of copper wire have solidified its place as a staple in the world of electrical engineering.
Aluminum Wire
Aluminum wire is a conductor material that offers a lightweight and cost-effective alternative to copper wire. It is commonly used in various electrical applications, particularly in situations where weight and cost are significant considerations.
One of the primary advantages of aluminum wire is its lighter weight compared to copper. Aluminum is less dense than copper, making it a preferred choice for applications that involve long-distance power transmission or situations where weight reduction is important. The lighter weight of aluminum wire helps reduce strain on supporting structures and simplifies installation processes.
In addition to its lighter weight, aluminum wire is more cost-effective than copper. Aluminum is abundant and less expensive compared to copper, making it an attractive option in projects with larger wiring requirements or tight budgets. The cost savings associated with aluminum wire can be significant for industries and projects that require extensive wiring installations.
However, it’s important to note that compared to copper wire, aluminum has a higher resistance. This means that a larger diameter aluminum wire is required to carry the same current as a copper wire. Without proper consideration, using smaller gauge aluminum wire can result in higher resistance, voltage drops, and potential issues with electrical performance.
Another factor to consider when working with aluminum wire is its lower tensile strength compared to copper. This means that aluminum wire is less resilient when it comes to mechanical stress, such as bending or twisting. Special care must be taken during installation to prevent damage to the wire, as it is more prone to breakage or deformation compared to copper wire.
To mitigate the challenges associated with aluminum wire, proper installation techniques and connectors designed specifically for aluminum wire are crucial. These connectors, often labeled as “CO/ALR” or “Al/Cu,” are approved for making safe and reliable connections between aluminum wire and copper wire or devices.
It is also important to note that in certain applications and regions, the use of aluminum wire may be subject to specific regulations and guidelines. Consulting local electrical codes and standards is essential to ensure compliance and safety when using aluminum wire.
In summary, aluminum wire offers a cost-effective and lightweight alternative to copper wire. Its lighter weight makes it suitable for long-distance power transmission and projects where weight reduction is important. However, proper installation techniques, larger wire sizes, and the use of appropriate connectors are essential to ensure safe and reliable electrical connections when working with aluminum wire.
Read more: What Is SOOW Electrical Wire
Uses of Electrical Wire
Electrical wire plays a crucial role in powering various devices and systems, making it an essential component in countless applications. Let’s explore some of the common uses of electrical wire:
Residential Wiring
One of the primary uses of electrical wire is in residential wiring. Electrical wires are responsible for delivering power to outlets, switches, lighting fixtures, and appliances throughout the home. They are used for both general-purpose electrical circuits, such as lighting and outlets in living spaces, as well as specialized circuits for specific appliances like refrigerators, air conditioners, and stoves.
Industrial Wiring
In industrial settings, electrical wire is used extensively for power distribution, machinery, and control systems. It is utilized to connect motors, generators, transformers, and other electrical equipment. Industrial wiring systems often involve heavy-duty electrical cables and wire, capable of handling high voltages and currents associated with industrial operations.
Electrical Appliances
Electrical wire is also found in a wide range of appliances that we use every day. From kitchen appliances like refrigerators, ovens, and dishwashers to household electronics like televisions and computers, electrical wires are crucial for powering these devices. The wires inside appliances connect the various components and circuits, allowing them to function properly.
Read more: What Electrical Wire To Run Underground
Telecommunication Systems
The telecommunications industry heavily relies on electrical wire for the transmission of voice, data, and video signals. A complex network of wires connects telephone lines, cable TV systems, and internet infrastructure to ensure seamless communication. These wires are designed to handle high-frequency signals and transmit them over long distances with minimal loss.
Automotive Wiring
In automobiles, electrical wire is used for wiring systems, such as the vehicle’s ignition system, lighting, and entertainment systems. It connects various components, sensors, and switches throughout the vehicle to facilitate electrical functions. The wires used in automotive applications are designed to withstand vibrations, extreme temperatures, and other challenging conditions.
Renewable Energy Systems
With the rise of renewable energy sources like solar and wind power, electrical wire is crucial for connecting the power generated by these systems to the electrical grid. Wires are used to transport and distribute the electricity from solar panels or wind turbines to homes, businesses, and the electric power grid.
These are just a few examples of the many uses of electrical wire. Whether it’s in residential, commercial, industrial, or specialized applications, electrical wiring is vital for enabling the safe and reliable distribution of electrical power and connectivity in various systems and devices that power our modern world.
Residential Wiring
Residential wiring refers to the electrical system that delivers power and connectivity to homes, ensuring the safe and efficient distribution of electricity throughout the various living spaces. It involves a complex network of electrical wires, circuits, outlets, and switches, providing power for lighting, appliances, and other electrical devices within the home.
Residential wiring typically starts at the main electrical panel, also known as the breaker box or distribution board. This panel acts as the central hub, receiving power from the utility company and distributing it to different circuits throughout the house. The panel contains circuit breakers or fuses that protect each circuit from overloads or short circuits, ensuring electrical safety.
The wiring system in a house is divided into different circuits, each serving a specific purpose. There are separate circuits for lighting, outlets, kitchen appliances, HVAC systems, and more. These circuits are designed to handle specific electrical loads and prevent excessive current flow that could cause damage or fires.
Electrical wires, typically made of copper, connect the electrical panel to outlets, switches, and lighting fixtures. The most commonly used wiring method is called Romex, which consists of multiple insulated wires, including a hot wire, a neutral wire, and a ground wire, all contained within a non-metallic sheathing for safety.
Outlets and switches are junction points where electrical devices are connected to the wiring system. Outlets provide power for appliances, lamps, and other electrical equipment, while switches control the on and off function of lighting fixtures and fans. These devices are strategically placed throughout the house to ensure convenient and safe access to electrical power.
Each room in a residential property has specific electrical requirements that must be met during the wiring process. Kitchen and bathroom areas, for example, have stringent electrical codes and regulations due to the use of water and the presence of specific appliances. GFCI (Ground Fault Circuit Interrupter) outlets are commonly installed in areas where water is present to protect against electrical shock.
In recent years, residential wiring has also seen advancements in technology, with the integration of smart home features. Wiring systems are now designed to accommodate devices that control lighting, thermostats, security systems, and entertainment systems, all linked to a home automation network. This allows homeowners to remotely control and monitor their electrical systems, enhancing convenience, comfort, and energy efficiency.
It is important to note that residential wiring should only be undertaken by qualified electricians who are familiar with local electrical codes and regulations. Proper installation techniques and adherence to safety standards are critical to ensure a safe and reliable electrical system in the home.
In summary, residential wiring is the backbone of the electrical system in a house, providing power and connectivity for lighting, appliances, and other electrical devices. It involves a network of wires, circuits, outlets, and switches that must be designed and installed according to electrical codes and safety standards. A properly wired home ensures the safe and efficient distribution of electricity, enabling homeowners to enjoy a reliable and comfortable living environment.
Read more: What Kind Of Copper Is Electrical Wire
Industrial Wiring
Industrial wiring refers to the electrical infrastructure used in industrial settings, such as factories, warehouses, and manufacturing facilities. It involves a complex network of electrical systems designed to provide power, control, and connectivity for a wide range of machinery, equipment, and processes.
Industrial wiring is characterized by its robustness, reliability, and capacity to handle high voltage and current loads. It is designed to meet the specific demands of various industrial operations, including the power requirements of heavy machinery, motors, and production lines.
The wiring in an industrial facility typically starts at the main electrical panel, where power from the grid is distributed to various electrical circuits. Industrial electrical panels are often larger and more powerful than those found in residential settings, as they need to handle higher current levels. These panels are equipped with circuit breakers, fuses, or other protective devices to prevent overloads or short circuits.
Industrial wiring systems often involve three-phase power, which provides a more efficient and balanced distribution of electricity compared to single-phase power used in residential wiring. Three-phase power allows for more stable operation of industrial machinery and reduces power losses across long distances.
Large conduits and cable trays are used to route the electrical wires throughout the industrial facility. These wiring conduits and trays protect the wiring from physical damage and provide a neat and organized system for easy maintenance and troubleshooting.
Industrial wiring serves a multitude of purposes within industrial settings:
Power Distribution
The primary function of industrial wiring is to distribute electrical power from the main electrical panel to different areas of the facility. This includes providing power to machines, equipment, lighting, and other electrical devices within the industrial setting. Different electrical loads may require separate circuits or dedicated power supplies to ensure optimal performance.
Machinery and Equipment
Heavy machinery and equipment are essential components of industrial operations. Industrial wiring connects motors, drives, control systems, and sensors to these machines, allowing for precise control and operation. The wiring system provides the electrical power necessary for the operation of motors, conveyors, pumps, compressors, and other industrial equipment.
Control Systems
Industrial facilities often incorporate complex control systems to monitor and regulate industrial processes. These control systems utilize various sensors and programmable logic controllers (PLCs) that require extensive wiring to connect and communicate with each other. Industrial wiring facilitates the integration of control systems, enabling efficient automation and control of processes.
Read more: What Color Is Black In Electrical Wire
Lighting Systems
An adequate and well-designed lighting system is imperative for maintaining a safe and productive working environment. Industrial wiring includes the installation of lighting fixtures and controls, ensuring sufficient lighting levels throughout the facility. Lighting systems in industrial settings are often designed to be durable, energy-efficient, and capable of withstanding harsh environmental conditions.
Industrial wiring demands stringent adherence to safety standards, compliance with industry regulations, and the expertise of skilled electricians. The complexity and high-power requirements of industrial electrical systems necessitate precision installation, regular maintenance, and proper grounding to ensure optimal performance and electrical safety.
In summary, industrial wiring is responsible for providing power, control, and connectivity in industrial settings. It enables the distribution of electrical power to machinery, equipment, and control systems, ensuring the smooth operation of industrial processes. Properly designed and installed industrial wiring systems are crucial for productivity, safety, and the efficient functioning of industrial facilities.
Electrical Appliances
Electrical appliances are an integral part of our daily lives, providing convenience, comfort, and functionality. From kitchen appliances to household electronics, electrical appliances rely on electrical wiring to deliver power and enable their operation.
Electrical appliances encompass a wide range of devices that serve various purposes:
Kitchen Appliances
Electrical appliances are found in abundance in the kitchen, providing essential functions for cooking, food storage, and preparation. These appliances include refrigerators, stoves, ovens, microwaves, dishwashers, and small appliances like blenders, toasters, and coffee makers. Electrical wiring delivers power to these appliances, allowing for the efficient operation of heating elements, motors, and control systems.
Laundry Appliances
Laundry appliances such as washing machines and dryers are commonly used in households. These appliances utilize electrical wiring to power their motors, heating elements, and control systems, enabling the washing and drying of clothes. Modern appliances may also incorporate smart features, allowing remote control and monitoring via home automation systems.
Read more: What Gauge Is House Electrical Wire
Home Entertainment Systems
Television sets, home theater systems, gaming consoles, and audio systems are some examples of electrical appliances used for home entertainment. These appliances require electrical wiring to connect and power their various components, ensuring a seamless audio and visual experience for users. In recent years, advancements in technology have seen the integration of wireless connectivity, allowing for easy streaming of content.
Computers and Electronics
Computers, laptops, tablets, and smartphones are examples of electrical appliances that have become indispensable in our lives. These devices rely on electrical wiring to power their internal components, including processors, memory, displays, and connectivity modules. They facilitate communication, productivity, and entertainment, and they play a vital role in our interconnected world.
Heating, Ventilation, and Air Conditioning (HVAC) Systems
HVAC systems keep our homes and workplaces comfortable by regulating temperature, humidity, and air quality. These systems rely on electrical appliances, such as air conditioners, heaters, fans, and ventilation systems. Electrical wiring connects these appliances to the electrical supply, allowing for efficient control and operation.
Small Household Appliances
Small electrical appliances abound in households, offering convenience for various tasks. These appliances include vacuum cleaners, hair dryers, electric toothbrushes, irons, and many others. They rely on electrical wiring to power their motors, heating elements, and electronic controls, making daily chores and personal care easier and more efficient.
Given the significance of electrical appliances in our lives, it is essential to ensure proper electrical wiring installation and maintenance. Faulty or inadequate wiring can lead to safety hazards, functionality issues, or electrical failures. By following electrical codes and relying on professional electricians for installation and repairs, we can ensure the safety, efficiency, and longevity of our electrical appliances.
In summary, electrical appliances cover a broad range of devices that enhance our daily lives. From kitchen appliances to home entertainment systems and personal gadgets, electrical wiring is vital for their operation. Proper installation and maintenance of electrical wiring play a critical role in ensuring the functioning and safety of our electrical appliances.
Read more: What Is Blue Electrical Wire Used For
Safety Precautions with Electrical Wire
Working with electrical wire requires utmost caution and adherence to safety measures to prevent electrical shocks, fires, and other hazards. Whether you’re a homeowner performing simple electrical tasks or a professional electrician, here are some important safety precautions to keep in mind:
1. Turn Off Power
Before working on any electrical wiring, always ensure that the power to the circuit you’re working on is turned off. Switch off the circuit breaker or remove the fuse associated with the specific circuit to prevent the flow of electricity. Use a non-contact voltage tester to confirm that there is no live current before touching or working on any wires.
2. Use Proper Insulation
Insulation acts as a protective barrier between electrical conductors and other materials or components. Ensure that all electrical wires are correctly insulated, and never expose live wires. Any damaged or worn-out insulation should be repaired or replaced immediately to avoid potential electrical hazards.
3. Avoid Overloading Circuits
Each electrical circuit has a maximum load capacity. Avoid plugging in too many appliances or devices into a single circuit, as it can overload the circuit and lead to overheating, tripped circuit breakers, or electrical fires. Spread out the electrical load among different circuits, especially for high-power appliances like space heaters or air conditioners.
Read more: What Is Electrical Wire Insulation Made Of
4. Proper Grounding
Proper grounding is essential for electrical safety. All electrical systems should be grounded to a suitable grounding electrode system by connecting the grounding wire to ensure the safe dissipation of electrical faults or excess current. Consult local electrical codes and regulations to ensure compliance with grounding requirements.
5. Beware of Wet Conditions
Avoid working with electrical wires or devices in wet or damp conditions. Water is an excellent conductor of electricity and increases the risk of electrical shock. Ensure that your hands, tools, and work area are dry before handling any electrical components or performing electrical work.
6. Use Protective Equipment
When working with electrical wires, wear appropriate personal protective equipment (PPE) to minimize the risk of injury. This may include insulated gloves, safety goggles, and non-conductive footwear. PPE provides an additional layer of protection against potential electrical shocks or arc flashes.
7. Avoid DIY If Uncertain
If you are uncertain or uncomfortable with electrical work, it’s best to leave it to a qualified electrician. Attempting complex electrical tasks without proper knowledge and training can be dangerous and lead to hazardous conditions. Remember, safety should always be the top priority when working with electrical wires.
In summary, electrical work should always be approached with caution, and safety precautions should be followed diligently. Remember to turn off power, use proper insulation, avoid overloading circuits, ensure proper grounding, be cautious in wet conditions, use protective equipment, and seek professional help if needed. By prioritizing safety, you can minimize the risk of accidents and maintain a safe working environment when dealing with electrical wire.
Read more: What Kind Of Electrical Wire To Use Outside
Electrical Wire Sizing
Proper electrical wire sizing is crucial for ensuring the safety and efficiency of an electrical system. Using the correct wire size ensures that the wire can handle the specific electrical load without overheating or causing voltage drops. There are several factors to consider when sizing electrical wires:
1. Current Carrying Capacity
The primary consideration in wire sizing is the current carrying capacity, often referred to as ampacity. The wire size must be able to handle the maximum current expected to flow through it without exceeding its ampacity rating. The ampacity rating is determined by the wire’s gauge (AWG – American Wire Gauge) and its material, such as copper or aluminum.
2. Voltage Drop
Another important consideration is voltage drop. Voltage drop refers to the reduction in voltage that occurs as current flows through the wire due to its resistance. Excessive voltage drop can lead to poor electrical performance and potential damage to devices or appliances. Wire size should be selected to minimize voltage drop, especially for long wire runs or circuits with high current demands.
3. Wire Length and Circuit Distance
The length of the wire, as well as the distance from the power source to the load, affects the selection of wire size. Longer wire runs tend to have higher resistance and, as a result, can experience greater voltage drops. The longer the circuit distance, the larger the wire gauge required to compensate for the voltage drop.
4. Environmental Conditions
Consideration should also be given to environmental conditions. Different environments, such as high temperatures or corrosive atmospheres, can impact wire performance. In some cases, the wire may need to be sized up to account for these factors and ensure long-term durability and reliability.
5. Electrical Codes and Regulations
Electrical codes and regulations play a vital role in determining the appropriate wire size for specific applications. Each jurisdiction may have its own set of codes and requirements that dictate the minimum wire size for certain applications, including residential, commercial, and industrial installations. Consulting with local electrical codes and regulations is essential to ensure compliance and safe installation.
Wire sizing charts, ampacity tables, and online calculators are available to assist in determining the optimal wire size based on the specific requirements of the electrical load and system. These resources take into account factors such as current rating, wire material, ambient temperature, and voltage drop limits.
It is important to note that undersized wires can lead to overheating, while oversized wires can be unnecessarily expensive and difficult to work with. Proper wire sizing strikes a balance between safety, electrical performance, and cost-effectiveness.
In summary, electrical wire sizing is a critical aspect of electrical installations. The size of the wire must be suitable for the expected current, length of the circuit, voltage drop limitations, environmental conditions, and compliance with electrical codes and regulations. When in doubt, it is advisable to consult with a qualified electrician or refer to industry-standard references to ensure proper wire sizing for a safe and efficient electrical system.
Conclusion
Electrical wire is a fundamental component of our modern world, enabling the safe and efficient transmission of electrical energy. Understanding the different types, conductor materials, and uses of electrical wire is essential for anyone working with or relying on electrical systems.
From residential wiring to industrial installations, electrical wire plays a vital role in powering our homes, offices, and industries. Solid wire provides rigidity and durability for permanent installations, while stranded wire offers flexibility for applications that require frequent movement or bending. Insulated wire ensures safety by providing a protective barrier, preventing electrical shocks and short circuits.
Copper wire, known for its excellent conductivity and durability, is the preferred choice for most electrical wiring applications. Its reliability and superior electrical properties make it ideal for residential, commercial, and industrial use. Aluminum wire, on the other hand, offers a cost-effective and lightweight alternative for long-distance power transmission.
Electrical wire finds its way into numerous electrical appliances that enhance our daily lives. From kitchen appliances to entertainment systems and electronics, these devices rely on electrical wiring to transmit power and enable their operation. Safety precautions are essential when working with electrical wire, including turning off power, using proper insulation, and following appropriate grounding techniques.
Electrical wire sizing is a crucial aspect of electrical installations, ensuring the safe and efficient distribution of electrical currents. Proper wire sizing considers factors such as current carrying capacity, voltage drop, wire length, and environmental conditions. Adherence to electrical codes and regulations is also essential to ensure compliance and safety.
In conclusion, electrical wire serves as the foundation of our electrical infrastructure, enabling the safe and reliable transmission of electricity to power our homes, businesses, and industries. Understanding its various types, conductor materials, uses, safety precautions, and sizing guidelines is vital in maintaining functional and safe electrical systems.
Whether you’re a homeowner, electrician, or someone interested in understanding the intricacies of electrical wire, equipping yourself with knowledge about this crucial component of our electrical systems empowers you to make informed decisions and ensure the efficiency and safety of electrical installations.
Frequently Asked Questions about What Is An Electrical Wire
Was this page helpful?
At Storables.com, we guarantee accurate and reliable information. Our content, validated by Expert Board Contributors, is crafted following stringent Editorial Policies. We're committed to providing you with well-researched, expert-backed insights for all your informational needs.
0 thoughts on “What Is An Electrical Wire”