Home>Articles>Which Would Ultimately Cause The Armature In An Electric Motor To Spin
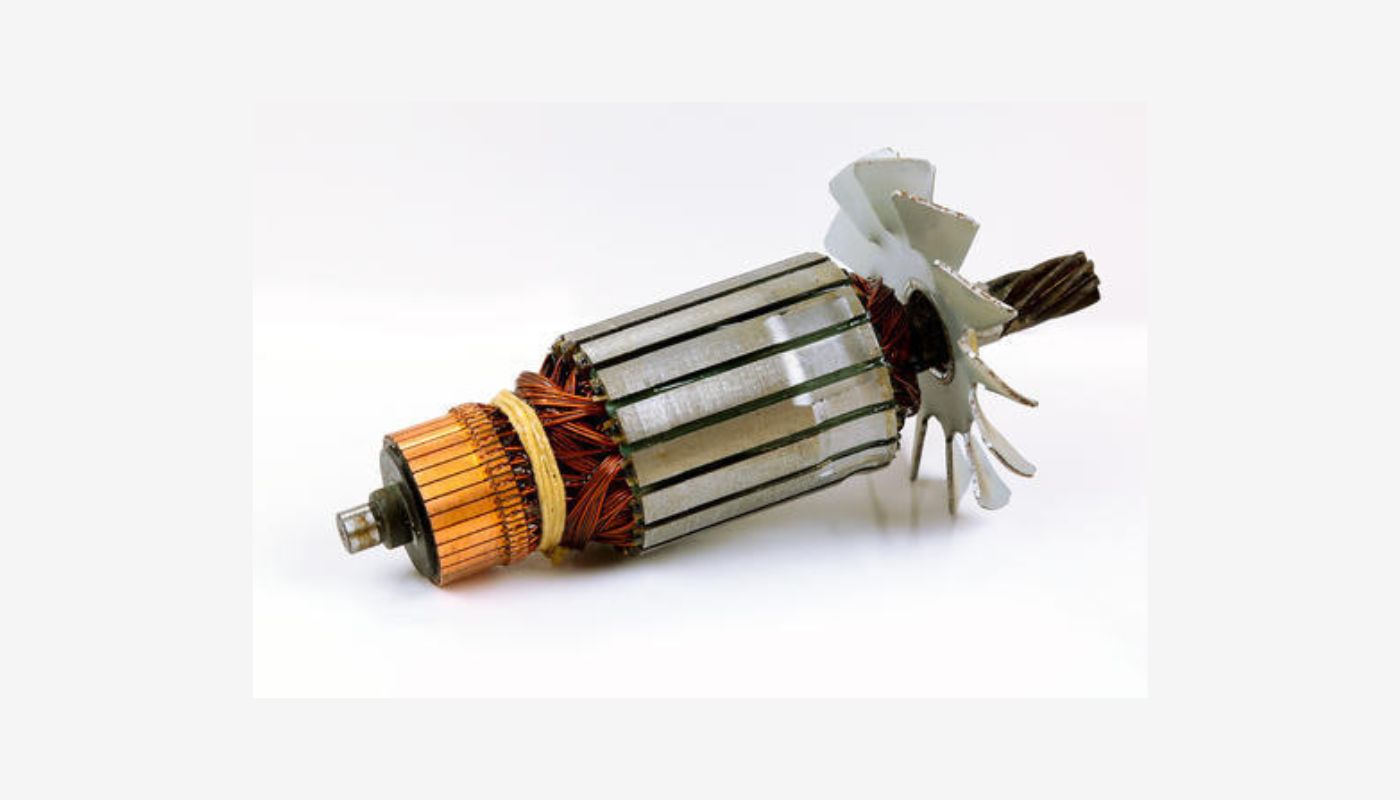
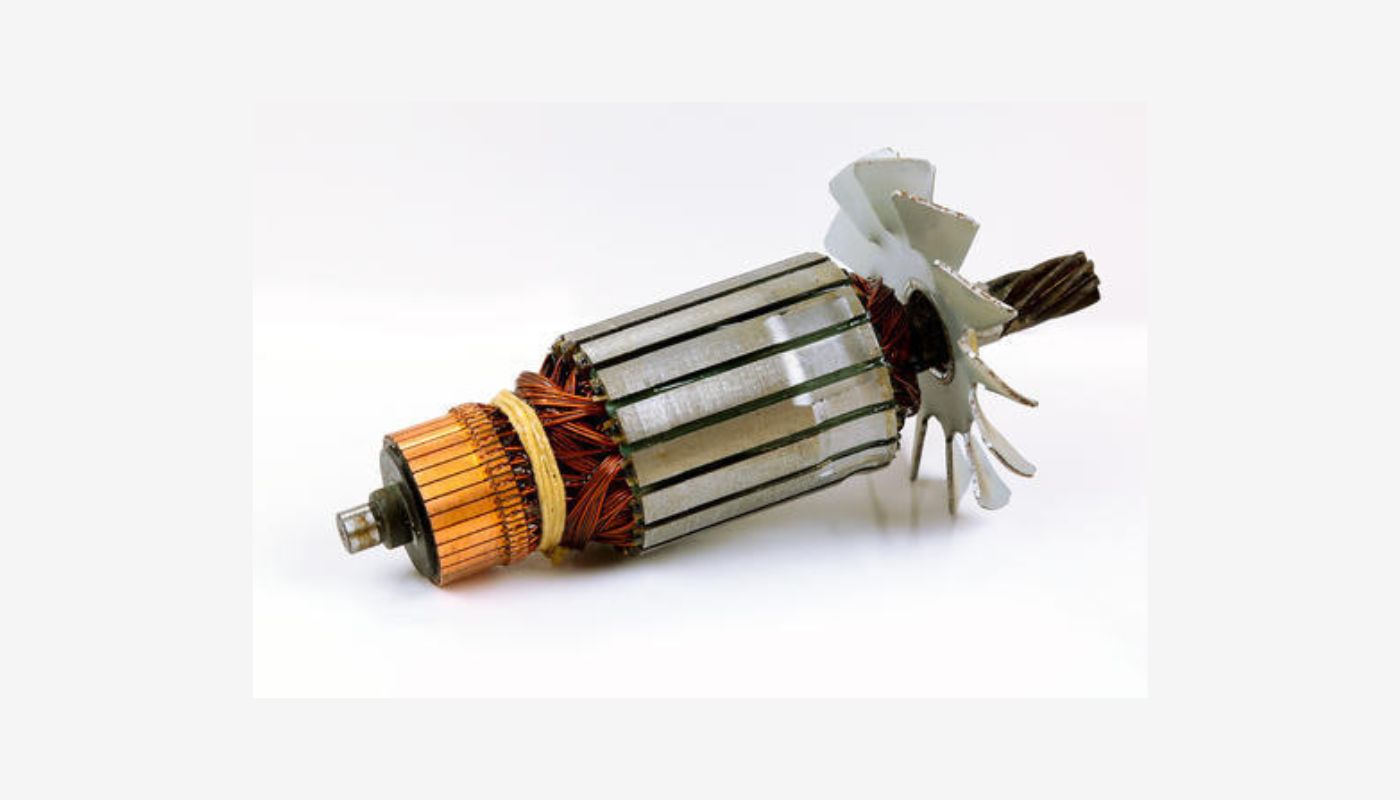
Articles
Which Would Ultimately Cause The Armature In An Electric Motor To Spin
Modified: August 26, 2024
Discover what causes the armature in an electric motor to spin in this informative article, packed with expert insights on the inner workings of electric motors.
(Many of the links in this article redirect to a specific reviewed product. Your purchase of these products through affiliate links helps to generate commission for Storables.com, at no extra cost. Learn more)
Introduction
Electric motors have revolutionized numerous industries and technologies, providing us with the power to propel vehicles, operate machinery, and generate electricity. At the heart of these motors lies the armature, a critical component responsible for converting electrical energy into mechanical motion. Understanding the intricacies of how the armature functions is key to comprehending the inner workings of electric motors.
In this article, we will delve into the principle of electromagnetism and explore the factors that influence the rotation of an armature in an electric motor. By gaining insight into these concepts, we can grasp the fundamental mechanisms that allow an electric motor to generate rotational motion.
So, let’s embark on this electrifying journey and uncover the secrets behind the spinning of the armature!
Key Takeaways:
- The spinning of the armature in an electric motor is driven by the fascinating principles of electromagnetism, showcasing the seamless conversion of electrical energy into mechanical motion.
- Factors such as current strength, magnetic field, commutator design, and motor construction all influence the speed and efficiency of the armature spin, highlighting the intricate balance required for optimal motor performance.
Read more: What Causes An Electric Motor To Overheat
The Principle of Electromagnetism
To understand how the armature in an electric motor spins, we must first grasp the basic principle of electromagnetism. Electromagnetism is the study of the relationship between electricity and magnetism, where electrical currents generate magnetic fields and vice versa.
This principle was first discovered by the Danish physicist Hans Christian Ørsted in 1820, who found that a compass needle located near a wire carrying an electric current would deflect. This observation led to the realization that electricity and magnetism are intrinsically linked.
When an electric current flows through a wire, it creates a magnetic field around it. The strength of the magnetic field depends on the magnitude of the current and the distance from the wire. This magnetic field can be enhanced by coiling the wire into a solenoid, which increases the number of wire loops and thus amplifies the magnetic effect.
Conversely, a magnetic field can induce an electric current in a nearby wire when the intensity of the magnetic field changes. This phenomenon is known as electromagnetic induction and was discovered by the English scientist Michael Faraday in the 1830s. Faraday’s experiments demonstrated that a moving magnet or a changing magnetic field could generate an electric current in a conductor.
This principle of electromagnetic induction is the driving force behind the rotation of the armature in an electric motor. By applying the concept of electromagnetism, we can harness the power of electricity to create mechanical motion and drive various devices.
Understanding the Armature in an Electric Motor
The armature is a critical component in an electric motor that converts electrical energy into mechanical motion. It consists of a cylindrical core, typically made of laminated iron or steel, with a series of wire windings wrapped around it. These wire windings are known as the armature coils.
The armature coils are arranged in a specific pattern, with each coil connected to a segment of the commutator. The commutator is a cylindrical structure made of copper segments that are insulated from each other. It is mounted on the same shaft as the armature and rotates with it.
When an electric current flows through the armature coils, it generates a magnetic field around them. This magnetic field interacts with the magnetic field produced by the field coils, which are stationary coils located around the armature. The interaction between these magnetic fields creates a force that causes the armature to rotate.
However, for the armature to continuously rotate, the direction of the current in the armature coils needs to change at regular intervals. This is where the commutator comes into play. As the armature rotates, the copper segments of the commutator come in contact with the brushes, which are stationary conductive contacts.
The brushes serve as the electrical connection between the power source and the armature coils. They deliver the electric current to different segments of the commutator, allowing the direction of the current in the armature coils to change as they move across the magnetic field produced by the field coils.
By constantly reversing the direction of the current in the armature coils through the action of the commutator and brushes, the armature experiences a torque that causes it to spin. This rotational motion is then harnessed to perform various tasks, such as driving a fan, powering a vehicle, or operating machinery.
Understanding the structure and function of the armature in an electric motor is crucial for comprehending how electrical energy is transformed into mechanical motion. The interaction between the magnetic fields, the role of the commutator and brushes, and the flow of current all contribute to the smooth rotation of the armature.
Interaction of Current and Magnetic Field
The interaction between an electric current and a magnetic field is the driving force behind the rotation of the armature in an electric motor. Understanding this interaction is crucial to comprehend how electrical energy is converted into mechanical motion.
When an electric current flows through the armature coils, it creates a magnetic field around them. This magnetic field interacts with the stationary magnetic field produced by the field coils, which are typically located outside the armature.
According to the right-hand rule, the interaction between these magnetic fields generates a force on the armature. The force is perpendicular to both the direction of the current and the magnetic field, resulting in a rotational motion.
The direction of the current in the armature coils determines the direction of the force acting on the armature. By reversing the direction of the current at regular intervals, the armature continuously experiences a torque that causes it to rotate.
The strength of the magnetic field is influenced by various factors, including the amount of current passing through the armature coils and the number of turns in the coils. Increasing the current or the number of turns enhances the magnetic field, resulting in a stronger force and faster rotation of the armature.
Similarly, the strength of the magnetic field produced by the field coils also plays a role in the interaction. By adjusting the strength of the field coils, it is possible to control the speed and torque of the armature rotation.
It’s important to note that the interaction between the current and magnetic field in the armature is not a one-way process. As the armature rotates, it cuts across the magnetic field lines produced by the field coils. This cutting of magnetic field lines induces a voltage in the armature coils, which in turn generates a back electromotive force (EMF).
The back EMF opposes the applied voltage and limits the current flowing through the armature coils. This is an important phenomenon in electric motors as it helps regulate the speed and prevent damage to the motor due to excessive currents.
By understanding the interaction between the current and magnetic field, we can appreciate how electric motors harness this phenomenon to convert electrical energy into mechanical motion. The proper control and manipulation of these forces enable electric motors to perform a wide range of tasks efficiently and effectively.
The armature in an electric motor spins due to the interaction between the magnetic field produced by the stator and the current flowing through the armature windings, creating a force known as the Lorentz force.
The Role of Brushes and Commutator
The brushes and commutator play a crucial role in the operation of an electric motor, specifically in the rotation of the armature. These components ensure the continuous and seamless flow of current to the armature coils, enabling the conversion of electrical energy into mechanical motion.
The brushes, typically made of carbon or graphite, are stationary conductive contacts positioned near the rotating commutator. Their purpose is to make electrical contact with the different segments of the commutator as it rotates. The brushes are mounted on holders and are pressed against the commutator with a gentle but firm pressure.
As the armature rotates, the copper segments of the commutator pass under the brushes, creating an electrical connection between the power source and the armature coils. This connection allows the flow of current to the armature coils, initiating the generation of a magnetic field and subsequent rotation of the armature.
The commutator, made up of a series of copper segments separated by insulating material, is an essential component in the process. Its main function is to reverse the direction of the current flowing through the armature coils as it rotates.
When a brush makes contact with a specific segment of the commutator, it provides a path for the electric current to flow into the corresponding armature coil. The specific armature coil connected to the segment where the brush is in contact will experience a current in a specific direction, creating the necessary magnetic field for rotation.
As the armature continues to rotate, the brushes maintain contact with the commutator, but the segment they are in contact with changes. This change in contact points ensures that the current in the armature coils reverses direction at regular intervals, providing the torque required to keep the armature spinning.
The proper alignment and adjustment of the brushes and commutator are critical for efficient motor operation. The brushes need to make consistent and reliable contact with the commutator segments to ensure a constant flow of current without sparking or excessive resistance.
The materials used for the brushes and commutator are carefully chosen for their electrical conductivity, wear resistance, and low friction properties. Regular maintenance, including cleaning and replacing worn-out brushes, is essential to keep the motor functioning optimally.
In summary, the brushes and commutator form a vital electrical connection in an electric motor, allowing the current to flow into the armature coils and reversing its direction as required. Their proper functioning and maintenance ensure the continuous rotation of the armature, enabling the motor to perform its intended tasks.
Factors Affecting the Armature Spin
The rotation of the armature in an electric motor can be influenced by several factors, which determine the speed and torque at which it spins. Understanding these factors is key to optimizing motor performance and achieving the desired motion.
1. Current Strength: The strength of the current passing through the armature coils has a direct impact on the speed and torque of the armature spin. Increasing the current results in a stronger magnetic field and greater force exerted on the armature, leading to faster rotation. However, it is essential to ensure that the current remains within safe operating limits to avoid overheating and damaging the motor.
2. Magnetic Field Strength: The strength of the magnetic field produced by the field coils also affects the armature spin. A stronger magnetic field generates a greater force on the armature, resulting in faster rotation. This can be achieved by increasing the number of turns in the field coils or using stronger permanent magnets, depending on the motor design.
3. Number of Armature Coils: The design and configuration of the armature coils can impact the armature spin. Increasing the number of coils enhances the magnetic field generated, resulting in a higher torque and rotational speed. However, adding more coils also increases the complexity and cost of the motor construction.
4. Commutator Design: The design of the commutator, including the number of segments and their arrangement, can influence the smoothness and efficiency of the armature spin. A properly designed commutator ensures seamless current flow to the armature coils and minimizes sparking and arcing, which can lead to energy losses and motor damage. Modern motor designs often incorporate advanced commutator technologies to enhance performance.
5. Friction and Load: The amount of friction and the load applied to the motor shaft can affect the armature spin. Higher levels of friction or heavier loads can increase the resistance experienced by the armature, slowing down the rotation. Proper lubrication and minimizing external mechanical loads on the motor can help optimize its performance.
6. Power Source Voltage: The voltage supplied to the motor from the power source affects the armature spin. A higher voltage can result in a faster rotation, provided that the motor is designed to handle the increased voltage. However, exceeding the voltage limits specified by the motor manufacturer can lead to overheating and motor failure.
7. Motor Construction and Efficiency: The overall construction and efficiency of the motor can impact the armature spin. Factors such as the quality of materials, design precision, and motor size all contribute to the motor’s ability to convert electrical energy into mechanical motion efficiently. Motors with higher efficiency tend to produce smoother and more consistent armature spins.
8. Temperature: The temperature of the motor and its components can affect the armature spin. Excessive heat can lead to increased electrical resistance, causing energy losses and reduced motor performance. Proper cooling mechanisms, such as fans or heat sinks, are often employed to maintain optimal operating temperatures.
It is important to note that these factors are interconnected and must be carefully balanced to achieve the desired armature spin. Motor manufacturers and designers consider these factors during the motor design and construction process to optimize performance for specific applications.
Conclusion
The spinning of the armature in an electric motor is a fascinating process that relies on the principles of electromagnetism and the interaction between current and magnetic fields. Understanding the intricacies of the armature spin helps us comprehend the inner workings of electric motors and appreciate their vital role in various industries and technologies.
Throughout this article, we have explored the principle of electromagnetism and how it forms the foundation for the rotation of the armature. We have also examined the structure and function of the armature, along with the importance of brushes and the commutator in facilitating the flow of current and the reversal of its direction.
Furthermore, we have delved into the factors that can influence the armature spin, including the strength of the current, magnetic field, number of armature coils, commutator design, friction and load, power source voltage, motor construction, and temperature. Each of these factors plays a significant role in determining the speed, torque, and efficiency of the armature’s rotation.
As technology continues to advance, electric motors are becoming more efficient, reliable, and versatile. Motor designers and manufacturers constantly strive to optimize motor performance by carefully considering and balancing these factors during the design and construction process.
In conclusion, the armature spin in an electric motor is the culmination of intricate mechanisms, from the principles of electromagnetism to the role of brushes and the commutator, as well as various influencing factors. By understanding these concepts, we gain a deeper appreciation for the power and potential of electric motors, which continue to drive innovation and progress across countless industries.
So, the next time you witness the smooth rotation of an electric motor, take a moment to marvel at the science and engineering behind the spinning armature!
Frequently Asked Questions about Which Would Ultimately Cause The Armature In An Electric Motor To Spin
Was this page helpful?
At Storables.com, we guarantee accurate and reliable information. Our content, validated by Expert Board Contributors, is crafted following stringent Editorial Policies. We're committed to providing you with well-researched, expert-backed insights for all your informational needs.
0 thoughts on “Which Would Ultimately Cause The Armature In An Electric Motor To Spin”