Home>Articles>Why The McDonald’s Ice Cream Machine Is Broken
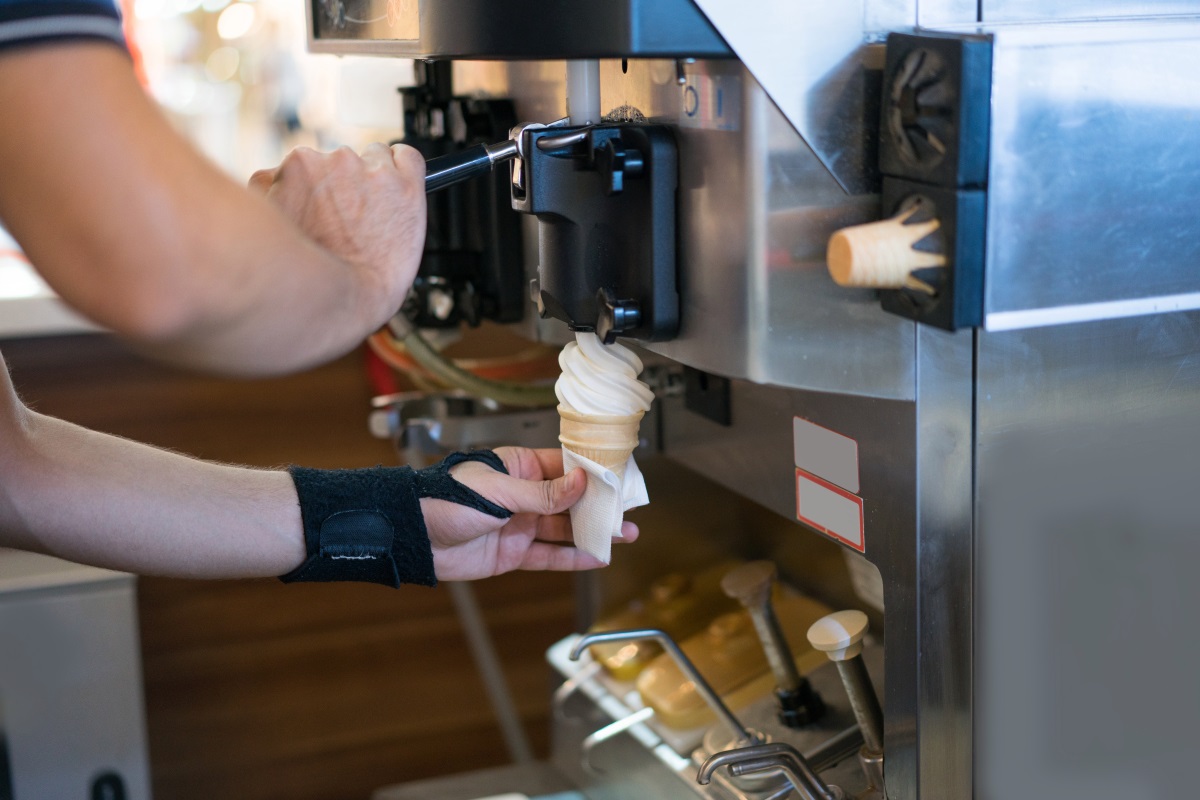
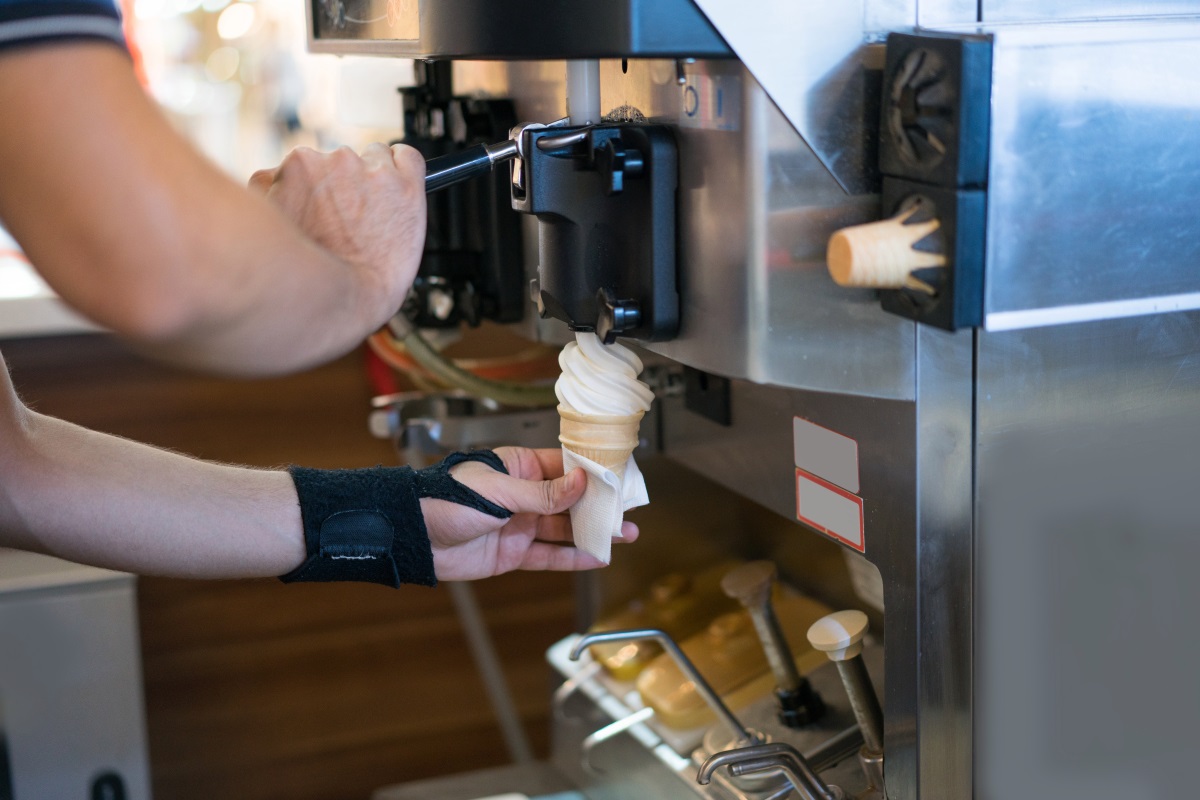
Articles
Why The McDonald’s Ice Cream Machine Is Broken
Modified: February 27, 2024
Explore articles on why the McDonald's ice cream machine is often broken, and uncover the reasons behind this frustrating phenomenon.
(Many of the links in this article redirect to a specific reviewed product. Your purchase of these products through affiliate links helps to generate commission for Storables.com, at no extra cost. Learn more)
Introduction
For decades, McDonald’s has been a go-to destination for fast food enthusiasts around the globe. From their iconic Big Mac to their golden fries, McDonald’s offers a variety of menu items that cater to different cravings. However, there is one item that has gained infamy and frustrates customers on a regular basis – the McDonald’s ice cream machine.
It seems that no matter what time of day or which McDonald’s location you visit, there is a high likelihood that the ice cream machine will be out of order. This perpetual state of dysfunction has caused countless disappointments and led to the creation of a popular internet meme – “the McDonald’s ice cream machine is always broken.”
With this recurring issue, it’s worth delving into the history and reasons behind the frequent breakdowns of McDonald’s ice cream machines, as well as the impact it has on customers and the franchise’s reputation.
Key Takeaways:
- McDonald’s is actively addressing the frequent breakdowns of its ice cream machines through collaboration with manufacturers, enhanced employee training, and streamlined maintenance processes, showcasing a commitment to customer satisfaction and reliability.
- Social media has amplified consumer frustrations over McDonald’s broken ice cream machines, influencing public opinion and consumer decision-making. McDonald’s proactive engagement and transparency demonstrate a dedication to resolving the issue and regaining trust.
History of McDonald’s Ice Cream Machines
The story of McDonald’s ice cream machines can be traced back to the early 1980s when the company introduced soft-serve ice cream to its menu. Initially, the machines were reliable and functioned efficiently, allowing customers to enjoy their favorite ice cream treats without any hassle.
However, as time went on, the ice cream machines started experiencing more and more issues. It became common for customers to arrive at a McDonald’s location only to find that the machine was out of order, preventing them from satisfying their ice cream cravings.
Frequency of McDonald’s Ice Cream Machine Breakdowns
The frequency of McDonald’s ice cream machine breakdowns is alarmingly high. Numerous reports and customer complaints confirm that it is a widespread issue across the franchise’s locations worldwide. Social media platforms are filled with memes, posts, and tweets expressing frustration over encountering a broken ice cream machine yet again.
Customers have voiced their disappointment and frustration over the lack of reliability of the machines, as well as the inconvenience it causes. It has become such a well-known problem that people jokingly advise others to check the status of the ice cream machine before visiting a McDonald’s location.
Key Takeaways:
- McDonald’s is actively addressing the frequent breakdowns of its ice cream machines through collaboration with manufacturers, enhanced employee training, and streamlined maintenance processes, showcasing a commitment to customer satisfaction and reliability.
- Social media has amplified consumer frustrations over McDonald’s broken ice cream machines, influencing public opinion and consumer decision-making. McDonald’s proactive engagement and transparency demonstrate a dedication to resolving the issue and regaining trust.
History of McDonald’s Ice Cream Machines
The story of McDonald’s ice cream machines dates back to the early 1980s when the company decided to introduce soft-serve ice cream to their menu. The machines were seen as a game-changer, allowing McDonald’s to tap into the lucrative dessert market and cater to customers’ sweet tooth cravings.
At first, the ice cream machines worked like a charm. They were reliable, efficient, and churned out creamy soft-serve ice cream that delighted customers. It quickly became a favorite treat for many, especially during the hot summer months.
However, as time went on, issues with the machines started to surface. Reports of machine breakdowns became more frequent, leaving customers disappointed and craving for their beloved ice cream. The phrase “the McDonald’s ice cream machine is always broken” started to circulate among exasperated fans.
One of the primary reasons behind the machine malfunctions can be attributed to their complex design. McDonald’s ice cream machines are known to be highly sophisticated, with a multitude of moving parts, electronic components, and intricate systems that work together to produce the perfect soft-serve ice cream. When even one of these components fails or experiences a glitch, it can result in a breakdown of the entire machine.
In addition to technical difficulties, the machines also require frequent cleaning and maintenance to ensure optimal performance. This poses a challenge for McDonald’s employees, who may not always have the time or training to properly maintain and clean the machines. Failure to clean the machines regularly can lead to clogs, bacterial growth, and other issues that can result in breakdowns.
It’s worth noting that McDonald’s ice cream machines are not exclusively manufactured for the fast-food giant. They are produced by a company called Taylor, which specializes in manufacturing foodservice equipment, including soft-serve machines. While the machines are designed with durability in mind, they still require regular maintenance and occasional repairs.
Despite the ongoing issues with the ice cream machines, McDonald’s remains committed to offering soft-serve ice cream as part of their menu. The popularity of ice cream treats, such as sundaes and McFlurries, cannot be underestimated, and McDonald’s recognizes the demand from customers.
In recent years, McDonald’s has taken steps to address the ice cream machine problem and improve the overall reliability of the machines. They have implemented training programs for employees to ensure proper maintenance and cleaning procedures. Additionally, the franchise has been working closely with Taylor to develop solutions that will minimize breakdowns and optimize the performance of the machines.
While progress has been made, the journey to fully resolving the issue is still ongoing. McDonald’s continues to listen to customer feedback and invest in finding ways to enhance the reliability of their ice cream machines so that customers can enjoy their favorite frozen treats without disappointment.
Frequency of McDonald’s Ice Cream Machine Breakdowns
It is no secret that the frequency of McDonald’s ice cream machine breakdowns has become a well-known issue across the franchise’s locations worldwide. Customers have shared their frustrations, experiences, and memes on social media, creating a collective understanding that the ice cream machine is often out of order.
One of the primary reasons behind the high frequency of breakdowns is the complexity of the ice cream machines themselves. The machines consist of various intricate parts, including motors, pumps, compressors, and freezing mechanisms, all working together to produce smooth soft-serve ice cream. With so many components, there is an increased risk of malfunctions and failures.
In addition, the machines require thorough cleaning and maintenance, which can be time-consuming and challenging for McDonald’s employees, especially during busy periods. Neglecting proper maintenance can lead to issues such as clogs and bacterial growth, causing the machines to break down more frequently.
Another contributing factor to the frequency of breakdowns is the demand placed on the machines. McDonald’s is known for serving a high volume of customers, particularly during peak hours. The constant use and demand for ice cream can put strain on the machines, leading to wear and tear and ultimately, more breakdowns.
Furthermore, the lack of training and knowledge among employees regarding the maintenance and repair of the machines can also contribute to the frequent breakdowns. Many employees may not fully understand the intricacies of the machines or how to properly troubleshoot and resolve issues, leading to prolonged downtime.
The frequent breakdowns of the ice cream machines have undoubtedly impacted McDonald’s reputation among customers. When customers visit a McDonald’s location with the intention of enjoying a soft-serve ice cream cone or a McFlurry, only to be told that the machine is broken, it leaves a negative impression. This recurring issue has led to a sense of skepticism and frustration, with many customers doubting whether they can rely on McDonald’s to provide a consistent ice cream experience.
Despite these challenges, McDonald’s has recognized the importance of addressing the ice cream machine problem. The franchise has implemented initiatives to improve training for employees, increase communication between restaurants and technicians, and collaborate with Taylor, the manufacturer of the ice cream machines, to develop more reliable and efficient models.
By focusing on both technical improvements and employee education, McDonald’s aims to reduce the frequency of ice cream machine breakdowns and regain the trust and satisfaction of their customers. Ensuring that the machines are consistently functional will not only enhance the overall dining experience but also contribute to the reputation and success of the McDonald’s franchise as a whole.
Reasons Behind the Frequent Breakdowns
The frequent breakdowns of McDonald’s ice cream machines can be attributed to several underlying reasons that contribute to the frustrating and often-encountered issue. Understanding these reasons can shed light on why the machines are prone to malfunction. Here are some of the key factors behind the frequent breakdowns:
1. Complex Design: McDonald’s ice cream machines are highly sophisticated devices, equipped with numerous intricate parts and mechanisms. These machines have motors, pumps, compressors, and freezing units, among others, all working together to create the desired soft-serve ice cream. The complexity of these components increases the likelihood of malfunctions or failures, leading to the breakdown of the machine.
2. Cleaning and Maintenance: Like any other foodservice equipment, ice cream machines require regular cleaning and maintenance to ensure optimal performance. However, the cleaning process for McDonald’s ice cream machines can be time-consuming and challenging. If proper cleaning procedures are not followed, the machines can experience issues such as clogs or bacterial growth, disrupting their functionality and causing breakdowns.
3. Heavy Usage: McDonald’s is a popular fast food chain globally, serving a significant number of customers daily. The ice cream machines are in constant demand and subjected to heavy usage, especially during peak hours. The continuous operation and high volume of ice cream production can put strain on the machines, leading to accelerated wear and tear, and ultimately, frequent breakdowns.
4. Lack of Maintenance Training: The proper maintenance and repair of ice cream machines require specialized knowledge and training. Unfortunately, not all McDonald’s employees receive comprehensive training on this aspect. As a result, they may lack the necessary expertise to perform regular maintenance or troubleshoot potential issues. This can lead to delays in identifying and resolving problems, resulting in extended downtime of the machines.
5. Technical Issues: Despite being manufactured by reputable companies like Taylor, technical issues can still arise with the ice cream machines. Equipment failures, electronic malfunctions, and other technical glitches can occur, leading to breakdowns. While routine maintenance can help mitigate some problems, unforeseen technical issues may still arise, causing unexpected machine failures.
Recognizing these reasons behind the frequent breakdowns, McDonald’s has been taking steps to address the issue. The franchise has been working closely with Taylor, the manufacturer of the ice cream machines, to improve their design, functionality, and reliability. Additionally, McDonald’s has implemented enhanced training programs for employees to ensure proper maintenance and cleaning procedures are followed.
By addressing these underlying factors, McDonald’s aims to reduce the frequency of ice cream machine breakdowns, enhance customer satisfaction, and rebuild the trust of their loyal fan base. Continuous efforts to improve the machines’ reliability and functionality remain a priority for the franchise, as they strive to provide a consistent and enjoyable ice cream experience for customers.
Tip: The McDonald’s ice cream machine may be broken due to the complex cleaning and maintenance process it requires. The machine has many parts that need to be disassembled and cleaned daily, which can lead to frequent malfunctions.
Technical Issues with McDonald’s Ice Cream Machines
McDonald’s ice cream machines are notorious for their frequent breakdowns, leaving customers disappointed and craving their favorite frozen treats. While there are various reasons behind these malfunctions, technical issues play a significant role in the ongoing problems experienced with these machines. Here are some of the most common technical issues that plague McDonald’s ice cream machines:
1. Temperature Regulation: One of the key technical challenges faced by McDonald’s ice cream machines is maintaining the optimal temperature for producing soft-serve ice cream. These machines rely on a delicate balance of refrigeration and freezing mechanisms to create the smooth texture desired by customers. However, temperature inconsistencies can arise, leading to issues such as ice cream that is too soft or too hard, or even freezing up of the machine itself.
2. Machine Calibration: Proper calibration is essential for the seamless operation of ice cream machines. Calibration ensures that the right amounts of mix and air are combined, resulting in the desired consistency and texture of the ice cream. When the machines are not accurately calibrated, it can lead to imbalanced mixtures, causing improper freezing, and ultimately resulting in breakdowns.
3. Sensor Malfunctions: Ice cream machines are equipped with sensors that monitor various factors such as temperature, mix consistency, and the level of the mixture in the hopper. When these sensors malfunction, they may provide inaccurate readings or fail to detect issues, leading to operational failures. For example, a faulty temperature sensor may prevent the machine from properly freezing the ice cream or cause it to overfreeze, resulting in breakdowns.
4. Software Glitches: In today’s technologically advanced age, ice cream machines often come with embedded software that controls and regulates various aspects of their operation. However, software glitches can occur, causing the machines to malfunction. These glitches may disrupt the communication between different components of the machine or cause errors in the timing and sequencing of processes, leading to breakdowns.
5. Parts and Component Failures: Like any mechanical device, ice cream machines are made up of numerous parts and components that work together to create the end product. Over time, these parts can experience wear and tear or suffer from natural degradation. If these parts are not properly inspected, maintained, and replaced when necessary, they may fail, resulting in the breakdown of the machine.
To address these technical issues, McDonald’s has been working closely with the manufacturers of their ice cream machines, such as Taylor, to improve their design and functionality. Collaborative efforts have been made to develop more reliable sensors, enhance temperature control systems, and reduce the likelihood of software glitches. These improvements aim to minimize technical failures and improve the overall reliability of the machines.
Regular maintenance and inspection of the machines are also crucial in preventing technical problems. McDonald’s is continually investing in training programs for their employees to ensure they have the knowledge and skills required to identify and resolve technical issues promptly. By prioritizing regular maintenance and technical support, McDonald’s aims to reduce the frequency of breakdowns and provide customers with a more consistent and enjoyable ice cream experience.
Lack of Maintenance and Training
The frequent breakdowns of McDonald’s ice cream machines can be attributed, in part, to the lack of proper maintenance and training. Without regular maintenance and employees equipped with the necessary skills, the machines are more likely to experience malfunctions and failures. Here are some of the key factors contributing to the lack of maintenance and training:
1. Time Constraints: McDonald’s is known for its fast-paced environment, with employees often pressured to provide quick and efficient service to a large volume of customers. This can result in limited time available for proper maintenance of the ice cream machines. Cleaning, inspecting, and performing routine maintenance on the machines can be time-consuming, especially during peak hours, leading to neglect and increased risk of breakdowns.
2. Inadequate Training: Maintaining and troubleshooting ice cream machines require specialized knowledge and skills that not all employees may possess. Limited training opportunities can leave employees unfamiliar with the machines’ complexities and prevent them from effectively identifying and addressing potential issues. Without the necessary training, they may not be able to perform routine maintenance tasks, leading to further machine dysfunction.
3. Lack of Technical Expertise: Resolving technical issues with ice cream machines often requires a level of technical expertise not readily available among McDonald’s employees. Without the necessary knowledge and understanding of how the machines operate, employees may struggle to diagnose and correct issues that arise. This lack of technical expertise can result in delays in repairing the machines and prolonged downtime, frustrating both employees and customers.
4. Communication Gaps: Effective communication between restaurant staff and maintenance technicians is vital for timely repairs and addressing maintenance needs. However, communication gaps can occur when there is a breakdown in communication channels or a lack of clear protocols for reporting issues. These gaps can lead to delays in getting the necessary support, exacerbating maintenance problems and prolonging machine downtime.
5. Overreliance on External Technicians: McDonald’s franchises often rely on technicians from the manufacturers, such as Taylor, to service and repair their ice cream machines. While this can be effective, it can also result in delays if technicians are not readily available or if there are logistic challenges. This overreliance can hinder quick resolutions to maintenance issues and contribute to the recurring breakdowns.
In recent years, McDonald’s has recognized the importance of addressing the lack of maintenance and training for ice cream machines. The franchise has implemented initiatives to enhance employees’ technical knowledge, providing training programs to ensure they have the required skills to properly maintain and troubleshoot issues. McDonald’s has also focused on improving communication channels and establishing clear reporting procedures to streamline maintenance processes.
Additionally, the franchise has been working closely with the manufacturers to develop user-friendly maintenance protocols and provide resources to guide employees in performing routine maintenance tasks effectively. By empowering employees with the necessary training and resources, McDonald’s aims to minimize breakdowns resulting from inadequate maintenance and increase the overall reliability of their ice cream machines.
Regular and proactive maintenance, along with well-trained employees, are crucial in optimizing the performance and longevity of ice cream machines. By addressing the lack of maintenance and training, McDonald’s can enhance their ability to provide consistent and reliable ice cream services to customers, ultimately improving the overall satisfaction and experience at their restaurants.
Impact on Customers and Franchise Reputation
The frequent breakdowns of McDonald’s ice cream machines have had a significant impact on both customers and the franchise’s reputation. The frustration and disappointment experienced by customers, coupled with the widespread knowledge of the issue, have contributed to a negative perception of the franchise. Here are some of the key impacts on customers and the franchise’s reputation:
1. Customer Dissatisfaction: When customers visit a McDonald’s restaurant, they have certain expectations, including the availability of their favorite menu items, such as soft-serve ice cream. However, the recurring issue of broken ice cream machines has left customers feeling disappointed, as they are unable to satisfy their cravings. This pattern of disappointment has led to a significant level of customer dissatisfaction, affecting their overall experience at McDonald’s.
2. Inconvenience and Inefficiency: The frequent breakdowns of ice cream machines have resulted in inconvenience for customers. Whether it’s wasting time waiting in line, only to be informed that the machine is broken, or the disappointment of having to alter their order due to the unavailability of ice cream, these incidents contribute to a sense of inefficiency and frustration among customers.
3. Negative Word-of-Mouth: The frustration experienced by customers has resulted in negative word-of-mouth spreading both offline and online. Customers share their negative experiences with friends, family, and colleagues, creating a ripple effect of dissatisfaction. Furthermore, social media platforms are filled with memes, posts, and tweets expressing disappointment and joking about the broken ice cream machines, further cementing the reputation issue.
4. Diminished Trust and Loyalty: The recurring breakdowns of ice cream machines have eroded the trust and loyalty that customers once had for the McDonald’s brand. Customers may hesitate to visit McDonald’s for ice cream, as they have learned to expect disappointment. This loss of trust can extend to other aspects of the franchise’s offerings, affecting customer loyalty and potentially leading them to seek alternatives.
5. Franchise Reputation: The issues with the ice cream machines have had a direct impact on the franchise’s reputation as a whole. McDonald’s is known for its commitment to quality and customer satisfaction, and the ongoing problem with the ice cream machines has tarnished that reputation. Customers may question the franchise’s ability to deliver consistent, reliable experiences, not only in terms of ice cream but also in other areas, leading to an overall decline in the brand’s reputation.
Recognizing the impact of the broken ice cream machines on customers and the franchise’s reputation, McDonald’s has taken steps to address the issue. They have prioritized improving the machines’ reliability through collaborations with the manufacturers and enhancing training programs for employees to ensure proper maintenance and troubleshooting. By actively seeking solutions to this problem, McDonald’s aims to rebuild customer trust and loyalty, ultimately repairing their brand reputation.
However, regaining customer trust and restoring the franchise’s reputation will require consistent efforts, effective communication, and a commitment to providing reliable ice cream services. By ensuring that the ice cream machines are consistently functional and meeting customer expectations, McDonald’s can work towards reestablishing their reputation as a trusted and dependable fast-food brand.
Actions Taken by McDonald’s to Address the Issue
Recognizing the frustration and customer dissatisfaction caused by the frequent breakdowns of their ice cream machines, McDonald’s has taken several actions to address the issue. Understanding the importance of providing reliable and consistent service, the franchise is actively working towards improving the functionality and reliability of their ice cream machines. Here are some of the key actions taken by McDonald’s:
1. Collaboration with Manufacturers: McDonald’s has been collaborating closely with the manufacturers of their ice cream machines, such as Taylor, to improve their design and functionality. By working together, they aim to identify and address the underlying technical issues that contribute to the frequent breakdowns. This collaboration allows for targeted improvements to the machines, ensuring greater reliability and performance.
2. Enhanced Training Programs: McDonald’s has implemented enhanced training programs for their employees regarding ice cream machine maintenance and troubleshooting. Recognizing the importance of empowering their staff, the franchise provides comprehensive training to ensure that employees have the necessary skills to perform routine maintenance, identify potential issues, and take appropriate action in a timely manner. This training equips employees with the knowledge required to address problems promptly and minimize downtime.
3. Streamlined Maintenance Processes: McDonald’s has focused on streamlining maintenance processes for their ice cream machines. This includes establishing clear guidelines for regular cleaning and maintenance tasks, as well as creating protocols for reporting and addressing issues. By streamlining these processes, the franchise aims to ensure that maintenance is regularly performed, reducing the risk of breakdowns and optimizing the machines’ performance.
4. Continuous Monitoring and Support: McDonald’s has implemented ongoing monitoring and support measures to address issues with the ice cream machines. This includes implementing systems and protocols to track the performance of individual machines across different locations. By monitoring the machines closely, the franchise can identify patterns, anticipate potential issues, and provide timely support to restaurants that require assistance.
5. Customer Feedback and Communication: McDonald’s actively encourages customer feedback regarding their ice cream machines and the overall dining experience. They have established channels for customers to report issues or provide suggestions for improvement. By actively seeking and listening to customer feedback, the franchise gains valuable insights into the specific problems customers face and can take appropriate action to address them.
6. Continuous Improvement Efforts: McDonald’s is committed to continuously improving the reliability and functionality of their ice cream machines. They have invested in research and development to implement technical advancements that will enhance the machines’ performance and reduce the likelihood of breakdowns. This ongoing commitment to improvement ensures that McDonald’s remains proactive in addressing the issue and providing a better experience for customers.
Through these actions, McDonald’s aims to improve the reliability and functionality of their ice cream machines, ultimately providing a consistent and enjoyable ice cream experience for customers. By collaborating with manufacturers, enhancing employee training, streamlining maintenance processes, actively monitoring performance, and fostering communication with customers, McDonald’s is actively working towards resolving the ongoing issue of ice cream machine breakdowns.
While challenges may still persist, McDonald’s recognizes the importance of addressing this issue to restore customer trust and satisfaction. The franchise remains dedicated to taking the necessary steps and investing in ongoing improvements to ensure that their ice cream machines deliver on customers’ expectations consistently.
Consumer Backlash and Social Media Influence
One of the significant repercussions of the frequent breakdowns of McDonald’s ice cream machines is the consumer backlash generated through social media platforms. Social media has become a powerful tool for expressing frustrations, sharing experiences, and influencing public opinion. Here’s a closer look at the consumer backlash and the significant role of social media in shaping perceptions:
1. Amplification of Consumer Frustrations: Social media platforms serve as amplifiers for consumer frustrations regarding the broken ice cream machines. Customers who experience disappointment take to platforms such as Twitter, Facebook, Instagram, and Reddit to vent their frustrations and share their experiences. As a result, these platforms become hotbeds for discussions and complaints, often garnering significant attention and engagement. This amplification reinforces the perception of the issue and draws attention to the ongoing problems faced by consumers.
2. Creation of Memes and Viral Content: The broken ice cream machines have become a source of amusement and frustration for internet users. Memes, jokes, and viral content related to the issue have spawned on social media. These humorous yet relatable posts contribute to the spread of the phenomenon, showcasing the widespread nature of the problem and further deepening the negative perception among consumers.
3. Influencing Consumer Decision-Making: Social media has a significant impact on consumer decision-making. The abundance of posts and discussions about McDonald’s broken ice cream machines can influence a consumer’s choice to visit or avoid a McDonald’s location. Seeing and hearing about others’ negative experiences can deter potential customers from engaging with the brand, ultimately impacting sales and customer loyalty.
4. Rapid Spread of Information: Social media provides a platform for the rapid dissemination of information. When a customer encounters a broken ice cream machine and shares their experience on social media, the information can quickly reach a large audience. As more and more people become aware of the issue, the negative perception is reinforced, creating a reputation challenge for McDonald’s.
5. Pressure for Transparency and Accountability: Consumers on social media often demand transparency and accountability from prominent brands. They expect companies to address their concerns promptly and take visible steps to resolve issues. When consumers express their frustration about McDonald’s broken ice cream machines, they often tag the official McDonald’s social media accounts, creating pressure for the brand to respond and take action. The public nature of these interactions adds to the sense of accountability and heightens consumer expectations for resolution.
6. Shift of Power to Consumers: Social media has shifted the power dynamics between companies and consumers. Brands can no longer control the narrative solely through traditional marketing channels. Instead, consumers have a platform to voice their opinions and experiences, which can significantly impact a brand’s reputation. The consumer backlash experienced by McDonald’s due to broken ice cream machines underscores the influence of social media in shaping consumer sentiment and holding brands accountable for their actions or lack thereof.
Recognizing the power of social media, McDonald’s has started to actively monitor and engage with customers through these platforms. They not only respond to individual complaints but also use the feedback to drive improvements and boost customer satisfaction. Additionally, McDonald’s has been transparent about their efforts to address the issue, reinforcing their commitment to resolving the problem and regaining consumer trust.
However, the impact of consumer backlash on social media suggests that repairing brand reputation requires proactive and ongoing efforts. McDonald’s must continue to address the broken ice cream machine issue and reinforce their dedication to providing a consistent and reliable customer experience. By engaging with consumers, improving transparency, and delivering on their promises, McDonald’s can gradually rebuild trust and mitigate the negative influence of consumer backlash on social media.
Conclusion
The frequent breakdowns of McDonald’s ice cream machines have undoubtedly frustrated customers and impacted the franchise’s reputation. These recurring issues have led to customer dissatisfaction, negative word-of-mouth, and a sense of disbelief in the brand’s ability to deliver consistency and reliability. However, McDonald’s has not remained idle in the face of this challenge. The franchise has taken several actions to address the broken ice cream machine problem and restore customer trust.
Through collaboration with manufacturers, McDonald’s has worked towards improving the design and functionality of their ice cream machines. By enhancing training programs for employees, the franchise has equipped its workforce with the necessary knowledge and skills to properly maintain and troubleshoot the machines. Streamlining maintenance processes and establishing clear communication channels have further contributed to the resolution of issues in a timely manner.
Social media has played a significant role in shaping the narrative surrounding the broken ice cream machines. It has given voice to customer frustrations and amplified their negative experiences online. The dissemination of information, creation of memes, and rapid spread of consumer experiences have influenced public opinion and affected consumer decision-making.
Despite the challenges posed by the consumer backlash on social media, McDonald’s has recognized the importance of active engagement. They have actively monitored and responded to customer feedback, taking steps to address concerns and improve their services. By embracing transparency, McDonald’s has showcased its commitment to resolving the issue and regaining consumer trust.
While the road to fully resolving the broken ice cream machine problem may still have obstacles, McDonald’s continuous efforts to enhance reliability and functionality indicate a commitment to customer satisfaction. The franchise’s actions demonstrate a desire to return to the core values that made them a beloved fast-food brand in the first place.
In conclusion, the broken ice cream machines at McDonald’s have posed challenges to customer satisfaction and brand reputation. However, McDonald’s proactive approach in collaborating with manufacturers, enhancing employee training, streamlining maintenance processes, and engaging with customers signifies a commitment to address the issue and provide a better experience. By valuing customer feedback and continuously improving their offerings, McDonald’s aims to regain consumer trust and solidify its position as a reliable and enjoyable fast-food destination.
Frequently Asked Questions about Why The McDonald's Ice Cream Machine Is Broken
Was this page helpful?
At Storables.com, we guarantee accurate and reliable information. Our content, validated by Expert Board Contributors, is crafted following stringent Editorial Policies. We're committed to providing you with well-researched, expert-backed insights for all your informational needs.
0 thoughts on “Why The McDonald’s Ice Cream Machine Is Broken”