Home>diy>Building & Construction>What Does Warm Shell Mean In Construction
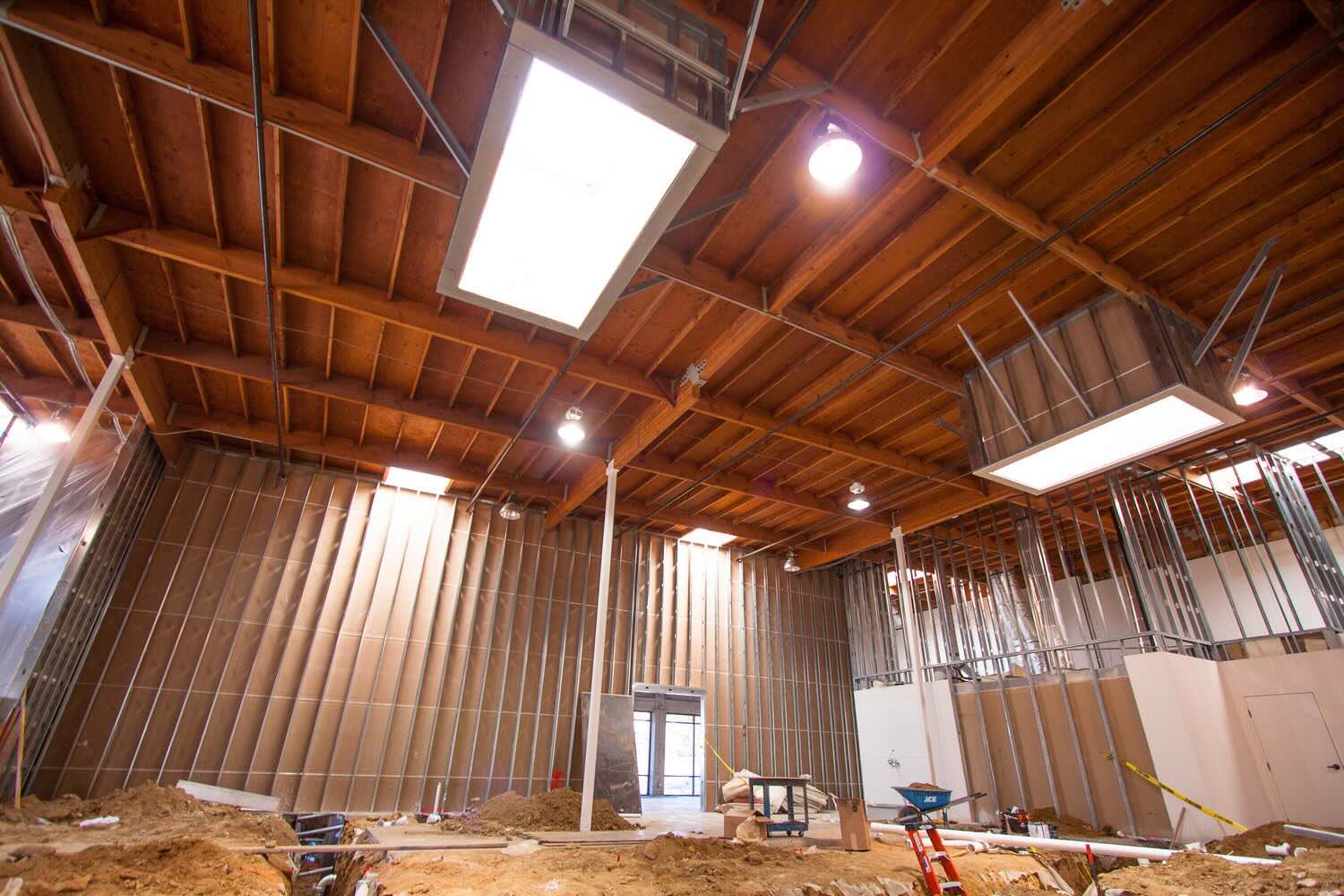
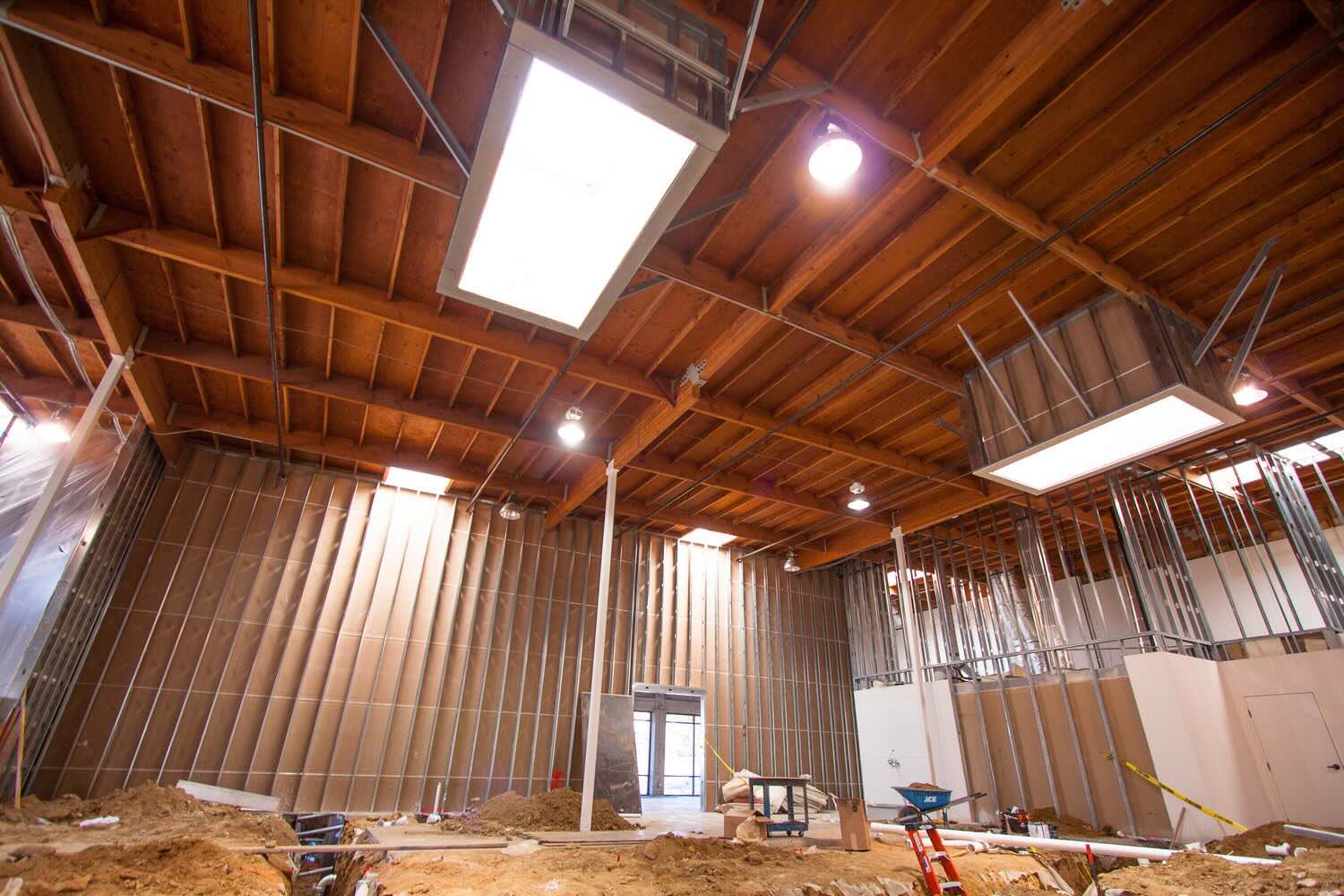
Building & Construction
What Does Warm Shell Mean In Construction
Modified: December 7, 2023
Discover the meaning of warm shell in building construction and how it affects the final outcome. Explore the importance of this term in the construction industry.
(Many of the links in this article redirect to a specific reviewed product. Your purchase of these products through affiliate links helps to generate commission for Storables.com, at no extra cost. Learn more)
Introduction
In the world of construction, there are various terminologies used to describe different stages and processes. One such term is “Warm Shell”. In this article, we will explore what warm shell means in construction and its significance in building development.
When it comes to constructing commercial buildings or office spaces, the concept of warm shell plays a crucial role. It refers to the completion of the building’s shell or core structure, including the essential systems and finishes necessary for a functional space. The warm shell is an intermediate stage between the raw construction and a fully finished and customized interior.
Understanding what warm shell entails and the benefits it offers can help building owners and developers make informed decisions regarding their construction projects. So, let’s delve into the definition of warm shell in construction and explore its implications.
Key Takeaways:
- Warm shell construction provides a cost-effective and flexible solution, allowing for quicker occupancy and customization while reducing initial investment and construction timelines.
- When considering warm shell construction, evaluate functional requirements, budget constraints, timeline expectations, flexibility needs, tenant agreements, local regulations, and available expertise to make an informed decision.
Definition of Warm Shell in Construction
Warm shell, also known as “builder’s finish” or “vanilla shell,” refers to the completion of the core structure and essential systems of a building, allowing for the customization of the interior by the occupants. It is the stage between the raw construction and the fully finished space. Although the warm shell does not include the final cosmetic touches and personalized design elements, it provides the necessary amenities and infrastructure to make the space functional.
A warm shell typically includes the installation of HVAC systems, electrical wiring, plumbing, fire protection systems, and basic finishes such as walls, ceilings, and flooring. It may also include the installation of doors, windows, and restrooms. These components are essential for the basic functionality of the space and provide a solid foundation for the future occupants to build upon.
One important aspect of warm shell construction is that it allows for flexibility and customization. The building owner or tenant can determine how they want to design and outfit the interior based on their specific needs and preferences. This flexibility is especially beneficial for businesses that require unique layouts, specialized equipment, or specific branding elements. By providing the necessary infrastructure while leaving the interior finishes open, warm shell construction allows for easier customization without the need for major renovations or alterations.
It’s essential to note that warm shell construction varies depending on the specific project and location. Local building codes and regulations may dictate certain requirements that need to be included in the warm shell stage. Therefore, it’s crucial to consult with architects, contractors, and engineers to ensure that the warm shell construction aligns with the applicable standards and codes.
Benefits of Using Warm Shell Construction
Warm shell construction offers several advantages for building owners, developers, and tenants. Let’s explore some of the key benefits:
- Cost Savings: By opting for warm shell construction, owners and tenants can save on upfront costs. The basic infrastructure and essential systems are already in place, reducing the need for extensive renovations or installations.
- Flexibility and Customization: Warm shell construction allows for greater flexibility and customization of the interior space. The occupants can design and configure the layout according to their specific needs and preferences, whether it’s an open-concept office, a retail store with unique fixtures, or a restaurant with specialized kitchen equipment.
- Quicker Occupancy: Since the core structure and essential systems are already completed, tenants can move in and start their business operations sooner. This accelerated occupancy timeline can result in faster revenue generation and a competitive advantage in the market.
- Reduced Construction Time: Warm shell construction can significantly reduce the overall construction time compared to starting from scratch. With the major infrastructure already in place, the focus shifts to interior finishes and customization, which can be completed in a shorter timeframe.
- Adaptability to Changing Needs: Warm shell spaces offer adaptability to accommodate future changes in the business. If the tenant’s needs evolve over time, it is easier to modify the interior layout or upgrade systems without disrupting the entire building.
- Improved Tenant-Landlord Relationships: The flexibility provided by warm shell construction can improve the relationship between landlords and tenants. Tenants have the freedom to modify and personalize their space, resulting in a greater sense of ownership.
These benefits make warm shell construction an attractive option for both building owners and tenants. It provides a solid foundation while allowing for customization and flexibility to meet specific business requirements.
Warm Shell Features and Components
Warm shell construction includes several features and components that provide the basic infrastructure and functionality of a building. Here are the key elements typically found in a warm shell:
- HVAC Systems: Heating, ventilation, and air conditioning (HVAC) systems are essential for maintaining a comfortable indoor environment. Warm shell construction includes the installation of HVAC equipment and ductwork to ensure adequate temperature control and air circulation.
- Electrical Wiring: A vital component of warm shell construction is the installation of electrical wiring and outlets throughout the space. This allows for lighting, power supply, and connectivity for various equipment and devices.
- Plumbing: Warm shell construction includes the installation of basic plumbing systems, including pipes, fixtures, and bathroom facilities. This ensures access to water supply and sanitary facilities within the building.
- Fire Protection Systems: To ensure the safety of occupants, warm shell construction incorporates fire protection systems such as fire alarms, sprinklers, and fire exits. These systems are designed to detect and mitigate fire hazards in the building.
- Walls, Ceilings, and Flooring: Basic finishes for walls, ceilings, and flooring are typically included in warm shell construction. They provide a clean and functional backdrop for future interior customization and design.
- Doors and Windows: Warm shell construction involves the installation of doors and windows to secure the building and allow natural light to enter the space. These components are often left unfinished, awaiting further customization by the occupants.
- Common Areas: Depending on the type of building or project, warm shell construction may include the creation of common areas such as lobbies, corridors, and shared spaces. These areas are designed to enhance the functionality and accessibility of the overall building.
It’s important to note that warm shell construction may vary depending on the specific project requirements and local building codes. Some projects may include additional features or components based on the intended use of the building. Consulting with professionals in the construction industry can help ensure compliance with regulations and the inclusion of all necessary features.
Examples of Warm Shell Construction Projects
Warm shell construction is a popular approach for various types of buildings and commercial spaces. Let’s explore some examples of warm shell construction projects:
- Office Buildings: Many office buildings are constructed using warm shell construction. The core structure, essential systems, and basic finishes are completed, allowing businesses to lease and customize the interiors according to their specific needs. This flexibility is especially beneficial for companies with unique office layouts or specialized equipment requirements.
- Retail Spaces: Warm shell construction is commonly utilized in retail spaces, such as shopping malls or standalone stores. The building’s shell is completed, including HVAC, electrical, and plumbing systems, allowing retailers to design and create a tailored space that aligns with their brand and product displays.
- Restaurants: Warm shell construction is particularly advantageous for restaurants. The basic infrastructure, including fire protection systems, plumbing, and electrical wiring, is already in place. This allows restaurant owners to focus on customizing the interior layout, kitchen equipment installations, and decor to create a unique dining experience.
- Co-working Spaces: With the surge in popularity of co-working spaces, warm shell construction has become a popular approach. The core structure and essential infrastructure are completed, allowing co-working operators to provide a flexible and customizable environment for their members. This includes shared workstations, meeting rooms, and communal areas.
- Mixed-Use Developments: Warm shell construction is also utilized in mixed-use developments, where a building houses multiple functions such as residential units, office spaces, and retail establishments. Completing the warm shell stage allows for flexibility in designing and configuring each individual component to meet the specific requirements of the different uses within the development.
Each warm shell construction project is tailored to the specific needs of the building and its intended use. This approach ensures that the basic infrastructure and functionality are in place while allowing for customization and flexibility to accommodate the unique requirements of different businesses.
A warm shell in construction refers to a space that is partially finished, with completed structural elements, HVAC, and utilities, but without interior finishes. This allows for flexibility in customizing the space to fit specific needs.
Read more: What Is Shell Construction
Cost Considerations of Warm Shell Construction
When embarking on a construction project, cost considerations play a crucial role in decision-making. Here are some important factors to consider regarding the costs associated with warm shell construction:
- Initial Investment: While warm shell construction offers cost savings compared to fully finished spaces, there is still an initial investment required for completing the core structure and essential systems. This includes the cost of materials, labor, and contracting services.
- Customization Costs: While warm shell construction allows for customization, it’s important to consider the costs associated with outfitting the space according to specific needs and preferences. This may include additional expenses for interior design, fixtures, furniture, and technology infrastructure.
- Tenant Improvements: In some cases, tenants may require further improvements beyond what the warm shell provides. This can include specialized equipment, modifications to the infrastructure, or customized finishes. These tenant improvements may incur additional costs, and it’s essential to factor them into the overall budget.
- Operating Expenses: While warm shell construction provides the essential infrastructure, tenants should also consider ongoing operating expenses. This includes utilities, maintenance costs, insurance, and property taxes. It’s important to evaluate these expenses to ensure they are aligned with the budget and overall financial plan.
- Timeline Implications: Although warm shell construction can save time compared to starting from scratch, it’s important to consider the timeline implications. Delays in completing the warm shell stage can result in increased costs due to extended construction timelines, potential penalties, and loss of revenue for tenants unable to occupy the space on schedule.
- Resale or Lease Value: Investing in warm shell construction may enhance the resale or lease value of the property. By providing a partially finished space, the building may attract a wider range of potential buyers or tenants who can see the value in customizing the interior to suit their specific needs. This potential increase in value should be considered when evaluating the overall cost implications of warm shell construction.
It’s important to work closely with construction professionals, architects, and contractors to develop a comprehensive cost estimate for the warm shell construction project. Careful planning, thorough budgeting, and regular monitoring of costs are essential to ensure that the project remains within financial constraints while delivering the desired outcome.
Comparison of Warm Shell and Cold Shell Construction
When it comes to constructing commercial buildings, two common approaches are warm shell and cold shell construction. Let’s compare these two methods to understand their differences and determine which approach may be more suitable for specific projects.
Warm Shell Construction:
Warm shell construction involves the completion of the core structure and essential systems of a building, providing a functional space that requires minimal additional work. Some key characteristics of warm shell construction include:
- – HVAC systems, electrical wiring, plumbing, and fire protection systems are installed
- – Basic finishes for walls, ceilings, and flooring are included
- – Doors, windows, and restrooms are typically installed
- – Flexibility for occupants to customize and design the interior space
Cold Shell Construction:
Cold shell construction, on the other hand, is the initial phase of construction, where the building is incomplete and lacks essential systems and finishes. Some key characteristics of cold shell construction include:
- – Basic infrastructure such as structural elements and external walls are constructed
- – No installation of HVAC, electrical, plumbing, or fire protection systems
- – No interior finishes for walls, ceilings, or flooring
- – No installation of doors, windows, or restrooms
- – The space is essentially a blank canvas, requiring extensive work for functionality
Comparison:
Now let’s compare warm shell and cold shell construction based on a few key factors:
- Cost: Warm shell construction generally has a lower upfront cost compared to cold shell construction. The initial investment for warm shell is reduced as it includes essential systems and basic finishes, while cold shell requires additional work and infrastructure.
- Timeline: Warm shell construction can be completed relatively faster than cold shell construction, as the essential systems and finishes are already in place. Cold shell construction may require significant time for installation of systems and finishes.
- Flexibility and Customization: Warm shell construction offers more flexibility and customization options for occupants, as the basic infrastructure is completed. Cold shell construction provides a blank canvas, but requires extensive work for customization.
- Occupancy: Warm shell construction allows for quicker occupancy, as the space is functional with the necessary systems. Cold shell construction requires more time and effort to make the space usable.
Ultimately, the choice between warm shell and cold shell construction depends on the specific needs and requirements of the project. Warm shell construction offers a cost-effective and flexible solution that allows for customization and quicker occupancy. However, cold shell construction provides a blank canvas for complete customization at the cost of longer timelines and higher initial investment.
Factors to Consider When Deciding on Warm Shell Construction
When deciding whether to pursue warm shell construction for a commercial building or office space, several factors should be taken into consideration. These factors will help determine if warm shell construction is the right choice for your specific project. Here are some key considerations:
- Functional Requirements: Evaluate the functional requirements of your business or organization. Does the space need to be customized to meet specific operational needs? Warm shell construction offers flexibility for customization, so consider if this aligns with your requirements.
- Budget Constraints: Understand your budget limitations. Warm shell construction generally requires a lower upfront investment compared to starting from scratch. Assess whether the cost savings and ability to customize within your budget make warm shell construction a feasible option.
- Timeline Expectations: Consider the urgency for occupancy and timelines. Warm shell construction allows for faster occupancy, as the core structure and essential systems are already completed. If time is of the essence, warm shell might be the preferred option.
- Flexibility for Future Changes: Determine if your business requires the flexibility to modify or expand the space in the future. Warm shell construction allows for easier modifications or upgrades, as the infrastructure is already in place.
- Tenant or Ownership Agreement: If you are a tenant, review your lease agreement to understand whether the landlord offers warm shell construction as an option. If you are building as an owner, consider the preferences of potential tenants and their likelihood of leasing a warm shell space.
- Local Building Codes and Regulations: Familiarize yourself with local building codes and regulations. Ensure that warm shell construction complies with all relevant requirements and obtain any necessary permits or approvals.
- Expertise and Resources: Assess your expertise and resources in managing the construction process. Warm shell construction requires coordination with architects, engineers, and contractors. Make sure you have the necessary knowledge or access to professionals who can guide you through the process.
Every project is unique, and what may be suitable for one may not be the best choice for another. By considering these factors, you can make an informed decision about whether warm shell construction aligns with your needs, budget, timeline, and future aspirations for the space.
Conclusion
Warm shell construction serves as an important intermediate stage between raw construction and fully finished spaces in the world of building development. It provides a functional and customizable core structure with essential systems and finishes, allowing for flexibility and personalization by the occupants. Throughout this article, we have explored the definition of warm shell construction, its benefits, features, cost considerations, comparisons to cold shell construction, and factors to consider when deciding on its implementation.
Warm shell construction offers several advantages, including cost savings, flexibility for customization, quicker occupancy, and adaptability to changing needs. It provides a solid foundation for businesses to design and create their ideal working or retail space while reducing the initial investment and construction timeline compared to starting from scratch. The ability to modify and upgrade the interior without major renovations further enhances its appeal.
However, the decision to pursue warm shell construction should be based on careful consideration of functional requirements, budget constraints, timeline expectations, flexibility needs, tenant or ownership agreements, local regulations, and available expertise and resources. Each project is unique, and assessing these factors will help determine whether warm shell construction is the most suitable option.
Overall, warm shell construction offers a balance between functionality and customization, providing building owners, developers, and tenants with the opportunity to create spaces tailored to their specific needs. By understanding the concept of warm shell construction and considering its implications, stakeholders can make informed decisions that lead to successful and efficient building developments.
Frequently Asked Questions about What Does Warm Shell Mean In Construction
Was this page helpful?
At Storables.com, we guarantee accurate and reliable information. Our content, validated by Expert Board Contributors, is crafted following stringent Editorial Policies. We're committed to providing you with well-researched, expert-backed insights for all your informational needs.
0 thoughts on “What Does Warm Shell Mean In Construction”